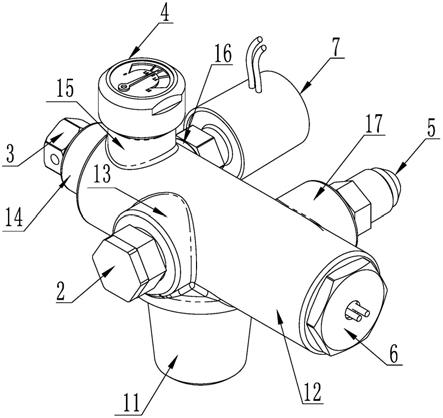
1.本实用新型涉及电动汽车配备的电池箱火灾抑制装置,尤其涉及电池箱火灾抑制装置中的电爆阀。
背景技术:
2.电爆阀广泛应用于气液系统中,多用作隔离阀,实现气液系统的启动控制或介质隔离,在电动汽车上都要求配备电池箱火灾抑制装置,目前,在电池箱火灾抑制装置中所使用的电爆阀如图1所示,它包阀体1、单向充气阀2、泄压阀3、压力表4、灭火剂喷射头5、复位电爆组件6、在阀体1上设有容器连接端11、电爆端12、充气加压端13和释放端14,在阀体1的充气加压端13设置有单向充气阀2和压力表4,复位电爆组件6设置在电爆端12,容器连接端11 与灭火瓶密封连接,这种结构的电爆阀在实际使用过程中存在如下问题:
3.①
在充气加压端13上同时安装有单向充气阀2和压力表4,使用时必须先将压力表4拆除然后才能通过单向充气阀2进行灭火剂介质的充入,充完后再将压力表4旋上,这样既不方便,也存在压力表4虚接漏气现象。
4.②
复位电爆组件6在冲破阀膜片65的过程中,装有刺膜刀63的导向套61 在电爆头60点燃引爆后瞬间的气压作用下,将弹簧62压并在导向套61和膜压套64之间,由于此时的弹簧62处于压并状态,虽然在刺膜刀63上设有出气侧壁长孔66,但灭火剂只能从挤压的弹簧62的细小缝隙中进入,因此,灭火剂释放量受到很大阻力,不能全截面大流量释放,直接影响到灭火效率。
5.为了解决现有技术存在的上述不足,申请人提供了一种低阻尼大流量释放的电爆阀,灭火剂充入便捷,压力表无需拆卸,电爆头点燃引爆后,灭火剂能全截面喷出释放,克服了现有技术中充气不便捷,充气或灌装效率低下。
技术实现要素:
6.本实用新型的目的在于提供一种低阻尼全截面释放的电爆阀,以解决上述背景技术中提出的问题。
7.为实现上述目的,本实用新型提供如下技术方案:
8.一种低阻尼大流量释放的电爆阀,包括阀体、单向充气阀、泄压阀、压力表、灭火剂喷射头、复位电爆组件和压力传感器,阀体包括容器连接端、电爆端、充气加压端、释放端、压力表连接端、传感器连接端和喷射端,电爆端和释放端对称设置在容器连接端上方,压力表连接端与传感器连接端设置在释放端一侧,充气加压端和喷射端分别设置在阀体的两端,单向充气阀设置在充气加压端,泄压阀设置在释放端,压力表设置在压力表连接端,灭火剂喷射头设置在喷射端上,复位电爆组件设置在电爆端,压力传感器设置在传感器连接端上,容器连接端与灭火器容器的旋接口密封连接。
9.进一步,在所述阀体的电爆端内部从外向内顺序设有爆破卡口、导向孔、复位泄压孔和压套孔,在压力表连接端内设有表连接孔,在释放端内部设有泄压阀孔,在压套孔和泄
压阀孔之间设有阀体通孔,在充气加压端内设有充气阀孔,在喷射端内设有出液孔,所述出液孔与复位泄压孔相连通,在传感器连接端内设有传感器连接孔,传感器连接孔与阀体通孔相连通,在容器连接端内设有灭火剂通孔;灭火剂通孔与阀体通孔相连通,压力传感器密封地安装在传感器连接孔中。
10.进一步,所述单向充气阀包括充气阀座、充气口压簧、充气芯、充气口盖和充气密封圈,充气阀座设置在充气阀孔内,充气口压簧设置在充气阀座内部,充气芯设置在充气口压簧上端,充气口盖设置在充气阀座上,在充气芯与充气阀座连接处、充气阀座与充气口盖连接处以及充气阀座与充气阀孔连接处均设有充气密封圈,所述灭火剂喷射头包括四氟垫片和管接头,管接头与喷射端之间固定设有四氟垫片。
11.进一步,所述泄压阀包括泄压阀套、泄压阀垫圈和泄压阀膜片,所述泄压阀套通过泄压阀孔设置在释放端上,泄压阀垫圈设置在泄压阀孔内并与泄压阀套间隙配合,在泄压阀垫圈顶部密封设有泄压阀膜片。
12.进一步,所述泄压阀为单向阀,可以重复使用。
13.进一步,所述压力表包括压力表窗口和连接端,压力表通过连接端密封地安装在表连接孔内。
14.进一步,所述复位电爆组件的结构为:包括电爆头、导向套、弹簧、刺膜刀、膜压套、阀膜片和侧壁长孔,电爆头固定设于爆破卡口内,导向套可活动的设于导向孔内并置于电爆头内侧,弹簧设置在导向套上,并置于复位泄压孔中,刺膜刀固定设于导向套上,在刺膜刀上设有侧壁长孔,阀膜片密封设置在膜压套上,膜压套设在压套孔内,使得刺膜刀的刀锋对应于阀膜片的方向,弹簧设于膜压套和导向套之间,导向套与导向孔之间以及电爆头与爆破卡口连接处均设有密封圈。
15.进一步,所述电爆头与爆破卡口连接处设有型密封圈,o型密封圈与爆破卡口的内壁贴合;在导向套与导向孔之间通过密封圈密封固定,所述弹簧的一端卡在膜压套与阀膜片相对应的一侧,弹簧的另一端套在导向套上。
16.进一步,所述刺膜刀为锥头多刀,所述锥头多刀包括锥头刀体和锥面刀片,锥面刀片沿锥头刀体的周向间隔分布。
17.与现有技术相比,本实用新型的有益效果是:本实用新型将单向充气阀与压力表分别单独设置,当进行充气或灌装时,直接使用单向充气阀,无需拆卸压力表,且充气芯四周的开孔使充气或灌装的速度加大,极大的提高充气效率,使用方便且降低磨损率,本实用新型在电爆端内侧增设复位泄压孔,当电爆头点燃引爆后瞬间,导向套被巨大的压力向膜压套处推送时,导向套滑移进入复位泄压孔时,复位泄压孔与导向套右端的爆炸腔内相通,二者间相通等压,此时,灭火瓶内的高压气体推动导向套向右移动复位,弹簧恢复伸展,这样灭火瓶中带压灭火剂液体通过刺膜刀上开设的侧壁长孔及复位后增大的电爆阀弹簧的间隙释放,该复位泄压孔的设置平衡了腔体内瞬时爆破的压力,同时增大了弹簧的间隙,增大了灭火剂液体的释放流量,大大的解决了现有的不足,提高了灭火剂的灭火效率。
18.将现有的管式斜面刀结构刺膜刀改进成锥头径向多刀结构,在锥头管体的关部锥面上沿周向间隔设置了锥面刀片,锥头管体的另一端固定安装在导向套上,这样,当导向套在左移刺破阀膜片的过程中,当导向套左移到极限位置时,固定在头部锥面上锥面刀片能从阀膜片的中心开始将阀膜片沿径向刺破成多个伞面拼接子膜片,在高压液体灭火剂的作
用下,所有子膜片直接被向右侧掀起,能实现满截面液体流出,从而克服了现有技术中刺膜刀刺破阀膜片后不能全截面大流量释放的问题,保证了灭火剂在电爆阀开启时能低阻尼全截面通过,它是提高电池箱火灾抑制装置的灭火效率的关键点之一。
附图说明
19.图1为现有技术的结构示意图;
20.图2为本实用新型的立体结构示意图;
21.图3为本实用新型的另一侧的立体结构示意图;
22.图4为本实用新型的结构示意图;
23.图5为图4的a-a剖视图;
24.图6为图4的b-b剖视图;
25.图7为本实用新型阀体的结构示意图;
26.图8为图4的一侧结构示意图;
27.图9为图8的c-c剖视图;
28.图10为图9的d-d剖视图;
29.图11为刺膜刀的一种结构示意图;
30.图12为图11的右视图;
31.图中:1-阀体;2-单向充气阀;3-泄压阀;4-压力表;5-灭火剂喷射头; 6-复位电爆组件;7-压力传感器;11-容器连接端;12-电爆端;13-充气加压端; 14-释放端;15-压力表连接端;16-传感器连接端;17-喷射端;21-充气阀座; 22-充气口压簧;23-充气芯;24-充气口盖;25-充气密封圈;31-泄压阀套;32
‑ꢀ
泄压阀垫圈;33-泄压阀膜片;51-四氟垫片;52-管接头;60-电爆头;61-导向套;62-弹簧;63-刺膜刀;64-膜压套;65-阀膜片;66-侧壁长孔;101-爆破卡口;102-导向孔;103-复位泄压孔;104-压套孔;105-表连接孔;106-泄压阀孔;107-阀体通孔;108-充气阀孔;109-出液孔;110-传感器连接孔;111-灭火剂通孔;631-锥头刀体;632-锥面刀片。
具体实施方式
32.下面将结合本实用新型的实施例和附图对本实用新型实施的技术方案进行清楚、完整地描述,显然,所描述的实施例仅仅是本实用新型一部分实施例,而不是全部的实施例。基于本实用新型中的实施例,本领域普通技术人员在没有做出创造性劳动前提下所获得的所有其他实施例,都属于本实用新型保护的范围。
33.实施例1:一种低阻尼大流量释放的电爆阀,如图2-10所示,包括阀体1、单向充气阀2、泄压阀3、压力表4、灭火剂喷射头5、复位电爆组件6和压力传感器7,阀体1包括容器连接端11、电爆端12、充气加压端13、释放端14、压力表连接端15、传感器连接端16和喷射端17,电爆端12和释放端14对称设置在容器连接端11上方,压力表连接端15与传感器连接端16设置在释放端 14一侧,充气加压端13和喷射端17分别设置在阀体1的两侧,在阀体1的电爆端12内部从外向内顺序设有爆破卡口101、导向孔102、复位泄压孔103和压套孔104,在压力表连接端15内设有表连接孔105,在释放端14内部设有泄压阀孔106,在压套孔104和泄压阀孔106之间设有阀体通孔107,在充气加压端13内设有充气阀孔108,在喷射端17内设有出
液孔109,所述出液孔109与复位泄压孔103相连通,在传感器连接端16内设有传感器连接孔110,传感器连接孔110与阀体通孔107相连通,在容器连接端11内设有灭火剂通孔111,灭火剂通孔111与阀体通孔107相连通,单向充气阀2包括充气阀座21、充气口压簧22、充气芯23、充气口盖24和充气密封圈25,充气阀座21设置在充气阀孔108内,充气口压簧22设置在充气阀座21内部,充气芯23设置在充气口压簧22上端,充气口盖24设置在充气阀座21上,在充气芯23与充气阀座21 连接处、充气阀座21与充气口盖24连接处以及充气阀座21与充气阀孔108连接处均设有充气密封圈25,泄压阀3包括泄压阀套31、泄压阀垫圈32和泄压阀膜片33,泄压阀套31通过泄压阀孔106设置在释放端14上,泄压阀垫圈32 设置在泄压阀控32内并与泄压阀孔106间隙配合,在泄压阀垫圈32顶部密封设有泄压阀膜片33,其中压力表4包括压力表窗口和连接端,连接端置于表连接孔105内,压力表窗口设在连接端上且置于阀体1的外端面上,在连接端与表连接孔105之间设有密封圈,将压力表4的连接端嵌入在所述电爆阀阀体1 的内部,确保安装结构稳固,其中灭火剂喷射头5包括四氟垫片51和管接头52,管接头52设置在出液孔109内部,管接头52与出液孔109之间固定设有四氟垫片51;复位电爆组件6包括电爆头60、导向套61、弹簧62、刺膜刀63、膜压套64、阀膜片65和侧壁长孔66,电爆头60固定设于爆破卡口101内,导向套61可活动的设于导向孔102内并置于电爆头60内侧,弹簧62设置在导向套 61上,并置于复位泄压孔103中,刺膜刀63固定设于导向套61上,在刺膜刀 63上设有侧壁长孔66,阀膜片65密封设置在膜压套64上,膜压套64设在压套孔104内,使得刺膜刀63的刀锋对应于阀膜片65的方向,弹簧62设于膜压套64和导向套61之间,导向套61与导向孔102之间以及电爆头60与爆破卡口101连接处均设有密封圈,电爆头60与爆破卡口101连接处的密封圈与爆破卡口101的内壁贴合,导向套61与导向孔102之间通过密封圈密封固定,能够确保密封效果良好,在传感器连接孔110中密封地设有压力传感器7。
34.本实用新型的工作原理:本实用新型设置单向充气阀2,当需要充气或灌装液体时,只需将充气口盖24取下,随后将充气或灌装工具旋装到充气阀座21 上,此时充气芯23被顶开,充气口压簧22压缩,气体或液体通过充气芯23的四周并进入周身四个孔内,从而进入电爆阀阀体1内部,进行充气或灌装时,充气芯23四周的开孔使充气或灌装的速度加大,可提高生产效率,在充气或灌装完成后,取下充气或灌装工具,充气芯23在受充气口压簧22的作用下回复到原位,并通过充气密封圈25完成密封,解决了现有的电爆阀充气或灌装时效率低下的问题。
35.本实用新型在阀体1的电爆端12内部设置复位泄压孔103,在外部电流作用下,电爆头60燃烧并快速瞬时产生强大气体,在气压力下导向套61快速沿气移动,使得刺膜刀63刺破阀膜片65,使容器内液体在预制压力的作用下通过管接头52释放出来,在移动过程中,当导向套61移动至复位泄压孔103时,导向套61与复位泄压孔103之间产生缝隙,导向套61所在腔体内的压力快速通过缝隙释放,弹簧62得以轻松复位,此时液体通过刺膜刀63上的侧壁长孔 66及复位后增大的弹簧62间隙释放,该复位泄压孔103的设置增大了压簧间隙,增大了灭火剂液体释放流量,避免了现有的灭火剂液体在释放时流量受限以及不能达到流量要求的问题。
36.实施例2:与实施例1不同之处在于刺膜刀63,如图11~12所示,在实施例1中,所述刺膜刀63为管式斜面笔尖结构,它只能对阀膜片65进行半周长切割刺破,不能满圆刺破分割,影响灭火剂的全截面释放。为了实现即开就能实现全截面释放,本例中刺膜刀63采用锥
头多刀结构,所述锥头多刀包括锥头刀体631和锥面刀片632,锥面刀片632沿锥头刀体631的周向间隔分布,该结构能够使得阀膜片65均匀被刺破,减少了部分膜片可能影响灭火剂液体的释放流量。
37.需要说明的是,以上仅为本实用新型的优选实施例而已,并不用于限制本实用新型,尽管参照前述实施例对本实用新型进行了详细的说明,对于本领域的技术人员来说,其依然可以对前述各实施例所记载的技术方案进行修改,或者对其中部分技术特征进行等同替换。凡在本实用新型的精神和原则之内,所作的任何修改、等同替换、改进等,均应包含在本实用新型的保护范围之内。