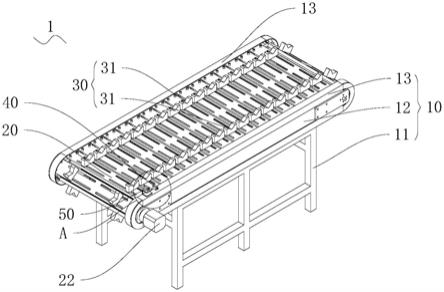
1.本实用新型属于零件加工技术领域,具体涉及一种零件下料装置。
背景技术:
2.零件如电机转子轴在生产线进行生产时,需要经过上料、加工、下料、存储等工序,现有技术中零件在加工机床加工完成后,工人需要在加工机床出料处等待,机械手将加工完成的零件夹取至出料处后,再由工人将零件从机械手上取下后存储入库。上述下料方式工人需一直在下料处等待,造成了人力资源的浪费,且工人直接与机械手接触,存在安全隐患。
技术实现要素:
3.本实用新型提供一种零件下料装置,旨在解决现有技术中零件下料时工人需一直在下料处等待,造成了人力资源的浪费,且工人直接与机械手接触,存在安全隐患的问题。
4.为实现上述目的,本实用新型采用的技术方案是:提供一种零件下料装置,其特征在于,包括:架体;输送组件,设于所述架体,具有循环的输送轨道;多个支撑组件,沿输送方向间隔设于所述输送轨道上;第一检测传感器,设于所述输送轨道的输送末端,且与所述支撑组件的高度相对应;以及第二检测传感器,设于所述输送轨道的输送末端,且与所述第一检测传感器具有高度差,在所述输送组件运行时,所述支撑组件承载有被输送的零件,所述第一检测传感器能够检测所述支撑组件的位置是否到位,所述第二检测传感器能够检测所述支撑组件上是否承载有所述零件。
5.在一种可能的实现方式中,所述输送组件包括:两个传动轴,平行且可转动地分设于所述架体两端;驱动元件,设于所述架体,且与其中一个所述传动轴传动连接;两个传动元件,均绕设于两个所述传动轴,且与所述传动轴传动配合;以及多个支撑板,沿输送方向间隔设置,每个所述支撑板设于两个所述传动元件之间,多个所述支撑板与多个所述支撑组件一一对应连接,所述传动元件和所述支撑板构成所述输送轨道。
6.在一种可能的实现方式中,每个所述支撑组件均包括:若干支撑垫块,设于所述支撑板;以及若干紧固件,连接于对应的所述支撑垫块和所述支撑板。
7.在一种可能的实现方式中,所述支撑垫块上开设有用于承载所述零件的容纳槽。
8.在一种可能的实现方式中,所述支撑板垂直于输送方向开设有若干可供所述支撑垫块滑动的调节槽,所述支撑垫块在与所述调节槽的对应位置开设有与所述紧固件配合的安装孔。
9.在一种可能的实现方式中,每个所述传动轴均设有两个链轮,所述传动元件为与对应的所述链轮相啮合的链条,每个所述支撑板与两个所述链条均连接。
10.在一种可能的实现方式中,所述架体包括:支架;两个安装架,平行设于所述支架上,所述安装架开设有用于容纳所述链轮的第一安装槽,以及用于容纳所述链条的第二安装槽,两个所述传动轴均设于两个所述安装架之间,且两个所述传动轴的两端均分别与两
个所述安装架转动配合,所述驱动元件安装于其中一个所述安装架;以及用于容纳所述链条的第二安装槽,所述驱动元件安装于其中一个所述安装架;以及两个护罩,对应罩设于两个所述安装架外。
11.在一种可能的实现方式中,零件下料装置还包括设于所述架体且位于所述输送组件下方的托轮组件。
12.在一种可能的实现方式中,所述托轮组件包括:托轮架,设于所述架体,且位于所述输送轨道的下方;以及多个承托轮,沿输送方向可转动地设于所述托轮架,且位于所述输送轨道的下方。
13.在一种可能的实现方式中,所述第一检测传感器和所述第二检测传感器均为光电传感器。
14.本实用新型实施例中输送组件设于架体,多个支撑组件沿输送方向间隔设于输送组件。当加工机床的零件加工完成后,机械手将零件从加工机床取出,输送组件停止运行,方便机械手将零件放到与之邻近的支撑组件上。在机械手完成该动作后,输送组件继续运行,带动支撑组件和其上的零件一同向输送末端运动一个行程距离,即相邻的两个支撑组件的距离,以使得后续的支撑组件到达机械手下料处,工人无需与机械手接触,提高了生产作业的安全性。
15.本实用新型的输送轨道用于安装支撑组件,并对支撑组件和其上的零件进行转移。输送组件上设有多个用于支撑零件的支撑组件,能够起到零件支撑和临时存放的作用。当零件下料装置上存放的零件到达一定数量后,工人可以进行统一收取,无需工人一直在下料处等待,与现有的每条生产线至少需要一个工人在下料处等待相比,单个工人可以同时照看多个生产线,减小了人力资源的浪费。
16.本实用新型在输送末端设有第一检测传感器,能够检测支撑组件的位置,使得输送组件在停止运行时支撑组件能够与机械手的下料位置相对应,保证支撑组件能够准确接收由机械手转运的零件;输送末端还设有第二检测传感器,当第二检测传感器检测到零件时,说明零件下料装置上的零件数量达到饱和,整个生产线停止运行,能够防止零件从输送末端掉落。
附图说明
17.图1为本实用新型一实施例零件下料装置的立体图;
18.图2为图1中a部的局部放大图;
19.图3为本实用新型一实施例零件下料装置的结构示意图;
20.图4为本实用新型一实施例零件下料装置另一角度的结构示意图;
21.图5为图4中b-b方向的剖视图;
22.图6为本实用新型一实施例中输送组件的结构示意图;
23.图7为本实用新型一实施例中安装架的结构示意图;
24.图8为本实用新型一实施例中支撑板与支撑组件的安装示意图;
25.图9为本实用新型一实施例中支撑板与支撑组件另一角度的安装示意图。
26.附图标记说明:
27.1、零件下料装置
28.10、架体
ꢀꢀꢀꢀꢀꢀꢀꢀꢀꢀꢀꢀꢀꢀ
11、支架
ꢀꢀꢀꢀꢀꢀꢀꢀꢀꢀꢀꢀꢀꢀ
12、安装架
29.121、第一安装槽
ꢀꢀꢀꢀꢀꢀꢀ
122、第二安装槽
ꢀꢀꢀꢀꢀꢀꢀ
13、护罩
30.20、输送组件
ꢀꢀꢀꢀꢀꢀꢀꢀꢀꢀ
21、传动轴
ꢀꢀꢀꢀꢀꢀꢀꢀꢀꢀꢀꢀ
211、链轮
31.22、驱动元件
ꢀꢀꢀꢀꢀꢀꢀꢀꢀꢀ
23、传动元件
ꢀꢀꢀꢀꢀꢀꢀꢀꢀꢀ
24、支撑板
32.241、调节槽
ꢀꢀꢀꢀꢀꢀꢀꢀꢀꢀꢀ
30、支撑组件
ꢀꢀꢀꢀꢀꢀꢀꢀꢀꢀ
31、支撑垫块
33.311、容纳槽
ꢀꢀꢀꢀꢀꢀꢀꢀꢀꢀꢀ
32、紧固件
ꢀꢀꢀꢀꢀꢀꢀꢀꢀꢀꢀꢀ
40、第一检测传感器
34.50、第二检测传感器
ꢀꢀꢀꢀ
60、托轮组件
ꢀꢀꢀꢀꢀꢀꢀꢀꢀꢀ
61、托轮架
35.62、承托轮
具体实施方式
36.为了使本实用新型所要解决的技术问题、技术方案及有益效果更加清楚明白,以下结合附图及实施例,对本实用新型进行进一步详细说明。应当理解,此处所描述的具体实施例仅仅用以解释本实用新型,并不用于限定本实用新型。
37.需要说明的是,当元件被称为“固定于”、“固定”、“固设”另一个元件,它可以直接在另一个元件上或者也可以存在居中元件。当一个元件被认为是“连接于”、“连接”另一个元件,它可以是直接连接到另一个元件或者可能同时存在居中元件。当元件被称为“设置于”、“设于”另一个元件,它可以直接在另一个元件上或者也可以存在居中元件。“多个”指两个及以上数量。“至少一个”指一个及以上数量。“若干”指一个及以上数量。
38.除非另有定义,本文所使用的所有的技术和科学术语与属于本实用新型的技术领域的技术人员通常理解的含义相同。
39.请参阅图1至图9,现对本实用新型实施例所提供的零件下料装置1进行说明。
40.请参阅图1和图2,本实用新型实施例提供一种零件下料装置1,包括:包括:架体10;输送组件20,设于架体10,具有循环的输送轨道;多个支撑组件30,沿输送方向间隔设于输送轨道上;第一检测传感器40,设于输送轨道的输送末端,且与支撑组件30的高度相对应;以及第二检测传感器50,设于输送轨道的输送末端,且与第一检测传感器40具有高度差,在输送组件20运行时,支撑组件30承载有被输送的零件,第一检测传感器40能够检测支撑组件30的位置是否到位,第二检测传感器50能够检测支撑组件30上是否承载有零件。
41.本实用新型实施例中输送组件20设于架体10,多个支撑组件30沿输送方向间隔设于输送轨道上。当加工机床的零件加工完成后,机械手将零件从加工机床取出,输送组件20停止运行,方便机械手将零件放到与之邻近的支撑组件30上。输送轨道邻近机械手的一端为输送起始端,远离机械手的一端为输送末端。在机械手完成零件释放动作后,输送组件20继续运行,带动支撑组件30和其上的零件一同向输送末端运动一个行程距离,即相邻的两个支撑组件30的距离,以使得后续的支撑组件30到达机械手下料处,工人无需与机械手接触,提高了生产作业的安全性。
42.本实用新型实施例中输送组件20用于安装支撑组件30,并对支撑组件30和其上的零件进行转移。输送组件20具体可以是带式输送机、链板输送机等。输送组件20上设有多个用于支撑零件的支撑组件30,能够起到零件支撑和临时存放的作用。当零件下料装置1上存放的零件到达一定数量后,工人可以进行统一收取,无需工人一直在下料处等待,与现有的每条生产线至少需要一个工人在下料处等待相比,单个工人可以同时照看多个生产线,减
小了人力资源的浪费。
43.本实用新型实施例中输送末端设有第一检测传感器40,能够检测支撑组件30的位置,使得输送组件20在停止运行时支撑组件30能够与机械手的下料位置相对应,保证支撑组件30能够准确接收由机械手转运的零件;输送末端还设有第二检测传感器50,当第二检测传感器50检测到零件时,说明零件下料装置1上的零件数量达到饱和,整个生产线停止运行,能够防止零件从输送末端掉落。
44.本实用新型实施例中支撑组件30的形状应当与零件的形状相适配,支撑组件20具体可以是单个或多个支撑块、支撑板、支撑座组合形成的结构形式,安装在输送轨道上。为了保证支撑组件30能够对零件进行稳定的支撑,必要时,还可在支撑组件30上设置限位槽、限位板或其他能够起到限位支撑作用的结构。
45.需要说明的是,本实用新型实施例中第一检测传感器40、第二检测传感器50、零件下料装置1和加工机床、机械手均电连接,并通过plc控制程序进行控制。第一检测传感器40和第二检测传感器50均设置在输送末端,分别用于对支撑组件30和零件进行检测。第一检测传感器40和第二检测传感器50的高度不同,可通过不同高度的固定板安装固定。具体的,第一检测传感器40和第二检测传感器50可以是红外传感器、光电传感器、光纤传感器等,本实用新型实施例对此不作限制。
46.需要说明的是,第一检测传感器40和第二检测传感器50同设于输送轨道的输送末端,且具有高度差。二者检测对象不同,第一检测传感器40和第二检测传感器50可以通过一个安装座安装于同一位置,也可以分别通过各自的安装座安装于相邻或相对的位置,本实用新型实施例对此不作限制。
47.请参阅图6,在一些可能的实施例中,输送组件20包括:两个传动轴21,平行且可转动地分设于架体10两端;驱动元件22,设于架体10,且与其中一个传动轴21传动连接;两个传动元件23,均绕设于两个传动轴21,且与传动轴21传动配合;以及多个支撑板24,沿输送方向间隔设置,每个支撑板24设于两个传动元件23之间,多个支撑板24与多个支撑组件30一一对应连接,传动元件23和支撑板24构成输送轨道。
48.本实施例中两个传动元件23均绕设于两个传动轴21,支撑板24的两端分别连接于两个传动元件23的外周壁,驱动元件22工作时将动力传递至传动轴21和传动元件23,使支撑板24和支撑板24上的支撑组件30以及零件能够逐渐从邻近机械手的一端向另一端移动。
49.本实施例中传动轴21与传动元件23传动配合,传动轴21上可以设置带轮或链轮211,对应的传动元件23可以是皮带或链条。驱动元件22与其中一个传动轴21传动连接,驱动元件22可以是电机、气缸等。驱动元件22与传动轴21之间还可以设置联轴器、曲柄等结构,具体的结构形式可以根据实际使用需要进行选择,本实施例对此不作限制。
50.在一个具体的实施例中,输送组件20中驱动元件22为电机,传动元件23为链条,电机通过传动轴21将动力传输至链条,由链条带动支撑板24移动。电机与传动轴21之间可根据实际情况设置减速器、联轴器等。
51.在另一个具体的实施例中,输送组件20中驱动元件22为往复伸缩的气缸,传动元件23为皮带,气缸通过曲柄连杆机构带动传动轴21转动,由皮带带动支撑板24移动。
52.请参阅图8和图9,在一些可能的实施例中,每个支撑组件30均包括:若干支撑垫块31,设于支撑板24;以及若干紧固件32,连接于对应的支撑垫块31和支撑板24。
53.本实施例中支撑垫块31通过紧固件32可拆卸地安装在支撑板24上,方便对支撑垫块31的形状、位置和数量进行调整或更换。例如,当零件为电机转子轴时,支撑垫块31的数量可以是两个,两个支撑垫块31的位置分别邻近转子轴的两端设置。当零件体积较小时,支撑垫块31可以设置一个。紧固件32用于将支撑垫块31固定在支撑板24上,紧固件32可以是螺钉、卡扣等。
54.请参阅图8和图9,在一些可能的实施例中,支撑垫块31上开设有用于承载零件的容纳槽311,容纳槽311用于容纳或部分容纳零件,其形状和尺寸应当与零件相适配。例如,当零件为电机转子轴时,容纳槽311可以为v形槽。当支撑垫块31具有多个时,多个支撑垫块31的容纳槽311应当相贯通。
55.需要说明的是,当零件的表面质量要求高时,为了避免支撑垫块31对零件表面造成磕碰或划伤,支撑垫块31可以采用树脂、木材等材料制作。当支撑垫块31为铸铁、黄铜、不锈钢等材料制作时,可以在边缘设置倒角以免划伤零件。
56.请参阅图8和图9,在一些可能的实施例中,支撑板24垂直于输送方向开设有若干可供支撑垫块31滑动的调节槽241,支撑垫块31在与调节槽241的对应位置开设有与紧固件32配合的安装孔。
57.本实施例中支撑垫块31可沿调节槽241滑动,能够调节支撑垫块31的位置和相邻两个支撑垫块31之间的距离,以适应不同规格尺寸的零件。支撑垫块31通过紧固件32固定在支撑板24上,紧固件32具体可以是螺钉、销钉等零件,对应的安装孔可以是螺纹孔或销孔等。
58.请参阅图4、图5和图6,在一些可能的实施例中,每个传动轴21均设有两个链轮211,传动元件23为与对应的链轮211相啮合的链条,每个支撑板24与两个链条均连接。
59.本实施例中传动轴21上设有两个链轮211,两个链轮211分别与两个传动元件23啮合传动,支撑板24的两端分别搭设于两个链条上,并通过螺栓安装固定。当传动元件23为皮带时,传动轴21上应当设置与皮带配合传动的带轮。
60.请参阅图1、图4和图7,在一些可能的实施例中,架体10包括:支架11;两个安装架12,平行设于支架11上,所述安装架12开设有用于容纳所述链轮211的第一安装槽121,以及用于容纳链条的第二安装槽122,两个传动轴21均设于两个安装架12之间,且两个传动轴21的两端均分别与两个安装架12转动配合,驱动元件22安装于其中一个安装架12;以及两个护罩13,对应罩设于两个安装架12外。
61.本实施例中支架11可以采用多个型钢焊接制作,用于对安装架12进行支撑,两个安装架12平行设于支架11两侧。传动轴21的两端分别与两个安装架12通过轴承转动配合,链轮211容置于第一安装槽121,链条容置于第二安装槽122,护罩13设于安装架12外,能够防止灰尘等杂质进入链条和链轮211,导致传动卡滞。
62.由于实际使用时传动元件23和支撑板24的重量较大,位于下方的支撑板24和传动元件23受重力的影响会下垂,且靠近架体10中间位置的支撑板24下垂距离最大,长此以往,会导致支撑板24之间的间隙增大,输送组件20在运行时行程距离也会增大,导致支撑组件30无法准确地接收机械手转运的零件。
63.为了解决上述问题,请参阅图4和图5,在一些可能的实施例中,零件下料装置1还包括设于架体10且位于输送组件20下方的托轮组件60,用于支撑并托起位于下方的支撑板
24,避免其长时间使用后变形较大,影响输送组件20的运行精度。
64.需要说明的是,本实施例中托轮组件60的数量为一个,且与支撑板24的中间位置相对应。当支撑板24的重量较重时,可以根据需要设置两个或多个托轮组件60,多个托轮组件60可以平行排列设于输送组件20的下方。
65.除上述增加托轮组件60数量的方式外,当输送组件20下方仅设有一个托轮组件60时,为了对输送组件20的支撑板24和传动元件23形成稳定的支撑,还可以通过调节托轮组件60的尺寸来改变托轮组件60的支撑范围。
66.请参阅图4和图5,在一些可能的实施例中,托轮组件60包括:托轮架61,设于架体10,且位于输送轨道的下方;以及多个承托轮62,沿输送方向可转动地设于托轮架61,且位于输送轨道的下方。承托轮62用于支撑下方的支撑板24,为了减小承托轮62对支撑板24的磨损或划伤,承托轮62可以采用塑料、橡胶等材质制作。
67.在一个具体的实施例中,请参阅图8,为了避免承托轮62与调节槽241干涉,本实施例中承托轮62对应设置在支撑板24的中间位置,支撑板24上关于承托轮62两侧各设置有两个调节槽241。
68.除上述实施例所记载的托轮组件60的结构外,作为一个变形的实施例中,托轮架61还可以具有多个平行设置的托轮安装槽,多个托轮安装槽内均可转动地设有多个承托轮62。
69.请参阅图1和图2,在一些可能的实施例中,第一检测传感器40和第二检测传感器50均为光电传感器。光电传感器检测距离长,响应时间短,且不易受到光照、振动、噪音等环境因素的干扰,工作可靠稳定。
70.当然,实际使用时可根据实际需要选择其他种类的传感器或检测元件,如激光距离传感器、感应光栅等。例如,第一检测传感器40和第二检测传感器50均可以是设置在架体10位于输送组件20的两侧的一组感应光栅,感应光栅包括相对设置的发射端和接收端,能够判断支撑组件30或零件的位置。
71.可以理解的是,上述实施例中的各部分可以进行自由地组合或删减以形成不同的组合实施例,在此不再赘述各个组合实施例的具体内容,在此说明之后,可以认为本实用新型说明书已经记载了各个组合实施例,能够支持不同的组合实施例。
72.以上所述仅为本实用新型的较佳实施例而已,并不用以限制本实用新型,凡在本实用新型的精神和原则之内所作的任何修改、等同替换和改进等,均应包含在本实用新型的保护范围之内。