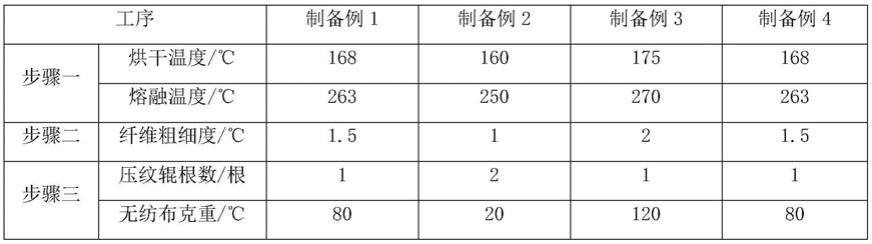
1.本技术涉及人造花的领域,尤其是涉及一种无纺布仿真花制作工艺及仿真花。
背景技术:
2.仿真花是指用绷绢、皱纸、涤纶、塑料、水晶等材料制成的假花,业界泛称为人造花。仿真花一般由织物花瓣组成主体部分,模仿花瓣的织物片被模塑成逼真的造型,并着色和/或印制,在视觉上提供逼真的外表。布匹由于容易制造等优点,被广泛于无纺布制作,通常为了使得花瓣长久保持硬挺、立体的造型,以机织物制作仿真花花瓣更为常见,特别是以聚酯机织物制作仿真花。这类以机织物为原料制作仿真花的工艺通常会存在如下问题:机织物由织线或纤维横纵交织而成,在将机织物裁切成花瓣形状的料片时,边缘部位容易出现“毛边脱开”问题。
3.针对上述问题,相关技术中主要有以下解决方式:其一,采用加热熔化或熔合的方式消除织物边缘部位的织线或纤维的作用,减少毛边脱开,该种方式相应地也增加了仿真花制作工艺的工序繁琐度。
4.其二,直接采用热切的方式对织物进行裁切,即在裁切花瓣形状的料片时使纤维的切端口融合从而防止其散开脱落,但是该种方式通常适用于单层织物裁切,多层织物叠放后裁切时容易使得织物层之间发生黏连,影响加工效率以及裁切效果,限制了仿真花制作效率的提升。
5.其三,对机织物进行涂层处理,提升机织物硬挺度的同时使得机织物的织线或纤维被涂层黏连,裁切后边缘部位织线或纤维不易脱开,但该种方式不可避免地存在voc污染问题。
6.因而,如何寻找一种能更好地解决仿真花制作过程中“毛边脱开”问题的替代解决方案仍是本领域技术人员有待解决的问题。
技术实现要素:
7.为了减少仿真花制作过程中的毛边脱开,本技术提供一种无纺布仿真花制作工艺及仿真花。
8.第一方面,本技术提供一种无纺布仿真花制作工艺,采用如下的技术方案:一种无纺布仿真花制作工艺,以无纺布为制作花瓣的原料,所述无纺布的制作工艺包括如下步骤:步骤一、将纺丝粒子烘干,加热熔融,形成纺丝料;步骤二、将纺丝料经喷丝口喷出纺制成纤维长丝;步骤三、将纤维长丝平铺成网后,用至少一根压纹辊与承压辊配合进行热压定型,得无纺布;所述压纹辊表面均布有压纹凸块。
9.通过采用上述技术方案,以特定工艺制得的无纺布作为制作仿真花的原料,裁切
后不易出现“毛边脱开”问题,省去了常规的“熔化或熔合”工序,极大精简了工序。同时,由于无纺布制备过程中采用带有压纹凸块的压纹辊进行热压,使得无纺布表面形成凹凸纹路,在后续制作工序中花瓣受热呈现一定的收缩,使得花瓣可以长久保持立体的造型效果,与相关技术相比较无需对无纺布进行涂层处理,具有低voc、绿色环保的优势。此外,由于采用无纺布作为原料,相较于机织物生产更高效,使得利用本发明可以更高效地制作无纺布仿真花,经济效益显著。
10.优选地,步骤一所用纺丝粒子为pet粒子、pp粒子、或者pet粒子与pbt粒子的混合物。
11.通过采用上述技术方案,制得的无纺布不进行涂层处理也均具有良好的尺寸稳定性,制成的仿真花造型立体且持久,裁切后边缘不易出现“毛边脱开”问题。
12.优选地,步骤二制成的纤维长丝的粗细度为1~2d;步骤三所得无纺布的克重为20~120g/m2。
13.通过采用上述技术方案,制得无纺布原料更为轻薄,但同时能够保持花瓣造型后的耐久度,制作的仿真花更为逼真。
14.优选地,包括如下步骤,裁切工序:将无纺布裁切成花瓣形状,得裁切料片;染色工序:将裁切料片浸渍于染液,浸渍结束后脱液、烘干,得上色料片;定型工序:于180-250℃将上色料片模塑热压成型,得具有立体花瓣形状的发色料片;组装工序:用粘合剂将发色料片与花蕊部件、花萼部件和花柄部件粘合固定,得仿真花。
15.通过采用上述技术方案,经裁切步骤得到裁切料片外缘齐整,不易出现“毛边脱开”问题;染色工序和定型工序相互关联,染色工序浸渍、脱液和烘干,染料附着于料片,在模塑热压时,可同时获得立体造型和使得染料上染固着,得到发色料片不仅颜色鲜艳且形状立体持久;最后,经过组装即可得到完成立体造型的仿真花。按照本技术工艺制作仿真花,无需对花瓣外缘进行额外的“熔化或熔合”处理,也无需进行喷涂上色,精简了工序,提高了仿真花制作效率。
16.优选地,所述裁切工序将至少两片无纺布层叠后同步裁切,得多片裁切料片;和/或,所述染色工序将至少两片裁切料片层叠后同步浸渍染液,得多片上色料片;和/或,所述成型工序将至少两片上色料片层叠后同步模塑热压成型,得多片发色料片。
17.通过采用上述技术方案,在裁切工序、染色工序和成型工序可同时加工多片料片,极大提高仿真花制作效率、减小了同批次加工料片的尺寸差异,制得的仿真花质量均一性更好。
18.优选地,所述裁切工序将至少两片无纺布层叠后同步裁切,得多片裁切料片;且,所述染色工序将至少两片裁切料片层叠后同步浸渍染液,得多片上色料片;且,所述成型工序将至少两片上色料片层叠后同步模塑热压成型,得多片发色料片。
19.通过采用上述技术方案,进一步提高了仿真花制作效率、减小了同批次加工的仿真花的质量差异。
20.优选地,所述裁切工序层叠的无纺布层数是2~20层,所述染色工序层叠的裁切料片层数是2~20层,所述成型工序层叠的上色料片的层数是2~20层。
21.通过采用上述技术方案,在提高制作效率、减少质量差异的同时,具有更好的可操作性。
22.优选地,所述染色工序采用料片夹紧固定装置对层叠的料片进行固定;所述料片夹紧固定装置包括定夹板、动夹板、连接杆和用于产生抵推作用力驱使动夹板靠近定夹板的锁紧件,所述连接杆一端固定于定夹板、另一端贯穿动夹板设置,所述锁紧件设置于连接杆远离定夹板一端。
23.通过采用上述技术方案,染色时使得连接杆依次贯穿层叠的料片,然后在连接杆的端部套设动夹板并用锁紧件锁紧,使得层叠的料片被夹紧在动夹板、定夹板之间,根据染色效果需要可以调整夹持松紧度。然后,将层叠的料片和料片夹紧装置共同浸渍于染液,浸渍时间根据染色需要进行灵活调整即可。浸渍结束后,将料片夹紧固定装置取出,采用离心等方式脱液,去除残余染液,然后烘干使得染料附着于料片,之后再进行成型工序即可。按照该种方式上色,可以使得花瓣外缘形成由外至内的上色效果,着色更加自然,制得的仿真花更为逼真。
24.在实际应用中,根据仿真花花瓣形状的不同,可以使用各种形状的定夹板和动夹板,以形成染色区域非染色区域整齐过度或者非整齐过度的着色效果。
25.优选地,所述连接杆内设有注液流道,所述注液流道至少一端延伸至连接杆端部形成注液口,所述注液口处可拆卸设有封堵件,所述连接杆的圆周侧面均布有与注液流道连通的出液微孔。
26.通过采用上述技术方案,卸去封堵件后可经由注液口向注液流道内注入染液,然后再将注液口封堵。如此,注液流道内的染液可以缓慢经由出液微孔渗出,使得料片由中心部向外晕染,形成渐变染色效果。再配合整体浸渍染色效果,可以获得多种多样的染色效果,能够制作出各种各样的装饰效果的仿真花。
27.优选地,所述压纹凸块在压纹辊表面成列分布,相邻两列所述压纹凸块之间间距为0.40-0.65毫米;所述压纹凸块的宽度为0.10-0.25毫米,长度为0.20-0.5毫米,厚度为0.2-0.5毫米;同列相邻所述压纹凸块之间的间距为0.2-0.3毫米。
28.通过采用上述技术方案,制得的无纺布表面纹路细腻,经过后续裁切、染色、成型后,基本无法分辨纹路,制得的仿真花更为逼真。
29.优选地,每列压纹凸块均沿平行于压纹辊轴线方向设置,且相邻两列的压纹凸块间错设置;相邻两列所述压纹凸块之间间距为0.5毫米;所述压纹凸块的宽度为0.15毫米,长度为0.2毫米,厚度为0.5毫米;同列相邻所述压纹凸块之间的间距为0.25毫米。
30.通过采用上述技术方案,制得的无纺布仿真花不良率低、造型稳定性高和“毛边脱开”率极低的效果。
31.第二方面,本技术提供一种仿真花,采用如下的技术方案:一种仿真花,由前述任一项无纺布仿真花制作工艺制得。
32.综上所述,本技术包括以下至少一种有益技术效果:1、本技术以特殊工艺制备的无纺布作为制作花瓣的原料,可以完全代替现有的聚酯机织物,有效解决了“毛边脱开”问题:其一、由于原料不存在横纵交织结构,长丝纤维是相互纠缠且经热压黏连在一起,本身不易出现“毛边脱开”问题;其二、无纺布制备工艺中选择特定热压辊热压成型,使得无纺布具有特殊纹路,不仅装饰效果佳且制成的花瓣有良好的硬
挺度和造型持久度;其三、无纺布原料无需涂层处理,具有低voc释放的优点,更为绿色环保。
33.2、本技术的无纺布仿真花制作工艺包括裁切工序、染色工序、成型工序和组装工序,无需对花瓣外缘进行额外的“熔化或熔合”处理,极大精简了工序;经染色工序上色后在成型过程中染料即完成对料片的固色,无需进行额外的喷涂着色,制得的花瓣颜色鲜艳。
34.3、本技术的无纺布制作工艺的裁切工序、染色工序以及成型工序均可以至少两侧料片层叠进行,大幅提高仿真花制作效率的同时,使得同批次制得的仿真花尺寸均一性更好。
35.4、本技术的优选方案中用特制的料片夹紧固定装置进行染色,可使得花瓣外缘形成由外至内的渐变染色效果,使得能够制作出色彩更佳丰富、逼真的仿真花。
附图说明
36.图1是制备例1中压纹辊的结构示意图一。
37.图2是制备例1中压纹辊的结构示意图二。
38.图3是制备例1中压纹凸块的剖视图。
39.图4是制备例2中压纹辊的结构示意图。
40.图5是制备例3中压纹辊的结构示意图。
41.图6是制备例4中压纹辊的结构示意图。
42.图7是实施例中无纺布仿真花制作工艺的工艺流程图。
43.图8是实施例中料片夹持固定装置的爆炸图。
44.图9是实施例中料片夹持固定装置的剖视图。
45.图10是图9中a部分的放大图。
46.图11是实施例中料片夹持固定装置的使用工况图。
47.附图标记说明:1、无纺布;2、裁切料片;3、上色料片;4、发色料片;5、无纺布仿真花;6、压纹辊;61、压纹凸块;7、料片夹持固定装置;71、定夹板;72、连接杆;721、注液流道;722、注液口;7221、螺纹旋塞;723、出液微孔;73、动夹板;74、锁紧螺帽。
具体实施方式
48.以下结合附图1-10对本技术作进一步详细说明。
49.制备例制备例1-4制备例1-4均涉及一种无纺布制备工艺,工艺步骤如下:步骤一、将纺丝粒子于160-175℃烘干,然后加热至250-270℃使得纺丝粒子熔融,形成纺丝料;纺丝粒子可以选择pet粒子、pp粒子、或者pet粒子与pbt粒子的混合物;步骤二、将纺丝料经喷丝口喷出纺制成粗细度为1~2d的纤维长丝;步骤三、将纤维长丝平铺成网后,用至少一根压纹辊与承压辊配合进行热压定型,得到克重为20~120g/m2的无纺布;压纹辊表面均布有压纹凸块,压纹凸块呈直线条状或弧形条状,横截面呈矩形或者梯形。热压时选择多跟压纹辊与承压辊配合时,优选压纹凸块设置方式不同的压纹辊。
50.制备例1-4的区别在于纺丝粒子的选择、具体工艺参数的选择以及压纹辊的选择不同。
51.制备例1-4纺丝粒子的具体选择如表1所示。
52.表1.制备例原料选择表
制备例制备例1制备例2制备例3制备例4纺丝粒子pet粒子pet粒子+pbt粒子,两者质量比为8:2pp粒子pet粒子
其中,pet粒子,牌号fr943-bk507,纤维级,来自美国杜邦;pp粒子,牌号5d49,纤维级,来自美国杜邦;pbt粒子,牌号xb3036,纤维级来自美国杜邦。在其他制备例中用市售其他纤维级的pet粒子、pp粒子和pbt粒子亦可。
53.制备例1-4各步骤的工艺参数如表2所示。
54.表2.制备例工艺参数表制备例1-4压纹辊的选择各不相同,具体地:参照图1,制备例1使用的压纹辊6表面沿平行压纹辊6轴线方向设置有若干成列的压纹凸块61,各列压纹凸块61沿压纹辊6的周向等间距分布,同列的压纹凸块61等间距分布。
55.参照图2和图3,制备例1中压纹凸块61呈直线条状,横截面形状呈等腰梯形。压纹凸块61的长度记为l,宽度记为b,高度记为h;同列相邻压纹凸块61之间间距记为a,相邻两列压纹凸块61之间间距记为d,其各自取值范围见表3。制备例1中压纹凸块61的长度l,宽度b,高度h;同列相邻压纹凸块61之间间距a,相邻两列压纹凸块61之间间距d具体值见表3。
56.参照图2,制备例2中相邻两列的压纹凸块61位置一一对应,在其他制备例中也可以间错设置。
57.参照图4,制备例2使用的压纹辊6表面同样设有若干列压纹凸块61,每列压纹凸块61均沿压纹辊6的圆周面螺旋分布,且相邻压纹凸块61之间间距相等,相邻两列压纹凸块61之间间距相等。制备例2中压纹凸块61呈弧形条状,压纹凸块61的轴线方向偏离压纹辊6的轴线方向。制备例2中压纹凸块61的长度l(指压纹凸块61顶面两棱边弧长的平均值),宽度b,高度h;同列相邻压纹凸块61之间间距a,相邻两列压纹凸块61之间间距d具体值见表3。
58.参照图5,制备例3使用的压纹辊6与制备例2使用的压纹辊6相似,区别在于制备3中压纹凸块61为与压纹辊6同轴设置的弧形条状。制备例3中压纹凸块61的长度l(指压纹凸块61顶面两棱边弧长的平均值),宽度b,高度h;同列相邻压纹凸块61之间间距a,相邻两列压纹凸块61之间间距d具体值见表3。
59.参照图6,制备例4的压纹辊6与制备例1选用的压纹辊6相似,区别在于相邻两列压纹凸块61之间间错设置。制备例4中压纹凸块61的长度l,宽度b,高度h;同列相邻压纹凸块61之间间距a,相邻两列压纹凸块61之间间距d具体值见表3。
60.表3.压纹凸块参数表项目取值范围制备例1制备例2制备例3制备例4l/mm0.2-0.50.350.50.20.2b/mm0.1~0.250.220.180.250.15h/mm0.2-0.50.50.30.20.5a/mm0.2-0.30.250.30.20.25d/mm0.4~0.650.650.460.420.5实施例
61.实施例1一种无纺布仿真花制作工艺,以制备例1制得的无纺布作为花瓣制作原料,参照图6,具体工艺步骤如下:(1)裁切工序将无纺布裁切成花瓣形状,得裁切料片。为了便于后续借助料片夹紧固定装置,在裁切时同步在裁切料片中央部裁切形成通孔。为了提高裁切效果,裁切时可将2~20片的无纺布层叠后同步裁切,能够一次得到多片花瓣形状的裁切料片。本实施例中裁切时,一次层叠10片无纺布。
62.(2)染色工序参照图7和图8,染色工序需要料片夹紧固定装置完成。料片夹紧固定装置包括圆形的定夹板71、圆形的动夹板73、连接杆72以及锁紧螺帽74。连接杆72一端贯穿定夹板71,且与定夹板71固定连接。动夹板73的圆心处开有供连接杆72插入的通孔。紧螺帽螺纹连接于连接杆72远离定夹板71的末端。使用时,将2-20片裁切料片2层叠后套设于连接杆72,然后在连接杆72上套设动夹板73,再旋紧锁紧螺帽74,使得层叠的裁切料片2被夹紧在定夹板71、动夹板73之间。本实施例中,每次将10片裁切料片2层叠套设于连接杆72。如此,染色时染料能够从裁切料片2的外缘向中心部位渗透,呈现出渐变的上色效果。
63.参照图8和图9,连接杆72内设置有贯通的注液流道721,注液流道721在连接杆72的两端均形成注液口722。连接杆72两端的注液口722处均螺纹连接有螺纹旋塞7221。连接杆72的杆体部分,且位于定夹板71和动夹板73之间的区域,均匀开设有出液微孔723。出液微孔723均与注液流道721连通。将多层裁切料片2夹紧固定后,卸除螺纹旋塞7221,向注液流道721内注入染液,然后旋紧螺纹旋塞7221,如此使得染液可以由内向外逐渐渗透,从裁切料片2中心部位形成由内之外的渐变染色效果。
64.参照图10,最后将夹紧固定裁切料片2整体浸渍于染液,浸渍结束后离心脱液,于100-110℃烘干,得上色料片3。本实施例中染色烘干温度为100℃。
65.染液使用分散染料按照常规分散染料染液配方进行配置即可,本实施例中仅以蓝色分散为例进行说明,在其他实施例中颜色以及浓度根据实际需要进行选择即可。
66.染液配方为:分散蓝2bln
ꢀꢀꢀ
1.5g/l润湿剂jfc
ꢀꢀꢀꢀ
1ml/l扩散剂
ꢀꢀꢀꢀꢀꢀꢀ
1g/l使用时,需要先用醋酸将染液ph值调至5~6。
67.(3)定型工序使用花瓣热压成型模具于180-250℃将上色料片模塑热压成型,此过程中在高温作用下染料进入无纺布纤维内容形成完成固色,得到具有立体花瓣形状和足够颜色牢度的发色料片。本实施例中模塑热压成型温度为220℃。模塑成型时可以同时将2~20片上色料片层叠后进行模塑热压,一次得到多片发色料片,本实施例中每次模塑热压10片上色料片。
68.(4)组装工序用粘合剂将发色料片与花蕊部件、花萼部件和花柄部件粘合固定,得造型逼真、形状稳定持久的无纺布仿真花。制作仿真花所用的花蕊部件、花萼部件和花柄部件采用本领域常规方法制得或通过商业途径购买即可,此处不再赘述。
69.实施例2:一种无纺布仿真花制作工艺,以制备例2制得的无纺布作为花瓣制作原料,与实施例1的区别仅在于:各步骤的工艺参数有区别,具体见表4。
70.实施例3:一种无纺布仿真花制作工艺,以制备例3制得的无纺布作为花瓣制作原料,与实施例1的区别仅在于:各步骤的工艺参数有区别,具体见表4。
71.实施例4:一种无纺布仿真花制作工艺,以实施例1为基础,区别仅在于:以制备例4制得的无纺布作为花瓣制作原料。
72.表4.各实施例工艺参数表对照例1:一种仿真花制作工艺,与实施例1的区别仅在于:以克重为80g/m2的68d/24f fdy全涤半光平纹聚酯机织物作为花瓣制作原料。
73.对照例2:一种仿真花制作工艺,与实施例1的区别仅在于:在无纺布制造的“步骤三”中采用两根光滑的热压辊进行热压定型。
74.性能试验(1)毛边脱开试验分别取实施例1-4和对照例1-2的“成型工序”得到上色料片,层叠15层后在中部缝合固定制成试样料片束。以纺织印染领域常见的三足离心脱水机作为试验设备(内容直径960
㎜
),将10束试样料片束放入三足离心脱水机,开启离心脱水机以1000rpm的转速处理试样料片束10min。结束后观察试样料束状态,并让三位在仿真花成品质检岗位工作满5年的熟练工人进行评分,记录各束试样料片束评分平均值作为试验结果。
75.评分标准如下:无毛边脱开
ꢀꢀꢀꢀꢀꢀꢀ
4~5分毛边轻微松脱
ꢀꢀꢀꢀꢀ
2~3分毛边脱开严重
ꢀꢀꢀꢀꢀ
0~1分试验结果如表5所示。
76.表5.毛边脱开试验结果表
试样料片束实施例1实施例2实施例3实施例4实施例1对照例2毛边脱开性试验得分4.94.84.851.24.1
由表5试验数据可知:按照本技术无纺布仿真花制作工艺制仿真花,不仅无需对花瓣原料进行涂层处理,减少了voc排放,也无需对花瓣边缘进行熔化或熔合处理,精简了工序,得到仿真花不易出现毛边脱开问题。
77.(2)造型稳定性试验分别取实施例1-4和对照例1-2的“成型工序”得到上色料片,层叠15层后在中部缝合固定制成试样料片束,同时拍照记录处理前试样料片束状态。分别取10束试样料片束,于80℃、湿度为90%rh条件下保存7d。结束后观察试样料束状态,并让三位在仿真花成品质检岗位工作满5年的熟练工人将处理后的试样料片束与处理前进行对比并评分,记录各束试样料片束评分平均值作为试验结果。
78.评分标准如下:造型立体无明显变化
ꢀꢀꢀꢀꢀꢀꢀ
4~5分轻微变形
ꢀꢀꢀꢀꢀꢀꢀꢀꢀꢀꢀꢀꢀꢀꢀꢀꢀ
2~3分严重变形
ꢀꢀꢀꢀꢀꢀꢀꢀꢀꢀꢀꢀꢀꢀꢀꢀꢀ
0~1分试验结果如表6所示。
79.表6.毛边脱开试验结果表
试样料片束实施例1实施例2实施例3实施例4对照例1对照例2造型稳定性试验得分4.94.84.84.94.74.3
由表6试验数据可知:按照本技术无纺布仿真花制作工艺制仿真花具有良好的造型稳定性,耐受高温高湿可以保持造型不便,且与对照例相比保持造型的效果更佳,其可能的原因是经过压纹辊热压后在无纺布表面形成特殊的凹凸纹,后续经过染色后烘干、模塑热压使得无纺布的结构更佳牢靠紧密,因而本获得了相较于常规横纵交织机织布更优造型保持效果。
80.(3)不良率检测分别对按照实施例1-4和对照例1-2方法制得的仿真花进行抽检,凡存在不可接受的划伤、色花、色斑、毛边脱开、造型残缺或与设计形状偏差过大等问题的仿真花视为不良品,并记录不良率如表7所示。
81.表7.不良率统计表项目实施例1实施例2实施例3实施例4对照例1对照例2不良率0.1%0.2%0.1%0.08%4.8%1.5%由表7试验数据可知:按照本技术无纺布仿真花制作工艺制作仿真花能够大幅降低仿真花的不良率。
82.以上均为本技术的较佳实施例,并非依此限制本技术的保护范围,故:凡依本技术的结构、形状、原理所做的等效变化,均应涵盖于本技术的保护范围之内。