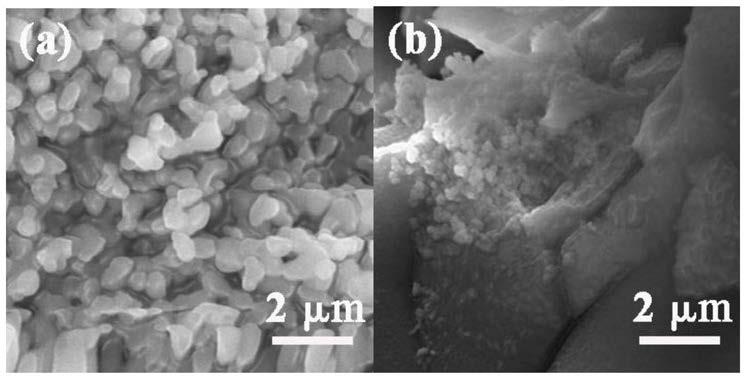
1.本发明涉及环行器复合基板技术领域,特别是一种镁钙钛微波介质陶瓷粉体及其制备方法 和应用。
背景技术:
2.5g基站里的核心器件环行器能够将进入其任一端口的入射波按照由静偏磁场确定的方 向顺序传入下一端口,即一种能够单向传输高频信号能量的非可逆器件。镁钙钛微波介质陶 瓷(称为为mct)材料主要作为外环和旋磁铁氧体匹配共烧,适用于微波频率(300mhz~300 ghz)下的环行器和隔离器,凭借其高稳定性、高介电常数和低损耗等特点,可拓展带宽, 缓解器件互调问题。现有技术的异质共烧复合基板陶瓷和铁氧体交界处有很大缝隙,两相分 离开裂使得器件性能不稳定,大大降低产品的合格率,同时传统固相法中mct陶瓷粉体预 烧温度在1100℃左右,陶瓷的烧结温度在1400℃以上,因而还存在各组分分布不均匀、粉 体预烧温度过高和预烧时间过长造成资源浪费增加碳排放等一系列问题。
3.近年来由于欧美对5g基站电子器件材料的进口限制,急需自主研发的低介电损耗材料替代。因此,制备高性能预烧粉体以及优化环行器复合基板共压成型工艺使陶瓷粉体和铁氧体结合紧密对提高产品性能和生产效率有着重要意义,可以为5g射频基站提供高性能材料核心器件奠定基础,给人民的生活和社会发展带来巨大便利。
技术实现要素:
4.针对现有技术的不足,本发明提出了一种镁钙钛微波介质陶瓷粉体及其制备方法和应用。 通过采用pechini溶胶-凝胶法制备镁钙钛微波介质陶瓷粉体,制备的粉体组分分布均匀、结 晶性良好;将该粉体和铁氧体通过共压和冷等静压二次压制成型制得环行器复合基板,其不 仅降低了粉体煅烧和陶瓷烧结温度,同时极大缩小两相界面的缝隙,实现了mct微波陶瓷 外环和ni-zn铁氧体磁芯紧密结合的目的。
5.本发明是通过以下技术方案来实现的:
6.一种镁钙钛微波介质陶瓷粉体的制备方法,包括如下步骤:
7.s1按照化学式mg
0.95
tio
3-ca
0.05
tio3中金属离子摩尔比称取一水乙酸钙和六水合硝酸镁 并分别溶解于超纯水中,制得乙酸钙溶液和硝酸镁溶液;将钛酸四正丁酯、乙二醇、一水合 柠檬酸和酒精按照质量比为1:3:12:18称量后进行充分混合,制得澄清溶液;
8.s2依次将所述乙酸钙溶液和硝酸镁溶液加入到所述澄清溶液中并充分混合,制得稳定聚 合物前驱体溶胶;
9.s3将所述溶胶依次经第一次干燥、陈化和第二次干燥后制得干凝胶;
10.s4将所述干凝胶经冷冻干燥后制得疏松多孔的焦糖色干凝胶;
11.s5将所述焦糖色干凝胶研磨分散后进行煅烧,制得mg
0.95
tio
3-ca
0.05
tio3纳米粉体,即 镁钙钛微波介质陶瓷粉体。
12.本发明通过pechini溶胶-凝胶法合成的聚合物前驱体溶胶经过陈化烘干和冷冻
干燥等手 段制得高性能mct陶瓷纳米粉体,其中冷冻干燥步骤解决了凝胶排水和有机物小分子造成 网络结构空间体积较大的问题,进而克服了传统固相法各组分分布不均匀的技术难关,制备 的mct陶瓷纳米粉体组分分布均匀、结晶性良好。
13.优选的,所述s3中,第一次干燥温度为80℃,干燥时间为12h;所述s3中,第二次干 燥温度为110℃,干燥时间为6-8h。
14.优选的,所述s3中,陈化温度为常温,陈化时间为12h。
15.优选的,所述s4中,冷冻干燥的温度为-60℃,时间为12h。该温度和时间能进一步促 使mct陶瓷纳米粉体组分分布均匀、结晶性良好。
16.优选的,所述s5的煅烧步骤中,煅烧温度为750℃,保温时间为3h。
17.。煅烧温度过低或时间过短会导致陶瓷粉体结晶性差,组分分布不均匀;煅烧温度过高 和预烧时间过长造成资源浪费增加碳排放等一系列现象。
18.一种镁钙钛微波介质陶瓷粉体的应用,用于环行器复合基板。
19.优选的,所述环行器复合基板由共压成型法制备;
20.所述共压成型法为:将所述镁钙钛微波介质陶瓷粉体和ni-zn铁氧体胚体共压成型,再 烧结制得复合基板。经过共压成型工艺制备的环行器复合基板性能更加稳定,其中的陶瓷外 环和铁氧体此磁芯结合更加紧密,极大程度降低了二相交接处的缝隙。
21.优选的,将镁钙钛微波介质陶瓷粉体和ni-zn铁氧体胚体共压成型后,还需经冷等静压 压制,待二次压制成型后,再烧结制得复合基板。由共压成型和冷等静压二次压制成型工艺 制备的环行器复合基板,相较单独采用共压成型单次压制工艺而言,其性能能实现更优,且 陶瓷外环和铁氧体磁芯两相界面的缝隙能够实现完全消失的目的,体现了本发明工艺具有显 著的进步。
22.优选的,所述环行器复合基板由嵌套成型法制备;
23.所述嵌套成型法为:将所述陶瓷粉体先压制成环,再和ni-zn铁氧体坯体嵌套成型,再 烧结制得复合基板。现有技术常采用固相法制备陶瓷粉体再与铁氧体嵌套成型,制备的环行 器复合基板中两相的交界处缝隙极大,导致环行器复合基板的性能极不稳定;本发明采用 pechini溶胶-凝胶法制备的陶瓷粉体和铁氧体磁芯嵌套成型后,制备的环行器复合基板相较现 有技术,具有极大的进步,二相直接的界面缝隙明显降低,体现pechini溶胶-凝胶法制备陶 瓷粉体工艺的优越性。
24.本发明的有益效果是:
25.1.本发明通过pechini溶胶-凝胶法合成的聚合物前驱体溶胶经过陈化烘干和冷冻干燥等 手段制得高性能mct陶瓷纳米粉体,其中冷冻干燥步骤解决了凝胶排水和有机物小分子造 成网络结构空间体积较大的问题,进而克服了传统固相法各组分分布不均匀、粉体预烧温度 过高和预烧时间过长造成资源浪费增加碳排放等一系列现象。制备的mct陶瓷纳米粉体组 分分布均匀、结晶性良好,粒径尺寸为5.3~21.8μm,粉体粒度分布窄。
26.2.在不改变组分的前提下,采用pechini溶胶-凝胶法制备陶瓷粉体降低了陶瓷粉预烧煅 烧温度(即形成陶瓷体粉体时的煅烧温度),同时极大程度缩小陶瓷粉体和铁氧体粉体两相界 面的缝隙;在共压和冷等静压二次压制成型工艺共同作用下,两相界面处缝隙完全消失,实 现了mct微波陶瓷外环和ni-zn铁氧体磁芯的紧密共烧的目的。
27.3.本发明拓宽了pechini溶胶-凝胶法在工业生产中的涉及领域,改善了异质复合
zn铁 氧体坯体嵌套成型,再在1200℃下烧结,保温5h制得复合基板。
49.实施例4
50.陶瓷粉体制备方法同实施例1;
51.环行器复合基板的制备方法为:先将镁钙钛微波介质陶瓷粉体压制成环,再和ni-zn铁 氧体坯体嵌套成型,其后用冷等静压机在300mpa压力下保压10min使其二次压制成型,再 在1200℃下烧结,保温5h制得复合基板。
52.实施例5
53.仅制备陶瓷粉体,将s13中的第二次干燥时间改为8h,其余步骤同实施例1。
54.实施例6
55.仅制备陶瓷粉体,将s13中的第二次干燥时间改为7h,其余步骤同实施例1。
56.对比例1
57.采用固相法制备陶瓷粉体:
58.s1按照化学式mg
0.95
tio
3-ca
0.05
tio3所示的配比称量氢氧化镁、二氧化钛、氧化钙共计 约60g粉体,加入聚氨酯球磨罐;
59.s2将锆球、原料、超纯水按质量比为5:1:2称量后加入所述球磨罐中,再滴加20滴 聚丙烯酸分散剂,以1500r/min的转速球磨6h,制得初产品;
60.s3将初产品在60℃下烘干24h,研磨过100目筛,再在1120℃下烧结,保温4h后, 制得陶瓷粉体。
61.环行器复合基板的制备:
62.将陶瓷粉体和ni-zn铁氧体胚体(ni-zn铁氧体胚体通过固相法制备,铁氧体胚体为圆柱 体)共压成型后,用冷等静压机在300mpa压力下保压10min使其二次压制成型,再在1200℃ 下烧结,保温5h制得环行器复合基板(陶瓷粉体成型后称为陶瓷外环,铁氧体胚体成型后称 作铁氧体磁芯)。
63.对比例2
64.陶瓷粉体制备方法同对比例1;
65.环行器复合基板的制备方法中不进行二次压制成型,其余步骤同对比例1。
66.对比例3
67.陶瓷粉体制备方法同对比例1;
68.环行器复合基板的制备方法为:先将陶瓷粉体压制成环,再和ni-zn铁氧体坯体嵌套成型, 再在1200℃下烧结,保温5h制得复合基板。
69.对比例4
70.陶瓷粉体制备方法同对比例1;
71.环行器复合基板的制备方法为:先将陶瓷粉体压制成环,再和ni-zn铁氧体坯体嵌套成型, 其后用冷等静压机在300mpa压力下保压10min使其二次压制成型,再在1200℃下烧结, 保温5h制得复合基板。
72.二、实验比较。
73.1.测量实施例1-6和对比例1-4中的陶瓷粉体粒径尺寸,具体数据如表所示:
[0074] 粒径尺寸(μm)实施例15.3
实施例27.6实施例36.9实施例49.3实施例521.8实施例617.3对比例1123.6对比例2183.5对比例3206.9对比例4100.9
[0075]
结论:
[0076]
(1)通过上表可知:实施例1-6中的陶瓷粉体的粒径尺寸集中于5.3~21.8μm,远小于对 比例1-4中通过固定相制备的陶瓷粉体的粒径尺寸,具有显著的进步,体现了本发明中pechini 溶胶-凝胶法的优越性;
[0077]
(2)通过图1和图2可知,用pechini溶胶-凝胶法制备的陶瓷粉体相较固相法制备的陶 瓷粉体,具有高结晶度、窄粒度分布等优异性能;
[0078]
综上,通过pechini溶胶-凝胶法制备的陶瓷粉体均为超细纳米陶瓷粉体,因其具有均一 成分、高结晶度、窄粒度分布等优异特性,当其用于制备环行器复合基板时,能够为降低陶 瓷外环和铁氧体磁芯两相界面缝隙打下坚实的基础。
[0079]
2.比较实施例1-4和对比例1-4中制备的环行器复合基板中的陶瓷体和铁氧体之间的缝 隙。
[0080]
(1)对比例1和对比例2均采用共压的方式制备环行器复合基板,因陶瓷粉体粒径尺寸 大,且分布不均匀等原因,导致制备的环行器复合基板出现大面积碎裂的情况,且陶瓷体和 铁氧体二相之间的缝隙极大,此工艺制备的环形其复合基板中的二相交接处缝隙相较实施例 1-4和对比例3-4均较差;
[0081]
(2)通过图3可知,实施例3中的环行器复合基板的二相交接处缝隙相较对比例3更小, 证明采用pechini溶胶-凝胶法制备的陶瓷粉体运用在环行器复合基板时,对降低两相界面的 缝隙发挥了极为显著的作用;而实施例4中采用二次共压共艺,其制备的环行器复合基板中 的两相界面缝隙相较实施例3更小;
[0082]
(3)通过图4可知,实施例1中采用pechini溶胶-凝胶法制备陶瓷粉体,并将该陶瓷粉 体和铁氧体采用共压成型和冷等静压二次成型的方式制得环行器复合基板,环行器复合基板 中二相界面处缝隙完全消失,此为最优方案,克服了现有技术中二相界面因存在缝隙而导致 环行器复合基板性能不稳定等缺陷;
[0083]
(4)实施例2中的环行器复合基板中二相的缝隙相较对比例3而言更小,其仅次于实施 例2。综上,采用pechini溶胶-凝胶法制备的陶瓷粉体,具有组分分布均匀、结晶性好等特点, 将其运用于环行器复合基板制备时,无论和铁氧体采用嵌套或者共压或者共压和冷等静压结 合的方式,制备的环行器复合基板中的两相交界处的缝隙均得以降低,进而提高环行器复合 基板的性能。
[0084]
以上仅是本发明的优选实施方式,应当理解本发明并非局限于本文所披露的形式,不应看 作是对其他实施例的排除,而可用于各种其他组合、修改和环境,并能够在本文
构想范围内, 通过上述教导或相关领域的技术或知识进行改动。而本领域人员所进行的改动和变化不脱离 本发明的精神和范围,则都应在本发明所附权利要求的保护范围内。