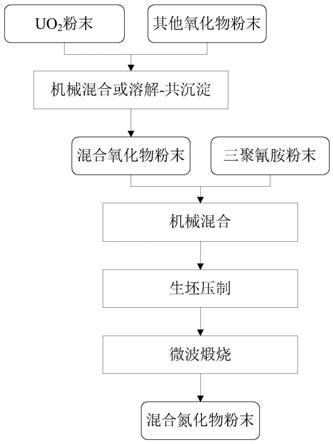
1.本发明属于核能燃料制造领域,涉及一种混合氮化物粉末的制备方法。
背景技术:
2.氮化物燃料是第四代核能系统中金属冷却快堆的重要候选燃料,其具备铀密度高、熔点高、热导率高、辐照稳定性好、裂变气体释放率低等优点。总体来看,氮化物燃料的应用领域非常明确,主要为金属冷却快堆,应用场景包括大型商用快堆、空间堆等,同时氮化物燃料也可用于ads燃料、嬗变燃料等领域。
3.混合氮化物粉末一般通过两种技术路线生产制造,第一种是un直接氮化法,将u、pu、zr等金属制成粉末,在氮气或氨气气氛中反应生成氮化物,该反应过程为放热反应,易造成合成的粉末自发烧结,且由于金属氮化反应温度较低,即使使用u、pu等混合金属氮化,直接获得un、pun等单一氮化物的混合粉末,无法直接获得(u,pu)n混合固溶体粉末,需要通过粉末的固溶处理或调整烧结工艺获得(u,pu)n混合固溶体,而(u,pu)n混合固溶体的形成是混合氮化物燃料的一个重要指标,直接关系到芯块内pu的均匀性,最终影响燃料的堆内安全可靠性。第二种技术路线则是最常见的混合氮化物粉末制备工艺,也就是碳热还原氮化法,将uo2、puo2等氧化物粉末与碳粉混合,在氮气气氛下于1500~1700℃左右反应生成(u,pu)n混合固溶体粉末。
4.由于氮化物结构的特点,两种不同的氮化物互扩散形成混合氮化物固溶体速度较慢,在此过程中消耗能量也较多。从过往研究经验来看,通过碳热还原氮化法一步合成混合氮化物粉末需要较高的温度或较长的反应时间,在高温长时间作用后,粉末杂质含量较低,但粉末颗粒粗,烧结活性低,后续需增加破碎球磨等工序,如合成温度太低,混合氮化物粉末中c、o杂质含量较高。
5.而且为了保证混合氮化物燃料芯块的强度、刚度和结构完整性,一般要求芯块密度至少大于80%td。氮化物是以共价键为主的陶瓷,原子扩散速率非常低,氮化物燃料芯块的烧结难度远大于二氧化铀,且氮化铀烧结温度不宜过高,氮化铀在1900℃以上会迅速分解成液态金属铀,因此烧结温度不宜过高,在1800℃烧结时只有少量氮化铀分解。一方面要求烧结温度不宜过高,另一方面又需要保证芯块密度,如果通过破碎球磨方式细化碳热还原氮化得到的混合氮化物粉末也可能引入杂质,因此开发一种粉末粒度较细,烧结活性高、杂质含量低的混合氮化物粉末制备工艺是最为理想的选择。
技术实现要素:
6.针对现有技术中所存在的缺陷,本发明的目的在于提供一种混合氮化物粉末的制备方法,在较低的温度下反应合成得到单一固溶体相、杂质含量较低的亚微米混合氮化物燃料粉末,该粉末可以直接用于后续的混合氮化物燃料芯块烧结,无需再经破碎球磨等处理,简化现有混合氮化物燃料的生产工艺流程。
7.为实现此目的,本发明提供一种混合氮化物粉末的制备方法,所述制备方法包括
如下步骤:
8.(1)混合氧化物粉末制备:按燃料设计比例称量氧化物粉末,所述氧化物粉末选自uo2粉末、puo2粉末、npo2粉末、amo2粉末、ceo2粉末、zro2粉末中的一种或几种;并将称量的氧化物粉末混合,获得混合氧化物粉末;
9.(2)原料粉末准备:按设计比例称量三聚氰胺粉末,与所述混合氧化物粉末再次混合,混合均匀后得到的原料粉末暂存待用;
10.(3)生坯压制:将原料粉末置于模具中,在压机上压制为生坯,将生坯装入坩埚,放入微波气氛炉内;
11.(4)微波煅烧:将微波气氛炉抽真空后充入氮气,保持微波气氛炉内处于真空状态,开启微波加热,升温至设定的煅烧温度,并在煅烧温度保温设定的煅烧时间后,将反应得到的混合氮化物粉末随炉冷却,开始降温时再次对炉内抽真空并切换炉内气氛,一直维持到冷却过程结束。
12.进一步,所述将称量的氧化物粉末混合的方法为机械混合方法或溶解-共沉淀混合方法。
13.进一步,所述机械混合方法为将所述称量的氧化物粉末装入球磨罐,并球磨罐内放入磨球,再将球磨罐置入行星式球磨机进行球磨混合获得混合氧化物粉末。
14.进一步,所述溶解-共沉淀混合方法为将所述称量的氧化物粉末溶解于硝酸后,再通过共沉淀法获得混合氧化物粉末。
15.进一步,所述三聚氰胺粉末的物质的量为所述混合氧化物粉末总物质的量的4~10倍。
16.进一步,所述再次混合采用机械混合方法,所采用的机械混合设备为三维运动混合机。
17.进一步,开启微波加热之前,所述将微波气氛炉抽真空后充入氮气的操作重复三次以上后,再保持微波气氛炉内处于真空状态。
18.进一步,所述设定的煅烧温度的取值范围为1200~1600℃。
19.进一步,所述设定的煅烧时间的取值范围为0.5~6小时。
20.进一步,所述炉内气氛切换为ar-5h2气氛或h2气氛。
21.本发明的有益效果在于,采用本发明所提供的混合氮化物粉末的制备方法,通过在较低的温度下反应合成得到单一固溶体相、杂质含量较低的亚微米混合氮化物燃料粉末,该粉末能够直接用于后续的混合氮化物燃料芯块烧结,无需再经破碎球磨等处理,简化了现有混合氮化物燃料的生产工艺流程。本发明所提供的混合氮化物粉末的制备方法可用于混合氮化物燃料的生产,通过引入微波煅烧碳热还原工艺,将常规氮化物燃料生产中的碳粉更改为三聚氰胺粉,实现了亚微米混合氮化物燃料粉末的制备。同时,采用本发明所提供的方法制备的混合氮化物粉末具备极高的烧结活性,可以用于高密度氮化物燃料芯块的生产,而且混合氮化物粉末中的主要杂质c、o含量均较低。
附图说明
22.图1为本发明实施方式提供的混合氮化物粉末制备方法流程图。
23.图2为本发明实施例1制备的混合氮化物粉末样品的sem图。
具体实施方式
24.下面结合附图和具体实施方式对本发明作进一步描述。
25.本实施方式中的实施例所选用的实验装置包括:电子天平、行星式球磨机、三维运动混合机、液压机、微波气氛炉、激光粒度衍射仪等;原材料包括uo2、ceo2、zro2、三聚氰胺粉末等。
26.实施例1
27.如图1所示,本发明所提供的一种混合氮化物粉末的制备方法,包括如下步骤:
28.(1)混合氧化物粉末制备:按摩尔比7:3分别称量uo2粉末及ceo2粉末,将两种粉末装入球磨罐,球磨罐内放入磨球,置入行星式球磨机进行球磨混合,获得混合氧化物粉末;
29.(2)原料粉末准备:称取混合氧化物粉末总物质的量5倍的三聚氰胺粉末,与混合氧化物粉末一起装入三维运动混合机再次混合,混合均匀后的原料粉末暂存待用;
30.(3)生坯压制:将原料粉末使用模具在压机上压制为生坯,将生坯装入坩埚,放入微波气氛炉内;
31.(4)微波煅烧:将微波气氛炉抽真空后充入氮气,重复该过程三次后保持微波气氛炉内真空状态;开启微波加热,升温至1500℃,保温2小时后,将反应得到的混合氮化物粉末随炉冷却,开始降温时再次对炉内抽真空,切换炉内气氛为ar-5h2气氛,一直维持到冷却过程结束。
32.使用激光粒度衍射仪测试本实施例制备得到的(u,ce)n混合氮化物粉末中位粒径,中位粒径为0.74μm。
33.由本实施例制备得到的混合氮化物粉末样品的扫描电镜图如图2所示,从图中可以看出,制备得到的亚微米级混合氮化物燃料粉末为单一固溶体相,且主要杂质c、o含量较低。
34.实施例2
35.本发明所提供的一种混合氮化物粉末的制备方法,包括如下步骤:
36.(1)混合氧化物粉末制备:按摩尔比7:3分别称量uo2粉末及zro2粉末,将两种粉末装入球磨罐,球磨罐内放入磨球,置入行星式球磨机进行球磨混合,获得混合氧化物粉末;
37.(2)原料粉末准备:称取混合氧化物粉末总物质的量10倍的三聚氰胺粉末,与混合氧化物粉末一起装入三维运动混合机再次混合,混合均匀后的原料粉末暂存待用;
38.(3)生坯压制:将原料粉末使用模具在压机上压制为生坯,将生坯装入坩埚,放入微波气氛炉内;
39.(4)微波煅烧:将微波气氛炉抽真空后充入氮气,重复该过程三次后保持微波气氛炉内真空状态;开启微波加热,升温至1600℃,保温6小时后,将反应得到的混合氮化物粉末随炉冷却,开始降温时再次对炉内抽真空,切换炉内气氛为h2气氛,一直维持到冷却过程结束。
40.实施例3
41.本发明所提供的一种混合氮化物粉末的制备方法,包括如下步骤:
42.(1)混合氧化物粉末制备:按摩尔比9:1分别称量uo2粉末及zro2粉末,溶解于硝酸后共沉淀,获得混合氧化物粉末;
43.(2)原料粉末准备:称取混合氧化物粉末总物质的量9倍的三聚氰胺粉末,与混合
氧化物粉末一起装入三维运动混合机再次混合,混合均匀后的原料粉末暂存待用;
44.(3)生坯压制:将原料粉末使用模具在压机上压制为生坯,将生坯装入坩埚,放入微波气氛炉内;
45.(4)微波煅烧:将微波气氛炉抽真空后充入氮气,重复该过程三次后保持微波气氛炉内真空状态;开启微波加热,升温至1400℃,保温0.5小时后,将反应得到的混合氮化物粉末随炉冷却,开始降温时再次对炉内抽真空,切换炉内气氛为h2气氛,一直维持到冷却过程结束。
46.上述实施例只是对本发明的举例说明,本领域的技术人员可以对本发明进行各种改动和变型而不脱离本发明的精神和范围。这样,倘若本发明的这些修改和变型属于本发明权利要求及其等同技术的范围之内,则本发明也意图包含这些改动和变型在内。