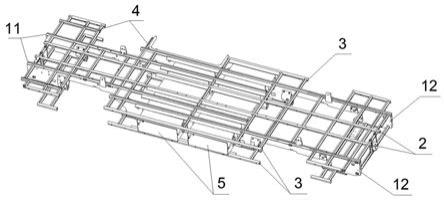
1.本实用新型涉及新能源汽车制造技术领域,具体为一种组合纵梁式一体化铝合金车架。
背景技术:
2.传统商用车钢结构车架一般采用梯形结构,即,车架由两根钢纵梁和一组钢横梁组成,然后用铆接法或者焊接法将纵梁与横梁连接形成坚固的刚性结构。在车架上有一系列的硬点支座,硬点支座通常通过螺栓、铆接或焊接方式固定在车架上。硬点支座是用于将底盘系统的载荷传递到车架上,其中受力最大的是前后板簧硬点支座,由于前后板簧宽度不同,两根钢纵梁在前后部位之间的宽度也不相同,为此,通过弯曲工艺将钢纵梁制造成前后段偏置平行的弯曲形状,装配后,形成前窄后宽的双纵梁梯形结构。钢结构梯形结构车架非常成熟可靠,但是也有一系列缺陷:1)车架的重量偏大;2)车架内部空间利用率不高;3)耐腐蚀能力较差,首先,钢结构自身易锈蚀,其次,在钢铝接触部位易出现电化学腐蚀。
3.在新能源汽车领域,为了大幅减轻整车重量,车架结构(包括硬点支座)的轻量化是重点,这是因为车架重量比车身重量的占比更大;但是,车架的轻量化难度远远高于车身,主要原因是:1)车架是整车的受力基础,对其力学要求高,特别是扭转刚度、弯曲刚度要求高;2)车架上装配各种底盘系统(如前后桥)和设施(如电池包),车架必须为相关系统及设施提供合理的安装空间或工作空间,避免空间干涉或装配困难;3)各类系统在车架上的硬点(固定点)载荷比较大,必须提供牢固、稳定的硬点结构。虽然铝合金是很好的轻量化材料,但是也有明显的短板:1)和钢材相比,铝合金强度较弱;2)难焊,且焊缝将导致材料的强度显著下降;3)“直来直去”,不易弯曲,特别是大型截面型材,很难弯曲。因此,铝合金车架结构与传统钢结构车架必然具有很大的差异性,不是简单的用铝合金替代钢材。鉴于上述原因,全铝合金车架设计属于“无人区”,至今没有铝合金车架的成熟解决方案。
4.查询到关于车辆铝合金车架的公开文献如下:关键词,车架、铝合金
5.1、一种“二纵四横”铝合金车架结构及汽车;申请号:cn201821389751.7;申请人:武汉智能控制工业技术研究院有限公司;华中科技大学;摘要:一种“二纵四横”铝合金车架结构及汽车,属于汽车技术领域。“二纵四横”铝合金车架结构包括两条纵梁和四条组合横臂。两条纵梁左右对称布置。四条组合横臂从前至后依次榫卯连接于纵梁上。汽车包括上述的“二纵四横”铝合金车架结构。这种“二纵四横”铝合金车架结构在实现轻量化的同时,保证了其具有很好的整体刚度和强度,易于制造,还易于铝合金底盘硬点系统的安装。该汽车轻量化程度高。
6.2、一种铝合金汽车底盘硬点系统及汽车;申请号:cn201810985616.7;申请人:武汉智能控制工业技术研究院有限公司;摘要:一种铝合金汽车底盘硬点系统及汽车,属于汽车技术领域。包括车架,前板簧前支座,前板簧后支座,后板簧前支座,后板簧后支座,电机硬点支座,转向硬点支座。车架包括左纵梁、右纵梁、第一组合横臂、第二组合横臂、第三组合横臂和第四组合横臂,四者从前至后依次榫卯连接并固定于左纵梁和右纵梁上。前板簧
前支座连接于第一组合横臂。前板簧后支座连接于第二组合横臂。后板簧前支座连接于第三组合横臂。后板簧后支座连接于第四组合横臂。电机硬点支座固定于左纵梁和右纵梁之间。电机硬点支座固定于左纵梁或右纵梁。这种铝合金汽车底盘硬点系统,在实现轻量化的同时,具有很好的硬点刚度和强度。
7.3、一种采用轻量化客车底盘结构的纯电动汽车底盘系统;申请号:cn201410847147.4;申请人:东莞中山大学研究院; 东莞三新电动汽车技术有限公司;摘要:一种采用轻量化客车底盘结构的纯电动汽车底盘系统,包括两条纵向大梁和若干横梁,若干横梁分布于两条纵向大梁的不同高度层面及不同纵向位置,若干横梁榫接于两条纵向大梁形成整体受力的双纵梁多层底盘架;双纵梁多层底盘架的前部连接有前桥架,前桥架通过两条纵向大梁进行固定;双纵梁多层底盘架的后部连接有后桥架;后桥架通过两条纵向大梁进行固定;前桥架连接有前桥总成,后桥架连接有后桥总成,双纵梁多层底盘架设置有驱动总成和能源总成,纵向大梁的整体结构刚性较好,简化前、后桥架与底盘架的组装工艺,连接牢靠并实现整体受力,多层地板结构设计便于电池、电机的安装,节约底盘空间。
8.4、一种仿蜂窝结构拓扑的轻量化车架;申请号:cn202010828647.9;申请人:华中科技大学; 南宁华数轻量化电动汽车设计院有限公司;摘要:一种仿蜂窝结构拓扑的轻量化车架,其特征在于:包括两根边梁,至少一根纵梁,以及至少两根中横梁;所述纵梁位于两根边梁之间,所述中横梁两端分别与边梁榫接,中部与纵梁榫接;所述边梁、纵梁以及中横梁均包括中部截面呈“工”字型的腹板,以及上下两端截面分别呈矩形的上方管、下方管;边梁、纵梁以及中横梁之间形成能够用于容纳蓄电池的电池舱。本发明采用多舱式蜂窝结构的车架,重量轻且又有相当高的强度和刚度,能够形成既能承载又能减重的双重功能。
9.以上为本技术人进行的前代设计,展示了车架从不完全铝合金轻量化到完全铝合金轻量化的过程。但是,两个“全铝合金车架”仍然存在一些问题:1)由于纵梁均为整体设计,为了适应前后板簧硬点的不同宽度,做了较为复杂的纵梁设计和组合横梁设计,致使车架整体结构较为复杂,装配难度加大,成本较高,不方便后续整车装配(例如申请号cn201821389751.7和申请号cn202010828647.9);2)板簧硬点载荷由组合横臂承担,其效果没有直接由纵梁承担的力学效果好(例如申请号cn201821389751.7和申请号cn202010828647.9);3)电池空间的一体化程度不高,申请号cn201821389751.7的电池包安装在整体大梁的外侧,为了保证电池电量,只能加大电池包的高度,导致电池包突出大梁的上表面,占据了车内乘用空间,破坏了车内地板的平整;申请号cn202010828647.9可存放的电池包数量多,但是每一个电池空间单元较小,导致电池包数目多,装配工艺和接线复杂;4)车架的横向结构偏弱,由于横向结构为一系列的小截面型材,受力能力较弱,导致车架的横向弯曲刚度和扭转刚度偏弱。因此,有必要针对上述不足继续迭代优化。
技术实现要素:
10.本实用新型组合纵梁式一体化铝合金车架,在原有的前代铝合金车架基础上进行优化改进,采用组合纵梁与电池仓穿榫连接,形成主结构拓扑,两根组合纵梁的前纵梁之间的横向距离与后纵梁之间的横向距离不等、并分别与前后板簧宽度适配,车架整体结构刚度高,抗扭强度高,连接形式无需大面积焊接且不易失效开裂,型材截面结构合理易于生产,可以大大降低车架的生产成本,提高生产效率。
11.为达到上述目的,本实用新型的技术方案如下:
12.一种组合纵梁式一体化铝合金车架,车架纵向布置左右两根组合纵梁,其由前纵梁和后纵梁组成,两者横向偏置、并纵向形成一段重叠组合区,车架横向布置若干电池仓,至少一个横向电池仓同时穿榫通过左右两根组合纵梁的重叠组合区,进一步,在电池仓外表面通过法兰边与组合纵梁的侧面连接,车架上部和下部横向布置若干横梁,横梁与组合纵梁的上下腔体穿榫连接,车架纵向布置若干小纵梁,小纵梁与横梁榫卯穿插,小纵梁与电池仓表面接触并连接。
13.纵梁截面为竖直布置的6个腔体型材,此设计易于生产,且具有双腹杆的特性,具有较强的抗弯和抗扭拧效果。前纵梁、后纵梁和电池仓三者之间形成交叉的主结构拓扑,具有很强的结构刚度和抗扭强度,其次,组合后的纵梁,两个后纵梁之间的间距可以在一定范围内调整,极大方便了纵梁上板簧支座等硬点支座的安装位置适应性调整,无需对纵梁进行弯折加工,极大降低了车架的制造成本。组合纵梁与电池仓穿榫边缘处包括水平纵向和竖直两个方向的相交面,均固定角铝型法兰边进行铆接固定,从两个方向与电池仓连接;再加上收边梁与小纵梁相交处的法兰边,承载电池的电池仓具有很好的固定效果,在经受高速惯性的状态下也能保持电池仓不形变不移位。
14.所述车架上表面布置地板蒙皮,蒙皮与接触的纵梁、小纵梁、收边梁、横梁之间通过激光熔透焊接固定,或通过粘接加铆接进行连接固定。
15.所述横梁的两端分别设置收边梁,收边梁与横梁的端部榫卯连接。收边梁型材截面为方管,收边梁外侧通过螺栓连接侧围边梁。
16.所述小纵梁及收边梁与电池仓的表面均设置法兰边进行连接固定。
17.所述电池仓由两部分槽型板组合而成,两个槽型板连接部位设置工字连接件进行连接。此种双板拼接结构可以实现大截面的腔体成型,而不需要大吨位的挤压机生产,降低生产成本。
18.所述组合纵梁和横梁型材截面穿榫相交处均设计插槽,插槽处设置三角片固定连接。
19.所述前纵梁和后纵梁的重叠组合区设置水平连接插板,连接插板两侧边沿部分别与前纵梁和后纵梁的侧面插槽固定连接。前纵梁与后纵梁主要通过横梁的连接作用固定定位,在此基础上,前纵梁和后纵梁之间增设连接插板,进一步增加两者的连接节点,在实际生产中,前纵梁和后纵梁定尺长度生产完成后,先采用连接插板将两者固定定位,构成组合式纵梁,然后再将组合式纵梁与横梁、电池隧道腔等进行连接。
20.本发明的优点:
21.本实用新型通过将整体式纵梁分解成前后偏置重叠的两端纵梁,在重叠组合区与电池仓结构榫卯连接,再通过“法兰边粘接+铆接”进行固定,进一步,将地板蒙皮与所接触的车架上的各类纵梁、横梁、边梁之间通过激光熔透焊接、或粘接加铆接进行连接固定,获得“榫卯腔梁”式车架结构,带来了一系列的优点:
22.1、由于纵梁和电池舱的截面尺寸大、截面惯性矩大,因此,由“大梁+大腔”组成的车架主结构提供了强大的结构基础,进一步通过各种小梁与主结构之间的连接、以及地板蒙皮与车架结构的连接耦合,最终获得了高力学性能的全铝合金轻量化车架结构。计算与测试结果表明,该车架的扭转刚度超过30000牛米/度,已高于同类钢车架的扭转刚度。
23.2、组合纵梁的前后段之间的间距可以灵活调整,提供了与前后板簧支座宽度的适配灵活性,车架的应用广泛。
24.3、组合纵梁避免了对整体纵梁进行弯折加工,同时,车架结构在装配时只需要进行简单的榫卯穿插及固定,车架的制造工艺简单、制造成本显著降低。
25.4、电池舱即是车架的主拓扑结构、又是电池包的安装空间,实现了车架空间的充分利用,便于电池包的安装。
26.5、各类硬点结构可直接装配到车架大梁上,承载能力强,装配性好,工艺成本低。
27.6、采用该“榫卯腔梁”全轻量化车架的轻量化汽车实现了整车减重30%以上的轻量化效果。
28.附图说明:
29.图1为本实用新型外观结构图;
30.图2为本实用新型俯视结构图;
31.图3为图2中b-b断面结构图;
32.图4为图3中ⅲ处的放大结构图;
33.图5为图2中c-c断面结构图;
34.图6为本实用新型俯视状态下半剖结构图;
35.图7为图6中ⅰ处放大结构图;
36.图8为组合纵梁、横梁和电池仓位置关系结构图;
37.图9为图8中ⅱ处的放大结构图;
38.图10为组合纵梁型材截面图;
39.图11为实施例3的组合纵梁型材截面图;
40.图12为三角片位置结构图;
41.图13为实施例2组合纵梁外形结构图;
42.图中标号名称为:1、组合纵梁;11、前纵梁;12、后纵梁;13、连接插板;2、小纵梁;3、收边梁;4、横梁;5、电池仓;51、工字连接件;6、法兰边;7、三角片。
具体实施方式
43.实施例1
44.一种组合纵梁式一体化铝合金车架,车架纵向布置左右两根组合纵梁1,其由前纵梁11和后纵梁12组成,两者横向偏置、并纵向形成一段重叠组合区,车架横向布置若干电池仓5,至少一个横向电池仓5同时穿榫通过左右两根组合纵梁1的重叠组合区,进一步,在电池仓5外表面通过法兰边6与组合纵梁1的侧面连接,车架上部和下部横向布置若干横梁4,横梁4与组合纵梁1的上下腔体穿榫连接,车架纵向布置若干小纵梁2,小纵梁2与横梁4榫卯穿插,小纵梁2与电池仓5表面接触并连接。
45.所述车架上表面布置地板蒙皮,蒙皮与接触的纵梁1、小纵梁2、收边梁3、横梁4之间通过激光熔透焊接固定,或通过粘接加铆接进行连接固定。
46.所述横梁4的两端分别设置收边梁3,收边梁3与横梁4的端部榫卯连接。
47.所述小纵梁2及收边梁3与电池仓5的表面均设置法兰边6进行连接固定。
48.所述电池仓5由两部分槽型板组合而成,两个槽型板连接部位设置工字连接件51
进行连接。
49.所述组合纵梁1和横梁4型材截面穿榫相交处均设计插槽,插槽处设置三角片7固定连接。
50.所述组合纵梁1型材截面的腔体中,长腔体的两侧设置若干加强肋。
51.所述前纵梁1和后纵梁12的重叠组合区设置水平连接插板13,连接插板13两侧边沿部分别与前纵梁11和后纵梁12的侧面插槽固定连接。
52.实施例2
53.与实施例1不同之处在于:所述前纵梁11和后纵梁12通过连接插板13连接,前纵梁1和后纵梁2的交叠连接部位设置连接插板13,连接插板13两侧面端部分别与前纵梁11和后纵梁12的侧面插槽固定连接。即取消每一支大纵梁1中前纵梁1和后纵梁12之间的法兰边,纵梁1和后纵梁2之间设置连接插板13直接相连的部分;
54.一个横向电池仓5穿榫通过两根组合纵梁1的重叠组合区。
55.实施例3
56.与实施例1不同之处在于:所述组合纵梁1型材截面的腔体中,长腔体的两侧设置若干加强肋。
57.应用实施例:
58.本实用新型实施例1铝型材采用均使用6005a-t6材料进行加工制造,车架总长为5800mm,总宽度1830mm;车架总重量为320kg;
59.对比例为背景文件中的文件1中的“二纵四横”铝合金车架结构,对比例车架结构尺寸与发明实施例1车架外形尺寸相同;
60.得到以下比较数据:
[0061][0062]
以上扭转刚度实验过程遵循《普通乘用车白车身扭转刚度试验方法》2020年征求意见稿中的实验方法:
[0063]
满足 jb/t 7974-1999 的要求的测试装置,白车身与模拟悬架之间采用球铰接,车身底部共左右对称设置20个测点,最大加载载荷取整车最大加载载荷的四分之一;
[0064]
顺指针加载至最大载荷
‑‑‑‑
卸载
‑‑‑‑
逆时针加载至最大载荷
‑‑‑‑
卸载
‑‑‑‑
静置消除弹性变形
‑‑‑‑
顺时针加载至最大载荷30%
‑‑‑‑
卸载
‑‑‑‑
逆时针加载至最大载荷30%
‑‑‑‑
卸载
‑‑‑‑‑
静置消除弹性变形
‑‑‑‑
顺时针分级加载
‑‑‑‑
卸载消除弹性变形
‑‑‑‑
逆时针加载至最大载荷30%
‑‑‑‑
卸载
‑‑‑‑‑
逆时针分级加载
‑‑‑‑
卸载消除弹性变形
‑‑‑‑
重复若干次步骤6-16,至少2次。
[0065]
计算公式:扭转刚度=车身所承受载荷/前后悬架横截面上的扭转角之差的绝对值
[0066]
由上述可见,与对比例相比,本实用新型车架的抗扭拧能力得到大幅度的提高,在总重量和总造价方面也有不小的降低。