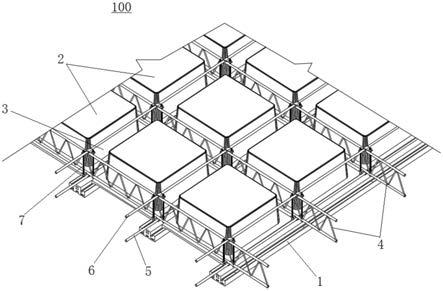
一种轻型预置装配式空间网架密肋楼板模板
【技术领域】
1.本实用新型属于楼板支模技术领域,特别是涉及一种轻型预置装配式空间网架密肋楼板模板。
背景技术:
2.现有市场上的密肋楼板、空心楼板、现浇梁板楼板,都是在支撑架上,搭设主龙骨,再在主龙骨上根据楼板空间尺寸搭设需要的方木次龙骨,把模板铺设在方木上,然后人工在模板上放轴线和肋梁尺寸线,再把填充箱或一次性模壳按施工图放置在模板上,最大的缺点就是填充箱或一次性模壳属于永久性预埋,无法重复利用,增加了相应成本,或可重复使用的模壳须按传统的方木及模板搭设完成后,现场高空作业放线,然后放置模壳在相应楼板位置才能使用,并没有减少方木次龙骨的用量,模板的用量也没有减少或减少的有限,同时增加了高空放肋梁线的工作量,无准确定位的人工放置填充箱或模壳造成箱子或模壳易移位,这样就产生了肋梁不在同一条线上或肋梁的宽度不均等衍生问题,既不方便又增加作业安全风险,也不符合装配式产业政策,同时模壳移位造成肋宽不均又会增加相应的质量安全隐患。
3.因此,有必要提供一种新的轻型预置装配式空间网架密肋楼板模板来解决上述技术问题。
技术实现要素:
4.本实用新型的主要目的在于提供一种轻型预置装配式空间网架密肋楼板模板,减少方木次龙骨、模板、填充箱或一次性模壳的投入和浪费,提高肋梁宽度的尺寸精度,提升支模铺设模壳的施工效率,符合绿色节能建筑要求。
5.本实用新型通过如下技术方案实现上述目的:一种轻型预置装配式空间网架密肋楼板模板,其包括平行间隔设置的若干金属龙骨、两边搭设在相邻两根所述金属龙骨上的若干模壳,相邻两根所述金属龙骨之间的同一列模壳无间隙挨个设置,所有的所述模壳与所述金属龙骨之间围绕形成纵横交错的肋梁槽,同一行所述肋梁槽中设置有与所述金属龙骨垂直分布的桁架单元,同一列所述肋梁槽中设置有与所述金属龙骨平行分布的下纵筋与上纵筋,所述金属龙骨上锁紧有桁架连接件,所述桁架单元、所述下纵筋与所述上纵筋整体构成钢筋网架且通过所述桁架连接件可拆卸的锁紧在所述金属龙骨上。
6.进一步的,所述金属龙骨为铝合金型材结构,所述模壳为铝合金壳体结构或塑料壳体结构。
7.进一步的,所述金属龙骨的顶部设置有龙骨顶面、位于所述龙骨顶面两侧的模板模壳支撑面、设置在所述龙骨顶面与所述模板模壳支撑面之间的且向下凹陷形成的模壳定位卡槽。
8.进一步的,所述模壳包括搭设在所述模板模壳支撑面上的底板、自所述底板表面向上隆起的且内部中空的壳体、自所述底板两边向下延伸形成与所述模壳定位卡槽配合的
模壳卡条。
9.进一步的,所述底板的上表面形成有围绕所述壳体分布的模壳基准面;所述模壳基准面与所述龙骨顶面齐平设置。
10.进一步的,所述金属龙骨的内部设置有通长的减重抽空腔。
11.进一步的,所述桁架单元为平面桁架结构或立体桁架结构,且包括上主筋与下主筋;所述桁架单元位于所述下纵筋与所述上纵筋之间。
12.进一步的,所述桁架连接件设置在所述金属龙骨上且位于所述肋梁槽纵横交汇位置。
13.进一步的,所述龙骨顶面上设置有若干螺栓孔,所述螺栓孔贯穿所述金属龙骨上下表面;
14.所述桁架连接件包括穿过所述螺栓孔的至少一对连接螺杆、上下位置可调的设置在所述连接螺杆上的支撑底套、两边套设在所述一对连接螺杆上且受所述支撑底套支撑的下托板、两边套设在所述一对连接螺杆上且压住所述上纵筋的上压板、以及在所述连接螺杆上锁紧所述上压板的螺母。
15.与现有技术相比,本实用新型一种轻型预置装配式空间网架密肋楼板模板的有益效果在于:采用自重轻强度高的铝合金或塑胶材质制作的可周转模壳和带卡槽的金属龙骨现场快速拼装组合,构成免支模、免放线、定位准的模壳密肋楼板模板,接着制作纵横交错的肋梁钢筋及板分布钢筋,然后浇筑混凝土后成型密肋楼板;本施工工艺大大减少了大量方木及模板材料的投入,拼装简单、模板组装快速、用工量少、低损耗、材料全周转无建筑垃圾,大大降低了装配式楼板的综合造价,提高了肋梁宽度的尺寸精度,同时在平整场地上进行快速拼装,提升支模铺设模壳的施工效率和人员操作的灵活便捷性及人员安全性,符合绿色节能建筑。
【附图说明】
16.图1为本实用新型实施例的局部结构示意图;
17.图2为本实用新型实施例中金属龙骨的结构示意图;
18.图3为本实用新型实施例中模壳的结构示意图;
19.图4为本实用新型实施例中模壳的剖视结构示意图;
20.图5为本实用新型实施例中金属龙骨与模壳组装的结构示意图;
21.图6为本实用新型实施例中桁架连接件的结构示意图;
22.图7为本实用新型实施例中桁架连接件的另一结构示意图;
23.图8为本实用新型实施例中桁架连接件与桁架单元、下纵筋、上纵筋的连接结构示意图;
24.图9为本实用新型实施例中桁架连接件与桁架单元、下纵筋、上纵筋的另一连接结构示意图;
25.图10为本实用新型实施例的局部放大结构示意图;
26.图11为本实用新型实施例的整体结构示意图;
27.图中数字表示:
28.1金属龙骨,11t型螺栓槽,12龙骨顶面,121螺栓孔,13模板模壳支撑面,131模壳定
位线,14模壳定位卡槽,15减重抽空腔。
29.2模壳,21底板,211模壳基准面,212第二减重槽,22壳体,221腔体,222气孔,223斜面结构,224加强肋,23模壳卡条,231第一减重槽;
30.3肋梁槽;
31.4桁架单元,41平面桁架结构,411第一下主筋,412第一上主筋,413第一连接筋,42立体桁架结构,421第二下主筋,422第三下主筋,423第二上主筋,424第二连接筋,425第三连接筋;
32.5下纵筋;6上纵筋;
33.7桁架连接件,71连接螺杆,711下段,712上段,72支撑底套,73下托板,731第一限位凹槽,732第二限位凹槽,733第一平面结构,74上压板,741第三限位凹槽,742第四限位凹槽,743第二平面结构,75螺母。
【具体实施方式】
34.实施例:
35.请参照图1-图11,本实施例一种轻型预置装配式空间网架密肋楼板模板100,其包括平行间隔设置的若干金属龙骨1、两边搭设在相邻两根金属龙骨1上的若干模壳2,相邻两根金属龙骨1之间的同一列模壳2无间隙挨个设置,所有的模壳2与金属龙骨1之间围绕形成纵横交错的肋梁槽3,同一行肋梁槽3中设置有与金属龙骨1垂直分布的桁架单元4,同一列肋梁槽3中设置有与金属龙骨1平行分布的下纵筋5与上纵筋6,金属龙骨1上锁紧有桁架连接件7,桁架单元4、下纵筋5与上纵筋6整体通过桁架连接件7可拆卸的锁紧在金属龙骨1上。
36.金属龙骨1为铝合金型材结构。金属龙骨1的底部为平面结构且开设有至少两条通长的t型螺栓槽11,其顶部设置有龙骨顶面12、位于龙骨顶面12两侧的且与龙骨顶面12存在高度差的模板模壳支撑面13、设置在龙骨顶面12与模板模壳支撑面13之间的且向下凹陷形成的模壳定位卡槽14。t型螺栓槽11可用于预设螺栓头,用于与其他结构件连接。本实施例中t型螺栓槽11设置有三条。
37.金属龙骨1的内部设置有通长的减重抽空腔15,有助于减轻龙骨整体的重量,便于运输和搬运。金属龙骨1的底部设置为平面结构,有助于实现水平定位。
38.金属龙骨1的长度可与设计的楼板长度相同,或可根据设计的楼板长度由若干段拼接而成。
39.为了提高模板模壳的装配效率和便捷度,本实施例中模板模壳支撑面13上设置有若干模壳定位线131。通过模壳定位线131沿其长度方向上将金属龙骨1划分为模板安装区域与模壳安装区域。模壳定位线131一方面可以对边缘模板3的装配位置进行快速的定位,另一方面也可以对模壳2的装配位置进行快速定位。模壳定位线131之间的距离可根据模板和模壳的宽度进行灵活设置。
40.龙骨顶面12与模板模壳支撑面13之间的高度差与边缘模板3、模壳2对应部位的厚度对应一致,从而使得边缘模板3和模壳2在装配到金属龙骨1上后,其表面平齐形成一个水平基准面。
41.模壳2整体为铝合金结构或塑胶材质结构。模壳2包括底板21、自底板21表面向上隆起的且内部中空的壳体22,底板21的上表面形成有围绕壳体22分布的模壳基准面211,底
板21的相对两侧边缘向下延伸设置有与模壳定位卡槽14配合的模壳卡条23。模壳基准面211与龙骨顶面12齐平设置。
42.在装配模壳2时,模壳2的两边搭设在模板模壳支撑面13上,且模壳2两边的模壳卡条23卡入到模壳定位卡槽14内,与两侧的金属龙骨1形成一个整体,且一端靠着模壳定位线131放置,相邻两个模壳2无间隙挨个设置,平铺满相邻两根金属龙骨1之间的空间,其中,模壳2的模壳基准面211两边可与龙骨顶面12无缝拼接,形成水平基准面。为了能够让模壳2上的模壳卡条23快速卡入模壳定位卡槽14内。
43.底板21的厚度为5~50mm,和金属龙骨1中模板模壳支撑面13与龙骨顶面12之间的高度差对应相等,以使得模壳2搭设在金属龙骨1上后其模壳基准面211与龙骨顶面12表面平齐。
44.模壳卡条23向下凸出模壳底部支撑面212的高度为5~50mm,模壳卡条23的宽度与模壳定位卡槽14配合,其宽度为5~50mm。
45.壳体22的顶面为平面结构且顶面上设置有与内部腔体221连通的气孔222。壳体22的四个外周面为斜面结构223。壳体22的整体高度为50~800mm。通过气孔222与斜面结构223的设计,更加利于模壳2的脱模。壳体22的内壁厚度为1~5mm。壳体22的内壁表面均匀设置有若干加强肋224。
46.为了减轻模壳2整体的重量,模壳卡条23上设置有第一减重槽231。第一减重槽231可以为模壳卡条23的内部通槽结构,也可以自模壳卡条23的下表面向上凹陷形成的凹槽结构。底板21上设置有若干第二减重槽212。第二减重槽212可以为底板21内部的通槽结构,也可以自底板21下表面向上凹陷形成的凹槽结构。
47.底板21的前后端面为平面结构或为前后可配合形成无间隙对接结构的端面结构。以使得多个模壳2装配在金属龙骨1上后,前后可紧挨设置,大大提高了模壳的装配效率与装配便捷度。
48.桁架单元4为平面桁架结构41或立体桁架结构42。所述平面桁架结构41包括第一下主筋411、位于第一下主筋411上方的第一上主筋412、连接第一上主筋412与第一下主筋411的第一连接筋413。第一连接筋413整体呈波浪形,且在波峰波谷处与对应的第一上主筋412或第一下主筋411焊接在一起。所述立体桁架结构42包括位于同一平面且平行设置的第二下主筋421与第三下主筋422、与第二下主筋421和第三下主筋422构成三角结构的第二上主筋423、连接第二下主筋421与第二上主筋423的第二连接筋424、以及连接第三下主筋433与第二上主筋423的第三连接筋425。第二连接筋424与第三连接筋425整体呈波浪形,且在波峰波谷处与对应的第二上主筋423或与第二下主筋421或第三下主筋422焊接在一起。
49.桁架单元4位于下纵筋5与上纵筋6之间。
50.龙骨顶面12上还设置有若干用于固定桁架连接件7的螺栓孔121,螺栓孔121贯穿金属龙骨1上下表面。
51.桁架连接件7设置在金属龙骨1上且位于肋梁槽3纵横交错位置。
52.桁架连接件7包括穿过金属龙骨1的至少一对连接螺杆71、上下位置可调的设置在连接螺杆71上的支撑底套72、两边套设在一对连接螺杆71上且受支撑底套72支撑的下托板73、两边套设在一对连接螺杆71上且压住上纵筋6的上压板74、以及在连接螺杆71上锁紧上压板74的螺母75。
53.连接螺杆71的头部抵持在金属龙骨1的下表面,实现限位,连接螺杆71的螺杆部穿过金属龙骨1中的螺栓孔121并向上延伸至上纵筋6上方。支撑底套72螺纹配合设置在连接螺杆71上,支撑底套72与连接螺杆71的头部分别位于金属龙骨1的上表面、下表面,两者相互配合将连接螺杆71锁紧在金属龙骨1上。支撑底套72还用于支撑定位下托板73的作用,以此限定下纵筋5的高度。
54.在另一实施例中,连接螺杆71可采用两段式结构,其包括下段711与上段712,下段711的长度与金属龙骨1的厚度配合,支撑底套72通过螺纹配合拧紧在下段711顶部。支撑底套72可固定设置在上段712的底部,或通过螺纹配合,将上段712拧入支撑底套72的螺纹孔中实现连接。
55.下托板73上设置有第一限位凹槽731、与第一限位凹槽731垂直的第二限位凹槽732,所述第一限位凹槽731两侧为第一平面结构733,第一平面结构733上设置有通孔,用于穿过连接螺杆71。下纵筋5架设在所述第一限位凹槽731中,桁架单元4中的下主筋放置在第二限位凹槽732中,且下纵筋5在下,桁架单元4中的下主筋在上,通过下托板73支托住下纵筋5与桁架单元4。
56.上压板74上设置有第三限位凹槽741、与第三限位凹槽741垂直的第四限位凹槽742,第三限位凹槽741两侧为第二平面结构743,第二平面结构743上设置有通孔,用于穿过连接螺杆71。上纵筋6卡设在第三限位凹槽741中,桁架单元4中的上主筋卡设在第四限位凹槽742中,且桁架单元4中的上主筋在下,上纵筋6在上,通过上压板74向下压住上纵筋6与桁架单元4,再通过螺母75将上压板74向下锁紧。
57.桁架连接件7根据需求可设置为两根连接螺杆71,或四根连接螺杆71。
58.本实施例一种轻型预置装配式空间网架密肋楼板模板的施工工艺的施工步骤如下:
59.1)在金属龙骨1上安装连接螺杆71与下托板73:将连接螺杆71从金属龙骨1的下方穿入螺栓孔121,然后将支撑底套72拧入贴紧金属龙骨1的龙骨顶面12,再将下托板73的两边套在连接螺杆71上,并向下移动放置到支撑底套72上;
60.2)将上述装有连接螺杆71和下托板73的金属龙骨1按照设定的间距平行摆放;
61.3)在相邻两根金属龙骨1之间摆放满模壳2,模壳2两边搭设在模板模壳支撑面13上,且两边的模壳卡条23卡入模壳定位卡槽14内,实现定位,模壳2的前后端与模壳定位线131对应并齐;同一列的模壳2无间隙挨个设置,同一行的模壳2对应对齐设置,保持纵横肋梁槽3的间距对应一致;此时,模壳2与金属龙骨1围绕形成纵横交错的肋梁槽3,连接螺杆71位于肋梁槽3中纵横交汇处;
62.4)在下托板73上放置与金属龙骨1平行的下纵筋5;下纵筋5放置在下托板73的第一限位凹槽731中;
63.5)在下托板73上下纵筋5的上面放置与金属龙骨1垂直的桁架单元4;桁架单元4中的下主筋放置在下托板73的第二限位凹槽732中;
64.6)在桁架单元4的上面放置与桁架单元4垂直的上纵筋6;
65.7)在连接螺杆7上安装上压板74,其中上压板74中的第三限位凹槽741卡在上纵筋6的上面,第四限位凹槽742卡在桁架单元4的上主筋上,然后用螺母75将上压板74锁紧,从而将下纵筋5、桁架单元4与上纵筋6组成的钢筋网架结构锁紧在金属龙骨1上,形成密肋楼
板模板,待吊装至主龙骨上,进行下一步工序。
66.本实施例一种轻型预置装配式空间网架密肋楼板模板,具有自重轻、承载力高、重复次数多、拼装快速简单、定位精准、无损耗、平地作业、安全性高、肋梁钢筋与模板构成组合空间网架等优点,节省大量的人工、材料投入,降低装配式楼板的综合造价,符合绿色节能建筑。
67.本实施例一种轻型预置装配式空间网架密肋楼板模板100,采用自重轻强度高的铝合金或塑胶材质制作的可周转模壳、带卡槽的金属龙骨、连接件、桁架(平面桁架/立体桁架)、下纵筋和上纵筋在现场平地上快速拼装组合,构成免支模、免放线、定位准、强度高的空间网架密肋楼板模板,后根据需要吊装至相应楼板位置。本方案轻型装配式空间网架模板与其它填充箱或模壳模板相比,具有以下特点:
68.1)模壳采用铝合金或塑胶结构,可重复使用;
69.2)模壳与龙骨组合形成快速免支模板、免放线的支模技术方案;
70.3)模壳设计有卡条,卡条宽度与龙骨卡槽相匹配,能快速精准的安装模壳,避免模壳移位造成的施工质量隐患;
71.4)模壳的基准面至支撑面的高度与配套使用的模板厚度、龙骨顶面至龙骨支撑面的高度相等,在相应构件的尺寸设计上达到装配组合后的龙骨顶面、模壳基准面、模板上表面在同一平面内,其误差控制在5mm以内;
72.5)龙骨同侧模壳之间紧靠放置,无须增加方木构件,降低施工难度,提高施工效率;
73.6)龙骨为金属材质,提升龙骨的耐用性和周转次数,提高龙骨的承载力;
74.7)龙骨支撑面与顶面设计有高度差,方便模壳或模板的快速放置无须调节高度,达到其上表面在同一平面上;
75.8)龙骨设计有定位卡槽,方便模壳的快速扣合,即保证了模壳的定位,又保证了肋间距;
76.9)龙骨、模壳的快速组合一次性完成,免去了支模板、放线和放置模壳等一系列繁琐工作,提升施工效率,提高施工质量;
77.10)龙骨模壳组合可周转模板,大量减少方木龙骨、木模板的使用量,最大程度降低木材投入和施工损耗;
78.11)通过桁架连接件把肋梁的钢筋或部分钢筋与金属龙骨固定在一起,形成双向受力的空间网架;
79.12)所有模板构件在平整场地上可一次性组装完成,免除了高空作业,施工效率高、安全性高,可大大缩短施工工期;
80.13)肋梁钢筋(桁架/纵筋)已提前装配进模板中,减少了后期的肋梁钢筋工作量;
81.14)桁架单元具有较高的稳定性,提升了楼板的整体性能;
82.15)桁架连接件属于一次性构件,埋入了成型后的密肋楼板中,连接件螺杆的螺孔可以很好的用于后期走管或吊顶的连接孔,减少后期钻孔对楼板造成的损伤。
83.以上所述的仅是本实用新型的一些实施方式。对于本领域的普通技术人员来说,在不脱离本实用新型创造构思的前提下,还可以做出若干变形和改进,这些都属于本实用新型的保护范围。