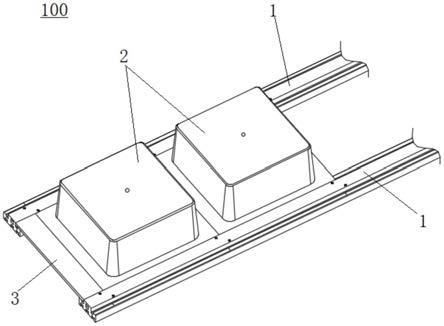
一种快拼式龙骨模壳组合模板
【技术领域】
1.本实用新型属于楼板支模技术领域,特别是涉及一种快拼式龙骨模壳组合模板。
背景技术:
2.现有市场上的密肋楼板、空心楼板、现浇梁板楼板,都是在支撑架上,搭设主龙骨,再在主龙骨上根据楼板空间尺寸搭设需要的方木次龙骨,把模板铺设在方木上,然后人工放轴线和肋梁尺寸线,再把填充箱或一次性模壳按施工图放置在模板上,最大的缺点就是填充箱或一次性模壳属于永久性预埋,无法重复利用,增加了相应成本,或可重复使用的模壳须按传统的方木及模板搭设完成后,现场高空作业放线,然后放置模壳在相应楼板位置才能使用,并没有减少方木次龙骨的用量,模板的用量也没有减少或减少的有限,同时增加了高空放肋梁线的工作量,无准确定位的人工放置填充箱或模壳造成箱子或模壳易移位,这样就产生了肋梁不在同一条线上或肋梁的宽度不均等衍生问题,既不方便又增加作业安全风险,也不符合装配式产业政策,同时模壳移位造成肋宽不均又会增加相应的质量安全隐患。
3.因此,有必要提供一种新的快拼式龙骨模壳组合模板来解决上述技术问题。
技术实现要素:
4.本实用新型的主要目的在于提供一种快拼式龙骨模壳组合模板,替换现有密肋楼板或空心楼板体系中的支模方案,减少方木次龙骨、模板、填充箱或一次性模壳的投入和浪费,提高肋梁宽度的尺寸精度,提升支模铺设模壳的施工效率,符合绿色节能建筑要求。
5.本实用新型通过如下技术方案实现上述目的:一种快拼式龙骨模壳组合模板,其包括若干金属龙骨与若干模壳,所述金属龙骨平行间隔设置形成龙骨支撑面结构,相邻两根所述金属龙骨之间铺设有所述模壳,所述金属龙骨的顶部设置有龙骨顶面、位于所述龙骨顶面两侧的模板模壳支撑面、设置在所述龙骨顶面与所述模板模壳支撑面之间的且向下凹陷形成的模壳定位卡槽,所述模壳的两边搭设在所述模板模壳支撑面上且向下延伸形成有与所述模壳定位卡槽配合的模壳卡条。
6.进一步的,位于相同两根所述金属龙骨之间的所述模壳无间隙挨个设置。
7.进一步的,所有的所述模壳与所述金属龙骨共同形成一楼板模板结构;所述楼板模板结构的外周一圈设置有若干封堵边缘的边缘模板,所述边缘模板与所述龙骨顶面平齐设置。
8.进一步的,所述金属龙骨为铝合金型材结构,所述模壳为铝合金结构或塑胶结构。
9.进一步的,所述金属龙骨的底部为平面结构且开设有至少两条通长的t型螺栓槽。
10.进一步的,所述金属龙骨沿长度方向上为多段拼接结构,且相邻两根所述金属龙骨通过拼接固定件和固定螺栓连接在一起,所述固定螺栓的头部嵌设在所述t型螺栓槽内。
11.进一步的,所述拼接固定件包括与所述金属龙骨宽度匹配的第一底板、自所述第一底板两侧向上延伸形成的且卡住所述金属龙骨两侧表面的定位板。
12.进一步的,所述模壳包括第二底板、自所述第二底板表面向上隆起的且内部中空的壳体,所述模壳卡条设置在所述第二底板的相对两边下方;所述底板的上表面形成有围绕所述壳体分布的模壳基准面;所述模壳基准面与所述龙骨顶面齐平设置。
13.进一步的,所述第二底板的下表面形成有与所述模板模壳支撑面配合形成支撑结构的模壳底部支撑面。
14.进一步的,所述壳体的顶面为平面结构且顶面上设置有与内部腔体连通的气孔。
15.与现有技术相比,本实用新型一种快拼式龙骨模壳组合模板的有益效果在于:采用自重轻强度高的铝合金或塑胶材质制作的可周转模壳和带卡槽的金属龙骨现场快速拼装组合,构成免支模、免放线、定位准的模壳密肋楼板模板,具有自重轻、承载力高、重复次数多、拼装快速简单、定位精准、无损耗等优点,节省大量的人工、材料投入,降低装配式楼板的综合造价,符合绿色节能建筑。
【附图说明】
16.图1为本实用新型实施例的结构示意图;
17.图2为本实用新型实施例中金属龙骨的结构示意图;
18.图3为本实用新型实施例中金属龙骨拼接的结构示意图;
19.图4为本实用新型实施例中模壳的结构示意图;
20.图5为本实用新型实施例中模壳的前视结构示意图;
21.图6为本实用新型实施例中模壳的前视剖面结构示意图;
22.图7为本实用新型实施例中模壳与金属龙骨的装配结构示意图;
23.图8为本实用新型实施例的铺设状态结构示意图;
24.图中数字表示:
25.100快拼式龙骨模壳组合模板;
26.101钢管支撑架;102水平主龙骨;
27.1金属龙骨,11t型螺栓槽,12龙骨顶面,121螺栓孔,13模板模壳支撑面,131模壳定位线,14模壳定位卡槽,141装配导入面,15减重抽空腔,16拼接固定件,161第一底板,162定位板;17固定螺栓。
28.2模壳,21第二底板,211模壳基准面,212模壳底部支撑面,213第二减重槽,22壳体,221腔体,222气孔,223斜面结构,224加强肋,23模壳卡条,231装配导入斜面结构,232第一减重槽;
29.3边缘模板。
【具体实施方式】
30.实施例:
31.请参照图1-图8,本实施例一种快拼式龙骨模壳组合模板100,其包括平行间隔设置的若干金属龙骨1、搭设在相邻两根金属龙骨1之间的若干模壳2,位于相同两根金属龙骨1之间的模壳2无间隙挨个设置,所有的模壳2与金属龙骨1共同形成一楼板模板结构。
32.所述楼板模板结构的外周一圈设置有若干封堵边缘的边缘模板3。
33.本实施例中,金属龙骨1为铝合金型材结构。金属龙骨1的底部为平面结构且开设
有至少两条通长的t型螺栓槽11,其顶部设置有龙骨顶面12、位于龙骨顶面12两侧的且与龙骨顶面12存在高度差的模板模壳支撑面13、设置在龙骨顶面12与模板模壳支撑面13之间的且向下凹陷形成的模壳定位卡槽14。
34.金属龙骨1的内部位于龙骨顶面12的下方设置有通长的减重抽空腔15,有助于减轻龙骨整体的重量,便于运输和搬运。金属龙骨1的底部设置为平面结构,有助于实现水平定位。本实施例中t型螺栓槽11设置有三条。
35.金属龙骨1的长度可与设计的楼板长度相同,或可根据设计的楼板长度由若干段拼接而成。
36.本实施例中,同一直线上的相邻两根金属龙骨1通过拼接固定件16连接在一起。在装配楼板制作时,本实施例金属龙骨1预先被截成设定长度的一段一段的结构,在现场装配时,两个金属龙骨1端面相对,再通过拼接固定件16和固定螺栓17锁紧在t型螺栓槽11即可实现两个金属龙骨1的连接,从而实现各种长度的应用。本实施例中,拼接固定件16包括与金属龙骨1宽度匹配的第一底板161、自第一底板161两侧向上延伸形成的且卡住金属龙骨1两侧表面的定位板162。第一底板161上开设有若干与t型螺栓槽11对应的连接孔(图中未标识)。固定螺栓17的头部从金属龙骨1的一端滑入t型螺栓槽11内,然后将拼接固定件16卡包住相邻两个拼接的龙骨a与龙骨b,并将固定螺栓17的螺杆穿过所述连接孔,然后再用螺母将拼接固定件16与龙骨a、龙骨b一一锁紧,实现拼接。
37.为了提高模板模壳的装配效率和便捷度,本实施例中模板模壳支撑面13上设置有若干模壳定位线131。通过模壳定位线131沿其长度方向上将金属龙骨1划分为模板安装区域与模壳安装区域。模壳定位线131一方面可以对边缘模板3的装配位置进行快速的定位,另一方面也可以对模壳2的装配位置进行快速定位。模壳定位线131之间的距离可根据模板和模壳的宽度进行灵活设置。
38.龙骨顶面12上还设置有若干用于装配连接螺杆的螺栓孔121,连接螺杆用于固定上层钢筋结构。螺栓孔121贯穿金属龙骨1上下表面。
39.龙骨顶面12与模板模壳支撑面13之间的高度差与边缘模板3、模壳2对应部位的厚度对应一致,从而使得边缘模板3和模壳2在装配到金属龙骨1上后,其表面平齐形成一个水平基准面。
40.模壳2包括第二底板21、自第二底板21表面向上隆起的且内部中空的壳体22,第二底板21的上表面形成有围绕壳体22分布的模壳基准面211,第二底板21的相对两侧边缘向下延伸设置有与模壳定位卡槽14配合的模壳卡条23。
41.模壳基准面211与龙骨顶面12齐平设置。
42.在装配模壳2时,模壳2的两边搭设在模板模壳支撑面13上,且模壳2两边的模壳卡条23卡入到模壳定位卡槽14内,与两侧的金属龙骨1形成一个整体,且一端靠着模壳定位线131放置,相邻两个模壳2无间隙挨个设置,平铺设相邻两根金属龙骨1之间的空间,其中,模壳2的模壳基准面211两边可与龙骨顶面12无缝拼接,形成水平基准面。为了能够让模壳2上的模壳卡条23快速卡入模壳定位卡槽14内,本实施例中模壳定位卡槽14的上部还设置有装配导入用的装配导入面141。装配导入面141为一斜面倒角结构。
43.第二底板21的下表面形成有与金属龙骨1上的模板模壳支撑面13配合形成支撑结构的模壳底部支撑面212,模壳基准面211与模壳底部支撑面212之间的厚度为5~50mm,和
金属龙骨1中模板模壳支撑面13与龙骨顶面12之间的高度差对应相等。
44.模壳卡条23向下凸出模壳底部支撑面212的高度为5~50mm,模壳卡条23的宽度与模壳定位卡槽14配合,其宽度为5~50mm。模壳卡条23的底部两侧设置有斜面倒角,形成与装配导入面141配合实现模壳卡条23快速导入的装配导入斜面结构31。
45.多个模壳2装配在一起时,壳体22的外周表面与模壳基准面211共同围绕形成肋梁成型腔。壳体22的顶面为平面结构且顶面上设置有与内部腔体221连通的气孔222。壳体22的四个外周面为斜面结构223。壳体22的整体高度为50~800mm。通过气孔222与斜面结构223的设计,更加利于模壳2的脱模。
46.壳体22的内壁厚度为1~5mm。壳体22的内壁表面均匀设置有若干加强肋224。
47.为了减轻模壳2整体的重量,模壳卡条23上设置有第一减重槽232。第一减重槽232可以为模壳卡条23的内部通槽结构,也可以自模壳卡条23的下表面向上凹陷形成的凹槽结构。第二底板21上设置有若干第二减重槽213。第二减重槽213可以为第二底板21内部的通槽结构,也可以自第二底板21下表面向上凹陷形成的凹槽结构。
48.第二底板21的前后端面为平面结构或为前后可配合形成无间隙对接结构的端面结构。以使得多个模壳2装配在金属龙骨1上后,前后可紧挨设置,大大提高了模壳的装配效率与装配便捷度。
49.模壳2整体为铝合金结构或塑胶材质结构。
50.所述楼板模板结构在垂直于金属龙骨1的两个边缘部位,每两根金属龙骨1之间设置有一个边缘模板3,边缘模板3的两端搭设在金属龙骨1中的模板模壳支撑面13上,且边缘模板3的上表面与龙骨顶面12、模壳基准面211平齐。所述楼板模板结构在平行于金属龙骨1的两个边缘部位,采用通长的边缘模板3,其一边搭设在模板模壳支撑面13上,另一边搭设在主龙骨上或设置在主龙骨上的方木龙骨或垫块上。
51.本实施例一种快拼式龙骨模壳组合模板100的组装步骤为:
52.1)搭设钢管支撑架101;
53.2)在钢管支撑架顶端层铺设水平主龙骨102;
54.3)在水平主龙骨102上按照设定间隔距离铺设金属龙骨1形成次龙骨层,金属龙骨1与水平主龙骨102垂直设置;
55.4)在次龙骨层上搭设模壳2:每相邻两根金属龙骨1之间铺设满模壳2,模壳2的两边搭设在模板模壳支撑面13上,模壳2下方两边的模壳卡条23卡入在金属龙骨1的模壳定位卡槽14内,同一列的相邻两个模壳2靠拢设置,同一行的模壳2对齐设置,保持纵横肋间距相等;
56.5)所有的模壳2铺设完成后,再在外周边缘铺设边缘模板3,形成快拼式龙骨模壳组合模板结构。
57.本实施例一种快拼式龙骨模壳组合模板100替换现有密肋楼板或空心楼板体系中的支模方案,减少方木次龙骨、模板、填充箱或一次性模壳的投入和浪费,提高肋梁宽度的尺寸精度,提升支模铺设模壳的施工效率,符合绿色节能建筑要求。
58.本实施例一种快拼式龙骨模壳组合模板100,采用自重轻强度高的铝合金或塑胶材质制作的可周转模壳和带卡槽的金属龙骨现场快速拼装组合,构成免支模、免放线、定位准的模壳密肋楼板模板,具有自重轻、承载力高、重复次数多、拼装快速简单、定位精准、无
损耗等优点,节省大量的人工、材料投入,降低装配式楼板的综合造价,符合绿色节能建筑。具体的,
59.1)模壳可重复使用,且脱模方便;
60.2)模壳与龙骨组合形成快速免支模板、免放线的支模技术;
61.3)模壳设计有卡条,卡条宽度与龙骨卡槽相匹配,能快速精准的安装模壳,避免模壳移位造成的施工质量隐患;
62.4)模壳的基准面至龙骨支撑面的高度与配套使用的模板厚度、龙骨顶面至龙骨支撑面的高度相等,在相应构件的尺寸设计上达到装配组合后的龙骨顶面、模壳基准面、模板上表面在同一平面内,其误差控制在5mm以内;
63.5)龙骨同侧的模壳之间紧靠放置,无须增加方木构件,降低施工难度,提高施工效率;
64.6)龙骨为金属材质,提升龙骨的耐用性和周转次数,提高龙骨的承载力;
65.7)龙骨支撑面与顶面设计有高度差,方便模壳或模板的快速放置无须调节高度,达到其上表面在同一平面上;
66.8)龙骨设计有定位卡槽,方便模壳的快速扣合,即保证了模壳的定位,又保证了肋间距;
67.9)龙骨、模壳的快速组合一次性完成,免去了支模板、放线和放置模壳等一系列繁琐工作,提升施工效率,提高施工质量;
68.10)龙骨模壳组合可周转模板,大量减少方木龙骨、木模板的使用量,最大程度降低木材投入和施工损耗。
69.以上所述的仅是本实用新型的一些实施方式。对于本领域的普通技术人员来说,在不脱离本实用新型创造构思的前提下,还可以做出若干变形和改进,这些都属于本实用新型的保护范围。