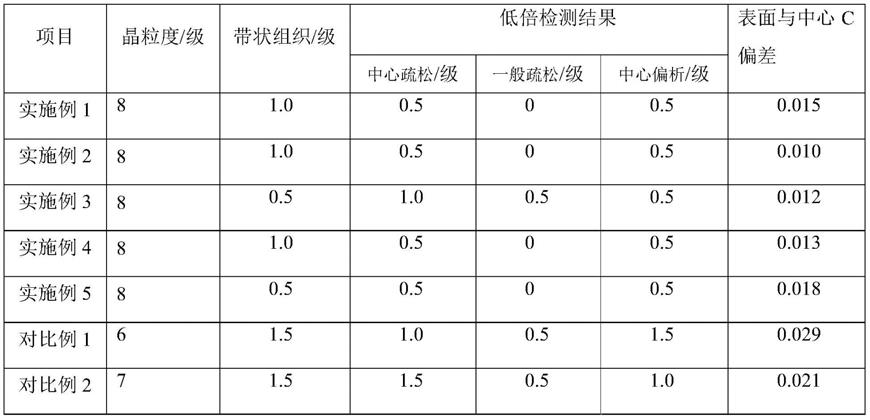
1.本发明属于冶金领域,具体涉及一种传动轴用非调质钢及其锻件的制备方法。
背景技术:
2.非调质钢是在中碳锰钢的基础上加入钒、钛、铌微合金化元素,使其在加热过程中溶于奥氏体中,因奥氏体中的钒、钛、铌的固溶度随着冷却而减小。微合金元素钒、钛、铌将以细小的碳化物的氮化物形式在先析出的铁素体和珠光体中析出。这些析出物与母相保持共格关系,使钢强化。这类钢在热轧状态、锻造状态或正火状态的力学性能既缩短了生产周期,又节省了能源。
3.非调质钢的力学性能取决于基体显微组织和析出相的强化。非调质钢分为热锻用非调质钢、直接切削用非调质钢、冷作强化非调质钢和高韧性非调质钢。热锻用非调质钢用于热锻件(如传动轴、曲轴、连杆等),直接切削用非调质钢用热轧件直接加工成零件,冷作强化非调质钢用于标准件(如螺母等),高韧性非调质钢用于要求韧性较高的零部件,非调质钢具有以下优点:
4.(1)与调质的42crmo、40cr、45相比,机械性能更好,从心部到边缘的硬度更均匀,疲劳寿命更长。
5.(2)大幅降低制造成本:无需调质处理及相关的矫直、运输。
6.(3)直接进入机加工工序,制造周期更短。
7.(4)非调质钢为设备小型化或达到更高性能提供更大的设计空间。
8.(5)非调质钢有利于降低碳排放。
9.汽车传动轴用非调质钢,对其产品的加工性能、疲劳性能及质量的稳定性要求极为严格;此外作为含硫含铝钢,生产过程的稳定控制难度较大。如何克服上述困难,成为行业的一大难点。
技术实现要素:
10.本发明的目的是提供汽车传动轴用非调质钢及其锻件的制备方法,采用本发明方法可以获得均匀致密的材料组织,提高材料的综合性能,同时大量简化了生产工艺,提高了生产效率。
11.本发明的目的是通过以下技术方案来实现的:
12.传动轴用非调质钢,按重量百分比其元素组成为:c 0.39~0.46%、si 0.20~0.45%、mn 1.20~1.60%、cr≤0.25%、v 0.060~0.120%、p≤0.030%、s 0.030~0.070%、ni≤0.25%、mo≤0.25%、cu≤0.20%,余量是fe和不可避免的杂质。
13.优选的,传动轴用非调质钢按重量百分比其元素组成为:c 0.40~0.45%、si 0.25~0.35%、mn 1.30~1.40%、cr 0.10~0.20%、v 0.070~0.100%、al0.012~0.025%、p≤0.020%、s 0.040~0.055%、mo≤0.15%、cu≤0.15%、ni≤0.25%、nb 0.015~0.035%,n 100~140ppm,余量是fe和不可避免的杂质。
14.传动轴用非调质钢的制备方法,工艺包括冶炼、连铸、轧制工序,其工艺流程具体步骤如下:
15.(1)电炉冶炼
16.100吨电炉冶炼,为保证出钢量稳定,严格控制每炉的入炉钢铁料重量:88
±
2.0吨铁水及20
±
1.5吨自产废钢(轧钢返废及连铸切头切尾料)。控制电炉终点放钢:c≥0.10%、p≤0.015%。留钢流渣操作,偏心底出钢,同时稳定控制出钢量100
±
1.0吨,杜绝出钢过程下渣。出钢过程不使用含铝材料,加入碳化硅120千克/炉进行钢水前期脱氧,造渣材料石灰600千克/炉加护炉剂200千克/炉。
17.(2)lf炉精炼
18.为提高s元素收得率,lf精炼造低碱度渣,过程不得补加石灰等渣料,控制lf炉终渣二元碱度1.8~2.5,lf精炼过程使用碳粉50~80千克、碳化硅100~150千克进行钢水的扩散脱氧及炉渣的维护工作,精炼过程不使用含铝脱氧材料进行脱氧。
19.精炼过程元素调整确保成分稳定,确保主要元素成分波动范围:c
±
0.01%,mn、cr
±
0.02%,si
±
0.03%,精炼过程加硫铁来对s含量进行调整,控制出lf硫含量0.050~0.060%,精炼出钢前喂入铝线进行铝含量调整,控制出lf铝含量0.040~0.055%。
20.(3)vd真空处理
21.要求极限真空度保持时间10~15分钟,vd工序不得进行元素成分的调整,vd结束后钢水软吹15~35分钟。
22.(4)连铸
23.控制连浇炉数5~8炉;控制钢水过热度,开浇炉≤30℃、连浇炉≤28℃;采用恒定低拉速浇注,控制拉速0.80
±
0.02m/min;含硫钢属于裂纹敏感性钢种,连铸二冷采用弱冷,控制比水0.25l/kg。为减轻成分偏析等问题,采用首末端电磁搅拌,并加强电磁搅拌强度,其中,结晶器电磁搅拌强度选用:电流300
±
5a,频率2
±
0.2hz;末端电磁搅拌电流350
±
5a,频率6
±
0.2hz,进行留钢操作,留钢量3
±
1吨,要求铸坯进缓冷坑温度≥450℃,缓冷36小时后出坑。
24.(5)轧制
25.为解决偏析,带状组织等问题,轧制过程采用高温扩散加热工艺,具体参数为:控制均热段加热温度1190~1230℃,且高温的均热段加热时间不得少于120min,轧后得到φ80mm的圆钢,并采用避风堆冷的冷却方式。
26.本发明利用上述非调质钢制造传动轴锻件的方法,包括锻造、冷却,步骤如下:
27.该锻造工艺用“高温加热+摊开散冷”代替传统的“非高温加热+吹风强冷”工艺。
28.(1)φ80mm规格圆钢下料后采用感应加热方式,加热温度1270
±
20℃,然后锻造成传动轴毛坯。
29.(2)与传统的非调质钢锻后冷却采用风冷工艺不同,本发明的非调质钢制锻件采用摊开散冷,且内外组织更均匀致密。
30.本发明的有益效果是:
31.①
、电炉严格控制入炉钢铁料数量,并严格控制出钢量,为后续精炼过程实现窄成分控制打下基础。
32.②
、造低碱度渣,从而提高硫的收得率,防止因碱度过高带来的脱硫,从而造成硫
含量控制困难并带来大幅度波动。
33.③
、精炼末期再加铝,一方面在炉渣脱氧充分的条件下加铝可以提高铝的收得率,此外使得钢水中能保留有一定的细小弥散的三氧化二铝夹杂,在连铸凝固过程中,这些三氧化二铝夹杂能成为mns的凝固核心,从而提高纺垂体状硫化物比例,改善材料的切削性能。
34.④
、连铸过程,采用低过热度浇注,并加大电磁搅拌力度,打碎枝晶,减轻材料偏析。
35.⑤
、轧制过程采用高温扩散加热工艺,并制定了适合该钢种的高温加热工艺参数,有利于均匀材料组织。
36.⑥
、锻造过程采用“高温加热+锻件摊开散冷”代替传统非调质钢“非高温加热+吹风强冷”工艺从而获得了材料内外均匀一致的组织。
具体实施方式
37.实施例1
38.以f42mnvs(c 0.42%、si 0.29%、mn 1.33%、cr 0.15%、v 0.085%、al 0.018%、p 0.013%、s 0.047%、mo 0.001%、cu 0.04%、ni 0.002%、nb 0.026%,n 123ppm)的生产为例说明:
39.采用“100吨电炉冶炼-lf精炼-vd真空处理-220mm
×
260mm断面连铸机拉浇-轧制-锻造-冷却”的工艺路线来进行生产,其生产控制方法如下:
40.电炉工艺
41.高炉铁水87.8吨+21.1吨连铸切头切尾废钢,电炉终点c≥0.12%,终点p≤0.013%,出钢量100.3吨。出钢加入造渣材料,600千克石灰与200千克护炉剂造渣。同时加入120千克碳化硅对钢水进行预脱氧。
42.lf炉精炼工艺
43.lf精炼造低碱度渣,过程不得补加石灰等渣料,控制lf炉终渣二元碱度2.2,精炼过程采用碳粉和碳化硅进行脱氧,不使用含铝材料脱氧,精炼过程加硫铁来对s含量进行调整,控制出lf硫含量0.050~0.060%,精炼出钢前喂入铝线进行铝含量调整,控制出lf铝含量0.040~0.055%。
44.通过稳定控制钢水量,同时通过加强造渣和炉渣脱氧,从而控制合金元素的收得率,确保主要元素成分波动范围:c
±
0.01%,mn、cr
±
0.02%,si
±
0.03%。
45.vd真空处理工艺
46.极限真空度保持时间10分钟,vd破空后迅速加入覆盖剂碳化稻壳对钢水进行保护,不进行任何成分调整,同时钢水软吹20分钟。
47.连铸工艺
48.控制拉速0.80m/min,控制钢水浇注过热度25℃,二冷段比水量设置0.25l/kg,结晶器,电磁搅拌电流设置300a,末端电磁搅拌电流设置350a,实现留钢操作,留钢量3-4吨。
49.轧制工艺
50.轧制过程加热工艺为:控制均热段加热温度1200~1230℃,高温的均热段加热时间不少于125min,轧后避风堆冷。
51.锻件工艺
52.锻造加热温度:1260~1280℃,锻后将锻件摊开散冷。
53.实施例2
54.电炉工艺:高炉铁水89.1吨,废钢20.5吨,出钢量100.8吨。
55.lf炉精炼工艺:lf炉终渣二元碱度2.3。
56.vd真空处理工艺:极限真空度保持时间11分钟,同时钢水软吹29分钟。
57.连铸工艺:钢水浇注过热度23℃。
58.其它同实施例1。
59.实施例3
60.电炉工艺:高炉铁水87.9吨,废钢19.8吨,出钢量99.4吨。
61.lf炉精炼工艺:lf炉终渣二元碱度2.0。
62.vd真空处理工艺:极限真空度保持时间13分钟,同时钢水软吹26分钟。
63.连铸工艺:钢水浇注过热度20℃。
64.其它同实施例1。
65.实施例4
66.电炉工艺:高炉铁水87.4吨,废钢21吨,出钢量100.6吨。
67.lf炉精炼工艺:lf炉终渣二元碱度1.9。
68.vd真空处理工艺:极限真空度保持时间12分钟,同时钢水软吹30分钟。
69.连铸工艺:钢水浇注过热度27℃。
70.其它同实施例1。
71.实施例5
72.电炉工艺:高炉铁水88.1吨,废钢19.8吨,出钢量99.8吨。
73.lf炉精炼工艺:lf炉终渣二元碱度2.4。
74.vd真空处理工艺:极限真空度保持时间15分钟,同时钢水软吹21分钟。
75.连铸工艺:钢水浇注过热度24℃。
76.其它同实施例1
77.按照上述工艺各冶炼1炉钢,共计5炉钢,并对应轧制成五个批次φ80mm规格圆钢。
78.对比例1
79.对比例1与实施例1相比,主要区别在于:没有严格控制钢水量,每炉钢水量波动3-吨,同时弱化造渣和炉渣脱氧(将精炼过程的脱氧材料碳粉和碳化硅的用量减少20%),从而合金元素收得率不稳定,主要元素成分波动范围c
±
0.02%,mn、cr
±
0.04%,si
±
0.05%,其它操作同实施例。
80.对比例2
81.对比例2与实施例1相比,主要区别在于:lf炉精炼补加石灰等渣料,终渣二元碱度4.2,其它操作同实施例。
82.对比例3
83.对比例3与实施例1相比,主要区别在于:连铸工艺参数不同,将末端搅拌电流降低为150a,连铸拉速提高至0.90m/min,其它操作同实施例。
84.对比例4
85.对比例4与实施例1相比,主要区别在于:轧制工艺不同,将铸坯在均热段加热温度降至1160~1180℃,均热段加热时间缩短至100min,其它操作同实施例。
86.对比例5
87.锻造加热温度:1180~1200℃,锻后将锻件吹风冷却。
88.(1)化学成份如下表1(wt%):
89.表1
90.项目c%si%mn%p%s%v%cr%cu%al%nb%n(ppm)实施例10.420.291.350.0120.0480.0890.180.0360.0230.025134实施例20.420.281.370.0110.0480.0890.170.0260.0170.027118实施例30.430.281.340.0120.0490.0850.170.0240.0200.027121实施例40.430.281.350.0100.0470.0850.170.0240.0150.026124实施例50.430.291.350.0130.0500.0890.1800.0220.0160.026120对比例10.400.311.400.0150.0520.0780.140.0420.0120.030110对比例20.430.271.300.0150.0430.0800.170.0360.0120.015124对比例30.430.391.380.0130.0520.0860.180.0270.0250.019110对比例40.420.401.310.0120.0440.0900.160.0370.0220.025105对比例50.430.351.350.0130.0430.0790.160.0320.0240.022107
91.(2)金相组织及低倍检测情况如下表2:
92.表2
[0093][0094][0095]
(3)热轧态力学性能如下表3:
[0096]
表3(轧制后的圆钢φ80mm)
[0097][0098]
结果表明:通过对化学成分的优化调整,尤其是v、nb、n等微量元素含量的调整,使得材料晶粒更细化;此外通过连铸拉速、过热度、电磁搅拌参数、高温扩散加热工艺及锻造工艺参数的优化,材料的成分偏析、组织均匀性得到了有效改进,从而稳定提高了材料的综合力学性能。
[0099]
本发明中所用原料、设备,若无特别说明,均为本领域的常用原料、设备;本发明中所用方法,若无特别说明,均为本领域的常规方法。以上所述仅为本发明的较好实施方式,并不用以限制本发明,凡是依据本发明的技术实质对以上实施例作的修改,均包含在本发明的保护范围之内。