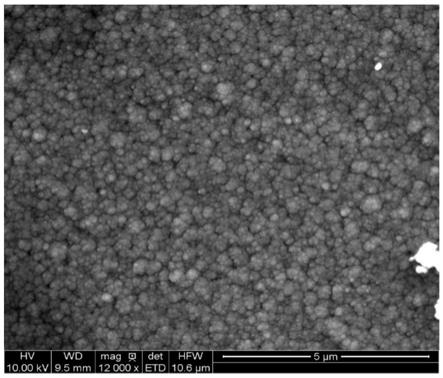
一种ti-al-c max相涂层及其低温成相制备方法
技术领域
1.本发明涉及表面处理技术领域,具体涉及ti3alc
2 max相涂层的低温成相制备方法。
背景技术:
2.max相材料是一大类热力学稳定、具有密排六方结构的层状高性能陶瓷金属材料,通式为m
n+1
axn,其中m位为过渡金属元素,包括ti、cr等,a位通常为元素周期表中第三主族或第四主族元素,如al、si等,x位元素为c或n,可以理解为由单层a原子分割的金属碳化物或金属氮化物纳米层状化合物。一般来说,m-x以强的共价键和离子键结合,而m-a依靠相对较弱的金属键结合。这种独特的层状结构和成键方式,使max相兼具金属和陶瓷的优异性能,如优异的机械稳定性、高硬度,热震耐受好,强的耐蚀性和高温抗氧化性,良好的电导率和热导率,以及自愈合特性和可加工性等。
3.在通式m
n+1
axn中,n值表示max相晶体结构中每两层a原子之间m原子的层数为n+1,目前大多数已知的max相材料n值主要有1、2、3,根据n值的不同将max相分为211,312,413相。典型的含al的max相材料通过形成保护性al2o3层而表现出显著的抗高温氧化和抗腐蚀性能,最具代表的ti-al-c体系和cr-al-c体系中又以ti-al-c化合物与al2o3的热膨胀系数相近成为不锈钢、钛合金、镍基高温合金等基体的合适防护涂层。
4.但是max相材料因较长的c轴和复杂的晶体结构,在合成过程中需要较长的扩散系数来分配元素,导致max相的合成制备是强烈依赖于温度的,且较低的温度无法满足合成条件,尤其是更高阶的312相与413相,较211相性能提升的同时,也需要更高的合成温度。ti-al-c体系中ti3alc2常见的块体制备方法,像热压法、等离子体烧结法等,合成的温度都在1200℃以上,而涂层薄膜系统,由于较短的扩散长度,合成的温度虽然能够有所降低,但是以目前制备max相涂层的主要技术pvd中的磁控溅射和阴极电弧镀来说,合成温度也在800~1000℃范围内。
5.max相高的制备温度限制了其在温度敏感基体上的应用,如何降低max相的制备温度,尤其是更高阶312相的合成,能够扩大其应用范围,也是目前max相材料的瓶颈之一。
技术实现要素:
6.本发明提供一种ti-al-c max相涂层的低温成相制备方法,该方法能够在较低温度下制备ti3alc
2 max相涂层。
7.一种ti3alc
2 max相涂层的低温成相制备方法,包括:
8.(1)以ti-al复合靶为溅射靶材,碳氢气体为反应气源,采用高功率脉冲磁控溅射技术,以500-1000hz的频率,5-10%的占空比,100-200μs的短脉冲对基体表面溅射得到tial
x-c涂层;
9.(2)热处理所述的tial
x-c涂层得到ti3alc
2 max相涂层,所述的热处理温度为600-700℃。
10.本发明通过调控上述的高功率脉冲磁控溅射(hipims)技术的参数,使得hipims提供足够的能量在tial
x-c涂层中形成ti-c晶格,然后通过较低的600-700℃热处理温度,使得tial
x-c涂层中的al离子扩散至ti-c晶格中形成ti3alc
2 max相涂层,从而在较低温度下就能够得到ti3alc2max相涂层,与现有技术中需要在900℃以上才能形成完整的ti3alc
2 312相与413相max相涂层相比,本发明的热处理温度较低。
11.步骤(1)中:
12.所述的ti-al复合靶的ti-al元素比为2:1.2~1.5。
13.所述的碳氢气体的流量为5~10sccm。进一步的,所述碳氢气体为甲烷或乙炔。
14.在所述的对基体表面溅射得到tial
x-c涂层之前,对基体进行等离子体辉光刻蚀处理。使得基体表面较为清洁。
15.进一步的,所述的等离子体为氩气,氮气中的任意一种。
16.进一步的,所述的等离子体辉光刻蚀参数为:等离子体流量为30~35sccm,离子源电压为1000~1200v,基体施加偏压-250~-150v,刻蚀时间为20~40min。
17.在所述的对基体进行等离子体辉光刻蚀处理之后,关闭所述的反应源,开起所述的ti-al复合靶,在所述的基体表面溅射一层过渡层。
18.进一步的,所述的过渡层为tial间化合物。
19.所述的溅射参数为:溅射功率1800~2400w,基体偏压为-100~0v。
20.在所述的基体表面溅射一层过渡层之前,通入保护性气体,所述的保护性气体的流量为150~250sccm,腔体气压为0.6~1.2pa。
21.为避免基体层与tial
x-c涂层中的元素互相扩散,使最终得到的ti3alc
2 max相涂层中存在其他的纳米晶颗粒,从而影响ti3alc
2 max相涂层的纯度,并且增加过渡层能够使得涂层与基体之间的热膨胀系数得以过度匹配从而使tial
x-c涂层的结合力增加。
22.步骤(2)中,所述的热处理时间为60~180min。
23.根据所述的一种ti-al-c max相涂层的低温成相制备方法制得ti-al-c max相涂层,所述的ti-al-c max相涂层的厚度为2-4μm。
24.与现有技术相比,本发明的优点包括:
25.(1)利用高功率脉冲磁控溅射hipims电源对ti-al复合靶进行脉冲溅射,较低的占空比和较高的靶材峰值功率密度,提高了靶材元素和反应气体的离化率,提高了溅射过程中等离子体能量,使后续能够在较低的热处理温度下制备出ti3alc
2 312系max相,降低了目前pvd技术中传统磁控溅射或阴极电弧镀制备ti3alc
2 312系max相所需的成相温度(传统900~1200℃),本发明在600-700℃则生成了较纯的ti3alc
2 312系max相,为max相涂层的制备提供了一个可靠思路。
26.(2)高功率脉冲hipims电源溅射沉积技术,综合了传统磁控溅射低温沉积、表面光滑、无颗粒缺陷和阴极电弧离子镀金属离化率高、膜层结合力强、涂层致密的优点,同时改善了靶材中毒打弧的问题,使得制备的涂层表面无颗粒聚积现象,颗粒更加细化,表面更加致密且平整光滑,粗糙度低至15-19nm。
附图说明
27.图1是本发明涂层制备中高功率脉冲磁控溅射hipims电源的放电特征。
28.图2是本发明实施例1与对比例1制得的ti-al-c max相涂层沉积态与退火态的xrd谱图。
29.图3是本发明实施例1制得的ti-al-c max相涂层的表面形貌图。
30.图4是本发明对比例1制得的ti-al-c max相涂层的表面形貌图。
31.图5是本发明实施例2与对比例2制得的ti-al-c max相涂层沉积态与退火态的xrd谱图。
32.图6是本发明实施例2制得的ti-al-c max相涂层的表面形貌图。
33.图7是本发明对比例2制得的ti-al-c max相涂层的表面形貌图。
具体实施方式
34.实施例1:
35.本实施例中,基体材料为1cr11ni2w2mov不锈钢,基体表面的ti3alc
2 max相涂层的具体制备步骤如下:
36.步骤1:使用400#~2000#的sic砂纸依次对1cr11ni2w2mov不锈钢表面进行打磨,再使用金刚石研磨膏进行抛光20min;
37.步骤2:将打磨抛光后的1cr11ni2w2mov不锈钢基体置于丙酮中超声清洗10min,而后冷风吹干用导电胶粘贴于样品架上备用。
38.步骤3:将粘贴有基体的样品架置于沉积腔体室中,待机械泵和分子泵抽真空至3
×
10-5
pa以下,设置腔体温度为100℃,向真空腔体中通入34sccm的高纯氩气,设置线性阳极离子源电流为0.2a,基体偏压为-200v,对1cr11ni2w2mov不锈钢基体的表面刻蚀清洗30min。
39.步骤4:ti-al过渡层的沉积条件与以下步骤5中的一致,区别在于通入的气体不同,过渡层的沉积不通入碳氢反应气体,通入200sccm的高纯氩气,
40.步骤5:采用高功率脉冲hipims技术沉积得到tial
x-c涂层,通入200sccm的高纯氩气,通入7.5sccm的高纯甲烷反应气体,溅射靶为ti、al比为2:1.5的复合靶,溅射源hipims电源设置为频率500hz,周期2000μs,占空比5%,脉冲时间100μs,设置沉积过程中功率恒定,为2000w,沉积过程中的放电特征如图1所示,基体偏压为0v,腔体气压为1pa,沉积时间为120min。
41.步骤6:将得到的沉积态tial
x-c涂层置于退火炉中,真空度低于2
×
10-3
pa,在700℃中保温90min,获得ti3alc
2 max相。
42.对比例1:
43.本实施例是上述实施例1的一个对比实施例。
44.本实施例中,基体与实施例1完全相同,基体的前期处理和表面氩离子辉光刻蚀也完全相同,所不同的是在步骤(4)与步骤(5)中,ti-al过渡层与tial
x-c涂层的沉积采用传统的直流磁控溅射技术,而非hipims高功率脉冲磁控溅射,沉积过程中直流溅射源同样设置为2000w的恒功率。后续的热处理条件也同实施例1中的一致。
45.图2为上述实施例1,对比例1所制得的涂层的沉积态和退火态x射线衍射谱图。由图2中可以看出,hipims高功率脉冲磁控溅射所得的沉积态涂层的成分为tial
x
化合物,而对比例中直流磁控溅射所得的沉积态涂层为非晶态,之后在相同的退火温度下,只有
hipims高功率脉冲磁控溅射技术在700℃的热处理过程中获得了ti3alc
2 312系max相,而对比例直流磁控溅射技术下,只生成了ti2alc 211系max相。xrd谱图中还有部分来自于基体和过渡层的峰。
46.图3和图4分别为上述实施例1,对比例1所制得的涂层的表面形貌图,hipims高功率脉冲磁控溅射制备的涂层较直流磁控溅射制备的涂层表面更加致密平整,颗粒更加细化。
47.实施例2:
48.本实施例中,基体材料为tc4钛合金,基体表面的ti3alc
2 max相涂层的具体制备步骤如下:
49.步骤1:使用400#~2000#的sic砂纸依次对tc4钛合金表面进行打磨,再使用金刚石研磨膏进行抛光20min;
50.步骤2:将打磨抛光后的tc4钛合金基体置于丙酮中超声清洗10min,而后冷风吹干用导电胶粘贴于样品架上备用。
51.步骤3:将粘贴有基体的样品架置于沉积腔体室中,待机械泵和分子泵抽真空至3
×
10-5
pa以下,设置腔体温度为100℃,向真空腔体中通入34sccm的高纯氩气,设置线性阳极离子源电流为0.2a,基体偏压为-200v,对tc4钛合金基体的表面刻蚀清洗30min。
52.步骤4:ti-al过渡层的沉积条件与以下步骤5中的一致,区别在于通入的气体不同,过渡层的沉积不通入碳氢反应气体,只通入200sccm的高纯氩气,
53.步骤5:采用高功率脉冲hipims技术沉积得到tial
x-c涂层,通入200sccm的高纯氩气,通入7.5sccm的高纯甲烷反应气体,溅射靶为ti、al比为2:1.5的复合靶,溅射源hipims电源设置为频率500hz,周期2000μs,占空比5%,脉冲时间100μs,设置沉积过程中功率恒定,为2000w,沉积过程中的放电特征如图1所示,基体偏压为0v,腔体气压为1pa,沉积时间为120min。
54.步骤6:将得到的沉积态tial
x-c涂层置于退火炉中,真空度低于2
×
10-3
pa,在700℃中保温90min,获得ti3alc
2 max相。
55.对比例2:
56.本实施例是上述实施例2的一个对比实施例。
57.本实施例中,基体与实施例2完全相同,基体的前期处理和表面氩离子辉光刻蚀也完全相同,所不同的是在步骤(4)与步骤(5)中,ti-al过渡层与tial
x-c涂层的沉积采用传统的直流磁控溅射技术,而非hipims高功率脉冲磁控溅射,沉积过程中直流溅射源同样设置为2000w的恒功率。后续的热处理条件也同实施例2中的一致。
58.图5为上述实施例2,对比例2所制得的涂层的沉积态和退火态x射线衍射谱图。由图5中可以看出,不同于直流磁控溅射(dc)下所得涂层的沉积态为非晶态,hipims高功率脉冲磁控溅射所得的沉积态涂层的成分为钛铝化合物tial
x
,在后续的退火处理中,同样只有hipims高功率脉冲磁控溅射技术在700℃的热处理过程中获得了ti3alc
2 312系max相,而对比例直流磁控溅射技术下,只生成了ti2alc 211系max相。xrd谱图中还有部分来自于基体和过渡层的峰。
59.图6和图7分别为上述实施例2,对比例2所制得的涂层的表面形貌图,直流磁控溅射制备的涂层存在聚集的球形颗粒组成的山丘特征,而hipims高功率脉冲磁控溅射制备的
涂层这种聚结现象得到了明显改善,涂层表面颗粒细化,涂层更加致密,表面更加平整光滑。
60.此外,本发明人还参照实施例1与实施例2的方式,以本说明书中列出的其他基体原料和条件进行了试验,并得到了同样的结果。
61.综上所述,通过hipims高功率脉冲磁控溅射技术,可以降低ti3alc
2 312系max相的成相温度,并且制备的涂层的质量更好。
62.以上实施例在以本发明技术方案为前提下进行实施,给出了详细的实施方式和具体的操作过程,但本发明的保护范围不限于上述的实施例。