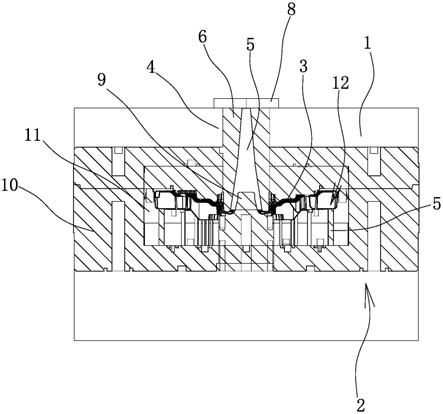
1.本实用新型属于压铸模具技术领域,涉及一种具有排气机构的圆盘型薄壁深型腔铝合金压铸模具。
背景技术:
2.压铸模具是铸造液态模锻的一种方法,一种在专用的压铸模锻机上完成的工艺。它的基本工艺过程是:金属液先低速或高速铸造充型进模具的型腔内,模具有活动的型腔面,它随着金属液的冷却过程加压锻造,既消除毛坯的缩孔缩松缺陷,也使毛坯的内部组织达到锻态的破碎晶粒。毛坯的综合机械性能得到显著的提高。
3.压铸模具主要用于生产合金压铸件,一般薄壁产品在压铸生产的过程中都会受压铸设备的制约性比较大,经常性的会存在冲型困难,严重的时候会存在产品难以成型。严重影响产品的外观和使用性能。
技术实现要素:
4.本实用新型的目的是针对上述问题,提供一种具有排气机构的圆盘型薄壁深型腔铝合金压铸模具。
5.为达到上述目的,本实用新型采用了下列技术方案:
6.一种具有排气机构的圆盘型薄壁深型腔铝合金压铸模具,包括上模与下模,所述的上模与下模之间形成有成型腔,其特征在于,所述的上模上设置有连接进料机与成型腔的进料组件,所述下模用于压铸件成型的上表面上设置有若干排气通道,若干所述的排气通道自下模的上表面向下延伸开设。
7.在上述的具有排气机构的圆盘型薄壁深型腔铝合金压铸模具中,所述的进料组件包括料筒,所述料筒的上端设置有定位套,所述料筒的下端穿入至成型腔内,所述的料桶内开设有与成型腔相连通的进料通道。
8.在上述的具有排气机构的圆盘型薄壁深型腔铝合金压铸模具中,所述的进料通道呈锥形设置,所述进料通道上端的直径小于进料通道下端的直径。
9.在上述的具有排气机构的圆盘型薄壁深型腔铝合金压铸模具中,所述下模与料筒相对应位置处设置有穿入至进料筒到内的分流锥。
10.在上述的具有排气机构的圆盘型薄壁深型腔铝合金压铸模具中,所述分流锥的下端可拆装连接于下模上。
11.在上述的具有排气机构的圆盘型薄壁深型腔铝合金压铸模具中,所述分流锥朝向进料通道一侧的上表面为弧形面。
12.在上述的具有排气机构的圆盘型薄壁深型腔铝合金压铸模具中,所述的下模包括外模座以及设置于外模座内的成型块,所述的分流锥设置于成型块的中心处,所述的成型块上设置有环绕分流锥分布的下凹成型面,若干所述的排气通道设置于下凹成型面的外侧。
13.在上述的具有排气机构的圆盘型薄壁深型腔铝合金压铸模具中,若干所述的排气通道环绕分流锥周向均匀分布于成型块上。
14.在上述的具有排气机构的圆盘型薄壁深型腔铝合金压铸模具中,每个所述的排气通道自成型块的上表面向下延伸贯穿成型块。
15.在上述的具有排气机构的圆盘型薄壁深型腔铝合金压铸模具中,所述的外模座上设置有若干定位块,若干所述的定位块周向均匀分布于外模座上。
16.与现有的技术相比,本实用新型的优点在于:
17.1、本实用新型的压铸模具压铸成型时通过排气通道将成型腔的空气排出,使压铸的过程中不会由于内腔气体的反压力原因造成冲型的困难,降低了对压铸设备的依赖并很好的改善产品的表面质量。
18.2、本实用新型的下模与料筒相对应位置处设置有穿入至进料筒到内的分流锥,通过分流锥将从进料组件内进入的材料均匀分散。
19.3、本实用新型的外模座上设置有若干定位块,下模通过定位块与上模的配合,提高配合性。
20.本实用新型的其它优点、目标和特征将部分通过下面的说明体现,部分还将通过对本实用新型的研究和实践而为本领域的技术人员所理解。
附图说明
21.图1是本实用新型的整体结构剖视图。
22.图2是本实用新型中下模的局部结构示意图。
23.图3是本实用新型中成型块内排气通道的分布图。
24.图中,1、上模;2、下模;3、成型腔;4、进料组件;5、排气通道;6、料筒;7、定位套;8、进料通道;9、分流锥;10、外模座;11、成型块;12、下凹成型面;13、定位块。
具体实施方式
25.下面结合附图对本实用新型进行进一步说明。
26.如图1至图3所示,一种具有排气机构的圆盘型薄壁深型腔铝合金压铸模具,包括上模1与下模2,上模1与下模2之间形成有成型腔3,上模1上设置有连接进料机与成型腔3的进料组件4,下模2用于压铸件成型的上表面上设置有若干排气通道6,若干排气通道6自下模2的上表面向下延伸开设。
27.在本实施例中,模具通过上模1与下模2配合实现压铸,材料通过进料组件4进入至压铸模具压铸成型时通过排气通道6将成型腔3的空气排出,使压铸的过程中不会由于内腔气体的反压力原因造成冲型的困难,降低了对压铸设备的依赖并很好的改善产品的表面质量。
28.在本实施例中,进料组件4包括料筒,所述料筒的上端设置有定位套7,料筒的下端穿入至成型腔3内,料桶内开设有与成型腔3相连通的进料通道8。进料通道8呈锥形设置,进料通道8上端的直径小于进料通道8下端的直径。料筒到的上端较小,有利于增大进料时的压强与流速,料桶下端的开口逐渐变大可以使物料均匀扩散至四周。
29.在本实施例中,下模2与料筒相对应位置处设置有穿入至进料筒到内的分流锥9,
分流锥9的下端可拆装连接于下模2上,分流锥9朝向进料通道8一侧的上表面为弧形面。通过分流锥9将从进料组件4内进入的材料均匀分散。
30.下模2包括外模座10以及设置于外模座10内的成型块11,分流锥9设置于成型块11的中心处,成型块11上设置有环绕分流锥9分布的下凹成型面12,若干排气通道6设置于下凹成型面12的外侧。
31.在本实施例中,若干排气通道6环绕分流锥9周向均匀分布于成型块11上,且每个排气通道6自成型块11的上表面向下延伸贯穿成型块11。在型腔薄壁位置或者冲型困难的位置设计排气通道6,排气通道6设计成扁平方形,流出型腔封浇面8mm-10mm,镶件的其他位置整圈进行避空0.05,并此镶件进行特殊的表面处理,使型腔内的气体能够通过此缝隙,而铝液无法通过。
32.在本实施例中,外模座10上设置有若干定位块13,若干定位块13周向均匀分布于外模座10上,上模1上设置有与定位块13相配合的内槽,外模座10上设置有若干定位块13,下模2通过定位块13与上模1的配合,提高配合性。
33.本实用新型的工作原理为:模具通过上模1与下模2配合实现压铸,薄壁深度大的产品在压铸的过程中铝水从料筒进入至成型腔3中,在高速高压的铝水冲击下,成型腔3内部的气体特别是薄壁的位置气体很难快速的排出到模具的外面,此种受压状态的气体在压力越大的情况下,其反作用力就比较的明显,严重的时候会造成此处存在难以成型的问题,通过排气通道6来实现该问题的解决。
34.具体的,排气通道6环绕分流锥9周向均匀分布于成型块11上,且每个排气通道6自成型块11的上表面向下延伸贯穿成型块11。在型腔薄壁位置或者冲型困难的位置设计排气通道6,排气通道6设计成扁平方形,流出型腔封浇面8mm-10mm,镶件的其他位置整圈进行避空0.05,并此镶件进行特殊的表面处理,使型腔内的气体能够通过此缝隙,而铝液无法通过,使压铸的过程中不会由于内腔气体的反压力原因造成冲型的困难,降低了对压铸设备的依赖并很好的改善产品的表面质量。
35.本文中所描述的具体实施例仅仅是对本实用新型精神作举例说明。本实用新型所属技术领域的技术人员可以对所描述的具体实施例做各种各样的修改或补充或采用类似的方式替代,但并不会偏离本实用新型的精神或者超越所附权利要求书所定义的范围。
36.尽管本文较多地使用水泵1、射流器2、空气输入机3、双轴电机4、浮台5、喷洒头6、过滤网7、射流嘴8、射流套9、负压形成腔10、锥形喷嘴11、负压吸引连接口12、锥形吸引腔13、混合通道14、释放口15、臭氧发生器100,第一阀门101、第二阀门102、第三阀门103、第四阀门104等术语,但并不排除使用其它术语的可能性。使用这些术语仅仅是为了更方便地描述和解释本实用新型的本质,把它们解释成任何一种附加的限制都是与本实用新型精神相违背的。