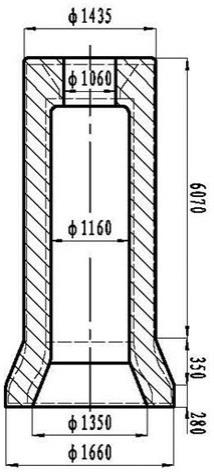
1.本发明属于锻造技术领域,具体涉及一种提高球墨铸铁管模使用寿命的工艺方法。
背景技术:
2.大型离心球墨铸铁管模为铸管行业中重要的消耗性设备,市场需求量极大,管模的工作环境极为恶劣,其各项技术指标要求很高,特别是技术指标通常限定最低折算拔出铸管支数(一般设定不低于1600支),否则需要折价赔偿。
3.目前,大型管模锻件使用中时常出现内壁金属脱落、承口端炸裂、整体变形等现象,主要原因在于工艺简图设计不尽合理,成分设计匹配性不高、形变量及温度控制不合理、钢锭的洁净度低和热处理强度指标不均匀等,导致拔出铸管支数不满足技术指标,不仅降低生产效率,也大大增加制造成本,不符合绿色制造要求。
技术实现要素:
4.为解决现有的型离心球墨铸铁管模使用中质量不稳定、拔出铸管支数偏少的问题,采用本发明的方法通过采用近净成形工艺,特殊法兰锻造成形方法,综合设定成分,控制主变形形变量,匹配芯棒拔长变形量和锻造温度,保证锻件总体性能一致性,提高锻件综合力学性能。
5.本发明为解决上述技术问题采用的技术方案是:一种提高球墨铸铁管模使用寿命的工艺方法,包括以下制备步骤:步骤一、采用近净成形技术:根据管模零件结构和使用特点综合设计锻件工艺图,差异化控制内外圆留量;步骤二、化学成分制定:根据步骤一对管模中关键成分和有害元素进行综合设计,管模包括如下质量百分比的化学成分:铬:2.30~2.60%,钼:0.40~0.60%,钒:0.04~0.10%,铝≤0.02%,铅≤0.010%,锡≤0.010%,锑≤0.010%,铋≤0.010%,砷≤0.015%, h≤1.0ppm,o≤20ppm,n≤60ppm,其余元素含量按照国家标准执行;步骤三、洁净钢冶炼:采用优选废钢和双真空冶炼工艺,得钢锭;步骤四、whf法主变形镦拔:将步骤三制备出的钢锭进行whf法镦粗拔长下料;步骤五、取步骤四的坯料经镦粗、冲孔、扩孔后对芯棒进行控形控温拔长:步骤六、将步骤五中的管模锻件锻后空冷到温度为400~450℃,进行回火处理,回火温度为640~660℃;步骤七、将步骤六管模经粗加工后进行正火+调质工艺,得成品。
6.进一步的,步骤一中外圆加工余量30~60mm、内孔加工余量80~120mm。
7.进一步的,步骤四中锻造温度为850~1240℃,主变形量≥2.6。
8.进一步的,步骤五中控形控温拔长的工艺为:第一次芯轴预拔长锻造温度为700~1200℃,拔长比为1.6~1.7;第二次芯轴预拔长锻造温度为1200~700℃,拔长比为1.5~
1.6;第三次芯轴预拔长锻造温度为1150~700℃,拔长比为1.2~1.3;第四次精整和收孔锻造温度为650~950℃,拔长比为1~1.1。
9.进一步的,步骤五在不同拔长阶段区别控制热摩擦系数,其中第一次和第二次拔长时充分润滑芯棒,降低摩擦助力,提高拔长效率,第三次拔长时法兰部位不润滑芯棒,增加法兰端内孔摩擦助力。
10.进一步的,步骤五中采用特殊法兰锻造成形方法,锻出法兰内外圆弧面,外圆弧面采用锥度成形控制法,设定不同压下量锻出弧度;内孔圆弧面采用锻造不同芯棒拔长阶段热摩擦系数控制法,利用摩擦阻力促使内孔产生内弧面。
11.本发明的有益效果为:本发明中通过综合设计锻件工艺图,差异化控制内外圆留量,保证了整体流线的完整性及强度一致性;同时,通过采用近净成形技术和特殊法兰锻造成形方法,设计最优管模法兰端内外圆弧面,提高管模总体质量一致性和法兰使用寿命。根据管模使用环境,设计最优成分配比和洁净钢控制技术,不仅为后续综合力学性能提升提供基础,而且避免管模使用中局部金属或者颗粒夹杂物脱落;钢锭经过whf法主变形,并采用控形控温芯棒拔长技术,设计最优的形变量和匹配温度,控制每火次锻造比和锻造温度,破碎铸态组织,提高金属致密性,防止晶粒粗化,为获得理想的金属晶粒和优良性能做准备;锻造完成后调整热处理控制技术,采用锻后回火+粗加工+正火、调质的工艺路线,避免毛坯锻件各部留量不均一、锻后直接正火效果不理想的问题,达到最佳的均质效果和强度一致性的目的,防止使用中管模局部变形等现象。
附图说明
12.图1是发明的实施例1锻造后管模的结构示意图;图2是发明实施例1中坯料镦粗的结构示意图;图3是发明实施例1中坯料冲孔的结构示意图;图4是发明实施例1中坯料扩孔的结构示意图;图5是发明拔长过程中坯料及芯棒的结构示意图;图6是发明实施例1中芯棒第一次拔长后的结构示意图;图7是发明实施例1中芯棒第二次拔长后的结构示意图;图8是发明实施例1中芯棒第三次拔长后的结构示意图;图示标记,1、拔长专用锤头,2、坯料,3、芯棒。
具体实施方式
13.结合具体实施方式对本发明实施例加以详细说明,本实施例以本发明技术方案为前提,给出了详细的实施方式和具体的操作过程,但本发明的保护范围不限于下述的实施例。
14.一种提高球墨铸铁管模使用寿命的工艺方法,包括以下制备步骤:步骤一、采用近净成形技术:根据管模零件结构和使用特点综合设计锻件工艺图,差异化控制内外圆留量,外圆加工余量30~60mm、内孔加工余量80~120mm,达到去除心部劣质金属、保留近表面优良柱状晶组织的目的,充分利于外端优良金属对管模主要使用部位内孔强度的增强、牵制作用;
步骤二、化学成分制定:根据步骤一对管模中关键成分和有害元素进行综合设计,管模包括如下质量百分比的化学成分:铬:2.30~2.60%,钼:0.40~0.60%,钒:0.04~0.10%,铝≤0.02%,铅≤0.010%,锡≤0.010%,锑≤0.010%,铋≤0.010%,砷≤0.015%, h≤1.0ppm,o≤20ppm,n≤60ppm,其余元素含量按照国家标准执行,综合设定管模锻件化学成分,提高总体耐热强度;步骤三、洁净钢冶炼:并采用高洁净钢控制技术进行钢锭冶炼,优选工艺锭型,并通过采用高洁净钢控制技术进行钢锭冶炼,ebt电炉初炼阶段优选废钢、lf精炼阶段控制出钢温度、vcd真空碳脱氧阶段控制气体含量,得钢锭;步骤四、whf法主变形镦拔:将步骤三制备出的钢锭进行whf法镦粗拔长下料,步骤四中锻造温度为850~1240℃,主变形量≥2.6,提高金属致密性;步骤五、取步骤四的坯料经镦粗、冲孔、扩孔后对芯棒进行控形控温拔长:第一次芯轴预拔长锻造温度为700~1200℃,拔长比为1.6~1.7;第二次芯轴预拔长锻造温度为1200~700℃,拔长比为1.5~1.6;第三次芯轴预拔长锻造温度为1150~700℃,拔长比为1.2~1.3;第四次精整和收孔锻造温度为650~950℃,拔长比为1~1.1,实现拔长难度系数和形变量与温度最佳匹配,并在不同拔长阶段区别控制热摩擦系数,其中第1次和2次拔长时充分润滑芯棒,降低摩擦助力,提高拔长效率,第3次拔长时法兰部位不润滑芯棒,增加法兰端内孔摩擦助力。
15.步骤六、将步骤五中的管模锻件锻后空冷到温度为400~450℃,进行回火处理,回火温度为640~660℃,消除形变、温度和组织转变应力,改善切削加工性能;步骤七、将步骤六管模经粗加工后进行正火+调质工艺,实现最佳的均质效果和强度一致性目的、提高综合力学性能。
16.进一步的,步骤五中控形控温拔长的工艺为:第一次芯轴预拔长锻造温度为700~1200℃,拔长比为1.6~1.7;第二次芯轴预拔长锻造温度为1200~700℃,拔长比为1.5~1.6;第三次芯轴预拔长锻造温度为1150~700℃,拔长比为1.2~1.3;第四次精整和收孔锻造温度为650~950℃,拔长比为1~1.1。
17.进一步的,步骤五在不同拔长阶段区别控制热摩擦系数,其中第一次和第二次拔长时充分润滑芯棒,降低摩擦助力,提高拔长效率,第三次拔长时法兰部位不润滑芯棒,增加法兰端内孔摩擦助力。
18.进一步的,步骤五中采用特殊法兰锻造成形方法,锻出法兰内外圆弧面,外圆弧面采用锥度成形控制法,设定不同压下量锻出弧度;内孔圆弧面采用锻造不同芯棒拔长阶段热摩擦系数控制法,利用摩擦阻力促使内孔产生内弧面。
19.本发明通过综合采用近净成形技术、特殊法兰锻造成形方法、高洁净钢技术、控形控温拔长技术和特殊热处理技术,差异化控制内外圆加工余量,锻出法兰内外圆弧面,提高钢锭纯净度,设计最优形变量和匹配温度,调整热处理工艺和参数,实现最佳的均质效果和强度一致性目的,有效提高管模使用寿命。
20.实施例1一种提高球墨铸铁管模使用寿命的工艺方法,采用工艺图设计—化学成分制定—洁净钢冶炼—whf法主变形镦拔—控形控温芯轴拔长(芯轴第1次拔长、第2次拔长、第3次拔长、第4次精整、收孔)—特殊热处理工艺设定(锻后回火—粗加工—正火+调质),具体过程
为:步骤一:采用近净成形技术,设计最优的工艺简图,并差异化控制各部金属余量,外圆留量55mm,内孔90mm。
21.步骤二:化学成分制定,铬:2.30~2.60%,钼:0.40~0.60%,钒:0.04~0.10%,铝≤0.02%,铅≤0.010%,锡≤0.010%,锑≤0.010%,铋≤0.010%,砷≤0.015%, h≤1.0ppm, o≤20ppm, n≤60ppm,其余元素含量按照国家标准执行。
22.步骤三:洁净钢冶炼:采用优选废钢和双真空冶炼工艺,提高钢锭纯净度。
23.步骤四:whf法主变形镦拔,镦粗尺寸:h1190~φ2230mm,压下量按照20%变形量控制、进砧量1400-1650mm,主变形后进行下料,锻造温度850~1240℃,主变形量2.65。
24.步骤五:坯料1经镦粗h1760~φ1850mm、冲孔φ600mm、扩孔φ1200mm后进行控形控温拔长:拔长时需用拔长专用锤头1将坯料固定,沿着芯棒3的中心轴线方向向外延伸拔长;首次芯轴预拔长锻造温度700~1200℃,拔长至l=3050mm,拔长比1.69;第二次芯轴预拔长锻造温度1200~700℃,拔长至l=4880mm,拔长比1.6;第三次芯轴预拔长锻造温度1150~700℃,拔长至l=6300mm,拔长比1.29;最后一火次精整和收孔锻造温度650~950℃,拔长比1.04。第1次和第2次拔长时充分时充分润滑芯棒,降低摩擦助力,提高拔长效率,第3次拔长时法兰部位不润滑芯棒,增加法兰端内孔摩擦助力,锻出内孔弧面。
25.步骤六:管模锻件锻造完成后空冷到400~450℃,然后执行650
±
10℃回火处理,去除形变、温度和组织转变应力、利于切削加工;步骤七:粗加工完成后的管模执行正火+调质工艺,实现最佳的均质效果和强度一致性的目的、提高综合力学性能。
26.本发明中采用近净成形技术,设计最优工艺简图,差异化控制各部金属余量的目的是:由于钢锭凝固的固有规律,外端金属属于优良柱状晶组织、内部金属极易存在夹杂物及异相质点,通过减少外端金属去除量和增加内部金属去除量手段,有利于外端优良金属对管模强度的增强、牵制作用,避免管模使用时内孔存在的可能夹杂物或者异相质点的脱落。
27.本发明中采用特殊法兰锻造成形方法,锻出法兰内外圆弧面得目的是:实际使用中,法兰端频繁炸裂现象经常发生,由于采用矩形截面锻造时各部切削量不均一,存在强度差异化问题,为炸裂提供了条件,采用特殊法兰锻造法后,法兰各部加工量比较均一,整体强度一致性较好,有利于控制法兰炸裂问题。
28.本发明中,所述的坯料经镦粗、冲孔、扩孔后进行控形控温拔长工序主要作用是:由于管模薄壁锻件属性,相对壁厚(t/d)一般小于0.1(t:管模壁厚;d:内孔直径),属于典型难变形薄壁套类锻件。在第一次拔长和第二次拔长时,坯料壁厚相对较厚(t/d=0.15-0.22),拔长难度相对较小,属于较有利于拔长阶段,采用高温大压下量拔长,设定较大的拔长比,提高锻打效率;在第三次拔长时,坯料相对壁厚t/d=0.11-0.13,极不利于金属的轴向走料,由于该阶段拔长比较小,破碎大型金属组织的能力弱,通过综合设定形变量和匹配锻造温度,尽量避免锻件在高温停留时间,控制晶粒长大风险,也达到节能降耗目的,符合绿色制造需求;在精整和收孔阶段,坯料基本接近锻件尺寸,变形量较小,锻造温度控制950℃(管模材质通常正火温度),降低金属加热时晶粒长大风险,同时该温度区间锻造也达到了
形变强化的目的。通过控形控温拔长,实现拔长难度系数和形变量与温度最佳匹配,提高锻件综合力学性能目的。
29.采用本发明锻制出的球墨铸铁管模很大程度改观了内壁金属脱落、法兰端头频繁炸裂、使用变形问题,很好的保证了锻件整体质量,也适合批量管模锻件的生产,在实际使用中,管模拔出铸管支数大于1600支,满足用户要求指标,创造了可观的经济价值。
30.应当指出,虽然通过上述实施方式对本发明进行了描述,然而本发明还可以有其他的多种实施方式。在不脱离本发明精神和范围的前提下,熟悉本领域的技术人员显然可以对本发明做出各种相应的改变和变形,但这些改变和变形都应当属于本发明所附权利要求及其等效物所保护的范围内。