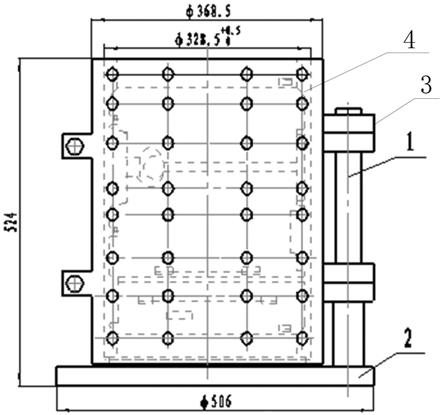
1.本发明涉及一种以高强度铸造铝合金制造的易变形薄壁壳体类零件的加工方法,具体为一种防止壳体固溶变形的工艺方法。
背景技术:
2.某产品铸造壳体,材料为高强度铸造铝合金,固溶时效后性能要求为:σb≥360mpa,σ0.2≥340mpa,δ5≥3.5%。壳体内腔不允许加工(凸台除外),在固溶时效工序检测内腔尺寸,公差为
±
0.3mm。
3.该壳体工艺路线为:铸造-粗加-测壁厚-探伤-固溶时效-检测内腔直径-半精加-去应力时效-精车外圆-测壁厚-去应力时效-加工孔系-涂漆-终检。壳体需经过3次热处理工序,根据产品图纸设计要求,确定热处理工艺方案为固溶时效、去应力时效、去应力时效。固溶时效工序为保证产品的最终性能满足图纸的设计要求,即σb≥360mpa,σ0.2≥340mpa,δ5≥3.5%。
4.固溶时效工序的工艺参数为:520℃+12h水冷170℃+10h空冷去应力时效工序为了消除机加过程中因切削,装夹而使产品产生的应力,从而稳定产品尺寸。
5.而实际生产中,自正样阶段以来,固溶后壳体的内腔尺寸公差均超过工艺要求,普遍在1-2mm,最大达到3mm,导致产品的报废。
6.理论分析壳体固溶后变形主要受壳体内腔的结构所导致,该壳体外形如图1、2所示,内腔多凸台(凸台上最后要加工通孔),环筋,成型壳体壁厚5.5
±
0.3mm。在加热和冷却过程中,受壁厚差的影响,不同部位的升温,冷却速度,组织转变是不同步的,同时,在铸造过程中,砂型的密实度区别也对壳体的变形产品不良影响,受综合因素的影响,壳体就发生了变形。因此,壳体的变形问题,要求从壳体形状,铸造,热处理等方面采取措施来解决。
技术实现要素:
7.本发明为解决某铸造壳体采用现有工艺路线加工后存在壳体内腔尺寸公差均超过工艺要求普遍在1-2mm,导致产品报废的技术问题,提供一种防止壳体固溶变形的工艺方法。
8.本发明所述方案采用如下技术方案实现:一种防止壳体固溶变形的工艺方法,包括铸造、粗加、固溶时效步骤;铸造出的毛坯壳体内腔多凸台;(a)粗加时,粗车外圆,并在内腔凸台位置粗铣出等效壁厚,等效壁厚比壳体内腔厚度小0.5-1mm;(b)固溶:将壳体凸台较多的一端朝下竖直放入固溶料筐内,吊料筐入炉加热,室温装炉,采用分步阶梯加热:450℃保温2h,由室温-450℃区间升温速度小于80℃/h;
500℃保温2h,450-500℃区间升温速度小于50℃/h;520℃保温12h,500-520℃区间升温速度小于30℃/h;保温结束后在5%或10%或15%三种不同浓度的pag淬火液中冷到室温;(c)校正:固溶后检测壳体指定位置的内腔直径并记录,而后将壳体放入多点位外顶工装内夹紧;所述多点位外顶工装包括底座以及竖直安装在底座一侧的立柱;立柱上通过合页安装有一对半圆形的夹持板,夹持板的另一端通过螺栓实现连接,一对夹持板将壳体夹紧,夹持板上还有多个螺纹通孔,螺纹通孔内配有螺钉;根据壳体壁厚值和内腔直径,在内腔直径大的位置调整对应点位的螺钉,用螺钉顶住并挤压壳体外壁,调整时将百分表的探头压在螺钉头部,并记录调整值,调整完毕后放入烘干箱内时效;(d)带工装入炉时效,室温装炉,升温速度不大于100℃/h,保温时间到后出炉空冷。
9.与现有技术相比具有的有益效果:该壳体变形难以控制的关键点在于内腔不允许加工(凸台除外),这就要求在固溶时效工序中就要将内腔直径控制在最终产品的公差范围内,而现有技术均是建立在内腔加工的基础上设计的,内腔留有足够的加工余量,固溶后通过加工内腔保证内腔直径。现有技术处理的壳体,内腔直径差均在1mm以上,显然,现有工艺不适用于该类壳体的处理。
10.本发明所述新的工艺方法,在充分了解yrz-02高强度铸造铝合金特性和壳体结构的基础上,采用在凸台等部位设计等效壁厚,分步阶梯加热,采用pag水基淬火液冷却,增加固溶防变形工装4方面措施,在保证性能指标的前提下,将壳体的变形控制在工艺要求范围内。
附图说明
11.图1 本发明所述壳体毛坯结构示意图。
12.图2 壳体等效壁厚示意图。
13.图3多点位外顶工装主视结构示意图。
14.图4多点位外顶工装俯视结构示意图。
15.1-立柱,2-底座,3-合页,4-壳体,5-夹持板,6-螺栓,7-螺母,8-螺钉。
具体实施方式
16.针对现有技术存在的情况,申请人经研究分析并进行多次工艺试验,决定采用以下4方面措施解决壳体的变形问题:1.1、在凸台等部位设计等效壁厚;1.2、分步阶梯加热;1.3、采用pag水基淬火液冷却;1.4、增加固溶防变形工装;2、具体技术方案2.1 粗加:粗车外圆,并在内腔凸台位置粗铣出等效壁厚(为最终尺寸留精加余量),等效壁厚比壳体内腔厚度小0.5-1mm(如图2中,标注为8-8.5的几个位置,壁厚为9mm)。按工艺要求测量指定点位的内腔直径及壁厚值并记录。
17.2.2固溶:将壳体凸台较多的一端朝下竖直放入固溶料筐内,吊料筐入炉加热。室温装炉。
18.450℃+2h室温-450℃区间升温速度小于80℃/h;500℃+2h450-500℃区间升温速度小于50℃/h;520℃+12h500-520℃区间升温速度小于30℃/h;保温结束后在5%,10%,15%不同浓度的pag淬火液中冷到室温。上述三种不同浓度的淬火液均可以用于本发明的淬火,实际应用中选择其中一种淬火液进行淬火;上述三种淬火液之间为“或”的关系。
19.2.3校正:固溶后检测壳体指定位置的内腔直径并记录,而后将壳体放入多点位外顶工装内夹紧(见图3、4所示),直至接触壳体外壁,将较大内腔直径两端的螺钉拧紧,在螺钉头部压百分表,继续拧紧螺钉,记录百分表变化值;同理调整其它点位,保证内腔直径的公差在
±
0.3mm范围内,调整完毕后放入烘干箱内时效。
20.2.4时效:带工装入炉时效,室温装炉,升温速度不大于100℃,保温时间到后出炉空冷:170℃+10h空冷。
21.2.5检测:出炉后,将壳体从工装上卸下,检测指定位置的内腔直径并记录,带性能检测合格后进行半精车工序。
22.按此工艺方法处理了5件壳体,经检测,内腔尺寸全部控制在
±
0.3mm以内。
23.如图1、2中,壳体外径为330mm,高度为498mm,凸台的厚度为36mm;凸台以外的壁厚为9mm,加工出的等效壁厚为8-8.5mm。
24.如图3、4为本发明所述多点位外顶工装的结构示意图,多点位外顶工装包括底座2以及竖直安装在底座2一侧的立柱1;立柱1上通过合页3安装有一对半圆形的夹持板5,夹持板5的另一端通过螺栓6实现连接,一对夹持板5将壳体4夹紧,夹持板5上还有多个螺纹通孔,螺纹通孔内配有螺钉8。夹持板形成的夹持圆环外径为368mm,底座外径为506mm。
25.夹持板5上的螺纹通孔排列成多条水平行和多条竖直纵列,螺纹通孔之间等间距排布,这样能够方便对整个壳体外壁进行点对点的调整。
26.立柱1上设有上下两个合页3,分别连接一个夹持板5;一对夹持板5的另一端均设有上下两个凸出部,上下两个凸出部均设有螺孔,穿过两个夹持板5对应的螺孔设有螺栓6及螺母7将一对夹持板5连接起来。校正步骤中,百分表的安装座固定在底座2上。
27.本发明的创新点:1、设计适用于高强度铝合金的分步阶梯加热工艺,配合升温速度的严格控制,控制加热过程的变形趋势。
28.2、在凸台等位置加工出等效壁厚,使壳体形状趋近与等壁厚壳体,并摸索出等效壁厚值,控制加热,冷却过程的变形趋势。
29.3、设计多点位外顶工装,点对点的对超差的点位进行校正,保证壳体内腔直径在工艺要求范围内。
30.4、通过在不同浓度的pag水基淬火液中试验,在保证性能指标的前提下,选择最大的浓度,降低冷却,减少壳体的变形。
31.新工艺方法的关键工艺参数是经过一次次的试验逐渐摸索出来的,并在实际生产中经过了验证,证明了其合理性。