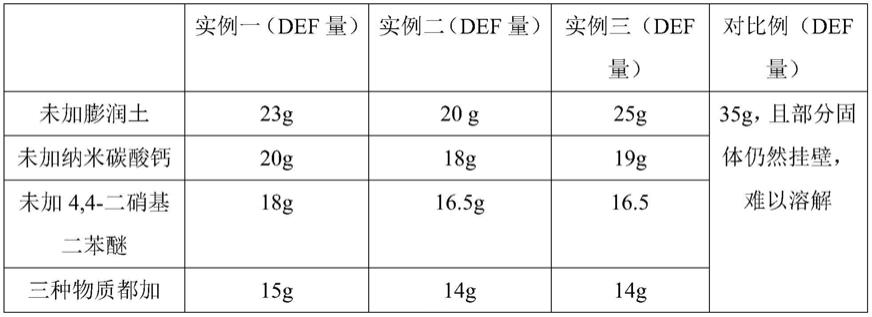
可粉末化自修复阻燃低voc聚氨酯涂料的制备方法及汽车革中应用
技术领域
1.本发明涉及一种聚氨酯涂料的制备和应用方法,特别涉及可粉末化、自修复阻燃、低voc聚氨酯涂料的制备方法,本发明还涉及所述聚氨酯涂料在汽车坐垫革中的应用。
背景技术:
2.水性聚氨酯具有安全、无害、附着力强优点,广泛应用于家具、织物涂层、汽车皮革等领域。其中在汽车革领域,由于聚氨酯涂饰剂大都呈现液体,这增加了企业运输难度,由于聚氨酯进行固化,处理不当,加水很难恢复到原来的性质,而目前国内外现有报道中没有可粉末化聚氨酯涂饰剂,因此有必要对其进行改进。
3.授权公告号cn112646475b的中国授权发明专利“阻燃耐磨耗低voc聚氨酯涂料的制备及应用方法”,在反应容器中加入聚酯二元醇、异氰酸酯、二月桂酸二丁基锡,于75~90℃搅拌反应得聚氨酯预聚体,向聚氨酯预聚体中加入亲水扩链剂二羟甲基丙酸、氮磷膨胀型阻燃剂,丙酮溶剂,于70~90℃条件下搅拌反应1~2h;再加入三乙胺以及水乳化20~60min,再加入物质a和端环氧聚醚硅油,调节ph到6.5,70~80℃下搅拌反应得到阻燃耐磨耗低voc聚氨酯涂料,所得聚氨酯膜在有焰燃烧时间、耐熔滴等方面明显均显示比较好的阻燃、耐磨耗性,所用的聚氨酯为水性聚氨酯。
4.水性聚氨酯在作为涂层材料使用过程中,往往受到摩擦、碰撞、弯曲等作用,表面会出现划痕、微裂纹等物理损伤进而导致涂层被破坏、功能丧失,使用寿命缩短。自修复聚合物材料具有修复外界物理损伤的能力,表现在材料的功能性功能下降,为了提高聚氨酯的使用寿命,需要对其进行自修复,尤其在汽车革领域,汽车革经常与人体接触,不断受到人体的挤压、摩擦、弯曲等,导致皮革的阻燃性能下降,因此迫切需要一种可修复的汽车革。
5.烟台大学皮革蛋白质实验室长期致力于汽车革及其配套化工材料的研究与开发,其专利号为cn201910405405.6的中国发明专利涉及一种防污、超低总碳散发、耐磨耗牛皮汽车坐垫革制造工艺,底涂涂料包括水性颜料膏、耐光性涂料、耐光性丙烯酸酯类树脂涂料、耐光性水性聚氨酯、阻燃性涂料和阳离子油;中涂涂料包括消光聚氨酯、亮光聚氨酯、交联剂、材料、耐磨耗聚氨酯、碳化二亚胺、ptfe乳液和抑制烟雾材料;顶涂涂料包括手感剂和阳离子油。所制备的牛皮汽车坐垫革在保持阻燃、耐光和低雾化的基础上,进一步提高了防污、耐磨耗性能,并且降低了总碳散发。由于汽车革与人紧密接触,其涂层随着人体日久磨损尤其容易造成涂层脱落,而且现有汽车商对汽车革的标准是不同的,所以对汽车革的耐磨耗需要进一步提高。
6.中国是目前世界上最大的汽车消费市场,2020年中国汽车产销分别达到2531.1万辆和2576.9万辆,产销量继续蝉联全球第一,其中20%配备真皮座椅,市场对汽车用真皮皮革的需求量是非常大的,随着车市的繁荣,汽车制革的商机被越来越多的皮革企业所关注。2017年底,中国皮革协会年会报告中提到,在全国皮革行业的所有制品利润普遍下降的环境下,唯独汽车革的利润保持增长。
7.汽车坐垫在使用过程中,由于皮革中的小分子化合物迁移会释放特殊的气味,而这些释放的气体中包含甲醛、乙醛、苯、甲苯等化合物,因此有必要降低汽车革的气味。
8.皮革加工中,陈化工序中会以粒面对粒面,肉面对肉面进行放置,但经过最后一道工序涂饰后,皮革粒面粘结性增强,放置过程中会造成粒面与粒面涂层相互黏连,分开时可能会造成部分涂层脱落或者颜色不一致的问题。
9.综上所述,有必要针对比较突出的可粉末化、自修复阻燃、低voc聚氨酯涂料进行研究,同时用于汽车革加工中,主要针对解决汽车革受长时间磨损后,阻燃性能下降的缺陷进行改进。
技术实现要素:
10.本发明所要解决的技术问题是,提供可粉末化自修复阻燃低voc聚氨酯涂料的制备方法及应用,所制备的聚氨酯可固化,固化后能够在def中基本恢复到原来的性质,同时也可具有更好的耐磨耗性能和更低的voc,并解决涂饰皮革陈化过程中的粒面层黏连难题,所得汽车革磨损或切条件下进行部分自修复来恢复阻燃性。
11.本发明的技术方案如下:
12.可粉末化聚氨酯涂料a和自修复阻燃、低voc聚氨酯涂料b的制备步骤分别为:
13.在氮气保护的反应容器中,加入聚四氢呋喃醚二醇18.6g、二异氰酸酯11.8g,将体系温度升至70~80℃,并加入二月桂酸二丁基锡0.24~0.31g,搅拌反应2~4h,在体系中加入扩链剂0.4~3.2g,反应时间2~3h;降温至50~70℃,加入降稠剂n,n-二乙基甲酰胺def15~30ml;再降温至40℃,并加入三乙胺1.7~2.5g,反应时间0.5~1h,再加入膨润土7~8g、纳米碳酸钙1~2g和4,4-二硝基二苯醚1.6~2.4g,60~70℃下搅拌反应1~2h,得到粘稠液体;真空干燥4h,磨碎,密封封存,得到可粉末化聚氨酯涂料a;
14.向1.7~4.3g氮磷膨胀型阻燃剂中,加入去离子水65~75ml、环氧树脂e51为12~17g、三羟甲基丙烷三甲基丙烯酸酯0.9g和3,4'-二氨基联苯醚1.4g,65~75℃下,搅拌反应60~90min,得自修复阻燃、低voc聚氨酯涂料b。
15.所述二异氰酸酯为4,4'-二苯基甲烷二异氰酸酯、异佛尔酮二异氰酸酯和甲苯二异氰酸酯的任意一种。
16.扩链剂为2,2-二羟甲基丙酸、2,2-二羟甲基丁酸的任意一种。
17.所述氮磷膨胀型阻燃剂的制备方法如下:
18.(1)往三口烧瓶中加入季戊四醇27.2g、磷酸138.4g,室温搅拌30~60min,将体系温度升高至90~130℃,反应1~5h,即得季戊四醇磷酸酯;将季戊四醇磷酸酯降至室温,加入三氯氧磷20.8g,再将体系升温至45~50℃,保温搅拌30~60min,降至室温,于30~60min内滴加乙醇胺12.2g,继续反应1~2h,得阻燃剂中间体a;
19.(2)将硼酸6.2~8.4g、四羟甲基硫酸磷81.2g、浓硫酸0.98g,70~90℃下搅拌反应1~3h,再加入氢氧化钠溶液调节ph调至6.0,再加入3-氨丙基三乙氧基硅烷2.5~3.6g(kh550)于反应容器中,于70~110℃下搅拌反应1~7h,既得中间体b;
20.(3)取步骤(1)的阻燃剂中间体a、步骤(2)的中间体b、木质素磺酸钠4.2~8.6g,于60~70℃下搅拌反应1~2h,再加入丁酸酐1.2~1.7g、2,4-二羟基苯甲醛0.6~1.2g,于70~80℃下反应1~3h,再加入乙二胺四乙酸0.5~1.2g、4-羧基苯硼酸0.2~0.4g、2-乙酰氧
基异丁酰氯0.1~0.4g,于70~80℃反应2-3h,得氮磷膨胀型阻燃剂。
21.所述涂饰工序包括三次底涂、二次中涂和一次顶涂;涂饰均采用滚涂,滚涂温度101~105℃,各层涂料组成如下:
22.(a)底涂涂料重量份数配比:水性颜料膏0.7~2.5份、水32份以及阳离子油0.2~0.5份;
23.(b)中涂涂料重量份数配比:40~50℃水30份,消光聚氨酯20~70份,亮光聚氨酯7~18份,交联剂2~4份,可粉末化、自修复阻燃、低voc聚氨酯涂料6~8份,碳化二亚胺0.3~0.6份、成膜促进剂1.4~2.8份,0.1份的三羟甲基丙烷,乙烯基三甲氧基硅烷0.1~0.2份以及对苯二胺0.05份;
24.(c)顶涂涂料重量份数配比:水16份,防粘结材料1.6~2.1份、手感剂5~7份以及阳离子油0.2~0.3份。
25.顶涂涂料所用组分中的防粘结材料的制备方法为:三氟乙酰胺12份中加入1,2-苯二酚6~9份和水12份,于50~60℃下搅拌反应1~2h,烘干,再加入苯基磷酰二氯2.1~3.8份和苯13份,于60~65℃下搅拌反应1h,再将剩余苯蒸馏去除,剩余物烘干,得防粘结材料。
26.顶涂涂料所用组分中的成膜促进剂的制备方法为:将聚乙烯亚胺6g与2-乙酰氧基异丁酰氯8.2~9.4g,50~60℃下搅拌反应1~2h,再加入水杨酸1.1~1.4g,氨基脲1.1~2.3g,于50~70℃下反30~90min,得成膜促进剂。
27.本发明的积极效果在于:
28.(1)本发明采用聚四氢呋喃醚二醇和二异氰酸酯作为反应的催化剂,经过三乙胺封端处理后,采用纳米碳酸钙在4,4-二硝基二苯醚协效帮助下负载或者分散在水性聚氨酯,再将所得材料插层在蒙脱土的空间层状中,阻止了不同分子链状聚氨酯在紧密接触条件下,潜在聚合形成支化或者网状聚氨酯的可能性,为降低了后续的真空干燥后聚合反应发生的可能性,同时将固化聚氨酯与阻燃剂、自修复材料b分开存放,便于聚氨酯运输和性能稳定,固化聚氨酯在def和搅拌作用下基本恢复到原来的性质。
29.(2)以磷酸为酸源、季戊四醇为炭源,通过酯化反应合成出季戊四醇磷酸酯。其中,炭源是受热生成炭化物,形成炭质层的基础;酸源受热分解,生成物可以促进有机物脱水成炭。在此基础上添加pocl3以补充体系中的酸源,后添加乙醇胺作为气源,气源受热生成不燃、难燃气体,分布在炭层内,促使炭层发泡,拉远热源与基材的距离,降低燃烧时的传质、传热作用,以求达到更佳的阻燃性能,达到了氮、磷的协同作用;再采用硼酸为酸源,四羟甲基硫酸磷兼有酸源和碳源,在浓硫酸催化条件下,合成出笼状的含有羟基的化合物,采用3-氨丙基三乙氧基硅烷进行与笼状的含有羟基的化合物进行反应,引入硅基进入,所合成的中间体b既有笼状的刚性,又有乙氧基的侧链,提高了中间体的强度,同时也达到了硼、磷、硅的协调阻燃;再将阻燃中间体a和中间b进行反应,其中阻燃中间体a的羟基在受热中,会与硼上的羟基进行反应,将中间体a和中间体b反应接枝起来,反应所得产物分散在以c—c键、c—o—c键为主的等形式连接而成的聚酚类三维网状空间结构的木质素磺酸钠(济南盛世创富化工有限公司)上,使所得产物均匀分散,再采用丁酸酐与所得产物中未反应的羟基进行丁酸酐的开环,2,4-二羟基苯甲醛与开环所得羟基反应,体系中引入羧基和醛基,采用乙二胺四乙酸与体系的羟基进行反应,既引入了羧基,也增加了体系的刚性,再采用4-羧基苯硼酸、2-乙酰氧基异丁酰氯与体系的羟基、氨基(亚胺)进行反应,使所得阻燃剂有大量羟
基、羧基、醛基及亚胺基,便于后续的阻燃自修复,同时阻燃体系分散于木质素磺酸钠为构造体系的三维网状结构中,便于阻燃的构造出形成致密炭层,燃烧过程中释放的气体被包覆在致密炭层中,难以短时间释放出来,起到隔热的作用,同时本阻燃剂采用氮、磷、硅、硼的协同作用,发挥出现氮磷膨胀型阻燃剂难以达到的膨胀率和剩炭率高的优势。
30.(3)本发明利用聚氨酯和环氧树脂聚合物互相贯穿,而形成的交织网络聚合物,其中环氧树脂参与分散于聚氨酯大分子之间,交叉渗透、相互缠结,起到了相互贯穿、互相协同的作用。环氧树脂和聚氨酯互相缠结,使不同结构微细化,这种网络间的缠结能够明显地提高聚氨酯的分散性,改善聚氨酯的性质,尤其是在聚氨酯在环氧树脂e51(济南云佰汇生物科技有限公司)作用下,聚氨酯分子链和环氧树脂e51的分子链相互交错,同时利用三羟甲基丙烷三甲基丙烯酸酯、3,4'-二氨基联苯醚的支链多,空间位阻力大,使聚氨酯和环氧树脂的链状分布均匀而不缠结太紧密,便于其部分受损后,能够及时进行修复,同时由于n,n-二乙基甲酰胺def的相比丙酮、dmf对聚氨酯的分散性要差,采用三羟甲基丙烷三甲基丙烯酸酯、3,4'-二氨基联苯醚的分散性进行提高。
31.(4)在成膜过程中,为了加速聚氨酯的成膜,需要def、甲苯、水分子能够快速挥发或后续缓慢释放,本发明采用聚乙烯亚胺与2-乙酰氧基异丁酰氯进行反应。虽然聚乙烯亚胺是本领域的固化剂,但在聚氨酯制备方面效果不是特别理想,本发明采用聚乙烯亚胺的亚胺与2-乙酰氧基异丁酰氯的酰氯进行反应,再加入氨基脲与剩余酰氯反应,所得化合物在聚氨酯成膜过程中与聚氨酯的羟基和羧基进行反应,加速voc的释放。同时,氨基也可以与丙酮的羰基进行反应,尤其是在成膜进行加热的环境(如皮革涂层涂饰中需要在烘道内进行烘干),会提高聚氨酯的voc释放,本发明采用聚乙烯亚胺、2-乙酰氧基异丁酰氯和氨基脲的优势在于能够快速去除voc,三羟甲基丙烷是提高聚乙烯亚胺的交联,通过交联,也可对未释放的voc进行固定,乙烯基三甲氧基硅烷在40~50℃下水解,对阻燃剂和聚乙烯亚胺残留基团进行固定,而采用二苯胺是对乙烯基三甲基硅烷是进行反应,由于乙烯基三甲基氧基硅烷能增加交联后中涂的柔顺性,采用二苯胺是放置太柔顺,延伸性太强,并进一步提高汽车革的阻燃性。
32.(5)聚乙烯亚胺与2-乙酰氧基异丁酰氯的亚胺与酰氯反应,在引进水杨酸与氨基脲,提高聚氨酯的成膜性,提高其的耐磨耗性;三氟乙酰胺与1,2-苯二酚在水体系中进行反应,利用其中酰胺的氨基与酚羟基反应,再在苯体系中与苯基磷酰二氯进行改性反应,获得放置涂层黏连的防粘剂。
具体实施方式
33.下面结合实例进一步说明本发明。
34.实例一
35.一、可粉末化、自修复阻燃、低voc聚氨酯涂料按照以下步骤制备:
36.(1)在氮气保护的三口烧瓶中,加入聚四氢呋喃醚二醇18.6g(分子量为1000g/mol)、4,4'-二苯基甲烷二异氰酸酯11.8g,将体系温度升至70℃,并加入二月桂酸二丁基锡0.24g,搅拌反应2h,再加入2,2-二羟甲基丙酸0.4g,反应时间2h;降温至50℃,加入降稠剂n,n-二乙基甲酰胺def15ml;再降温至40℃,并加入三乙胺1.7g,反应时间0.5h,再加入膨润土7g、纳米碳酸钙1g和4,4-二硝基二苯醚1.6g,60℃下搅拌反应1h,得到粘稠液体;真空干
燥4h,磨碎,密封封存,得到可粉末化聚氨酯涂料a;
37.(2)自修复阻燃、低voc聚氨酯涂料b:往1.7g氮磷膨胀型阻燃剂中加入去离子水65ml、环氧树脂e51为12g、三羟甲基丙烷三甲基丙烯酸酯0.9g和3,4'-二氨基联苯醚1.4g,65℃下,搅拌反应60min,得自修复阻燃、低voc聚氨酯涂料b。
38.所述氮磷膨胀型阻燃剂的制备方法为:
39.(1)往三口烧瓶中加入季戊四醇27.2g、磷酸138.4g,室温搅拌30min,将体系温度升高至90℃,反应1h,即得季戊四醇磷酸酯;将季戊四醇磷酸酯降至室温,加入三氯氧磷20.8g,再将体系升温至45℃,保温搅拌30min,降至室温,于30min内滴加乙醇胺12.2g,继续反应1h,得阻燃剂中间体a;
40.(2)将硼酸6.2g、四羟甲基硫酸磷81.2g、浓硫酸0.98g,70℃下搅拌反应1h,再加入氢氧化钠溶液(质量分数20%,下同)调节ph调至6.0,再加入3-氨丙基三乙氧基硅烷2.5g(kh550)于反应容器中,于70℃下搅拌反应1h,即得中间体b;
41.(3)取步骤(1)的阻燃剂中间体a(全部)、步骤(2)的中间体b(全部)、木质素磺酸钠4.2g,于60℃下搅拌反应1h,再加入丁酸酐1.2g、2,4-二羟基苯甲醛0.6g,于70℃下反应1h,再加入乙二胺四乙酸0.5g、4-羧基苯硼酸0.2g、2-乙酰氧基异丁酰氯0.1g,于70℃反应2h,得氮磷膨胀型阻燃剂。
42.二、以下是应用例
43.挂晾、干燥、回潮:常规工艺;(海宁森德皮革有限公司的2021.06.15牛皮汽车坐垫革坐垫革皮胚依据工厂工艺进行挂晾、干燥、回潮)
44.涂饰工序包括依次进行的底涂、中涂和顶涂,涂饰均采用滚涂,滚涂温度101℃,底涂滚三次,中涂滚二次,顶涂滚一次,各层涂料如下:
45.(a)、底涂涂料重量份数配比:水性颜料膏neosan 2000(克莱恩化工有限公司)0.7份、水32份、阳离子油0.2份euderm oil kwo-c 0.4份(阳离子,朗盛化学);
46.(b)、中涂涂料重量份数配比:40℃水30份,消光聚氨酯matt 200(温州国仕邦高分子材料有限公司)20份,亮光聚氨酯hpv-c(美国氰特cyte份公司)7份,交联剂xl-701(美国斯塔尔)2份,可粉末化、自修复阻燃、低voc聚氨酯涂料6份,碳化二亚胺0.3份、成膜促进剂1.4份,三羟甲基丙烷0.1份,乙烯基三甲氧基硅烷0.1份,对苯二胺0.05份;
47.可粉末化、自修复阻燃、低voc聚氨酯涂料:其需将可粉末化聚氨酯涂料a100g、n,n-二乙基甲酰胺18g、自修复阻燃、低voc聚氨酯涂料b180g,40℃下搅拌反应1h,沉淀静置分层2h,让纳米碳酸钙和膨润土充分沉淀,得到滤液,得到可粉末化、自修复阻燃、低voc聚氨酯涂料;份可以等同g,也可根据比例适当调整,下同;
48.成膜促进剂的制备方法为:将聚乙烯亚胺6g与2-乙酰氧基异丁酰氯8.2g,50℃下搅拌反应1h,再加入水杨酸1.1g,氨基脲1.1g,于50℃下反应30min,得成膜促进剂。
49.(c)、顶涂涂料重量份数配比:水16份,防粘结材料1.6份、手感剂5份2229w(山东川泽商贸有限公司)和阳离子油euderm oil kwo-c(阳离子,朗盛化学)0.2份;
50.其中,防粘结材料的制备方法为:三氟乙酰胺12份中加入1,2-苯二酚6份和水12份,于50℃下搅拌反应1h,烘干,再加入苯基磷酰二氯2.1份和苯13份,于60℃下搅拌反应1h,再将剩余苯蒸馏去除,剩余物烘干即得该防粘结材料。
51.实例二
52.一、可粉末化、自修复阻燃、低voc聚氨酯涂料按照以下步骤制备:
53.(1)在氮气保护的反应容器中,加入聚四氢呋喃醚二醇18.6g、异佛尔酮二异氰酸酯11.8g,将体系温度升至80℃,并加入二月桂酸二丁基锡0.31g,搅拌反应4h,在体系中加入2,2-二羟甲基丁酸3.2g,反应时间3h;降温至70℃,加入降稠剂n,n-二乙基甲酰胺def30ml;再降温至40℃,并加入三乙胺2.5g,反应时间1h,再加入膨润土8g、纳米碳酸钙2g和4,4-二硝基二苯醚2.4g,70℃下搅拌反应2h,得到粘稠液体;真空干燥4h,磨碎,密封封存,得到可粉末化聚氨酯涂料a;
54.(2)自修复阻燃、低voc聚氨酯涂料b:往4.3g氮磷膨胀型阻燃剂中加入去离子水75ml、环氧树脂e51为17g、三羟甲基丙烷三甲基丙烯酸酯0.9g和3,4'-二氨基联苯醚1.4g,75℃下,搅拌反应90min,得自修复阻燃、低voc聚氨酯涂料b。
55.所述氮磷膨胀型阻燃剂的制备方法为:
56.(1)往三口烧瓶中加入季戊四醇27.2g、磷酸138.4g,室温搅拌60min,将体系温度升高至130℃,反应5h,即得季戊四醇磷酸酯;将季戊四醇磷酸酯降至室温,加入三氯氧磷20.8g,再将体系升温至50℃,保温搅拌60min,降至室温,于60min内滴加乙醇胺12.2g,继续反应2h,得阻燃剂中间体a;
57.(2)将硼酸8.4g、四羟甲基硫酸磷81.2g、浓硫酸0.98g,90℃下搅拌反应3h,再加入氢氧化钠溶液调节ph调至6.0,再加入3-氨丙基三乙氧基硅烷3.6g(kh550)于反应容器中,于110℃下搅拌反应7h,既得中间体b;
58.(3)取步骤(1)的阻燃剂中间体a(全部)、步骤(2)的中间体b(全部)、木质素磺酸钠8.6g,于70℃下搅拌反应2h,再加入丁酸酐1.7g、2,4-二羟基苯甲醛1.2g,于80℃下反应3h,再加入乙二胺四乙酸1.2g、4-羧基苯硼酸0.4g、2-乙酰氧基异丁酰氯0.4g,于80℃反应3h,得氮磷膨胀型阻燃剂。
59.二、以下是应用例
60.(海宁森德皮革有限公司的2021.06.15牛皮汽车坐垫革坐垫革皮胚依据海宁森德皮革有限公司工艺进行挂晾、干燥、回潮,也属于本领域常规工艺)
61.涂饰工序包括依次进行的底涂、中涂和顶涂,涂饰均采用滚涂,滚涂温度105℃,底涂滚三次,中涂滚二次,顶涂滚一次,各层涂料如下:
62.(a)、底涂涂料重量份数配比:水性颜料膏neosan 2000(克莱恩化工有限公司)2.5份、水32份、阳离子油euderm oil kwo-c(阳离子,朗盛化学)0.5份;
63.(b)、中涂涂料重量份数配比:50℃水30份,消光聚氨酯matt 200(温州国仕邦高分子材料有限公司)70份,亮光聚氨酯hpv-c(美国氰特cyte份公司)18份,交联剂xl-701(美国斯塔尔)4份,可粉末化、自修复阻燃、低voc聚氨酯涂料8份,碳化二亚胺0.6份、成膜促进剂2.8份,0.1份的三羟甲基丙烷,乙烯基三甲氧基硅烷0.2份,对苯二胺0.05份;
64.可粉末化、自修复阻燃、低voc聚氨酯涂料:其需将可粉末化聚氨酯涂料a100g、n,n-二乙基甲酰胺25g、自修复阻燃、低voc聚氨酯涂料b200g,50℃下搅拌反应2h,沉淀静置分层2h,让纳米碳酸钙和膨润土充分沉淀,得到滤液,得到可粉末化、自修复阻燃、低voc聚氨酯涂料;份可以等同g,也可根据比例适当调整,下同;
65.(c)、顶涂涂料重量份数配比:水16份,防粘结材料2.1份、手感剂2229w(山东川泽商贸有限公司)7份和阳离子油的euderm oil kwo-c(阳离子,朗盛化学)0.3份;
66.其中,防粘结材料的制备方法为:三氟乙酰胺12份中加入1,2-苯二酚9份和水12份,于60℃下搅拌反应2h,烘干,再加入苯基磷酰二氯3.8份和苯13份,于65℃下搅拌反应1h,再将剩余苯蒸馏去除,剩余物烘干即得该防粘结材料。
67.成膜促进剂的制备方法为:将聚乙烯亚胺6g与2-乙酰氧基异丁酰氯9.4g,60℃下搅拌反应2h,再加入水杨酸1.4g,再加入氨基脲2.3g,于70℃下反应90min,得成膜促进剂。
68.实例三
69.一、可粉末化、自修复阻燃、低voc聚氨酯涂料按照以下步骤制备:
70.(1)在氮气保护的反应容器中,加入聚四氢呋喃醚二醇18.6g、甲苯二异氰酸酯11.8g,将体系温度升至75℃,并加入二月桂酸二丁基锡0.27g,搅拌反应3h,在体系中加入2,2-二羟甲基丙酸1.8g,反应时间2.5h;降温至60℃,加入降稠剂n,n-二乙基甲酰胺def22.5ml;再降温至40℃,并加入三乙胺2.1g,反应时间45min,再加入膨润土7.5g、纳米碳酸钙1.5g和4,4-二硝基二苯醚2.0g,65℃下搅拌反应1.5h,得到粘稠液体;真空干燥4h,磨碎,密封封存,得到可粉末化聚氨酯涂料a;
71.(2)自修复阻燃、低voc聚氨酯涂料b:将3.0g氮磷膨胀型阻燃剂中加入去离子水70ml、环氧树脂e51为14.5g、三羟甲基丙烷三甲基丙烯酸酯0.9g和3,4'-二氨基联苯醚1.4g,70℃下,搅拌反应75min,得自修复阻燃、低voc聚氨酯涂料b。
72.所述氮磷膨胀型阻燃剂的制备方法为:
73.(1)往三口烧瓶中加入季戊四醇27.2g、磷酸138.4g,室温搅拌45min,将体系温度升高至110℃,反应3h,即得季戊四醇磷酸酯;将季戊四醇磷酸酯降至室温,加入三氯氧磷20.8g,再将体系升温至45℃,保温搅拌45min,降至室温,于45min内滴加乙醇胺12.2g,继续反应1.5h,得阻燃剂中间体a;
74.(2)将硼酸7.3g、四羟甲基硫酸磷81.2g、浓硫酸0.98g,80℃下搅拌反应2h,再加入氢氧化钠溶液调节ph调至6.0,再加入3-氨丙基三乙氧基硅烷3.0g(kh550)于反应容器中,于90℃下搅拌反应4h,既得中间体b;
75.(3)取步骤(1)的阻燃剂中间体a(全部)、步骤(2)的中间体b(全部)、木质素磺酸钠6.4g,于65℃下搅拌反应1.5h,再加入丁酸酐1.45g、2,4-二羟基苯甲醛0.9g,于75℃下反应2h,再加入乙二胺四乙酸0.8g、4-羧基苯硼酸0.3g、2-乙酰氧基异丁酰氯0.25g,于75℃反应2.5h,得氮磷膨胀型阻燃剂。
76.二、以下是应用例
77.涂饰工序包括依次进行的底涂、中涂和顶涂,涂饰均采用滚涂,滚涂温度103℃,底涂滚三次,中涂滚二次,顶涂滚一次,各层涂料如下:
78.(a)、底涂涂料重量份数配比:水性颜料膏neosan 2000(克莱恩化工有限公司)1.6份、水32份、阳离子油euderm oil kwo-c(阳离子,朗盛化学)0.35份;
79.(b)、中涂涂料重量份数配比:45℃水30份,消光聚氨酯matt 200(温州国仕邦高分子材料有限公司)45份,亮光聚氨酯hpv-c(美国氰特cyte份公司)12.5份,交联剂xl-701(美国斯塔尔)3份,可粉末化、自修复阻燃、低voc聚氨酯涂料7份,碳化二亚胺0.45份、成膜促进剂2.1份,0.1份的三羟甲基丙烷,乙烯基三甲氧基硅烷0.15份,对苯二胺0.05份;
80.可粉末化、自修复阻燃、低voc聚氨酯涂料:其需将可粉末化聚氨酯涂料a100g、n,n-二乙基甲酰胺22g、自修复阻燃、低voc聚氨酯涂料b190g,45℃下搅拌反应1.5h,沉淀静置
分层2h,让纳米碳酸钙和膨润土充分沉淀,得到滤液,得到可粉末化、自修复阻燃、低voc聚氨酯涂料;份可以等同g,也可根据比例适当调整,下同;
81.成膜促进剂的制备方法为:将聚乙烯亚胺6g与2-乙酰氧基异丁酰氯8.7g,55℃下搅拌反应1.5h,再加入水杨酸1.25g,再加入氨基脲1.7g,于60℃下反应60min,得成膜促进剂。
82.(c)、顶涂涂料重量份数配比:水16份,防粘结材料1.8份、手感剂2229w(山东川泽商贸有限公司)6份和阳离子油的euderm oil kwo-c(阳离子,朗盛化学)0.25份;
83.其中,防粘结材料的制备方法为:三氟乙酰胺12份中加入1,2-苯二酚7.5份和水12份,于55℃下搅拌反应1.5h,烘干,再加入苯基磷酰二氯3.0份和苯13份,于60℃下搅拌反应1h,再将剩余苯蒸馏去除,剩余物烘干即得该防粘结材料。
84.聚氨酯膜的性能测试:
85.gb/t5455-1997纺织品燃烧性能试验垂直法测定聚氨酯涂料所成膜的有焰燃烧时间(续燃时间),试样长20cm乘以10cm,厚度1mm。
86.voc测定方法:金属平底皿在105
±
2℃烘箱中烘30min,然后放在干燥器中至使用。聚氨酯混合后,平铺于金属平底皿,在温度23
±
2℃、湿度50
±
5%条件下放置24h,再在105
±
2℃烘箱中烘60min,平行做两份试验。称量加热之前m1(金属容器m0和反应物质量之和)和加热之后的质量m2(见201710902448.6);
87.表1 聚氨酯涂料固化(步骤1聚氨酯的制备)
[0088][0089][0090]
从表1(可粉末化聚氨酯涂料a)可以发现,经过聚氨酯处理的材料其可以进行固化,固化情况是通过实验现象进行观察而定,固化根据视觉看。
[0091]
表2 聚氨酯涂料固化(步骤1聚氨酯的制备)
[0092][0093]
未加膨润土、纳米碳酸钙和4,4-二硝基二苯醚是建立在步骤(1)可粉末化聚氨酯涂料a的工艺中(取固化聚氨酯8g来计算对应常温所需的def量),是在其中加入def(进行搅拌)进行固体溶解而得到的实验数据,固化效果根据溶剂的恢复量来定。
[0094]
对比例的工艺:在氮气保护的反应容器中,加入聚四氢呋喃醚二醇18.6g、甲苯二异氰酸酯11.8g,将体系温度升至75℃,并加入二月桂酸二丁基锡0.27g,搅拌反应3h,在体
系中加入2,2-二羟甲基丙酸1.8g,反应时间2.5h;降温至60℃,加入降稠剂n,n-二乙基甲酰胺def22.5ml;再降温至40℃,并加入三乙胺2.1g,反应时间0.5h,真空干燥,磨碎,密封封存。
[0095]
本发明实施例涉及到的未指定厂家的的化工材料,可以使用辉鹰兴业皮革有限公司同类产品进行替换,湿热稳定性参考gbt 4689.8-1984,qb/t 3812.5-1999测定抗张强度和最大断裂伸长率,干摩擦色牢度、湿摩擦色牢度、涂层粘着牢度、皮革雾化性能、皮革耐磨性能、耐光性能、参见俞从正丁绍兰和孙根行(皮革分析检验技术,2005年6月出版);干热收缩温度参见刘捷,汤克勇,期刊中国皮革,2001年9月,氧指数,垂直燃烧法、烟密度可以参考段宝荣系列发表学术论文或者(段宝荣等,磷系阻燃剂对皮革阻燃性能的影响【j】,中国皮革,2012年8月;ts-int-002-2008车用材料及零部件总碳散发测定方法),其他如标准不清,或者没有写明,请参考轻工标准或者汽车的检测方法进行测试,也可参考皮革分析检验技术,2005年6月出版。
[0096]
皮革自修复阻燃测试:1切的自修复取测试样品厚度1.2cm,长度每1cm处用刀片切深度0.02cm,对切口进行染色,在80℃(烘箱)下烘1h,达到修复效果后测试(简称“切”)。
[0097]
2磨损自修复:取测试样品厚度1.2cm,耐磨耗性能按gb/t22374-2018,100g/100r,50次磨损,其他不改变进行,在80℃(烘箱)下烘1h,达到修复效果后测试(简称“磨”)。
[0098]
分别对按照本发明实施例制备的可粉末化、自修复阻燃、低voc聚氨酯涂料及应用汽车革和现有同类汽车坐垫革进行检测,检测数据如表1。
[0099]
表3 汽车坐垫革制造工艺测试数据
[0100][0101]
对比文件采用202011643278的实例,其中voc以超低总碳散发来进行表示,涂层相互不粘着性是采用3名熟练涂饰工程师各从100张牛皮坐垫革中确定皮粒面粘着的几率,求其不粘着几率的平均值,对比文件的涂层相互不粘着性是本团队前期测量数据。
[0102]
表4 未加部分化工材料的汽车坐垫革测试数据(以实例二为例)
[0103]
[0104][0105]
从表4可以看出,未加成膜促进剂、三羟甲基丙烷、乙烯基三甲氧基硅烷、对苯二胺、氮磷膨胀型阻燃剂,其耐磨耗、涂层相互不粘着性、超低总碳散发、氧指数和烟密度性能均低于加入上述材料的汽车革性质。
[0106]
表5 汽车坐垫革自修复能力测试数据(以实例二为例)
[0107][0108]
从表5可以发现,对本发明以实例二为例的在切、磨条件下,相比较没有切或者磨条件下,氧指数下降比较大,而经过修复后,其氧指数比对比文件修复的要好得多,显示本发明具有自修复能力。
[0109]
表6 未加入部分材料的汽车坐垫革自修复能力测试数据(以实例二为例)
[0110][0111]
未加入环氧树脂e51、三羟甲基丙烷三甲基丙烯酸酯的切、磨自修复能力均比加入上述材料下降幅度5~8%之间(以自修复为基准,来计算变化幅度的百分比,下同),显示环
氧树脂e51、三羟甲基丙烷三甲基丙烯酸酯确实可以提高材料的自修复能力,同理也发现,未加入丁酸酐、2,4-二羟基苯甲醛在切、磨阻燃性(氧指数下降幅度)比经过修复氧指数下滑2.3~3.5%,显示丁酸酐、2,4-二羟基苯甲醛在切、磨修复中也发挥了作用。