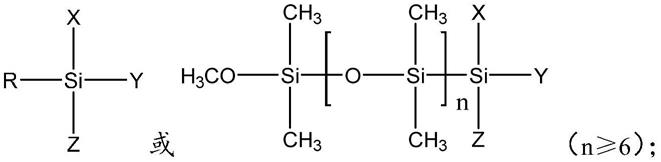
1.本发明属于导热材料领域,具体涉及导热填料及其表面处理方法。
背景技术:
2.聚合物热界面材料是指在在聚合物中填充导热粉体,使得导热粉体在聚合物中可以起到热传导的作用,从而可以提升聚合物热界面材料的导热性能。一般来说,聚合物中填充的导热粉体含量越多,聚合物的导热系数越高。为了提升导热粉体的填充量,需要对导热粉体进行表面处理,从而提升导热粉体和聚合物的相容性,另外还可以降低体系的界面热阻。
3.目前,对于导热粉体的表面处理方法有很多,但是仍然存在一些问题:表面处理不完全、处理工艺不稳定以及表面处理剂过量导致固化过程中蒸发造成聚合物热界面材料产生空隙等。这些问题使得聚合物热界面材料的性能难以满足实际需求。低沸点的表面处理剂对导热填料进行表面处理时,未反应的表面处理剂很难除去,就会游离在体系中。其在固化或使用过程中容易挥发,使得聚合物热界面材料产生空隙的风险,从而影响聚合物界面材料的导热性能及其他性能。高沸点的表面处理剂虽然很难挥发,但是采用高沸点的表面处理剂完全代替低沸点的表面处理剂,可以降低聚合物热界面材料产生空隙的风险。然而,高沸点的表面处理剂的分子量较高,会使得体系的粘度和储能模量增加从而影响材料的性能以及粘合线厚度(blt)。其次,目前市场上采用的大多为单一的表面处理剂进行处理,很难对导热填料进行完全包覆。另外,虽然也有部分采用多种表面处理剂,但是往往存在处理工艺不稳定、处理效果不理想或存在上述问题等;传统的导热填料进行表面处理时如果想要处理的较为彻底,往往需要复杂的处理工艺以及大量的能耗,因此成本较高。
技术实现要素:
4.针对现有处理工艺不稳定或处理效果不理想的问题,本发明的导热填料的表面处理方法能够使用简单工艺,表面处理剂易得、生产成本较低、处理效果好以及操作工艺稳定。
5.本发明在一方面提供一种导热填料的表面处理方法,所述表面处理方法包括以下步骤:(1)加入第一表面处理剂处理导热填料,其中所述第一表面处理剂的沸点低于160℃;(2)然后加入第二表面处理剂,其中所述第二表面处理剂的沸点高于210℃。该导热填料的表面处理方法可以降低低沸点表面处理剂的挥发,从而降低聚合物热界面材料产生空隙的风险,避免导热填料颗粒被氧化,降低体系的粘度和储能模量,还可以改善聚合物热界面材料与基材之间的润湿性,从而降低界面热阻,从而更好的发挥聚合物热界面材料的效果,处理工艺相对简单、表面处理剂易得、生产成本较低、处理效果好以及操作工艺稳定。
6.在一些实施方式中,所述第一导热填料选自铝、银、铜、氮化铝、氧化铝、氧化锌、氮化硼、氮化铝、碳纤维中的至少一种。
7.在一些实施方式中,所述导热填料的最大粒径为80μm;所述导热填料的平均粒径
为5~20μm,优选8~15μm;在一些实施方式中,所述导热填料优选为氧化铝。在一些实施方式中,所述氧化铝为球形氧化铝。在一些实施方式中,所述球形氧化铝包括中位粒径20μm的球形氧化铝和中位粒径2μm的球形氧化铝,其中该中位粒径20μm的球形氧化铝和中位粒径2μm的球形氧化铝的质量比为3:2。在一些实施方式中,所述球形氧化铝包括中位粒径20μm的球形氧化铝和中位粒径5μm的球形氧化铝;其中该中位粒径20μm的球形氧化铝和中位粒径5μm的球形氧化铝的质量比为1:1。在一些实施方式中,所述球形氧化铝包括中位粒径20μm的球形氧化铝和中位粒径2μm的球形氧化铝,其中所述中位粒径20μm的球形氧化铝和中位粒径2μm的球形氧化铝的质量比为3:2。该导热填料的表面处理方法可以降低低沸点表面处理剂的挥发,从而降低聚合物热界面材料产生空隙的风险,避免导热填料颗粒被氧化,降低体系的粘度和储能模量,还可以改善聚合物热界面材料与基材之间的润湿性,从而降低界面热阻,从而更好的发挥聚合物热界面材料的效果,处理工艺相对简单、表面处理剂易得、生产成本较低、处理效果好以及操作工艺稳定。
8.在一些实施方式中,所述第一表面处理剂选自γ
‑
缩水甘油醚氧丙基三甲氧基硅烷、乙烯基三甲氧基硅烷、甲基三甲氧基硅烷和乙基三甲氧基硅烷中的至少一种。
9.在一些实施方式中,所述第二表面处理剂选自:
10.其中,
11.r为6个碳以上的烷基,x、y、z独立地是可水解的基团。在一些实施方式中,所述烷基为己基、苯基或十二烷基。在一些实施方式中,所述可水解的基团为烷氧基或氯基。
12.在一些实施方式中,所述表面处理方法为湿法或干法。
13.在一些实施方式中,所述表面处理方法为湿法,在所述湿法中加入溶剂与所述导热填料的体积比为10:1~2:1。在一些实施方式中,所述溶剂为有机溶剂,所述有机溶剂选自甲醇、乙醇、异丙醇、甲苯、二甲苯、丙酮。
14.在一些实施方式中,所述第一表面处理剂的用量为导热填料重量的1%~0.01%。在一些实施方式中,所述第一表面处理剂的用量为所述导热填料重量优选为0.6%~0.1%。
15.在一些实施方式中,所述第二表面处理剂的用量为导热填料重量的1%~0.01%。在一些实施方式中,所述第一表面处理剂的用量为所述导热填料重量优选为0.6%~0.1%。
16.本发明再一方面提供一种导热填料,所述导热填料由任一种上述表面处理方法所述的表面处理方法进行制备。在一些实施方式中,所述导热填料的吸油值<10.5g/100g。在一些实施方式中,8g/100g<所述导热填料的吸油值<9.5g/100g。在一些实施方式中,所述导热填料的粘度<25000mpa
·
s。在一些实施方式中,所述导热填料的粘度<20000mpa
·
s。该导热填料降低聚合物热界面材料产生空隙的风险,避免导热填料颗粒被氧化,降低体系的粘度和储能模量,还可以改善聚合物热界面材料与基材之间的润湿性,从而降低界面热阻,从而更好的发挥聚合物热界面材料的效果,处理工艺相对简单、表面处理剂易得、生产成本较
低、处理效果好以及操作工艺稳定。
17.本发明再一方面提供一种导热填料组合物,所述组合物包括:导热填料;第一表面处理剂,所述第一表面处理剂的处理导热填料,其中所述第一表面处理剂的沸点低于160℃,所述第一表面处理剂的用量为导热填料重量的1%~0.01%;第二表面处理剂,所述第二表面处理剂的沸点高于210℃,所述第二表面处理剂的用量为导热填料重量的1%~0.01%。在一些实施方式中,所述导热填料为球形氧化铝。在一些实施方式中,所述第一表面处理剂的用量为所述导热填料重量优选为0.6%~0.1%。在一些实施方式中,所述第一表面处理剂的用量为所述导热填料重量优选为0.6%~0.1%。
18.本发明导热填料的表面处理方法和导热填料,能够提供以下优势中的至少一个:
19.(1)通过控制低沸点的表面处理剂的用量(可以通过经验公式进行计算),则可以使得绝大部分甚至全部被用来包覆导热填料颗粒,因此可以降低低沸点表面处理剂的挥发,从而降低聚合物热界面材料产生空隙的风险。
20.(2)通过多组分表面处理体系对导热填料进行包覆,可以使得导热填料颗粒可以更好的分散在聚合物基体中,并且可以避免导热填料颗粒被氧化。
21.(3)较少量的低沸点表面处理剂或者过多的高沸点表面处理剂游离在体系中,可以降低体系的粘度和储能模量,还可以改善聚合物热界面材料与基材之间的润湿性,从而降低界面热阻,从而更好的发挥聚合物热界面材料的效果。
22.(4)本发明采用的导热填料的处理方法较传统的处理方法,处理工艺相对简单、表面处理剂易得、生产成本较低、处理效果好以及操作工艺稳定等。
具体实施方式
23.实施例1
24.将称量好的导热填料(中位粒径20μm的球形氧化铝60份,中位粒径2μm的球形氧化铝40份)置于改性处理的分散设备中,加入异丙醇(溶剂和导热填料的体积比为3:1),搅拌分散(转速为500rpm,时间为5min),滴加γ
‑
缩水甘油醚氧丙基三甲氧基硅烷(2min加完,以导热填料为100份计,添加量为0.2份),滴加完后提升转速到1000rpm,搅拌10min;降低搅拌转速到500rpm,然后滴加十二烷基三甲氧基硅烷(2min加完,以导热填料为100份计,添加量为0.6份),滴加完后提升转速到1000rpm,搅拌10min,出料后在120℃下烘干。
25.实施例2
26.将称量好的导热填料(中位粒径20μm的球形氧化铝50份,中位粒径5μm的球形氧化铝50份)置于改性处理的设备中,加入异丙醇(溶剂和导热填料的体积比为3:1),搅拌分散(转速为500rpm,时间为5min),滴加乙烯基三甲氧基硅烷(2min加完,以导热填料为100份计,添加量为0.3份),滴加完后提升转速到1000rpm,搅拌10min;降低搅拌转速到600rpm,然后滴加十烷基三甲氧基硅烷(3min加完,以导热填料为100份计,添加量为0.5份),滴加完后提升转速到1200rpm,搅拌10min,出料后在120℃下烘干。
27.实施例3
28.将称量好的导热填料(中位粒径20μm的球形氧化铝60份,中位粒径2μm的球形氧化铝40份)置于改性处理的分散设备中,加入异丙醇(溶剂和导热填料的体积比为3:1),搅拌分散(转速为600rpm,时间为6min),滴加乙基三甲氧基硅烷(2min加完,以导热填料为100份
计,添加量为0.3份),滴加完后提升转速到1200rpm,搅拌12min;降低搅拌转速到600rpm,然后滴加辛基三甲氧基硅烷(2min加完,以导热填料为100份计,添加量为0.5份),滴加完后提升转速到1200rpm,搅拌12min,出料后在120℃下烘干。
29.实施例4
30.将称量好的导热填料(中位粒径20μm的球形氧化铝50份,中位粒径5μm的球形氧化铝50份)置于改性处理的设备中,搅拌分散(转速为800rpm,时间为8min),滴加甲基三甲氧基硅烷(2min加完,以导热填料为100份计,添加量为0.2份),滴加完后提升转速到1500rpm,搅拌20min;降低搅拌转速到800rpm,然后滴加十六烷基三甲氧基硅烷(2min加完,以导热填料为100份计,添加量为0.2份),滴加完后提升转速到1200rpm,搅拌12min,完成导热填料的改性处理过程。
31.对比例1
32.将称量好的导热填料(中位粒径20μm的球形氧化铝60份,中位粒径2μm的球形氧化铝40份)置于改性处理的分散设备中,加入异丙醇(溶剂和导热填料的体积比为3:1),搅拌分散(转速为500rpm,时间为5min),滴加γ
‑
缩水甘油醚氧丙基三甲氧基硅烷(4min加完,以导热填料为100份计,添加量为0.8份),滴加完后提升转速到1000rpm,搅拌20min,出料后在120℃下烘干。
33.对比例2
34.将称量好的导热填料(中位粒径20μm的球形氧化铝60份,中位粒径2μm的球形氧化铝40份)置于改性处理的分散设备中,加入异丙醇(溶剂和导热填料的体积比为3:1),搅拌分散(转速为500rpm,时间为5min),滴加十二烷基三甲氧基硅烷(4min加完,以导热填料为100份计,添加量为0.8份),滴加完后提升转速到1000rpm,搅拌20min,出料后在120℃下烘干。
35.性能测试
36.将上述实施例和对比例处理的导热填料,以下组份按质量份数比例,将100份粘度为500m pa
·
s的乙烯基硅油,加入700份处理过的导热填料中,搅拌混合均匀,用于测试粘度;然后加入0.06份50%的3
‑
甲基
‑2‑
丁炔醇、0.7份0.1%的含氢硅油和0.6份0.3%的含氢硅油,最后加入0.3份5000ppm的铂金催化剂,搅拌均匀脱泡,然后放在模具中,在150℃条件下硫化成型制得导热硅胶片,用于测试导热系数和硬度以及观察断面孔洞。
37.性能参数测试:
38.(1)导热系数:按照astm
‑
d5470测试样品的导热系数。
39.(2)硬度:按照gb/t 531.1—2008测试样品的硬度。
40.(3)吸油值:取5g导热填料样品,置于瓷板中,然后用微量滴定管滴加邻苯二甲酸二辛酯(dop),同时用刮刀不断翻动研磨,开始呈现分散状态,后逐渐被dop所润湿,确定dop的用量。按照以下公式来计算:
41.吸油值=(m1/m)
×
100
42.其中,m1为消耗dop的质量,g
43.m为氧化铝的质量,g
44.(4)粘度:按照gb/t 2794—2013测试样品的粘度。
45.(5)断面孔洞:通过在液氮中脆断固化好的样片,在显微镜下观察是否存在孔洞。
46.测试结果:
[0047][0048]
通过对比例1、对比例2与实施例1的对比可以看出,通过单一的高低沸点的表面处理剂进行导热填料的表面处理,它们的吸油值和粘度都较高,同时导热系数都较低。对比例1中通过单一的低沸点表面处理剂进行导热填料的处理,其会产生断面孔洞;对比例2中通过单一的高沸点表面处理剂进行导热填料的处理,其硬度偏高,样品的模量偏高,影响使用过程中的粘合线厚度(blt)。与之相对地,通过本发明方法制备的导热填料具有显著更低的体系粘度,具有更优的材料性能。
[0049]
最后所应当说明的是,以上实施例仅用以说明本发明的技术方案而非对本发明保护范围的限制,尽管参照较佳实施例对本发明作了详细说明,本领域的普通技术人员应当理解,可以对本发明的技术方案进行修改或者等同替换,而不脱离本发明技术方案的实质和范围。