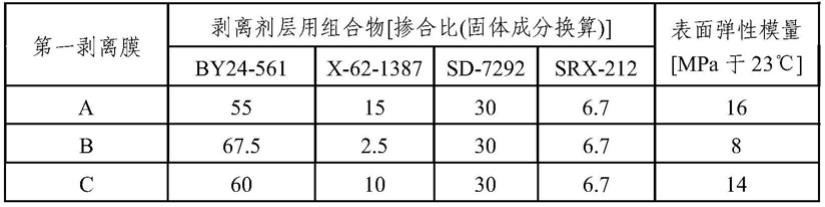
1.本发明涉及一种保护膜形成用片及其制造方法。特别涉及一种具备适合使用于保护半导体晶圆等工件或加工工件而得到的半导体芯片等加工品的保护膜形成膜的保护膜形成用片、以及该保护膜形成用片的制造方法。
背景技术:
2.近年来,通过被称作倒装芯片键合的安装法制造半导体装置。在该安装法中,在安装具有形成有凸点(bump)等凸状电极的电路面的半导体芯片时,使半导体芯片的电路面侧反转(面朝下(face down))键合在芯片搭载部。因此,半导体装置具有半导体芯片的未形成电路的背面侧露出的结构。
3.因此,为了在搬运时等的冲击下保护半导体芯片,多数情况下会在半导体芯片的背面侧形成由有机材料形成的硬质保护膜。为了形成这种保护膜,使用有作为其前驱体的未固化的树脂膜(以下称为“保护膜形成膜”)。保护膜形成膜贴附在半导体晶圆的背面,并与晶圆一同被切割而芯片化。通过使保护膜形成膜固化,可得到在背面具有保护膜的芯片。
4.作为保护膜形成膜的产品形态,已知有如图1所示在第一剥离膜12上以可剥离的方式层叠有保护膜形成膜11的双层结构的保护膜形成用片10、或者如图3所示在两片剥离膜(12、13)之间挟持有保护膜形成膜11的三层结构的保护膜形成用片20。此外,上述保护膜形成用片为长条且被卷绕成卷状进行保管、运输。这种保护膜形成用片有时也会将保护膜形成膜预先冲孔加工为与工件(半导体晶圆等被粘物的总称)大致相同的形状而贴附在工件上。这种经过冲孔加工的保护膜形成用片将冲孔加工为规定的封闭形状的保护膜形成膜16层叠在第一剥离膜12上(图2),或将其夹持在两片剥离膜(12、13)之间(图4)。
5.经过冲孔加工的保护膜形成用片通过利用冲模将保护膜形成膜冲裁为规定的封闭形状而制造,并以去除经过冲孔加工的保护膜形成膜16的周边的无用部分17的方式而使用。在为由保护膜形成膜11与第一剥离膜12构成的双层结构的保护膜形成用片时,以将保护膜形成膜11完全冲裁为规定的封闭形状且不完全冲裁第一剥离膜12的方式切出切口14,并使规定的封闭形状的保护膜形成膜16残留在第一剥离膜12上,去除周边的无用部分17。在为保护膜形成膜11夹持在两片剥离膜(12、13)之间的三层结构的保护膜形成用片时,以将保护膜形成膜11与一侧的第二剥离膜13完全冲裁为规定的封闭形状且不完全冲裁另一侧的第一剥离膜12的方式切出切口14,并使规定的封闭形状的保护膜形成膜16残留在第一剥离膜12上,去除周边的无用部分17与第二剥离膜13。
6.以双层结构的保护膜形成用片的情况为例进一步进行详细说明。如图5所示,对由保护膜形成膜11与第一剥离膜12构成的保护形成用片10,以将保护膜形成膜11完全冲裁为规定的封闭形状且不完全冲裁第一剥离膜12的方式切出切口14,制成经过冲孔加工的保护膜形成用片。该工序被称为“冲孔加工工序”。
7.然后,为了用于将经过冲孔加工的保护膜形成用片贴附在工件上,去除冲裁为规定的封闭形状的保护膜形成膜16的周边的无用部分17(图6)。该工序被称为“废料去除工
序”。结果可得到具有能够用于贴附在工件上的、在第一剥离膜12上被冲裁为规定的封闭形状的保护膜形成膜16的层叠体。
8.在为三层结构的保护膜形成用片时,除了在冲孔加工工序中在保护膜形成膜11上具有另一个剥离膜13(第二剥离膜13),且第二剥离膜13也被完全冲裁为规定的封闭形状,以及在废料去除工序中去除第二剥离膜13以外,与双层结构的保护膜形成用片的情况相同。
9.作为保护膜形成用片,要求能够稳定地进行冲孔加工工序(操作稳定性)。特别是在对保护膜形成膜进行冲孔加工之后,要求去除无用部分的废料去除工序的操作稳定性。更具体而言,在废料去除工序中,要求不产生应残留的保护膜形成膜16意外地与无用部分17一同从第一剥离膜12上剥离的问题(以下,称为“废料去除的不良”)。
10.为了解决上述问题,例如,专利文献1提出了将剥离膜与保护膜形成膜之间的剥离力控制在规定范围。现有技术文献专利文献
11.专利文献1:国际公开wo2017/145735
技术实现要素:
本发明要解决的技术问题
12.若发生废料去除的不良,则需要停止生产线并废弃不良品,产品的生产率下降,成本增大。因此,要求进一步抑制废料去除的不良。
13.本发明的发明人进一步不懈研究废料去除不良的原因,得到了以下见解。
14.在冲孔加工工序之后至废料去除工序之前,以控制保护膜形成用片的张力等为目的,保护膜形成用片10会通过导辊等多个辊。此时,如图7所示,保护膜形成用片10有时会以切口14的上部侧(冲模所进入的一侧的面)为辊19侧的方式弯曲。弯曲结果会导致在特别是与片10的短边方向几乎平行的切口部分,切口14的宽度变窄,同时保护膜形成膜16被挤压而发生少许变形,这作为部分原因有时会导致邻接的保护膜形成膜16与无用部分17发生接触、附着。
15.在通过辊19后,多数情况下保护膜形成膜16与无用部分17的附着部会再度分离,但有时也会不分离而维持附着。若以保护膜形成膜16与无用部分17附着的状态进行废料去除,则应残留在第一剥离膜12上的保护膜形成膜16会意外地与应去除的无用部分17一同从第一剥离膜12上剥离,发生废料去除的不良。
16.本发明鉴于上述实际请况而成,其目的在于提供一种即使在冲孔加工时的切口宽度较窄的情况下也能够充分抑制废料去除的不良的保护膜形成用片及其制造方法。解决技术问题的技术手段
17.本发明的方案如下所述。(1)一种保护膜形成用片,其为长条片,并具有保护膜形成膜和设置在所述保护膜形成膜的一个面上的第一剥离膜,其中,于23℃用2kgf的载荷将两片保护膜形成膜贴附2分钟后的附着力为19n/25mm以下。
(2)根据(1)所述的保护膜形成用片,其中,所述第一剥离膜的与保护膜形成膜相接的面的表面弹性模量为17mpa以下。(3)根据(1)或(2)所述的保护膜形成用片,其中,在所述保护膜形成用片上,以在俯视所述保护膜形成用片时保护膜形成用片的一部分具有规定的封闭形状的方式形成有切口,所述切口在所述保护膜形成用片的厚度方向贯穿所述保护膜形成膜并到达至所述第一剥离膜的一部分。(4)根据(3)所述的保护膜形成用片,其中,所述保护膜形成膜与所述第一剥离膜的界面上的所述切口的宽度为8μm以上。(5)一种经过冲孔加工的保护膜形成用片的制造方法,其具有以使上述(1)或(2)所述的保护膜形成用片的一部分具有规定的封闭形状的方式形成切口的工序,所述切口在所述保护膜形成用片的厚度方向贯穿所述保护膜形成膜并到达至所述第一剥离膜的一部分。(6)根据(5)所述的经过冲孔加工的保护膜形成用片的制造方法,其中,所述保护膜形成膜与所述第一剥离膜的界面上的所述切口的宽度为8μm以上。发明效果
18.根据本发明,可提供一种即使在冲孔加工时的切口宽度较窄的情况下也能够充分抑制废料去除的不良的保护膜形成用片及其制造方法。
附图说明
19.图1为实施方案的保护膜形成用片的剖面示意图图2为示出对实施方案的保护膜形成用片进行冲孔加工后的状态的剖面示意图。图3为另一个实施方案的保护膜形成用片的剖面示意图。图4为示出对另一个实施方案的保护膜形成用片进行冲孔加工后的状态的剖面示意图。图5为冲孔加工工序后的保护膜形成用片的概略透视图。图6为表示废料去除工序的概略透视图。图7为示出冲孔加工工序后的保护膜形成用片通过辊的状态的剖面图。图8为具有将本实施方案的保护膜形成膜保护膜化而得到的保护膜的芯片的一个例子的剖面示意图。图9为用于说明将本实施方案的保护膜形成用片贴附在晶圆上的工序的剖面示意图。图10为用于说明将带保护膜的晶圆单颗化(singulation)的工序的剖面示意图。图11为用于说明将带保护膜的芯片配置在基板上的工序的剖面示意图。附图标记说明10:保护膜形成用片(本实施方案);11:保护膜形成膜;12:第一剥离膜;13:第二剥离膜;14:切口;16:经过冲孔加工的保护膜形成膜;17:无用部分;19:辊;20:保护膜形成用片(另一个实施方案);21:晶圆;22:切割片;30:带保护膜的芯片;31:芯片;32:保护膜;33:凸状电极;50:基板。
具体实施方式
20.首先,对本说明书中使用的主要术语进行说明。
21.工件为贴附在本实施方案的保护膜形成膜上并待加工的板状体。作为工件,例如可列举出晶圆、面板。具体而言,可列举出半导体晶圆、半导体面板。作为工件的加工品,例如可列举出将晶圆单颗化而得到的芯片。具体而言,可例示出将半导体晶圆单颗化而得到的半导体芯片。此时,保护膜形成在晶圆及芯片的背面侧。
22.晶圆等工件的“表面”是指形成有电路及凸点等凸状电极等的面,“背面”是指未形成电路、电极(例如凸点等凸状电极)等的面。
23.在本说明书中,例如“(甲基)丙烯酸酯”用作表示“丙烯酸酯”及“甲基丙烯酸酯”这两者的术语,其他类似术语也相同。
24.剥离膜为以可剥离的方式支撑保护膜形成膜的膜。对于膜,并不限定厚度,以包含片的概念使用。
25.保护膜形成膜用组合物、剥离剂层用组合物的相关说明中的质量比基于有效成分(固体成分),只要没有特别说明,则溶剂不计算在内。
26.以下,根据具体的实施方案,以以下的顺序对本发明进行详细说明。
27.(1.保护膜形成膜)如图1、图5所示,本实施方案的保护膜形成用片10为具有保护膜形成膜11和设置在保护膜形成膜11的一个面上的第一剥离膜12的长条片,其通常被卷收为卷状。
28.保护膜形成膜11通过贴附在工件上并进行保护膜化,从而形成用于保护工件或工件的加工品的保护膜。
[0029]“进行保护膜化”是指使保护膜形成膜11成为具有充分的用以保护工件或工件的加工品的特性的状态。具体而言,当本实施方案的保护膜形成膜为固化性时,“进行保护膜化”是指将未固化的保护膜形成膜制成固化物。换言之,经过保护膜化的保护膜形成膜为保护膜形成膜的固化物,其与保护膜形成膜不同。
[0030]
在固化性保护膜形成膜上叠合工件之后,使保护膜形成膜固化,由此能够将保护膜牢固地粘合在工件上,能够形成具有耐久性的保护膜。
[0031]
当保护膜形成膜11不含有固化性成分而以非固化的状态使用时,在将本实施方案的保护膜形成膜贴附在工件上的时刻,该保护膜形成膜被保护膜化。换言之,保护膜也可与保护膜形成膜相同。
[0032]
在不要求高保护性能的情况下,由于无需使保护膜形成膜固化,因此保护膜形成膜可以为非固化性。
[0033]
在本实施方案中,优选保护膜形成膜为固化性。因此,优选保护膜为固化物。作为固化物,例如可例示出热固化物、能量射线固化物。在本实施方案中,更优选保护膜为热固化物。
[0034]
此外,保护膜形成膜优选在常温(23℃)下具有粘着性或优选通过加热而发挥出粘着性。由此,能够在将工件与保护膜形成膜叠合时将两者贴合。因此,可在使保护膜形成膜固化之前确实地进行定位。
[0035]
保护膜形成膜可以由一层(单层)构成,也可以由两层以上的多个层构成。当保护膜形成膜具有多个层时,这些多个层可彼此相同,也可彼此不同,构成这些多个层的层的组
合没有特别限定。
[0036]
在本实施方案中,优选保护膜形成膜为一层(单层)。若保护膜形成膜由多个层构成,则在发生温度变化的工序(回流焊处理时或使用装置时)中,存在因层间的热伸缩性的差异而发生层间剥离的风险,若为一层则能够降低该风险。
[0037]
保护膜形成膜的厚度没有特别限制,但优选为100μm以下,更优选为70μm以下,进一步优选为45μm以下,特别优选为30μm以下。若保护膜形成膜的厚度在上述范围内,则即使在冲孔加工工序后通过辊时经过冲孔加工的保护膜形成膜与无用部分发生了接触、附着,在通过辊之后也易于再度分离。此外,保护膜形成膜的厚度优选为5μm以上,更优选为10μm以上,进一步优选为15μm以上。若保护膜形成膜的厚度在上述范围内,则得到的保护膜的保护性能变得良好。
[0038]
另外,保护膜形成膜的厚度是指保护膜形成膜整体的厚度。例如,由多个层构成的保护膜形成膜的厚度是指构成保护膜形成膜的所有层的合计厚度。
[0039]
以下,对形成在作为工件的加工品的芯片上的保护膜进行说明。具体而言,利用图8所示的带保护膜的芯片30,对本实施方案的保护膜形成膜进行保护膜化而形成的保护膜进行说明。
[0040]
如图8所示,带保护膜的芯片30在芯片31的背面侧(在图8中为上方侧)形成有保护膜32,在芯片31的表面侧(在图8中为下方侧)形成有凸状电极33。
[0041]
芯片31的表面侧形成有电路,且凸状电极33以与电路电连接的方式形成在该表面侧。带保护膜的芯片30以形成有凸状电极33的面与芯片搭载用基板相对的方式而配置。然后,通过规定的加热处理(回流焊处理),经由凸状电极33,与该基板电连接并机械连接,从而得以安装。作为凸状电极33,可例示出凸点、柱状(pillar)电极等。
[0042]
(1.1保护膜形成膜彼此的附着力)在本实施方案中,通过将构成保护膜形成用片的保护膜形成膜彼此贴附时的附着力控制在规定范围内,抑制废料去除的不良。具体而言,本实施方案的特征在于,于23℃用2kgf的载荷将两片保护膜形成膜贴附2分钟后的附着力为19n/25mm以下。该附着力优选为15n/25mm以下,进一步优选为11n/25mm以下。此外,若该附着力过小,则有时工件的保持性能会下降,因此附着力优选为0.1n/25mm以上,进一步优选为1n/25mm以上,特别优选为3n/25mm以上。另外,将附着力的测定设为将保护膜形成膜彼此贴附2分钟后的理由在于,在进行废料去除及对工件的贴附的装置中,在保护膜形成用片通过辊19的工序中,切口的部分与辊19相接并停止的时间约为2分钟。
[0043]
如上所述,通过将保护膜形成膜彼此的附着力控制在规定范围内,即使在冲孔加工工序后弯曲保护膜形成用片,经过冲孔加工的保护膜形成膜16与无用部分17发生附着,保护膜形成膜16与无用部分17也能够在保护膜形成用片通过辊之后再度分离,可降低废料去除的不良。
[0044]
(1.2保护膜形成膜用组合物)只要保护膜形成膜具有上述的物性,则保护膜形成膜的组成没有特别限定。在本实施方案中,构成保护膜形成膜的组合物(保护膜形成膜用组合物)优选为至少含有聚合物成分(a)、固化性成分(b)、及填充材料(e)的树脂组合物。聚合物成分被视作聚合性化合物进行聚合反应而形成的成分。此外,固化性成分为可进行固化(聚合)反应的成分。另外,本
发明中的聚合反应还包括缩聚反应。
[0045]
此外,聚合物成分中含有的成分有时也属于固化性成分。在本实施方案中,当保护膜形成膜用组合物含有这种既属于聚合物成分也属于固化性成分的成分时,视作保护膜形成膜用组合物含有聚合物成分及固化性成分。
[0046]
(1.2.1聚合物成分)聚合物成分(a)使保护膜形成膜具有膜形成性(成膜性),并给予其适度的粘性,使得保护膜形成膜确实地均匀贴附在工件上。聚合物成分的重均分子量通常在5万~200万的范围内,优选在10万~150万的范围内,特别优选在20万~100万的范围内。若重均分子量过低,则有保护膜形成膜彼此的附着力增大的倾向。另一方面,若重均分子量过高,则与其他成分的相容性变差,结果会妨碍形成均一的膜。作为这种聚合物成分,例如可使用丙烯酸树脂、氨基甲酸酯树脂(urethane resin)、苯氧基树脂、有机硅树脂、饱和聚酯树脂等,特别优选使用丙烯酸树脂。
[0047]
另外,在本说明书中,只要没有特别说明,则“重均分子量”为通过凝胶渗透色谱(gpc)法测定的聚苯乙烯换算值。作为通过该方法进行的测定,例如可使用在tosoh corporation制造的高效gpc装置“hlc-8120gpc”中依次连接有高效色谱柱“tsk gurd column h
xl-h”、“tsk gel gmh
xl”、“tsk gel g2000 h
xl”(以上,均为tosoh corporation制造)的设备,在色谱柱温度为40℃、进液速度为1.0ml/分钟的条件下,以示差折光仪为检测器进行测定。
[0048]
作为丙烯酸树脂,例如可列举出由(甲基)丙烯酸酯单体与衍生自(甲基)丙烯酸衍生物的结构单元构成的(甲基)丙烯酸酯共聚物。其中,作为(甲基)丙烯酸酯单体,可优选列举出烷基的碳原子数为1~18的(甲基)丙烯酸烷基酯,具体而言,可列举出(甲基)丙烯酸甲酯、(甲基)丙烯酸乙酯、(甲基)丙烯酸丙酯、(甲基)丙烯酸丁酯等。此外,作为(甲基)丙烯酸衍生物,例如可列举出(甲基)丙烯酸、(甲基)丙烯酸缩水甘油酯、(甲基)丙烯酸羟乙酯等。
[0049]
在本实施方案中,优选使用甲基丙烯酸缩水甘油酯等向丙烯酸树脂中导入缩水甘油基。导入了缩水甘油基的丙烯酸树脂与后述的作为热固性成分的环氧树脂的相容性增高,保护膜形成膜的固化后的玻璃化转变温度(tg)变高,耐热性增高。此外,在本实施方案中,为了控制对工件的粘合性或粘着物性,优选使用丙烯酸羟乙酯等向丙烯酸树脂中导入羟基。
[0050]
丙烯酸树脂的玻璃化转变温度优选为-70℃~40℃,进一步优选为-35℃~35℃,更优选为-20℃~30℃,更加优选为-10℃~25℃,特别优选为-5℃~20℃。通过将丙烯酸树脂的玻璃化转变温度设为上述范围,可抑制保护膜形成膜及保护膜的加热时的流动性,因而易于得到平滑的保护膜。若玻璃化转变温度过低,则有保护膜形成膜彼此的附着力增大的倾向。若玻璃化转变温度过高,则与其他成分的相容性变差,结果会妨碍形成均一的膜。
[0051]
当丙烯酸树脂具有m种(m为2以上的整数)结构单元时,可以以如下方式计算出该丙烯酸树脂的玻璃化转变温度。即,对于衍生出丙烯酸树脂中的结构单元的m种单体,分别依次分配由1至m的任一非重复的序号,并将它们命名为“单体m”时,能够使用如下所示的fox公式计算出丙烯酸树脂的玻璃化转变温度(tg)。[数学式1]
式中,tg为丙烯酸树脂的玻璃化转变温度,m为2以上的整数,tgk为单体m的均聚物的玻璃化转变温度,wk为丙烯酸树脂中的衍生自单体m的结构单元m的质量分数,且wk满足下式。[数学式2]式中,m及wk与上述m及wk相同。
[0052]
作为tgk,可以使用高分子数据手册(高分子
データ
·
ハンドブック
)、粘着手册(粘着
ハンドブック
)或聚合物手册(polymer handbook)等中记载的值。例如,丙烯酸甲酯的均聚物的tgk为10℃、丙烯酸正丁酯的均聚物的tgk为-54℃、甲基丙烯酸甲酯的均聚物的tgk为105℃、丙烯酸2-羟基乙酯的均聚物的tgk为-15℃、甲基丙烯酸缩水甘油酯的均聚物的tgk为41℃、丙烯酸2-乙基己酯的tgk为-70℃。
[0053]
将保护膜形成膜用组合物的总重量设为100质量份时,聚合物成分的含量优选为5~80质量份,进一步优选为8~70质量份,更优选为10~60质量份,更加优选为12~55质量份,进一步优选为14~50质量份,特别优选为15~45质量份。通过使聚合物成分的含量在上述范围内,可将增大保护膜形成膜彼此的附着力的低分子量成分的量限制在适宜的范围内,因此使得保护膜形成膜用组合物的材料设计变得容易。
[0054]
(1.2.2热固性成分)固化性成分(b)使保护膜形成膜固化,从而形成硬质的保护膜。作为固化性成分,可使用热固性成分、能量射线固化性成分或它们的混合物。在通过照射能量射线使其固化时,本实施方案的保护膜形成膜由于含有后述的填充材料及着色剂等,透光率下降。因此,例如当保护膜形成膜的厚度变厚时,能量射线固化容易变得不充分。
[0055]
另一方面,即使热固性的保护膜形成膜的厚度变厚,也能够通过加热而充分固化,因此能够形成保护性能高的保护膜。此外,通过使用加热烘箱等常规加热设备,可一次性加热多片保护膜形成膜,使其热固化。
[0056]
因此,在本实施方案中,固化性成分最好为热固性。即,本实施方案的保护膜形成膜优选为热固性。
[0057]
可通过以下方式判断保护膜形成膜是否为热固性。首先,将常温(23℃)的保护膜形成膜加热至高于常温的温度,接着冷却至常温,由此形成加热并冷却后的保护膜形成膜。接着,在相同温度下,比较加热并冷却后的保护膜形成膜的硬度和加热前的保护膜形成膜的硬度,当加热并冷却后的保护膜形成膜更硬时,判断该保护膜形成膜为热固性。
[0058]
作为热固性成分,例如优选使用环氧树脂、热固性聚酰亚胺树脂、不饱和聚酯树脂及这些树脂的混合物。另外,热固性聚酰亚胺树脂是指通过进行热固化形成聚酰亚胺树脂的低分子量、低粘性的单体或前驱体聚合物的总称。热固性聚酰亚胺树脂的非限制性的具体实例,例如记载于纤维学会志“纤维与工业”,vol.50,no.3(1994),p106-p118中。
[0059]
作为热固性成分的环氧树脂具有受热时进行三维网状化、形成强固的覆膜的性质。作为这种环氧树脂,可使用公知的各种环氧树脂。在本实施方案中,环氧树脂的分子量
(式量)优选为300以上且小于50000,为300以上且小于10000,300以上且小于5000,300以上且小于3000。此外,环氧树脂的环氧当量优选为50~5000g/eq,更优选为100~2000g/eq,进一步优选为150~1000g/eq。
[0060]
作为这种环氧树脂,具体而言,可列举出双酚a、双酚f、间苯二酚、苯酚酚醛清漆(phenol novolak)、甲酚酚醛清漆(cresol novolak)等酚类的缩水甘油醚;丁二醇、聚乙二醇、聚丙二醇等醇类的缩水甘油醚;邻苯二甲酸、间苯二甲酸、四氢邻苯二甲酸等羧酸的缩水甘油醚;用缩水甘油基取代苯胺异氰脲酸酯(aniline isocyanurate)等的与氮原子键合的活性氢而成的缩水甘油型或烷基缩水甘油型的环氧树脂;乙烯基环己烷二环氧化物、3,4-环氧环己基甲基-3,4-二环己烷羧酸酯、2-(3,4-环氧)环己基-5,5-螺(3,4-环氧)环己烷-间二氧六环等通过将分子内的碳碳双键例如氧化而导入有环氧基的所谓脂环式环氧化物。除此以外,也可以使用具有联苯骨架、二环己二烯骨架、萘骨架等的环氧树脂。
[0061]
当使用热固性成分作为固化性成分(b)时,优选同时使用固化剂(c)作为助剂。作为针对环氧树脂的固化剂,优选热活性型潜伏性环氧树脂固化剂。“热活性型潜伏性环氧树脂固化剂”为,于常温(23℃)下难以与环氧树脂反应,但通过加热至某种温度以上而活性化,从而与环氧树脂进行反应的类型的固化剂。对于热活性型潜伏性环氧树脂固化剂的活性化方法,有在基于加热的化学反应中产生活性种(阴离子、阳离子)的方法;在常温附近下稳定分散于环氧树脂中,但在高温下与环氧树脂相容、溶解并引发固化反应的方法;利用分子筛封入型的固化剂在高温下溶出并引发固化反应的方法;基于微胶囊的方法等。
[0062]
在所例示的方法中,优选在常温附近下稳定分散于环氧树脂中,但在高温下与环氧树脂相容、溶解并引发固化反应的方法。
[0063]
作为热活性型潜伏性环氧树脂固化剂的具体实例,能够列举出各种鎓盐、二元酸二酰肼化合物、二氰二胺、胺加成物固化剂、咪唑化合物等高熔点活性氢化合物等。这些热活性型潜伏性环氧树脂固化剂可以单独使用一种,或者也可以组合使用两种以上。在本实施方式中,特别优选二氰二胺。
[0064]
此外,作为针对环氧树脂的固化剂,还优选酚醛树脂。作为酚醛树脂,可无特别限制地使用烷基酚、多元酚、萘酚等酚类与醛类等的缩合物等。具体而言,可以使用苯酚酚醛清漆树脂、邻甲酚酚醛清漆树脂、对甲酚酚醛清漆树脂、叔丁基苯酚酚醛清漆树脂、双环戊二烯甲酚树脂、聚对乙烯基酚醛树脂、双酚a型酚醛清漆树脂、或它们的改性物等。
[0065]
这些酚醛树脂中所含的酚羟基,能够通过加热而易于与上述的环氧树脂的环氧基进行加成反应,从而形成抗冲击性高的固化物。
[0066]
相对于环氧树脂100质量份,固化剂(c)的含量优选为0.01~30质量份,进一步优选为0.1~20质量份,更优选为0.2~15质量份,特别优选为0.3~10质量份。通过将固化剂(c)的含量设为上述范围,保护膜的网状结构变得致密,易于得到作为保护膜的、保护工件的性能。
[0067]
当使用二氰二胺作为固化剂(c)时,优选进一步同时使用固化促进剂(d)。作为固化促进剂,例如优选2-甲基咪唑、2-苯基咪唑、2-苯基-4-甲基咪唑、2-苯基-4,5-二羟甲基咪唑、2-苯基-4-甲基-5-羟甲基咪唑等咪唑类(一个以上氢原子被除氢原子之外的基团取代而成的咪唑)。其中,特别优选2-苯基-4-甲基-5-羟甲基咪唑。
[0068]
相对于环氧树脂100质量份,固化促进剂的含量优选为0.01~30质量份,进一步优
选为0.1~20质量份,更优选为0.2~15质量份,特别优选为0.3~10质量份。通过将固化促进剂(d)的含量设为上述范围,保护膜的网状结构变得致密,因此易于得到作为保护膜的、保护工件的性能。
[0069]
将保护膜形成膜用组合物的总重量设为100质量份时,热固性成分及固化剂的合计含量优选为3~80质量份,进一步优选为5~60质量份,更优选为7~50质量份,进一步优选为9~40质量份,特别优选为10~30质量份。若以上述比例掺合热固性成分与固化剂,则能够在固化前表现出适度的粘性,稳定地进行贴附操作。此外,在固化后,易于得到作为保护膜的、保护工件的性能。
[0070]
作为热固性成分及固化剂,若使用低分子量的化合物,则有时保护膜形成膜的粘性会上升,保护膜形成膜彼此的附着力增大。因此,优选以将粘性控制至适当值的方式在上述范围内选择热固性成分及固化剂的种类及其掺合量。
[0071]
(1.2.3能量射线固化性成分)当固化性成分(b)为能量射线固化性成分时,能量射线固化性成分优选未固化,优选具有粘着性,更优选未固化且具有粘着性。
[0072]
能量射线固化性成分为通过照射能量射线而固化的成分,为用于赋予保护膜形成膜成膜性、可挠性等的成分。
[0073]
作为能量射线固化性成分,例如优选具有能量射线固化性基团的化合物。作为这种化合物,可列举出公知的能量射线固化性成分。
[0074]
作为能量射线固化性成分,若使用低分子量的化合物,则有时保护膜形成膜的粘性会上升,保护膜形成膜彼此的附着力增大。因此,优选以将粘性控制至适当值的方式选择能量射线固化性成分及的种类及其掺合量。
[0075]
(1.2.4填充材料)通过使保护膜形成膜含有填充材料(e),使保护膜形成膜保护膜化而得到的保护膜的热膨胀系数的调整变得容易,通过使该热膨胀系数接近工件的热膨胀系数,使用保护膜形成膜得到的封装的粘合可靠性进一步增高。此外,通过使保护膜形成膜含有填充材料(e),可得到硬质的保护膜,进一步降低保护膜的吸湿率,封装的粘合可靠性进一步增高。
[0076]
填充材料(e)可以为有机填充材料及无机填充材料中的任意一种,从高温下的形状稳定性的角度出发,优选为无机填充材料。
[0077]
作为优选的无机填充材料,例如可列举出二氧化硅、氧化铝、滑石、碳酸钙、红氧化铁、碳化硅、氮化硼等粉末;将这些无机填充材料球形化而得到的珠子;这些无机填充材料的表面改性物;这些无机填充材料的单晶纤维;玻璃纤维等。其中,优选二氧化硅及经过表面改性的二氧化硅。作为经过表面改性的二氧化硅,优选使用偶联剂进行了表面改性,更优选使用硅烷偶联剂进行了表面改性。
[0078]
填充材料的平均粒径优选为0.02~10μm,进一步优选为0.05~5μm,特别优选为0.10~3μm。
[0079]
通过将填充材料的平均粒径设为上述值,保护膜形成膜用组合物的操作性变得良好。因此,保护膜形成膜用组合物及保护膜形成膜的品质易于稳定。
[0080]
另外,只要没有特别说明,则本说明书中的“平均粒径”是指通过激光衍射散射法而求得的粒度分布曲线中累计值50%处的粒径(d50)的值。
[0081]
将保护膜形成膜用组合物的总重量设为100质量份时,填充材料的含量优选为15~80质量份,进一步优选为30~75质量份,更加优选为40~70质量份,特别优选为45~65质量份。
[0082]
通过将填充材料的含量设为上述值,易于将保护膜形成膜彼此的附着力控制在适当的范围内。若填充剂的含量过少,则保护膜形成膜的粘性增加,保护膜形成膜彼此的附着力过度增大。另一方面,若填充剂的掺合量过多,则有时保护膜形成膜的保形性会下降,由于在辊上的弯曲而使膜无法保持形状,保护膜形成膜的粘性及对工件的粘着性过度下降。
[0083]
此外,保护膜形成膜优选含有两种以上的填充材料。即,填充材料(e)优选为两种以上的填充材料的混合物。“含有两种以上的填充材料”可以含有两种以上材质不同的填充材料,可以含有两种以上平均粒径不同的填充材料。
[0084]
在本实施方案中,优选含有两种以上平均粒径不同的填充材料。通过使保护膜形成膜中含有平均粒径不同的填充材料,易于在平均粒径较大的填充材料的空隙中配置平均粒径较小的填充材料。结果可得到上述效果,并且易于将保护膜形成膜彼此的附着力设定在上述范围内。
[0085]
当含有两种以上平均粒径不同的填充材料时,优选平均粒径最大的填充材料的平均粒径为平均粒径最小的填充材料的平均粒径的1.5倍~100倍,更优选为2~20倍,进一步优选为3~18倍。
[0086]
另外,可通过观察保护膜或保护膜形成膜的剖面来确认保护膜或保护膜形成膜是否含有两种以上平均粒径不同的填充材料。
[0087]
(1.2.5偶联剂)保护膜形成膜优选含有偶联剂(f)。通过含有偶联剂,能够在保护膜形成膜固化后不损害保护膜的耐热性,并提高保护膜与工件的粘合性,同时能够提高耐水性(耐湿热性)。作为偶联剂,从其通用性与成本优势的角度出发,优选硅烷偶联剂。
[0088]
作为硅烷偶联剂,例如可列举出γ-缩水甘油醚氧基丙基三甲氧基硅烷、γ-缩水甘油醚氧基丙基甲基二乙氧基硅烷、β-(3,4-环氧环己基)乙基三甲氧基硅烷、γ-(甲基丙烯酰氧丙基)三甲氧基硅烷、γ-氨基丙基三甲氧基硅烷、n-6-(氨基乙基)-γ-氨基丙基三甲氧基硅烷、n-6-(氨基乙基)-γ-氨基丙基甲基二乙氧基硅烷、n-苯基-γ-氨基丙基三甲氧基硅烷、γ-脲基丙基三乙氧基硅烷、γ-巯基丙基三甲氧基硅烷、γ-巯基丙基甲基二甲氧基硅烷、双(3-三乙氧基甲硅烷基丙基)四硫化物、甲基三甲氧基硅烷、甲基三乙氧基硅烷、乙烯基三甲氧基硅烷、乙烯基三乙酰氧基硅烷、咪唑硅烷等。这些硅烷偶联剂可单独使用一种,或者可混合使用两种以上。
[0089]
将保护膜形成膜用组合物的总重量设为100质量份时,偶联剂的含量优选为0.01~20质量份、0.1~10质量份、0.2~5质量份、0.3~3质量份。
[0090]
(1.2.6着色剂)保护膜形成膜优选含有着色剂(g)。由此,由于芯片等工件的加工品的背面被遮盖,因此能够屏蔽电子设备内产生的各种电磁波,能够减少芯片等工件的加工品的故障。此外,当发生了废料去除的不良时,能够立刻通过肉眼发现。
[0091]
作为着色剂(g),例如可使用无机类颜料、有机类颜料、有机类染料等公知的着色剂。在本实施方案中,优选无机类颜料。
[0092]
作为无机类颜料,例如可列举出炭黑、钴类色素、铁类色素、铬类色素、钛类色素、钒类色素、锆类色素、钼类色素、钌类色素、铂类色素、ito(氧化铟锡)类色素、ato(氧化锑锡)类色素等。其中,特别优选使用炭黑。通过炭黑能够遮断较宽波长范围的电磁波。
[0093]
保护膜形成膜中的着色剂(特别是炭黑)的掺合量因保护膜形成膜的厚度而异,例如,当保护膜形成膜的厚度为20μm时,将保护膜形成膜用组合物的总重量设为100质量份时,着色剂的含量优选为0.01~10质量份,进一步优选为0.03~7质量份,更优选为0.05~4质量份。
[0094]
着色剂(特别是炭黑)的平均粒径优选为1~500nm,特别优选为3~100nm,进一步优选为5~50nm。若着色剂的平均粒径在上述范围内,则易于将透光率控制在所需范围内。
[0095]
(1.2.7其他添加剂)在不损害本发明的效果的范围内,保护膜形成膜用组合物例如可含有作为其他添加剂的光聚合引发剂、交联剂、增塑剂、抗静电剂、抗氧化剂、吸杂剂、增粘剂、剥离剂等。
[0096]
其中,优选保护膜形成膜用组合物中的剥离剂的含量少于规定量。在本实施方案中,相对于保护膜形成膜的总质量,优选小于0.00099质量%。若剥离剂的含量过多,则有保护膜与工件的粘合可靠性下降的倾向。作为剥离剂,例如可例示出醇酸类剥离剂、有机硅(silicone)类剥离剂、氟类剥离剂、不饱和聚酯类剥离剂、聚烯烃类剥离剂、蜡类剥离剂。
[0097]
(1.2.8保护膜形成膜彼此的附着力的控制)如上所述,本实施方案的特征在于,通过将构成保护膜形成用片的保护膜形成膜彼此贴附时的附着力控制在规定范围内,并由此抑制废料去除的不良。
[0098]
保护膜形成膜彼此的附着力可通过构成保护膜形成膜的各成分的种类及其掺合量进行控制。
[0099]
若聚合物成分(a)的重均分子量低,则有附着力增大的倾向。若聚合物成分(a)的玻璃化转变温度低,则有附着力增大的倾向。此外,若使用低分子量的化合物作为固化性成分(b)、固化剂(c)、固化促进剂(d)、能量射线固化性成分,则有附着力增大的倾向。若填充剂(e)的掺合量多,则有附着力下降的倾向。
[0100]
通过将保护膜形成膜部分固化,也可控制附着力。例如通过将固化性成分(b)部分固化,能够降低附着力。将保护膜形成膜部分固化的时机没有特别限定,例如只要是在对保护膜形成用片进行冲孔加工时通过辊19之前的阶段即可。然而,从将后述的剥离力f1及f2设置在适当的范围内的角度、以及对工件的粘着性的角度出发,保护膜形成膜优选如后述的实施例所述未进行部分固化。
[0101]
(2.保护膜形成用片)保护膜形成膜在使用前,可以如图1所示,以在第一剥离膜12上层叠有可剥离的保护膜形成膜11的双层结构的保护形成用片10的形态被卷收、保管。此外,也可以如图3所示,以在两片剥离膜(第一剥离膜12、第二剥离膜13)之间夹持有保护膜形成膜11的三层结构的保护膜形成用片20的形态(另一个实施方案)被卷收、保管。剥离膜在使用保护膜形成膜时被剥离。
[0102]
上述保护膜形成用片为长条且被卷绕成卷状进行保管、运输。作为这种保护膜形成用片,还已知有预先将保护膜形成膜冲孔加工为与工件大致相同的形状的保护膜形成用片。这种经过冲孔加工的保护膜形成用片的冲孔加工为规定的封闭形状的保护膜形成膜16
被层叠在第一剥离膜12上(图2),或夹持在两片剥离膜(12、13)之间(图4)。
[0103]
第一剥离膜可以由一层(单层)或两层以上的基材构成,从控制剥离性的角度出发,基材的表面可经过剥离处理。即,基材的表面可被改性,也可在基材的表面形成并非来自基材的材料。在本实施方案中,优选第一剥离膜具有基材与剥离剂层。通过具有剥离剂层,易于控制第一剥离膜中形成有剥离剂层的面的物性。在本实施方案中,在基材的一个面上涂布含有后述的剥离剂层用组合物的涂布剂之后,将该涂膜干燥并固化,由此形成剥离剂层。由此可得到第一剥离膜。
[0104]
第一剥离膜12的厚度没有特别限定,但优选为30~100μm,进一步优选为40~80μm,更优选为45~70μm。
[0105]
通过使第一剥离膜12的厚度的下限值为上述值,能够防止在使用切割刀切下保护膜形成膜时,切割刀贯穿第一剥离膜12而切断第一剥离膜12。此外,在保护膜形成用片10被放卷且保护膜形成膜11被切出后,在被运输至下一道工序之前,保护膜形成用片10会通过装置内的导辊等辊,但通过使第一剥离膜12的厚度的上限值为上述值,能够防止保护膜形成膜11从第一剥离膜12上剥离。
[0106]
另外,第一剥离膜12的厚度是指第一剥离膜整体的厚度。例如,由多个层构成的第一剥离膜的厚度是指构成第一剥离膜的所有层的合计厚度。
[0107]
作为第一剥离膜12的基材,可列举出树脂膜及纸等。作为树脂膜的树脂,可列举出聚对苯二甲酸乙二醇酯、聚乙烯、聚丙烯、聚丁烯、聚丁二烯、聚甲基戊烯、聚氯乙烯、氯乙烯共聚物、聚对苯二甲酸丁二醇酯、聚氨酯、乙烯-乙酸乙烯酯共聚物、离聚物树脂、乙烯(甲基)丙烯酸共聚物、聚苯乙烯、聚碳酸酯、氟树脂、低密度聚乙烯、线性低密度聚乙烯及三乙酰纤维素等。作为纸,可列举出优质纸、涂布纸(coat paper)、玻璃纸及层压纸等。这些基材可单独使用一种,也可同时使用两种以上。其中,从廉价且具有刚性的角度出发,优选聚对苯二甲酸乙二醇酯膜。
[0108]
第一剥离膜12的至少一个面(与保护膜形成膜层叠的面)可通过剥离剂层用组合物进行了剥离处理。剥离剂层的厚度优选为30nm以上200nm以下,更优选为50nm以上180nm以下。
[0109]
第一剥离膜12的与保护膜形成膜11相接的面的表面弹性模量(23℃)优选为17mpa以下,进一步优选为14mpa以下,更优选为13mpa以下特别优选为12mpa以下,表面弹性模量为表面的变形容易程度的指标。通过将第一剥离膜12的与保护膜形成膜11相接的面的表面弹性模量设在上述范围内,能够在冲孔加工工序中,在按压冲模然后将其拉起时,抑制在保护膜形成膜11与第一剥离膜12之间产生浮起(1~4mm左右的剥离)。认为这是由于第一剥离膜12的表面比较柔软,即使存在基于冲模的压缩与基于其脱离的脱压,第一剥离膜表面也会追随保护膜形成膜的变形。通过抑制浮起的发生,可进一步减少废料去除的不良。第一剥离膜12的与保护膜形成膜11相接的面的表面弹性模量的下限没有特别限定,但若表面弹性模量过低,则剥离力有时会增大,因此优选为3mpa以上,进一步优选为4mpa以上,特别优选为5mpa以上。
[0110]
23℃下的第一剥离膜12的与保护膜形成膜11相接的面的表面弹性模量可使用具备悬臂的原子力显微镜而测定。即,对第一剥离膜12的与保护膜形成膜11相接的面进行悬臂的按压和拉离,得到力曲线。对得到的力曲线进行基于jkr理论式的拟合,求出弹性模量,
作为本发明的表面弹性模量。具体的测定方法会在后述的实施例中详细说明。
[0111]
为了将后述的剥离力f1设置在适当的范围内,并将第一剥离膜12的表面弹性模量设置在上述范围内,在本实施方案中,作为剥离剂层用组合物,例如优选醇酸类脱模剂、有机硅类脱模剂、氟类脱模剂、不饱和聚酯类脱模剂、聚烯烃类脱模剂、蜡类脱模剂,其中,优选有机硅类脱模剂,特别优选含有有机硅类脱模剂与重剥离添加剂。
[0112]
作为有机硅类脱模剂,可使用掺合有具有二甲基聚硅氧烷作为基本骨架的有机硅的有机硅脱模剂。
[0113]
该有机硅可以为加成反应型、缩合反应型以及紫外线固化型及电子束固化型等能量射线固化型中的任意一种,但优选为加成反应型有机硅。加成反应型有机硅反应性高,生产率优异,且与缩合反应型相比,具有制造后的剥离力的变化小、无固化收缩等优点。
[0114]
作为加成反应型有机硅的具体实例,可列举出在分子的末端和/或侧链具备2个以上乙烯基、烯丙基、丙烯基及己烯基等碳原子数为2~10的烯基的有机聚硅氧烷。从降低表面弹性模量的角度出发,优选加成反应型有机硅中的烯基数少。
[0115]
将剥离剂层用组合物(不包括后述的催化剂)的总重量设为100质量份时,由二甲基聚硅氧烷构成的有机硅的含量优选小于100质量份,进一步优选小于90质量份,更优选小于80质量份,特别优选小于70质量份。
[0116]
在使用这种加成反应型有机硅时,优选同时使用交联剂及催化剂。
[0117]
作为交联剂,例如可列举出在一分子中至少具有2个与氢原子键合的硅原子的有机聚硅氧烷。从降低表面弹性模量的角度出发,优选剥离剂层用组合物中的交联剂含量少。
[0118]
作为交联剂的具体实例,可列举出二甲基氢硅氧烷基末端封端二甲基硅氧烷-甲基氢硅氧烷共聚物、三甲基硅氧烷基末端封端二甲基硅氧烷-甲基氢硅氧烷共聚物、三甲基硅氧烷基末端封端甲基氢聚硅氧烷、聚(氢倍半硅氧烷)等。
[0119]
作为催化剂,可列举出微粒状铂、吸附在碳粉末载体上的微粒状铂、氯铂酸、醇改性氯铂酸、氯铂酸的烯烃络合物、钯及铑等铂族金属类化合物等。
[0120]
通过使用这种催化剂,能够更加有效进行剥离剂层用组合物的固化反应。
[0121]
从将表面弹性模量设在上述范围内的角度以及将后述的剥离力f1设在适当范围内的角度出发,将剥离剂层用组合物(不包括催化剂)的总重量设为100质量份时,有机硅类脱模剂的含量优选为30~100质量份,进一步优选为50~100质量份。
[0122]
重剥离添加剂用于增大后述的剥离力f1。作为重剥离添加剂,例如可列举出有机硅树脂、硅烷偶联剂等有机硅烷,其中,优选有机硅树脂。
[0123]
作为有机硅树脂,例如优选使用mq树脂,其含有作为单官能度硅氧烷单元[r3sio
1/2
]的m单元与作为四官能度硅氧烷单元[sio
4/2
]的q单元。另外,m单元中的3个r各自独立地表示氢原子、羟基或有机基团。从易于抑制有机硅转移的角度出发,m单元中的3个r中的1个以上优选为羟基或乙烯基,更优选为乙烯基。从降低表面弹性模量的角度出发,优选剥离剂层用组合物中的有机硅树脂(特别是mq树脂)的含量少。
[0124]
将剥离剂层用组合物(不包括催化剂)的总重量设为100质量份时,重剥离添加剂的含量优选为0~50质量份,进一步优选为5~45质量份,特别优选为10~40质量份。
[0125]
从调整粘度、提高对基材的涂布性的角度出发,剥离剂层用组合物优选作为除了含有上述各种有效成分以外还含有稀释溶剂的涂布剂进行使用。在本说明书中,“有效成
分”是指在含有作为对象的组合物的涂布剂中所含有的成分中除去稀释溶剂以外的成分。
[0126]
作为稀释溶剂,可列举出甲苯等芳香族烃、乙酸乙酯等脂肪酸酯、甲基乙基酮等酮、己烷、庚烷等脂肪族烃等有机溶剂等。这些稀释溶剂可单独使用一种,也可同时使用两种以上。
[0127]
含有剥离剂层用组合物的涂布剂的有效成分(固体成分)浓度优选为0.3~10质量%,更优选为0.5~5质量%,进一步优选为0.5~3质量%。
[0128]
在不损害本发明的效果的范围内,剥离剂层用组合物可含有在剥离剂层中通常使用的添加剂。作为这种添加剂,可列举出染料及分散剂等。
[0129]
在本实施方案的保护膜形成用片10中,优选将保护膜形成膜11冲孔加工为规定的形状。即,优选在所述保护膜形成用片上以在俯视保护膜形成用片10时保护膜形成用片10的一部分具有规定的封闭形状的方式形成有切口14。另外,从在工件上贴附保护膜形成膜时保护膜形成膜不从工件上溢出的角度出发,优选冲孔加工后的保护膜形成膜的形状小于工件的形状。
[0130]
(3.保护膜形成用片的制造方法)保护膜形成膜的制造方法没有特别限定。该膜可使用含有上述保护膜形成膜用组合物的涂布剂而制造。涂布剂可通过利用公知的方法混合构成保护膜形成膜用组合物的成分而制备。
[0131]
使用辊涂机、刮刀涂布机、辊刀涂布机、气刀涂布机、模涂机、棒涂机、凹版涂布机、幕涂机等涂布机,将得到的涂布剂涂布在第一剥离膜12的剥离面上并使其干燥,可得到在第一剥离膜12上具有保护膜形成膜11的、本实施方案的保护膜形成用片10。另外,也可在其他的树脂膜上涂布涂布剂并使其干燥,将得到的保护膜形成膜转印至第一剥离膜上。在欲得到另一个实施方案的保护膜形成用片20时,在与第一剥离膜12层叠的保护膜形成膜11的露出面上贴合第二剥离膜13,得到在两片剥离膜中夹持有保护膜形成膜11的保护膜形成用片20。
[0132]
(4.经过冲孔加工的保护膜形成用片的制造方法)针对对保护膜形成用片10进行冲孔加工并在第一剥离膜12上得到冲孔加工为规定的封闭形状的保护膜形成膜16的方法进行说明。
[0133]
(4.1冲孔加工工序)首先,准备图1所示的未经过冲孔加工的保护膜形成用片10。利用冲模(未图示),自保护膜形成用片10的保护膜形成膜11侧的面,以贯穿保护膜形成膜11并到达至第一剥离膜12的表面的一部分的方式切出切口14。将以到达至表面的一部分的方式切出切口而未完全切断的操作称为半切(half-cut)。结果在保护膜形成用片10的表面的一部分上以具有规定的封闭形状的方式形成切口14(参照图2、图5)。此处,在将保护膜形成膜转印至半导体晶圆上的情况下,规定的封闭形状为与晶圆大致相同的形状。即,以成为与保护膜形成膜11所贴附的工件的形状或与应形成保护膜的区域大致相同的形状的方式形成切口14。该工序被称为“冲孔加工工序”。
[0134]
通过冲孔加工工序,保护膜形成膜11被分为冲孔加工为规定的封闭形状的保护膜形成膜16、及在其周围的连续的无用部分17。在保护膜形成用片10的长边方向上,在多处设有冲孔加工为规定的封闭形状的保护膜形成膜16。
[0135]
在冲孔加工工序中,可适当使用公知的冲模。冲孔加工以完全切断保护膜形成膜11且不完全切断第一剥离膜12的方式进行半切而进行。
[0136]
如图2、图4所示,切口14的剖面形状大致为楔型,切口14的宽度在冲模所进入的保护膜形成膜11的上表面侧较宽,且在下表面侧(保护膜形成膜11与第一剥离膜12的界面)变窄。切口14的宽度没有特别限定,但从防止经过冲孔加工的保护膜形成膜16与无用部分17的接触、附着的角度出发,或从缩短接触、附着的时间的角度出发,保护膜形成膜11的下表面部(即,第一剥离膜12的上表面部)的切口14的宽度d优选为8μm以上,更优选为10μm以上,进一步优选为15μm以上,特别优选为20μm以上。作为宽度d,可将保护膜形成用片沿厚度方向切断,并将剖面的第一剥离膜12的上表面部的切口的宽度作为宽度d进行测定。宽度d的上限值没有特别限定,但考虑到能够确实地切断保护膜形成膜的切割刀的宽度,通常为100μm以下,优选为80μm以下,更优选为60μm以下,进一步优选为40μm以下。为了形成这种切口14,作为冲模,优选使用具有前端部的刀刃宽度较宽的切割刀的冲模。
[0137]
经过上述工序,可得到经过冲孔加工的保护膜形成用片10。在保护膜形成用片上,以在从保护膜形成膜11的上表面俯视经过冲孔加工的保护膜形成用片10时保护膜形成用片的一部分具有规定的封闭形状(例如,与半导体晶圆的平面形状大致相同的形状)的方式形成有切口14,且切口14在保护膜形成用片10的厚度方向到达至第一剥离膜12的一部分。即,在第一剥离膜12的与保护膜形成膜11相接的表面上也形成有切口。通过使切割刀到达至第一剥离膜12,能够将保护膜形成膜11完全切断。
[0138]
(4.2废料去除工序)在冲孔加工工序之后至废料去除工序之前,以控制保护膜形成用片的张力等为目的,保护膜形成用片10会通过导辊等多个辊。
[0139]
如图6所示,在废料去除工序中,从第一剥离膜12上剥离连续的无用部分17,使经过冲孔加工的保护膜形成膜16残留在第一剥离膜12上。被剥离的无用部分17被卷绕在提废用辊上。
[0140]
根据本实施方案的保护膜形成用片10,由于保护膜形成膜彼此的附着力低,即使在冲孔加工工序后通过辊19等时经过冲孔加工的保护膜形成膜16与无用部分17发生了接触、附着,在通过辊之后,保护膜形成膜16与无用部分17也可再度分离。结果可抑制废料去除工序中的废料去除的不良。
[0141]
经过冲孔加工的保护膜形成用片10可卷绕成卷状进行保管、运输。
[0142]
(5.工件的加工方法)作为使用有本实施方案的经过冲孔加工的保护膜形成用片的工件的加工方法的一个例子,对在基板上配置有对贴附有保护膜形成膜的晶圆进行加工而得到的带保护膜的芯片的封装的制造方法进行说明。
[0143]
本实施方案的装置的制造方法至少具有以下的工序1至工序9。工序1:对保护膜形成用片10进行冲孔加工的工序工序2:经过冲孔加工的保护膜形成用片通过辊间的工序工序3:去除保护膜形成用片10的无用部分17的工序工序4:将保护膜形成用片10的保护膜形成膜11贴附在晶圆背面的工序工序5:将贴附的保护膜形成膜保护膜化的工序
工序6:从保护膜或保护膜形成膜上剥离第一剥离膜的工序工序7:将背面具有保护膜或保护膜形成膜的晶圆单颗化,得到多个带保护膜或保护膜形成膜的芯片的工序工序8:将带保护膜或保护膜形成膜的芯片配置在基板上的工序工序9:对配置在基板上的带保护膜或保护膜形成膜的芯片与基板进行加热的工序
[0144]
工序1~工序3如上所述。工序5可在工序6之前进行,也可在工序6~工序9中的任意一道工序之后进行。即,将保护膜形成膜保护膜化的工序可在将保护膜形成膜贴附在晶圆上之后的任意阶段进行。
[0145]
参照附图,对具有上述工序1至工序9的装置的制造方法进行说明。
[0146]
图2、图4、图5如上所述示出了工序1的概略。图6示出了工序3的概略。如图9所示,在晶圆21的背面贴附保护膜形成用片10的保护膜形成膜11(工序4)。然后,将贴附的保护膜形成膜11保护膜化,形成保护膜32(工序5),得到带保护膜的晶圆。当保护膜形成膜11为热固性时,以规定温度对保护膜形成膜11加热适当的时间即可。此外,当保护膜形成膜11为能量射线固化性时,使用能量射线透射膜作为第一剥离膜12且自第一剥离膜12侧入射能量射线即可。
[0147]
另外,保护膜形成膜11的固化也可在后述的切割工序后进行,也可在从切割片上拾取带保护膜形成膜的芯片后使保护膜形成膜11固化。
[0148]
然后,将带保护膜的晶圆21转印至公知的切割片22上,对带保护膜的晶圆21进行切割,如图10所示,得到具有保护膜32的芯片31(带保护膜的芯片30)(工序7)。然后,根据需要沿平面方向扩展切割片22,利用吸嘴(未图示)等从切割片22上拾取带保护膜的芯片30。
[0149]
可将拾取的带保护膜的芯片30搬运至下一道工序,也可暂时将其收纳保管在盘、胶带等上,并在规定期间后搬运至下一道工序。
[0150]
如图11所示,搬运至下一道工序的带保护膜的芯片30被吸嘴搬运至基板50上,在基板上的端子部从吸嘴上脱离,并被配置在凸点等凸状电极33与焊盘(pad)等端子部可进行连接的位置上(工序8)。此时,与带保护膜的芯片30不同的其他芯片也可安装在基板50上。因此,可以在该基板上安装多个芯片。
[0151]
对配置在基板上的规定位置的带保护膜的芯片进行加热处理(回流焊处理)(工序9)。作为回流焊处理条件,例如优选最高加热温度为180~350℃,回流焊时间为2~10分钟。
[0152]
在回流焊处理中,带保护膜的芯片30的凸状电极33熔融,与基板上的端子部电连接并机械连接,带保护膜的芯片30被安装在基板上。
[0153]
(6.变形例)以上,对于本发明的实施方案,以在第一剥离膜12上具有保护膜形成膜11的双层结构的保护膜形成用片为例进行了说明,但也可在保护膜形成膜11的露出面上层叠有第二剥离膜13。即,保护膜形成用片也可以为在第一剥离膜12与第二剥离膜13之间夹持有保护膜形成膜11的形态的保护膜形成用片20(参照图3、图4)。此时,对于第二剥离膜13,在将保护膜形成膜11贴附在工件上之前将其剥离即可。
[0154]
保护膜形成用片20的保护膜形成膜11的材质及其优选的形态与上述实施方案相同,且第一剥离膜12也与对上述实施方案进行说明时的情况相同。
[0155]
此外,在本实施方案中,在保护膜形成用片20中,将从保护膜形成膜11上剥离第一
剥离膜12时的剥离力设为f1、并将从保护膜形成膜11上剥离第二剥离膜13时的剥离力设为f2时,f1与f2优选满足f1>f2的关系。通过满足这种关系,在从保护膜形成用片20上去除第二剥离膜13时,应残留的保护膜形成膜16不会与第二剥离膜13一同被去除,保护膜形成膜16容易残留在第一剥离膜12上,可进一步抑制废料去除的不良。
[0156]
因此,第一剥离膜12为剥离力强的重剥离膜,第二剥离膜13为剥离力弱的轻剥离膜。
[0157]
另外,剥离力f1优选为50mn/100mm以上,进一步优选为70mn/100mm以上,更优选为90mn/100mm以上,更加优选为110mn/100mm以上,特别优选为130mn/100mm以上。通过使f1在上述范围内,能够抑制保护膜形成膜11与第一剥离膜12意外剥离。
[0158]
剥离力的调整例如可通过剥离剂层用组合物的种类、剥离剂层的厚度等控制。第二剥离膜13被设计为剥离力小于第一剥离膜12。当第二剥离膜13具有剥离剂层时,只要剥离剂层由可赋予剥离性的材料构成,则没有特别限制。例如,第二剥离膜13的剥离剂层可与第一剥离膜12的剥离剂层相同,使含有有机硅的剥离剂层用组合物固化而得到。
[0159]
第二剥离膜13的剥离剂层用组合物只要满足上述的f1与f2的关系,则能够从第一剥离膜12中例示的材料中进行选择。其中,对于作为重剥离添加剂而例示的材料,优选少于在第一剥离膜12中的含量、或不包含。
[0160]
第二剥离膜13的厚度没有特别限制,但优选为10μm以上75μm以下。此外,第二剥离膜的厚度更优选为18μm以上,进一步优选为24μm以上。此外,第二剥离膜的厚度更优选为60μm以下,进一步优选为45μm以下。从将剥离力f2与剥离力f1设为上述的f1>f2的角度出发,第二剥离膜的厚度优选为第一剥离膜的厚度以下,更优选小于第一剥离膜的厚度。
[0161]
另外,第二剥离膜的厚度是指第二剥离膜整体的厚度。例如,由多个层构成的第二剥离膜的厚度是指构成第二剥离膜的所有层的合计厚度。
[0162]
保护膜形成用片20的制造方法如实施方案中所述,在与第一剥离膜12层叠的保护膜形成膜11的露出面上贴合第二剥离膜13即可。
[0163]
在对保护膜形成用片20进行冲孔加工时,除了使冲模自第二剥离膜13侧进入,并将保护膜形成膜11与第二剥离膜13切断为规定的封闭形状以外,与上述实施方案相同。结果在第一剥离膜12上得到经过冲孔加工的保护膜形成膜11与第二剥离膜13。经过冲孔加工的保护膜形成用片20可被卷绕为卷状进行保管、运输。
[0164]
在废料去除工序中,同时卷绕第二剥离膜13与无用部分17而将第二剥离膜13与无用部分17去除。此时,经过冲孔加工的被完全切断后的第二剥离膜13通过使用长条状的粘着胶带再度接合,易于去除第二剥离膜13。结果切断为规定的封闭形状的保护膜形成膜16残留在第一剥离膜12上。
[0165]
以上,对本发明的实施方案进行了说明,但本发明不受上述实施方案的任何限定,可在本发明的范围内以各种形态进行改变。实施例
[0166]
以下,利用实施例对发明进行进一步详细说明,但本发明不受这些实施例限定。
[0167]
(保护膜形成用片的制造)[第一剥离膜(重剥离膜)]《含有剥离剂层用组合物的涂布剂》
准备下述剥离剂层用组合物原料。
·
含有具备乙烯基的有机聚硅氧烷及具备氢硅烷基(hydrosilyl group)的有机聚硅氧烷的有机硅类脱模剂(dow corning toray co.,ltd.制造,by24-561,固体成分为30质量%)
·
二甲基聚硅氧烷(重均分子量:2000)(shin-etsu chemical co.,ltd.制造,x-62-1387,固体成分为100质量%)
·
作为重剥离添加剂的具备乙烯基的mq树脂(dow corning toray co.,ltd.制造,sd-7292,固体成分为71质量%)
·
铂(pt)催化剂(dow corning toray co.,ltd.制造,srx-212,固体成分为100质量%)
[0168]
以表1中记载的掺合比(固体成分换算),在甲苯与甲基乙基酮的混合溶剂(甲苯/甲基乙基酮=1/1(质量比))中添加上述原料,将总固体成分调整为2质量%,制备含有剥离剂层用组合物的涂布剂。
[0169]
《第一剥离膜的制造》在pet膜(mitsubishi chemical corporation制造,商品名称:diafoil(注册商标)t-100,厚度:50μm)上,以使干燥后的膜厚为0.15μm的方式,涂布含有剥离剂层用组合物的涂布剂,并进行加热、干燥,从而在pet膜上形成剥离剂层,制造第一剥离膜(重剥离膜)a~c。
[0170]
《表面弹性模量的测定》通过以下方式测定所得到的第一剥离膜的剥离处理面的表面弹性模量。在原子力显微镜(brukercorporation制造,multimode8)上设置氮化硅素材的悬臂(brukercorporation制造,商品名称:mlct,前端半径:20nm,共振频率:125khz,弹簧常数:0.6n/m)。将制造的第一剥离膜放置在原子力显微镜上,通过设置的悬臂,以2nm的按压量、10hz的扫描速度,对制造的第一剥离膜的剥离剂层的表面进行按压与拉离。该操作在23℃下进行。对通过该操作得到的力曲线进行基于jkr理论式的拟合,计算出表面弹性模量。对于表面弹性模量,在第一剥离膜的剥离剂层的表面1μm
×
1μm中测定4096个点,取这些值的平均值并将小数点后一位四舍五入,作为表面弹性模量(mpa)。将结果示于表1。[表1]
[0171]
[第二剥离膜(轻剥离膜)]使用lintec corporation制造的“sp-pet 381130(厚度为38μm)”。
[0172]
[含有保护膜形成膜用组合物的涂布剂]以表2所示的掺合比(固体成分换算)混合下述各成分,以使固体成分浓度为50质量%的方式用甲基乙基酮进行稀释,制备涂布剂。
[0173]
(a)聚合物成分(a-1)由10质量份的丙烯酸正丁酯、70质量份的丙烯酸甲酯、5质量份的甲基丙烯酸缩水甘油酯及15质量份的丙烯酸2-羟基乙酯共聚而成的(甲基)丙烯酸酯共聚物(重均分子量:40万,玻璃化转变温度:-1℃)(a-2)由10质量份的丙烯酸正丁酯、65质量份的丙烯酸甲酯、12质量份的甲基丙烯酸缩水甘油酯、及13质量份的丙烯酸2-羟基乙酯共聚而成的(甲基)丙烯酸酯共聚物(重均分子量:45万,玻璃化转变温度:2℃)(b)固化性成分(热固性成分)(b-1)双酚a型环氧树脂(mitsubishi chemical corporation制造,jer828,环氧当量为184~194g/eq)(b-2)丙烯酸橡胶微粒分散双酚a型液状环氧树脂(nippon shokubai co.,ltd.制造,bpa328,环氧当量为230g/eq,丙烯酸橡胶含量为20phr)(b-3)二环戊二烯型环氧树脂(dic corporation制造,epiclon hp-7200hh,软化点为88~98℃、环氧当量为255~260g/eq)(c)固化剂:二氰二胺(mitsubishi chemical corporation制造,dicy7)(d)固化促进剂:2-苯基-4,5-二羟基甲基咪唑(shikoku chemicals corporation制造,curezol 2phz)(e)填充材料(e-1)环氧基修饰球状二氧化硅填料(admatechs公司制造,sc2050ma,平均粒径为0.5μm)(e-2)二氧化硅填料(admatechs公司制造的“yc100c-mla”,平均粒径为0.1μm)(f)硅烷偶联剂:γ-缩水甘油醚氧基丙基三甲氧基硅烷(shin-etsu chemical co.,ltd.制造,kbm403,甲氧基当量为12.7mmol/g,分子量为236.3)(g)着色剂:炭黑(mitsubishi chemical corporation制造,ma600b,平均粒径为28nm)
[0174]
[表2]
[0175]
将制备的保护膜形成膜用组合物涂布在所述第一剥离膜(上述a~c中的任意一种)的剥离处理面上,于100℃干燥2分钟,形成厚度为20μm的保护膜形成膜。然后,将第二剥离膜贴附在保护膜形成膜上,得到在保护膜形成膜的两面形成有剥离膜的三层结构的保护膜形成用片。作为贴附条件,温度为60℃,压力为0.4mpa,速度为1m/分钟。然后,将保护膜形成用片裁切为208mm的宽度,并卷绕50米的长度,形成卷体。
[0176]
使用所得到的保护膜形成用片,进行下述测定及评价。
[0177]
[保护膜形成膜彼此的附着力]通过以下方式使保护膜形成膜从保护膜形成用片中露出,并将保护膜形成膜彼此贴附,测定附着力。
[0178]
《将保护膜形成膜固定在粘着胶带上》i.将第二剥离膜/保护膜形成膜/第一剥离膜的三层结构的保护膜形成用片的、第二剥离膜剥下。ii.于23℃,在露出的保护膜形成膜上贴附lintec corporation制造的粘着胶带(产品名称pet50pl
シン
:丙烯酸类粘着剂层/50μm pet基材),制成“pet基材/丙烯酸类粘着剂层/保护膜形成膜/第一剥离膜”的层叠体样本。iii.将层叠体样本切割成宽25mm、长250mm的条状。
[0179]
《将保护膜形成膜固定在sus板上》i.在sus板(0.5mm厚
×
70mm
×
150mm)的整个面上贴附将pet膜作为芯材的双面胶带。ii.将第二剥离膜/保护膜形成膜/第一剥离膜的三层结构的保护膜形成用片的、第二剥离膜剥下。iii.将露出的保护膜形成膜贴附在上述双面胶带的粘着剂面的整个面上,得到“sus板/双面胶带/保护膜形成膜/第一剥离膜”的层叠体样本。
iv.剥下第一剥离膜,使保护膜形成膜露出。
[0180]
《附着力的测定》从“pet基材/丙烯酸类粘着剂层/保护膜形成膜/第一剥离膜”的层叠体样本中剥下第一剥离膜,使保护膜形成膜露出。将“pet基材/丙烯酸类粘着剂层/保护膜形成膜”的层叠体与“sus板/双面胶带/保护膜形成膜”的层叠体,以保护膜形成膜彼此相对的方式进行层叠,利用2kg的辊,于23℃下进行贴合。
[0181]
在不加温的状态下进行静置,在贴附后经过2分钟(
±
20秒)之后,通过下述测定方法测定附着力。使用万能型拉伸试验机(shimadzu corporation制造,产品名称“autograph ag-is”),针对70mm的测定距离,以300mm/分钟的剥离速度、23℃的温度、180
°
的剥离角度,测定剥离力。将去除了测定距离的最初10mm与最后10mm的、50mm之间的测定值的平均作为“保护膜形成膜彼此的附着力”。
[0182]
[从保护膜形成膜上剥离第一剥离膜时的剥离力f1]从得到的保护膜形成用片中剥离第二剥离膜。通过热层压(70℃、1m/分钟),在通过剥离而露出的保护膜形成膜的表面贴附厚度为25μm的良粘合pet(toyobo co.,ltd.制造,pet25a-4100)的良粘合面,制成层叠体样本。将层叠体样本切成100mm的宽度,制成测定用样本。使用双面胶带将测定用样本的第一剥离膜的背面固定在硬质支撑板上。
[0183]
使用万能型拉伸试验机(shimadzu corporation制造,产品名称“autograph(注册商标)ag-is”),以180
°
的剥离角度、1m/分钟的剥离速度,从第一剥离膜上剥离保护膜形成膜/良粘合pet的复合(一体型)体,并测定此时的载荷。测定距离总计100mm,将去除了最初10mm与最后10mm的、80mm之间的测定值的平均作为剥离力f1。将结果示于表2。
[0184]
[从保护膜形成膜上剥离第二剥离膜时的剥离力f2]将得到的保护膜形成用片切成100mm的宽度,制成测定用样本。使用双面胶带将测定用样本的第一剥离膜的背面固定在硬质支撑板上。
[0185]
使用万能型拉伸试验机(shimadzu corporation制造,产品名称“autograph(注册商标)ag-is”),从测定用样本中剥离第二剥离膜,以与测定上述f1时相同的条件,测定此时的载荷,作为剥离力f2。
[0186]
对得到的剥离力f1及f2进行比较,对于所有试样,确认到f1大于f2。
[0187]
[保护膜形成用片的冲孔加工及废料去除]以200mm晶圆用的规格使用lintec corporation制造的rad-3600f/12,使冲模自保护膜形成用片的第二剥离膜侧进入,将保护膜形成膜与第二剥离膜冲裁为圆形(内径为198mm)。此时,对于第一剥离膜,以不完全冲裁的方式切出切口(冲孔加工工序)。使用切割刀的刀刃宽度不同的四种冲模,进行切口宽度不同的半切。进行40次冲孔加工。
[0188]
在冲孔加工工序后,使保护膜形成用片在多个辊之间移动。然后,将冲裁为圆形的部分残留在第一剥离膜上,并去除第二剥离膜及冲裁为圆形的部分的周边无用部分(废料去除工序)。此时,利用长条的粘着胶带将经过冲孔加工的完全被切断后的第二剥离膜再度接合,在此基础上去除第二剥离膜。
[0189]
《切口宽度》
以第一剥离膜的切口部不变形的方式沿厚度方向切断废料去除工序后的保护膜形成用片,使保护膜形成用片保持平坦,使用扫描型电子显微镜(sem,keyence corporation制造的“ve-9800”)观察剖面。测定第一剥离膜与保护膜形成膜的界面上的残留在第一剥离膜上的切口的宽度。
[0190]
从所具有的40个圆形部分中选择第20个,在该一个圆的圆周上以等间隔在6个点(若将点连接则为正六角形)进行测定。将6个点中的最小值作为“切口宽度”。并将小数点后一位四舍五入。
[0191]
切口宽度越宽,则保护膜形成膜彼此不附着,越能够顺利地进行废料去除。
[0192]
《废料去除性的评价》在废料去除工序时,对所具有的40个圆形部分中,圆形部分的保护膜形成膜随着无用部分一起浮起的片数进行计数。浮起的片数越少,则表示保护膜形成膜彼此不附着,越能够顺利进行废料去除。
[0193]
将以上的结果汇总于表3。[表3]
[0194]
由表3可确认到,若保护膜形成膜彼此的附着力为19n以下,则在冲孔加工工序后,保护膜形成膜彼此不附着,能够顺利进行废料去除。此外可知,如实施例7所示,若切口宽度变窄,则有冲孔加工工序后保护膜形成膜彼此附着而无法顺利进行废料去除的倾向。工业实用性
[0195]
如上所述,根据本发明,可提供一种即使在冲孔加工时的切口宽度较窄的情况下也能够充分抑制废料去除的不良的保护膜形成用片及其制造方法。