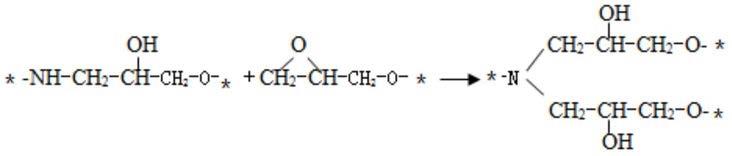
1.本发明涉及防腐蚀材料技术领域,具体而言,涉及一种高温耐磨重防腐粉末涂料及其制备方法和涂装方法。
背景技术:
2.油田采油过程中,需要大量使用油井管和抽油机,油井管和抽油杆在油井管内长期做往复运动,不可避免地相互产生摩擦,同时其所接触的腐蚀环境主要包油气井产出物等在内的复杂介质,腐蚀类型主要是硫化氢、二氧化碳、溶解氧及硫酸盐还原菌srb等。如何提高油井管和抽油杆的耐腐蚀性和耐磨性等是当前石油天然气钻采所面临的关键技术问题,但由于腐蚀环境苛刻,一般的有机涂层难以达到其耐磨和腐蚀防护的要求。
3.目前油田使用的耐磨油井管大多为钨基合金镀层油井管,抽油杆大多为玻璃钢抽油杆或钨基合金镀层抽油杆,玻璃钢抽油杆价格比较低,但使用效果差,杆的柔韧性差,容易磨损掉渣,堵塞抽油泵。钨基合金镀层油井管和抽油杆耐磨性能好,但价格昂贵,需要电镀,不符合环保要求,而且不耐油井管内溶解氧的腐蚀。
4.申请公布号为cn101070449a的中国申请专利公开了一种二硫化钼基防腐减磨涂料,以双酚a环氧树脂作为涂层主成膜物,双氰胺或葵二酸二酰肼作为固化剂,二硫化钼作为耐磨材料制得。首先,从涂层主成膜物的化学结构分析,双酚a环氧树脂耐化学腐蚀和耐热性能都不如酚醛环氧树脂,通过对比实验验证表明:采用的双酚a环氧树脂作为涂层成膜物难以抵抗高温高压下h2s、co2腐蚀,不能满足油井管涂层技术标准sy/t 6717
‑
2016的要求;其次,从实施案例分析其所制得的防腐减磨涂料为溶剂型涂料,其有机溶剂含量超过50%,不符合当前的国家环保要求。
5.申请公布号为cn101423726a的中国申请专利公开了一种二硫化钼高分散改性环氧树脂耐磨涂层材料及其制备方法,也是以双酚a环氧树脂作为涂层主成膜物,胺类树脂作为固化剂,二硫化钼作为耐磨材料制得,其存在的问题和缺点与专利cn101070449a是一样的,同样不能满足油井管和抽油杆技术指标要求和国家环保要求。
6.文献《高耐磨性防腐涂料在钻杆中的应用》介绍了由美国tuboscope公司研制的新型耐磨防腐涂料tk
‑
34xt,其性能指标能达到油井管涂层技术标准sy/t 6717
‑
2016的要求,但未介绍其涂料的组成成分,且该涂料为溶剂型液体涂料,不符合国家环保要求。
技术实现要素:
7.本发明的主要目的在于提供一种高温耐磨重防腐粉末涂料及其制备方法和涂装方法,以解决现有技术中耐磨涂料不环保、不能耐受高温高压下硫化氢、二氧化碳腐蚀的问题。
8.为了实现上述目的,根据本发明的一个方面,提供了一种高温耐磨重防腐粉末涂料,包括:按质量份计,酚醛改性环氧树脂50~65份、固化剂3~9份、有机耐磨填料3~5份、无机耐磨填料5~10份、固体耐磨润滑剂3~7份、固化促进剂0.2~0.5份、流平剂0.8~1.5
份、颜填料15~30份。
9.进一步地,酚醛改性环氧树脂为苯酚甲醛环氧树脂和/或甲酚甲醛环氧树脂,优选酚醛改性环氧树脂的环氧当量为190~280。
10.进一步地,固化剂为双氰胺类固化剂,优选固化剂与酚醛改性环氧树脂的当量比例为 0.8~1.2。
11.进一步地,有机耐磨填料为聚四氟乙烯粉末和/或聚丙烯粉末,优选有机耐磨填料的粒径小于5μm。
12.进一步地,无机耐磨填料选自氧化锆粉末、氧化铈粉末、氮化硼粉末中的一种或多种,优选无机耐磨填料的粒径小于200nm。
13.进一步地,固体耐磨润滑剂为二硫化钼和/或乙撑双硬脂酰胺,优选固体耐磨润滑剂的粒径在325~1250目之间。
14.进一步地,有机耐磨填料、无机耐磨填料、固体耐磨润滑剂的总质量份为17~21份。
15.进一步地,颜填料为颜料、钛白粉和石英粉中的两种或多种;优选颜填料的粒径在 600~1250目之间。
16.进一步地,固化促进剂选自二甲基咪唑、2
‑
甲基咪唑脲、三氟化硼乙胺络合物中的一种或多种。
17.进一步地,流平剂选自聚丙烯酸甲酯、有机改性聚硅氧烷、氟碳化合物中的一种或多种。
18.为了实现上述目的,根据本发明的一个方面,提供了一种高温耐磨重防腐粉末涂料的制备方法,制备方法包括:按照上述高温耐磨重防腐粉末涂料的组成称取各组分;将上述组分混合,得到预混料;将预混料进行熔融混炼、挤出、压片,得到成型物;将成型物粉碎,得到高温耐磨重防腐粉末涂料。
19.根据本发明的另一方面,提供了一种上述高温耐磨重防腐粉末涂料的涂装方法,涂装方法采用静电热喷涂。
20.应用本发明的技术方案,高温耐磨粉末涂料的组成成分均为市购材料,简单易得,成本低廉;采用高强度、耐热、耐酸碱的酚醛改性环氧树脂作为主成膜物,在h2s/co2严苛的腐蚀环境下仍能保持长效防腐性能,减少了因腐蚀而造成的油井维护和维修费用,同时,采用有机耐磨材料和无机耐磨材料复配,形成互穿网络,一方面通过高于钢铁硬度的无机耐磨材料有效抵御了钢铁对涂层的磨耗,另一方面,通过有机高分子聚合物耐磨材料的“弹性让渡”降低磨耗压力,再加上固体润滑剂的作用,减少摩擦面的摩擦系数,从而可以利用本技术的高温耐磨重防腐粉末涂料得到具有高温耐磨的防腐蚀涂层。此外,本技术所制备的高温耐磨涂料为固体涂料,在生产和使用过程中零voc排放,满足了国家绿色环保的要求。可见,本技术的涂料为固体涂料,不但高耐磨,而且在严苛的腐蚀环境下能保持长效防腐,同时又是符合当前国家环保要求的高性能防腐涂层材料。
具体实施方式
21.需要说明的是,在不冲突的情况下,本技术中的实施例及实施例中的特征可以相互组合。下面将结合实施例来详细说明本发明。
22.如本技术背景技术所分析的,现有技术中耐磨涂料存在不环保、不能耐受高温高压下硫化氢、二氧化碳腐蚀等问题,不能满足油井管涂层技术标准。为了解决该问题,本技术提供了一种高温耐磨重防腐粉末涂料及其制备方法和涂装方法。
23.在本技术的一种典型的实施方式中,提供了一种高温耐磨重防腐粉末涂料,包括:按质量份计,酚醛改性环氧树脂50~65份、固化剂3~9份、有机耐磨填料3~5份、无机耐磨填料 5~10份、固体耐磨润滑剂3~7份、颜填料15~30份、固化促进剂0.2~0.5份、流平剂0.8~1.5 份。
24.本技术高温耐磨粉末涂料的组成成分均为市购材料,简单易得,成本低廉;采用高强度、耐热、耐酸碱的酚醛改性环氧树脂作为主成膜物,在h2s/co2严苛的腐蚀环境下仍能保持长效防腐性能,减少了因腐蚀而造成的油井维护和维修费用,同时,采用有机耐磨材料和无机耐磨材料复配,形成互穿网络,一方面通过高于钢铁硬度的无机耐磨材料有效抵御了钢铁对涂层的磨耗,另一方面,通过有机高分子聚合物耐磨材料的“弹性让渡”降低磨耗压力,再加上固体润滑剂的作用,减少摩擦面的摩擦系数,从而可以利用本技术的高温耐磨重防腐粉末涂料得到具有高温耐磨的防腐蚀涂层。此外,本技术所制备的高温耐磨涂料为固体涂料,在生产和使用过程中零voc排放,满足了国家绿色环保的要求。可见,本技术的涂料为固体涂料,不但高耐磨,而且在严苛的腐蚀环境下能保持长效防腐,同时又是符合当前国家环保要求的高性能防腐涂层材料。
25.同时,本技术的高温耐磨重防腐粉末涂料还包括颜填料、固化促进剂和流平剂,因此,既可以使该高温耐磨重防腐粉末涂料具有良好的遮盖力,而且具有快速固化的优势、可以提高作业效率,同时利用流平剂的作用可以加快涂料形成平整光滑均匀涂膜的速率。
26.为了提高涂层耐h2s、co2腐蚀性能,上述酚醛改性环氧树脂为苯酚甲醛改性环氧树脂和 /或甲酚甲醛环氧树脂。
27.作为本技术的固化剂,可以选择酚醛改性环氧树脂常用的固化剂种类,为了提高固化效率,优选上述固化剂为双氰胺类固化剂,比如双氰胺、芳香族改性双氰胺等,上述芳香族改性双氰胺可以为瑞士ciba geigy公司的ht2833,ht2844,日本旭化成公司的aehd
‑
610, aehd
‑
210。
28.利用上述双氰胺作为固化剂时,固化成膜机理如下:双氰胺固化剂含有两个活泼氢原子,首先是伯胺上的活泼氢原子与酚醛改性环氧树脂的环氧基团进行加成反应,然后是产生的仲胺上的活泼氢与另一个环氧基团进行加成反应,此外,反应体系中的羟基也参与环氧基团反应,最终形成高度交联的三维网状结构,主要反应过程如下所示:
29.a.伯胺上的活泼氢原子与酚醛环氧树脂的环氧基团进行加成反应:
[0030][0031]
b.上述反应产生的仲胺上的活泼氢与酚醛环氧树脂的另一个环氧基团进行加成反应:
[0032][0033]
c.反应体系中的羟基也参与环氧基团反应:
[0034][0035]
为了使酚醛改性环氧树脂形成尽可能稳定的交联网络,优选酚醛改性环氧树脂的环氧当量为190~280,进一步优选固化剂与酚醛改性环氧树脂的当量比例为0.8~1.2。
[0036]
用于本技术的有机耐磨填料可以从现有技术中常用的有机耐磨材料中进行选择,为了使其在高温环境中更稳定地发挥耐磨作用,优选上述有机耐磨填料为聚四氟乙烯粉末和/或聚丙烯粉末。为了提高有机耐磨填料和其它组分的混合均匀性,优选上述有机耐磨填料的粒径小于5μm。
[0037]
用于本技术的无机耐磨填料也可以从现有技术中常用的无机耐磨材料中进行选择,为了提高其对高温和腐蚀环境的适应能力,优选上述无机耐磨填料选自氧化锆粉末、氧化铈粉末、氮化硼粉末中的一种或多种。同样地,为了提高无机耐磨填料和其他有机基材的相容性,优选上述无机耐磨填料的粒径小于200nm。
[0038]
在一些实施例中,上述固体耐磨润滑剂为二硫化钼和/或乙撑双硬脂酰胺,上述二硫化钼和乙撑双硬脂酰胺的润滑效果较为突出,且具有优异的耐温耐腐蚀性能。为了提高润滑效果的发挥,优选固体耐磨润滑剂的粒径在325~1250目之间。
[0039]
本技术一些实施例中,为了尽可能提高涂料形成的涂层的耐磨性和稳定性,优选上述有机耐磨填料、无机耐磨填料、固体耐磨润滑剂的总质量份为17~21份。
[0040]
本技术对颜填料的种类没有特别的限制,为了尽可能提高涂料的遮盖力,优选颜填料为颜料、钛白粉和石英粉中的两种或多种;优选颜填料的粒径为600~1250目。
[0041]
为了进一步适应本技术的酚醛改性环氧树脂的树脂体系,加快涂料固化,在一些实施例中,固化促进剂为二甲基咪唑。当然,本领域技术人员也可以选择其他类型的固化促进剂,比如2
‑
甲基咪唑脲、三氟化硼乙胺络合物。
[0042]
在一些实施例中,为了使流平剂更充分第在体系中发挥作用,优选流平剂为聚丙烯酸甲酯。当然,本领域技术人员也可以选择其他类型的流平剂,比如有机改性聚硅氧烷、氟碳化合物。
[0043]
在本技术的一些实施例中,上述涂料包括酚醛改性环氧树脂的质量含量为50~65%、固化剂的质量含量3~9%、有机耐磨填料的质量含量3~5%、无机耐磨填料的质量含量5~10%、固体耐磨润滑剂的质量含量为3~7%、颜填料15~30%、固体促进剂0.2~0.5%、流平剂0.8~1.5%。优选上述涂料包括酚醛改性环氧树脂的质量含量为50~65%、固化剂的质量含量3~8.6%、有机耐磨填料的质量含量3~5%、无机耐磨填料的质量含量5~10%、固体耐磨润滑剂的质量含量为3~7%、颜填料15~30%、固体促进剂0.2~0.5%、流平剂0.8~1.5%。
[0044]
在本技术另一种典型的实施方式中,提供了一种高温耐磨重防腐粉末涂料的制备方法。该制备方法包括:按照上述高温耐磨重防腐粉末涂料的组成称取各组分;将组分预混合,得到预混料;将预混料进行混炼、挤出、压片,得到成型物;将成型物粉碎,得到高温耐磨重防腐粉末涂料。
[0045]
本技术的高温耐磨重防腐粉末涂料的制备过程中,不需要使用水或有机溶剂,完全符合环保要求;另外,上述过程中各步骤均为现有技术常规操作所能实现的步骤,因此易于推广使用,所得到的高温耐磨重防腐粉末涂料为固体涂料,不但高耐磨,而且在严苛的腐蚀环境下能保持长效防腐,同时又是符合当前国家环保要求的高性能防腐涂层材料。
[0046]
上述预混采用高速预混器实施。上述粉碎可以采用本领域常用的气流粉碎。
[0047]
在本技术又一种典型的实施方式中,提供了一种上述高温耐磨重防腐粉末涂料的涂装方法,该涂装方法采用静电热喷涂。该涂装方法可以实现零voc排放,一次厚涂成膜,涂装施工高效,特别适用于工厂自动化流水线作业涂装。所得到的涂层不但高耐磨,而且在严苛的腐蚀环境下能保持长效防腐,同时又符合当前国家环保要求。
[0048]
以下结合具体实施例对本技术作进一步详细描述,这些实施例不能理解为限制本技术所要求保护的范围。
[0049]
实施例1
[0050]
实施例1的高温耐磨重防腐粉末涂料包括:苯酚甲醛环氧树脂(环氧当量为270)的质量含量为50份、双氰胺3.9份(双氰胺与苯酚甲醛环氧树脂的当量比例为1.0)、聚四氟乙烯微粉(粒径小于5μm,滴熔点大于300℃)5份、纳米氧化锆(粒径小于200nm)6份、二硫化钼6 份(粒径在325~1250目之间)、二甲基咪唑0.3份、聚丙烯酸甲酯1.5份、钛白粉、石英粉和炭黑27.3份(粒径在600~1250目之间)。
[0051]
按上述配比将物料称量投入高速预混器中,以3000转/分钟的转速在室温下混料3min,混合均匀后通过送料管道送入挤出机,经挤出机熔融混炼一次挤出,挤出机温度控制:混炼区温度为75℃,挤出区温度为95℃。混炼挤出的物料经过压片机压至1mm厚,经冷却、破碎成5~10mm2的薄片,然后经过acm磨磨成粉末,并经旋风分离器分离,再过180目筛筛分得到粉末涂料。
[0052]
实施例2
[0053]
本实施例2与实施例1基本相同,不同之处在于,高温耐磨重防腐粉末涂料的组分包括:苯酚甲醛环氧树脂(环氧当量为240)60份、双氰胺4.2份(双氰胺与苯酚甲醛环氧树脂的当量比例为0.8)、聚四氟乙烯微粉(粒径小于5μm,滴熔点大于150℃)5份、纳米氧化锆(粒径小于200nm)6份、二硫化钼(粒径在325~1250目之间)6份,二甲基咪唑0.3份,聚丙烯酸甲酯1份,钛白粉和石英粉(粒径在600~1250目之间)17.5份。
[0054]
实施例3
[0055]
本实施例3与实施例1基本相同,不同之处在于,高温耐磨重防腐粉末涂料的组分包括:苯酚甲醛环氧树脂(环氧当量为190)65份、双氰胺8.6份(双氰胺与苯酚甲醛环氧树脂的当量比例为1.2)、聚四氟乙烯微粉(粒径小于5μm,滴熔点大于300℃)5份、纳米氧化锆(粒径小于200nm)6份、二硫化钼(粒径在325~1250目之间)6份,二甲基咪唑0.3份,聚丙烯酸甲酯0.8份,钛白粉、石英粉和炭黑(粒径在600~1250目之间)8.3份。
[0056]
实施例4
[0057]
本实施例4与实施例1基本相同,不同之处在于,高温耐磨重防腐粉末涂料的组分包括:苯酚甲醛环氧树脂(环氧当量为270)50份、双氰胺3.9份(双氰胺与苯酚甲醛环氧树脂的当量比例为1.0)、聚四氟乙烯微粉(粒径小于5μm,滴熔点大于300℃)3份、纳米氧化锆(粒径小于200nm)6份、二硫化钼(粒径在325~1250目之间)6份,二甲基咪唑0.3份,聚丙烯酸甲酯1.5份,钛白粉、石英粉和炭黑(粒径在600~1250目之间)29.3份。
[0058]
实施例5
[0059]
本实施例5与实施例1基本相同,不同之处在于,高温耐磨重防腐粉末涂料的组分包括:苯酚甲醛环氧树脂(环氧当量为270)50份、双氰胺3.9份(双氰胺与苯酚甲醛环氧树脂的当量比例为1.0)、聚四氟乙烯微粉(粒径小于5μm,滴熔点大于300℃)5份、纳米氧化锆(粒径小于200nm)10份、二硫化钼(粒径在325~1250目之间)6份,二甲基咪唑0.3份,聚丙烯酸甲酯1.5份,钛白粉、石英粉和炭黑(粒径在600~1250目之间)23.3份。
[0060]
实施例6
[0061]
本实施例6与实施例1基本相同,不同之处在于,高温耐磨重防腐粉末涂料的组分包括:苯酚甲醛环氧树脂(环氧当量为270)50份、双氰胺3.9份(双氰胺与苯酚甲醛环氧树脂的当量比例为1.0)、聚四氟乙烯微粉(粒径小于5μm,滴熔点大于300℃)5份、纳米氧化锆(粒径小于200nm)5份、二硫化钼(粒径在325~1250目之间)6份,二甲基咪唑0.3份,聚丙烯酸甲酯1.5份,钛白粉、石英粉和炭黑(粒径在600~1250目之间)28.3份。
[0062]
实施例7
[0063]
本实施例7与实施例1基本相同,不同之处在于,高温耐磨重防腐粉末涂料的组分包括:苯酚甲醛环氧树脂(环氧当量为270)50份、双氰胺3.9份(双氰胺与苯酚甲醛环氧树脂的当量比例为1.0)、聚四氟乙烯微粉(粒径小于5μm,滴熔点大于300℃)5份、纳米氧化锆(粒径小于200nm)9份、二硫化钼(粒径在325~1250目之间)3份,二甲基咪唑0.3份,聚丙烯酸甲酯1.5份,钛白粉、石英粉和炭黑(粒径在600~1250目之间)27.3份。
[0064]
实施例8
[0065]
本实施例8与实施例1基本相同,不同之处在于,高温耐磨重防腐粉末涂料的组分包括:苯酚甲醛环氧树脂(环氧当量为270)50份、双氰胺3.9份(双氰胺与苯酚甲醛环氧树脂的当量比例为1.0)、聚四氟乙烯微粉(粒径小于5μm,滴熔点大于300℃)4份、纳米氧化锆(粒径小于200nm)6份、二硫化钼(粒径在325~1250目之间)7份,二甲基咪唑0.3份,聚丙烯酸甲酯1.5份,钛白粉、石英粉和炭黑(粒径在600~1250目之间)27.3份。
[0066]
实施例9
[0067]
本实施例9与实施例1基本相同,不同之处在于,高温耐磨重防腐粉末涂料的组分包括:甲酚甲醛环氧树脂(环氧当量为270)50份、双氰胺3.9份(双氰胺与甲酚甲醛环氧树脂的当量比例为1.0)、聚四氟乙烯微粉(粒径小于5μm,滴熔点大于300℃)5份、纳米氧化锆(粒径小于200nm)6份、二硫化钼(粒径在325~1250目之间)6份,二甲基咪唑0.3份,聚丙烯酸甲酯1.5份,钛白粉、石英粉和炭黑(粒径在600~1250目之间)27.7份。
[0068]
实施例10
[0069]
本实施例10与实施例1基本相同,不同之处在于,高温耐磨重防腐粉末涂料的组分包括:苯酚甲醛环氧树脂25份,甲酚甲醛环氧树脂25份,苯酚甲醛环氧树脂和甲酚甲醛环氧树脂的混合物环氧当量为260、双氰胺4.0份(双氰胺与苯酚甲醛环氧树脂的当量比例为
1.0)、聚四氟乙烯微粉(粒径小于5μm,滴熔点大于300℃)5份、纳米氧化锆(粒径小于200nm)6份、二硫化钼(粒径在325~1250目之间)6份,二甲基咪唑0.3份、聚丙烯酸甲酯1.5份、钛白粉、石英粉和炭黑(粒径在600~1250目之间)27.2份。
[0070]
实施例11
[0071]
本实施例11与实施例1基本相同,不同之处在于,高温耐磨重防腐粉末涂料的组分包括:苯酚甲醛环氧树脂(环氧当量为270)50份、双氰胺3.9份(双氰胺与苯酚甲醛环氧树脂的当量比例为1.0)、聚四氟乙烯微粉(粒径小于5μm,滴熔点大于300℃)5份、纳米氧化锆(粒径小于200nm)6份、乙撑双硬脂酰胺(粒径在325~1250目之间)6份,二甲基咪唑0.3份、聚丙烯酸甲酯1.5份、钛白粉、石英粉和炭黑(粒径在600~1250目之间)27.3份。
[0072]
实施例12
[0073]
本实施例12与实施例1基本相同,不同之处在于,高温耐磨重防腐粉末涂料的组分包括:苯酚甲醛环氧树脂(环氧当量为270)50份、双氰胺3.9份(双氰胺与苯酚甲醛环氧树脂的当量比例为1.0)、聚四氟乙烯微粉(粒径小于5μm,滴熔点大于300℃)5份、纳米氧化锆(粒径在250~500nm)6份、二硫化钼3份、乙撑双硬脂酰胺3份,二硫化钼和乙撑双硬脂酰胺粒径在325~1250目之间,二甲基咪唑0.3份,聚丙烯酸甲酯1.5份,钛白粉、石英粉和炭黑(粒径在600~1250目之间)27.3份。
[0074]
实施例13
[0075]
本实施例13与实施例1基本相同,不同之处在于,高温耐磨重防腐粉末涂料包括:苯酚甲醛环氧树脂(环氧当量为270)的质量含量为50份、双氰胺3.9份(双氰胺与苯酚甲醛环氧树脂的当量比例为1.0)、聚丙烯微粉(粒径小于5μm,滴熔点大于160℃)5份、纳米氧化铈(粒径小于200nm)6份、二硫化钼6份(粒径在325~1250目之间)、2
‑
甲基咪唑脲0.3份、聚丙烯酸甲酯1.5份、钛白粉、石英粉和炭黑27.3份(粒径在600~1250目之间)。
[0076]
实施例14
[0077]
本实施例14与实施例1基本相同,不同之处在于,高温耐磨重防腐粉末涂料包括:苯酚甲醛环氧树脂(环氧当量为270)的质量含量为50份、双氰胺3.9份(双氰胺与苯酚甲醛环氧树脂的当量比例为1.0)、聚四氟乙烯微粉(粒径小于5μm,滴熔点大于300℃)3份、聚丙烯微粉(粒径小于5μm,滴熔点大于160℃)2份、纳米氧化锆(粒径小于200nm)6份、二硫化钼6份(粒径在325~1250目之间)、2
‑
甲基咪唑脲0.3份、聚丙烯酸甲酯1.5份、钛白粉、石英粉和炭黑27.3份(粒径在600~1250目之间)。
[0078]
对比例1
[0079]
商购美国tuboscope公司研制的tk
‑
34xt油井管耐磨涂层(以其涂层性能指标为标准进行对比)。
[0080]
对比例2
[0081]
本对比例2与实施例1基本相同,不同之处在于,高温耐磨重防腐粉末涂料的组分包括:苯酚甲醛环氧树脂(环氧当量为180)65份、双氰胺9.9份(双氰胺与苯酚甲醛环氧树脂的当量比例为1.3)、聚四氟乙烯微粉5份、纳米氧化锆6份,二硫化钼(粒径在325~1250目之间)6份,二甲基咪唑0.3份、聚丙烯酸甲酯0.8份、钛白粉、石英粉和炭黑7份(粒径在600~1250 目之间)。
[0082]
对比例3
[0083]
本对比例3与实施例1基本相同,不同之处在于,高温耐磨重防腐粉末涂料的组分包括:苯酚甲醛环氧树脂(环氧当量为290)50份、双氰胺2.5份(双氰胺与苯酚甲醛环氧树脂的当量比例为0.7)、聚四氟乙烯微粉5份、纳米氧化锆6份、二硫化钼(粒径在325~1250目之间)6份、二甲基咪唑0.3份、聚丙烯酸甲酯1.5份、钛白粉、石英粉和炭黑28.7份(粒径在 600~1250目之间)。
[0084]
对比例4
[0085]
本对比例4与实施例1基本相同,不同之处在于,高温耐磨重防腐粉末涂料的组分包括:苯酚甲醛环氧树脂(环氧当量为290)50份、双氰胺1.2份(双氰胺与苯酚甲醛环氧树脂的当量比例为0.7)、聚四氟乙烯微粉5份、纳米氧化锆6份、二硫化钼(粒径在325~1250目之间)6份、二甲基咪唑0.3份、聚丙烯酸甲酯1.5份、钛白粉、石英粉和炭黑30份(粒径在 600~1250目之间)。
[0086]
对比例5
[0087]
本对比例5与实施例1基本相同,不同之处在于,高温耐磨重防腐粉末涂料的组分包括:苯酚甲醛环氧树脂(环氧当量为270)50份、双氰胺3.9份(双氰胺与苯酚甲醛环氧树脂的当量比例为1.0)、聚四氟乙烯微粉11份、二硫化钼(粒径在325~1250目之间)6份、二甲基咪唑0.3份、聚丙烯酸甲酯1.5份、钛白粉、石英粉和炭黑27.3份(粒径在600~1250目之间)。
[0088]
对比例6
[0089]
本对比例6与实施例1基本相同,不同之处在于,高温耐磨重防腐粉末涂料的组分包括:苯酚甲醛环氧树脂(环氧当量为270)50份、双氰胺3.9份(双氰胺与苯酚甲醛环氧树脂的当量比例为1.0)、纳米氧化锆11份、二硫化钼(粒径在325~1250目之间)6份、二甲基咪唑 0.3份、聚丙烯酸甲酯1.5份、钛白粉、石英粉和炭黑27.3份(粒径在600~1250目之间)。
[0090]
对比例7
[0091]
本对比例7与实施例1基本相同,不同之处在于,高温耐磨重防腐粉末涂料的组分包括:苯酚甲醛环氧树脂(环氧当量为270)50份、双氰胺3.9份(双氰胺与苯酚甲醛环氧树脂的当量比例为1.0)、聚四氟乙烯微粉8份、纳米氧化锆9份、二甲基咪唑0.3份、聚丙烯酸甲酯1.5份、钛白粉、石英粉和炭黑27.3份(粒径在600~1250目之间)。
[0092]
对比例8
[0093]
本对比例8与实施例1基本相同,不同之处在于,高温耐磨重防腐粉末涂料的组分包括:苯酚甲醛环氧树脂(环氧当量为270)35份、双氰胺2.7份(双氰胺与苯酚甲醛环氧树脂的当量比例为1.0)、聚四氟乙烯微粉5份、纳米氧化锆6份、二硫化钼(粒径在325~1250目之间)6份、二甲基咪唑0.3份、聚丙烯酸甲酯1.5份、钛白粉、石英粉和炭黑43.5份(粒径在 600~1250目之间)。
[0094]
对比例9
[0095]
本对比例9与实施例1基本相同,不同之处在于,高温耐磨重防腐粉末涂料的组分包括:苯酚甲醛环氧树脂(环氧当量为190)70份、双氰胺9.3份、(双氰胺与苯酚甲醛环氧树脂的当量比例为1.2)、聚四氟乙烯微粉5份、纳米氧化锆6份、二硫化钼(粒径在325~1250目之间)6份、二甲基咪唑0.3份、聚丙烯酸甲酯0.8份、钛白粉、石英粉和炭黑2.6份(粒径在600~1250目之间)。
[0096]
对比例10
[0097]
本对比例10与实施例1基本相同,不同之处在于,高温耐磨重防腐粉末涂料的组分包括:苯酚甲醛环氧树脂(环氧当量为270)50份、双氰胺3.9份(双氰胺与苯酚甲醛环氧树脂的当量比例为1.0)、聚四氟乙烯微粉2份、纳米氧化锆6份、二硫化钼(粒径在325~1250目之间)6份、二甲基咪唑0.3份、聚丙烯酸甲酯1.5份、钛白粉、石英粉和炭黑30.3份(粒径在 600~1250目之间)。
[0098]
对比例11
[0099]
本对比例11与实施例1基本相同,不同之处在于,高温耐磨重防腐粉末涂料的组分包括:苯酚甲醛环氧树脂(环氧当量为270)50份、双氰胺3.9份(双氰胺与苯酚甲醛环氧树脂的当量比例为1.0)、聚四氟乙烯微粉5份、纳米氧化锆4份、二硫化钼(粒径在325~1250目之间)6份、二甲基咪唑0.3份、聚丙烯酸甲酯1.5份、钛白粉、石英粉和炭黑29.3份(粒径在 600~1250目之间)。
[0100]
对比例12
[0101]
本对比例12与实施例1基本相同,不同之处在于,高温耐磨重防腐粉末涂料的组分包括:苯酚甲醛环氧树脂(环氧当量为270)50份、双氰胺3.9份(双氰胺与苯酚甲醛环氧树脂的当量比例为1.0)、聚四氟乙烯微粉5份、纳米氧化锆6份、二硫化钼(粒径在325~1250目之间)2份、二甲基咪唑0.3份、聚丙烯酸甲酯1.5份、钛白粉、石英粉和炭黑31.3份(粒径在 600~1250目之间)。
[0102]
对各实施例和对比例的涂料进行涂装施工方法:
[0103]
基材表面处理:彻底清除油井管和抽油杆表面的油脂和污垢等附着物,在室温,相对湿度小于90%的条件下进行喷砂除锈,除锈等级应达到sa2.5级,锚纹深度40μm;
[0104]
涂装施工工艺:经喷砂除锈的油井管和抽油杆放入170℃的预热炉预热60min;马上静电喷涂各实施例和对比例制得的粉末涂料,再放入210℃的烘炉烘烤60min,出炉自然冷却,涂层的厚度为350μm~650μm,厚度对涂层性能影响不大;然后进行涂层性能检测。第二次耐磨性试验是在第一次耐磨性试验中磨损的涂层表面进行再次耐磨性试验。
[0105]
涂层性能测试检测结果表明,本技术实施例的涂层性能指标完全满足sy/t 6717
‑
2016标准要求,其耐磨性能达到甚至超过了国外知名品牌的同类产品,具体见表1和表2。本技术对比例的涂层性能指标见表3和表4。
[0106]
表1
[0107]
[0108][0109]
[0110]
表2
[0111]
[0112][0113]
表3
[0114]
[0115]
[0116][0117]
表4
[0118]
[0119][0120]
从以上的描述中,可以看出,本发明上述的实施例实现了如下技术效果:
[0121]
本技术高温耐磨粉末涂料的组成成分均为市购材料,简单易得,成本低廉;采用高强度、耐热、耐酸碱的酚醛改性环氧树脂作为主成膜物,在h2s/co2严苛的腐蚀环境下仍能保持长效防腐性能,减少了因腐蚀而造成的油井维护和维修费用,同时,采用有机耐磨材料和无机耐磨材料复配,形成互穿网络,一方面通过高于钢铁硬度的无机耐磨材料有效抵御了钢铁对涂层的磨耗,另一方面,通过有机高分子聚合物耐磨材料的“弹性让渡”降低磨耗压力,再加上固体润滑剂的作用,减少摩擦面的摩擦系数,从而可以利用本技术的高温耐磨重防腐粉末涂料得到具有高温耐磨的防腐蚀涂层。此外,本技术所制备的高温耐磨涂料为固体涂料,在生产和使用过程中零voc排放,满足了国家绿色环保的要求。可见,本技术的涂料为固体涂料,不但高耐磨,而且在严苛的腐蚀环境下能保持长效防腐,同时又是符合当前国家环保要求的高性能防腐涂层材料。为了提高涂料对h2s、co2的防腐蚀性能,上述酚醛改性环氧树脂为酚醛改性环氧树脂和/或甲酚甲醛环氧树脂。同时,本技术的高温耐磨重防腐粉末涂料还包括颜填料、固化促进剂和流平剂,因此,既可以使该高温耐磨重防腐粉末涂料具有良好的遮盖力,而且具有快速固化的优势、可以提高作业效率,同时利用流平剂的作用可以加快涂料形成平整光滑均匀涂膜的速率。
[0122]
以上所述仅为本发明的优选实施例而已,并不用于限制本发明,对于本领域的技术人员来说,本发明可以有各种更改和变化。凡在本发明的精神和原则之内,所作的任何修改、等同替换、改进等,均应包含在本发明的保护范围之内。