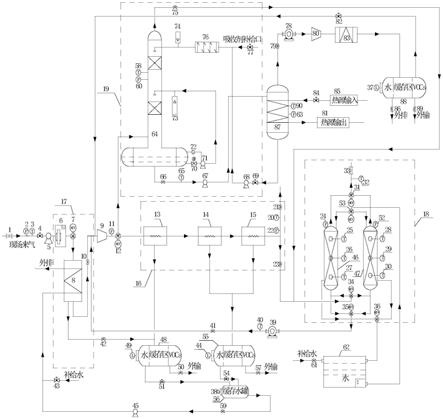
加压多级吸收/冷凝
—
吸附的二合一油气回收系统
技术领域
1.本实用新型涉及一种加压多级吸收/冷凝—吸附的二合一油气回收系统,属于油气回收技术领域。
背景技术:
2.随着我国工业化进程不断加快,能源需求不断增加,轻质油品由于其易挥发性,在开采、加工、储存、运输和使用等过程中产生大量油气,对大气造成严重污染。油气回收技术发展至今,吸收法、吸附法、冷凝法和膜分离法四种油气回收技术最为成熟。按照工艺温度的不同吸收法可分为常温吸收和低温吸收,根据组分间溶解度差异进行处理,但是传统的吸收工艺出口浓度较高,难以满足严格的排放要求;冷凝法是根据各组分沸点高低,在低温条件下回收油气的方法,但是该方法对冷凝温度要求严格,运行能耗大;虽然膜分离法的回收效果良好,但是膜的制作成本较高,对大处理量油气不适用;而吸附法由于其工艺流程简单,成本较低且易于回收,被广泛应用于油气回收技术,但吸附剂的吸附容量有限,吸附穿透后出口浓度会急剧上升,吸附剂解吸再生困难,现阶段适合于工业应用的解吸工艺的解吸效果均不理想,吸附剂重复利用率较低,不仅增加了油气回收技术的成本,也降低了资源利用率。因此,常规单一回收技术或者两种回收方法集成难以高效处理大流量、高浓度油气,且整个回收过程能耗高、资源浪费,无法达标排放。
技术实现要素:
3.本实用新型所要解决的技术问题是克服现有技术的缺陷,提供一种加压多级吸收/冷凝—吸附的二合一油气回收系统,利用加压冷却预处理、加压多级吸收/冷凝、多功能吸附塔吸附提高对大流量、高浓度油气的回收效率,降低运行能耗,实现超低浓度达标排放,充分利用吸收、冷凝、吸附各自优势,巧妙地实现模块组合式多功能回收。
4.为解决上述技术问题,本实用新型提供一种加压多级吸收/冷凝—吸附的二合一油气回收系统,包括预处理系统、加压多级吸收系统、吸附系统和加压多级冷凝系统,所述预处理系统分别与加压多级吸收系统、加压多级冷凝系统相连接;所述加压多级吸收系统包括多级吸收塔,所述多级吸收塔顶部排气口与所述吸附系统相连接,所述多级吸收塔底部富油出口与解吸塔相连接,所述解吸塔顶部排气口与油水分离器相连接;所述加压多级冷凝系统出气口连接大气或与吸附系统相连接,所述加压多级冷凝系统底部排液口与油水分离器相连接。
5.进一步地,所述的预处理系统包括加压设备、三通阀、水冷换热器、闸阀,现场来气集气管道经过阻火器、压力传感器、温度传感器、球阀、抽气泵与加压设备进口连接,加压设备出气口经过三通阀与水冷换热器进口连接,水冷换热器出气口经过闸阀与压缩机进气口连接。
6.进一步地,所述预处理系统通过压缩机与加压多级吸收系统相连接,压缩机出口经过压力传感器、三通阀连接多级吸收塔底部进气口,多级吸收塔顶部排气口经过闸阀与
吸附系统进气三通阀连接;多级吸收塔底部富油出口经过闸阀、温度传感器、离心泵与解吸塔顶部进口连接,多级吸收塔侧面排液口经过自动控制阀、离心泵与多级吸收塔下层喷淋口连接,解吸塔底部贫油出口经过闸阀、离心泵、换热器、流量计与多级吸收塔上层喷淋口连接;解吸塔顶部排气口经过闸阀、真空泵、压缩机、换热器与油水分离器连接,油水分离器顶部出气口经过闸阀与压缩机进口相连。
7.进一步地,所述预处理系统通过压缩机与加压多级冷凝系统相连接,所述加压多级冷凝系统包括依次连接的一级冷凝、二级冷凝和三级冷凝,压缩机出口经过压力传感器、三通阀连接一级冷凝进气口,三级冷凝出口连接大气或经过闸阀与吸附系统进气口三通阀连接,一级冷凝冷凝室底部排液口与油水分离器进口连接,二级冷凝与三级冷凝冷凝室底部排液口均与油水分离器进口连接,油水分离器底部均设有两个排放口,闸阀与缓存水罐进口连接,闸阀连接外输管道,缓存水罐出口经过离心泵与水冷换热器连接。
8.进一步地,所述吸附系统设有两个吸附塔,吸附塔进气口三通阀与三级冷凝出气口闸阀以及多级吸收塔出气口闸阀连接,吸附塔排气口三通阀与温度传感器、阻火器连接,吸附塔底部三通阀经过真空泵、温度传感器与压缩机进口连接,恒温水浴箱进出口分别与吸附塔、内部换热盘管进出口三通阀连接。
9.进一步地,所述油水分离器为卧式分离器,侧面设有液位计、油水分离器,内部左右两侧设有两个隔板,将油水分离器内部分为左侧水区、中间缓存区、右侧vocs存储区;油水分离器左侧水区连接缓存水罐,通过闸阀控制开闭;油水分离器与缓存水罐外部整体设有保温层,保温层厚度为100~300 mm。
10.进一步地,所述解吸塔内部设有密集换热器,换热器热源由外界提供,塔身侧面设有用于实时监测塔内温度的温度传感器和实时监测塔内压力的压力传感器。
11.进一步地,所述多级吸收塔为立式塔,所述多级吸收塔为分段喷淋式,设有两层喷淋,上层喷淋入口与流量计、换热器连接,换热器冷量由外界提供,上层喷淋量为10~100 m3/h;下层喷淋入口与离心泵、自动调节阀连接。
12.进一步地,所述加压多级冷凝系统包括一级冷凝,二级冷凝,三级冷凝,各级冷凝换热器温度分别设计为1~5℃、-40~-60℃和-70~-100℃,一级冷凝冷凝室的气体通道面积比为3.5~6.0:1,换热面积比为0.5~1.5:1;二级冷凝的气体通道面积比为5.5~8.0:1,换热面积比为1.5~3.5:1;三级冷凝冷凝室的气体通道面积比为3.0~5.0:1,换热面积比为0.5~1.5:1。
13.进一步地,所述油水分离器为卧式分离器,长度为1000~3000 mm,直径为500~1500 mm,侧面设有高度为400~1200 mm的液位计;油水分离器内部左右两侧设有两个高度500~1200 mm隔板,隔板之间距离为500~1200 mm,将油水分离器内部分为左侧水区、中间缓存区、右侧vocs存储区;油水分离器左侧水区连接缓存水罐,通过闸阀控制开闭,缓存水罐长度为800~1500 mm,直径500~1000 mm;油水分离器与缓存水罐外部整体设有保温层,保温层厚度为100~300 mm。
14.本实用新型所达到的有益效果:
15.1.本实用新型加压多级吸收/冷凝—吸附的二合一油气回收系统,相比于常压吸收或冷凝,充分发挥吸收、冷凝、吸附各自优势,避免了单一回收方法存在的弊端,巧妙地实现模块组合式多功能回收效果。
16.2.本实用新型可根据工程需要选择最优化的回收系统,对于大流量、高浓度、易与吸收剂互溶的油气采用“加压多级吸收—吸附”的回收系统,对于中流量、高浓度但轻烃含量低、高沸点的油气采用“加压多级冷凝—吸附”的回收系统,实现高回收率(≥99%),超低浓度(≤60 mg/m3)达标排放目标。
附图说明
17.图1为本实用新型一种加压多级吸收/冷凝—吸附的二合一油气回收系统流程图;
18.附图标记列示如下:
19.1、33—阻火器,2、11、22、24、52、60、63—压力传感器,3、20、25、26、27、28、29、30、32、40、58、65、90—温度传感器,4、43、51、54、69、77、82、84—球阀,5—抽气泵,6—加压设备,7、12、31、34、35、36、53—三通阀,8、76、83—换热器, 9、80—压缩机,10、21、23、41、42、50、57、59、61、66、75、79、86、89—闸阀,13—一级冷凝,14—二级冷凝,15—三级冷凝,16—加压多级冷凝系统,17—预处理系统,18—吸附系统,19—加压多级吸收系统,37、38、44、49、72—液位计,39、78—真空泵,45、67、68、71—离心泵,46、47—吸附塔,48、55、88—油水分离器,56—缓存水罐,62—恒温水浴箱,64—吸收塔,70—自动控制阀,73、74—流量计,81—热源输出,85—热源输入,87—解吸塔。
具体实施方式
20.下面结合附图对本实用新型作进一步描述。以下实施例仅用于更加清楚地说明本实用新型的技术方案,而不能以此来限制本实用新型的保护范围。
21.实施例一:
22.某码头装卸油过程中产生大量油气,油气排放量为1500 m3/h,浓度为563.367 g/m3,易溶于特种吸收剂的高浓度油气,要求处理后的油气排放浓度小于80 mg/m3,利用一种“加压多级吸收—吸附”的油气回收系统对其高效回收,借助附图1进行说明。
23.(1)本实用新型系统技术方案如下:
24.一种“加压多级吸收—吸附”的油气回收系统:该系统主要由阻火器1,压力传感器2、11、63,温度传感器3、40、90,球阀4、43、51、54、82、84,抽气泵5,三通阀12,换热器83,压缩机9、80,闸阀41、42、50、57、59、61、79、86、89,液位计37、38、44、49,真空泵39、78,离心泵45,油水分离器48、55、88,缓存水罐56,恒温水浴箱62,热源输出81,热源输入85,解吸塔87,加压多级冷凝系统16,预处理系统17,吸附系统18,加压多级吸收系统19以及管道组成。
25.①ꢀ
一种“加压多级吸收—吸附”的油气回收系统的预处理系统17由闸阀1,加压设备6,三通阀7以及水冷换热器8组成。
26.进一步,加压设备6压力为0.2 mpa。
27.进一步,水冷换热器8的气体通道面积比为5.0:1,换热面积比为1.5:1,冷却介质水温度为20℃。
28.②ꢀ
一种“加压多级吸收—吸附”的油气回收系统的加压多级吸收系统19由闸阀66、75,离心泵67、68、71,流量计73、74,球阀69、77,温度传感器58、65,多级吸收塔64,换热器76,自动控制阀70,压力传感器60以及液位计72组成。
29.进一步,多级吸收塔64为立式塔,高度5000 mm,直径1200 mm,多级吸收塔64设计
为分段喷淋式,设有两层喷淋,上层喷淋入口与流量计74、换热器76连接,柴油喷淋量为70 m3/h。
30.③ꢀ
一种“加压多级吸收—吸附”的油气回收系统的吸附系统吸附塔46、47,三通阀31、34、35、36、53,压力传感器24、52,温度传感器25、26、27、28、29、30、32以及阻火器33组成。
31.进一步,吸附塔46、47的高度为6000 mm,直径1500mm,内部设有翅片管,均匀分布于塔内,吸附塔46、47进气口由三通阀34控制切换。
32.进一步,吸附塔46、47内部设有换热器,换热器进出口由三通阀53、36控制开闭,与恒温水浴箱62进出口连接,恒温水浴箱62温度为85℃,其尺寸为长2000 mm,宽1200 mm,高1000 mm。
33.④ꢀ
一种“加压多级吸收—吸附”的油气回收系统的解吸塔87高度为3000 mm,直径1000 mm,内部设有密集换热器,热量由外界提供,塔身侧面装有温度传感器90、压力传感器63,实时监测塔内温度压力。
34.⑤ꢀ
一种“加压多级吸收—吸附”的油气回收系统的油水分离器48、88为卧式分离器,长度为2500 mm,直径1000 mm。
35.进一步,油水分离器48、88侧面设有高度为800 mm液位计,内部左右两侧设有2个高度为800 mm隔板,隔板之间距离为1200 mm,将油水分离器48、88内部分为左侧的水区、中间的缓存区、右侧的vocs存储区。
36.(2)一种“加压多级吸收—吸附”的油气回收系统连接方式如下:
37.①ꢀ
码头装卸现场来气集气管道经过阻火器1、压力传感器2、温度传感器3、球阀4、抽气泵5与加压设备6进口连接,加压设备6出口管道经过三通阀7与水冷换热器8进口连接,水冷换热器8出气口经过闸阀与压缩机9进气口连接,压缩机9出口与三通阀12连接。
38.②ꢀ
压缩机9出口经过压力传感器11、三通阀12连接多级吸收塔64底部进气口,多级吸收塔64顶部排气口经过闸阀75与吸附系统18进气三通阀34连接,多级吸收塔64底部富油出口经过闸阀66、温度传感器65、离心泵67与解吸塔87顶部进口连接,多级吸收塔64底部侧面排液口经过自动控制阀70、离心泵71与多级吸收塔64下层喷淋口连接,解吸塔87底部贫油出口经过闸阀69、离心泵68、换热器76、流量计74与多级吸收塔64上层喷淋口连接,解吸塔87顶部排气口经过闸阀79、真空泵78、压缩机80、换热器83与油水分离器88连接,油水分离器88顶部出气口经过闸阀82与压缩机9进口相连。
39.③ꢀ
吸附塔46、47进气口三通阀34与吸收塔64出口闸阀75连接,吸附塔46、47排气口三通阀31与温度传感器32、阻火器33连接,吸附塔46、47底部三通阀35经过真空泵39、温度传感器40与压缩机9进口连接,恒温水浴箱62进出口分别与吸附塔46、47内部换热盘管进出口三通阀53、36连接。
40.(3)一种“加压多级吸收—吸附”的油气回收系统回收方法如下:
41.①ꢀ
打开进气闸阀4,铁路装卸过程中产生的高浓度大流量油气在抽气泵5作用下经过阻火器1、压力传感器2、温度传感器3进入预处理系统17,经过加压设备6加压浓缩后,进入水冷换热器8冷却处理,产生的部分凝结液经过闸阀42储存于油水分离器48中,在油水分离器48分离作用下,冷凝水通过闸阀51存储于缓存水罐56中,液态油气外输再利用。
42.②ꢀ
预处理后油气经过压缩机9、压力传感器11、三通阀12后进入多级吸收塔64底
部进气口,在与低温吸收剂逆流接触作用下,大部分油气被低温吸收剂溶解吸收,产生的富油液沉降于多级吸收塔64底部,根据吸收塔64侧面的液位计72示数,自动控制阀70自行调节开度,部分富油吸收剂在离心泵71作用下,输送至多级吸收塔64下层喷淋口循环利用,大部分富油吸收剂在离心泵67作用下输送至解吸塔87解吸再生,经过加热抽真空后的新鲜吸收剂在离心泵68作用下经过闸阀69、换热器76被输送至吸收塔64上层喷淋口循环利用,换热器76冷量由外界提供;富油吸收剂经加热真空解吸后产生的油气经过压缩机80加压后进入换热器83,生成的混合液储存于油水分离器88中,分离后外输再利用;未液化的油气被输送至加压多级吸收系统19进气口与预处理后气体混合再返回到加压多级吸收系统19。
43.③ꢀ
经过加压多级吸收系统19处理后气体由多级吸收塔64顶部排出,打开截止阀75进入吸附系统18,通过调节进气三通阀34使气体先进入吸附塔46,待吸附塔46吸附穿透后,调节三通阀34、31,切换吸附塔47进行吸附,同时打开三通阀53、35、36,对吸附塔46抽真空解吸再生,解吸出的高浓度油气经过闸阀41与预处理后气体混合再返回到加压多级吸收系统19再处理,吸附塔加热源来自恒温水浴箱;先后经过加压冷却预处理、加压多级吸收、吸附后的高浓度大流量油气,吸附塔46、47出口排放浓度低于80 mg/m3,油气总回收率大于99%。
44.实施例二:
45.某炼化厂装卸油过程中排放大量油气,主要为c3及以上重组分,轻烃含量较少,排放量为500 m3/h,浓度为456.54 g/m3,要求处理后的油气排放浓度小于60 mg/m3,针对中流量、高浓度及轻烃组分含量低油气,利用一种“加压多级冷凝—吸附”的油气回收系统对其高效回收,借助附图1进行说明。
46.(1)本实用新型技术方案如下:
47.一种“加压多级冷凝—吸附”的油气回收系统:主要由阻火器1,压力传感器2、11、63,温度传感器3、40、90,球阀4、43、51、54、82、84,抽气泵5,三通阀12,换热器83,压缩机9、80,闸阀41、42、50、57、59、61、79、86、89,液位计37、38、44、49,真空泵39、78,离心泵45,油水分离器48、55、88,缓存水罐56,恒温水浴箱62,热源输出81,热源输入85,解吸塔87,多级加压冷凝系统16,预处理系统17,吸附系统18,加压多级吸收系统19以及管道组成。
48.①ꢀ
一种“加压多级冷凝—吸附”的油气回收系统的预处理系统17由加压设备6,三通阀7,水冷换热器8,以及闸阀10组成。
49.进一步,加压设备压力为0.2 mpa。
50.进一步,水冷换热器8的气体通道面积比为3.5:1,换热面积比为1.5:1,冷却介质水温度为15℃。
51.②
一种“加压多级冷凝—吸附”的油气回收系统的加压多级冷凝系统16由一级冷凝13,二级冷凝14,三级冷凝15,闸阀21、23,压力传感器22以及温度传感器20组成。
52.进一步,各级冷凝换热器温度分别设计为4℃、-40℃和-80℃。
53.进一步,一级冷凝室的气体通道面积比为4.0:1,换热面积比为1.5:1,二级冷凝室的气体通道面积比为6.0:1,换热面积比为2.0:1,三级冷凝室的气体通道面积比为4.0:1,换热面积比为1.5:1。
54.③ꢀ
一种“加压多级冷凝—吸附”的油气回收系统的吸附系统18由吸附塔46、47,三通阀31、34、35、36、53,压力传感器24、52,温度传感器25、26、27、28、29、30、32以及阻火器33
组成。
55.进一步,吸附塔46、47的高度为3000 mm,直径800mm,内部设有翅片管,均匀分布于塔内,吸附塔46、47进气口由三通阀34控制切换,与加压多级冷凝系统16排气口相连接。
56.进一步,吸附塔46、47内部设有换热器,换热器进出口由三通阀53、36控制开闭,与恒温水浴箱62连接,恒温水浴箱62温度为85℃,其尺寸为长1000 mm,宽800 mm,高800 mm。
57.④ꢀ
一种“加压多级冷凝—吸附”的油气回收系统的油水分离器48、55为卧式分离器,长度为1000 mm,直径800 mm。
58.进一步,油水分离器48、55侧面设有高度为600 mm液位计,内部左右两侧设有2个高度为600 mm隔板,隔板之间距离为500 mm,将油水分离器48、55内部分为左侧的水区、中间的缓存区、右侧的vocs存储区。
59.(2)一种“加压多级冷凝—吸附”的油气回收系统连接方式如下:
60.①ꢀ
化工厂集气管道经过阻火器1、压力传感器2、温度传感器3、球阀4、抽气泵5与加压设备6进口连接,加压设备6出气口管道经过三通阀7与水冷换热器8进口连接,水冷换热器8出气口经过闸阀与压缩机9进气口连接,压缩机9出口与三通阀12连接。
61.②ꢀ
压缩机9出口经过压力传感器11、三通阀12连接一级冷凝13进气口,三级冷凝出口连接大气或经过闸阀23与吸附系统进气口三通控制阀34连接,一级冷凝13冷凝室底部排液口与油水分离器48进口连接,二级冷凝14与三级冷凝15冷凝室底部排液口均与油水分离器55进口连接,油水分离器48、55底部设有两个排放口,闸阀51、54与缓存水罐56进口连接,闸阀50、57连接外输管道,缓存水管出口经过离心泵45与水冷换热器8连接。
62.③ꢀ
吸附塔46、47进气口三通阀34与三级冷凝15出口闸阀23连接,吸附塔46、47排气口三通阀31与温度传感器32、阻火器33连接,吸附塔46、47底部三通阀35经过真空泵39、温度传感器40与压缩机9进口连接,恒温水浴箱62进出口分别与吸附塔46、47内部换热盘管进出口三通阀53、36连接。
63.(3)一种“加压多级冷凝—吸附”的油气回收系统回收方法如下:
64.①ꢀ
打开进气闸阀4,化工厂排放的高浓度油气在抽气泵5作用下经过阻火器1、压力传感器2、温度传感器3进入预处理系统17,经过加压设备6加压浓缩后,进入水冷换热器8冷却处理,产生的部分凝结液经过闸阀42储存于油水分离器48中,在油水分离器48分离作用下,冷凝水通过闸阀51存储于缓存水罐56中,液态油外输再利用。
65.②ꢀ
预处理后油气经过压缩机9、压力传感器11、三通阀12后进入加压多级冷凝系统16,依次经过一级冷凝13、二级冷凝14、三级冷凝15,经过一级冷凝13后,油气中大部分水蒸气及部分重组分被冷凝下来,二级冷凝14后大部分油气被冷凝回收,经过一级冷凝13、二级冷凝14后含有少量轻组分废气进入三级冷凝15深度冷凝处理,该过程中大量轻组分达到饱和由气态相变为液态,一级冷凝13的冷凝液在自身重力作用下流入油水分离器48中间的缓存区,二级冷凝14与三级冷凝15产生的冷凝液均流入油水分离器55中间缓存区,经过分离后进入左侧水区和右侧vocs区,通过观察液位计49、44示数,打开闸阀51、54流入缓存水罐56,液态油经过闸阀50、57外输再利用,缓存水罐中低温水在离心泵45作用下经过闸阀59与补给水混合作为冷却介质进入水冷换热器8。
66.③ꢀ
关闭闸阀21打开闸阀23,通过调节吸附系统18进气三通阀34使三级冷凝后气体先进入吸附塔46,待吸附塔46吸附穿透后,通过调节三通阀34、31,切换吸附塔47吸附,同
时打开三通阀53、35、36,对吸附塔46抽真空解吸再生,解吸出的高浓度油气经过闸阀41与预处理后气体混合再次进入加压多级冷凝系统16再处理。先后经过加压冷却预处理、加压多级冷凝、吸附回收处理后的高浓度油气,吸附塔46、47出口排放浓度低于60 mg/m3,油气总回收率大于99%。
67.以上所述仅是本实用新型的优选实施方式,应当指出,对于本技术领域的普通技术人员来说,在不脱离本实用新型技术原理的前提下,还可以做出若干改进和变形,这些改进和变形也应视为本实用新型的保护范围。