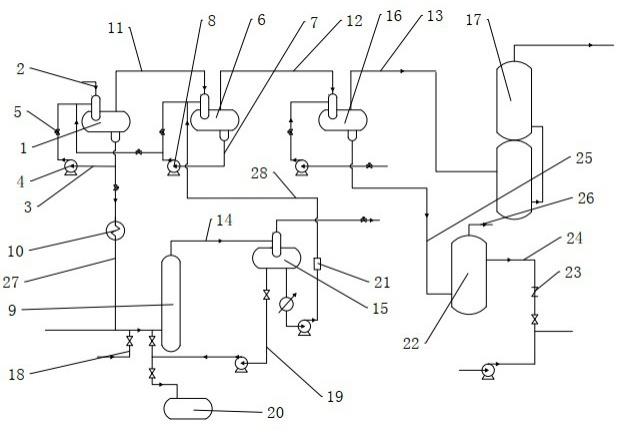
1.本实用新型涉及一种新型液化气脱硫醇装置。
背景技术:
2.催化装置采用140万吨/年重油催化裂化装置,随着高硫原油加工种类和数量增加,催化裂化原料硫从含量0.7%提高到1%左右,造成液化气脱硫醇负荷增加;为保证产品质量,液化气脱硫醇系统需频繁更换碱液,增大了碱渣处理排放的难度。同时碱液氧化过程中发现硫化物无法从碱液中析出,在对三相分离罐隔板右侧无硫化物生成,导致只能频繁的换碱来保证硫化物随碱液排出,耗碱增加。经化验室分析二硫化物和碱液的密度相近,无法脱除二硫化物。现有工艺水洗水采用除盐水对液化气中的碱液进行水洗,水洗后带碱污水排至污水处理系统,水洗后的废水ph值约为9
‑
11,在排放时尾气中会夹带一部分轻烃,直接排放易导致地下井可燃气超标,存在安全隐患,污水处理成本也较高。
技术实现要素:
3.本实用新型要解决的技术问题是提供一种新型液化气脱硫醇装置,通过添加反提取油,实现二硫化物和氢氧化钠碱液分离,实现碱液的循环利用,对轻烃进行有效回收利用。
4.为了解决上述技术问题,本实用新型包括连通有液化气进气管路的一级碱洗沉降罐,一级碱洗沉降罐通过第一管路连通到二级碱洗沉降罐,一级碱洗沉降罐的上部和下部之间设有第一循环管路,二级碱洗沉降罐的上部和下部之间设有第二循环管路,第一循环管路通过第一碱液管路连通到氧化塔,所述氧化塔通过第四管路连通到二硫化物分离罐,二硫化物分离罐通过第二碱液管路连通到第二循环管路,二级碱洗沉降罐通过第二管路连通到水洗碱沉降罐,水洗碱沉降罐通过第三管路连通到吸附塔,其结构特点是所述第四管路上连通有加氢重石脑油管路,二硫化物分离罐与所述氧化塔之间还通过第三循环管路连通,所述水洗碱沉降罐的下部通过水洗水直排管线连通到脱烃器,所述脱烃器的中部通过脱烃水管路连通到烟气脱硫塔,所述脱烃器的上部通过排烃管路将脱出的烃类送入火炬。
5.作为一种改进的技术方案,所述第三循环管路上通过排出管路连通到用以存放高浓度硫化物的催化粗汽油罐。
6.作为一种改进的技术方案,所述第三循环管路设有再生循环泵,再生循环泵前后的第三循环管路上设有闸阀。
7.作为一种改进的技术方案,所述脱烃水管路上依次设有单向阀和闸阀,所述脱烃水管路上还连通有工艺水管路。
8.作为一种改进的技术方案,所述第二碱液管路上设有用以清除碱渣的碱液过滤器。
9.本实用新型的优点效果是:
10.1. 加氢重石脑油管路将加氢重石脑油送入氧化塔,加氢重石脑油对二硫化物进
行抽提,然后氧化塔将抽提二硫化物的加氢重石脑油送入二硫化物分离罐进行分离,从而实现二硫化物和氢氧化钠碱液分离,实现碱液的循环利用,降低了更换碱液频次,降低碱渣排放;自二硫化物分离罐排出的反抽提油硫含量提高,说明改造后液化气脱硫醇系统大大提高了抽提能力,同时增强循环剂活性和再生能力,延长循环剂的运行周期,减少废渣产生,碱液再生能力提高,实现了常温下碱液强化再生,净化溶剂和脱除催化氧化活性。
11.2.脱硫醇系统废水排放大幅度降低,定期监测水洗水ph值,对水洗液化气后的碱性除盐水进行轻烃回收,降低了工艺水的使用,外派的碱性除盐水经脱烃后送至烟气脱硫塔循环利用,脱出的烃类气体送入火炬进行燃烧实现热量回收。
附图说明
12.下面结合附图和实施例对本实用新型作进一步说明:
13.图1是现有技术的液化气脱硫醇装置的结构示意图;
14.图2是本实用新型的结构示意图;
15.图中:1
‑
一级碱洗沉降罐,2
‑
液化气进气管路,3
‑
第一循环管路,4
‑
一级碱洗泵,5
‑
闸阀,6
‑
二级碱洗沉降罐,7
‑
第二循环管路,8
‑
二级碱洗泵,9
‑
氧化塔,10
‑
碱液加热器,11
‑
第一管路,12
‑
第二管路,13
‑
第三管路,14
‑
第四管路,15
‑
二硫化物分离罐,16
‑
水洗碱沉降罐,17
‑
吸附塔,18
‑
加氢重石脑油管路,19
‑
第三循环管路,20
‑
催化粗汽油罐,21
‑
碱液过滤器,22
‑
脱烃器,23
‑
单向阀,24
‑
脱烃水管路,25
‑
水洗水直排管线,26
‑
排烃管路,27
‑
第一碱液管路,28
‑
第二碱液管路。
具体实施方式
16.为了对本实用新型的设计思想和基于设计思想而做出的具体实施方式有一个更加清楚的理解,在描述本实用新型的具体实施方式之前有必要对现有的液化气脱硫醇装置进行简单的介绍。参照图1所示,液化气脱硫醇装置包括一级碱洗沉降罐1,一级碱洗沉降罐1的上部连通有液化气进气管路2,一级碱洗沉降罐1的上部和下部之间设有第一循环管路3,第一循环管路3上连通有一级碱洗泵4和闸阀5,经过处理的液化气送入一级碱洗沉降罐1,一级碱洗沉降罐1通过第一管路11连通到二级碱洗沉降罐6,二级碱洗沉降罐6的上部和下部之间设有第二循环管路7,第二循环管路7上连通有二级碱洗泵8和闸阀5,第二循环管路7通过支路连通到第一循环管路3。其中一级碱洗沉降罐1和二级碱洗沉降罐6发生的反应式是rsh+naoh=nasr+h2o,第一循环管路3通过第一碱液管路27连通到氧化塔9,第一碱液管路27设有闸阀5和碱液加热器10,经过碱液加热器10加热的脱硫醇液体送入氧化罐处理,氧化罐通过进气管路连通外界,外界空气通过进气管送入氧化塔9,氧化塔9内进行的反应式为2nasr +1/2o2+h2o= 2naoh+rssr,得到二硫化物和氢氧化钠的混合液体,氧化塔9的上部通过第四管路14连通到二硫化物分离罐15,二硫化物分离罐15通过第二碱液管路28连通到第二循环管路7,二硫化物和氢氧化钠的混合液体在二硫化物分离罐15中进行分离,分离后的氢氧化钠溶液通过第二碱液管路28送入第二循环管路7实现碱液的再生处理。但是碱液氧化过程中发现硫化物无法从碱液中析出,在对二硫化物分离罐隔板右侧无硫化物生成,导致只能频繁的换碱来保证硫化物随碱液排出,耗碱增加。二级碱洗沉降罐6通过第二管路12连通到水洗碱沉降罐16,水洗碱沉降罐16通过第三管路13连通到吸附塔17,水洗碱沉降
罐16的上部连通有除盐水进水管,除盐水进水管上设有除盐水泵和闸阀5,水洗碱沉降罐16的下部连通有污水管。二级碱洗沉降罐6将液化气送入水洗碱沉降罐16,除盐水对液化气的碱液进行水洗,水洗后带碱污水排至污水处理系统,水洗后的废水ph值约为9
‑
11,在排放时尾气中会夹带一部分轻烃,直接排放易导致地下井可燃气超标,存在安全隐患,污水处理成本也较高。
17.参照图2所示,该新型液化气脱硫醇装置的结构与上述结构基本相同,包括包括一级碱洗沉降罐1,一级碱洗沉降罐1的上部连通有液化气进气管路2,一级碱洗沉降罐1的上部和下部之间设有第一循环管路3,第一循环管路3上连通有一级碱洗泵4和闸阀5,一级碱洗沉降罐1通过第一管路11连通到二级碱洗沉降罐6,二级碱洗沉降罐6的上部和下部之间设有第二循环管路7,第二循环管路7上连通有二级碱洗泵8和闸阀5,第二循环管路7通过支路连通到第一循环管路3,支路上设有闸阀5。第一循环管路3通过第一碱液管路27连通到氧化塔9,第一碱液管路27设有闸阀5和碱液加热器10,氧化塔9通过进气管路连通外界,氧化塔9的上部通过第四管路14连通到二硫化物分离罐15,二硫化物分离罐15通过第二碱液管路28连通到第二循环管路7,二硫化物和氢氧化钠的混合液体在二硫化物分离罐15中进行分离,分离后的氢氧化钠溶液通过第二碱液管路28送入第二循环管路7实现碱液的再生处理,二级碱洗沉降罐6通过第二管路12连通到水洗碱沉降罐16,水洗碱沉降罐16通过第三管路13连通到吸附塔17,水洗碱沉降罐16的上部连通有除盐水进水管,除盐水进水管上设有除盐水泵和闸阀5,水洗碱沉降罐16的下部连通有污水管。不同之处在于,第四管路14上连通有加氢重石脑油管路18,加氢重石脑油管路18上设有闸阀5,引高压低硫的加氢重石脑油做反抽提油,在氧化塔9中将碱液中的二硫化物抽提至反抽提油中,氧化塔15反应之后通过反抽提油将二硫化物携带至二硫化物分离罐15;二硫化物分离罐15与氧化塔9之间还通过第三循环管路19连通,第三循环管路19通过排出管路连通到催化粗汽油罐20,排出管路上设有闸阀5,催化粗汽油罐20可以用以存放高浓度硫化物,第三循环管路19设有再生循环泵,再生循环泵前后的第三循环管路19上设有闸阀5,其中一个闸阀5设于催化粗汽油罐20与氧化塔9之间的第三循环管路19上。当二硫化物分离罐15运行一段时间后,关闭催化粗汽油罐20与氧化塔9之间的第三循环管路19的闸阀5,打开排出管路上的闸阀5,第三循环管路19将高浓度硫化物送入催化粗汽油罐20;当第三循环管路19正常循环使用时,关闭排出管路上的闸阀5,开启催化粗汽油罐20与氧化塔9之间的第三循环管路19的闸阀5,使硫化物分离罐中的溶液持续不断的进入氧化塔9,降低碱液的浪费,提高硫化物的浓度,节约碱液。第二碱液管路28上设有用以清除碱渣的碱液过滤器21,碱液过滤器21包括壳体,壳体内可拆卸安装有滤罩,滤罩上开设有若干小孔,碱液通过碱液过滤器21时,滤罩能将碱液中的碱渣过滤下来,运行一段时间后将滤罩拿出清洗,碱液过滤器21能够有效降低再生碱液中的滤渣。水洗碱沉降罐16的下部通过水洗水直排管线25连通到脱烃器22,脱烃器22通过脱烃水管路24连通到烟气脱硫塔(图中未示出),脱烃水管路24上依次设有单向阀23和闸阀5,脱烃水管路24上还连通有工艺水管路,脱硫醇系统废水排放大幅度降低,定期监测水洗水ph值,水洗液化气后的碱性除盐水回收至烟气脱硫塔替代部分工艺水。脱烃器22的上部通过排烃管路26将脱出的烃类送入火炬(图中未示出),脱出的烃类气体送入火炬进行燃烧实现热量回收。
18.其中上述的一级碱洗沉降罐1、液化气进气管路2、一级碱洗泵4、二级碱洗沉降罐
6、二级碱洗泵8、氧化塔9、碱液加热器10、二硫化物分离罐15、水洗碱沉降罐16、吸附塔17、催化粗汽油罐20、碱液过滤器21和脱烃器22的结构和运行原理均为现有技术,为本技术领域技术人员所熟知,此处不多做赘述。
19.本实用新型在使用时,液化气送入一级碱洗沉降罐1进行碱洗沉降,一级碱洗沉降罐1将处理后的液化气送入二级碱洗沉降罐6进行碱洗沉降,二级碱洗沉降罐6将处理后的液化气送入水洗碱沉降罐16进行水洗脱碱,脱碱之后的液化气送入吸附塔17处理,吸附塔17将液化气送出,水洗碱沉降罐16水洗之后产生的废液部分通过脱烃水管路24送入脱烃器22中,水洗液化气后的碱性除盐水在脱烃器22中脱烃后回收至烟气脱硫塔替代部分工艺水,碱性除盐水在脱烃器22脱烃产生的烃类通过脱烃器22上部连通的排烃管路26送到火炬进行燃烧实现热量回收。其中一级碱洗沉降罐1内的碱液部分送入氧化塔9进行氧化,外界空气和加氢重石脑油一并送入氧化塔9,加氢重石脑油做反抽提油,将碱液中的二硫化物抽提至反抽提油中,通过反抽提油将二硫化物携带至二硫化物分离罐15,从而实现二硫化物和氢氧化钠碱液分离,实现碱液的循环利用,降低了更换碱液频次,降低碱渣排放;自二硫化物分离罐15排出的反抽提油硫含量提高,说明改造后液化气脱硫醇系统大大提高了抽提能力,同时增强循环剂活性和再生能力,延长循环剂的运行周期,减少废渣产生,碱液再生能力提高,实现了常温下碱液强化再生,净化溶剂和脱除催化氧化活性。