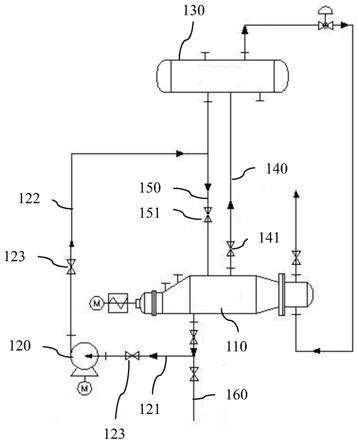
1.本发明涉及烷基化生产技术领域,特别涉及一种快速开工停工的烷基化反应系统。
背景技术:
2.烷基化反应是指利用加成或置换反应将烷基引入有机物分子中的反应过程,烷基化反应作为一种重要的合成手段,广泛应用于许多化工生产过程。
3.烷基化反应器是烷基化反应过程中的重要部件,目前,烷基化装置反应器中的原料烯烃和异丁烷在硫酸催化剂存在下,生成烷基化油,反应完全的酸—烃乳化液经上升管直接进入酸沉降器,并在此进行酸和烃类的沉降分离,分出的酸液下降管返回反应器重新使用反应,在沉降系统中,酸的循环是借助在上升管和下降管中物料的比重差自然循环的。
4.但是,反应器停工再开工时,需要把反应器中的酸排走,因为反应器中存在大量的酸就启动反应器时,反应器的启动电流会过大导致反应器无法开启,所以正常的处置步骤是首先需把酸液下降管阀门关闭,然后把反应器中的酸和油沉降进行充分分离,接着把酸相全部排至废酸储罐,再通过注入新酸把沉降罐的酸界位补充至正常液位,最后才能把反应器再次开启。这个过程中沉降需要0.5小时,排酸需要1小时,补酸需要0.5小时,总共需要花费2小时左右的时间,导致效率低下,而且,反应器的酸往废酸储罐排放时难免会夹带部分烃类往外走,导致资源的浪费,存在不足。
技术实现要素:
5.本发明的目的在于提供一种快速开工停工的烷基化反应系统,以解决上述背景技术中提出的问题。
6.为实现上述目的,本发明提供如下技术方案:一种快速开工停工的烷基化反应系统,包括:
7.反应单元,所述反应单元包括反应器本体、倒酸泵与沉降罐;
8.精制单元,所述精制单元包括依次设置且相连通的酸洗罐、碱洗罐与水洗罐,所述酸洗罐与反应单元相连通;
9.分馏单元,所述分馏单元包括依次设置且相连通的换热器、脱异丁烷模块与脱正丁烷模块,所述换热器与水洗罐相连通;
10.其中,所述反应器本体一侧设置有上升管道与下降管道,所述上升管道与下降管道均与沉降罐相连通,所述反应器本体另一侧设置有排酸管道,所述倒酸泵设置在排酸管道与下降管道之间。
11.在数个实施方式中,倒酸泵两侧设置有输入管道与输出管道,所述输入管道与排酸管道相连通,所述输出管道与下降管道相连通,所述输入管道与输出管道上均设置有控制阀门。
12.在数个实施方式中,下降管道上设置有下降管阀门,所述下降管阀门设置在反应
器本体与输出管道之间。
13.在数个实施方式中,在上升管道上也同样设置有上升管阀门。
14.在数个实施方式中,脱异丁烷模块包括脱异丁烷塔、空气冷却器、第一回流罐与第一电泵,所述空气冷却器与脱异丁烷塔的顶部出口相连通,所述第一回流罐与空气冷却器相连通,所述第一电泵用以连通脱异丁烷塔与第一回流罐。
15.在数个实施方式中,脱正丁烷模块包括脱正丁烷塔、冷凝换热器、第二回流罐与第二电泵,所述冷凝换热器与脱正丁烷塔的顶部出口相连通,所述第二回流罐与冷凝换热器相连通,所述第二电泵用以连通脱正丁烷塔与第二回流罐。
16.本发明的技术效果和优点:
17.本发明由沉降罐进行停工再开工时的沉降分离酸的过程,大大缩短了停工后再次开工的时间,从原来的2小时缩至0.5小时;而且分离出的酸可以再次回用至反应器本体,无需外排,节约了新酸的使用量,提高资源的利用率。
附图说明
18.图1为本发明的实施例1中的反应单元的局部放大结构示意图;
19.图2为本发明的实施例1中的整体结构示意图。
具体实施方式
20.下面将结合本发明实施例中的附图,对本发明实施例中的技术方案进行清楚、完整地描述,显然,所描述的实施例仅仅是本发明一部分实施例,而不是全部的实施例。基于本发明中的实施例,本领域普通技术人员在没有做出创造性劳动前提下所获得的所有其他实施例,都属于本发明保护的范围。
21.实施例1
22.本发明提供了如图1
‑
2所示的一种快速开工停工的烷基化反应系统,主要包括反应单元100、精制单元200与分馏单元300,三者依次分布,由此进行反应与精制分馏工序。
23.具体的,反应单元100包括反应器本体110、倒酸泵120与沉降罐130,反应器本体110一侧设置有上升管道140与下降管道150,所述上升管道140与下降管道150均与沉降罐130相连通,所述反应器本体110另一侧设置有排酸管道160,所述倒酸泵120设置在排酸管道160与下降管道150之间。
24.并且在倒酸泵120两侧设置有输入管道121与输出管道122,所述输入管道121与排酸管道160相连通,所述输出管道122与下降管道150相连通,所述输入管道121与输出管道122上均设置有控制阀门123。
25.基于上述,在下降管道150上设置有下降管阀门151,上升管道140上设置有上升管阀门141,且其中的下降管阀门151设置在反应器本体110与输出管道122之间。
26.当反应器停工后,打开输入管道121上的控制阀门123,启动倒酸,120把反应器本体内的酸烃混合物一起通过下降管道150往沉降罐130输送,此时下降管道150上的下降管阀门151闭合,混合物到达沉降罐130后酸沉降到沉降罐130底部,油相通过上升管道140重新回到反应器本体,由此,可以把反应器中的酸快速转移到沉降罐中,一般只需要0.5小时。
27.精制单元200包括依次设置且相连通的酸洗罐210、碱洗罐220与水洗罐230,所述
酸洗罐210与反应单元100相连通用以承接来自反应单元100的物料。
28.分馏单元300包括依次设置且相连通的换热器310、脱异丁烷模块与脱正丁烷模块,所述换热器310与水洗罐230相连通。
29.其中,脱异丁烷模块包括脱异丁烷塔321、空气冷却器322、第一回流罐323与第一电泵324,所述空气冷却器322与脱异丁烷塔321的顶部出口相连通,所述第一回流罐323与空气冷却器322相连通,所述第一电泵324用以连通脱异丁烷塔321与第一回流罐323。
30.相应的,脱正丁烷模块包括脱正丁烷塔331、冷凝换热器332、第二回流罐333与第二电泵334,所述冷凝换热器332与脱正丁烷塔331的顶部出口相连通,所述第二回流罐333与冷凝换热器332相连通,所述第二电泵334用以连通脱正丁烷塔331与第二回流罐333。
31.工作时,物料进入烷基化反应器本体110,在硫酸催化剂的作用下反应,反应生成物和硫酸的混合物进入沉降罐130,分出的酸液大部分返回反应器循环使用,少部分90%酸排至90%酸罐进行储存;自沉降罐上部分出的物流经反应器本体的热侧部分汽化进入闪蒸罐,部分经换热升温后去精制系统进行处理;反应流出物经换热后与酸混合进入酸洗罐210酸洗,酸洗罐210中酸相沉降下来返回反应器循环使用,油相与10%naoh混合后进入碱洗罐220脱除酸性物,碱相循环使用,定期排出系统;油相再经过水洗罐230水洗洗去盐类物质,水洗后油相再通过换热器310加热后进入脱异丁烷塔321分离出异丁烷,塔顶馏出物经空气冷却器322冷凝后进入塔顶侧的第一回流罐323,部分通过第一电泵324进行回流至脱异丁烷塔321,部分经冷却器冷却作为循环异丁烷返回反应系统,多余异丁烷送去异丁烷罐;随后脱异丁烷塔321底部的烃类自压送入脱正丁烷塔331,塔顶分出正丁烷,经冷凝换热器332换热后进入塔顶侧的第二回流罐333,部分通过第二电泵334进行回流至脱正丁烷塔331,部分送去产品罐组;塔底产品为烷基化油,烷基化油先与脱异丁烷塔进料换热降温,再冷却后送去产品罐组。
32.最后应说明的是:以上所述仅为本发明的优选实施例而已,并不用于限制本发明,尽管参照前述实施例对本发明进行了详细的说明,对于本领域的技术人员来说,其依然可以对前述各实施例所记载的技术方案进行修改,或者对其中部分技术特征进行等同替换,凡在本发明的精神和原则之内,所作的任何修改、等同替换、改进等,均应包含在本发明的保护范围之内。