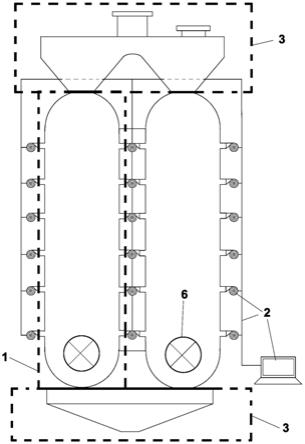
1.本实用新型涉及一种立窑污泥碳化炉,具体涉及一种立式低温双循环升流碳化设备。
背景技术:
2.污泥一直以来都是极其重要的重金属与有毒有机物水体污染源汇,其中富集了大量的多环芳烃、杂环类、有机农药与重金属等“三致”(致癌、致畸、致突变)污染,处理不当将会引起严重的生态问题,甚至引起人类健康风险事件。对于污泥的处理,由于污染物含量高,且难于泥污分离,所以污泥一直以来都是作为固体危险废物来处理,不仅处理费用高,而且填埋等处理方式对于未来生态环境将造成潜在隐患。
3.污泥无氧碳化由于其重金属污染固定化、有机污染物消减化与废料资源化等技术优势,在环境保护行业内得到广泛认可与推广。并且污泥无氧碳化后所得的污泥生物碳作为一种环保型材料,可以用做建筑材料等,既减轻了生态环境在污泥堆积难以处理方面的压力,而且可以缓解建筑材料制作过程中形成的土地资源浪费,一举两得。
4.但是,在污泥无氧碳化处理过程中的污泥碳化设备效率低下、故障率高与碳化过程废气产生等问题一直是污泥碳化的痛点。中国专利(专利号为: cn111704337a)一种工业污泥等处理用于碳化、热解装置,是一种旋窑滚筒式污泥碳化的装置,通过间接加热炉壁来达到污泥碳化的目的,但事实上间接加热会导致热量散失与利用不充分的问题,另外旋窑滚筒式污泥碳化故障率高、在高温下难以稳定运行,且经常发生臭气外泄等问题。中国实用新型专利(申请公布号为:cn210287221u)污泥无害化处理用碳化炉,作为旋窑碳化炉与上述专利类似,同样面临热量不完全利用、故障率高与臭气问题的困扰。尽管大部分污泥无氧碳化装置都通过各种方式提升其碳化效率,但都没有做到简单实用。
5.开发一种结构简单、能广泛性使用、成本低廉、便于拆卸组装、维护难度低、能源清洁的污泥无氧碳化装置,是迫切需要解决的首要问题。本实用新型是基于无氧碳化原理,特点如下:立式结构大大降低了碳化炉的故障率,内部高效热循环成倍提高了碳化的热效率;循环提升使颗粒充分受热,污泥碳化更充分;直接喷烧式加热法,避免了间接加热的热量损失;生物质与污泥共烧解充分提高了生物碳产率,提高了污泥生物碳热值,并通过生物质碳化形成多孔结构吸附烧解形成的粉尘与有害气体,成倍降低废气排放量。
技术实现要素:
6.本实用新型的主要目的在于提供立窑污泥碳化炉,其次要目的在于一种立式低温双循环升流碳化设备。
7.本实用新型的技术方案如下。
8.一种立式低温双循环升流碳化设备,包括立窑传动循环提升式炉体系统、喷烧温控系统与加料排料排气系统;所述立窑传动循环提升式炉体系统顶部和底部连接有加料排料排气系统,所述喷烧温控系统与立窑传动循环提升式炉体系统连接;
9.所述立窑传动循环提升式炉体系统包括传动轴、耐高温履带、电动机、循环提升碗形扇叶、立窑桶式炉腔与混合燃气接口;所述耐高温履带由传动轴带动,所述传动轴由电动机带动;所述耐高温履带上固定有循环提升碗形扇叶;所述耐高温履带位于立窑桶式炉腔内部;所述立窑桶式炉腔上开设有混合燃气接口。
10.进一步地,所述喷烧温控系统包括测温电子喷烧一体化设备、数据传输线与温控中央系统;所述测温电子喷烧一体化设备设置于混合燃气接口上,所述测温电子喷烧一体化设备通过数据传输线与温控中央系统连接。
11.进一步地,所述加料排料排气系统包括储料仓与出料仓;所述储料仓位于立窑桶式炉腔上方,所述出料仓位于立窑桶式炉腔下方;所述储料仓通过炉体加料口与立窑桶式炉腔连通;所述出料仓通过炉体出料口与立窑桶式炉腔连通。
12.进一步地,进一步地本实用新型还包括外部出料口;所述外部出料口与出料仓连通。
13.进一步地,本实用新型还包括外部加料口和外部排气口;所述外部加料口设置于储料仓上方;所述外部排气口设置于储料仓上方。
14.进一步地,由电动机带动耐高温履带,进而带动循环提升碗形扇叶对立窑桶式炉腔内的干燥污泥与生物质混合物进行分散化与链式喷烧。
15.进一步地,喷烧温控系统通过测温电子喷烧一体化设备对不同层级的温度进行准确检测,将温度信息通过数据传输线传至温控中央系统,然后通过测温电子喷烧一体化设备喷烧加热炉腔,保持各层级炉腔温度为350~600℃。
16.进一步地,电动机采用的功率为5.5~7.5kw。
17.一种立式低温双循环升流碳化设备的使用方法,干燥污泥与生物质混合物通过外部加料口进入储料仓,后由炉体加料口进入立窑传动循环提升式炉体系统,进行1~1.5小时的无氧碳化处理,然后经过炉体出料口进入出料仓,最终由外部出料口排出。
18.上述方法中,测温电子喷烧一体化设备在得到温控中央系统升温指令后,将天然气与空气的混合气体按照1:5~7.5的比例输入立窑桶式炉腔,同时电子点火引燃混合气体,达到喷烧升温的目的。
19.上述方法中,每次通过炉体加料口加入每个耐高温履带与循环提升碗形扇叶之间隔层的干燥污泥与生物质混合物的质量为10~15千克。
20.上述方法中,立窑传动循环提升式炉体系统与喷烧温控系统工作过程中,外部加料口、炉体出料口与外部出料口均为密闭,保证立窑桶式炉腔中的无氧环境。
21.上述碳化炉组装方法为,将各部分先分别组装,安装由下而上的原则进行组装。
22.一种立式低温双循环升流碳化设备的使用方法,包括如下步骤:开启电源,电动机采用的功率为5.5~7.5kw,天然气与空气的混合气体按照1:5~7.5的比例输入立窑桶式炉腔,通过测温电子喷烧一体化设备喷烧加热炉腔,保持各层级炉腔温度为350~600℃;干燥污泥与生物质混合物通过外部加料口进入储料仓,后由炉体加料口进入立窑传动循环提升式炉体系统,10~15千克干燥污泥与生物质混合物通过炉体加料口加入在每个耐高温履带与循环提升碗形扇叶之间隔层;由电动机带动耐高温履带与循环提升碗形扇叶,对立窑桶式炉腔内的干燥污泥与生物质混合物进行分散化与链式喷烧;喷烧温控系统通过测温电子喷烧一体化设备对不同层级的温度进行准确检测,适时注入点燃混合气体,喷烧加热炉腔;
进行1~1.5小时的无氧碳化处理,立窑传动循环提升式炉体系统与喷烧温控系统工作过程中,外部加料口、炉体出料口与外部出料口均为密闭,保证立窑桶式炉腔中的无氧环境;然后经过炉体出料口进入出料仓,最终由外部出料口排出。
23.本实用新型是基于无氧碳化原理设计,特点如下:1、立式结构大大降低了碳化炉的故障率,内部高效热循环成倍提高了碳化的热效率;2、循环提升使颗粒充分受热,污泥碳化更充分;3、直接喷烧式加热法,避免了间接加热的热量损失;4、生物质与污泥共烧解充分提高了生物碳产率,提高了污泥生物碳热值,并通过生物质碳化形成多孔结构吸附烧解形成的粉尘与有害气体,成倍降低废气排放量。
24.与现有技术相比,本实用新型的优势在于:
25.立式结构大大降低了碳化炉的故障率,内部高效热循环成倍提高了碳化的热效率;循环提升使颗粒充分受热,污泥碳化更充分;直接喷烧式加热法,避免了间接加热的热量损失;生物质与污泥共烧解充分提高了生物碳产率,提高了污泥生物碳热值,并通过生物质碳化形成多孔结构吸附烧解形成的粉尘与有害气体,成倍降低废气排放量。
附图说明
26.图1为本实用新型立窑高效生物质共烧解循环提升式污泥碳化炉的外观结构示意图;
27.图2为本实用新型立窑高效生物质共烧解循环提升式污泥碳化炉的纵剖面结构示意图;
28.图3为本实用新型立窑高效生物质共烧解循环提升式污泥碳化炉的横剖面结构示意图。
29.图中各个部件如下:立窑传动循环提升式炉体系统1、喷烧温控系统2、加料排料排气系统3、传动轴4、耐高温履带5、电动机6、循环提升碗形扇叶7、立窑桶式炉腔8与混合燃气接口9、测温电子喷烧一体化设备10、数据传输线 11、温控中央系统12、外部加料口13、外部排气口14、储料仓15、炉体加料口 16、炉体出料口17、出料仓18与外部出料口19。
具体实施方式
30.下面结合具体实施例对本实用新型作进一步地具体详细描述,但本实用新型的实施方式不限于此,对于未特别注明的工艺参数,可参照常规技术进行。
31.如图1~图3所示,一种立式低温双循环升流碳化设备,包括立窑传动循环提升式炉体系统1、喷烧温控系统2与加料排料排气系统3;所述立窑传动循环提升式炉体系统1由内向外依次包括传动轴4、耐高温履带5、电动机6、循环提升碗形扇叶7、立窑桶式炉腔8与混合燃气接口9;所述立窑传动循环提升式炉体系统1包括传动轴4、耐高温履带5、电动机6、循环提升碗形扇叶7、立窑桶式炉腔8与混合燃气接口9;所述耐高温履带5由传动轴4带动,所述传动轴 4由电动机6带动;所述耐高温履带5上固定有循环提升碗形扇叶7;所述耐高温履带5位于立窑桶式炉腔8内部;所述立窑桶式炉腔8上开设有混合燃气接口 9。所述喷烧温控系统2包括测温电子喷烧一体化设备10、数据传输线11与温控中央系统12;所述测温电子喷烧一体化设备10设置于混合燃气接口9上,所述测温电子喷烧一体化设备10通过数据传输线11与温控中央系统12连接。所述加料排料排气系统3包括储料仓15与出料仓18;所述储料
仓15位于立窑桶式炉腔8上方,所述出料仓18位于立窑桶式炉腔8下方;所述储料仓15通过炉体加料口16与立窑桶式炉腔8连通;所述出料仓18通过炉体出料口17与立窑桶式炉腔8连通。本实施例还包括外部出料口19;所述外部出料口19与出料仓 18连通。本实施例还包括外部加料口13和外部排气口14;所述外部加料口13 设置于储料仓15上方;所述外部排气口14设置于储料仓15上方。
32.本实施例中电动机6采用的功率为7.5kw,天然气与空气的混合气体按照1: 7.5的比例输入立窑桶式炉腔8,且每次通过炉体加料口16加入每个耐高温履带 5与循环提升碗形扇叶7之间隔层的干燥污泥与生物质混合物的质量为15千克,各层级炉腔温度为600℃;
33.其中,循环提升碗形扇叶7支撑稳定固定在耐高温履带5上;由电动机6 带动耐高温履带5,进而带动循环提升碗形扇叶7对立窑桶式炉腔8内的干燥污泥与生物质混合物进行分散化与链式喷烧;喷烧温控系统2通过测温电子喷烧一体化设备10对不同层级的温度进行准确检测,将温度信息通过数据传输线11传至温控中央系统12,然后通过测温电子喷烧一体化设备10喷烧加热炉腔;干燥污泥与生物质混合物通过外部加料口13进入储料仓15,后由炉体加料口16进入立窑传动循环提升式炉体系统1,进行1~1.5小时的无氧碳化处理,然后经过炉体出料口17进入出料仓18,最终由外部出料口19排出;测温电子喷烧一体化设备10在得到温控中央系统12升温指令后,同时电子点火引燃混合气体,达到喷烧升温的目的;立窑传动循环提升式炉体系统1与喷烧温控系统2工作过程中,外部加料口13、炉体出料口17与外部出料口19均为密闭,保证立窑桶式炉腔8中的无氧环境;
34.实施例1
35.将某机构采集的工业废水处理厂污泥1吨,混合干燥碎木屑之后总重为1.2 吨,通过烘干等方法将含水率降低至30%左右。
36.开启电源,电动机采用的功率为7.5kw,天然气与空气的混合气体按照1: 7.5的比例输入立窑桶式炉腔,通过测温电子喷烧一体化设备喷烧加热炉腔,保持各层级炉腔温度为600℃;干燥污泥与生物质混合物通过外部加料口进入储料仓,后由炉体加料口进入立窑传动循环提升式炉体系统,15千克干燥污泥与生物质混合物通过炉体加料口加入在每个耐高温履带与循环提升碗形扇叶之间隔层;由电动机带动耐高温履带与循环提升碗形扇叶,对立窑桶式炉腔内的干燥污泥与生物质混合物进行分散化与链式喷烧;喷烧温控系统通过测温电子喷烧一体化设备对不同层级的温度进行准确检测,适时注入点燃混合气体,喷烧加热炉腔;进行1小时的无氧碳化处理,立窑传动循环提升式炉体系统与喷烧温控系统工作过程中,外部加料口、炉体出料口与外部出料口均为密闭,保证立窑桶式炉腔中的无氧环境;然后经过炉体出料口进入出料仓,最终由外部出料口排出。
37.实施例2
38.将某机构采集的印染污泥1吨,混合干燥废弃碎木屑之后总重为1.15吨,通过烘干等方法将含水率降低至35%左右。
39.开启电源,电动机采用的功率为7.5kw,天然气与空气的混合气体按照1:7.5 的比例输入立窑桶式炉腔,通过测温电子喷烧一体化设备喷烧加热炉腔,保持各层级炉腔温度为600℃;干燥污泥与生物质混合物通过外部加料口进入储料仓,后由炉体加料口进入立窑传动循环提升式炉体系统,15千克干燥污泥与生物质混合物通过炉体加料口加入在每个耐高温履带与循环提升碗形扇叶之间隔层;由电动机带动耐高温履带与循环提升碗形扇叶,
对立窑桶式炉腔内的干燥污泥与生物质混合物进行分散化与链式喷烧;喷烧温控系统通过测温电子喷烧一体化设备对不同层级的温度进行准确检测,适时注入点燃混合气体,喷烧加热炉腔;进行 1小时的无氧碳化处理,立窑传动循环提升式炉体系统与喷烧温控系统工作过程中,外部加料口、炉体出料口与外部出料口均为密闭,保证立窑桶式炉腔中的无氧环境;然后经过炉体出料口进入出料仓,最终由外部出料口排出。
40.实施例3
41.将某机构采集的造纸污泥1吨,混合干燥废弃碎木屑之后总重为1.2吨,通过烘干等方法将含水率降低至37%左右。
42.开启电源,电动机采用的功率为7.5kw,天然气与空气的混合气体按照1:7.5 的比例输入立窑桶式炉腔,通过测温电子喷烧一体化设备喷烧加热炉腔,保持各层级炉腔温度为600℃;干燥污泥与生物质混合物通过外部加料口进入储料仓,后由炉体加料口进入立窑传动循环提升式炉体系统,15千克干燥污泥与生物质混合物通过炉体加料口加入在每个耐高温履带与循环提升碗形扇叶之间隔层;由电动机带动耐高温履带与循环提升碗形扇叶,对立窑桶式炉腔内的干燥污泥与生物质混合物进行分散化与链式喷烧;喷烧温控系统通过测温电子喷烧一体化设备对不同层级的温度进行准确检测,适时注入点燃混合气体,喷烧加热炉腔;进行 1.5小时的无氧碳化处理,立窑传动循环提升式炉体系统与喷烧温控系统工作过程中,外部加料口、炉体出料口与外部出料口均为密闭,保证立窑桶式炉腔中的无氧环境;然后经过炉体出料口进入出料仓,最终由外部出料口排出。
43.实施例4
44.将某机构采集的制革污泥1吨,混合干燥废弃碎木屑之后总重为1.07吨,通过烘干等方法将含水率降低至39%左右。
45.开启电源,电动机采用的功率为7.5kw,天然气与空气的混合气体按照1:7.5 的比例输入立窑桶式炉腔,通过测温电子喷烧一体化设备喷烧加热炉腔,保持各层级炉腔温度为600℃;干燥污泥与生物质混合物通过外部加料口进入储料仓,后由炉体加料口进入立窑传动循环提升式炉体系统,15千克干燥污泥与生物质混合物通过炉体加料口加入在每个耐高温履带与循环提升碗形扇叶之间隔层;由电动机带动耐高温履带与循环提升碗形扇叶,对立窑桶式炉腔内的干燥污泥与生物质混合物进行分散化与链式喷烧;喷烧温控系统通过测温电子喷烧一体化设备对不同层级的温度进行准确检测,适时注入点燃混合气体,喷烧加热炉腔;进行 1.5小时的无氧碳化处理,立窑传动循环提升式炉体系统与喷烧温控系统工作过程中,外部加料口、炉体出料口与外部出料口均为密闭,保证立窑桶式炉腔中的无氧环境;然后经过炉体出料口进入出料仓,最终由外部出料口排出。