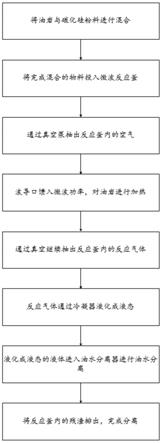
1.本发明属于采油行业原油泄漏回收处理技术领域,具体为一种油岩油泥裂解分离工艺。
背景技术:
2.油泥是石油开采、储运和炼制加工等工业过程中产生的含有原油和泥沙等的典型危险污染物,其性质多变,相态复杂,对环境危害大,必须进行处理。
3.然而,现有的油泥分离处理剂主要利用常规碱性或酸性化学助剂、高毒溶剂以及表面活性剂等复杂化合物,其使用量大,分离过程成本高,二次污染严重,原油的剥离效果差,分离不彻底,处理后的泥沙含油率达不到排放标准。
技术实现要素:
4.本发明的目的在于提供一种油岩油泥裂解分离工艺,以解决背景技术中提出的现有技术中,使用化学药剂处理油泥的使用量大、分离成本高的问题。
5.为解决上述技术问题,本发明所采用的技术方案是:
6.一种油岩油泥裂解分离工艺,包括以下步骤:
7.步骤s1:将油岩与吸波材料进行混合
8.步骤s2:将完成混合的物料投入裂解釜;
9.步骤s3:通过抽真空装置抽出裂解釜内的空气;
10.步骤s4:波导压力窗馈入微波功率,对油岩进行加热;
11.步骤s5:通过抽真空装置继续抽出裂解釜内的反应气体;
12.步骤s6:反应气体通过冷凝器液化成液态;
13.步骤s7:液体进入油水分离器进行油水分离;
14.步骤s8:将裂解釜内的残渣排出,完成分离。
15.根据上述技术方案,步骤s1中的油岩与吸波材料的比例为:0.3%~10%。
16.根据上述技术方案,步骤s3中裂解釜内的气压保持在
‑
0.09~0.097mpa。
17.根据上述技术方案,步骤s4中裂解釜内的温度升至450℃。
18.根据上述技术方案,步骤s7中,下层的水进入水接收罐,上层的油进入油接收罐。
19.根据上述技术方案,步骤s8中,裂解釜中的残渣,通过减温隔氧出料机排出。
20.根据上述技术方案,步骤s1中的吸波材料为碳化硅粉料、碳基铁粉料或者石墨粉料及其改性物。
21.根据上述技术方案,所述抽真空装置包括连接管道、缓冲罐和真空泵,连接管道连接至冷凝器与油水分离器之间的管道上,连接管道和缓冲罐、真空泵连接。
22.根据上述技术方案,所述冷凝器与抽真空装置连接。
23.与现有技术相比,本发明具有以下有益效果:
24.在本发明中,使用微波加热分离油岩的分离工艺切实可行。使用微波加热分离工
艺,用料更少、步骤简单,且最终分离效果良好,是一种优秀可行的分离工艺。分离出的油可再利用,且剩余的残渣满足《农用污泥中污染物控制标准》gb4284
‑
1984的标准,要求的含油量小于0.3%的标准。
附图说明
25.图1为油岩油泥裂解分离工艺流程图;
26.图2为本发明使用装置整体结构示意图之一;
27.图3为本发明使用装置整体结构示意图之二;
28.图4为裂解釜结构示意图;
29.图5为减温隔氧出料机结构示意图。
30.图中:1
‑
裂解釜,2
‑
油水分离器,3
‑
水接收罐,4
‑
油接收罐,5
‑
真空泵,6
‑
微波发生器,7
‑
直波导,8
‑
环行器,9
‑
水负载,10
‑
耦合器,11
‑
波导窗,12
‑
波导连接管,13
‑
缓冲罐,14
‑
减温隔氧出料机,15
‑
螺旋输送机,16
‑
电机,17
‑
氮气进入口,18
‑
固体残渣入口,19
‑
固体残渣出口,20
‑
进水口,21
‑
出水口,22
‑
搅拌棒,23
‑
螺旋叶片,24
‑
气相出口,25
‑
保温层。
具体实施方式
31.下面将结合本发明实施例中的附图,对本发明实施例中的技术方案进行清楚、完整地描述,显然,所描述的实施例仅仅是本发明一部分实施例,而不是全部的实施例。基于本发明中的实施例,本领域普通技术人员在没有做出创造性劳动前提下所获得的所有其他实施例,都属于本发明保护的范围。
32.实施例一
33.如图1所示,一种油岩油泥裂解分离工艺,包括以下步骤:
34.步骤s1:将油岩与吸波材料进行混合
35.步骤s2:将完成混合的物料投入裂解釜1;
36.步骤s3:通过抽真空装置抽出裂解釜1内的空气;
37.步骤s4:波导压力窗馈入微波功率,对油岩进行加热;
38.步骤s5:通过抽真空装置继续抽出裂解釜1内的反应气体;
39.步骤s6:反应气体通过冷凝器液化成液态;
40.步骤s7:液体进入油水分离器2进行油水分离;
41.步骤s8:将裂解釜1内的残渣排出,完成分离。
42.进一步的,步骤1中的吸波材料为碳化硅粉料、碳基铁粉料或者石墨粉料。
43.进一步的,微波的功率为5800mhz/2450mhz/915mhz。
44.步骤s1中吸波材料的使用比例为:0.3%~10%。
45.步骤s3中裂解釜1内的气压保持在
‑
0.09~0.097mpa。
46.步骤s4中裂解釜1内的温度升至450℃。
47.步骤s7中,下层的水进入水接收罐3,上层的油进入油接收罐4。
48.步骤s8中,裂解釜1中的残渣,通过减温隔氧出料机14排出。
49.步骤s1中的吸波材料为碳化硅粉料、碳基铁粉料或者石墨粉料及其改性物。
50.所述抽真空装置包括连接管道、缓冲罐13和真空泵5,连接管道连接至冷凝器与油
水分离器2之间的管道上,连接管道和缓冲罐13、真空泵5连接。
51.所述冷凝器与抽真空装置连接。
52.裂解釜1上设置有搅拌装置,搅拌装置包括搅拌电机、联轴器、搅拌棒22和螺旋叶片23;搅拌电机安装在裂解釜1上方,搅拌棒22通过联轴器与第一电机16相连;螺旋叶片23设置在搅拌棒22上;
53.裂解釜1上设置有波导连接管12,微波从波导连接管12进入裂解釜1中,波导连接管12的波导长度为80~400mm。裂解釜1顶部设置有气相出口24。
54.进一步的,裂解釜1的外部还设置有保温层25,保温层25用于保持裂解釜1内部的温度,防止温度消散过快,导致分离效果变差。
55.进一步的,减温隔氧出料机14包括螺旋输送机15、电机16和氮气进入口17,螺旋输送机15的转轴与电机16连接;氮气进入口17连接供氮装置;螺旋输送机15上设置固体残渣入口18、固体残渣出口19、进水口20和出水口21。其中,固体残渣入口18与裂解釜1连接,通过螺旋输送机15将裂解釜1内的残渣进行运输,并通过供氮装置向螺旋输送机15内输送氮气进行降温,最后经过冷却的残渣排出。
56.进一步的,冷凝器与油水分离器2之间设置缓冲罐13,缓冲罐13与抽真空装置连接。抽真空装置用来抽真空,缓冲罐13防止抽真空装置抽速过高,气流不稳定造成对装置的冲击和破坏。
57.进一步的,微波发生装置与波导连接,波导连接裂解釜1;裂解釜1上设置有波导连接管12,微波从波导连接管12进入裂解釜1中,波导连接管12上面安装有波导窗11。
58.进一步的,微波发生装置与弯波导连接,弯波导连接环行器8,环行器8与耦合器10连接,耦合器10与矩形波导(即直波导7)连接,矩形波导通过矩圆过渡波导连接圆波导;
59.进一步地,环行器8还连接水负载9,水负载9可以吸收来自裂解釜1的反射功率,起到保护微波源(微波发生器6)的作用。
60.环行器8是一个微波传输的单向器件,和水负载9一起使用可以让裂解釜1中产生的反射功率传导到水负载9上,让水负载9吸收后转变成热量耗散掉,防止反射的功率传导到微波源(微波发生器6)上,影响微波源的稳定使用。
61.耦合器10可以在大功率微波环境下耦合出100mw以下的小功率用于检测微波功率的大小和功率传输是否正常。耦合器10通过电缆(同轴电缆)连接功率计,功率计用于显示功率具体数值。
62.矩形波导和弯波导是传导微波功率的器件,让微波功率从微波源传导到裂解釜1并馈入。
63.在裂解釜1中产生的反射功率会使裂解釜1的效率下降、同时反射的微波功率还会干扰微波源的稳定工作和使用寿命,三销钉调配器可以在一定范围内调节反射功率的大小,让反射的功率维持在尽可能低的水平。
64.波导压力窗是由微波透波材料制成的一个密封器件,可以隔绝空气流动而且不影响微波功率通过。
65.实施例二
66.1、取100千克油岩,混入0.5%(即0.5千克)吸波材料。然后将混合后的物料通过进料机放入裂解釜1中。使用搅拌棒22充分搅拌使吸波材料料均匀分布在油页岩混合物中。接
着利用抽真空装置抽出裂解釜1中的空气,使裂解釜1中的气压保持在
‑
0.09mpa。抽负压有三个目的:一、引导挥发出的油气进入气相出口24;二、隔绝氧气;三、防止油气在高温环境下燃烧。
67.2、通过波导压力窗向裂解釜1中馈入微波,对物料进行加热。其中,微波的功率为915mhz,通过微波对物料进行加热,当温度达到80℃时,水分首先蒸发,当温度达到110℃时,油泥中的油气开始挥发,温度达到450℃时,油页岩中的油出尽。
68.3、抽真空装置抽出的气体经过冷凝器液化成液态,进入油水分离器2,通过油水分离器2分离开,下层的水进入水接收罐3,上层的油进入油接收罐4。在裂解釜1中的残渣,通过减温隔氧出料机14排出。经检测残渣油含量为0.28%,符合国家环保标准,可回归土地。(请确认实验数据是否正确)
69.通过微波加热升温,使得油岩的油气、水气挥发,残渣沉底,达到油岩分离成油、水、残渣的效果。但油岩中最能吸收微波的是水,随着温度升高,水分蒸发最快,剩余混合物对微波不敏感,无法继续加热升温。在油岩中混入0.3%~10%的吸波材料料,通过吸波材料料吸收微波发热,温度继续升高加热油岩,达到分离目的。
70.实施例三
71.本实施例为实施例二的进一步细化。1、取100千克油岩,混入2%(即2千克)吸波材料。然后将混合后的物料通过进料机放入裂解釜1中。使用搅拌棒22充分搅拌使吸波材料料均匀分布在油页岩混合物中。接着利用抽真空装置抽出裂解釜1中的空气,使裂解釜1中的气压保持在
‑
0.097mpa。
72.2、通过波导压力窗向裂解釜1中馈入微波,对物料进行加热。其中,微波的功率为2450mhz,通过微波对物料进行加热,当温度达到80℃时,水分首先蒸发,当温度达到110℃时,油泥中的油气开始挥发,温度达到450℃时,油页岩中的油出尽。
73.3、抽真空装置抽出的气体经过冷凝器液化成液态,进入油水分离器2,通过油水分离器2分离开,下层的水进入水接收罐3,上层的油进入油接收罐4。在裂解釜1中的残渣,通过减温隔氧出料机14排出。经检测残渣油含量为0.26%,符合国家环保标准,可回归土地。
74.实施例四
75.本实施例为实施例二的进一步细化。1、取100千克油岩,混入5%(即5千克)吸波材料。然后将混合后的物料通过进料机放入裂解釜1中。使用搅拌棒22充分搅拌使吸波材料料均匀分布在油页岩混合物中。接着利用抽真空装置抽出裂解釜1中的空气,使裂解釜1中的气压保持在
‑
0.09mpa。
76.2、通过波导压力窗向裂解釜1中馈入微波,对物料进行加热。其中,微波的功率为915mhz,通过微波对物料进行加热,80℃水分首先蒸发,当温度达到110℃时,油泥中的油气开始挥发,温度达到450℃时,油页岩中的油出尽。
77.3、抽真空装置抽出的气体经过冷凝器液化成液态,进入油水分离器2,通过油水分离器2分离开,下层的水进入水接收罐3,上层的油进入油接收罐4。在裂解釜1中的残渣,通过减温隔氧出料机14排出。经检测残渣油含量为0.25%,符合国家环保标准,可回归土地。
78.实施例五
79.本实施例为实施例二的进一步细化。1、取100千克油岩,混入8%(即8千克)吸波材料。然后将混合后的物料通过进料机放入裂解釜1中。使用搅拌棒22充分搅拌使吸波材料料
均匀分布在油页岩混合物中。接着利用抽真空装置抽出裂解釜1中的空气,使裂解釜1中的气压保持在
‑
0.095mpa。
80.2、通过波导压力窗向裂解釜1中馈入微波,对物料进行加热。其中,微波的功率为2450mhz,通过微波对物料进行加热,80℃水分首先蒸发,当温度达到110℃时,油泥中的油气开始挥发,温度达到450℃时,油页岩中的油基本出尽。
81.3、抽真空装置抽出的气体经过冷凝器液化成液态,进入油水分离器2,通过油水分离器2分离开,下层的水进入水接收罐3,上层的油进入油接收罐4。在裂解釜1中的残渣,通过减温隔氧出料机14排出。经检测残渣油含量为0.21%,符合国家环保标准,可回归土地。
82.需要说明的是,在本文中,诸如第一和第二等之类的关系术语仅仅用来将一个实体或者操作与另一个实体或操作区分开,而不一定要求或者暗示这些实体或操作之间存在任何这种实际的关系或者顺序。而且,术语“包括”、“包含”或者其任何其他变体意在涵盖非排他性的包含,从而使得包括一系列要素的过程、方法、物品或者设备不仅包括那些要素,而且还包括没有明确列出的其他要素,或者是还包括为这种过程、方法、物品或者设备所固有的要素。
83.最后应说明的是:以上所述仅为本发明的优选实施例而已,并不用于限制本发明,尽管参照前述实施例对本发明进行了详细的说明,对于本领域的技术人员来说,其依然可以对前述各实施例所记载的技术方案进行修改,或者对其中部分技术特征进行等同替换。凡在本发明的精神和原则之内,所作的任何修改、等同替换、改进等,均应包含在本发明的保护范围之内。