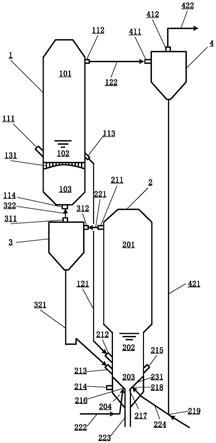
1.本发明涉及一种油气产品的生成装置及其制备方法。
背景技术:
2.目前工业化的煤气化或热解技术按气化炉床层特点可以分为:固定床(也叫移动床)、流化床(也叫沸腾床)、气流床三类;从发展时间来看,是从固定床到流化床再到气流床逐步发展演化的。
3.传统的固定床煤热解技术,以块煤为原料,生产半焦(兰炭)、荒煤气和油品。以此类技术生产的油品由于热解反应升温速率慢,固体颗粒停留时间长的同时油气体停留时间也长,二次反应(裂解和聚合)程度高,导致油品产量低,而且油品中主要以重质焦油为主,经济效益相应也较低。
4.气流床气化的优点是反应物在炉内停留时间短、碳转化率达到95%~99%,合成气质量高;但是高温气化为了使灰渣易于排出,要求所用煤灰熔点低(小于1300℃),含灰量低(低于10%~15%),否则需加入助熔剂(cao或fe2o3)并增加运行成本,这一点特别不利于我国煤种的使用。
5.流化床技术以粉煤为原料、且以空气或氧气等为气化剂,在适当的煤粒度和气速下,使床层中粉煤沸腾,气固两相充分混合接触,发生气化反应。其适用的煤种类较广、运行成本较低,且生产的油品质量相对固定床技术较高,从而受到越来越多的关注。传统流化床气化炉出口产品气中的粉尘含量较高,导致原料煤碳转化率低;并且一般的流化床气化炉由于物料和气体的停留时间、炉膛内的温度分布等因素的影响不能灵活控制原料煤、油气产品的停留时间以及热解反应程度。
6.中国专利申请cn106995728a中,为了实现高碳转化率、提高油气产品的质量,在采用流化床热解单元和流化床气化单元的基础上,增加了燃烧装置(流化床或者流化床与气流床结合),但由于燃烧装置的热废气作为热源、气化剂,进入气化单元和热解单元,造成粉煤热解过程中的氢气分压降低,影响了油品(焦油)的品质,而且该专利技术所涉及的系统有多个反应器耦合,系统复杂,操作难度高。
7.中国专利cn203890304u中,采用鼓泡床层和射流床层相结合,延长固态物料的停留时间,从而提高碳转化率;其中,控制气化炉内两段床层的反应温度使其具有温度梯度,提高气体(主要是是指甲烷)的产率,但由于其气化炉出口温度高,热解产物在高温下的停留时间长,无法生成油品。
8.因此,亟需一种能够生产出高品质油气产品以及较为简单的装置及方法。
技术实现要素:
9.本发明要解决的技术问题是克服现有流化床技术中粉煤在热解过程中停留时间短、油气产品停留时间长,油气产品产率低、且其中轻质芳烃的含量低、粉尘含量高,原料煤的碳转化率低的缺陷,而提供一种油气产品的生成装置及其制备方法。
10.为解决上述技术问题,本发明提供以下技术方案:
11.一种油气产品的生成装置,其包括依次连接的射流鼓泡流化床气化炉、鼓泡流化床热解炉和第一气固分离器;
12.所述射流鼓泡流化床气化炉的炉体内由下至上依次包括气化炉气室、气化炉气体分布板、气化炉密相区和气化炉稀相区;
13.所述气化炉密相区的炉体侧壁上设有气化炉半焦进口;所述气化炉气体分布板上设有第一气固分离器返料口和氧化剂进口、且所述氧化剂进口的轴线与所述第一气固分离器返料口的轴线相交;
14.所述鼓泡流化床热解炉设有热解炉半焦下料口和热解炉进气口;
15.所述第一气固分离器设有第一气固分离器下料管;
16.所述热解炉进气口与所述射流鼓泡流化床气化炉上设置的气化炉出气口连接;
17.所述热解炉半焦下料口与所述气化炉半焦进口连接;
18.所述第一气固分离器下料管与所述第一气固分离器返料口连接。
19.本发明中,所述气体分布板上设置的所述氧化剂进口会使得此处的氧气浓度较高,在点火之后即可形成一个射流高温氧化区,所述射流高温氧化区位于靠近所述气体分布板的上方区域、且位于所述气化炉密相区的下方。所述射流高温氧化区的温度一般高于1300℃。
20.其中,所述氧化剂进口的轴线与所述第一气固分离器返料口的轴线相交点是为了确保所述第一气固分离器返回的半焦与氧气充分接触混合;由于射流鼓泡流化床气化炉中氧气集中的地方就是高温区,半焦在此区域会发生剧烈二次反应,提高原料煤的碳转化率。
21.本发明中,所述气化炉出气口一般设置在所述气化炉稀相区的炉体侧壁上。所述气化炉出气口可用于排出高温合成气与半焦。较佳地,所述气化炉出气口通过气化炉出气管与所述热解炉进气口相连。
22.本发明中,较佳地,所述气化炉密相区的侧壁上还设置有气化炉粉煤进口。所述气化炉粉煤进口可根据需要设置若干个。
23.本发明中,较佳地,所述气化炉气体分布板为倒锥体式的气体分布板,且所述气化炉气体分布板的大口端与所述射流鼓泡流化床气化炉的侧壁相连接。
24.其中,较佳地,所述气化炉气体分布板的小口端与气化炉出渣口相连。所述气化炉出渣口较佳地连接有伸出所述气化炉气室的气化炉排渣管。所述气化炉出渣口以及所述气化炉排渣管用于排放所述气化炉气室内的料渣。
25.较佳地,所述氧化剂进口的轴线、所述第一气固分离器返料口的轴线与所述气化炉出渣口的轴线相交于一点。由于出渣口位于氧化段底部中央的位置,半焦在高温氧化区反应后生成的炉渣,易于从出渣口排出。
26.本发明中,所述第一气固分离器的返料口较佳地通过第一气固分离器返料吹送管与所述第一气固分离器下料管连接。
27.其中,较佳地,所述第一气固分离器返料吹送管还连接有第一气固分离器吹送气进口。所述第一气固分离器吹送气进口用于通入将来自所述第一气固分离器的物料吹送至所述射流高温氧化区的气体。
28.本发明中,所述氧化剂进口较佳地连接有氧化剂进气管。
29.本发明中,较佳地,所述气化炉气室的侧壁上设有气化炉流化气进口。
30.本发明中,所述鼓泡流化床热解炉的底部较佳地高于所述射流鼓泡流化床气化炉的顶部。用于保证从低压往高压输送物料时顺利进行。
31.本发明中,所述热解炉半焦下料口较佳地通过热解炉半焦下料管与所述气化炉半焦进口相连。
32.本发明中,所述鼓泡流化床热解炉的炉体内由下至上可依次包括热解炉气室、热解炉气体分布板、热解炉密相区和热解炉稀相区。
33.其中,较佳地,所述热解炉半焦下料口设置于所述热解炉密相区的炉体侧壁上。所述热解炉密相区的炉体侧壁上一般还设置有热解炉粉煤进口。所述热解炉粉煤进口可根据需要设置若干个。
34.其中,所述热解炉气体分布板可为圆形面板式的气体分布板,较佳地为从外侧至轴心厚度渐缩的气体分布板。
35.其中,较佳地,所述热解炉进气口设置于所述热解炉气室的底部。
36.本发明中,较佳地,所述第一气固分离器还设有第一气固分离器出气口和第一气固分离器进气口。所述第一气固分离器出气口可连接用于排出油气产品的第一气固分离器出气管。
37.其中,较佳地,所述第一气固分离器进气口通过热解炉出气管与热解炉出口连接。所述热解炉出口一般设置在所述热解炉稀相区的炉体侧壁上。为了生成油气产品,所述热解炉出口的温度一般为550-700℃之间。
38.本发明中,较佳地,所述油气产品生成装置还包括第二气固分离器,所述第二气固分离器设有第二气固分离器进气口、第二气固分离器出气口和第二气固分离器下料管;
39.所述气化炉出气口与所述第二气固分离器进气口连接;
40.所述第二气固分离器出气口与所述热解炉进气口连接;
41.所述第二气固分离器下料管与所述气化炉密相区的炉体侧壁上设置的第二气固分离器返料口连接。
42.本发明中,通过设置第二气固分离器,确保大量的半焦不会短时间进入鼓泡流化床热解炉磨损其中的分布板,并且所述第二气固分离器捕集的半焦回到所述气化炉密相区,起到稳定床层的作用。
43.其中,较佳地,所述热解炉进气口通过第二气固分离器出气管与所述第二气固分离器出气口连接。
44.其中,较佳地,所述气化炉出气口通过所述气化炉出气管与所述第二气固分离器进气口连接。
45.本发明中,所述第二气固分离器用于分离所述射流鼓泡流化床气化炉产生的半焦和高温合成气。所述高温合成气可作为所述鼓泡流化床热解炉反应的热载体。
46.本发明中涉及的稀相区、密相区为流化床领域的通用名称,流化床界面以下称为密相区,也叫浓相区,界面以上称为稀相区。
47.本发明还提供一种油气产品的制备方法,其采用如上所述油气产品生成装置;
48.所述制备方法包括:在所述油气产品生成装置中加入原料反应即可。
49.本发明中,较佳地,所述制备方法包括以下步骤:
50.s10:粉煤、半焦、流化气和氧化剂在所述射流鼓泡流化床气化炉内气化,得高温合成气和半焦;
51.s30:粉煤与所述高温合成气在所述鼓泡流化床热解炉内热解,得油气产品和半焦;
52.s40:所述第一气固分离器中分离所述油气产品和半焦,分离后的半焦送至所述射流鼓泡流化床气化炉内进一步气化。
53.其中,所述氧化剂较佳地含有氧气,且含有氮气、蒸汽和二氧化碳中的一种或多种。
54.其中,较佳地,所述高温合成气的温度为900℃-1000℃。
55.其中,所述高温合成气主要可包含一氧化碳、二氧化碳、氢气、甲烷等气体,其中氢气的体积浓度为20-40%,并且根据进入气化炉的蒸汽量可再提高。所述流化气可为本领域常规,可为蒸汽、氮气、二氧化碳或所述油气产品分离后循环回来的气体。
56.本发明中,较佳地,步骤s30之前还包括步骤s20:s10中的高温合成气和半焦在所述第二气固分离器内分离;分离后的半焦送至所述射流鼓泡流化床气化炉内进一步气化,分离后的所述高温合成气进入所述鼓泡流化床热解炉。
57.本发明中,较佳地,s10和s30中,粉煤的最大粒径不超过10毫米、且粉煤粒径小于0.1毫米的颗粒重量不超过粉煤总重量的10wt%。
58.本发明中,s10中的半焦可包括所述第一气固分离器捕集分离的半焦和加入的原料半焦,或者可包括所述第一气固分离器捕集分离的半焦、所述第二气固分离器捕集分离的半焦和加入的原料半焦。本发明的半焦是广义的常规的,是指原料煤通过热解脱除挥发分后或气化后的颗粒,其含碳量相对炉渣来说较高,均通称为半焦(char)。
59.本发明中,所述油气产品可为本领域常规理解的油气产品,其一般是指在所述鼓泡流化床热解炉内粉煤与来自所述射流鼓泡流化床气化炉的高温合成气或者其他热载体充分接触换热后发生快速热解反应生成的,主要包含油品、一氧化碳、二氧化碳、氢气、甲烷、水蒸气以及其他气体;所述油品可为本领域常规理解的油品,其中主要含有焦油、轻质芳烃和其他脂肪族有机物。
60.本发明中的油品产率可高达所述鼓泡流化床热解炉的入炉粉煤“格金指数”的1.5倍以上。油品中轻质芳烃含量可达70%以上。轻质芳烃(不含酚类)中,苯和甲苯等单环物质约占80%,其他双环和三环芳烃约占20%。
61.本发明中,所述第二气固分离器的总分离效率的范围较佳地为65-75%,dp50为100-200μm(分离效率为50%以下颗粒的直径)。
62.其中,所述第一气固分离器的总的分离效率较佳地大于99%,dp50为10-20微米。
63.在符合本领域常识的基础上,上述各优选条件,可任意组合,即得本发明各较佳实例。
64.本发明所用试剂和原料均市售可得。
65.本发明的积极进步效果在于:
66.1)采用本发明的油气产品生成装置,粉煤进入鼓泡流化床热解炉的升温速率快,粉煤的停留时间提升,油气产品停留时间缩短,使得粉煤热解反应充分大幅提高油品(焦油)产率;
67.2)采用本发明的油气产品生成装置,由本发明气化炉生成的高温合成气中的氢气分压较高(可达20-40%),从而进入热解炉后,提高了油品产率及油品中轻质芳烃的含量;油品产率可以高达鼓泡流化床热解炉入炉粉煤“格金指数”的1.5倍以上,油品中轻质芳烃含量可达70%以上,轻质芳烃(不含酚类)中,苯和甲苯等单环物质约占80%,其他双环和三环芳烃约占20%;
68.3)采用本发明的油气产品生成装置,降低了物料循环倍率以及油气产品中的粉尘含量;并且能够强制细半焦颗粒发生剧烈的二次反应,提高了粉煤热解气化过程中入炉原料煤的碳转化率,可达97%以上。
69.4)本发明的油气产品生成装置操作灵活方便。
附图说明
70.图1为油气产品生成装置图。
71.图2为油气产品制备的工艺流程图。
72.其中:1.鼓泡流化床热解炉,101.热解炉稀相区,102.热解炉密相区,103.热解炉气室,111.热解炉粉煤进口,112.热解炉出口,113.热解炉半焦下料口,114.热解炉进气口,121.热解炉半焦下料管,122.热解炉出气管,131.热解炉气体分布板,2.射流鼓泡流化床气化炉,201.气化炉稀相区,202.气化炉密相区,203.射流高温氧化区,204.气化炉气室,211.气化炉出气口,212.气化炉半焦进口,213.第二气固分离器返料口,214.气化炉流化气进口,215.气化炉粉煤进口,216.氧化剂进口,217.气化炉出渣口,218.第一气固分离器返料口,219.第一气固分离器吹送气进口,221.气化炉出气管,222.氧化剂进气管,223.气化炉排渣管,224.第一气固分离器返料吹送管,231.气化炉气体分布板,3.第二气固分离器,311.第二气固分离器出气口,312.第二气固分离器进气口,321.第二气固分离器下料管,322.第二气固分离器出气管,4.第一气固分离器,411.第一气固分离器进气口,412.第一气固分离器出气口,421.第一气固分离器下料管,422.第一气固分离器出气管。
具体实施方式
73.下面通过实施例的方式进一步说明本发明,但并不因此将本发明限制在所述的实施例范围之中。下列实施例中未注明具体条件的实验方法,按照常规方法和条件,或按照商品说明书选择。
74.实施例1油气产品生成装置
75.如图1所示的油气产品生成装置包括鼓泡流化床热解炉1,射流鼓泡流化床气化炉2,第二气固分离器3和第一气固分离器4。
76.鼓泡流化床热解炉1的炉体内由下至上依次包括热解炉气室103、热解炉气体分布板131、热解炉密相区102和热解炉稀相区101。热解炉密相区102的炉体侧壁上设置有热解炉半焦下料口113和热解炉粉煤进口111;热解炉稀相区101的炉体侧壁上设置有热解炉出口112;热解炉气室103的底部设置有热解炉进气口114。
77.射流鼓泡流化床气化炉2的炉体内由下至上依次包括气化炉气室204、气化炉气体分布板231、气化炉密相区202和气化炉稀相区201。气化炉密相区202的炉体侧壁上设有气化炉半焦进口212、第二气固分离器返料口213和气化炉粉煤进口215;气化炉半焦进口212
通过热解炉半焦下料管121与热解炉半焦下料口113连接;气化炉稀相区201的炉体侧壁上设有气化炉出气口211,气化炉出气口211通过气化炉出气管221与热解炉进气口114连接;气化炉气室204的炉体侧壁上设有气化炉流化气进口214。气化炉气体分布板231上设有第一气固分离器返料口218和氧化剂进口216;氧化剂进口216连接有氧化剂进气管222,此处的氧气浓度较高,在点火之后即可形成一个射流高温氧化区203,射流高温氧化区203位于靠近气体分布板21的上方区域、且位于气化炉密相区202的下方,所述射流高温氧化区的温度一般高于1300℃。
78.其中,气化炉气体分布板231为倒锥体式的气化炉气体分布板,倒锥体的大口端与射流鼓泡流化床气化炉2的侧壁相连接;倒锥体的小口端与气化炉出渣口217连接,气化炉出渣口217连接有伸出气化炉气室204的气化炉排渣管223。
79.第一气固分离器4设有第一气固分离器进气口411、第一气固分离器出气口412和第一气固分离器下料管421;第一气固分离器出气口412连接用于排出油气产品的第一气固分离器出气管422。热解炉出口112通过热解炉出气管122与第一气固分离器4连接。第一气固分离器的返料口218通过第一气固分离器返料吹送管224与第一气固分离器下料管421连接;第一气固分离器返料吹送管224还连接有第一气固分离器吹送气进口219。第一气固分离器吹送气进口219用于通入将来自第一气固分离器4的物料吹送至射流高温氧化区203的气体。
80.第二气固分离器3设有第二气固分离器进气口312、第二气固分离器出气口311和第二气固分离器下料管321;第二气固分离器下料管321与第二气固分离器返料口213连接,热解炉进气口114通过第二气固分离器出气管311与第二气固分离器出气口322连接。
81.其中,氧化剂进口216的轴线、第一气固分离器返料口218的轴线与气化炉出渣口217的轴线相交于射流高温氧化区203中的一点。
82.实施例2油气产品制备方法
83.按照如图1所示的装置制备油气产品。
84.如图2所示,步骤s10,粉煤、半焦、流化气和氧化剂在射流鼓泡流化床气化炉2内气化,得高温合成气和半焦:粉煤、鼓泡流化床热解炉1的半焦和第二气固分离器3的半焦分别通过气化炉粉煤进口215和气化炉半焦进口212和第二气固分离器返料口213进入气化炉密相区202,与由氧化剂进气管222通入的氧化剂和流化气进口214通入的流化气充分混合,并发生剧烈的化学反应生成高温合成气和半焦。反应后生成的炉渣通过气化炉出渣口217和气化炉排渣管223排出装置气化炉,生成的高温合成气经由气化炉稀相区201,通过气化炉出气口211、气化炉出气管221进入第二气固分离器3。
85.步骤s20,步骤s10中的高温合成气和半焦由第二气固分离器进气口312进入并在第二气固分离器3内分离;分离后的半焦由热解炉半焦下料管121送至射流鼓泡流化床气化炉2内进一步气化,分离后的高温合成气温度在900-1000℃之间,进入鼓泡流化床热解炉1内作为热载体。
86.步骤s30:粉煤与高温合成气在鼓泡流化床热解炉1内热解,得油气产品和半焦:分离后的高温合成气由第二气固分离器出气口311和第二气固分离器出气管322进入热解炉气室103,在热解炉炉膛内,粉煤通过粉煤进口111进入热解炉密相区102,与高温合成气充分混合,发生快速热解反应生成油气产品(温度550-700℃之间)和半焦;热解反应生成的半
焦通过热解炉半焦下料口113和热解炉半焦下料管121进入射流鼓泡流化床气化炉2继续参与气化反应,油气产品由热解炉出口112和热解炉出气管122进入第一气固分离器4。
87.步骤s40:在第一气固分离器4中分离油气产品和半焦,分离后的半焦由第一气固分离器下料管421送至射流高温氧化区203继续反应。分离后的油气产品经第一气固分离器4出气口412和出气管422送至下游系统。
88.通过本实施例的制备方法,油品产率可以高达鼓泡流化床热解炉1入炉粉煤“格金指数”的1.5倍以上,油品中轻质芳烃含量可达70%以上,轻质芳烃(不含酚类)中,苯和甲苯等单环物质约占80%,其他双环和三环芳烃约占20%;碳转化率达97%以上。