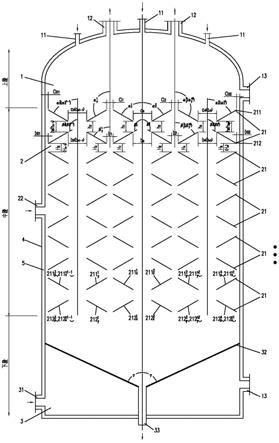
给热热解方法,存在传热效率不高、吸热效率低导致热量利用效率低、热解反应速度慢、反应时间较长、能耗高、热解固态残渣不能满足超洁净排放环保指标要求等问题。
技术实现要素:
8.为了提高有机固废热解提馏过程的给热效率与吸热效率,降低能耗,本技术提供一种热载体直接给热式多级串并联湍动床热解提馏反应器。
9.本技术提供的一种热载体直接给热式多级串并联湍动床热解提馏反应器,采用如下的技术方案:
10.一种热载体直接给热式多级串并联湍动床热解提馏反应器,包括反应器壳体,所述反应器壳体包括相互连通的反应器上段、反应器中段、反应器下段和耐火隔热衬里;
11.所述反应器上段设置有机固废物料进口以及混合物出口,所述反应器中段具有若干组串联的并联湍动微反应床,所述反应器下段具有热载体进口、热解固态残渣出口;固废物料与高温热载体直接接触换热进行热解提馏反应,在反应器的内部有机固废物料自上而下流动,高温热载体与有机固废热解提馏产物气态有机质两者的混合物自下而上流动;所述并联湍动微反应床内以及相邻串联的并联湍动微反应床之间均具有主反应区,所述并联湍动微反应床与所述耐火隔热衬里的内壁形成有副反应区,所述主反应区和所述副反应区相互并联。
12.通过采用上述技术方案,高温热载体由反应下段的热载体进口上升,有机固废物由反应上段的固废进口向下流动,高温热载体与有机固废于反应中段的提馏反应区直接接触,因此通过有机固废与高温热载体(热量)直接接触的“直接式”给热方法,大大提高了有机固废热解提馏过程的给热效率与吸热效率,提高了热量利用效率、有效降低了能耗。
13.构建多级串联的并联湍动微反应床,使有机固废物料在每一组微反应床中呈现气固两相以湍动悬浮的充分混合状态与高温热载体携带的热量直接接触高效换热,一方面大大提高了有机固废热解提馏过程的给热效率与吸热效率,提高了热量利用效率、有效降低了能耗,另一方面多级串联的并联湍动悬浮微反应床有效延长了有机固废物料的停留时间,充分的气固两相湍动悬浮混合状态大大提高了有机固废物料去除有毒有害物质和转化为低分子量的气态烃类物质及/或气相油品的热解反应和提馏反应速度、缩短了热解提馏反应时间、提高了有机固废中的有机质转化回收产率,达到有机固废热解固态残渣满足超洁净排放环保指标要求、避免了二次污染,实现有机固废彻底无害化治理和有机质资源化转化回收的环境友好和资源节约的有益效果。
14.主反应区和副反应区可提供多层次的反应区域,使有机固废更充分地在反应器中段进行热提馏反应,进一步提高热解效率。
15.可选的,所述并联湍动微反应床包括至少一组复合式上导流板和至少一组复合式下导流板。
16.通过采用上述技术方案,通过上导流板和下导流板的组合即可形成主反应区和副反应区,一方面可根据实际产品需要调整上导流板和下导流板的组合搭配,从而适应提馏不同的有机固废原料;另一方面设备生产简单,且配件较少便于后期维护。
17.可选的,所述反应器中段具有与所述反应器壳体内连通的二次热载体进口。
18.通过采用上述技术方案,可随时补充热载体,使热载体与并联湍动微反应床内的
有机固废原料充分接触,从而提升有机固废原料的分解提馏效率。
19.可选的,所述二次热载体进口位于相邻的并联湍动微反应床之间。
20.通过采用上述技术方案,热载体可充分接触副反应区和主反应区,从而进一步提升热提馏效率。
21.可选的,所述反应器下段设置有用于均匀分配热载体的热载体分布器。
22.通过采用上述技术方案,可将热载体均匀分配,从而进一步提升热提馏效率。
23.可选的,所述反应器上段和反应器下段均设置有人孔。
24.通过采用上述技术方案,可供工作人员进入进行检修。
25.可选的,所述反应器壳体内的反应压力为
‑
0.1
‑
10mpag,反应温度为300
‑
1000℃;高温热载体的压力为0.01
‑
10mpag,温度为300
‑
1000℃。
26.通过采用上述技术方案,上述参数具有较好的热提馏效果同时节省能量消耗。
27.综上所述,本技术包括以下至少一种有益技术效果:
28.1.本技术公开的技术针对现有通过高温热载体“间接式”给热的含有机质的固体废弃物质热解反应器技术存在的不足,采用有机固废贫氧或无氧环境的中高温热解提馏工艺,通过有机固废与高温热载体(热量)直接接触的“直接式”给热方法并构建多级串联的并联湍动微反应床,使有机固废物料在每一组微反应床中呈现气固两相以湍动悬浮的充分混合状态与高温热载体携带的热量直接接触高效换热,一方面大大提高了有机固废热解提馏过程的给热效率与吸热效率,提高了热量利用效率、有效降低了能耗,
29.另一方面多级串联的并联湍动悬浮微反应床有效延长了有机固废物料的停留时间,充分的气固两相湍动悬浮混合状态大大提高了有机固废物料去除有毒有害物质和转化为低分子量的气态烃类物质及/或气相油品的热解反应和提馏反应速度、缩短了热解提馏反应时间、提高了有机固废中的有机质转化回收产率,达到有机固废热解固态残渣满足超洁净排放环保指标要求、避免了二次污染,实现有机固废彻底无害化治理和有机质资源化转化回收的环境友好和资源节约的有益效果,此外,串联的并联湍动微反应床比单纯串联并联湍动微反应床大大增加了主反应区的数量和区域,特别适合应用于大型化规模装置。
30.2.本技术采用的热载体为单一组分气体(氧气除外)或贫氧或无氧的多组分气体混合物。如n2、氩气等惰性气体、co2气体、过热蒸汽或燃料燃烧后的烟气、热解尾气、合成气(主要化学成份为h2、co)、炼厂干气或石化废气或弛放尾气等单一组分气体或此类气体的多组分气体混合物,均具有易获得性、安全性和可实现废气的再利用。
31.3.采用多级串并联湍动床兼具固定床停留时间长和流化床的反应性能更好优点,采用直接给热式加热方式克服了旋转炉(窑)传热效率不高的缺点。
附图说明
32.图1是本技术实施例1的结构示意图。
33.图2是本技术实施例2的结构示意图。
34.图3是本技术实施例3反应器中段的结构示意图。
35.图4是本技术实施例3并联湍动微反应床的主视图。
36.图5是本技术实施例4反应器中段的结构示意图。
37.图6是本技术实施例4并联湍动微反应床的主视图。
38.附图标记说明:1、反应器上段;2、反应器中段;3、反应器下段;4、反应器壳体;5、耐火隔热衬里;11、有机固废物料进口;12、混合物出口;13、人孔;21、并联湍动微反应床;22、二次热载体加入口;210、湍动微反应床单体;211、复合式上导流板;212、复合式下导流板;31、热载体进口;32、热载体分布器;33、热解固态残渣出口;210、并联湍动微反应床单体;211、复合式上导流板;212、复合式下导流板;211x、上导流板单体x;211y、上导流板单体y;212x、下导流板单体x;212y、下导流板单体y;211x1、第一块上导流板单体x;211x2、第二块上导流板单体x;211x3、第三块上导流板单体x;211x4、第四块上导流板单体x;211xn、第n块上导流板单体x;211y1、第一块上导流板单体y;211y2、第二块上导流板单体y;211y3、第三块上导流板单体y;211y4、第四块上导流板单体y;211yn、第n块上导流板单体y;212x1、第一块下导流板单体x;212x2、第二块下导流板单体x;212x3、第三块下导流板单体x;212x4、第四块下导流板单体x;212xn、第n块下导流板单体x;212y1第一块下导流板单体y;212y2、第二块下导流板单体y;212y3、第三块下导流板单体y;212y4、第四块下导流板单体y;212yn、第n块下导流板单体y。
具体实施方式
39.以下结合附图1
‑
6对本技术作进一步详细说明。
40.本技术实施例公开一种热载体直接给热式多级串并联湍动床热解提馏反应器。一种热载体直接给热式多级串并联湍动床热解提馏反应器,参照图1,包括反应器壳体4,反应器壳体4包括相互连通的反应器上段1、反应器中段2、反应器下段3和耐火隔热衬里5。
41.反应器上段1、中段2和下段3的反应器壳体4及其耐火隔热衬里5的截面形状可以是圆筒形或椭圆形,也可以是矩形(正方形或长方形)或多边形,反应器上段1、中段2和下段3的反应器壳体4及耐火隔热衬里5的截面形状可以是相同截面结构和截面面积,也可以是不同截面形状、不同截面面积及其不同结构的组合。
42.反应器耐火隔热衬里5可以是n(n≥1)层耐火隔热浇注料结构,也可以是n(n≥1)层的耐火隔热砖结构,也可以是耐火隔热浇注料与耐火隔热砖的组合结构,也可以是列管式或盘管式的膜式水冷壁结构,也可以是冷却夹套结构,也可以是这几种结构形式的不同组合。
43.反应器的上段1、中段2、下段3及反应器壳体4和耐火隔热衬里5可以是整体结构,也可以是分段连接结构。
44.反应器壳体内的热解提馏反应压力为
‑
0.1
‑
10mpag,反应温度为300
‑
1000℃;高温热载体的压力为0.01
‑
10mpag,温度为300
‑
1000℃。
45.反应器上段的顶部或侧面上部位置设置 n(n≥1)个有机固废物料进口、n(n≥1)个气态有机质热解提馏产物和热载体混合物出口及人孔。
46.反应器中段2为有机固废物料热解提馏段,设置有n(n≥1)组串联的并联湍动微反应床21和n(n≥0)个二次热载体加入口22。
47.反应器中段2的n(n≥1)组并联湍动悬浮微反应床21相互串联构成,每一组并联湍动悬浮微反应床21由一组复合式上导流板211和一组复合式下导流板212构成,且以反应器壳体4中心线为中心轴对称布置或非对称布置;每一组复合式上导流板211以反应器壳体4中心线为中心轴由n(n≥2,且n=n1+n2)个上导流板单体x(211xn1)和上导流板单体y
(211yn2)组成,且以n1(n1≥1)个上导流板单体x(211x)和n2(n2≥1)个上导流板单体y(211y)两种形状对称或非对称依次交错并联组合构成;同理,每一组复合式下导流板212以反应器壳体4中心线为中心轴由n(n≥2,且n=n1+n2)个下导流板单体x(212x)和下导流板单体y(212y)组成,且以n1(n1≥1)个下导流板单体x(212x)和n2(n2≥1)个下导流板单体y(212y)两种形状对称或非对称依次交错并联组合构成。
48.反应器中段2的每一组并联湍动悬浮微反应床21的每一组复合式上导流板211,其n1(n1≥1)个上导流板单体x(211x n1)的上表面与反应器壳体4中心线的夹角αxn(上标n≥1)为0
‑
180
°
之间的任一角度,且αx1和αx2、αx3 和 αx4、
ꢀ…ꢀ
αxn
‑
1和αxn成对同时为锐角(0
°
<αxn ≤ 90
°
)或同时为钝角(90
°
≤αxn < 180
°
);其n2(n2≥1)个上导流板单体y(211yn2)的上表面与反应器壳体4中心线的夹角αyn(上标n≥1)为0
‑
180
°
之间的任一角度,且αy1 和 αy2、 αy3和αy4、
ꢀ…ꢀ
αyn
‑
1和αyn成对同时为锐角(0
°
<αyn ≤ 90
°
)或同时为钝角(90
°
≤αyn < 180
°
);并且,当αxn为锐角(0
°
<αxn ≤ 90
°
)时 αyn为钝角(90
°
≤αyn < 180
°
),当αxn为钝角(90
°
≤αxn < 180
°
)时αyn为锐角(0
°
<αyn ≤ 90
°
); 以反应器壳体4中心线为对称轴设置的两个相邻上导流板单体x(211x 1 及 / 或211x 2)之间中心区域的底部(0
°
<αx1 和αx2 < 90
°
时)或顶部(90
°
≤αx1 和αx2 < 180
°
时)开有宽度或直径为a0(a0≥0)的缺口;上导流板单体x(211x n1)与其相邻的上导流板单体y(211yn2)之间中心区域的顶部和底部开设宽度为an(a1、a2、a3、
…ꢀ
an,an≥0)的缺口或环隙或不开设缺口或环隙;上导流板单体x(211x n1 及/或211x n1
‑
1)及/或上导流板单体y(211y n2及/或211y n2
‑
1)与反应器耐火隔热衬里5内壁面之间开有宽度为a01和a02( a01≥0、a02≥0)的缺口或环隙,开设的此类缺口或环隙均为固态物料下行和气态物料上行的通道,且a0、a1、a2、a3、
…ꢀ
an和a01及a02均不同时为0;上导流板单体x(211x n1 及 / 或211y n2)的形状与反应器壳体4及其耐火隔热衬里5的截面形状相匹配。
49.反应器中段2的每一组并联湍动悬浮微反应床21的每1组复合式下导流板212,其n1(n1≥1)个下导流板单体x(212x n1)的上表面与反应器壳体4中心线的夹角βxn(上标n≥1)为0
‑
180
°
之间的任一角度,且βx1和βx2、βx3 和 βx4、
ꢀ…
βxn
‑
1和βxn成对同时为锐角( 0
°
<βxn ≤ 90
°
)或同时为钝角(90
°
≤βxn < 180
°
);其n2(n2≥1)个下导流板单体y(212yn2)的上表面与反应器壳体4中心线的夹角βyn(上标n≥1)为0
‑
180
°
之间的任一角度,且βy1 和 βy2、 βy3和βy4、
ꢀ…ꢀ
βyn
‑
1和βyn成对同时为锐角(0
°
<βyn ≤ 90
°
)或同时为钝角(90
°
≤αyn < 180
°
);并且,当βxn为锐角(0
°
<βxn ≤ 90
°
)时 αyn为钝角(90
°
≤αyn < 180
°
),当βxn为钝角(90
°
≤βxn < 180
°
)时βyn为锐角(0
°
<βyn ≤ 90
°
);以反应器壳体4中心线为对称轴设置的两个相邻下导流板单体x(212x1 及 / 或212x 2)之间中心区域的底部(0
°
<βx1 和βx2 < 90
°
时)或顶部(90
°
≤βx1 和βx2 < 180
°
时)开有宽度或直径为b0(b0≥0)的缺口;下导流板单体x(212x n1)与其相邻的下导流板单体y(212yn2)之间中心区域的顶部和底部开设宽度为bn(b1、b2、b3、
…ꢀ
bn,bn≥0)的缺口或环隙或不开设缺口或环隙;下导流板单体x(212x n1 及/或212x n1
‑
1)及/或下导流板单体y(212y n2及/或212y n2
‑
1)与反应器耐火隔热衬里5内壁面之间开有宽度为b01和b02(b01≥0、b02≥0)的缺口或环隙,开设的此类缺口或环隙均为固态物料下行和气态物料上行的通道,且b0、b1、b2、b3、
…ꢀ
bn和b01及b02均不同时为0;下导流板单体x和下导流板单体y(212x n1 及 / 或212y n2)的形状与反应器壳体4及其耐火隔热衬里5的截面形状相匹配。
50.反应器中段2每一组并联湍动悬浮微反应床21的复合式上导流板211的n1(n1≥1)个上导流板单体x(211x n1)上表面与反应器壳体4中心线的夹角αxn(上标n≥1,且αx1和αx2、αx3 和 αx4、
ꢀ…ꢀ
αxn
‑
1和αxn同时成对)为锐角(0
°
<αxn ≤ 90
°
)时,相对应的复合式下导流板212n1(n1≥1)个下导流板单体x(212x n1)上表面与反应器壳体4中心线的夹角βxn(上标n≥1,且βx1和βx2、βx3 和 βx4、
ꢀ…
βxn
‑
1和βxn同时成对)为钝角(90
°
≤βxn < 180
°
);同理,复合式上导流板211的n1(n1≥1)个上导流板单体x(211x n1)上表面与反应器壳体4中心线的夹角αxn(上标n≥1,且αx1和αx2、αx3 和 αx4、
ꢀ…ꢀ
αxn
‑
1和αxn同时成对)为锐角(90
°
≤αxn < 180
°
)时,相对应的复合式下导流板212n1(n1≥1)个下导流板单体x(212x n1)上表面与反应器壳体4中心线的夹角βxn(上标n≥1,且βx1和βx2、βx3 和 βx4、
ꢀ…
βxn
‑
1和βxn同时成对)为钝角(0
°
≤βxn < 90
°
)。
51.反应器中段2的每一组并联湍动悬浮微反应床21内部,由复合式上导流板211的n1(n1≥1)个上导流板单体x(211x n1)和n2(n2≥1)个上导流板单体y(211yn2)分别与复合式下导流板212所相对应位置的n1(n1≥1)个下导流板单体x(212x n1)和n2(n2≥1)个下导流板单体y(212yn2)之间区域构成n1(当0
°
<αxn ≤ 90
°
,且n1=n2时)或n1
‑
1(当90
°
≤αxn < 180
°
,且n1=n2时)或n2(当0
°
<αxn ≤ 90
°
,且n1≠n2时)或n2+1(当90
°
≤αxn < 180
°
,且n1≠n2时)个截面主体形状为菱形或椭圆形的相并联的主反应区; 最外侧的上导流板单体x(212x n1 及/或212x n1
‑
1)和最外侧的下导流板单体y(212x n2及/或212x n2
‑
1)与反应器耐火隔热衬里5内壁面之间区域构成2个截面主体形状为半菱形或半椭圆形的副反应区,并与主反应区相并联。
52.反应器中段2的每相邻两组串联的并联湍动悬浮微反应床21之间,即上一组(第n
‑
1组)并联湍动悬浮微反应床21复合式下导流板212的n1(n1≥1)个下导流板单体x(212x n1)和n2(n2≥1)个下导流板单体y(212yn2)分别与下一组(第n
‑
1组)并联湍动悬浮微反应床21复合式上导流板211所相对应位置的n1(n1≥1)个上导流板单体x(211x n1)和n2(n2≥1)个上导流板单体y(211yn2)之间区域构成n1
‑
1(当0
°
<αxn ≤ 90
°
,且n1=n2时)n1(当90
°
≤αxn < 180
°
,且n1=n2时)或n2+1(当0
°
<αxn ≤ 90
°
,且n1≠n2时)或n2(当90
°
≤αxn < 180
°
,且n1≠n2时)个截面主体形状为菱形或椭圆形的相并联的主反应区;上一组(第n
‑
1组)并联湍动悬浮微反应床21最外侧的下导流板单体y(212x n2及/或212x n2
‑
1)和下一组(第n
‑
1组)最外侧的上导流板单体x(212x n1 及/或212x n1
‑
1)与反应器耐火隔热衬里5内壁面之间区域构成2个截面主体形状为半菱形或半椭圆形的副反应区,并与主反应区相并联。
53.反应器中段2每一组并联湍动悬浮微反应床21的复合式上导流板211的n1(n1≥1)个上导流板单体x(211x n1)和 n2(n2≥1)个上导流板单体y(211yn2)与相对应的复合式下导流板212的n1(n1≥1)个下导流板单体x(212x n1)和 n2(n2≥1)个下导流板单体y(212yn2)相对应位置竖直方向之间的床内间距hn(下标n=n1+n2,且h1和h2、h3 和 h5、 h4 和 h6、
ꢀ…ꢀ
hn
‑
2和hn同时成对),与相对应位置的缺口或环隙an(a0、a1、a2、a3、
…ꢀ
an,an≥0)和 bn(b0、b1、b2、b3、
…ꢀ
bn,bn≥0)以及 a01和a02 、b01和b02应不同时为0。
54.反应器中段2每相邻两组并联湍动悬浮微反应床21之间,即第n
‑
1组并联湍动悬浮微反应床21复合式下导流板212的n1(n1≥1)个下导流板单体x(212x n1)和 n2(n2≥1)个下导流板单体y(212yn2)与相对应的第n组并联湍动悬浮微反应床21复合式上导流板211的
n1(n1≥1)个上导流板单体x(211x n1)和 n2(n2≥1)个上导流板单体y(211yn2)相对应位置竖直方向两床之间的间距hn(下标n=n1+n2,h1、h2、 h3 、h4、
ꢀ…ꢀ
hn),与相对应位置的缺口或环隙an(a1、a2、a3、
…ꢀ
an,an≥1)和 bn(b1、b2、b3、
…ꢀ
bn,bn≥1)以及 a01和a02 、b01和b02应不同时为0。
55.反应器中段2的每一组并联湍动微反应床21复合式上导流板211的n(n≥2,且n=n1+n2)个上导流板单体x(211xn1)和上导流板单体y(211yn2)也可以分别由若干块单板呈阶梯状布置组成,同理,复合式下导流板212的n(n≥2,且n=n1+n2)个下导流板单体x(212xn1)和下导流板单体y(212yn2)也可以分别由若干块单板呈阶梯状布置组成。
56.反应器中段2的每一组并联湍动微反应床21复合式上导流板211的n(n≥2,且n=n1+n2)个上导流板单体x(211xn1)和上导流板单体y(211yn2)与复合式下导流板212的n(n≥2,且n=n1+n2)个下导流板单体x(212xn1)和下导流板单体y(212yn2),其上表面形状是以有利于物料流动的结构,可以是平直的,也可以是波纹状,也可以是开设导流槽结构,也可以是这几种结构的不同组合。
57.反应器中段2的每一组并联湍动微反应床21复合式上导流板211的n(n≥2,且n=n1+n2)个上导流板单体x(211xn1)和上导流板单体y(211yn2)与复合式下导流板212的n(n≥2,且n=n1+n2)个下导流板单体x(212xn1)和下导流板单体y(212yn2)上可以开设 n(n≥1)个通气孔,总开孔数量和总开孔面积根据有机固废物料粒径分布、处理规模和多级串联的并联湍动微反应床的气相流速和压降确定;也可以不开设通气孔(n=0)。
58.反应器中段设置有n(n≥0)个二次热载体加入口,二次热载体加入口设置在任何相邻两组并联湍动微反应床21之间位置,根据有机固废物料组成、处理规模、气态有机质热解提馏产物出口温度和热解固态残渣出口33组成确定其数量为0个(不设置)或n个。
59.反应器下段3的底部或侧面设置有高温热载体进口31、热解固态残渣出口33和人孔13,数量可以分别是n(n≥1)个设置在不同位置。
60.反应器下段设置有热载体分布器32,用于使热载体均匀分配进入反应器中段2,其形状与反应器下段3的截面形状相匹配。热载体分布器32上表面与反应器壳体4中心线的夹角γ为0
‑
90
°
之间的任一角度,并开设有n(n≥1)个气体分配孔。
61.具体地,参见图1,反应器壳体4为立式圆筒形结构,由反应器上段1、中段2和下段3组成并同轴同直径且相互连通,反应器壳体4内直径为3600mm,耐火隔热衬里5内直径3100mm,反应器上段1直筒段高度2000mm,中段2高度28800mm,下段3高度3000mm。热解提馏反应压力为1.0mpag,反应温度区间为350
‑
900℃;高温热载体为n2气,其进入反应器的压力为1.20mpag,温度为900℃。
62.反应器上段1的顶部设置5个有机固废物料进口11,其位置在顶部中心位置1个,在距离反应器壳体4中心线为1025mm的中心圆上对称设置4个;顶部设置4个气态有机质热解提馏产物和热载体混合物出口12,其位置在距离反应器壳体4中心线为780mm的中心圆上对称设置;侧面距离第一组并联湍动微反应床21最上层缺口平面800mm位置对称设置2个人孔13。
63.反应器中段2有机固废物料热解提馏段设置24组串联的并联湍动微反应床21,每一组并联湍动悬浮微反应床21由1组复合式上导流板211和1组复合式下导流板212构成,且以反应器壳体4中心线为中心轴对称布置;每一组复合式上导流板211由4个上导流板单体x
(211x1、211x2、211x3、211x4)和2个上导流板单体y(211y1、211y2)两种圆锥形结构形状对称依次交错并联组合构成,其中,211x1和211x2为以反应器壳体4中心线为中心轴对称的同一倒圆锥并位于中心层,其上均布开设150个直径为5mm的通气孔,211y1和211y2为以反应器壳体4中心线为中心轴对称的同一正圆锥并位于中间层,其上均布开设500个直径为5mm的通气孔,211x3和211x4为以反应器壳体4中心线为中心轴对称的同一正圆锥并位于最外层,其上均布开设800个直径为5mm的通气孔,a0=a3=a4=400mm,a1=a2=40mm,a01=a02=10mm,αx1=αx2=αx3 =αx4 = 45
°
,αy1 =αy2=135
°
;每一组复合式下导流板212由4个下导流板单体y(212x1、212x2、212x3、212x4)和2个下导流板单体y(212y1、212y2)两种圆锥形结构形状对称依次交错并联组合构成,其中,212x1和212x2为以反应器壳体4中心线为中心轴对称的同一正圆锥并位于中心层,其上均布开设150个直径为5mm的通气孔,212y1和212y2为以反应器壳体4中心线为中心轴对称的同一倒圆锥并位于中间层,其上均布开设500个直径为5mm的通气孔,212x3和212x4为以反应器壳体4中心线为中心轴对称的同一正圆锥并位于最外层,其上均布开设800个直径为5mm的通气孔,b0=b3=b4=40mm, b1=b2=400mm, b01=b02=100mm,βx1=βx2=βx3 =βx4 = 45
°
,βy1 =βy2=135
°
;每一组并联湍动悬浮微反应床21的复合式上导流板211与相对应的复合式下导流板212之间的竖直床间距h1=h2=h3=h5=h4=h6 =400mm;相邻两组串联的并联湍动微反应床21之间的竖直床间距h1=h2=h3=h4=400mm,h5=h6=390mm;设置3层12个二次热载体加入口22,其位置在从上往下的第6组、第12组、第18组并联湍动微反应床21中间位置且每层对称均匀设置4个,相邻两层二次热载体加入口22相互错开90
°
。
64.反应器下段3设置1个热解固态残渣出口33,其位于中心位置;设置4个高温热载体进口31,其位置对称均布设置在侧面;热载体分布器32为圆锥形结构,与反应器壳体4中心线的夹角γ为60
°
,并开设9000个直径为10mm的气体分配孔;在侧面位置对称设置2个人孔13。
65.反应器耐火隔热衬里5由耐火隔热浇注料和耐火隔热砖两层组合构成,总厚度300mm,耐火隔热浇注料采用高致密隔热浇注料,设置在反应器壳体4内侧,厚度为224mm,耐火隔热砖耐火隔热砖采用高铬砖(cr2o3含量大于86.0%,设置在反应器炉膛内侧,厚度76mm。
66.在反应器的上段1和中段2之间设置分段法兰连接结构,以便于24组串联的并联湍动微反应床21的安装。
67.本技术实施例1的实施原理为:高温热载体自反应器下段3的热载体进口31进入反应器下段3,通过热载体分布器32分配均匀后从反应器中段2底部进入n级串联的并联湍动微反应床21的最底部,自下而上流动为并联湍动微反应床进行的热解提馏反应提供热量;
68.同时,含有机质的固体废弃物质(有机固废)自反应器上段1的有机固废物料进口11进入反应器上段1内靠重力下行,与上行的气态热解提馏产物与热载体的混合物直接接触换热,并经过吸热预热下行流入反应器中段2的顶部。
69.经反应器上段1预热的有机固废自上而下流动依次进入n级串联的并联湍动微反应床21进行热解提馏反应,在每一组并联湍动悬浮微反应床21内部,复合式上导流板211的n1个上导流板单体x(211x n1)和n2个上导流板单体y(211yn2)分别与复合式下导流板212所相对应位置的n1个下导流板单体x(212x n1)和n2个下导流板单体y(212yn2)之间区域构
成了若干个截面主体形状为菱形或椭圆形的相并联的主反应区;最外侧的上导流板单体x(212x n1 及/或212x n1
‑
1)和最外侧的下导流板单体y(212x n2及/或212x n2
‑
1)与反应器耐火隔热衬里5内壁面之间区域构成2个截面主体形状为半菱形或半椭圆形的副反应区,并与主反应区相并联;同时,在每相邻两组串联的并联湍动悬浮微反应床21之间,即上一组并联湍动悬浮微反应床21复合式下导流板212的n1个下导流板单体x(212x n1)和n2个下导流板单体y(212yn2)分别与下一组(第n
‑
1组)并联湍动悬浮微反应床21复合式上导流板211所相对应位置的n1个上导流板单体x(211x n1)和n2个上导流板单体y(211yn2)之间区域也构成了若干个截面主体形状为菱形或椭圆形的相并联的主反应区;上一组并联湍动悬浮微反应床21最外侧的下导流板单体y(212x n2及/或212x n2
‑
1)和下一组最外侧的上导流板单体x(212x n1 及/或212x n1
‑
1)与反应器耐火隔热衬里5内壁面之间区域构成2个截面主体形状为半菱形或半椭圆形的副反应区,并与主反应区相并联。下行的经预热的有机固废与上行的高温热载体和气态热解提馏产物两者的混合物在反应区内部呈现气固两相湍动悬浮的充分混合状态直接接触换热,有机固废吸收高温热载体携带的热量发生有机质的裂解反应和提馏反应产生低分子量的气态烃类物质及/或气相油品,并与梯级放热降温的高温热载体组成混合物自下而上流动,在反应器中段2完成热解提馏的有机固废固体残渣物料下行流进反应器下段3。
70.流进反应器下段3的有机固废固体残渣物料经热载体分布器32汇集形成一定厚度的物料移动态床层,与经热载体分布器32分配均匀后上行的高温热载体直接接触换热并继续进行裂解反应和提馏反应,产生的气态反应产物随高温热载体一起上行,最终热解固态残留物(热解残渣)自热解固态残渣出口33流出反应器,进入后续残渣冷却与余热回收工序。
71.根据气态有机质热解提馏产物出口温度和热解固态残渣出口33组成分析,如发现热解固态残渣中残余有机质含量超标则说明有机固废热解反应进行不完全,或气态有机质热解提馏产物出口温度偏低时,则可以从反应器下段3的热载体进口301加大热载体的流量(当没有设置二次热载体加入口24时),也可以通过设置在反应器中段2的n(自然数n≥1)个二次热载体加入口24加入一定流量的热载体,也可以同时从反应器下段3的热载体进口31加大热载体的流量及从n个二次热载体加入口24的其中一个或多个同时加入一定流量的热载体。
72.气态烃类和气相油品与梯级放热降温的热载体组成的混合物最后经反应器上段1的气态有机质热解提馏产物和热载体混合物出口12流出反应器,进入后续热解提馏产物余热回收利用与有机质分离回收工序。
73.实施例2
74.参见图2,一种热载体直接给热式多级串并联湍动床热解提馏反应器,参见图2,包括立式方形结构的反应器壳体4,由反应器上段1、中段2和下段3组成并相互连通,其截面形状为长方形等截面积,反应器壳体4截面长x宽为4000x3500mm,反应器上段1的反应器壳体4直段高度2000mm,反应器中段2的反应器壳体4直段高度20840mm,反应器下段3的反应器壳体4直段高度4000mm。热解提馏反应压力区间为
‑
0.05 mpag(顶部)
‑ꢀ
+0.1 mpag(底部)mpag,反应温度区间为300℃(顶部)
‑ꢀ
700℃(底部);高温热载体为过热蒸汽,其进入反应器的压力为0.20mpag,温度为700℃。
75.反应器上段1顶部的宽度方向中心线两侧各对称设置2个有机固废物料进口11,分别距离宽度方向中心线两侧为500mm和1500mm;顶部中心位置设置1个、沿长度方向距离反应器中心线1000mm的两侧各对称设置1个共3个气态有机质热解提馏产物和热载体混合物出口12;长度方向两侧面的中心位置各对称设置1个人孔13。
76.反应器中段2有机固废物料热解提馏段设置12组串联的并联湍动微反应床21,每一组并联湍动悬浮微反应床21由1组复合式上导流板211和1组复合式下导流板212构成,且以反应器壳体4中心线为中心轴对称布置;每一组复合式上导流板211由4个上导流板单体x(211x1、211x2、211x3、211x4)和4个上导流板单体y(211y1、211y2、211y3、211y4)两种长方形结构形状对称依次交错并联组合构成,其中,211x1和211x2为以反应器壳体4中心线为中心轴对称位于中心层,其上均布开设1100个直径为5mm的通气孔,211y1和211y2、211x3和211x4分别以反应器壳体4中心线为中心轴对称位于中间层,其上均布开设850个直径为5mm的通气孔,211y3和211y4为以反应器壳体4中心线为中心轴对称位于最外层,其上均布开设500个直径为5mm的通气孔,a0=a3=a4=40mm,a1=a2=a5=a6=400mm,a01=a02=10mm,αx1=αx2=αx3 =αx4 =150
°
,αy1 =αy2=αy3 =αy4 =30
°
;每一组复合式下导流板212由4个下导流板单体y(212x1、212x2、212x3、212x4)和4个下导流板单体y(212y1、212y2、212y3、212y4)两种长方形结构形状对称依次交错并联组合构成,其中,212x1和212x2为以反应器壳体4中心线为中心轴对称位于中心层,其上均布开设1100个直径为5mm的通气孔,212y1和212y2、212x3和212x4分别以反应器壳体4中心线为中心轴对称位于中间层,其上均布开设850个直径为5mm的通气孔,212y3和212y4为以反应器壳体4中心线为中心轴对称位于最外层,其上均布开设500个直径为5mm的通气孔,b0=b3=b4=400mm,b1=b2=b5=b6=40mm, b01=b02=200mm,βx1=βx2=βx3 =βx4 = 30
°
,βy1 =βy2=βy3 =βy4 =150
°
;每一组并联湍动悬浮微反应床21的复合式上导流板211与相对应的复合式下导流板212之间的竖直床间距h1=h2=h3=h5=h4=h6=h7=h8=400mm;相邻两组串联的并联湍动微反应床21之间的竖直床间距h1=h2=h3=h4=h5=h6=400mm,h7=h8=382mm;设置2层16个二次热载体加入口22,其位置在从上往下的第4组和第8组并联湍动微反应床21中间位置且每层沿长度方向两侧中心线位置各对称设置1个、每层沿宽度方向两侧在中心线位置对称设置1个、每层沿宽度方向两侧距离中心线1000mm位置各对称设置2个。
77.反应器下段3设置3个热解固态残渣出口33,1个位于中心位置、2个位于长度方向两侧距离中心线各1000mm对称位置;设置6个高温热载体进口31,2个对称位于宽度方向两侧的中心线位置、4个对称位于长度方向两侧各500mm的中心线位置;热载体分布器32为单侧面长方形结构且沿长度方向中心线对称设置,与反应器壳体4中心线的夹角γ为30
°
,并开设12000个直径为10mm的气体分配孔;在侧面位置对称设置2个人孔13。
78.反应器耐火隔热衬里5由里外两层耐火隔热浇注料构成,外层采用高致密耐磨浇注料,设置在反应器炉膛内侧,厚度50mm;里层采用高致密隔热浇注料,设置在反应器壳体4侧,反应器上段1厚度为115mm,反应器中段2厚度为220mm,反应器下段3厚度为250mm。
79.在反应器的中段2和下段3之间设置分段法兰连接结构,以便于24组串联的并联湍动微反应床21和热载体分布器32的安装。
80.实施例3
81.本实施例与实施例1的不同之处在于,并联湍动微反应床的结构不同。具体地,参
照图3和图4,反应器中段2有机固废物料热解提馏段设置24组串联的并联湍动微反应床21。每一组并联湍动悬浮微反应床21由1组复合式上导流板211和1组复合式下导流板212构成,且以反应器壳体4中心线为中心轴对称布置;每一组复合式上导流板211由4个上导流板单体x(211x1、211x2、211x3、211x4)和2个上导流板单体y(211y1、211y2)两种长方形(与反应器耐火隔热衬里5内壁部分为圆弧形)结构形状对称依次交错并联组合构成,其中,211x1和211x2为以反应器壳体4中心线为中心轴对称位于中心层,其上均布开设850个直径为5mm的通气孔,211y1和211y2为以反应器壳体4中心线为中心轴对称位于中间层,其上均布开设500个直径为5mm的通气孔,211x3和211x4为以反应器壳体4中心线为中心轴对称位于最外层,其上均布开设200个直径为5mm的通气孔,a0=a3=a4=400mm,a1=a2=40mm,环隙a01=a02=10mm,αx1=αx2=αx3 =αx4 = 45
°
,αy1 =αy2=135
°
;每一组复合式下导流板212由4个下导流板单体y(212x1、212x2、212x3、212x4)和2个下导流板单体y(212y1、212y2)两种长方形(与反应器耐火隔热衬里5内壁部分为圆弧形)结构形状对称依次交错并联组合构成,其中,212x1和212x2为以反应器壳体4中心线为中心轴对称位于中心层,其上均布开设850个直径为5mm的通气孔,212y1和212y2为以反应器壳体4中心线为中心轴对称位于中间层,其上均布开设500个直径为5mm的通气孔,212x3和212x4为以反应器壳体4中心线为中心轴对称位于最外层,其上均布开设200个直径为5mm的通气孔,b0=b3=b4=40mm, b1=b2=400mm, 环隙b01=b02=100mm,βx1=βx2=βx3 =βx4 = 45
°
,βy1 =βy2=135
°
;每一组并联湍动悬浮微反应床21的复合式上导流板211与相对应的复合式下导流板212之间的竖直床间距h1=h2=h3=h5=h4=h6 =400mm;相邻两组串联的并联湍动微反应床21之间的竖直床间距h1=h2=h3=h4=400mm,h5=h6=390mm;设置3层每层6个共18个二次热载体加入口22,其位置在从上往下的第6组与第7组、第12组与第13组、第17组与第13组并联湍动微反应床21之间的中间位置、且每层二次热载体加入口22与复合式上导流板211长度方向的中心线和距离中心线1000mm两侧中间位置各对称设置3个共6个。
82.实施例4
83.本实施例与实施例1的不同之处在于,并联湍动微反应床的结构不同。具体地,参照图5和图6,反应器中段2的每一组并联湍动微反应床21可以由 m(m≥1)个并联湍动微反应床单体210相互并联组成,且每个并联湍动微反应床单体210由上导流板单体x(211x)和下导流板单体x(212x)构成,如图4所示,上导流板单体x(211x)和下导流板单体x(212x)的立体形状为圆锥(圆台)形或多面体(多棱台)形,其截面形状为圆形或椭圆形或多边形或几种形状的组合。上导流板单体x(211x)的上表面与反应器壳体4中心线的夹角α为0
‑
180
°
之间的任一角度,下导流板单体x(212x)的上表面与反应器壳体4中心线的夹角β为0
‑
180
°
之间的任一角度,且当α为钝角(90
°
≤α< 180
°
)时β为锐角(0
°
< β ≤ 90
°
)、当α为锐角(0
°
< α ≤ 90
°
)时β为钝角(90
°
≤β< 180
°
);上导流板单体x(211x)的顶部(90
°
≤α< 180
°
)或底部(0
°
< α ≤ 90
°
)中心区域开设有直径为a0(a0≥0)的缺口,对应地,下导流板单体x(212x)的底部(0
°
< β ≤ 90
°
)或顶部(90
°
≤β< 180
°
)中心区域开设有直径为b0(b0≥0)的缺口;上导流板单体x(211x)与下导流板单体x(212x)相对应位置竖直方向之间的床内间距h1与a0及b0均不同时为0;每一组并联湍动微反应床21的 m个并联湍动微反应床单体210相互并联,除不与反应器耐火隔热衬里5内壁相邻近的中间区域的每个并联湍动微反应床单体210与周围相邻的m1个并联湍动微反应床单体210之间的横向间距am1(a1、a2、a3、 a4、
…ꢀ
am1,
为相邻两个上导流板单体x(211x)之间的间距)和bm1(b1、b2、b3、 b4、
…ꢀ
bm1,为相邻两个下导流板单体x(212x)之间的间距)、以及m2个并联湍动微反应床单体210与相邻反应器耐火隔热衬里5内壁之间的横向间距a0m2( a01、a02、a03、 a04、
…ꢀ
a0m2,为上导流板单体x(211x)与反应器耐火隔热衬里5内壁之间的间距或环隙)和 b0m2(b01、b02、b03、 b04、
…ꢀ
b0m2,为下导流板单体x(212x)与反应器耐火隔热衬里5内壁之间的间距或环隙)应不同时为0;相互并联的 m个并联湍动微反应床单体210的排列方式可以是正方形排列,也可以是三角形排列,也可以是同心圆排列,也可以是多种形状组合排列,并与反应器壳体4及其耐火隔热衬里5的截面形状相匹配;特别地,可以由m个不同结构尺寸的并联湍动微反应床单体210相互并联构成一组并联湍动微反应床21,其m个并联湍动微反应床单体210的每一组上导流板单体x(211x)与下导流板单体x(212x)竖直方向之间的床内间距hm(h1、h2、 h3 、h4、
ꢀ…ꢀ
hm)与其相对应位置的a0及b0均不同时为0,同理, n(n≥2)组串联构成的并联湍动悬浮微反应床21的每相邻两组也可以是m个不同结构尺寸的并联湍动微反应床单体210相互并联构成;每相邻两组串联的并联湍动悬浮微反应床21竖直方向两床之间的间距,即第n
‑
1组并联湍动悬浮微反应床21m个并联湍动微反应床单体210的下导流板单体x(212x)与相对应的第n组并联湍动悬浮微反应床21m个并联湍动微反应床单体210的上导流板单体x(211x)相对应位置竖直方向之间的间距hm(h1、h2、 h3 、h4、
ꢀ…ꢀ
hm),与相对应位置的a0和 b0以及 a0m2 、b0m2应不同时为0;上导流板单体x(211x)和下导流板单体x(212x)其上表面形状是以有利于物料流动的结构,可以是平直的,也可以是波纹状,也可以是开设导流槽结构,也可以是这几种结构的不同组合;上导流板单体x(211x)和下导流板单体x(212x)其上可以开设 n(n≥1)个通气孔,总开孔数量和总开孔面积根据有机固废物料粒径分布、处理规模和多级串联的并联湍动微反应床的气相流速和压降确定;也可以不开设通气孔(n=0)。
84.具体地,反应器中段2有机固废物料热解提馏段设置12组并联湍动微反应床21,每一组湍动微反应床21由二十三个相同结构尺寸的湍动微反应床单体210相互并联组成且以正三角形排列,每个湍动微反应床单体210由正圆锥或圆台形的上导流板单体x(211x)和倒圆锥(圆台)形的下导流板单体x(212x)构成,其上均布开设75个直径为5mm的通气孔。上导流板单体x(211x)的上表面与反应器壳体4中心线的夹角α为150
°
,下导流板单体x(212x)的上表面与反应器壳体4中心线的夹角β为30
°
,上导流板单体x(211x)顶部中心区域开设直径为a0=40mm的圆形开口,下导流板单体x(212x)底部中心区域开设直径为b0=400mm的圆形开口,上导流板单体x(211x)与下导流板单体x(212x)相对应位置竖直方向之间的床内间距h1=400mm。除不与反应器耐火隔热衬里5内壁相邻近的中间区域的每个湍动微反应床单体210的上导流板单体x(211x)与周围相邻的6个湍动微反应床单体210上导流板单体x(211x)之间的横向间距均相等a1=a2=a3=a4=a5=a6=40mm,相邻两个下导流板单体x(212x)之间的横向间距均相等 b1=b2=b3=b4=b5=b6=40mm。与反应器耐火隔热衬里5内壁相邻的16个湍动微反应床单体210其上导流板单体x(211x)与反应器耐火隔热衬里5内壁之间的横向间距 a0m2均相等a01=a02=a03=a04=a04=
ꢀ…ꢀ
=a015=a016=200mm,下导流板单体x(212x)与反应器耐火隔热衬里5内壁之间的横向间距均相等b01=b02=b03=b04 =
ꢀ…ꢀ
=b015=b016=5mm。每相邻两组串联的湍动悬浮微反应床21竖直方向两床之间的间距hm均相等 h1=h2=h3=h4 =
ꢀ…ꢀ
=h22=h23=400mm。
85.以上均为本技术的较佳实施例,并非依此限制本技术的保护范围,故:凡依本技术
的结构、形状、原理所做的等效变化,均应涵盖于本技术的保护范围之内。