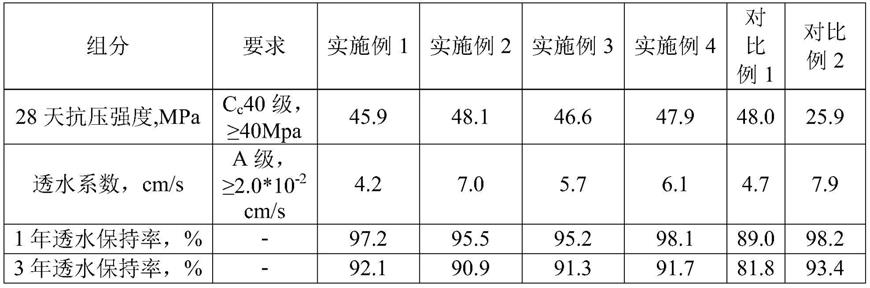
1.本发明涉及建材制品领域,尤其涉及一种复合透水砖及其制备方法。
背景技术:
2.据统计,我国每年产生钢渣近1.5亿吨,综合利用率却不足40%,建筑垃圾每年产生近30亿吨,大量的钢渣、建筑垃圾亟待处理利用。随着国家环保政策的日趋收紧,以及碳达峰、碳中和战略目标方案的实施,钢渣、建筑垃圾、废旧陶瓷等固废的清洁化处理及资源化利用显得尤为紧迫。海绵城市建设是近年来国家大力发展基础设施绿色工程之一,透水砖制品铺装是海绵城市建设的重要一环,近五年来,国内形成了钢渣透水砖、陶瓷透水砖、砂基透水砖等主流技术,并分别在各自市场上得到应用。但现有技术仍存在以下几个问题:
3.钢渣、再生骨料、陶瓷透水砖单一化利用各有利弊。1)钢渣“刚性”太强。单独钢渣透水混凝土强度高,但施工性能不佳,碾压时出现碎裂、空鼓、粘粒等问题。2)再生骨料“柔性”有余、“刚性”不足。单独再生骨料透水混凝土强度低,28d抗压强度小于10mpa,不具有使用效果。3)钢渣、再生骨料材料自身不具备快速渗水性,因此需要较大、较多的表面孔隙实现透水功能,路面的垃圾、颗粒物等容易通过表面孔隙进行砖本体,日积月累,造成砖的透水性衰减甚至堵塞。4)陶瓷砖美观大方、保持低孔隙率的条件下透水性好,但强度较低且需要烧制,能耗较高。
4.现有技术中公开了陶瓷作为集料制备透水砖,如cn106045472b公开了一种复合材料生态陶瓷透水砖的制备方法,该方法以废瓷粒为面料的原料,但需要经高温烧制,能耗和成本都较高。
技术实现要素:
5.鉴于以上所述现有技术的缺点,本发明的目的在于提供一种复合透水砖及其制备方法,用于解决现有技术中存在的问题。
6.为实现上述目的及其他相关目的,本发明是通过以下技术方案获得的。
7.一种复合透水砖,所述复合透水砖包括面层和底层,所述复合透水砖包括面层和底层,
8.所述面层原料包括废陶瓷粒和粘结剂,所述粘结剂和废陶瓷的质量比为(2.5-3.5):100;
9.所述底层原料包括钢渣、再生骨料、水泥和水,所述钢渣、再生骨料、水泥和水的质量比为(120-150):(35-50):(38-40):(12-13)。
10.本技术中的粘结剂和废陶瓷比例不能太高也不能太低,如果粘结剂的比例偏高就会导致透水率低甚至不透水;如果粘结剂的比例偏低,会导致复合透水砖的强度偏低。
11.本技术中的钢渣和再生骨料之间的比例超过本技术的范围,容易使得透水砖的强度偏低,脆性增高,容易破裂;水泥用量超过本技术的范围将会造成透水砖的孔隙率偏低,从而透水率低;用水量过高会导致透水砖的强度低、用水量过低则无法保证透水砖成型。
12.优选地,所述粘结剂和废陶瓷的质量比可为(2.5-3.0):100,也可以为(2.7-3.2):100,也可以为(3.0-3.5):100。
13.优选地,所述钢渣、再生骨料、水泥和水的质量比可为(120-130):(35-45):(38-40):(12-13),也可以为(125-150):(40-50):(38-40):(12-13)。具体地,所述钢渣、再生骨料、水泥和水的质量比135:42:39:12.5。
14.优选地,所述废陶瓷的粒径为0.5-2mm。在本技术的废陶瓷的粒径范围内形成的透水砖不仅外观美观,而且面层的空隙率小,不利于污染物进入至底层中。
15.优选地,以废陶瓷的总质量为基准计,所述废陶瓷的含水率≤0.2%。本技术中含水率检测方法参照《gb/t 14684-2011建设用砂》进行。
16.优选地,以废陶瓷的总质量为基准计,所述废陶瓷的含泥量≤0.2%。本技术中含泥量检测方法参照《gb/t 14684-2011建设用砂》进行。
17.优选地,所述废陶瓷由淄博嘉彩工贸有限公司生产。
18.优选地,所述粘结剂为胶粘石专用粘结剂。具体地,所述胶粘石专用粘结剂由上海岚石新材料科技有限公司生产。更优选地,所述胶粘石专用粘结剂为ab胶,所述a胶为本胶,所述b胶为硬化剂,所述a胶和b胶的质量比为(2-3):1。具体地,所述a胶和b胶的质量比为2.5:1。
19.优选地,所述水泥为硅酸盐水泥。
20.更优选地,所述水泥为太仓海螺水泥有限公司的po 42.5水泥。
21.优选地,所述钢渣为电炉滚筒渣。具体地,所述钢渣由宝武集团宝钢股份公司炼钢产生的电炉滚筒渣,经破碎、磁选、筛分后,获得。
22.优选地,以钢渣的总质量为基准计,所述钢渣中的游离钙f.ca0≤1.4%。本技术中f-cao含量的检测方法参考《yb/t 140~2009钢渣化学分析方法》进行。
23.优选地,所述钢渣的粒径为3-5mm。
24.优选地,所述再生骨料为建筑物拆除后经破碎的颗粒料。
25.优选地,所述再生骨料的粒径为5-20mm。
26.优选地,以再生骨料的总质量为基准计,所述再生骨料的泥块含量≤0.5%。本技术中泥块含量的检测方法《gb/t 14684-2011建设用砂》进行检测。
27.本发明的目的之二在于提供上述所述的复合透水砖的制备方法,包括以下步骤:
28.混合所述面层中的原料组分以得到面料;
29.混合所述底层中的原料组分以得到底料;
30.将所述底料进行第一次成型,然后将面料铺设于成型后的底料上,进行第二次成型,养护,得到所述复合透水砖。
31.优选地,所述面层中的原料组分混合包括将所述废陶瓷和粘结剂搅拌混合。
32.更优选地,所述面层中原料组分的搅拌时间为180-300秒。
33.优选地,所述底层中的原料组分混合包括先将钢渣、再生骨料、水泥搅拌混合,最后加水搅拌混合。
34.更优选地,所述底层中的原料组分的搅拌时间为70-80秒。
35.优选地,所述第一次成型方式为振压成型,压力为150-220kn。
36.更优选地,所述振压成型的压力为200kn。
37.优选地,所述第二次成型方式为静压成型,压力为80-1000kn。
38.优选地,所述静压成型的压力为94kn。
39.优选地,所述养护包括养护窑养护和自然养护。
40.更优选地,所述养护窑养护的温度为20-25℃。具体地,所述养护窑养护的温度为22℃。
41.更优选地,所述养护窑养护的湿度为60%-80%。具体地,所述养护窑养护的湿度为70%。
42.更优选地,所述养护窑养护的时间为20-24h。具体地,所述养护窑养护的时间为22h。
43.本发明通过对原料如钢渣、再生骨料、废陶瓷和粘结剂进行筛选和控制,从而使得采用这些原料制备获得的复合透水砖,不仅具有陶瓷的美观性和防堵性,还避免了现有技术中陶瓷砖需要高温烧制的环节,同时本发明的复合透水砖还具有高强度和高透水性。
44.本发明中的面层以废陶瓷粒和粘结剂为原料,利用废陶瓷颗粒本身具有高渗水性,采用粘结剂减小废陶瓷颗粒之间的空隙,在保证透水性能的同时,能大幅减少环境污染物进入基层的透水系统中,且能保持陶瓷的美观性;底层采用小颗粒钢渣和大颗粒再生骨料,二者互配增大了底层的空隙率,增加底层的透水性能;面层和底层形成的复合透水砖,在保证面层的整体性、美观性,同时又能确保复合透水砖的透水性和强度,使得复合透水砖的3年透水保持率在90%以上。
45.与现有技术相比,本发明具有以下有益效果:
46.1)本发明的复合透水砖通过选择特定粒径的废陶瓷和粘结剂,能减少表面空隙率,减少路面的垃圾、颗粒物等污染物通过表面孔隙进行砖本体而造成透水功能损失。
47.2)本发明的复合透水砖以废陶瓷、钢渣、建筑物拆除后的废弃物为原料,利用各自的优势,制备出强度高、透水性好、成本低的物美价廉的透水砖,能满足海绵城市铺装产品。
48.3)本发明的复合透水砖能最大程度上利用固废,降低生产成本,实现资源再利用。
附图说明
49.图1显示为本发明的复合透水砖的结构示意图。
50.图2显示为本发明的制备方法的流程图。
具体实施方式
51.下面结合具体实施例进一步阐述本发明,应理解,这些实施例仅用于说明本发明而不用于限制本发明的保护范围。
52.以下通过特定的具体实例说明本发明的实施方式,本领域技术人员可由本说明书所揭露的内容轻易地了解本发明的其他优点与功效。本发明还可以通过另外不同的具体实施方式加以实施或应用,本说明书中的各项细节也可以基于不同观点与应用,在没有背离本发明的精神下进行各种修饰或改变。
53.如图1所示,为本发明的复合透水砖的结构示意图,复合透水砖包括面层和底层,面层设于底层的上方,面层的厚度为1-2cm,底层的厚度为4-5cm。
54.以下通过具体的实施例来进一步阐述所述复合透水砖的制备方法。
55.本发明具体实施例中钢渣由宝武集团宝钢股份有限公司生产的转炉钢渣,以钢渣的总质量为基准计,钢渣中游离钙f.cao含量为0.6%,粒径为3-5mm;水泥为太仓海螺水泥有限公司的po 42.5水泥;粘结剂为上海岚石新材料科技有限公司的胶粘石专用粘结剂,胶粘石专用粘结剂包括a胶和b胶,a胶和b胶的质量比为2.5:1;再生骨料为建筑物拆除后经破碎的颗粒料,再生骨料的粒径为5-12mm,以再生骨料的总质量为基准计,所述再生骨料的泥块含量为0.3%;废陶瓷粒由淄博嘉彩工贸有限公司生产,废陶瓷粒的粒径为0.5-2.0mm,以废陶瓷的总质量为基准计,废陶瓷粒的含水率为0.1%,废陶瓷粒的含泥量为0.1%。
56.本技术的下述实施例中,振压成型采用的机器为福建泉工股份有限公司的qt10全自动砌块成型机;静压成型采用的机器为福建泉工股份有限公司的转盘式静压机hp-1200t。
57.实施例1
58.面料:粘结剂:3.5kg,废陶瓷:100kg。
59.底料:42.5级硅酸盐水泥:380;钢渣:1200kg;再生骨料:500kg。
60.按照工艺流程,将底料搅拌70s后放在模具里,在激振力为200kn下振压成型;面层搅拌250s后,摊在振压成型的底料上,静压成型,静压成型时的压力94kn。将压制成型好的制品送入养护窑进行养护(温度20℃,湿度60%),养护20h后,进行抗压强度、透水系数和透水保持率测定。
61.实施例2
62.面料:粘结剂:2.5kg,废陶瓷:100kg。
63.底料:42.5级硅酸盐水泥:400;钢渣:1500kg;再生骨料:500kg。
64.按照工艺流程,将底料搅拌70s后放在模具里,在激振力为200kn下振压成型;面层搅拌250s后,摊在振压成型的底料上,静压成型,静压成型时的压力94kn。将压制成型好的制品送入养护系统进行养护(温度25℃,湿度80%),养护20h后,进行抗压强度、透水系数和透水保持率测定。
65.实施例3
66.面料:粘结剂:3kg,废陶瓷:100kg。
67.底料:42.5级硅酸盐水泥:390;钢渣:1300kg;再生骨料:450kg。
68.按照工艺流程,将底料搅拌70s后放在模具里,在激振力为200kn下振压成型;面层搅拌250s后,摊在振压成型的底料上,静压成型,静压成型时的压力94kn。将压制成型好的制品送入养护系统进行养护(温度20℃,湿度75%),养护24h后,进行抗压强度、透水系数和透水保持率测定。
69.实施例4
70.面料:粘结剂:2.8kg,废陶瓷:100kg。
71.底料:42.5级硅酸盐水泥:390;钢渣:1350kg;再生骨料:420kg。
72.按照工艺流程,将底料搅拌70s后放在模具里,在激振力为200kn下振压成型;面层搅拌250s后,摊在振压成型的底料上,静压成型,静压成型时的压力94kn。将压制成型好的制品送入养护系统进行养护(温度22℃,湿度75%),养护22h后,进行抗压强度、透水系数和透水保持率测定。
73.对比例1
74.面料:42.5级硅酸盐水泥:420kg;钢渣:2050kg;水:140kg。
75.底料:42.5级硅酸盐水泥:390kg;钢渣:1350kg,再生骨料420kg。
76.制备方法和养护条件同实施例4,然后进行抗压强度、透水系数和透水保持率测定。
77.对比例2
78.面料:粘结剂:2.8kg;废陶瓷:100kg。
79.底料:粘结剂:2.8kg;废陶瓷:100kg。
80.制备方法和养护条件同实施例4,然后进行抗压强度、透水系数和透水保持率测定。
81.参照《gb/t 25993-2010透水路面砖和透水路面板》对实施例1至4以及对比例1至2得到的样品检测其透水系数。
82.按照下式计算1年透水保持率和3年透水保持率:
83.1年透水保持率=工程竣工验收满一年之日透水系数/工程竣工验收之日透水系数100%;
84.3年透水保持率=工程竣工验收满三年之日透水系数/工程竣工验收之日透水系数*100%;
85.参照《gb 28635-2012混凝土路面砖》对实施例1至4以及对比例1至2得到的样品检测其28天抗压强度。
86.实施例1-4及对比例1和2的检测结果如表1所示:
87.表1实施例
[0088][0089]
从表1可知,本技术的透水砖的28d平均抗压强度在45mpa以上,满足国家标准要求中对混凝土路面砖的要求;透水砖的透水系数高于国家标准要求规定的2.0*10-2
cm/s。与全陶瓷透水砖即对比例2相比,本技术的复合透水砖28天抗压强度增加70%以上;相比全钢渣透水砖即对比例1相比,本技术的复合透水砖的1年、3年透水保持率有所增长,1年透水保持率达到95%以上,3年透水保持率达到90%以上;对比例2的透水保持率高,但是其强度差,不符合混凝土路面砖的标准要求。
[0090]
原有工艺配比(即对比例1)的情况下,透水砖很难同时达到强度、短期透水率以及长期透水率的要求,且成本较高。本技术将废陶瓷粒作为透水砖面层骨料、粘结剂作为粘结材料;钢渣和再生骨料作为透水砖底层骨料、水泥作为胶凝材料制备复合固废透水砖制品,兼顾透水砖的防堵性、美观性、高强度、高透水性等技术要求,因此,本技术的复合透水砖表面孔隙较少,铺装好的透水路面的整体性、美观性舒适性均有所提升。
[0091]
所以,本发明有效克服了现有技术中的种种缺点而具高度产业利用价值。上述实施例仅例示性说明本发明的原理及其功效,而非用于限制本发明。任何熟悉此技术的人士皆可在不违背本发明的精神及范畴下,对上述实施例进行修饰或改变。因此,举凡所属技术领域中具有通常知识者在未脱离本发明所揭示的精神与技术思想下所完成的一切等效修饰或改变,仍应由本发明的权利要求所涵盖。