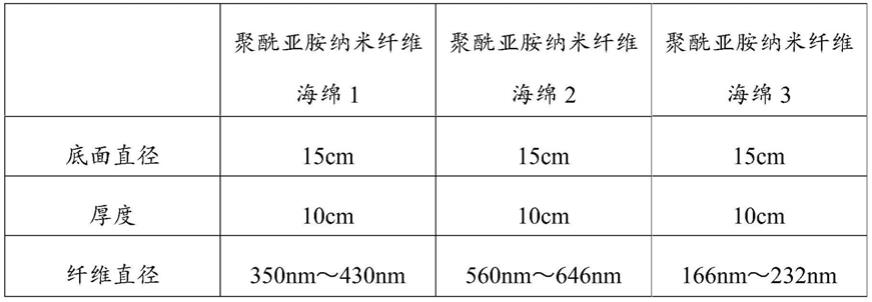
1.本发明属于纳米纤维材料技术领域,具体涉及一种聚酰亚胺纳米纤维海绵及其制备方法。
背景技术:
2.随着工业的生产,含油污废水、废液的排放,海上油污泄露等对地球生物的生存造成了极大威胁。当大量石油倾泻在海面上,会在海面形成厚厚的油膜隔绝空气,使得水体缺氧,附近海域内的生物缺氧死亡;同时油膜会影响大气与海水之间的气体交换,导致海洋生态环境严重失衡;另外,复杂的洋流环境和频繁的海上风浪,使得海上溢油很容易飘到海岸上,对周边的浅海养殖、盐田生产等造成污染,影响附近居民的生产生活,迫使人类亟需开发优良的吸油材料。
3.良好的油污吸附材料,具有疏水性和亲油性,高吸油量、成本低且可以在水面稳定漂浮等特点,但是传统的吸油材料存在各种各样的问题:吸油性能较低、材料成本高、浮力性质差、吸油的同时也吸水。因此,对高效、环保的有机吸油材料的研究具有十分重要的意义。
技术实现要素:
4.本发明旨在至少解决上述现有技术中存在的技术问题之一。为此,本发明提出一种聚酰亚胺纳米纤维海绵的制备方法,利用该法制备的聚酰亚胺纳米纤维海绵耐高温,具有疏水性和高吸油性,可以满足海上溢油清理的需求,且该制备方法可以用于纳米纤维的大规模生产。
5.本发明还提出一种采用上述制备方法制备的聚酰亚胺纳米纤维海绵。
6.根据本发明的一个方面,提出了一种聚酰亚胺纳米纤维海绵的制备方法,包括以下步骤:
7.s1:将助纺剂溶于溶剂中,制得助纺剂溶液;将聚酰胺酸溶液与所述助纺剂溶液混合,制得聚酰胺酸前躯体纺丝液;
8.s2:将所述的聚酰胺酸前驱体纺丝液进行气纺丝,制得聚酰胺酸纳米纤维海绵;
9.s3:热处理所述聚酰胺酸纳米纤维海绵,制得聚酰亚胺纳米纤维海绵。
10.根据本发明的一种优选的实施方式,至少具有以下有益效果:
11.1.由于助纺剂的溶解需要加热,聚酰胺酸溶液的制备需要在冰水浴的条件下进行,故将助纺剂溶于溶剂后再与聚酰胺酸溶液进行混合,可以改善溶解效果,同时也可以加快整个聚酰胺酸前驱体纺丝液的制备过程。
12.2.采用上述方法制备的聚酰亚胺纳米纤维海绵耐高温,具有疏水性和高吸油性,并且可以通过机械挤压或燃烧的方式达到循环再利用的目的,可以满足海上溢油吸油的需求。
13.3.操作简便,材料成本低,可用于大规模生产聚酰亚胺纳米纤维海绵。
14.在本发明的一些实施方式中,步骤s1所述的助纺剂采用聚合物助纺剂,包括聚氧化乙烯(peo)、聚乙烯吡咯烷酮(pvp)、聚乙烯醇(pva)、聚乙烯醇缩丁醛(pvb)中的至少一种。
15.在本发明的一些实施方式中,步骤s1所述的溶剂包括n,n-二甲基甲酰胺(dmf)、二甲基乙酰胺(dmac)、n-甲基吡咯烷酮(nmp)中的至少一种。
16.在本发明的一些实施方式中,步骤s1中所述溶剂的选择受所述助纺剂种类的限制。
17.在本发明的一些优选的实施方式中,步骤s1所述助纺剂选用30w分子量的peo,所述溶剂选用dmf。
18.在本发明的一些实施方式中,步骤s1所述助纺剂溶液中,助纺剂的质量分数为0.5%~30%。
19.在本发明的一些优选的实施方式中,步骤s1所述助纺剂溶液中,助纺剂的质量分数为1%~15%。
20.在本发明的一些实施方式中,步骤s1所述助纺剂溶于溶剂的过程可采用磁力搅拌、机械搅拌和超声振动中的至少一种方式辅助溶解,过程中可通过加热促进助纺剂的溶解,助纺剂和溶剂混合时的先后顺序不限。
21.在本发明的一些实施方式中,步骤s1所述的聚酰胺酸溶液,其制备方法具体包括:将二胺单体溶解在所述溶剂中,逐次加入二酐单体,进行缩聚反应,即得所述聚酰胺酸溶液。
22.在本发明的一些实施方式中,所述二胺单体包括十八胺(oda)、2,2
’‑
双(三氟甲基)-4,4
’‑
二氨基联苯(tmfb)、2,2-双[4-(4-氨基苯氧基)苯基]六氟丙烷(hfbapp)中的至少一种。
[0023]
在本发明的一些实施方式中,所述二酐单体包括均苯四甲酸二酐(pmda)、六氟二酐(6fda)、3,3’,4,4
’‑
二苯酮四酸二酐(btda)中的至少一种。
[0024]
在本发明的一些实施方式中,所述二胺单体和所述二酐单体的选择根据设计的聚酰亚胺结构而定。
[0025]
在本发明的一些实施方式中,步骤s1所述的聚酰胺酸溶液中,聚酰胺酸的质量分数为5%~20%。
[0026]
在本发明的一些优选的实施方式中,将oda溶解在dmf中,少量多次加入pmda,经缩聚反应制得质量分数为12%的所述聚酰胺酸溶液。
[0027]
在本发明的一些实施方式中,步骤s1所述的聚酰胺酸溶液,其制备过程中可采用机械搅拌辅助溶解,溶解条件为冰水浴,缩聚反应结束后混合2h以上,保证溶液粘度均匀。
[0028]
在本发明的一些实施方式中,步骤s1中所述聚酰胺酸溶液与所述助纺剂溶液混合,没有先后顺序,可采用磁力搅拌和机械搅拌中的至少一种方式混合,混合1h以上,过程中可通过短时间加热促进聚合物助纺剂的溶解。
[0029]
在本发明的一些实施方式中,所述聚酰胺酸溶液与所述助纺剂溶液的质量比为10:1~25:1。
[0030]
在本发明的一些实施方式中,进行步骤s2所述的气纺丝时,所述聚酰胺酸前驱体纺丝液的供给速度为20μl/min~50μl/min。
[0031]
在本发明的一些实施方式中,进行步骤s2所述的气纺丝时,针尖处的气流速度为10m/s~20m/s。
[0032]
在本发明的一些实施方式中,进行步骤s2所述的气纺丝时,所述聚酰胺酸前驱体纺丝液的供给速度和所述针尖处的气流速度根据所述聚酰胺酸前驱体纺丝液的固含量和所需要的纤维直径进行调节。
[0033]
在本发明的一些实施方式中,进行步骤s2所述的气纺丝时,所用气体包括空气、氧气、氮气、和氩气中的至少一种,气体湿度在60%以下,气体温度为10℃~80℃,通过控制气体温度可以控制溶剂的挥发速度,进而调控纤维的直径。
[0034]
在本发明的一些实施方式中,进行步骤s2所述的气纺丝时,出液针头距离滚筒表面的距离控制在10cm~50cm。
[0035]
在本发明的一些实施方式中,进行步骤s2所述的气纺丝时,纤维收集成纤维海绵依靠在金属篮上自然堆积形成。
[0036]
在本发明的一些实施方式中,步骤s3所述的热处理,在箱式炉中进行。
[0037]
在本发明的一些实施方式中,所述箱式炉中充有氧气、氮气、空气中的至少一种。
[0038]
在本发明的一些优选的实施方式中,所述箱式炉中充有氧气。
[0039]
在本发明的一些实施方式中,步骤s3所述的热处理,采用三段式工艺进行,具体包括:
[0040]
第一段,将温度从室温升高到80℃~100℃,升温速度为4℃/min~6℃/min,保温时间为50min~70min,使溶剂挥发完全;
[0041]
第二段,继续升温至280℃~320℃,升温速度为1℃/min~3℃/min,保温时间为110min~130min,使亚胺化反应完全;
[0042]
第三段,继续升温至380℃~420℃,升温速度为1℃/min~3℃/min,保温时间为110min~130min,使聚合物助纺剂挥发完全。
[0043]
在本发明的一些优选的实施方式中,第一段中所述的升温速度为5℃/min,所述保温时间为60min。
[0044]
在本发明的一些优选的实施方式中,第二段中所述升温至300℃,所述升温速度为2℃/min,所述保温时间为120min。
[0045]
在本发明的一些优选的实施方式中,第三段中所述升温至400℃,所述升温速度为2℃/min,所述保温时间为120min。
[0046]
根据本发明的再一个方面,提出了一种采用上述方法制备的聚酰亚胺纳米纤维海绵。
[0047]
根据本发明的一种优选的实施方式制备的聚酰亚胺纳米纤维海绵,至少具有以下有益效果:
[0048]
本发明中制备的聚酰亚胺纳米纤维海绵耐高温,具有疏水性和高吸油能力,能长期在350℃~450℃高温环境下使用,吸油率最高可达370g/g,并且可以通过机械挤压或燃烧的方式达到循环再利用的目的,可以满足海上溢油吸油的需求。
[0049]
在本发明的一些实施方式中,所述聚酰亚胺纳米纤维海绵为淡黄色圆柱体形状,底面直径由金属收集篮确定,为10cm~20cm,高度为5cm~20cm。
[0050]
根据本发明第三方面,提出了一种吸油装置。
[0051]
所述吸油装置包括骨架、浮力材料和吸油材料,所述吸油材料包括所述聚酰亚胺纳米纤维海绵。
[0052]
所述吸油装置为中空结构,所述浮力材料覆盖在所述骨架外侧,构成所述吸油装置的表面,所述浮力材料表面有多个孔,将所述吸油装置的内外导通,所述吸油材料设置在所述骨架的内侧。
附图说明
[0053]
下面结合附图和实施例对本发明做进一步的说明,其中:
[0054]
图1为本发明实施例聚酰胺酸前驱体纺丝液的制备过程示意图;
[0055]
图2为本发明实施例制备的聚酰亚胺纳米纤维海绵实物图;
[0056]
图3为本发明实施例1制备的聚酰亚胺纳米纤维微观形貌图;
[0057]
图4为本发明对比例1制备的聚酰亚胺纳米纤维微观形貌图;
[0058]
图5为本发明实施例1和对比例2制备的聚酰亚胺纳米纤维的力学性能图;
[0059]
图6为本发明实施例制备的聚酰亚胺纳米纤维海绵的热失重图;
[0060]
图7为本发明实施例制备的聚酰亚胺纳米纤维海绵的水接触角图。
具体实施方式
[0061]
下面详细描述本发明的实施例,所述实施例的示例在附图中示出,通过参考附图描述的实施例是示例性的,仅用于解释本发明,而不能理解为对本发明的限制。
[0062]
在本发明的描述中,以上、以下等理解为包括本数。除非另有明确的限定,搅拌、加热、溶解等词语应做广义理解,所属技术领域技术人员可以结合技术方案的具体内容合理确定上述词语在本发明中的具体含义。
[0063]
本发明的描述中,参考术语“一个实施例”、“一些实施例”、“示例”等的描述意指结合该实施例或示例描述的具体特征、方法或者材料包含于本发明的至少一个实施例或示例中。在本说明书中,对上述术语的示意性表述不一定指的是相同的实施例或示例。而且,描述的具体特征、方法或者材料可以在任何的一个或多个实施例或示例中以合适的方式结合。
[0064]
实施例中所使用的试验方法如无特殊说明,均为常规方法;所使用的材料、试剂等,如无特殊说明,均可从商业途径得到的试剂和材料。
[0065]
实施例1
[0066]
本实施例制备了一种聚酰亚胺纳米纤维海绵1,具体过程为:
[0067]
(1)制备聚酰胺酸前驱体纺丝液:将0.3866g的30w分子量的peo溶解在6.4432g dmf中,于60℃条件下磁力搅拌5h,获得助纺剂溶液;
[0068]
在冰水浴条件下,称取1.8503g oda单体溶解在28.3500g dmf中,经机械搅拌混合均匀后,取2.0156g pmda单体少量多次加入进行缩聚反应,缩聚反应结束后继续混合2h以上,保证溶液粘度均匀,获得聚酰胺酸溶液;
[0069]
将助纺剂溶液和聚酰胺酸溶液混合,于60℃条件下加热磁力搅拌1min后,在常温下磁力搅拌1h,获得聚酰胺酸前驱体纺丝液。
[0070]
(2)气纺丝:将获得的聚酰胺酸前驱体纺丝液放入气纺丝装置内进行气纺丝,获得
聚酰胺酸前驱体纳米纤维海绵。
[0071]
聚酰胺酸前驱体纺丝液的供给速度为30μl/min,针尖处的气流速度为15m/s,针头内径为180μm,气口直径为2mm。所用的气体为空气,湿度40%~60%,温度为室温。收集纤维海绵所用的金属篮底部直径为15cm,出液针头距离滚筒表面20cm。
[0072]
(3)热处理:将聚酰胺酸前驱体纳米纤维海绵放入含有氧气气氛的箱式炉内进行热处理。
[0073]
室温升温到80℃,升温速度为5℃/min,并在80℃保温60min,使溶剂挥发完全;将温度从80℃升高到300℃,升温速度为2℃/min,并在300℃下保温120min,使亚胺化反应完全;将温度从300℃升高到400℃,升温速度为2℃/min,并在400℃保温120min,使peo分解。
[0074]
实施例2
[0075]
本实施例制备了一种聚酰亚胺纳米纤维海绵2,具体过程为:
[0076]
(1)制备聚酰胺酸前驱体纺丝液:将0.3866g的30w分子量的peo溶解在6.4432g dmf中,于60℃条件下磁力搅拌5h,获得助纺剂溶液;
[0077]
在冰水浴条件下,称取1.8503g oda单体溶解在21.9068g dmf中,经机械搅拌混合均匀后,取2.0156g pmda单体少量多次加入进行缩聚反应,缩聚反应结束后继续混合2h以上,保证溶液粘度均匀,获得聚酰胺酸溶液;
[0078]
将助纺剂溶液和聚酰胺酸溶液混合,于60℃条件下加热磁力搅拌1min后,在常温下磁力搅拌1h,获得聚酰胺酸前驱体纺丝液。
[0079]
(2)气纺丝:将获得的聚酰胺酸前驱体纺丝液放入气纺丝装置内进行气纺丝,获得聚酰胺酸前驱体纳米纤维海绵。
[0080]
聚酰胺酸前驱体纺丝液的供给速度为30μl/min,针尖处的气流速度为15m/s,针头内径为180μm,气口直径为2mm。所用的气体为空气,湿度40%~60%,温度为室温。收集纤维海绵所用的金属篮底部直径为15cm,出液针头距离滚筒表面20cm。
[0081]
(3)热处理:将聚酰胺酸前驱体纳米纤维海绵放入含有氧气气氛的箱式炉内进行热处理。
[0082]
室温升温到80℃,升温速度为5℃/min,并在80℃保温60min,使溶剂挥发完全;将温度从80℃升高到300℃,升温速度为2℃/min,并在300℃下保温120min,使亚胺化反应完全;将温度从300℃升高到400℃,升温速度为2℃/min,并在400℃保温120min,使peo分解。
[0083]
实施例3
[0084]
本实施例制备了一种聚酰亚胺纳米纤维海绵3,具体过程为:
[0085]
(1)制备聚酰胺酸前驱体纺丝液:将0.3866g的30w分子量的peo溶解在9.6648g dmf中,于60℃条件下磁力搅拌5h,获得助纺剂溶液;
[0086]
在冰水浴条件下,称取1.8503g oda单体溶解在34.7931g dmf中,经机械搅拌混合均匀后,取2.0156g pmda单体少量多次加入进行缩聚反应,缩聚反应结束后继续混合2h以上,保证溶液粘度均匀,获得聚酰胺酸溶液;
[0087]
将助纺剂溶液和聚酰胺酸溶液混合,于60℃条件下加热磁力搅拌1min后,在常温下磁力搅拌1h,获得聚酰胺酸前驱体纺丝液。
[0088]
(2)气纺丝:将获得的聚酰胺酸前驱体纺丝液放入气纺丝装置内进行气纺丝,获得聚酰胺酸前驱体纳米纤维海绵。
[0089]
聚酰胺酸前驱体纺丝液的供给速度为30μl/min,针尖处的气流速度为15m/s,针头内径为180μm,气口直径为2mm。所用的气体为空气,湿度40%~60%,温度为室温。收集纤维海绵所用的金属篮底部直径为15cm,出液针头距离滚筒表面20cm。
[0090]
(3)热处理:将聚酰胺酸前驱体纳米纤维海绵放入含有氧气气氛的箱式炉内进行热处理。
[0091]
室温升温到80℃,升温速度为5℃/min,并在80℃保温60min,使溶剂挥发完全;将温度从80℃升高到300℃,升温速度为2℃/min,并在300℃下保温120min,使亚胺化反应完全;将温度从300℃升高到400℃,升温速度为2℃/min,并在400℃保温120min,使peo分解。
[0092]
对比例1
[0093]
本对比例制备了一种聚酰亚胺纳米纤维海绵4,与实施例1的区别在于前驱体纺丝液由聚酰亚胺纳米颗粒悬浮液和助纺剂溶液混合制成,热处理采用物理法完成,具体过程为:
[0094]
(1)制备前驱体纺丝液:将0.3866g的30w分子量的peo溶解在6.4432g dmf中,于60℃条件下磁力搅拌5h,获得助纺剂溶液;
[0095]
将购买的聚酰亚胺纳米颗粒配制成聚酰亚胺纳米颗粒悬浮液;
[0096]
将助纺剂溶液和聚酰亚胺纳米颗粒悬浮液混合,于60℃条件下加热磁力搅拌1min后,在常温下磁力搅拌1h,获得前驱体纺丝液。
[0097]
(2)气纺丝:将获得的前驱体纺丝液放入气纺丝装置内进行气纺丝,获得聚酰亚胺/peo复合纳米纤维海绵。
[0098]
前驱体纺丝液的供给速度为30μl/min,针尖处的气流速度为15m/s,针头内径为180μm,气口直径为2mm。所用的气体为空气,湿度40%~60%,温度为室温。收集纤维海绵所用的金属篮底部直径为15cm,出液针头距离滚筒表面20cm。
[0099]
(3)热处理:将聚酰亚胺/peo复合纳米纤维海绵放入含有氧气气氛的箱式炉内进行热处理。
[0100]
室温升高到最高温度400℃,升温速度为10℃/min,并在400℃保温120min,使peo分解,聚酰亚胺颗粒熔融烧结成纳米纤维。
[0101]
对比例2
[0102]
本对比例制备了一种聚酰亚胺纳米纤维海绵5,与实施例1的区别在于热处理采用一段式工艺进行,具体过程为:
[0103]
(1)制备聚酰胺酸前驱体纺丝液:将0.3866g的30w分子量的peo溶解在6.4432g dmf中,于60℃条件下磁力搅拌5h,获得助纺剂溶液;
[0104]
在冰水浴条件下,称取1.8503g oda单体溶解在28.3500g dmf中,经机械搅拌混合均匀后,取2.0156g pmda单体少量多次加入进行缩聚反应,缩聚反应结束后继续混合2h以上,保证溶液粘度均匀,获得聚酰胺酸溶液;
[0105]
将助纺剂溶液和聚酰胺酸溶液混合,于60℃条件下加热磁力搅拌1min后,在常温下磁力搅拌1h,获得聚酰胺酸前驱体纺丝液。
[0106]
(2)气纺丝:将获得的聚酰胺酸前驱体纺丝液放入气纺丝装置内进行气纺丝,获得聚酰胺酸前驱体纳米纤维海绵。
[0107]
聚酰胺酸前驱体纺丝液的供给速度为30μl/min,针尖处的气流速度为15m/s,针头
内径为180μm,气口直径为2mm。所用的气体为空气,湿度40%~60%,温度为室温。收集纤维海绵所用的金属篮底部直径为15cm,出液针头距离滚筒表面20cm。
[0108]
(3)热处理:将聚酰胺酸前驱体纳米纤维海绵放入含有氧气气氛的箱式炉内进行热处理。
[0109]
室温升高到最高温度400℃,升温速度为2℃/min,并在400℃保温120min,使peo分解。
[0110]
试验例
[0111]
本试验例测试了实施例制备的聚酰亚胺纳米纤维海绵的性能。
[0112]
1.聚酰亚胺纳米纤维海绵规格的测试
[0113]
通过对实施例1~3制备的聚酰亚胺纳米纤维海绵的大小规格进行了测量。
[0114]
测量方法:在自然状态下,对聚酰亚胺纳米纤维海绵的底面直径和厚度进行了测量,结果如表1所示。
[0115]
表1
[0116][0117]
实施例1~3制备的聚酰亚胺纳米海绵都为圆柱体形状,底面直径和厚度相同,但由于助纺剂溶液和聚酰胺酸溶液中助纺剂和聚酰胺酸所占的质量分数不同,所制得的纤维海绵的纤维直径不同,助纺剂和聚酰胺酸所占的质量分数越大,制得的纤维海绵的纤维直径越大。
[0118]
2.聚酰亚胺纳米纤维海绵微观结构的测试
[0119]
将实施例1和对比例1制备的聚酰亚胺纳米纤维海绵置于扫描电子显微镜下观察,结果如图3和图4所示。图3中,聚酰亚胺纳米纤维的形貌光滑,这是由于实施例1是将聚酰胺酸亚胺化为聚酰亚胺,热处理过程采用了化学法;而图4中,聚酰亚胺纳米纤维海绵的形貌较粗糙,这是由于对比例1是直接将聚酰亚胺纳米颗粒悬浮液与助纺剂溶液混合配制后进行气纺丝,热处理采用物理法,制备的聚酰亚胺纳米纤维由聚酰亚胺颗粒烧结在一起组成,导致形貌较粗糙。
[0120]
3.聚酰亚胺纳米纤维的力学性能测试
[0121]
由于实施例1中热处理采用三段式工艺进行,而对比例2中热处理采用一段式工艺进行,因此对实施例1和对比例2制备的聚酰亚胺纳米纤维的力学性能进行了测试。
[0122]
测试方法:使用万能试验机分别对实施例1和对比例2制备的聚酰亚胺纳米纤维薄膜进行拉伸性能测试,将纤维薄膜裁剪成长条形进行测试,测试速度为1.5mm/min,测试结果如图5所示。
[0123]
实施例1中的三段式热处理方式可以使每一步反应进行完全,从图5可以看出,实
施例1制得的聚酰亚胺纳米纤维的力学性能优于对比文件2的一段式热处理得到的聚酰亚胺纳米纤维的力学性能。
[0124]
4.聚酰亚胺纳米纤维海绵的吸油性能测试
[0125]
测试方法:称取一定质量的实施例1~3和对比例1、2制备的聚酰亚胺纳米纤维海绵,将其充分浸泡在装满机油的烧杯中1h后,取出并静置5min,测量吸油后的纳米纤维海绵的质量。
[0126]
计算聚酰亚胺纳米纤维海绵的吸油率,公式如下:
[0127][0128]
式中,q为纤维海绵的饱和吸油率,单位为g/g;m
t
为聚酰亚胺纳米纤维海绵吸油1h后的质量,单位为g;m0为聚酰亚胺纳米纤维海绵的初始质量,单位为g。
[0129]
测试时,分别称取实施例1、2、3和对比例1、2制备的聚酰亚胺纳米纤维海绵0.05g进行吸油试验,测试结果如表2所示。
[0130]
表2
[0131][0132]
5.聚酰亚胺纳米纤维海绵的热稳定性测试
[0133]
测试方法:利用热失重分析仪对本发明实施例制备的聚酰亚胺纳米纤维海绵的热稳定性进行测试,测试氛围选择空气,升温速率为10℃/min,温度范围为50℃~800℃,测试结果如图6所示。
[0134]
图6显示,当温度达到493℃时,聚酰亚胺纳米纤维海绵的质量开始降低,即温度达到493℃时聚酰亚胺纳米纤维海绵开始分解,表明本发明实施例制备的聚酰亚胺纳米纤维海绵的热稳定性优异,耐高温。
[0135]
6.聚酰亚胺纳米纤维海绵的疏水性测试
[0136]
测试方法:利用接触角测试仪对本发明实施例制备的聚酰亚胺纳米纤维海绵的疏水性能进行测试,测试结果如图7所示。
[0137]
当材料的接触角大于90
°
时,可评价该材料具有疏水性,角度越大疏水性越强。图7中显示,测得聚酰亚胺纳米纤维海绵的接触角为141.6
°
,表明本发明实施例制备的聚酰亚胺纳米纤维海绵具有较强的疏水性能。
[0138]
上面结合附图对本发明实施例作了详细说明,但是本发明不限于上述实施例,在所属技术领域普通技术人员所具备的知识范围内,还可以在不脱离本发明宗旨的前提下作出各种变化。此外,在不冲突的情况下,本发明的实施例及实施例中的特征可以相互组合。