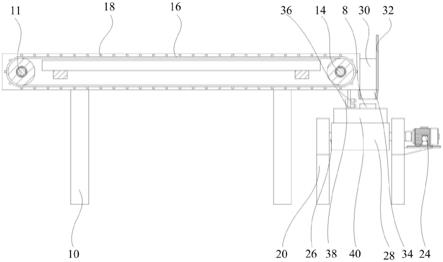
1.本实用新型属于包装分装技术领域,具体涉及一种包装设备。
背景技术:
2.目前,在相关技术中,医用口罩多采用一层或者多层非织造布复合制作而成,主要生产工艺包括熔喷、纺粘、热风或者针刺等,具有抵抗液体、过滤颗粒物和细菌等效用,是一种医疗防护用纺织品。医用口罩由口罩面体和拉紧带组成,其中口罩面体分为内、中、外三层,内层为亲肤材质,中层为隔离过滤层,外层为特殊材料抑菌层。现有的口罩包装设备具有三条传送装置,分别运送单个口罩、码放后的口罩和包装盒,先对单个口罩进行码放,将口罩按所需数量堆叠,再通过电动推杆将码放后的口罩同一推入放倒的包装盒内,生产线复杂,仅是输送过程就耗费大量时间,生产效率低下且成本较高。
技术实现要素:
3.为了解决上述现有技术中口罩包装时,需要先码放再统一装盒,耗时较长,效率低下等问题,本实用新型提供两级传送自动限位的口罩分装装置一种两级传送自动限位的口罩分装装置,通过两条传送装置解决口罩装盒的问题,省去先码放后装盒的步骤,方便省时,提高生产效率。其具体技术方案为:
4.一种两级传送自动限位的口罩分装装置,包括:第一支撑架、第一主动辊、第一电机、第一从动辊、第一皮带、隔条、第二支撑架、第二主动辊、第二电机、第二从动辊、第二皮带、连接板、挡板和导向套;所述第一主动辊垂直设置在所述第一支撑架的一端,且所述第一主动辊与所述第一支撑架转动连接;所述第一电机包括第一输出轴,所述第一电机固定在所述第一支撑架上,且所述第一输出轴与所述第一主动辊相连接;所述第一从动辊垂直设置在所述第一支撑架的另一端,且所述第一从动辊与所述第一支撑架转动连接;所述第一皮带同时套装在所述第一主动辊和所述第一从动辊的外侧;若干个所述隔条垂直设置在所述第一皮带的外壁上;所述第二支撑架垂直设置在所述第一支撑架一端的下方;所述第二主动辊垂直设置在所述第二支撑架的一端,且所述第二主动辊与所述第二支撑架转动连接;所述第二电机包括第二输出轴,所述第二电机固定在所述第二支撑架上,且所述第二输出轴与所述第二主动辊相连接;所述第二从动辊垂直设置在所述第二支撑架的另一端,所述第二从动辊与所述第二支撑架转动连接;所述第二皮带同时套装在所述第二主动辊和所述第二从动辊的外侧;两个所述连接板分别位于所述第一皮带的两侧,且两个所述连接板的一端同时与所述第一支撑架相连接;所述挡板垂直设置在所述第二支撑架的上方,且所述挡板同时两个所述连接板的另一端相连接;所述导向套同时与两个所述连接板和所述挡板相连接,且所述导向套的口径由靠近所述第一支撑架的一端向远离所述第一支撑架的一端逐渐减小。
5.另外,本实用新型提供的上述技术方案中的一种两级传送自动限位的口罩分装装置还可以具有如下附加技术特征:
6.在上述技术方案中,优选地,所述第一皮带的宽度为190~195mm。
7.在上述技术方案中,优选地,所述连接板的宽度为95~100mm。
8.在上述技术方案中,优选地,所述挡板的宽度为185~190mm。
9.在上述技术方案中,优选地,所述导向套的最小长度为184~188mm。
10.在上述技术方案中,优选地,所述导向套的最小宽度为94~98mm。
11.在上述技术方案中,优选地,所述两级传送自动限位的口罩分装装置还包括:红外感应器和连接架;两个所述红外感应器位于所述导向套的下方;所述连接架与所述第一支撑架相连接,且所述连接架与两个所述红外感应器相连接;其中,所述红外感应器与所述第一电机和所述第二电机电连接。
12.在上述技术方案中,优选地,所述第一电机和所述第二电机均为伺服电机。
13.在上述技术方案中,优选地,所述两级传送自动限位的口罩分装装置还包括:隔板;若干个所述隔板垂直设置在所述第二皮带的外壁上。
14.本实用新型的一种医用口罩分装装置一种两级传送自动限位的口罩分装装置,与现有技术相比,有益效果为:
15.一、本实用新型装置设置两条传送装置,与现有技术相比省去先码放后装盒的步骤,以轻易地实现口罩装盒操作,其结构简单,方便省时,节约生产成本。
16.二、设计运送口罩的传送装置和运送包装盒的传送装置,具有高度差的交叉设置,使口罩受自身重力而下落,并通过连接板和挡板限位,避免口罩具有惯性,继续向前运动,实现良好的定位效果。
17.三、通过导向套对口罩下落的方向进行导向,使口罩沿导向套的内壁逐一落在下方的包装盒内,使口罩码放与装盒同时进行,比起先码放口罩再统一装盒,省去装盒和运输的时间,工时缩短,效率更高。
18.四、第一电机和第二电机为伺服电机,两个红外感应器与第一电机和第二电机电连接,其中一个红外线感应器对口罩进行计数,另外一个检测包装盒的位置是否位于导向套下方。当上方的红外感应器计数数值与预设数值一致时,红外感应器传递信号,使第一电机暂停,第二电机启动;直至下方的红外感应器检测到后方的包装盒行走至导向套的下方,第一电机启动,第二电机暂停,如此循环,实现对口罩自动分装的技术效果,减少人工成本,从而达到减少生产成本的目的。
附图说明
19.图1为本实用新型实施例的一种两级传送自动限位的口罩分装装置的结构示意图;
20.图2为本实用新型实施例的一种两级传送自动限位的口罩分装装置的俯视图;
21.其中,图1和图2中的附图标记与部件名称之间的对应关系为:
22.8、包装盒;10、第一支撑架;11、第一主动辊;12、第一电机;14、第一从动辊;16、第一皮带;18、隔条;20、第二支撑架;22、第二主动辊;24、第二电机;26、第二从动辊;28、第二皮带;30、连接板;32、挡板;34、导向套;36、红外感应器;38、连接架;40、隔板。
具体实施方式
23.下面结合具体实施案例和附图1-2对本实用新型作进一步说明,但本实用新型并不局限于这些实施例。
24.实施例1
25.一种两级传送自动限位的口罩分装装置,如图1-2所示,包括:第一支撑架10、第一主动辊11、第一电机12、第一从动辊14、第一皮带16、隔条18、第二支撑架20、第二主动辊22、第二电机24、第二从动辊26、第二皮带28、连接板30、挡板32和导向套34;第一主动辊11垂直设置在第一支撑架10的一端,且第一主动辊11与第一支撑架10转动连接;第一电机12包括第一输出轴,第一电机12固定在第一支撑架10上,且第一输出轴与第一主动辊11相连接;第一从动辊14垂直设置在第一支撑架10的另一端,且第一从动辊14与第一支撑架10转动连接;第一皮带16同时套装在第一主动辊11和第一从动辊14的外侧;若干个隔条18垂直设置在第一皮带16的外壁上;第二支撑架20垂直设置在第一支撑架10一端的下方;第二主动辊22垂直设置在第二支撑架20的一端,且第二主动辊22与第二支撑架20转动连接;第二电机24包括第二输出轴,第二电机24固定在第二支撑架20上,且第二输出轴与第二主动辊22相连接;第二从动辊26垂直设置在第二支撑架20的另一端,第二从动辊26与第二支撑架20转动连接;第二皮带28同时套装在第二主动辊22和第二从动辊26的外侧;两个连接板30分别位于第一皮带16的两侧,且两个连接板30的一端同时与第一支撑架10相连接;挡板32垂直设置在第二支撑架20的上方,且挡板32同时两个连接板30的另一端相连接;导向套34同时与两个连接板30和挡板32相连接,且导向套34的口径由靠近第一支撑架10的一端向远离第一支撑架10的一端逐渐减小。
26.在该实施例中,优选地,通过使所述第一皮带16的宽度为190mm,使第一皮带16的宽度大于口罩的长度,以使口罩输送时摆放的更加整齐,便于装盒,同时避免口罩与第一支撑架10产生摩擦,保证口罩洁净。
27.在该实施例中,优选地,通过使连接板30的宽度为95mm,以使连接板30的宽度略大于口罩的宽度,使口罩以更加水平的状态落入第二皮带28上的包装盒8内,使装盒更加整齐。
28.在该实施例中,优选地,通过使挡板32的宽度为185mm,使挡板32的宽度略大于口罩的长度,在口罩下落时进行限位,提升下落位置的准确性,以保证装盒的连续性。
29.在该实施例中,优选地,通过使导向套34的最小长度为184mm,并使导向套34的最小宽度为94mm,缩小与口罩之间的间隙,更进一步对口罩下落时进行导向,保证口罩准确落入下方的包装盒8内,提高装盒的连续性,从而提高装盒效率。
30.在该实施例中,优选地,两级传送自动限位的口罩分装装置还包括:红外感应器36和连接架38;通过将红外感应器36位于导向套34的下方,并将连接架38与第一支撑架10相连接,且连接架38与红外感应器36相连接,以将红外感应器36固定在导向套34的一侧,对落入包装盒8内的口罩进行计数,代替人工计数,更加自动化,准确性也更高;通过使红外感应器36与第一电机12和第二电机24电连接,当红外感应器36计数为50个时,第一电机12停止转动,第二电机24开始转动,将后方的包装盒8输送至导向套34的下方,达到对口罩进行定量分装的目的,自动化程度更高,效率更高。
31.在该实施例中,优选地,通过使第一电机12和第二电机24均为伺服电机,伺服电机
可使控制速度,且位置精度非常准确,可以将电信号转化为转矩和转速以驱动控制第一皮带16和第二皮带28的运行,保证包装盒8准确达到导向套34的下方,确保口罩装入包装盒8内,保证工作质量,从而提升工作效率。
32.在该实施例中,优选地,两级传送自动限位的口罩分装装置还包括:隔板40;通过使若干个隔板40垂直设置在第二皮带28的外壁上,并使隔板40的间距略大于包装盒8的宽度,通过隔板40对包装盒8进行限位,保证包装盒8精准停在导向套34的下方,对口罩进行盛接,从而保证口罩准确落入包装盒8内,提升装盒的连续性,尽量避免通过操作者对包装盒8位置进行调整,提高自动化程度。
33.本实施例试应用在某口罩制造厂,对口罩进行输送和导向,本装置使口罩码放和装盒同步进行,减少输送长度,当每个包装盒8装入50个口罩时,装盒时间缩短40%左右。连接板30、挡板32和导向套34均设置为最小值,即限位和导向结构与口罩之间的间隙最小,此时,口罩下落时,与导向套34之间产生摩擦,下落时倾斜,导致堆叠在包装盒8内时,相邻口罩之间留有间隙,装盒结束后,需将口罩压实,使的装盒效率与理论值相比稍有下降,但总体效率提升34%左右。
34.实施例2
35.一种两级传送自动限位的口罩分装装置,如图1-2所示,包括:第一支撑架10、第一主动辊11、第一电机12、第一从动辊14、第一皮带16、隔条18、第二支撑架20、第二主动辊22、第二电机24、第二从动辊26、第二皮带28、连接板30、挡板32和导向套34;第一主动辊11垂直设置在第一支撑架10的一端,且第一主动辊11与第一支撑架10转动连接;第一电机12包括第一输出轴,第一电机12固定在第一支撑架10上,且第一输出轴与第一主动辊11相连接;第一从动辊14垂直设置在第一支撑架10的另一端,且第一从动辊14与第一支撑架10转动连接;第一皮带16同时套装在第一主动辊11和第一从动辊14的外侧;若干个隔条18垂直设置在第一皮带16的外壁上;第二支撑架20垂直设置在第一支撑架10一端的下方;第二主动辊22垂直设置在第二支撑架20的一端,且第二主动辊22与第二支撑架20转动连接;第二电机24包括第二输出轴,第二电机24固定在第二支撑架20上,且第二输出轴与第二主动辊22相连接;第二从动辊26垂直设置在第二支撑架20的另一端,第二从动辊26与第二支撑架20转动连接;第二皮带28同时套装在第二主动辊22和第二从动辊26的外侧;两个连接板30分别位于第一皮带16的两侧,且两个连接板30的一端同时与第一支撑架10相连接;挡板32垂直设置在第二支撑架20的上方,且挡板32同时两个连接板30的另一端相连接;导向套34同时与两个连接板30和挡板32相连接,且导向套34的口径由靠近第一支撑架10的一端向远离第一支撑架10的一端逐渐减小。
36.在该实施例中,优选地,通过使所述第一皮带16的宽度为190mm,使第一皮带16的宽度大于口罩的长度,以使口罩输送时摆放的更加整齐,便于装盒,同时避免口罩与第一支撑架10产生摩擦,保证口罩洁净。
37.在该实施例中,优选地,通过使连接板30的宽度为100mm,以使连接板30的宽度略大于口罩的宽度,使口罩以更加水平的状态落入第二皮带28上的包装盒8内,使装盒更加整齐。
38.通过使挡板32的宽度为190mm,使挡板32的宽度略大于口罩的长度,在口罩下落时进行限位,提升下落位置的准确性,以保证装盒的连续性。
39.在该实施例中,优选地,通过使导向套34的最小长度为188mm,并使导向套34的最小宽度为98mm,缩小与口罩之间的间隙,更进一步对口罩下落时进行导向,保证口罩准确落入下方的包装盒8内,提高装盒的连续性,从而提高装盒效率。
40.在该实施例中,优选地,两级传送自动限位的口罩分装装置还包括:红外感应器36和连接架38;通过将红外感应器36位于导向套34的下方,并将连接架38与第一支撑架10相连接,且连接架38与红外感应器36相连接,以将红外感应器36固定在导向套34的一侧,对落入包装盒8内的口罩进行计数,代替人工计数,更加自动化,准确性也更高;通过使红外感应器36与第一电机12和第二电机24电连接,当红外感应器36计数为50个时,第一电机12停止转动,第二电机24开始转动,将后方的包装盒8输送至导向套34的下方,达到对口罩进行定量分装的目的,自动化程度更高,效率更高。
41.在该实施例中,优选地,通过使第一电机12和第二电机24均为伺服电机,伺服电机可使控制速度,且位置精度非常准确,可以将电信号转化为转矩和转速以驱动控制第一皮带16和第二皮带28的运行,保证包装盒8准确达到导向套34的下方,确保口罩装入包装盒8内,保证工作质量,从而提升工作效率。
42.在该实施例中,优选地,两级传送自动限位的口罩分装装置还包括:隔板40;通过使若干个隔板40垂直设置在第二皮带28的外壁上,并使隔板40的间距略大于包装盒8的宽度,通过隔板40对包装盒8进行限位,保证包装盒8精准停在导向套34的下方,对口罩进行盛接,从而保证口罩准确落入包装盒8内,提升装盒的连续性,尽量避免通过操作者对包装盒8位置进行调整,提高自动化程度。
43.本实施例试应用在某口罩制造厂,对口罩进行输送和导向,本装置使口罩码放和装盒同步进行,减少输送长度,当每个包装盒8装入50个口罩时,装盒时间缩短40%左右。连接板30、挡板32和导向套34均设置为最大值,即限位和导向结构与口罩之间的间隙最大,此时,口罩下落时,可顺利通过连接板30、挡板32和导向套34,无倾斜,堆叠在包装盒8内时,码放整齐,装盒结束后,将盒盖扣好即可,效率与理论值近似,提升38%左右。