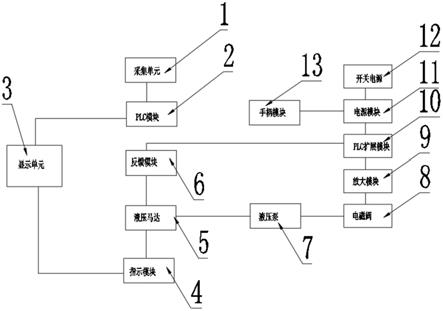
1.本实用新型涉及一种全回转拖轮舵桨控制系统,属于全回转拖轮舵桨控制技术领域。
背景技术:
2.全回转拖轮是港口生产的重要保障设备,上世纪八九十年代全回转拖轮舵桨设备多为进口设备,技术上和备件上完全依赖进口,随着我国社会发展和港口经济的发展,全回转拖轮设备性能升级速度加快,国内港口全回转拖轮的建造速度和设备性能快速发展,八九十年代的舵桨设备逐步被更新换代,基本处于被淘汰或维持使用的状态。
3.3600hp拖轮为1989年建造完成,主机为瓦锡兰柴油机-8r22md,舵桨为阿克马斯舵桨(现康士伯)-us1251。虽船龄较老,但一直作为主力拖轮使用,直接淘汰造成资源浪费,维持使用又存在诸多问题。
4.现有的液压控制系统如图5所示,该系统设有两台机带油泵,一台电动辅泵,润滑油和液压油都有这三台泵提供,在柴油机额定转速的80%以下时电动辅泵运转为系统供油,高于该转速辅泵油路旁通溢流,机带泵的排量可满足系统使用需求。液压润滑油路由一台主泵供油经滤器、减压安全阀,一路油经电磁换向阀(y11)驱动液压马达,一路去润滑油路,对齿轮箱各个点进行润滑和冷却。电动辅泵与该泵并联使用,作用有三点:1.在柴油机低转速,主泵排量不足时补偿主泵排量。2.在主泵故障或主机失去动力时作为备用油泵应急使用。 3.舵浆调试时使用。
5.液压离合油路由另一台主泵供油经滤器、减压安全阀,一路有经电磁换向阀(y12)驱动液压马达,一路经减压阀减压后为液压离合器提供动力油。
6.随着使用年限的加长,舵桨控制偶发性故障增多,转舵慢、转舵不同步、转舵卡滞等现象不定期出现。机械故障点多集中在液压泵、转舵电磁阀等部件上。电气及控制故障多集中在cpu-card、apq-card、指令模块和反馈模块、电源模块及其他控制模块上。故障多为间断式的,不持续的。随着温度、振动等因素的影响,偶发故障增多,这对发现问题,排除故障增加了难度。技术人员注重设备的技术革新工作,一直坚持加大设备的改造革新力度,不断优化设备性能,提高安全性和可靠性。
技术实现要素:
7.本实用新型针对上述现有技术中存在的不足,提供一种全回转拖轮舵桨控制系统。
8.本实用新型解决上述技术问题的技术方案如下:
9.一种全回转拖轮舵桨控制系统,包括两组plc模块,plc模块上设有采集单元和显示单元,显示单元上还设有指示模块,指示模块上依次设有液压马达、反馈模块和plc扩展模块,plc扩展模块上设有电源模块和放大模块,放大模块与液压马达之间设有液压泵,所述电源模块上还设有电源开关和手柄模块。
10.进一步,所述放大模块与液压泵之间设有电磁阀。
11.进一步,所述指示模块为指示电位计。
12.进一步,所述反馈模块为反馈电位计。
13.进一步,所述手柄模块为手柄电位计。
14.进一步,所述plc模块上还设有报警警示模块。
15.进一步,所述液压马达上设有并联连接的单向阀、冷却器和若干个润滑点,润滑点和冷却器之间设有背压阀,所述单向阀上设有双向变量泵,双向变量泵与冷却器之间设有油箱。
16.与现有技术相比,本实用新型的有益效果是:将原有的单柄控制改为半双柄控制,舵角转动范围较原系统前后方向扩展为35度,拖轮操控系统更加灵活。将原有的三台定量液压泵优化为一台变向变量泵,使得结构、性能更加优化。将原有的液压系统由阀控式优化为泵控式,系统组件减少,更加集成,周期维护费用大大降低,结构上减少了两台泵,两个阀组,使得成本降低。控制系统由集成电路改用为plc控制,通过放大模块将信号传输给电磁阀直接驱动液压马达,提高了拖轮的使用性能和安全性,同时提高适航性能和设备寿命。
附图说明
17.图1为本实用新型的控制系统电气原理图。
18.图2为本实用新型的其中一控制单元接线原理图。
19.图3为本实用新型的另一控制单元接线原理图。
20.图4为本实用新型的液压系统电气原理图。
21.图5为现有的液压系统电气原理图。
22.在图中,1、采集单元;2、plc模块;3、显示单元;4、指示模块;5、液压马达;6、反馈模块;7、液压泵;8、电磁阀;9、放大模块;10、plc扩展模块;11、电源模块;12、电源开关;13、手柄模块;51、单向阀;52、润滑点; 53、冷却器;54、背压阀;55、双向变量泵;56、油箱。
具体实施方式
23.以下结合附图对本实用新型的原理和特征进行描述,所举实例只用于解释本实用新型,并非用于限定本实用新型的范围。
24.如图1-图4所示,一种全回转拖轮舵桨控制系统,包括两组plc模块2, plc模块2上设有采集单元1和显示单元3,显示单元3上还设有指示模块4,指示模块4上依次设有液压马达5、反馈模块6和plc扩展模块10,plc扩展模块10上设有电源模块11和放大模块9,放大模块9与液压马达5之间设有液压泵7,所述电源模块11上还设有电源开关12和手柄模块13。所述放大模块9 与液压泵7之间设有电磁阀8。所述指示模块4为指示电位计。所述反馈模块6 为反馈电位计6。所述手柄模块13为手柄电位计。所述plc模块2上还设有报警警示模块。所述液压马达5上设有并联连接的单向阀51、冷却器53和若干个润滑点52,润滑点52和冷却器53之间设有背压阀54,所述单向阀51上设有双向变量泵55,双向变量泵55与冷却器53之间设有油箱56。一个双向变量泵55的排油方向和排量可根据指令改变,控制采用电比例控制,操作方便。双柄控制的方式,将一个手柄分解为两个手柄,手柄从前拉到后,舵角移动范围增加到240度。主要目的是解决船舶自由航行时的小舵角修正需求和作业时的横移需求,实
际使用中操作方便,灵活可靠,较单柄有很大优势。
25.在不改动原系统任何部件及线路基础上,充分利用plc控制的优势,追求模块化、结构化,以集成高效的模块布置于原驾控台内。根据技术人员的使用经验和习惯,将原有的单手柄控制改为左手柄和右手柄,左手柄和右手柄分别通过plc模块2控制,采集单元1采集信息反馈给相应的plc模块2,plc模块2将信号经显示单元3传输给指示模块4和反馈模块6,反馈模块6将信号输送给plc扩展模块10,通过plc扩展模块10和放大模块9直接驱动电磁阀8,放大模块9最大可输出4a工作电流,电磁阀8线圈消耗功率仅为15.6w,可有效简化系统,控制性能更可靠,其中的指示模块4和反馈模块6采用的是5k欧姆电位计,12v直流电压施加于手柄电位计上,随着电位计的转动,电压发生变化,经plc扩展模块10处理后的信号为
±
10v的直流信号,经放大模块9放大后输出相应电压直接接通电磁阀8,驱动液压马达5转动。随着舵角的转动,反馈模块6(反馈电位计)随之转动,并将信号差异反馈至plc扩展模块10,当信号无差异时,plc扩展模块10无信号输出,电磁阀8断电,液压马达5无输出。该系统结构简单,无需设计隔离模块,信号传输稳定;性能可靠,该型放大模块9最大可输出4a工作电流,电磁阀线圈消耗功率仅为15.6w,完全满足使用需求;控制方便,放大模块9具有斜坡控制功能,可根据需求调整两个方向的转舵速度;单柄控制改为半双柄控制,舵角转动范围较原系统前后方向扩展为35度,拖轮操控系统更加灵活。将原有的三台定量液压泵优化为一台变向变量泵,结构、性能更加优化;将原有的液压系统由阀控式优化为泵控式,系统组件减少,更加集成,周期维护费用大大降低,同时结构上减少了两台泵,两个阀组,成本降低。控制系统由集成电路改用为plc控制,通过放大模块9 将信号传输给电磁阀8直接驱动液压马达5,提高了拖轮的使用性能和安全性,同时提高适航性能和设备寿命,为安全生产提高了有效保障,改进后的3600hp 拖轮仍然发挥了主力拖轮的作用。
26.改进后,0-180度的转舵速度由22秒提高到15秒,舵角响应性大大提高。两桨的转舵速度同步,彻底消除了多年来,同样指令需求两螺旋桨速度不同步,安全性无法提高的问题。解决了指令与实际舵角存在差异的问题,性能得到恢复。转舵过程中,舵角卡顿问题解决,舵角转动过程中动作平滑,无冲击力,船体振动;液压、润滑原理采用的是同轴驱动的双向变量泵55单独供油系统,可有效保证液压油的清洁与独立,避免系统滑油对液压油产生影响,提高了液压系统的可靠性和稳定性。润滑油为单独油泵供油,除保证各个润滑点的润滑外,还提供液压马达7刹车用油。整个系统与原系统相比,具有系统独立,相互干扰小的优点,润滑油的最低压力通过溢流阀调节,以适应不同的润滑压力需求。实际使用中,液压油压力最大35bar,润滑油压力最大12bar,完全满足使用需求。双向变量泵55的性能,有效解决了转舵慢、转舵过程卡顿等系列问题,机械和液压性能大大提升,操控性和船舶安全性得到根本性改善。
27.以上所述仅为本实用新型的较佳实施例,并不用以限制本实用新型,凡在本实用新型的精神和原则之内,所作的任何修改、等同替换、改进等,均应包含在本实用新型的保护范围之内。