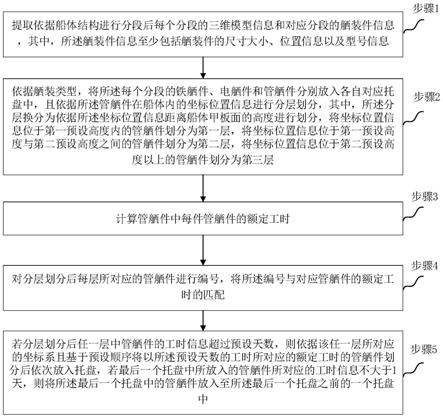
1.本发明涉及船舶建造技术领域,特别是一种舾装安装顺序智能化设计方法。
背景技术:
2.为在船舶建造过程中船舶舾装贯穿船舶整个建造过程,舾装作业面广,工程量大,舾装工程量通常占船舶建造总工程量的50%
‑
60%,对复杂船型和特种船甚至更高。为了缩短船坞周期,预舾装率会直接影响整个船舶建造周期,通常采用成组技术和托盘化管理,以此来提高分段预舾装率。目前国内的舾装率已经达到较高水准,但舾装作业仍存在问题。
3.为解决船厂预舾装托盘以分段为单位进行划分的弊端,通过调研相关的生产设计、生产管理、船装、信息部等部门,掌握舾装作业特点,以机舱分段为对象,分析舾装作业分解的原则和方法,研究船舶舾装安装顺序(dop)智能化设计方法,改变船厂粗放的预舾装现场作业现状,完成现场舾装托盘精细划分,达到精细化作业的目标,提高舾装效率。
4.舾装作业流程主要包括内场单元组装、分段预舾装、总段预舾装、船坞安装以及码头系泊试验这几个阶段,其中内场单元组装和分段预舾装、总段预舾装被称为先行舾装,船坞安装和码头系泊试验被称为后行舾装。对于大多数造船企业,在制定建造方针时,船厂的设计、采购和生产制造部门就己经根据生产节拍和节点要求,确定了船体各作业阶段的舾装工作量。由于大多数舾装作业具有相对独立性,为了满足精益造船的生产节拍要求,可以比较灵活地将其分配到船舶制造的各个阶段,并能逐一实现,最终确保各生产阶段舾装工程的完整。
5.为了尽可能地减少无效作业时间,提高舾装安装效率,在将舾装作业分配时应该遵循以下几项原则:
6.(1)作业内容的前移:舾装施工内容应尽可能考虑码头作业船坞做、船坞作业平台做、平台作业内场做,这样既确保了施工安全,同时也能有效提高施工质量和安装效率。
7.(2)作业环境的改变:为了充分考虑到作业人员安全以及生产效率,在生产设计阶段就应该充分考虑将一些在密闭的、狭小的、高空的、不安全区域的舾装作业放置到敞开的、宽敞的、低空的、安全的施工阶段和位置进行,以达到安全作业、高效作业的目的。
8.(3)扩大舾装作业量:应该通过内场单元组装、分段预舾装、总段预舾装等尽量扩大先行舾装的作业量,提高分段、总段的预舾装率,这样不仅可以有效改善作业条件,还可以提高生产效率,缩短造船周期。
9.(4)平衡工作包物量:对于每天或某个阶段的工作物量,应充分考虑均衡分配每一个工作包的工作量,合理安排生产计划,以达到连续作业的效果,使人、机、料始终处于流转的状态。尽可能避免等工、等料而导致的大量劳动力浪费,从而为实现生产效率的提升。
10.船舶上的舾装件种类繁多,且数量巨大。按专业分,可分为管舾件、铁舾件和电舾件;按物资种类分,可分为栏杆、直梯、斜梯、风管支架、管支架、管子、风管、电缆托架、电缆扁钢等。其中最为典型的是机舱内的舾装件,如图1所示。现场的施工需要按照一定的工序进行安装施工,即安装需要有先后顺序,否则就会出现舾装难以安装或是无法安装的情况.
11.预舾装作业的一般作业工序层次如图2所示,具体为:
12.第一层:电舾件安装,包括电缆托架、电缆扁钢等;
13.第二层:管舾件安装,包括管子、支架、阀附件、管附件等;
14.第三层:风管安装,包括风管、风管支架、风管附件等;
15.第四层:大型铁舾件,如平台、吊梁等。
16.其中管舾件安装与风管安装又分为热安装与冷安装,热安装是支架的定位、烧焊工序,冷安装为管子的连接安装,主要的连接形式有法兰连接、卡套连接、螺纹连接和套管连接等。其流程图如图3所示。
技术实现要素:
17.有鉴于现有技术中存在的上述问题,本发明实施例提供一种结合工时信息和管舾件的额定工时,实现了对托盘物量的精细化估算的舾装安装顺序智能化设计方法。
18.本发明实施例提供一种舾装安装顺序智能化设计方法,包括:
19.提取依据船体结构进行分段后每个分段的三维模型信息和对应分段的舾装件信息,其中,所述舾装件信息至少包括舾装件的尺寸大小、位置信息以及型号信息;
20.依据舾装类型,将所述每个分段的铁舾件、电舾件和管舾件分别放入各自对应托盘中,且依据所述管舾件在船体内的坐标位置信息进行分层划分,其中,所述分层换分为依据所述坐标位置信息距离船体甲板面的高度进行划分,将坐标位置信息位于第一预设高度内的管舾件划分为第一层,将坐标位置信息位于第一预设高度与第二预设高度之间的管舾件划分为第二层,将坐标位置信息位于第二预设高度以上的管舾件划分为第三层;
21.计算管舾件中每件管舾件的额定工时;
22.对分层划分后每层所对应的管舾件进行编号,将所述编号与对应管舾件的额定工时的匹配;
23.若分层划分后任一层中管舾件的工时信息超过预设天数,则依据该任一层所对应的坐标系且基于预设顺序将以所述预设天数的工时所对应的额定工时的管舾件划分后依次放入托盘,若最后一个托盘中所放入的管舾件所对应的工时信息不大于1天,则将所述最后一个托盘中的管舾件放入至所述最后一个托盘之前的一个托盘中。
24.在本发明的一些实施例中,所述第一预设高度为1米,所述第二预设高度为2m。
25.在本发明的一些实施例中,所述每件管舾件的额定工时基于管舾件对应的基础物量、修正属性以及物量单位确定。
26.在本发明的一些实施例中,所述预设天数为1.5天至3天;
27.所述预设顺序至少包括以所述每个分段对应的长度方向和宽度方向所形成的相互垂直的水平坐标系。
28.在本发明的一些实施例中,在所述提取依据船体结构进行分段后每个分段的三维模型信息和对应分段的舾装件信息之前,所述方法还包括:
29.构建管舾件安装知识库,包括:将管舾装件按照管径大小、安装类型、所在区域位置以及施工方式确定各个管舾件的安装工时。
30.与现有技术相比,本发明实施例提供的舾装安装顺序智能化设计方法的有益效果在于:其解决了船舶舾装生产设计托盘,特别是管系安装托盘的精细化划分问题,实现了对
托盘物量的精细化估算,结合安装管舾件的定额工时,实现对每个托盘中的物量的合理规划,提高了船舶舾装生产设计效率。
附图说明
31.图1为本发明实施例的舾装安装顺序智能化设计方法的流程图;
32.图2为本发明实施例的舾装安装顺序智能化设计方法的流程示意图;
33.图3为本发明实施例的舾装安装顺序智能化设计方法中机舱典型分段舾装件实物图;
34.图4为本发明实施例的舾装安装顺序智能化设计方法中的实物图详图;
35.图5为本发明实施例的舾装安装顺序智能化设计方法中舾装安装顺序示意图;
36.图6为本发明实施例的舾装安装顺序智能化设计方法中管舾件的一种安装总体布局图;
37.图7为本发明实施例的舾装安装顺序智能化设计方法的图6中管舾件的安装图分页图;
38.图8为本发明实施例的舾装安装顺序智能化设计方法中管舾件的另一种安装总体布局图;
39.图9为本发明实施例的舾装安装顺序智能化设计方法的图8中管舾件的安装图第一分页图;
40.图10为本发明实施例的舾装安装顺序智能化设计方法的图8中管舾件的安装图第二分页图;
41.图11为本发明实施例的舾装安装顺序智能化设计方法的图8中管舾件的安装图第三分页图。
具体实施方式
42.为使本领域技术人员更好的理解本发明的技术方案,下面结合附图和具体实施方式对本发明作详细说明。
43.此处参考附图描述本技术的各种方案以及特征。
44.通过下面参照附图对给定为非限制性实例的实施例的优选形式的描述,本技术的这些和其它特性将会变得显而易见。
45.还应当理解,尽管已经参照一些具体实例对本技术进行了描述,但本领域技术人员能够确定地实现本技术的很多其它等效形式,它们具有如权利要求所述的特征并因此都位于借此所限定的保护范围内。
46.当结合附图时,鉴于以下详细说明,本技术的上述和其它方面、特征和优势将变得更为显而易见。
47.此后参照附图描述本技术的具体实施例;然而,应当理解,所申请的实施例仅仅是本技术的实例,其可采用多种方式实施。熟知和/或重复的功能和结构并未详细描述以根据用户的历史的操作,判明真实的意图,避免不必要或多余的细节使得本技术模糊不清。因此,本文所申请的具体的结构性和功能性细节并非意在限定,而是仅仅作为权利要求的基础和代表性基础用于教导本领域技术人员以实质上任意合适的详细结构多样地使用本申
请。
48.本说明书可使用词组“在一种实施例中”、“在另一个实施例中”、“在又一实施例中”或“在其它实施例中”,其均可指代根据本技术的相同或不同实施例中的一个或多个。
49.本发明实施例提供一种舾装安装顺序智能化设计方法,所述方法包括构建管舾件安装知识库,具体为:将管舾装件按照管径大小、安装类型、所在区域位置以及施工方式确定各个管舾件的安装工时,管舾件至少包括管系舾装件和管支架。在实际操作过程中,需分别针对管系舾装件和管支架安装构建不同的工时知识库,针对管系舾装件工时知识库,可将管系舾装件按照管径大小、安装类型、所在区域位置等信息结合现场施工方式(现场施工习惯)确定其安装工时,建立舾装安装工时知识库,具体可参见如下管系安装定额表所示:
[0050][0051]
针对管支架安装工时知识库,则对于不同管支架重量、施工阶段、管支架安装方式进行分类,分区域按照现场实际安装工时进行统计,建立管支架安装工时知识库,具体可参见如下管支架安装工时定额表所示:
[0052]
管支架安装工时定额表
[0053][0054]
工时知识库的建立,使得对舾装工时的设计、舾装托盘的划分等的设计、管理更加有序化,使得宝贵的经验知识得以保留,方便设计人员查阅,节约设计人员计算思考的时间,减少舾装设计工作的工作量,提高设计人员工作效率的同时使得设计更加合理。
[0055]
但由于目前定额工时的准确率不高,只能当作工时参考,不能达到指导现场实际工时统计的目的,但可以作为托盘按照工时划分的参考依据。
[0056]
在建立工时知识库之后,如图1至图11所示,图1为本发明实施例提供的舾装安装顺序智能化设计方法的流程图,所述方法还包括如下步骤:
[0057]
步骤1:提取依据船体结构进行分段后每个分段的三维模型信息和对应分段的舾装件信息,其中,所述舾装件信息至少包括舾装件的尺寸大小、位置信息以及型号信息;
[0058]
步骤2:依据舾装类型,将所述每个分段的铁舾件、电舾件和管舾件分别放入各自对应托盘中,且依据所述管舾件在船体内的坐标位置信息进行分层划分,通常一个分段的铁舾件和电舾件数量有限,工作量大约在2
‑
3天,因此将铁舾件和电舾件分别放入两个托盘中,同时,所述分层换分为依据所述坐标位置信息距离船体甲板面的高度进行划分,将坐标位置信息位于第一预设高度内的管舾件划分为第一层,将坐标位置信息位于第一预设高度与第二预设高度之间的管舾件划分为第二层,将坐标位置信息位于第二预设高度以上的管舾件划分为第三层;在本发明的一些实施例中,所述第一预设高度为1米,所述第二预设高度为2m。
[0059]
在本实施例中,托盘具有尺寸要求和重量要求,其中,
[0060]
托盘的尺寸要求为:
[0061]
木质托盘承载舾装件(管支架、u码、大部分电舾件等较小的舾装件):以木托标准尺寸(1.2m x 0.9m)与堆放货架尺寸(1.5m x 1m x 0.9m)为依据,该类托盘应满足长<1.5m,宽<1m,高<0.7m;钢质托盘承载舾装件(较大的舾装件,如门、窗、贯穿件等):以钢托尺寸(3m x 1.6m x 0.9m)为约束,该类托盘应满足长<3m,宽<1.6m,高<1.2m;超长舾装件(直、斜梯,栏杆等):考虑到道路宽度等运输条件,该类舾装件托盘应满足长<6m,宽<1.6m,高<1.2m。
[0062]
托盘的重量要求为:
[0063]
钢托盘:钢托承重为5吨,考虑到叉车运力与钢托自重,其舾装件总重应<4500kg;
[0064]
木托盘:舾装件无规则摆放时<1000kg;规则平整摆放时<1500kg;紧凑、规则摆放时<2000kg。
[0065]
步骤3:计算管舾件中每件管舾件的额定工时;在本发明的一些实施例中,所述每件管舾件的额定工时基于管舾件对应的基础物量、修正属性以及物量单位确定,具体可依据以下公式进行计算:
[0066]
定额工时=基础物量*修正属性*物量单位。
[0067]
其中,基础物量是根据舾装类型进行分类的,主要分成管舾安装、电舾安装、铁舾安装等;管舾安装又可根据专业分为阀附件、管支架、管子等;管子又可分为多芯管、塑料管、舷侧管等;不同的种类基础物量工时是有差异的,基础物量也可理解成某种舾装件的单位工时。
[0068]
修正属性是根据同种舾装件的性质不同而改变的系数,并且考虑安装方式以及安装位置的不同而有所不同,以管子为例,根据管子的口径、壁厚、类型等的不同修正属性将改变,同种管子的弯角不同修正属性也不同;并且舾装件根据其安装在分总段位置以及安装方式的不同也会发生变化。
[0069]
物量单位是指根据舾装件的大小、尺寸等决定的,舾装件尺寸越大,管子越长,物量单位越大。
[0070]
根据作业工时、物量信息统计情况,确定基于托盘物量设置的舾装安装顺序基本原则如下:
[0071]
(1)施工班组人数固定,安装和焊接占比7:3,管舾件安装6
‑
7天,焊接2
‑
3天(以上时间是指同时开工时间);
[0072]
(2)分段一般分配给单个班组;
[0073]
(3)舾装顺序:
①
电舾件(电缆托架、扁钢、基座等);
②
管舾件(先支架后管系);
③
通风铁舾件(先支架后风管);
[0074]
(4)施工人员按照先铜工后电焊工的顺序工作,预舾装属于实物量承包,人员由班组自行分配。
[0075]
(5)典型机舱分段的管系安装标准周期一般设为十天。
[0076]
管舾件安装6
‑
7天,焊接2
‑
3天(以上时间是指同时开工时间)。
[0077]
步骤4:对分层划分后每层所对应的管舾件进行编号,将所述编号与对应管舾件的额定工时的匹配;
[0078]
步骤5:若分层划分后任一层中管舾件的工时信息超过预设天数,则依据该任一层所对应的坐标系且基于预设顺序将以所述预设天数的工时所对应的额定工时的管舾件划分后依次放入托盘,若最后一个托盘中所放入的管舾件所对应的工时信息不大于1天,则将所述最后一个托盘中的管舾件放入至所述最后一个托盘之前的一个托盘中。在本发明的一些实施例中,所述预设天数为1.5天至3天;所述预设顺序至少包括以所述每个分段对应的长度方向和宽度方向所形成的相互垂直的水平坐标系。作为示例,在工时信息与工件信息匹配后,判断某一层的定额工时是否超过2天,若工时超过2天,按照相互垂直的水平坐标系(如,x轴或y轴坐标)由小至大的顺序将同一层中同一系统的管子放入一个托盘,托盘容量按照2天的定额工时进行划分;直至本层管子全部划分完成,判断划分的最后一个托盘的工时是否小于等于1天,如果小于等于1天则将最后一批管子划分到上个一托盘中;至此某一
层的管舾件托盘划分完成。其余每一层都按照该方法直至分段的管舾件全部划分完毕。
[0079]
为了便于对上述技术方案进行理解,下面基于传统的舾装设计部门托盘划分现状,以及各托盘在生产中的作用,以典型机舱分段舾装托盘划分为例介绍如下:
[0080]
(1)生成安装图和托盘,舾装生产设计完成建模工作后,设计人员利用sem软件提取tribon中分段模型信息(舾装设计是以分段为单位进行的),并生成安装图和安装托盘,一个分段的管子安装托盘中大约有100
‑
200根管子。
[0081]
(2)安装图的划分,舾装设计部门的管子总体布局图是显示整个分段所有管舾件的安装视角的轴测图。其余分页是根据图面大小,调入适当数量的管子和支架,按安装视角作图。直到把所有管子及支架全部体现,并没有考虑管子的安装顺序。管子安装总体布置图及管子安装图分页如图6和图7所示。
[0082]
(3)生成制作托盘,舾装设计部将安装托盘下发给模块部sem系统,利用sem软件分托划分安装托盘为制作托盘,制作托盘按照管子的形状、管径、大小等特征进行分类,每个托盘大约有30
‑
60根管子。
[0083]
(4)管子加工,模块部门按管子的类型在不同生产线进行管子加工。最后再以分段为单位将制作托盘合并成安装托盘。
[0084]
(5)分拣集配,集配部门根据安装托盘对托盘进行分拣、集配。
[0085]
传统的托盘划分不符合详细舾装顺序,托盘内管子数量较多,托盘内的管子与安装图关联性较弱,现场工人在安装时会花费较多时间在找管子上,影响施工效率,不同设计人员的出图习惯也不尽相同,安装图可能出现不符合现场安装习惯的情况,不利于现场施工。
[0086]
基于上述研究,分段舾装安装顺序(dop)智能化设计以典型分段为例进行托盘划分和安装图出图,介绍如下:
[0087]
(1)提取分段模型信息、获取舾装件信息,提取分段的三维模型信息以及舾装件的尺寸大小、位置以及型号等信息,结合船体结构分段的划分考虑制作、吊运、安装工艺、安装阶段的合理性,模块划分考虑其结构尺寸、功能,尽量使小的设备、管子、部件、附件组装一个整体,形成功能完整而且独立的模块,简化系统构成。
[0088]
(2)将管舾件先按其位置信息进行分块分层,甲板面1m内为的管舾件划分为第一层,1
‑
2米内的管舾件划分为第二层,超过2m的管舾件作为第三层;
[0089]
(3)利用工时信息计算出管舾件安装所需要的定额工时,对托盘进行精细化划分,将每个托盘内管舾件安装的定额工时控制在2天以内,对于定额工时超过2天或者不足1天的进行重新划分,直至托盘划分完毕。
[0090]
(4)托盘划分完成后将信息导入设计软件内,利用托盘划分信息进行安装图分页划分,使得安装图分页与托盘相对应,得到符合详细舾装顺序的安装图。采用详细舾装顺序安装图如图8至图11所示。
[0091]
利用分段舾装安装顺序(dop)智能化设计方法所划分的托盘符合详细舾装顺序,托盘内管子数量适中,安装图按照托盘内的管子分页,现场工人在安装时会方便在托盘内找到自己需要的管子,提高施工效率,不同设计人员的出图习惯不相同,但在软件的条件下所出的安装图基本结构相差不大,减小了现场工人的识图难度,有利于现场施工。
[0092]
以上实施例仅为本发明的示例性实施例,不用于限制本发明,本发明的保护范围
由权利要求书限定。本领域技术人员可以在本发明的实质和保护范围内,对本发明做出各种修改或等同替换,这种修改或等同替换也应视为落在本发明的保护范围内。