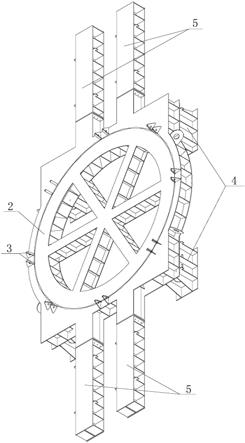
1.本实用新型涉及一种用于吸力桩导管架基础的运输工装。
背景技术:
2.吸力式导管架基础具有无桩体打桩施工、安装快速简便、节省施工时间、拆除方便等一系列优优势正越来越多地被用于海上风电基础。吸力式导管架基础建造完成后,通常采用竖直运输方式海运到施工现场。由于吸力式导管架基础的总体高度高、重量重,整体立运落驳工艺技术复杂,对码头、驳船和受涌浪影响大的海上立运稳定性要求高。为了确保吸力筒的底部全部着地且均匀受力,防止导管架基础在装载、运输过程中由于碰撞、摩擦等原因造成防腐涂层破坏、结构变形损伤,防止导管架基础在装载起吊过程中,避免钢丝绳、抱箍等接触、摩擦、刮碰导管架,避免造成防腐涂层的损坏,确保运输、上驳及长距离海上运输的安全可靠,需要设计专用的运输工装。
技术实现要素:
3.本实用新型的目的在于克服现有技术的缺陷而提供一种用于吸力桩导管架基础的运输工装,它的整体稳定性强,稳定性高,能满足吸力桩导管架基础在直立状态下的落驳运输要求。
4.本实用新型的目的是这样实现的:一种用于吸力桩导管架基础的运输工装,所述吸力桩导管架基础包括三根以连接线呈等边三角形布置的吸力桩筒、安装在三根吸力桩筒的顶面上的导管架和安装在导管架顶面上的过渡段;三个吸力桩筒各自采用一套运输工装;每套运输工装包括底座、八对导向板、四个支墩和四根加长横梁;其中,
5.所述底座的外轮廓基本呈矩形且中心开设一个直径小于所述吸力桩筒的内径的内孔,该底座的一对长边的中部为圆心位于底座的中心且直径大于所述吸力桩筒的外径的圆弧边,该底座的一对短边为直边,该一对短边的中部各自延伸两根横梁;
6.八对导向板固定在所述底座的顶面上并沿一个直径与所述吸力桩筒的外径相同的圆上均布布置;
7.四个支墩一一对应地安装在所述底座的一对短边的两个角部的底面上;
8.四根加长横梁一一对应地连接在所述底座的四根横梁的外端面上。
9.上述的用于吸力桩导管架基础的运输工装,其中,所述底座包括两块主底板、支撑筒和三根连接梁;两块主底板一一对应地固定在多块均布的主筋板的顶面和底面上;所述支撑筒的外径和壁厚一一对应地与所述吸力桩筒的外径和壁厚相同,该支撑筒的高度与所述主筋板的高度相同,该支撑筒与所述底座的内孔同轴地固定在两块主底板之间;三根连接梁以呈星号的连接方式跨接在所述底座的内孔的孔壁之间。
10.上述的用于吸力桩导管架基础的运输工装,其中,所述连接梁包括两块连接梁底板、多块连接在两块连接梁底板之间的横向筋板和一块连接在两块连接梁底板之间的纵向筋板。
11.上述的用于吸力桩导管架基础的运输工装,其中,所述支墩包括两块墩底板、若干块连接在两块墩底板之间的横向筋板和若干块连接在两块墩底板之间的纵向筋板。
12.上述的用于吸力桩导管架基础的运输工装,其中,所述加长横梁包括两块横梁底板、若干块连接在两块横梁底板之间的横向筋板和一块连接在两块横梁底板之间的纵向筋板。
13.本实用新型的用于吸力桩导管架基础的运输工装具有以下特点:
14.1)在底座的中心开设内孔,能减轻运输工装的重量,并在内孔中间设置连接梁,确保运输工装的整体稳定性;
15.2)在底座内设置与吸力桩筒的尺寸相同的支撑筒,既保证了运输工装的刚性,又能确保吸力桩筒稳定地坐落在运输工装上,能满足吸力桩导管架基础在直立状态下的落驳运输要求;
16.3)在底座上连接加长横梁,增加运输工装与模块运输车的接触面积,使吸力式导管架基础的整体重量分布地落在模块运输车上,避免集中载荷。
附图说明
17.图1是本实用新型的用于吸力桩导管架基础的运输工装的透视图;
18.图2是本实用新型的用于吸力桩导管架基础的运输工装的平面图;
19.图3是图2的侧视图;
20.图4是本实用新型的运输工装中底座的平面图;
21.图5是本实用新型的运输工装中支墩的结构示意图;
22.图6是本实用新型的运输工装中加长横梁的结构示意图;
23.图7a是本实用新型的运输工装在运输一个吸力桩筒时的立面图;
24.图7b是本实用新型的运输工装在运输整体吸力桩导管架基础时的平面图;
25.图7c是图7b的侧视图。
具体实施方式
26.下面将结合附图对本实用新型作进一步说明。
27.请参阅图1至图6,本实用新型的用于吸力桩导管架基础的运输工装有三套,分别用于支撑吸力桩导管架基础的三个吸力桩筒;吸力桩筒的外径为10m。
28.每套运输工装包括底座2、八对导向板3、四个支墩4和四根加长横梁5;其中,
29.底座2的外轮廓基本呈矩形且长为10.8m,宽为9m,底座2的厚度为0.8m;底座2的中心开设一个直径小于吸力桩筒的内径的内孔,内孔的直径为8m,该底座2的一对长边的中部为圆心位于底座2的中心且直径大于吸力桩筒的外径的圆弧边,圆弧边的直径为10.8m,该底座2的一对短边为直边,该一对短边的中部各自延伸两根横梁20,横梁20的宽度为1.2m,长度为1.5m,厚度为0.8m,两根横梁20的中心间距为2.9m;底座2包括两块主底板21、支撑筒22和三根连接梁23;两块主底板21通过多块呈射线状均布的主筋板211一上一下平行设置,两块主底板21之间在四个角的位置各自设置横向筋板213和纵向筋板212,两块主底板21之间在四根横梁20的位置设置各自两块纵向筋板200;支撑筒22的外径和壁厚一一对应地与吸力桩筒的外径和壁厚相同,该支撑筒22的高度与主筋板211的高度相同,该支撑筒22与底
座2的内孔同轴地固定在两块主底板21之间,保证运输过程中底座2的刚性;三根连接梁23以呈星号的连接方式跨接在底座2的内孔的孔壁之间,确保底座2的整体稳定性;连接梁23的宽度为0.6m,厚度为0.8m,连接梁23包括两块连接梁底板230、多块连接在两块连接梁底板230之间的横向筋板231和一块连接在两块连接梁底板230之间的纵向筋板232;底座2上还在一对圆弧边的两头各自设置一个吊耳板24;
30.八对导向板3固定在底座2的顶面上并沿一个直径与吸力桩筒11的外径相同的圆上均布布置;每块导向板3包括一块弧形挡板和一块连接在弧形挡板的外侧面中部的支撑板;弧形挡板的内侧面与吸力桩筒的外壁面贴合;
31.四个支墩4一一对应地通过螺栓安装在底座2的一对短边的两个角部的底面上;每个支墩4包括上墩底板41、下墩底板42、三块连接在上墩底板41和下墩底板42之间的横向筋板43以及两块连接在上墩底板41和下墩底板42之间的纵向筋板44;上墩底板41上对应底座2的底面上的螺纹孔开设安装孔;
32.四根加长横梁5一一对应地连接在底座2的四根横梁20的外端面上;每根加长横梁5的宽度为1.2m,长度为5.3m,厚度为0.8m;加长横梁5包括两块横梁底板51、若干块连接在两块横梁底板51之间的横向筋板52和一块连接在两块横梁底板51之间的纵向筋板53。
33.本实用新型的用于吸力桩导管架基础的运输工装,根据吸力桩导管架基础特点设计,考虑到吸力式导管架建造完成后,采用竖直方式运输,即吸力桩筒11的底面与运输工装直接接触。为了使吸力桩筒的筒壁的结构强度满足要求,需要保证吸力桩筒的底面与运输工装的接触面比率为100%。
34.吸力桩导管架采用自行式模块运输车spmt滚装上船的方式,因此运输工装的设计需考虑自行式模块运输车spmt的布置方式,运输工装设计还需考虑载运船舶的甲板尺寸。
35.本实用新型的用于吸力桩导管架基础的运输工装,在导管架12与三个吸力筒桩11拼装时就能使用,包括以下步骤:
36.1、三套运输工装200的底座2上都不连接加长横梁5;用履带吊将吸力桩筒11吊起,通过运输工装200的底座2上的八对导向板3精准地放置于底座2的顶面上,使吸力桩筒11的底面与底座2顶面的接触面比率为100%(见图7a);
37.2、在总拼装区域的地上划定导管架12的中心位置和三根吸力桩筒11的中心位置,先通过模块运输车依次转运三根已各自放在一个底座2上的吸力桩筒11至悬臂吊下方的总拼装区域,接着将已组焊好的导管架12+过渡段13用模块运输车运到悬臂吊和溜尾吊之间,再用悬臂吊和溜尾吊将导管架+过渡段由躺卧状态吊装至直立状态,并提升到一定高度,然后利用模块运输车将三根吸力桩筒11运到导管架12的下方,并一一对应地找正三根吸力桩筒11的地样位置,悬臂吊将导管架+过渡段下落,调整模块运输车300的位置,使导管架12的三根主管与吸力桩筒11对正,总组装完成。
38.3、吸力桩导管架基础100总体运输前,把三套运输工装200的加长横梁5与底座2上的横梁20连接好,以增加运输工装200与模块运输车300的接触面积,使吸力式导管架基础200的整体重量分布地落在模块运输车300上,避免集中载荷(见图7b和图7c)。
39.以上实施例仅供说明本实用新型之用,而非对本实用新型的限制,有关技术领域的技术人员,在不脱离本实用新型的精神和范围的情况下,还可以作出各种变换或变型,因此所有等同的技术方案也应该属于本实用新型的范畴,应由各权利要求所限定。