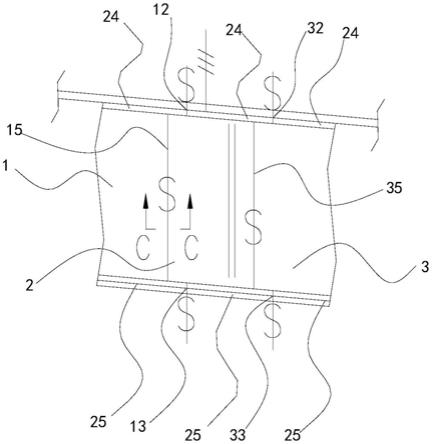
1.本实用新型涉及船舶建造技术领域,特别是涉及一种舭龙骨结构。
背景技术:
2.舭龙骨是一种沿船长方向设置于船舶舭部转圆区域的一种纵向结构,目的是增加船舶横摇时的阻尼,减轻横摇程度提高船舶稳定性与适航性。
3.建造舭龙骨时,一般是将舭龙骨结构沿船长方向按所在分段的长度分为若干段,每一段舭龙骨结构在船舶分段建造阶段安装于分度舭部相应位置,当船舶分段上船台合拢时,舭龙骨随分段进行合拢对接。但是由于舭龙骨依附在船体舭部外板处,当船体外板进行合拢时会阻碍舭龙骨附近外板焊接合拢环缝,同时舭龙骨在分段安装阶段会存在一定焊接变形,到舭龙骨随分段进入船台合拢阶段,相邻分段舭龙骨的合拢断口往往难以对齐,且存在一定间隙差的情况,影响舭龙骨的合拢安装。
技术实现要素:
4.本实用新型要解决的技术问题是提供一种既保留舭龙骨结构在分段安装时的优势,又不影响其焊接施工的舭龙骨结构及其施工方法。
5.为了解决上述技术问题,本实用新型提供了一种舭龙骨结构,包括沿船长方向设置的上腹板、下腹板、上垫板、下垫板、圆管,所述上腹板的内侧通过所述上垫板与船体外板光滑连接,所述下腹板的内侧通过所述下垫板与船体外板光滑连接,所述上腹板的外侧与所述下腹板的外侧通过所述圆管固定连接,所述上腹板、所述下腹板和所述船体外板共同形成三角形结构,所述舭龙骨结构包括依次连接的第一分段、嵌补段和第二分段,所述嵌补段横跨相邻的船体外板的连接处;
6.所述嵌补段的上垫板与所述第一分段的上垫板连接处为第一上垫板连接处,所述嵌补段的上垫板与所述第二分段的上垫板的连接处为第二上垫板连接处;
7.所述嵌补段的下垫板与所述第一分段的下垫板的连接处为第一下垫板连接处,所述嵌补段的下垫板与所述第二分段的下垫板的连接处为第二下垫板连接处;
8.所述嵌补段的圆管与所述第一分段的圆管的连接处为第一圆管连接处,所述嵌补段的圆管与所述第二分段的圆管的连接处为第二圆管连接处;
9.所述第一上垫板连接处、所述第一下垫板连接处和所述第一圆管连接处两两位置对应;所述第二上垫板连接处、所述第二下垫板连接处和所述第二圆管连接处两两位置对应。
10.作为本实用新型的优选方案,所述嵌补段的上腹板与所述第一分段的上腹板的连接处为第一上腹板连接处,所述嵌补段的上腹板与所述第二分段的上腹板的连接处为第二上腹板连接处;
11.所述嵌补段的下腹板与所述第一分段的下腹板的连接处为第一下腹板连接处,所述嵌补段的下腹板与所述第二分段的下腹板的连接处为第二下腹板连接处;
12.所述第一上腹板连接处和所述第一下腹板连接处交错设置,所述第二上腹板连接处和所述第二下腹板连接处交错设置。
13.作为本实用新型的优选方案,所述第一上腹板连接处和所述第一下腹板连接处分别与所述第一圆管连接处交错设置,所述第二上腹板连接处和所述第二下腹板连接处分别所述第二圆管连接处交错设置。
14.作为本实用新型的优选方案,还包括分别与所述上腹板和所述下腹板垂直连接的加强肘板,所述加强肘板通过塞焊钢质衬垫与所述上腹板连接。
15.本实用新型还提供了该舭龙骨结构的施工方法,包括以下步骤:
16.步骤一:将所述第一分段和所述第二分段分别安装在相邻的船体外板上,所述第一分段和所述第二分段之间设有用于安装所述嵌补段的嵌补区,相邻的船体外板的连接处设于所述嵌补区内;
17.步骤二:将所述嵌补段的上垫板和下垫板安装于所述嵌补区:首先将所述嵌补段的上垫板的上下两侧分别与船体外板进行点焊定位,然后将所述嵌补段的上垫板分别与所述第一分段的上垫板和所述第二分段的上垫板进行对接焊,最后对所述嵌补段的上垫板的上下两侧的边缘与船体外板进行角焊接,完成所述嵌补段的上垫板的安装;同理,完成所述嵌补段的下垫板的安装;
18.步骤三:将所述嵌补段的下腹板、圆管和加强肘板制作成下腹板部件:首先所述将嵌补段的圆管焊接在所述嵌补段的下腹板的外侧,其中所述嵌补段的下腹板的顶面与所述嵌补段的圆管的圆心对齐,然后在所述加强肘板的顶部安装用作后续安装所述嵌补段的上腹板塞焊时的钢衬垫,最后将安装完扁钢的所述加强肘板焊接安装在所述嵌补段的下腹板上;
19.步骤四:将所述下腹板部件安装于所述嵌补区:以所述嵌补段的下垫板的中心线为安装线,在所述嵌补段的下腹板的内侧边缘与所述嵌补段的下垫板的角接处进行点焊;将所述嵌补段的下腹板分别与所述第一分段的下腹板和所述第二分段的下腹板进行对接焊;将所述嵌补段的圆管分别与所述第一分段的圆管和所述第二分段的圆管进行对接焊;将所述嵌补段的下腹板与所述嵌补段的下垫板进行角接焊;将所述嵌补段的圆管分别与所述第一分段的下腹板和所述第二分段的下腹板进行角接焊;
20.步骤五:将所述嵌补段的上腹板安装于所述嵌补区:在所述嵌补段的上腹板与所述加强肘板的位置对应处开设若干个塞焊孔;以所述嵌补段的上垫板的中心线为安装线,将所述嵌补段的上腹板的内侧与嵌补段的上垫板进行点焊定位,将所述嵌补段的上腹板的外侧与所述嵌补段的圆管进行点焊定位;将所述嵌补段的上腹板分别与所述第一分段的上腹板和所述第二分段的上腹板进行对接焊;将所述嵌补段的上腹板与所述嵌补段的上垫板进行角接焊;将所述嵌补段的上腹板与所述嵌补段的圆管进行角接焊;将所述嵌补段的上腹板与所述加强肘板进行塞焊。
21.作为本实用新型的优选方案,在步骤二中,所述嵌补段的上垫板分别与所述第一分段的上垫板和所述第二分段的上垫板的对接焊采用 co2半自动气体保护焊进行单面焊,其焊缝处开朝上的焊接坡口,焊缝处下方贴薄铜质衬垫。
22.作为本实用新型的优选方案,在步骤四中,所述嵌补段的下腹板分别与所述第一分段的下腹板和所述第二分段的下腹板的对接焊采用co2半自动气体保护焊进行单面焊,
其焊缝处开朝上的焊接坡口,焊缝处下方贴陶质衬垫。
23.作为本实用新型的优选方案,在步骤五中,所述嵌补段的上腹板分别与所述第一分段的上腹板和所述第二分段的上腹板的对接焊采用 co2半自动气体保护焊进行单面焊,其焊缝处开朝上的焊接坡口,焊缝处下方为对接焊钢质衬垫;所述嵌补段的上腹板与所述嵌补段的上垫板的角接焊采用采用co2半自动气体保护焊进行单面焊,其焊缝处开朝上的焊接坡口,焊缝处下方为角接钢质衬垫。
24.作为本实用新型的优选方案,在步骤五前,先安装所述对接焊钢质衬垫和所述角接焊钢质衬垫:分别在第一分段和第二分段的上腹板靠近嵌补区的一端角焊接对接焊钢质衬垫;在嵌补段的上垫板的外侧角接焊角接焊钢质衬垫。
25.实施本实用新型的一种舭龙骨结构及其施工方法与现有技术相比,其有益效果在于:通过将舭龙骨合理增加断缝,将舭龙骨划分为第一分段、嵌补段和第二分段,先分别安装舭龙骨的第一分段和第二分段,舭龙骨的嵌补段在分段安装时暂缓安装,当船台阶段舭龙骨附近的外板合拢环缝焊接完成后,再安装嵌补段;通过设置舭龙骨嵌补段,既保留舭龙骨结构在分段安装优势,又不影响其焊接施工;通过舭龙骨嵌补段作为过渡连接区,消除舭龙骨在分段阶段焊接变形对舭龙骨断口合拢影响情况;通过结构端缝的交错设置,提高了舭龙骨结构的整体强度;通过合理的安装方法及焊接顺序,降低了舭龙骨嵌补段结构安装时的焊接变形影响。
附图说明
26.图1为本实用新型实施例的舭龙骨嵌补段横剖面图;
27.图2为本实用新型实施例的图1中的a向视图,为下腹板断缝示意图;
28.图3为本实用新型实施例的图1中的b向视图,为上腹板断缝示意图;
29.图4为本实用新型实施例的图2中的c
‑
c向剖视图,为陶质衬垫焊单面焊示意图;
30.图5为本实用新型实施例的图3中的d
‑
d向剖视图,为对接钢衬垫、塞焊钢衬垫安装位置示意图;
31.图6为本实用新型实施例的图3中的e
‑
e向剖视图,为角接钢衬垫安装位置示意图;
32.图7为本实用新型实施例的图3中的f向放大详图,为塞焊孔示意图;
33.图中,1、第一分段;11、第一上垫板连接处;12、第一下垫板连接处;13、第一圆管连接处;14、第一上腹板连接处;15、第一下腹板连接处;2、嵌补段;21、上腹板;211、塞焊孔;22、下腹板;23、上垫板;24、下垫板;25、圆管;26、加强肘板;3、第二分段;31、第二上垫板连接处;32、第二下垫板连接处;33、第二圆管连接处; 34、第二上腹板连接处;35、第二下腹板连接处;4、扁钢;5、对接焊钢质衬垫;6、角接焊钢质衬垫;7、陶质衬垫;8、船体外板。
具体实施方式
34.下面结合附图和实施例,对本实用新型的具体实施方式作进一步详细描述。以下实施例用于说明本实用新型,但不用来限制本实用新型的范围。
35.在本实用新型的描述中,应当理解的是,本实用新型中采用术语“中心”、“纵向”、“横向”、“上”、“下”、“前”、“后”、“左”、“右”、“竖直”、“水平”、“顶”、“底”“内”、“外”等指示的方位或位置关系为基于附图所示的方位或位置关系,仅是为了便于描述本实用新型和简化
描述,而不是指示或暗示所指的装置或元件必须具有特定的方位、以特定的方位构造和操作,因此不能理解为对本实用新型的限制。此外,术语“第一”、“第二”、“第三”仅用于描述目的,而不能理解为指示或暗示相对重要性。
36.如图1~7所示,本实用新型实施例优选实施例的本实用新型提供了一种舭龙骨结构,包括沿船长方向设置的上腹板21、下腹板22、上垫板23、下垫板24、圆管25,上腹板21的内侧(本实用新型中内侧为靠近船体外板8的一侧,外侧为原理船体外板8的一侧)通过上垫板23与船体外板8光滑连接,下腹板22的内侧通过下垫板24与船体外板8光滑连接,上腹板21的外侧与下腹板22的外侧通过圆管25固定连接,上腹板21、下腹板22和船体外板8共同形成三角形结构,舭龙骨结构包括依次连接的第一分段1、嵌补段2和第二分段3,嵌补段 2横跨相邻的船体外板8的连接处;嵌补段2的上垫板23与第一分段 1的上垫板23连接处为第一上垫板连接处11,嵌补段2的上垫板23 与第二分段3的上垫板23的连接处为第二上垫板连接处31;嵌补段2 的下垫板24与第一分段1的下垫板24的连接处为第一下垫板连接处 12,嵌补段2的下垫板24与第二分段3的下垫板24的连接处为第二下垫板连接处32;嵌补段2的圆管25与第一分段1的圆管25的连接处为第一圆管连接处13,嵌补段2的圆管25与第二分段3的圆管25 的连接处为第二圆管连接处33;第一上垫板连接处11、第一下垫板连接处12和第一圆管连接处13两两位置对应;第二上垫板连接处31、第二下垫板连接处32和第二圆管连接处33两两位置对应,通过将舭龙骨合理增加断缝,将舭龙骨划分为第一分段1、嵌补段2和第二分段 3,先分别安装舭龙骨的第一分段1和第二分段3,舭龙骨的嵌补段2 在分段安装时暂缓安装,当船台阶段舭龙骨附近的外板合拢环缝焊接完成后,再安装嵌补段2;通过设置舭龙骨嵌补段2,既保留舭龙骨结构在分段安装优势,又不影响其焊接施工;通过舭龙骨嵌补段2作为过渡连接区,消除舭龙骨在分段阶段焊接变形对舭龙骨断口合拢影响情况。
37.示例性的,嵌补段2的上腹板21与第一分段1的上腹板21的连接处为第一上腹板连接处14,嵌补段2的上腹板21与第二分段3的上腹板21的连接处为第二上腹板连接处34;嵌补段2的下腹板22与第一分段1的下腹板22的连接处为第一下腹板连接处15,嵌补段2的下腹板22与第二分段3的下腹板22的连接处为第二下腹板连接处35;第一上腹板连接处14和第一下腹板连接处15交错设置,第二上腹板连接处34和第二下腹板连接处35交错设置,第一上腹板连接处14和第一下腹板连接处15分别与第一圆管连接处13交错设置,第二上腹板连接处34和第二下腹板连接处35分别第二圆管连接处33交错设置,通过结构端缝的交错设置,提高了舭龙骨结构的整体强度。
38.示例性的,本实施例还包括分别与上腹板21和下腹板22垂直连接的加强肘板26,加强肘板26通过塞焊钢质衬垫与上腹板21连接,加强肘板26的设置加强舭龙骨的结构强度。
39.基于上面各项内容的舭龙骨结构,其施工方法包括以下步骤:
40.步骤一:将第一分段1和第二分段3分别安装在相邻的船体外板8 上,第一分段1和第二分段3之间设有用于安装嵌补段2的嵌补区,相邻的船体外板8的连接处设于嵌补区内;
41.步骤二:将嵌补段2的上垫板23和下垫板24安装于嵌补区:首先将嵌补段2的上垫板23的上下两侧分别与船体外板8进行点焊定位,然后将嵌补段2的上垫板23分别与第一分段1的上垫板23和第二分段3的上垫板23进行对接焊,最后对嵌补段2的上垫板23的上下两侧的边缘与船体外板8进行角焊接,其焊脚高度与垫板厚度一致,完成嵌补段2的上垫板23
的安装;同理,完成嵌补段2的下垫板24的安装;
42.步骤三:将嵌补段2的下腹板22、圆管25和加强肘板26制作成下腹板22部件:首先将嵌补段2的圆管25焊接在嵌补段2的下腹板 22的外侧,采用角接双面焊,其中嵌补段2的下腹板22的顶面与嵌补段2的圆管25的圆心对齐,然后在加强肘板26的顶部安装用作后续安装嵌补段2的上腹板21塞焊时的钢衬垫,最后将安装完扁钢4的加强肘板26焊接安装在嵌补段2的下腹板22上;
43.步骤四:将下腹板22部件安装于嵌补区:以嵌补段2的下垫板24 的中心线为安装线,在嵌补段2的下腹板22的内侧边缘与嵌补段2的下垫板24的角接处进行点焊;将嵌补段2的下腹板22分别与第一分段1的下腹板22和第二分段3的下腹板22进行对接焊;将嵌补段2 的圆管25分别与第一分段1的圆管25和第二分段3的圆管25进行对接焊,采用单面焊,圆管25开对接坡口;将嵌补段2的下腹板22与嵌补段2的下垫板24进行角接焊,采用双面填角焊;将嵌补段2的圆管25分别与第一分段1的下腹板22和第二分段3的下腹板22进行角接焊,采用双面填角焊;
44.步骤五:将嵌补段2的上腹板21安装于嵌补区:在嵌补段2的上腹板21与加强肘板26的位置对应处开设若干个塞焊孔211,塞焊孔 211长度不小于75mm,宽度不小于上腹板21板厚的2倍,塞焊孔211 孔边间距一般为2~3倍的塞焊孔211长度,但不必大于250mm;以嵌补段2的上垫板23的中心线为安装线,将嵌补段2的上腹板21的内侧与嵌补段2的上垫板23进行点焊定位,将嵌补段2的上腹板21的外侧与嵌补段2的圆管25进行点焊定位;将嵌补段2的上腹板21分别与第一分段1的上腹板21和第二分段3的上腹板21进行对接焊;将嵌补段2的上腹板21与嵌补段2的上垫板23进行角接焊;将嵌补段2的上腹板21与嵌补段2的圆管25进行角接焊;将嵌补段2的上腹板21与加强肘板26进行塞焊,将步骤三中所述的扁钢4与嵌补段2 上腹板21进行角接焊。
45.以上步骤通过合理的安装方法及焊接顺序,降低了舭龙骨嵌补段2 结构安装时的焊接变形影响,采用不同的焊接方式,连接结构牢固。
46.示例性的,嵌补段2的上垫板23分别与第一分段1的上垫板23 和第二分段3的上垫板23的对接焊采用co2半自动气体保护焊进行单面焊,其焊缝处开朝上的焊接坡口,焊缝处下方贴薄铜质衬垫。
47.示例性的,在步骤四中,嵌补段2的下腹板22分别与第一分段1 的下腹板22和第二分段3的下腹板22的对接焊采用co2半自动气体保护焊进行单面焊,其焊缝处开朝上的焊接坡口,焊缝处下方贴陶质衬垫7。
48.示例性的,在步骤五中,嵌补段2的上腹板21分别与第一分段1 的上腹板21和第二分段3的上腹板21的对接焊采用co2半自动气体保护焊进行单面焊,其焊缝处开朝上的焊接坡口,焊缝处下方为对接焊钢质衬垫5;嵌补段2的上腹板21与嵌补段2的上垫板23的角接焊采用采用co2半自动气体保护焊进行单面焊,其焊缝处开朝上的焊接坡口,焊缝处下方为角接钢质衬垫。
49.示例性的,在步骤五前,先安装对接焊钢质衬垫5和角接焊钢质衬垫6:分别在第一分段1和第二分段3的上腹板21靠近嵌补区的一端角焊接对接焊钢质衬垫5;在嵌补段2的上垫板23的外侧角接焊角接焊钢质衬垫6,预先安装对接焊钢质衬垫5和角接焊钢质衬垫6,便于其焊接施工。
50.以上所述仅是本实用新型的优选实施方式,应当指出,对于本技术领域的普通技术人员来说,在不脱离本实用新型技术原理的前提下,还可以做出若干改进和替换,这些改进和替换也应视为本实用新型的保护范围。