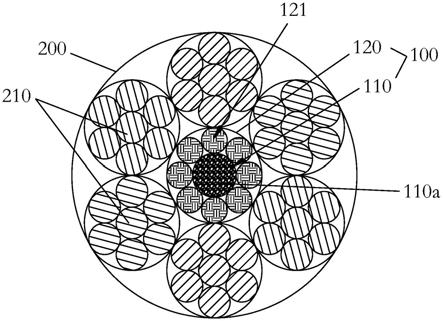
1.本实用新型涉及钢丝绳技术领域,尤其涉及一种超高分子钢丝绳。
背景技术:
2.钢丝绳是多根钢丝按照一定的规则捻制在一起的螺旋状钢丝束,在搬运机械中,钢丝绳用于供提升、牵引、拉紧和承载等用途。
3.现有高分子纤维绳缆,通过聚酯防护层包裹住高分子纤维材质的绳芯,虽然对绳芯起到了很好的保护,但是使绳缆失去了绳芯存储润润滑剂的功能,绳缆的润滑效果差,使用寿命短。
技术实现要素:
4.为克服现有技术的不足,本实用新型提供了一种超高分子钢丝绳,用于解决现有技术中高分子纤维绳缆润滑效果差和使用寿命短的问题。
5.为达上述目的,本实用新型提供的一种超高分子钢丝绳,包括绳芯及包覆在所述绳芯外的绳股层;
6.所述绳芯包括内芯层及超高分子量聚乙烯纤维层,其中,所述内芯层沿周向设置有环体,所述环体位于所述内芯层的外圆柱面上,所述超高分子量聚乙烯纤维层包覆在所述内芯层外。
7.优选的,所述环体包括多个凸环,且多个所述凸环沿所述内芯层的轴线方向分布。
8.优选的,相邻的两个所述凸环之间间隔预设距离。
9.优选的,所述环体为螺旋凸起,所述螺旋凸起沿所述内芯层的轴线方向延伸。
10.优选的,所述内芯层为橡胶棒体,所述橡胶棒体的外圆柱面设置有所述环体。
11.优选的,所述内芯层包括股芯及护套,所述护套套设于所述股芯上,所述护套的外圆柱面设置有所述环体。
12.优选的,所述内芯层还包括螺旋体,所述螺旋体嵌设于所述护套内,以使所述护套的外圆柱面形成所述环体,所述螺旋体的两端分别沿所述护套的轴线延伸。
13.优选的,所述超高分子量聚乙烯纤维层包括多根超高分子量聚乙烯纤维绳股,多根所述高分子量聚乙烯纤维绳股交错编织于或捻合于所述内芯层外。
14.相比于现有技术,本实用新型的有益效果:
15.本实用新型提供的超高分子钢丝绳,在内芯层外设有超高分子量聚乙烯纤维层,在使用润滑剂对超高分子钢丝绳进行润滑时,润滑挤透过绳股层进入超高分子量聚乙烯纤维层,超高分子量聚乙烯纤维层会存储一定量的润滑剂,使得超高分子钢丝绳在使用过程中保持良好的润滑效果。
16.同时,超高分子钢丝绳使用过程中,绳股层与内芯层之间会对超高分子量聚乙烯纤维层形成挤压,由于内芯层的外圆柱面设置有环体,因此,相对的环体与绳股层之间对超高分子量聚乙烯纤维层的挤压力更大,进而有效阻挡超高分子量聚乙烯纤维层内的润滑剂
沿轴线方向的流动,使得超高分子钢丝绳在使用过程中保持良好的润滑效果,进而延长使用寿命。
附图说明
17.图1是本实用新型提供的一种超高分子钢丝绳的截面结构示意图;
18.图2是本实用新型图1中超高分子钢丝绳中第一种内芯层的局部立体结构示意图;
19.图3是本实用新型图1中超高分子钢丝绳中第二种内芯层的局部立体结构示意图;
20.图4是本实用新型提供的另一种超高分子钢丝绳的截面结构示意图;
21.图5是本实用新型图4中超高分子钢丝绳中内芯层的结构示意图;
22.图6是本实用新型图5中内芯层中一种护套的局部立体结构示意图;
23.图7是本实用新型图5中内芯层中另一种护套的局部立体结构示意图;
24.图8是本实用新型图7中护套的第一种a-a向的剖视图;
25.图9是本实用新型图7中护套的第二种a-a向的剖视图。
具体实施方式
26.下面结合附图对本实用新型所提供的一种超高分子钢丝绳作进一步说明,需要指出的是,下面仅以一种最优化的技术方案对本实用新型的技术方案以及设计原理进行详细阐述。
27.实施例一
28.请参阅图1、图2以及图3,本实施例提供的一种超高分子钢丝绳,超高分子钢丝绳用于提升、牵引、拉紧和承载物体。
29.本实施提供的超高分子钢丝绳,包括绳芯100及包覆在绳芯100外的绳股层200。
30.绳股层200由多根钢丝股210捻合而成,且每根钢丝股210又由多根钢丝捻合而成。
31.在一些实施例中,绳股层200中钢丝股210的数量为6根、8根等其它数量。应当理解的,上述仅是举例说明,不作为本技术保护范围的限制。
32.绳芯100包括内芯层110及超高分子量聚乙烯纤维层120。其中,内芯层110沿周向设置有环体110b,环体110b位于内芯层110的外圆柱面上,超高分子量聚乙烯纤维层120包覆在内芯层110外,环体110b位于内芯层110的外圆柱面与超高分子量聚乙烯纤维层120之间,而超高分子量聚乙烯纤维层120位于内芯层110的外圆柱面与绳股层200之间。
33.可以理解的,超高分子钢丝绳制作完成后,在使用过程中,最外层的绳股层200与内部的内芯层110的外圆柱面形成对超高分子量聚乙烯纤维层120的挤压。
34.优选的,超高分子量聚乙烯纤维层120包括多根超高分子量聚乙烯纤维绳股121,其中,多根高分子量聚乙烯纤维绳股121交错编织于内芯层110外。即超高分子量聚乙烯纤维层120由多根超高分子量聚乙烯纤维绳股121交错编织而成,不易松散,使得绳芯100具有更好的抗拉性能。
35.如图1所示,在本实施例中,多根高分子量聚乙烯纤维绳股121捻合于内芯层110外,即超高分子量聚乙烯纤维层120由多根超高分子量聚乙烯纤维绳股121捻合而成,降低制作难度和成本,使得绳芯100结构更紧凑。
36.优选的,内芯层110为橡胶棒体110a,橡胶棒体110a的外圆柱面设置有环体100b。
采用橡胶棒体110a作为内芯层110,可以使绳芯100保护良好的柔韧性。
37.可优选的是,橡胶棒体110a与环体110b为一体结构。
38.如图2所示,在一些实施例中,环体110b包括多个凸环,且多个凸环沿内芯层110的轴线方向分布,即多个凸环沿橡胶棒体110a的轴线方向分布。
39.可优选的是,多个凸环沿橡胶棒体110a的轴线方向均匀分布。
40.可优选的是,相邻的两个凸环之间间隔预设距离,该预设距离大于等于超高分子钢丝绳直径的2倍。
41.如图3所示,在另一些实施例中,环体110b为螺旋凸起,螺旋凸起沿内芯层110的轴线方向延伸,即螺旋凸起沿橡胶棒体110a的轴线方向延伸。
42.可优选的是,螺旋凸起的螺距大于等于超高分子钢丝绳直径的2倍。
43.还需要说明的,超高分子量聚乙烯(ultra-high molecular weight polyethylene,uhmwpe)是由乙烯、丁二烯单体在催化剂的作用下,聚合而成的分子量150万以上的无支链的线性聚乙烯。其具有超强的耐磨性、自润滑性,强度较高、化学性质稳定、抗老化性能强等性能。
44.本实施例提供的超高分子钢丝绳,在内芯层110外设有超高分子量聚乙烯纤维层120,在使用润滑剂对超高分子钢丝绳进行润滑时,润滑挤透过绳股层200中的钢丝股210进入超高分子量聚乙烯纤维层120,超高分子量聚乙烯纤维层120会存储一定量的润滑剂,使得超高分子钢丝绳在使用过程中保持良好的润滑效果。
45.优选的,超高分子钢丝绳使用过程中,由于绳股层200与内芯层110之间会对超高分子量聚乙烯纤维层120形成挤压,而内芯层110的外圆柱面设置有环体110b,因此,相对的环体110b与绳股层200之间对超高分子量聚乙烯纤维层120的挤压力更大,进而有效阻挡超高分子量聚乙烯纤维层120内的润滑剂沿轴线方向的流动。即超高分子量聚乙烯纤维层120内的润滑剂很难越过凸环或螺旋凸起进行流动,使得润滑剂在超高分子量聚乙烯纤维层120的轴线方向均匀分布,进而避免润滑剂在受热或受挤压时流动聚集,即使得超高分子钢丝绳在使用过程中保持良好的润滑效果,进而延长使用寿命。
46.实施例二
47.请参阅图4至图9,本实施例提供的一种超高分子钢丝绳,超高分子钢丝绳用于提升、牵引、拉紧和承载物体。相比实施例一,区别之处在于:
48.请结合参阅图4和图5,在本实施例中,内芯层110包括股芯112及护套111,护套111套设于股芯112上,护套111的外圆柱面设置有环体110b。
49.股芯112为钢芯,在本实施例中,股芯112是由多根钢丝捻合成型,进而增加绳芯100的抗拉和抗压性能。
50.如图6所示,在一些实施例中,环体110b包括多个凸环,且多个凸环沿护套111的轴线方向分布。
51.可优选的是,多个凸环沿护套111的轴线方向均匀分布。
52.可优选的是,相邻的两个凸环之间间隔预设距离,该预设距离大于等于超高分子钢丝绳直径的2倍。
53.可优选的是,凸环与护套111为一体结构。
54.请结合参阅图7、图8以及图9,在另一些实施例中,如图7和图8所示,环体110b为螺
旋凸起,螺旋凸起沿护套111的轴线方向延伸。
55.可优选的是,螺旋凸起的螺距大于等于超高分子钢丝绳直径的2倍。
56.可优选的是,螺旋凸起与护套111为一体结构。
57.在又一实施例中,请结合参阅图7和图9,内芯层110还包括螺旋体113,螺旋体113嵌设于护套111内,以使得护套111的外圆柱面形成环体110b。螺旋体113的两端分别沿护套111的轴线延伸。也即是说,环体110b由内嵌在护套111内的螺旋体113形成,因此,螺旋凸起与螺旋体113的螺距相同。
58.可优选的是,螺旋体113为钢材质,例如弹簧钢。应当理解的,上述仅是举例说明,不作为本技术保护范围的限制。
59.螺旋体113的设置一方面增强了绳芯100的抗弯和抗拉性能,进而提升超高分子钢丝绳整体的抗弯和抗拉性能。
60.另外,本实施例提供的超高分子钢丝绳,在内芯层110中的护套111上设有环体110b,因此,本实施例也具有同上述实施例一同样的优点。
61.以上仅是本实用新型的优选实施方式,应当指出的是,上述优选实施方式不应视为对本实用新型的限制,本实用新型的保护范围应当以权利要求所限定的范围为准。对于本技术领域的普通技术人员来说,在不脱离本实用新型的精神和范围内,还可以做出若干改进和润饰,这些改进和润饰也应视为本实用新型的保护范围。