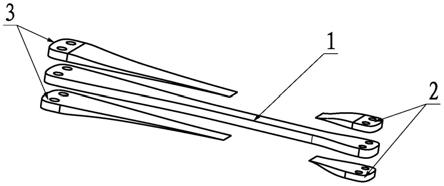
1.本发明属于无轴承旋翼柔性梁设计技术领域,公开了一种用于无轴承旋翼的多基体复合材料柔性梁。
背景技术:
2.对无轴承旋翼而言,需要通过柔性梁的挥舞、摆振和扭转变形来取代铰接式旋翼的挥舞铰、摆振铰和变距铰,根据这一特点,柔性梁从功能上由能实现桨叶的挥舞、摆振和扭转变形的变形段构成。通常,挥舞和摆振变形段在靠近柔性梁根部的位置,扭转变形段稍靠后,这样的布局可以减缓柔性梁承受载荷的严酷程度,提高柔性梁的寿命。
3.目前,国内外无轴承旋翼柔性梁变形区的设计大多是通过对柔性梁截面形状的设计来实现的,不同变形区在材料成分及成型方法上没有差别。在挥舞、摆振变形段,柔性梁的厚度尺寸和宽度尺寸沿展向递减,以获得较强的弯曲变形;在扭转变形段,则有各自独特的截面形状,使其在保留较大弯曲刚度的同时减小扭转刚度,从而获得较强的扭转变形,比如h135采用了
“╬”
十字开槽横截面,h145采用了“艹”草头形横截面,bell430采用了“*”星形横截面,科曼奇采用了“h”横截面等。从刚度分布上看,采用这种方法得到的设计结果可以满足柔性梁的功能,获得理想的变形能力,但是,这些复杂形状的截面给柔性梁的成型工艺带来了很大的麻烦,工艺加工难度大,需要通过长时间的工艺摸索才能提高工艺水平。
技术实现要素:
4.为了推进无轴承旋翼技术发展,研制出工艺性好,满足使用功能的长寿命复合材料柔性梁,本发明提出一种用于无轴承旋翼的多基体复合材料柔性梁,所述柔性梁包括:橡胶基扭转变形层、第一树脂基编织层和第二树脂基编织层;
5.所述橡胶基扭转变形层与桨叶连接一端编织有第一树脂基编织层;
6.所述橡胶基扭转变形层与桨榖连接一端编织有第二树脂基编织层;
7.第一树脂基编织层厚度沿远离桨叶方向逐渐降低;
8.第二树脂基编织层厚度沿远离桨榖方向逐渐降低;
9.第一树脂基编织层与第二树脂基编织层最小距离不小于柔性梁总长度的1/4。
10.进一步,所述橡胶基扭转变形层为橡胶基底纤维增强缠绕结构,成型方式如下:采用纤维干丝预先缠绕出外轮廓,然后注塑橡胶基体成型。橡胶基扭转变形层具有较小的扭转刚度,通过橡胶基扭转变形层的扭转变形实现无轴承旋翼的变距运动。
11.进一步,所述橡胶基扭转变形层总体厚度一致,以改善其成型工艺性,提高成型质量。
12.进一步,所述柔性梁扭转变形区的橡胶基扭转变形层宽度不变,以保证扭转变形区各剖面扭转刚度一致,从而改善扭转变形区的受载情况。
13.进一步,所述柔性梁桨毂连接区、弯曲变形区和桨叶连接区的橡胶基扭转变形层宽度与树脂基编织层宽度保持一致,由两端向中间逐渐缩小,直至扭转变形区后保持一致。
一方面,可以简化柔性梁成型工艺,另一方面,可以满足柔性梁的不同功能区域的刚度要求,实现柔性梁的功能。
14.进一步,所述第一树脂基编织层和第二树脂基编织层均以橡胶基扭转变形层为芯模,采用纤维干丝预先编织出各自外轮廓,然后分别注塑树脂基固化成型。第一树脂基编织层和第二树脂基编织层以橡胶基扭转变形层为芯模进行编织,以提高树脂基编织层与橡胶基扭转变形层之间的层间剪切性能。
15.进一步,第二树脂基编织层长度大于第一树脂基编织层长度。第一树脂基编织层处于柔性梁桨叶连接区,此区间与桨叶根部连接,长度较短;第二树脂基编织层处于柔性梁桨毂连接区和弯曲变形区,弯曲变形区需要一定的长度来实现柔性梁的刚度过渡,因此第二树脂基编织层长度较长。
16.进一步,所述柔性梁弦向截面为矩形。所述柔性梁各功能区间的刚度分布变化通过柔性梁宽度、厚度尺寸变化,同时搭配不同基体复合材料来实现,因此弦向截面采用矩形形状,改善成型工艺性,提高柔性梁成型质量。
17.有益效果:
18.本发明的多基体复合材料柔性梁充分利用了复合材料的力学特点,在简化截面形状的前提下,实现柔性梁的弯曲变形和扭转变形,具有良好的工艺性,此外通过编织工艺提高不同基体材料之间的抗剪切能力,进一步提高柔性梁疲劳性能。
附图说明
19.图1为柔性梁功能分区示意图;
20.图2为柔性梁各部分组成示意;
21.其中,1-橡胶基扭转变形层;2-第一树脂基编织层;3-第二树脂基编织层。
具体实施方式
22.下面通过具体实施方式对本发明做进一步说明:
23.本发明提出了一种用于无轴承旋翼的多基体复合材料柔性梁,这种柔性梁弦向截面为矩形,采用了橡胶基复合材料和树脂基复合材料,利用不同基体复合材料的力学性能不同的特点,在简化柔性梁截面形状的前提下,实现柔性梁的弯曲变形和扭转变形。
24.本发明柔性梁功能上包含桨毂连接区、桨叶连接区、弯曲变形区和扭转变形区。其中桨毂连接区和桨叶连接区具有较大的弯曲刚度和扭转刚度,用于提供柔性梁与桨毂、桨叶安装连接的平台;扭转变形区具有较小的扭转刚度,以实现柔性梁的扭转变形,且扭转变形区的扭转刚度沿柔性梁展向不变,以改善柔性梁的扭转受载情况;弯曲变形区具有较高的弯曲刚度和扭转刚度,且靠近桨毂连接区的弯曲刚度和扭转刚度最大,沿梁展向向内逐渐递减,直至与扭转变形区刚度一致,采用此种刚度分布使柔性梁在弯曲载荷的作用下实现弯曲变形。柔性梁功能分区见图1。
25.本发明柔性梁结构上由橡胶基扭转变形层1、第一树脂基编织层2和第二树脂基编织层3构成。橡胶基扭转变形层1具有较小的扭转刚度,同时具有较高的弯曲刚度,其厚度沿展向不变,宽度与柔性梁整体一致,由两端向扭转变形区逐渐递减。橡胶基扭转变形层1分布于柔性梁的桨毂连接区、桨叶连接区、弯曲变形区和扭转变形区。第一树脂基编织层2和
第二树脂基编织层3具有较高的扭转刚度和弯曲刚度,同时具有较好的层间剪切性能,其厚度沿展向变化,宽度与柔性梁整体一致,由两端向扭转变形区逐渐递减。第一树脂基编织层2分布于柔性梁的桨叶连接区,第二树脂基编织层3分布于柔性梁的桨毂连接区和弯曲变形区。柔性梁各部分组件示意见图2。
26.橡胶基扭转变形层1为橡胶基底纤维增强缠绕结构,采用纤维干丝预先缠绕,后注塑橡胶基体固化成型。第一树脂基编织层2和第二树脂基编织层3采用纤维编织后,注塑树脂基体固化成型。为了提高树脂基编织层与橡胶基扭转变形层之间的层间剪切性能,第一树脂基编织层2和第二树脂基编织层3分别以橡胶基扭转变形层1为芯模进行编织,形成一个整体。
27.以上所述,仅为本发明的具体实施例,对本发明进行详细描述,未详尽部分为常规技术。但本发明的保护范围不局限于此,任何熟悉本技术领域的技术人员在本发明揭露的技术范围内,可轻易想到的变化或替换,都应涵盖在本发明的保护范围之内。本发明的保护范围应以所述权利要求的保护范围为准。
技术特征:
1.一种用于无轴承旋翼的多基体复合材料柔性梁,其特征在于:所述柔性梁包括:橡胶基扭转变形层、第一树脂基编织层和第二树脂基编织层;所述橡胶基扭转变形层与桨叶连接一端编织有第一树脂基编织层;所述橡胶基扭转变形层与桨榖连接一端编织有第二树脂基编织层;第一树脂基编织层厚度沿远离桨叶方向逐渐降低;第二树脂基编织层厚度沿远离桨榖方向逐渐降低;第一树脂基编织层与第二树脂基编织层之间最小距离不小于柔性梁总长度的1/4。2.根据权利要求1所述的一种用于无轴承旋翼的多基体复合材料柔性梁,其特征在于:所述橡胶基扭转变形层为橡胶基底纤维增强缠绕结构,成型方式如下:采用纤维干丝预先缠绕出外轮廓,然后注塑橡胶基体固化成型。3.根据权利要求2所述的一种用于无轴承旋翼的多基体复合材料柔性梁,其特征在于:所述橡胶基扭转变形层总体厚度一致。4.根据权利要求3所述的一种用于无轴承旋翼的多基体复合材料柔性梁,其特征在于:所述柔性梁扭转变形区的橡胶基扭转变形层宽度一致。5.根据权利要求4所述的一种用于无轴承旋翼的多基体复合材料柔性梁,其特征在于:所述柔性梁桨毂连接区、弯曲变形区和桨叶连接区的橡胶基扭转变形层宽度与树脂基编织层宽度保持一致,由两端向中间逐渐缩小,直至扭转变形区后保持一致。6.根据权利要求5所述的一种用于无轴承旋翼的多基体复合材料柔性梁,其特征在于:所述第一树脂基编织层和第二树脂基编织层均以橡胶基扭转变形层为芯模,采用纤维干丝预先编织出各自外轮廓,然后分别注塑树脂基固化成型。7.根据权利要求6所述的一种用于无轴承旋翼的多基体复合材料柔性梁,其特征在于:第二树脂基编织层长度大于第一树脂基编织层长度。8.根据权利要求7所述的一种用于无轴承旋翼的多基体复合材料柔性梁,其特征在于:所述柔性梁弦向截面为矩形。
技术总结
本申请属于无轴承旋翼柔性梁设计技术领域,公开了一种用于无轴承旋翼的多基体复合材料柔性梁,包括:橡胶基扭转变形层、第一树脂基编织层和第二树脂基编织层;橡胶基扭转变形层与桨叶连接一端编织有第一树脂基编织层;橡胶基扭转变形层与桨榖连接一端编织有第二树脂基编织层;第一树脂基编织层厚度沿远离桨叶方向逐渐降低;第二树脂基编织层厚度沿远离桨榖方向逐渐降低;第一树脂基编织层与第二树脂基编织层之间最小距离不小于柔性梁总长度的1/4。橡胶基扭转变形层为橡胶基底纤维增强缠绕结构,成型方式如下:采用纤维干丝预先缠绕出外轮廓,然后注塑橡胶基体固化成型。然后注塑橡胶基体固化成型。然后注塑橡胶基体固化成型。
技术研发人员:江嘉吉 熊绍海 汪亚敏 李伟 袁翔 唐心凯
受保护的技术使用者:中国直升机设计研究所
技术研发日:2021.10.09
技术公布日:2022/1/21