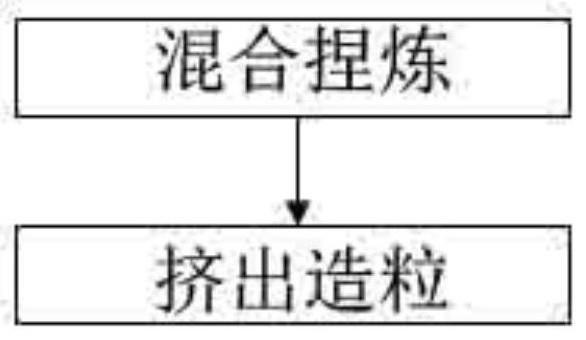
1.本发明涉及一种低烟无卤阻燃聚烯烃护套料及其制备方法,属高分子材料技术领域。
背景技术:
2.目前电路护套材料,是确保电缆绝缘性、阻燃性的重要材料,当前所使用的低烟无卤阻燃聚烯烃护套料往往均采用了传统的在高分子聚烯烃材料总混合诸如氢氧化铝、氢氧化镁等无机物填料混合而制备得到,虽然可以一定程度达到绝缘阻燃作业的需要,但生产成本较高,绝缘、阻燃性能单一,同时也导致护套材料的弹性形变能力、结构强度、韧性、耐磨性均相对较低,且材料整体重量相对较大,从而影响了电力线缆的整体性能,并为电力线缆运行留下了较大的安全隐患。
3.因此针对这一问题,迫切需要开发一种低烟无卤阻燃聚烯烃护套料及其制备方法,以满足实际使用的需要。
技术实现要素:
4.为了解决现有技术上的不足,本发明提供一种低烟无卤阻燃聚烯烃护套料及其制备方法。
5.一种低烟无卤阻燃聚烯烃护套料,由以下重量份数组分构成:碳纳米管8%—15.3%、碳化硅3%—5.6%、氢氧化铝3%—6.5%、 空心玻璃微波0%—3.5%、乙烯基硅烷1.1%—3.5%、增容剂0.5%—1.3%、偶联剂0.1%—1.5%、稳定剂0.5%—2.1%、脂环烃类溶剂3.5%—12.1%,余量为聚烯烃弹性体树脂。
6.进一步的,所述的碳化硅、二硫化钼粉及聚醚醚酮微粉粒径均不大于10—50纳米,空心玻璃微波粒径为30—50微米;。
7.一种低烟无卤阻燃聚烯烃护套料的制备方法,包括如下步骤:s1,混合捏炼,首先将碳纳米管、碳化硅、氢氧化铝、 空心玻璃微波、尼龙纤维、乙烯基硅烷、增容剂、偶联剂、稳定剂、脂环烃类溶剂及聚烯烃弹性体树脂一同添加到体积为以上各组分总体积0.8—2.5倍的去离子水中,并在捏炼设备对混合物机械搅拌混合均匀,然后对混合均匀后的混合液进行超声波均质,并在超声波均质过程中,将混合液温度匀速提升至80℃—120℃,将捏炼设备内气压降低至0.1—0.5倍标准大气压,超声波均质至混合液中含水量不大于50%后,通过捏炼设备对混合液在110℃—260℃环境下持续捏炼作业,并在完成捏炼后使混合物含水另为0,并保持捏炼状态备用;s2, 挤出造粒,在完成s1步骤后,将s1步骤中制备的捏炼物添加至挤出设备中,进行挤出造粒作业,得到粒径为1—20毫米的颗粒物料。
8.进一步的,所述s1步骤中捏炼设备包括承载机架、螺杆挤出机、捏炼机、混合搅拌罐、物料输送管及驱动电路,所述承载机架为轴线与水平面垂直分布的柱状框架结构,所述捏炼机嵌于承载机架内并与承载机架同轴分布,且捏炼机下端面通过物料输送管与1—4个
螺杆挤出机连通,上端面通过物料输送管与2—6个混合搅拌罐连通,其中所述捏炼机、混合搅拌罐与承载机架内侧面间通过滑槽滑动连接,所述螺杆挤出机轴线与承载机架底部呈0
°
—45
°
夹角,且每个螺杆挤出机均通过1—2个升降驱动机构与承载机架底部连接,且所述升降驱动机构分别与螺杆挤出机及承载机架铰接,并与螺杆挤出机轴线呈30
°
—90
°
夹角,所述驱动电路与承载机架外侧面连接,并分别与螺杆挤出机、捏炼机、混合搅拌罐、物料输送管及升降驱动机构电气连接。
9.进一步的,所述混合搅拌罐包括罐体、负压泵、远红外辐照加热机构、超声波搅拌机构、超声波均质机构、温湿度传感器、气压传感器,所述罐体为鼓型腔体结构,其上端面设一个加料口和一个排气口,下端面设一个排料口,所述加料口、排气口及排料口均设一个控制阀,所述排气口通过控制阀与负压泵连通,排料口通过控制阀与物料输送管连通,所述负压泵与承载机架外侧面连接,所述远红外辐照加热机构至少两个,位于罐体内并与罐体顶部连接,且两远红外辐照加热机构光轴均与罐体轴线相交并呈10
°
—60
°
夹角,所述超声波搅拌机构、超声波均质机构均至少两个,环绕罐体轴线均布并嵌于罐体侧壁内,且所述超声波搅拌机构、超声波均质机构间间隔分布,与罐体底部间间距不小于罐体高度的10%,所述温湿度传感器、气压传感器均一个,嵌于罐体内并与罐体底部连接,所述负压泵、远红外辐照加热机构、超声波搅拌机构、超声波均质机构、温湿度传感器、气压传感器均与驱动电路电气连接。
10.进一步的,所述物料输送管包括管体、旋转驱动机构、导流套、导流翅板及连接法兰,其中所述管体为圆柱空心管状结构,其上端面及下端面均与一个连接法连连接并同轴分布,所述管体内侧面设至少两个与管体同轴分布的驱动槽,各驱动槽沿管体轴线分布,所述导流套为与管体同轴分布的空心柱状结构,嵌于驱动槽内且其内侧面与管体内侧面平齐分布,外侧面通过旋转驱动机构与驱动槽槽底滑动连接,所述导流套内侧面与2—6个导流翅板连接,所述导流翅板板面与导流套轴线呈20
°
—60
°
夹角并环绕导流套轴线均布,所述导流翅板后端面与导流套内侧面间通过弹性铰链铰接,且导流翅板宽度为管体半径的10%—50%,所述旋转驱动机构与驱动电路电气连接。
11.进一步的,所述的升降驱动机构为液压柱、气压柱中的任意一种。
12.进一步的,所述的驱动电路为基于可编程控制器为基础的电路系统。
13.本发明生产原料成本低廉,来源广泛,生产工艺简单、生产效率高,可有效的降低生产成本及难度的同时,另有效的提高了材料的结构强度、韧性、耐磨性、耐火性绝缘性和弹性形变能力,同时有效的提高了材料的加工塑性能力,降低后续加工成型作业的难度及成本。
附图说明
14.下面结合附图和具体实施方式来详细说明本发明;图1为本发明生产流程示意图;图2为本捏炼设备结构示意图;图3为混合搅拌罐结构示意图;图4为物料输送管结构示意图。。
具体实施方式
15.为使本发明实现的技术手段、创作特征、达成目的与功效易于施工,下面结合具体实施方式,进一步阐述本发明。
16.实施例1如图1所示,一种低烟无卤阻燃聚烯烃护套料,由以下重量份数组分构成:碳纳米管8%、碳化硅3%、氢氧化铝3%、乙烯基硅烷1.1%、增容剂0.5%、偶联剂0.1%、稳定剂0.5%、脂环烃类溶剂3.5%,余量为聚烯烃弹性体树脂。
17.本实施例中,所述的碳化硅、二硫化钼粉及聚醚醚酮微粉粒径均不大于10纳米,空心玻璃微波粒径为30微米;。
18.一种低烟无卤阻燃聚烯烃护套料的制备方法,包括如下步骤:s1,混合捏炼,首先将碳纳米管、碳化硅、氢氧化铝、 空心玻璃微波、尼龙纤维、乙烯基硅烷、增容剂、偶联剂、稳定剂、脂环烃类溶剂及聚烯烃弹性体树脂一同添加到体积为以上各组分总体积0.8倍的去离子水中,并在捏炼设备对混合物机械搅拌混合均匀,然后对混合均匀后的混合液进行超声波均质,并在超声波均质过程中,将混合液温度匀速提升至80℃,将捏炼设备内气压降低至0.1倍标准大气压,超声波均质至混合液中含水量不大于50%后,通过捏炼设备对混合液在110℃环境下持续捏炼作业,并在完成捏炼后使混合物含水另为0,并保持捏炼状态备用;s2, 挤出造粒,在完成s1步骤后,将s1步骤中制备的捏炼物添加至挤出设备中,进行挤出造粒作业,得到粒径为1毫米的颗粒物料。
19.实施例2如图1所示,一种低烟无卤阻燃聚烯烃护套料,由以下重量份数组分构成:碳纳米管15.3%、碳化硅5.6%、氢氧化铝6.5%、 空心玻璃微波3.5%、乙烯基硅烷3.5%、增容剂1.3%、偶联剂1.5%、稳定剂2.1%、脂环烃类溶剂12.1%,余量为聚烯烃弹性体树脂。
20.其中,所述的碳化硅、二硫化钼粉及聚醚醚酮微粉粒径均不大于50纳米,空心玻璃微波粒径为50微米;。
21.一种低烟无卤阻燃聚烯烃护套料的制备方法,包括如下步骤:s1,混合捏炼,首先将碳纳米管、碳化硅、氢氧化铝、 空心玻璃微波、尼龙纤维、乙烯基硅烷、增容剂、偶联剂、稳定剂、脂环烃类溶剂及聚烯烃弹性体树脂一同添加到体积为以上各组分总体积2.5倍的去离子水中,并在捏炼设备对混合物机械搅拌混合均匀,然后对混合均匀后的混合液进行超声波均质,并在超声波均质过程中,将混合液温度匀速提升至120℃,将捏炼设备内气压降低至0.5倍标准大气压,超声波均质至混合液中含水量为30%后,通过捏炼设备对混合液在260℃环境下持续捏炼作业,并在完成捏炼后使混合物含水另为0,并保持捏炼状态备用;s2, 挤出造粒,在完成s1步骤后,将s1步骤中制备的捏炼物添加至挤出设备中,进行挤出造粒作业,得到粒径为20毫米的颗粒物料。
22.实施例3如图1所示,一种低烟无卤阻燃聚烯烃护套料,由以下重量份数组分构成:碳纳米管10.3%、碳化硅3.8%、氢氧化铝4.5%、 空心玻璃微波1.5%、乙烯基硅烷2.1%、增容剂0.9%、偶联剂0.5%、稳定剂1.5%、脂环烃类溶剂8.1%,余量为聚烯烃弹性体树脂。
23.此外,所述的碳化硅、二硫化钼粉及聚醚醚酮微粉粒径均不大于30纳米,空心玻璃微波粒径为40微米;。
24.一种低烟无卤阻燃聚烯烃护套料的制备方法,包括如下步骤:s1,混合捏炼,首先将碳纳米管、碳化硅、氢氧化铝、 空心玻璃微波、尼龙纤维、乙烯基硅烷、增容剂、偶联剂、稳定剂、脂环烃类溶剂及聚烯烃弹性体树脂一同添加到体积为以上各组分总体积1.5倍的去离子水中,并在捏炼设备对混合物机械搅拌混合均匀,然后对混合均匀后的混合液进行超声波均质,并在超声波均质过程中,将混合液温度匀速提升至90℃,将捏炼设备内气压降低至0.3倍标准大气压,超声波均质至混合液中含水量位40%后,通过捏炼设备对混合液在160℃环境下持续捏炼作业,并在完成捏炼后使混合物含水另为0,并保持捏炼状态备用;s2, 挤出造粒,在完成s1步骤后,将s1步骤中制备的捏炼物添加至挤出设备中,进行挤出造粒作业,得到粒径为10毫米的颗粒物料。
25.实施例4如图1所示,一种低烟无卤阻燃聚烯烃护套料,由以下重量份数组分构成:碳纳米管12.5%、碳化硅4.6%、氢氧化铝5.5%、 空心玻璃微波2%、乙烯基硅烷2.1%、增容剂0.8%、偶联剂1.4%、稳定剂1.3%、脂环烃类溶剂6.1%,余量为聚烯烃弹性体树脂。
26.本实施例中,所述的碳化硅、二硫化钼粉及聚醚醚酮微粉粒径均不大于20纳米,空心玻璃微波粒径为45微米;。
27.一种低烟无卤阻燃聚烯烃护套料的制备方法,包括如下步骤:s1,混合捏炼,首先将碳纳米管、碳化硅、氢氧化铝、 空心玻璃微波、尼龙纤维、乙烯基硅烷、增容剂、偶联剂、稳定剂、脂环烃类溶剂及聚烯烃弹性体树脂一同添加到体积为以上各组分总体积1.3倍的去离子水中,并在捏炼设备对混合物机械搅拌混合均匀,然后对混合均匀后的混合液进行超声波均质,并在超声波均质过程中,将混合液温度匀速提升至100℃,将捏炼设备内气压降低至0.3倍标准大气压,超声波均质至混合液中含水量为10%后,通过捏炼设备对混合液在200℃环境下持续捏炼作业,并在完成捏炼后使混合物含水另为0,并保持捏炼状态备用;s2, 挤出造粒,在完成s1步骤后,将s1步骤中制备的捏炼物添加至挤出设备中,进行挤出造粒作业,得到粒径为15毫米的颗粒物料。
28.此外本发明在具体实施中,如图2—4所示,所述s1步骤中捏炼设备包括承载机架1、螺杆挤出机2、捏炼机3、混合搅拌罐4、物料输送管5及驱动电路6,所述承载机架1为轴线与水平面垂直分布的柱状框架结构,所述捏炼机3嵌于承载机架1内并与承载机架1同轴分布,且捏炼机2下端面通过物料输送管5与1—4个螺杆挤出机2连通,上端面通过物料输送管5与2—6个混合搅拌罐4连通,其中所述捏炼机3、混合搅拌罐4与承载机架1内侧面间通过滑槽8滑动连接,所述螺杆挤出机2轴线与承载机架1底部呈0
°
—45
°
夹角,且每个螺杆挤出机2均通过1—2个升降驱动机构7与承载机架1底部连接,且所述升降驱动机构1分别与螺杆挤出机2及承载机架1铰接,并与螺杆挤出机2轴线呈30
°
—90
°
夹角,所述驱动电路6与承载机架1外侧面连接,并分别与螺杆挤出机2、捏炼机3、混合搅拌罐4、物料输送管5及升降驱动机构7电气连接。
29.需要说明的,所述混合搅拌罐4包括罐体41、负压泵42、远红外辐照加热机构43、超
声波搅拌机构44、超声波均质机构45、温湿度传感器46、气压传感器47,所述罐体41为鼓型腔体结构,其上端面设一个加料口411和一个排气口412,下端面设一个排料口413,所述加料口411、排气口412及排料口413均设一个控制阀414,所述排气口412通过控制阀414与负压泵42连通,排料口413通过控制阀414与物料输送管5连通,所述负压泵42与承载机架1外侧面连接,所述远红外辐照加热机构43至少两个,位于罐体41内并与罐体41顶部连接,且两远红外辐照加热机构43光轴均与罐体41轴线相交并呈10
°
—60
°
夹角,所述超声波搅拌机构44、超声波均质机构45均至少两个,环绕罐体41轴线均布并嵌于罐体41侧壁内,且所述超声波搅拌机构44、超声波均质机构45间间隔分布,与罐体41底部间间距不小于罐体41高度的10%,所述温湿度传感器46、气压传感器47均一个,嵌于罐体41内并与罐体41底部连接,所述负压泵42、远红外辐照加热机构43、超声波搅拌机构44、超声波均质机构45、温湿度传感器46、气压传感器47均与驱动电路6电气连接。
30.与此同时,所述物料输送管5包括管体51、旋转驱动机构52、导流套53、导流翅板54及连接法兰55,其中所述管体51为圆柱空心管状结构,其上端面及下端面均与一个连接法55连连接并同轴分布,所述管体51内侧面设至少两个与管体51同轴分布的驱动槽56,各驱动槽56沿管体51轴线分布,所述导流套53为与管体51同轴分布的空心柱状结构,嵌于驱动槽56内且其内侧面与管体51内侧面平齐分布,外侧面通过旋转驱动机构52与驱动槽56槽底滑动连接,所述导流套53内侧面与2—6个导流翅板54连接,所述导流翅板54板面与导流套53轴线呈20
°
—60
°
夹角并环绕导流套53轴线均布,所述导流翅板54后端面与导流套53内侧面间通过弹性铰链铰57接,且导流翅板54宽度为管体51半径的10%—50%,所述旋转驱动机构52与驱动电路6电气连接。
31.进一步优化的,所述的升降驱动机构7为液压柱、气压柱中的任意一种。
32.进一步优化的,所述的驱动电路6为基于可编程控制器为基础的电路系统。
33.本发明生产原料成本低廉,来源广泛,生产工艺简单、生产效率高,可有效的降低生产成本及难度的同时,另有效的提高了材料的结构强度、韧性、耐磨性、耐火性绝缘性和弹性形变能力,同时有效的提高了材料的加工塑性能力,降低后续加工成型作业的难度及成本。
34.以上显示和描述了本发明的基本原理和主要特征和本发明的优点。本行业的技术人员应该了解,本发明不受上述实施例的限制,上述实施例和说明书中描述的只是说明本发明的原理,在不脱离本发明精神和范围的前提下,本发明还会有各种变化和改进,这些变化和改进都落入要求保护的本发明范围内。本发明要求保护范围由所附的权利要求书及其等效物界定。