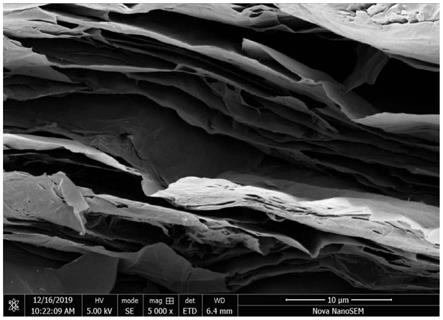
一种墨烯导热膜的制备方法
1.本技术为分案申请,母案的申请号为:202010257865.1,母案的申请日为:2020年04月03日,母案的发明名称为:火焰还原氧化石墨烯膜的方法及石墨烯膜。
技术领域
2.本发明涉及石墨烯膜的制备领域,具体涉及由氧化石墨烯还原的方法。
背景技术:
3.迄今为止,石墨烯导热膜的制备技术中,采用氧化石墨烯定向组装制备成氧化石墨烯膜,再经过热还原最终得到定向排列的石墨烯导热膜,具有很高的导热系数,导热系数≥1000w/m.k,已经广泛应用在手机、电脑等电子产品中。
4.但是由于氧化石墨烯内含氧官能团在热还原时排出大量的气体,形成毛细气体通道,造成氧化石墨烯膜在热还原的过程中厚度膨胀很厚,膨胀后的厚度是氧化石墨烯膜原膜厚度的2.2~3倍的厚度,降低了热处理设备的产能,热处理的能耗高。因此,解决或减少氧化石墨烯膜在热还原过程中厚度膨胀,是迫不及待的具有重大意义的工作。
5.背景技术部分的内容仅仅是发明人所知晓的技术,并不当然代表本领域的现有技术。
技术实现要素:
6.针对现有技术存在问题中的一个或多个,本发明提供一种氧化石墨烯膜的还原方法,对氧化石墨烯膜采用火焰烧制的方法进行还原。
7.根据本发明的一个方面,所述火焰烧制加热的方法具体为:将氧化石墨烯膜从火焰的上面经过,氧化石墨烯膜接触火焰的外焰处。
8.根据本发明的一个方面,所述火焰的外焰处温度为300-600℃。一般情况下,采用天烯气的燃烧火焰,使氧化石墨烯膜中的氧化石墨膜膜体中形成毛细气体通道。
9.优选地,所述火焰的外焰处温度为400
±
50℃。
10.根据本发明的一个方面,所述经过的速度为0.5~5m/min。经过速度过慢,会导致一直加热已经烧过的地方,热量会通过传导的方式传至未被烧过的地方,这样造成未被烧过的地方的变形,导致膜外观不一致不平整;经过速度过快,容易导致就是烧的不完整。经过长期的试验发现,将经过速度控制在0.5~5m/min时,可以有效的保证火焰处理的均匀性,膜外面平整度一致,且形成的毛细气体通道大小一致性高,分布均匀。所述经过的速度为1~2m/min时,效果较佳。
11.本发明还提供了一种石墨烯膜的制备方法,包括:
12.将氧化石墨烯膜采用上述的方法进行火焰还原处理;
13.再进行高温热原还;和
14.再进行压实,得到石墨烯膜。
15.根据本发明的一个方面,所述高温热原还的温度为2000~3000℃。
16.根据本发明的一个方面,所述高温热原还的具体方法为:将还原后的氧化石墨烯膜置于热还原设备中,设备内温度从室温逐渐升至2000~3000℃,升温的速度为2~10℃/min。
17.优选地,热原还设备内温度从室温至600℃采用2℃/min升温速度;进一步优选地,热原还设备内温度从600℃至最终还原温度采用4~5℃/min升温速度。火焰还原处理后,由于氧化石墨烯上还含有大量的含氧的官能团,升温速度过快会导致膜进一步的膨胀。通过反复调整和研究,火陷还原后的氧化石墨烯膜在高温处理时,采用上述分阶段的升温,效率高,成品率高。
18.根据本发明的一个方面,还原后的氧化石墨烯膜在2000~3000℃下恒温处理45-80min。
19.优选地,将多片氧化石墨烯膜叠在一起进行批量石墨化处理;进一步优选的,每相邻相片氧化石墨烯膜之间用石墨纸隔开。
20.根据本发明的一个方面,所述步骤压实采用辊压或者平压,压力≥20mpa。压力优选25~60mpa。
21.根据本发明的一个方面,在氧化石墨烯膜火焰还原处理之后,进行高温热还原之前,对火焰还原的氧化石墨烯膜进行压实处理,所述采用辊压或者平压,压力≥5mpa。压力优选10~15mpa。
22.根据本发明的一个方面,所述氧化石墨烯膜采用氧化石墨烯浆料通过分散、涂覆、干燥、剥离后制得,优选地,所述氧化石墨烯膜的厚度为4~300μm。
23.本发明先采用火焰快速还原,使膜体中形成很多的毛细气体通道,从而使得后续还原时,产生的气体可以沿着形成的毛细气体通道排出,避免了气体积存于膜体中,可有效减少膜厚的增加。
附图说明
24.附图用来提供对本发明的进一步理解,并且构成说明书的一部分,与本发明的实施例一起用于解释本发明,并不构成对本发明的限制。在附图中:
25.图1是本发明方法中氧化石墨烯膜(原料膜)外观照片;
26.图2是实施例1中火焰还原处理后的单层氧化石墨烯膜的样品外观照片;
27.图3是实施例1中石墨烯泡沫膜(高温处理后未压实之前)的样品外观照片;
28.图4是实施例1方法得到的产品石墨烯导热膜sem图;
29.图5是实施例2火焰还原处理后的两层氧化石墨烯并压实后的样品外观;
30.图6是实施例2石墨烯泡沫膜(高温处理后未压实之前)的样品外观照片;
31.图7是实施例2石墨烯导热膜sem图;
32.图8是实施例3石墨烯膜的样品外观照片;
33.图9是实施例3方法得到的产品石墨烯膜的sem图;
34.图10是实施例3石墨烯膜在水中的爬升现象;
35.图11是对比例1方法得到的石墨烯膜的外观;
36.图12是对比例1方法得到的石墨烯膜的sem图;
37.图13是对比例2方法得到的石墨烯膜的外观;
38.图14是对比例2方法得到的石墨烯膜的sem图。
具体实施方式
39.在下文中,仅简单地描述了某些示例性实施例。正如本领域技术人员可认识到的那样,在不脱离本发明的精神或范围的情况下,可通过各种不同方式修改所描述的实施例。因此,附图和描述被认为本质上是示例性的而非限制性的。
40.本发明的一个实施方式中,展示了一种新的氧化石墨烯膜的还原方法,即火焰还原法。下面详细说明该方法。
41.氧化石墨烯膜选自本公司制造量产的的氧化石墨烯膜,氧化石墨烯膜制备方法采用的是氧化石墨烯自组装定向排列法,过程有分散、涂覆、干燥、剥离、分切。也可以不分切,得到带状的氧化石墨烯膜,氧化石墨烯膜的厚度40~300μm;具体方法参见专利文献cn201510481379.7,cn201510480016.1。
42.将上述氧化石墨烯膜采用火焰还原,火焰采用天燃气燃烧火焰,火焰的温度为300~600℃,氧化石墨烯膜从火焰的上面经过,氧化石墨烯膜接触火焰的外焰处,经过的速度0.5~5m/min。经过速度过慢,会导致一直加热已经烧过的地方,热量会通过传导的方式传至未被烧过的地方,这样造成未被烧过的地方的变形,导致膜外观不一致不平整;经过速度过快,容易导致就是烧的不完整。经过长期的试验发现,将经过速度控制在0.5~5m/min时,可以有效的保证火焰处理的均匀性,膜外面平整度一致,且形成的毛细气体通道大小一致性高,分布均匀。本实施方式中优选以1-2m/min经过外焰。火焰还原的氧化石墨烯膜的厚度为300~3000μm。火焰还原的目的是使氧化石墨烯的在迅速的高温下部分官能团分解,将石墨烯片与片之间撑开形成毛细气体通道,一方面减少氧化石墨烯膜在热还原过程中产生的气体,另一方面,使热还原过程中产生的大量的气体可以从毛细气体通道有效的排出膜体外,最终减少氧化石墨烯膜在热还原过程中厚度的膨胀。火焰处理过程中,气体快速的排出,制造了很多的毛细气体通道,在后续热处理过程中,产生的气体可以从这些毛细通道排出。在多次的实验中,我们发现,经火陷还原,产生的这些毛细气体通道孔隙很小(一般在1微米以内),不会被物理的压实破坏。对比氧化石墨烯膜自组装时的氢键作用形成片层之间的紧密结合,阻止了在还原过程中的气体排出,从而造成还原过程中,膜整体厚度的增加。本发明采用火焰还原产生的毛细气体通道,使气体可以迅速排出,避免了积存于膜体中,可有效减少膜厚的增加。
43.本发明的另一个实施方式中,展示了一种石墨烯膜的制备方法采用氧化石墨烯定向组装制备的氧化石墨烯膜,此氧化石墨烯膜来自本公司正常生产的氧化石墨烯膜(参见专利cn201510481379.7,cn201510480016.1)将氧化石墨烯膜采用火焰还原,然后压实得到火焰还原的氧化石墨烯膜,再经过进一步的高温还原,得到还原的石墨烯泡沫膜,进一步压实得到石墨烯导热膜。
44.具体的制备方法,如下:
45.1、氧化石墨烯膜选自本公司制造量产的的氧化石墨烯膜,氧化石墨烯膜制备方法采用的是氧化石墨烯自组装定向排列法,过程有分散、涂覆、干燥、剥离、分切。氧化石墨烯膜的厚度40~300μm;
46.2、采用上述火焰还原的方法还原氧化石墨烯膜;
47.3、将上述火焰还原的氧化石墨烯膜,经过压实得到压实的火焰还原的氧化石墨烯膜;压实可以通过对辊机压实,也可以通过平压机压实,压实的压力大于5mpa;
48.压实可以将单层的火焰还原的氧化石墨烯膜压实,厚度在50~400μm;也可以将多层火焰还原的氧化石墨烯膜叠在一起压实,厚度200μm以上,达到毫米级别或厘米级别;
49.4、将上述压实的火焰还原的氧化石墨烯膜,进一步经过热还原,得到还原的石墨烯泡沫膜;火焰还原的氧化石墨烯膜叠起来放在石墨舟皿内,其片层之间采用石墨纸隔开,石墨纸为膨胀石墨压制而成,石墨纸的厚度为150~350μm,太薄的石墨纸作为隔层挺度不够,最终得到石墨烯导热膜的边缘不好,太厚的石墨纸占空间,影响产能;火焰还原的氧化石墨烯膜热还原的温度2000~3000℃,从室温升至最高温,升温的速率2~10℃/min;得到的石墨烯泡沫膜的厚度为,单层50~400μm,多层200μm以上,石墨烯泡沫膜的密度为0.4~1.1g/cm3,此密度是现有热还原工艺得到的石墨烯泡沫膜密度的2倍以上;石墨烯泡沫膜密度大幅度提升,厚度降低,单炉产能大幅提升,热还原成本得到有效的降低;从下面的具体实施例1和对比例1相比,两者使用的氧化石墨烯膜相同,对比例1未经火焰还原处理,实施例1经过火焰还原处理,两者在高温处理时,对比例1单炉可烧1622片石墨烯膜,而实施例1,单炉可以烧2235片石墨烯膜,实施例1相比对比例1,产能提高了37.8%。
50.5、将上述得到的石墨烯泡沫膜进一步压实得到石墨烯膜,压实可以采用辊压或者平压,压力≥20mpa,在本实施方式中,压力控制在25~60mpa范围。经压实后的石墨烯膜的厚度为微米级,在10μm以上,一般为30~400μm,导热系数≥1000w/m.k,密度≥1.9g/cm3。
51.本发明的另一个实施方式展示了另一种石墨烯膜的制备方法,该方法得到的石墨烯膜较上一实施方式得到的石墨烯膜更为轻质,可用为更轻质的电磁屏蔽材料,储热材料的导热支架,热管的毛细液芯等。该方法将火焰还原的氧化石墨烯膜,不经过上述的压实,直接进一步热还原,可以得到密度更低的石墨烯膜,密度可以达到0.02~0.07g/cm3。在该实施方式中,进一步热还原的处理温度为800~3000℃,从室温升至最高温的速率为2~10℃/min;采用氮气或氩气作为保护气体。
52.以下结合附图对本发明的优选实施例进行说明,应当理解,此处所描述的优选实施例仅用于说明和解释本发明,并不用于限定本发明。
53.实施例1:
54.一种石墨烯膜作为导热膜的制备方法:
55.如图1所示,采用本公司生产制造的定向自组装的氧化石墨烯膜,为原料膜,厚度138μm。
56.将上述的氧化石墨烯膜经过500℃的火焰还原,得到火焰还原氧化石墨烯膜,其厚度为1216μm。经火焰还原后的氧化石墨烯膜外观如图2所示。
57.将火焰还原氧化石墨烯膜,经对辊机辊压压实,辊压机的压力为10mpa,压实的火焰还原的氧化石墨烯膜的厚度为188μm。将上述压实的火焰还原的氧化石墨烯膜多层叠起来,层之间采用150μm的石墨纸隔开,堆叠在石墨舟皿内,进行热还原。石墨舟皿内的温度从室温升至2850℃,其中,从室温至600℃采用2℃/min升温,从600℃~2850℃采用4℃/min升温,升温到2850℃后保温1h,得到的还原的石墨烯泡沫膜的厚度为184μm,密度为0.43g/cm3,如图3所示。将上述的石墨烯泡沫膜采用辊压机压实,压力为25mpa,得到厚度为38μm,密度2.06g/cm3的石墨烯导热膜,导热系数1560w/m.k。所得石墨烯导热膜sem图如图4所示。
58.实施例2:
59.一种石墨烯膜作为导热膜的制备方法:
60.将实施例一中,火焰还原得到的氧化石墨烯膜,两张叠在一起,经平压机压实,平压机压力为15mpa,两张叠合压实的火焰还原的氧化石墨烯膜的厚度为360μm(如图5所示)。将上述压实的火焰还原的氧化石墨烯膜多层叠起来,层之间采用300μm的石墨纸隔开,堆叠在石墨舟皿内,进行热还原。石墨舟皿内的温度从室温升至2900℃,保温1h,室温至600℃采用2℃/min升温,600~2900℃采用5℃/min升温,得到的还原的石墨烯泡沫膜的厚度为276μm,密度为0.56g/cm3(如图6所示);将上述的石墨烯泡沫膜采用平压机压实,压力为40mpa,得到厚度为71μm,密度2.19g/cm3的石墨烯导热膜,导热系数1760w/m.k。所得石墨烯导热膜sem图如图7所示。
61.实施例3:
62.一种石墨烯膜作为热管中的介质传输芯的制备方法:
63.采用本公司生产制造的氧化石墨烯膜,厚度为70μm。将上述氧化石墨烯膜经过600℃的火焰还原,得到厚度为750μm的火焰还原氧化石墨烯膜。将其进一步热处理还原,从室温升至最高温900℃,保温1h,升温速率5℃/min,得到还原的石墨烯膜,厚度为690μm,其密度为0.067g/cm3。如图8所示,为石墨烯膜样品外观照片。如图9所示,为产品石墨烯膜的sem图。如图10所示,将得到的石墨烯膜垂直放入水中,观察水在其中的爬升现象,水垂直爬升的距离为85mm,是一个优秀的毛细液芯,可以作为热管中介质的传输芯。
64.对比例1:
65.采用本公司生产制造的定向自组装的氧化石墨烯膜,为原膜,厚度138μm;将上述氧化石墨烯膜多层叠起来,层之间采用150μm的石墨纸隔开,堆叠在石墨舟皿内,进行热还原,从室温升至2850℃,保温1h,室温至300℃采用0.5℃/min升温,300~900℃采用3℃/min升温,900℃~2850℃采用4℃/min,得到的还原的石墨烯泡沫膜的厚度为348μm,密度为0.22g/cm3;将上述的石墨烯泡沫膜采用辊压机压实,压力为25mpa,得到厚度为39μm,密度1.99g/cm3的石墨烯导热膜,导热系数1560w/m.k。
66.所得产品外面及sme图参见图11、12所示。相比实施例1来说,其得到的石墨烯泡沫的密度小,厚度大,严重影响设备产能。
67.对比例2:
68.采用本公司生产制造的定向自组装的氧化石墨烯膜,为原膜,厚度138μm;将上述氧化石墨烯膜多层叠起来,每两层之间采用300μm的石墨纸隔开,堆叠在石墨舟皿内,进行热还原,从室温升至2900℃,保温1h,室温至300℃采用0.5℃/min升温,300~900℃采用3℃/min升温,900℃~2900℃采用4℃/min,得到的还原的石墨烯泡沫膜的厚度为621μm,密度为0.25g/cm3;将上述的石墨烯泡沫膜采用辊压机压实,压力为25mpa,得到厚度为76μm,密度2.04g/cm3的石墨烯导热膜,导热系数1750w/m.k。
69.所得产品外面及sme图参见图13、14所示。相比实施例2来说,其得到的石墨烯泡沫的密度小,厚度大,严重影响设备产能。
70.从实施例1和2的sem图片看出,相同的比例尺下,明显对比例的空腔大。实施例1和2的产品sem图内,5μm以上的空隙很少,而对比例1和2的产品sem图内,5μm以上的空隙很多。并且,实施例中的石墨烯片很贴近,基本都小于2μm,石墨烯片层直接的距离更近。对比例的
sem图中,石墨烯层与层之间的距离较远。
71.最后应说明的是:以上所述仅为本发明的优选实施例而已,并不用于限制本发明,尽管参照前述实施例对本发明进行了详细的说明,对于本领域的技术人员来说,其依然可以对前述各实施例所记载的技术方案进行修改,或者对其中部分技术特征进行等同替换。凡在本发明的精神和原则之内,所作的任何修改、等同替换、改进等,均应包含在本发明的保护范围之内。