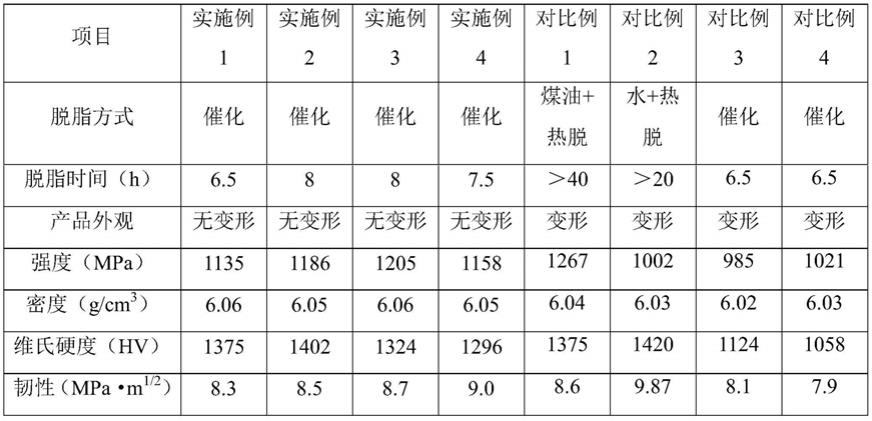
1.本发明属于氧化锆陶瓷注射成型领域,具体涉及一种氧化锆陶瓷注射成型催化脱脂喂料及其制备方法和应用。
背景技术:
2.粉末注射成型工艺是将先进的注射成型技术与粉末冶金技术完美结合起来形成的新型粉末冶金注射工艺,其优势在于可以制造尺寸精度高、一次成型特别复杂、机械加工程度高、易实现连续自动化生产等特点的零件,被国际上赞誉为“当今最热门成型技术之一”,已广泛应用于医疗器械、通信工程、航天工程、玩具器械等领域。
3.粉末注射成型工艺包括配料及密炼、注射成型、脱脂、烧结四个阶段,其中脱脂阶段既费时又复杂,缺陷多,而且过程特别难以控制。在实际生产中,脱脂阶段应用最多的是热脱脂和溶剂脱脂,但热脱脂工艺脱脂速率慢、容易产生缺陷,只适合精密小件,溶剂脱脂工艺复杂、生产周期长、易变形。
4.例如专利cn202010112736.3公开的表面改性的氧化锆注射成型溶剂脱脂喂料就是采用溶剂脱脂,其制备的喂料成型的生坯在脱脂时,需要在50~60℃煤油中浸泡40~50h,再在脱脂炉中进行脱脂。
5.专利cn202011579647.6公开的氧化锆陶瓷注射成型水溶剂脱脂喂料虽然改进了上述专利煤油作为溶剂脱脂的缺陷,其制备的喂料成型的生坯在脱脂时,可以用水作为溶剂,更加环保,但是水脱脂仍然存在陶瓷生坯易变形的问题。
6.鉴于热脱脂和溶剂脱脂在工业化使用过程中的缺点,需要研究一种新的氧化锆陶瓷注射成型喂料配方,达到环保无污染、快速脱脂。
技术实现要素:
7.本发明解决的技术问题是:针对现有热脱脂和溶剂脱脂的缺陷,提供一种氧化锆陶瓷注射成型催化脱脂喂料,大幅缩短了脱脂时间,脱脂过程安全环保,大大提高了生产效率;本发明还提供其制备方法和应用,脱脂烧结后得到的陶瓷产品力学性能优良。
8.本发明所述的氧化锆陶瓷注射成型催化脱脂喂料,由81~90wt%的氧化锆粉体和10~19wt%的粘结剂制成,粘结剂由主粘结剂、润滑剂、骨架树脂、增塑剂组成,其中主粘结剂、骨架树脂、润滑剂、增塑剂的质量比为70~80:15~20:3~8:2~5。
9.氧化锆粉体为钇稳定氧化锆粉体,粒径为40~80nm。
10.主粘结剂为聚甲醛。
11.润滑剂为微晶蜡或乙烯-醋酸乙烯共聚物。
12.骨架树脂为高密度聚乙烯、聚乙烯醇中的一种或两种。
13.增塑剂为邻苯二甲酸酯、邻苯二甲酸二酯、邻苯二甲酸二甲酯中的一种或多种。
14.其中,主粘结剂选用聚甲醛,因其对酸性气氛非常敏感,特别适合催化脱脂,在酸性气氛中,聚甲醛能快速裂解为甲醛气体,从而实现快速脱脂。在催化脱脂的过程中骨架树
脂使坯体形状保持稳定。润滑剂为表面活性剂,降低熔体的表面张力,增塑剂主要是降低熔体的粘度,提高其后期成型加工特性。粘结剂中各组分原料互相作用,各组分含量过多或过少对熔体的流动性产生消极影响,后期生坯催化脱脂会更易产生变形。
15.所述氧化锆陶瓷注射成型催化脱脂喂料的制备方法,包括以下步骤:
16.(1)密炼:密炼机温度设置为165~180℃,搅拌转速为10~20r/min,先加入主粘结剂和骨架树脂,搅拌10~20min,再加入占氧化锆粉体总质量2/3~3/4的氧化锆粉体和润滑剂,搅拌5~10min,加入剩余的氧化锆粉体,搅拌15~20min,最后加入增塑剂,搅拌90~120min,得到混合好的团状喂料;
17.(2)造粒:将混合好的团状喂料置于造粒机中进行造粒,得到颗粒状的氧化锆陶瓷注射成型催化脱脂喂料。
18.步骤(1)中,氧化锆粉体在密炼前需要进行预烘干,烘干温度为100~120℃,烘干时间为6~12h。
19.步骤(2)中,造粒机温度140~150℃,挤出转速15~20r/min,切粒转速10~20r/min。
20.所述氧化锆陶瓷注射成型催化脱脂喂料的应用,步骤如下:
21.将氧化锆陶瓷注射成型催化脱脂喂料成型为陶瓷生坯,然后在120℃~150℃酸性气氛中催化脱脂5h~8h,得到脱脂后的生坯,在烧结炉中1430~1480℃进行烧结,得到陶瓷产品。
22.酸性气氛为硝酸气体或草酸气体,浓度为0.1%~5%,通入速度为0.01~0.05ml/min。
23.催化脱脂在催化脱脂炉中进行。
24.烧结时升温速率为5~10℃/min,升温至1430~1480℃保温5~8h。
25.在酸性气体作用下,有机物载体分子裂解为很小的具有可挥发性的分子,同时,这些分子的蒸气压要高于其他脱脂方法中有机载体的分子的蒸气压,能够快速地从坯体中扩散出去。
26.与现有技术相比,本发明具有以下有益效果:
27.(1)本发明的氧化锆陶瓷注射成型催化脱脂喂料采用聚甲醛作为主粘结剂,在催化脱脂过程中,聚甲醛对酸性气氛敏感,在酸性气氛中发生快速降解,安全无污染,而且催化脱脂反应温度低于聚甲醛软化温度,整个脱脂过程没有液相产生,避免了塌陷等缺陷,烧结后的制品致密,形状完好;
28.(2)本发明采用主粘结剂、润滑剂、骨架树脂、增塑剂混合作为粘结剂,并与氧化锆粉体采用分批混合的方式进行密炼,避免了氧化锆粉体团聚,脱脂烧结后得到的陶瓷产品力学性能优良。
附图说明
29.图1是本发明氧化锆陶瓷注射成型催化脱脂喂料制备的白色氧化锆阀门。
具体实施方式
30.本发明下面将结合实施例作进一步详述。
31.实施例1
32.氧化锆陶瓷注射成型催化脱脂喂料的原料组成为:氧化锆粉体与粘结剂质量比为81:19;粘结剂中聚甲醛、高密度聚乙烯、微晶蜡、邻苯二甲酸酯的重量比例为72:18:6:4。
33.制备方法及应用方法为:
34.(1)密炼:将氧化锆粉体在100℃温度下烘干6h进行预处理,密炼机温度设置为170℃,搅拌转速为10r/min,加入聚甲醛和高密度聚乙烯,混炼10min,再加入占氧化锆粉体总质量2/3的氧化锆粉体和微晶蜡,混炼5min,加入剩余的氧化锆粉体,混炼15min,再加入邻苯二甲酸酯,混炼90min,得到混合好的团状喂料;
35.(2)造粒:将混合好的团状喂料置于造粒机中,设置温度140℃,挤出转速15r/min,切粒转速10r/min,进行造粒,得到颗粒状的氧化锆陶瓷注射成型催化脱脂喂料;
36.(3)催化脱脂:将氧化锆陶瓷注射成型催化脱脂喂料成型为陶瓷生坯,置于催化脱脂炉中,温度保持在125℃,向装置内通入浓度为0.1%的硝酸气体,气体通入速度为0.01ml/min,在酸性气氛中脱脂6.5h,得到脱脂后的生坯;
37.(4)烧结:将脱脂后的生坯在烧结炉中1430℃进行烧结,得到陶瓷产品。
38.实施例2
39.氧化锆陶瓷注射成型醇溶剂脱脂喂料的原料组成为:氧化锆粉体与粘结剂比例为83:17,粘结剂中聚甲醛、高密度聚乙烯、乙烯醋酸乙烯共聚物、邻苯二甲酸二酯的重量比例为74:17:7:2。
40.制备方法及应用方法为:
41.(1)密炼:将氧化锆粉体在105℃温度下烘干8h进行预处理,密炼机温度设置为175℃,搅拌转速为15r/min,加入聚甲醛和高密度聚乙烯,混炼8min,再加入占氧化锆粉体总质量3/4的氧化锆粉体和乙烯醋酸乙烯共聚物,混炼8min,加入剩余的氧化锆粉体,混炼20min,再加入邻苯二甲酸二酯,混炼100min,得到混合好的团状喂料;
42.(2)造粒:将混合好的团状喂料置于造粒机中,设置温度140℃,挤出转速15r/min,切粒转速10r/min,进行造粒,得到颗粒状的氧化锆陶瓷注射成型催化脱脂喂料;
43.(3)催化脱脂:将氧化锆陶瓷注射成型催化脱脂喂料成型为陶瓷生坯,置于催化脱脂炉中,温度保持在130℃,向装置内通入浓度为0.15%的硝酸气体,气体通入速度为0.02ml/min,在酸性气氛中脱脂8h,得到脱脂后的生坯;
44.(4)烧结:将脱脂后的生坯在烧结炉中1450℃进行烧结,得到陶瓷产品。
45.实施例3
46.氧化锆陶瓷注射成型醇溶剂脱脂喂料的原料组成为:氧化锆粉体与粘结剂比例为84:16,粘结剂中聚甲醛、聚乙烯醇、微晶蜡、邻苯二甲酸二甲酯的重量比例为75:16:6:3。
47.制备方法及应用方法为:
48.(1)密炼:将氧化锆粉体在110℃温度下烘干8h进行预处理,密炼机温度设置为165℃,搅拌转速为10r/min,加入聚甲醛和聚乙烯醇,混炼10min,再加入占氧化锆粉体总质量2/3的氧化锆粉体和微晶蜡,混炼10min,加入剩余的氧化锆粉体,混炼20min,再加入邻苯二甲酸二甲酯,混炼120min,得到混合好的团状喂料;
49.(2)造粒:将混合好的团状喂料置于造粒机中,设置温度145℃,挤出转速20r/min,切粒转速20r/min,进行造粒,得到颗粒状的氧化锆陶瓷注射成型催化脱脂喂料;
50.(3)催化脱脂:将氧化锆陶瓷注射成型催化脱脂喂料成型为陶瓷生坯,置于催化脱脂炉中,温度保持在135℃,向装置内通入浓度为0.2%的草酸气体,气体通入速度为0.03ml/min,在酸性气氛中脱脂8h,得到脱脂后的生坯;
51.(4)烧结:将脱脂后的生坯在烧结炉中1480℃进行烧结,得到陶瓷产品。
52.实施例4
53.氧化锆陶瓷注射成型醇溶剂脱脂喂料的原料组成为:氧化锆粉体与粘结剂比例为85:15,粘结剂中聚甲醛、高密度聚乙烯、乙烯醋酸乙烯共聚物、邻苯二甲酸酯的重量比例为78:15:4:3。
54.制备方法及应用方法为:
55.(1)密炼:将氧化锆粉体在120℃温度下烘干10h进行预处理,密炼机温度设置为180℃,搅拌转速为15r/min,加入聚甲醛和高密度聚乙烯,混炼15min,再加入占氧化锆粉体总质量2/3的氧化锆粉体和乙烯醋酸乙烯共聚物,混炼10min,加入剩余的氧化锆粉体,混炼20min,再加入邻苯二甲酸酯,混炼100min,得到混合好的团状喂料;
56.(2)造粒:将混合好的团状喂料置于造粒机中,设置温度140℃,挤出转速20r/min,切粒转速20r/min,进行造粒,得到颗粒状的氧化锆陶瓷注射成型催化脱脂喂料;
57.(3)催化脱脂:将氧化锆陶瓷注射成型催化脱脂喂料成型为陶瓷生坯,置于催化脱脂炉中,温度保持在125℃,向装置内通入浓度为0.3%的草酸气体,气体通入速度为0.04ml/min,在酸性气氛中脱脂7.5h,得到脱脂后的生坯;
58.(4)烧结:将脱脂后的生坯在烧结炉中1480℃进行烧结,得到陶瓷产品。
59.对比例1
60.与专利cn111233488a的实施例2进行对比,
61.(1)将氧化锆粉体的表面进行改性,具体实施步骤是:
62.步骤1,将氧化锆与纯水按质量比1:3在容器中进行混合,形成混合的氧化锆浆料;
63.步骤2,将氨水加入到氧化锆浆料中,边加入边搅拌,调节ph值在8
±
0.5的范围内,形成碱性的氧化锆浆料;
64.步骤3,将氧化锆浆料在烘箱中烘干,脱去水分,得到改性的氧化锆粉体。
65.(2)将改性的氧化锆粉体与粘结剂按质量比为82:18配料,其中,粘结剂中硬脂酸、聚丙烯、高密度聚乙烯、聚苯乙烯、苯乙烯类热塑性弹性体、全精炼石蜡、二甘醇二苯甲酸酯重量比为3:8:10:7:8:61:3,按照配比称量,得到喂料组成。
66.将改性的氧化锆粉体与粘结剂喂料组成进行造粒并制成陶瓷坯体,具体实施步骤如下:
67.步骤1,粉体和粘结剂的称量;按比例将粉体与粘结剂称量后分别置于容器中;
68.步骤2,部分粘结剂的预混;将骨架树脂、弹性体树脂、润滑助剂在200℃混合20min;
69.步骤3,喂料的密炼;密炼机温度设置为150℃,加入1/2的氧化锆粉体,加入表面活性剂,设置转速10r/min,混合40min,然后加入预混后的粘结剂,混合10min,然后加入剩余3/4氧化锆粉体,混合10min,然后加入增塑剂,混合120min;
70.步骤4,喂料的造粒;将混合好的团装喂料置于造粒机中,设置温度150℃,挤出转速10r/min,切粒转速10r/min,得到造粒后的喂料。
71.步骤5,生坯的溶剂脱脂;将喂料在注射成型机成型为陶瓷生坯,然后在50℃煤油中浸泡40h,得到溶脱后的产品;
72.步骤6,热脱脂烧结;将溶脱后的产品在脱脂炉进行脱脂,然后在烧结炉进行烧结,得到最终的陶瓷毛坯。
73.对比例2
74.与专利cn112723883a中的实施例1进行对比,其实施例1内容如下:
75.氧化锆陶瓷注射成型水溶剂脱脂喂料的原料组成为:氧化锆粉体与粘结剂质量比为82:18;粘结剂由以下质量百分数的原料组成:油酸3%,聚丙烯10%,低密度聚乙烯20%、聚丙烯酰胺20%、聚丙烯酸44%、亚硫酸钠3%。
76.制备方法为:
77.(1)预混:密炼机设置温度为180℃,转速为10r/min,将氧化锆粉体与油酸加入密炼机搅拌10min,得到预混后的氧化锆粉体;
78.(2)密炼:密炼机温度设置为200℃,转速为10r/min,在预混后的氧化锆粉体中,加入聚丙烯、低密度聚乙烯,搅拌40min,然后加入亚硫酸钠,搅拌10min,再次加入润滑助剂,搅拌20min,最后将密炼机温度设置为180℃,搅拌60min,得到混合好的团状喂料;
79.(3)造粒:将混合好的团状喂料取出冷却后在破碎机中破碎造粒,即得氧化锆陶瓷注射成型水溶剂脱脂喂料。
80.将氧化锆陶瓷注射成型水溶剂脱脂喂料在注射成型机成型为陶瓷生坯,然后在90℃水中浸泡20h后,脱去其中的润滑助剂,将溶脱后的产品在脱脂炉进行脱脂,然后在烧结炉进行烧结,得到的陶瓷推剪片毛坯。
81.对比例3
82.氧化锆陶瓷注射成型催化脱脂喂料的原料组成为:氧化锆粉体与粘结剂质量比为81:19;粘结剂中聚甲醛、高密度聚乙烯、微晶蜡、邻苯二甲酸酯的重量比例为60:28:10:2。
83.制备方法及应用方法为:
84.(1)密炼:将氧化锆粉体在100℃温度下烘干6h进行预处理,密炼机温度设置为170℃,搅拌转速为10r/min,加入聚甲醛和高密度聚乙烯,混炼10min,再加入占氧化锆粉体总质量2/3的氧化锆粉体和微晶蜡,混炼5min,加入剩余的氧化锆粉体,混炼15min,再加入邻苯二甲酸酯,混炼90min,得到混合好的团状喂料;
85.(2)造粒:将混合好的团状喂料置于造粒机中,设置温度140℃,挤出转速15r/min,切粒转速10r/min,进行造粒,得到颗粒状的氧化锆陶瓷注射成型催化脱脂喂料;
86.(3)催化脱脂:将氧化锆陶瓷注射成型催化脱脂喂料成型为陶瓷生坯,置于催化脱脂炉中,温度保持在125℃,向装置内通入浓度为0.1%的硝酸气体,气体通入速度为0.01ml/min,在酸性气氛中脱脂6.5h,得到脱脂后的生坯;
87.(4)烧结:将脱脂后的生坯在烧结炉中1430℃进行烧结,得到陶瓷产品。
88.对比例4
89.氧化锆陶瓷注射成型催化脱脂喂料的原料组成为:氧化锆粉体与粘结剂质量比为81:19;粘结剂中聚甲醛、高密度聚乙烯、微晶蜡、邻苯二甲酸酯的重量比例为72:18:6:4。
90.制备方法及应用方法为:
91.(1)密炼:将氧化锆粉体在100℃温度下烘干6h进行预处理,密炼机温度设置为170
℃,搅拌转速为10r/min,将已称重的全部氧化锆粉体和粘结剂一起加入到密炼机中,混炼15min后,转子转速设定为40r/min,继续混炼120min,得到混合好的团状喂料;
92.(2)造粒:将混合好的团状喂料置于造粒机中,设置温度140℃,挤出转速15r/min,切粒转速10r/min,进行造粒,得到颗粒状的氧化锆陶瓷注射成型催化脱脂喂料;
93.(3)催化脱脂:将氧化锆陶瓷注射成型催化脱脂喂料成型为陶瓷生坯,置于催化脱脂炉中,温度保持在125℃,向装置内通入浓度为0.1%的硝酸气体,气体通入速度为0.01ml/min,在酸性气氛中脱脂6.5h,得到脱脂后的生坯;
94.(4)烧结:将脱脂后的生坯在烧结炉中1430℃进行烧结,得到陶瓷产品。
95.将各实施例和对比例制备的陶瓷制品进行性能测试,其中强度参考gb/t232-2010弯曲试验标准进行测试,密度参考gb4472-84密度测定标准进行测试,维氏硬度参考gb/t4340.1-2009维氏硬度试验标准进行测试,韧性参考gb/t 4161-1984断裂韧度试验标准进行测试。测试数据见表1。
96.表1各实施例和对比例制备的陶瓷制品的性能测试结果
97.