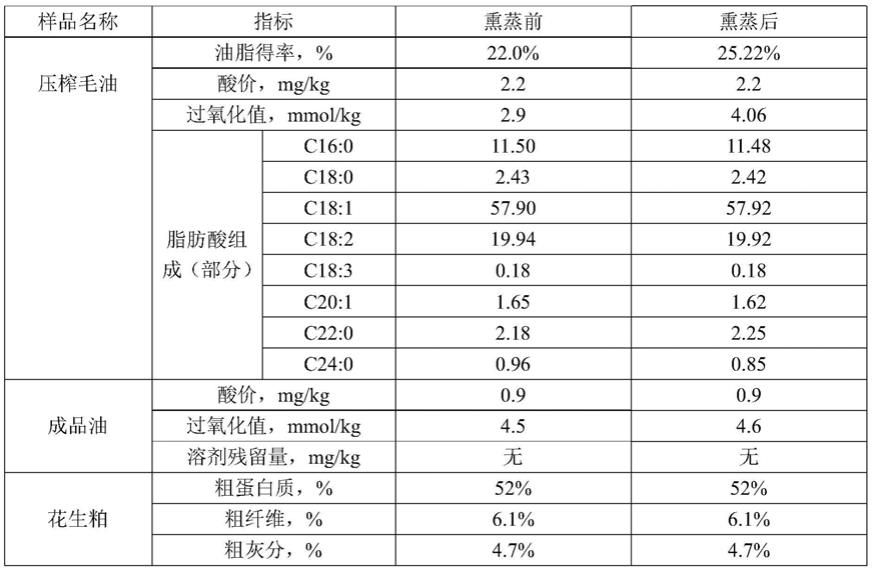
1.本发明涉及农产品加工领域,具体涉及一种熏蒸施药方法在油籽中的应用及其处理方法和制品。
背景技术:
2.油籽为油料种子,是指油料作物产的种子,主要包括大豆、花生、芝麻、油菜子、向日葵、棉籽、红花、椰子等。油料作物是以榨取油脂为主要用途的一类作物。世界四大主要油料作物为大豆、油菜、花生、向日葵。
3.从油料种子中获取成品油的方式,一般先物理压榨获取压榨毛油,压榨得到的油籽饼再进行溶剂萃取,进而获得浸出毛油,以减少油籽粕中的残油量。当压榨毛油的含量较低时,通常就需要更多的溶剂对油籽饼进行萃取获取浸出毛油和湿粕,而湿粕中的溶剂通常是采用加热的方式去除,当溶剂更多时,显然会导致湿粕处理能耗更高,生产成本更高。
4.因此,提高压榨毛油的出油率是降低能耗和成本的有益途径。
技术实现要素:
5.因此,本发明要解决的技术问题在于克服现有技术中的压榨毛油的出油率相对较低的缺陷,从而提供解决上述问题的一种熏蒸施药方法在油籽中的应用及其处理方法和制品。
6.一种利用二氧化氯气体熏蒸在提高压榨毛油出油率中的应用。
7.所述二氧化氯气体熏蒸中,二氧化氯气体的浓度为30~400g/m3,熏蒸处理时间为6~96h,二氧化氯为油籽干重的0.05wt%~0.5wt%。
8.二氧化氯气体的浓度为60~300g/m3,熏蒸处理时间为6~48h,二氧化氯为油籽干重的0.1wt%~0.4wt%。
9.所述油籽在密闭环境中进行二氧化氯气体的熏蒸,密闭环境中油籽的堆放厚度≤6m,平均油籽温度为0~22℃,空气相对湿度≤95%。
10.所述平均油籽温度为5~20℃。
11.所述熏蒸采用环流熏蒸的方式,在环流熏蒸过程中随机选择不少于3个的取样点,获取取样点位置处的二氧化氯浓度,计算获取的最低二氧化氯浓度与最高二氧化氯浓度的比值,当比值>0.6时,停止环流。
12.所述油籽中黄曲霉毒素b1为21.0~201.0μg/kg或总黄曲霉毒素为106.4~1036.6μg/kg。
13.油籽包含:花生、葵花籽、油菜籽、芝麻、大豆、亚麻籽、核桃仁、胡麻籽、山茶籽、火麻仁。
14.一种油籽的处理方法,包括:
15.预处理:将油籽放置到密封环境中;
16.熏蒸施药:将二氧化氯气体通入密封环境中,使密封环境中二氧化氯气体浓度达
到30~400g/m3,并且保证密封环境中二氧化氯的总含量为油籽干重的0.05wt%~0.5wt%;熏蒸处理6~96h后进行通风散气即可获得预处理后的油籽;
17.压榨:采用预处理后的油籽进行压榨获得压榨毛油和油籽饼。
18.油籽饼经过浸出处理后获得浸出毛油和湿粕,浸出毛油与压榨毛油进行精制后制成成品油;
19.湿粕经过溶剂脱除、加热干燥、冷却处理后获得油籽粕。
20.一种油籽及其制品,采用上述的一种油籽的处理方法制备得到;所述制品为压榨毛油、油籽饼、浸出毛油、湿粕或成品油。
21.本发明技术方案,具有如下优点:
22.1.本发明提供的应用,利用二氧化氯气体熏蒸能够有效提高压榨毛油出油率,可以将压榨出油率增幅接近15%,效果明显;且由于压榨毛油的出油率的增加,进而减少后续油籽饼浸出处理时所需的有机溶剂的量,减少溶剂使用与消耗,并且还能减少后续湿粕进行溶剂脱除所需的能耗,减少制备成本。
23.2.本发明提供的应用,更加适用于黄曲霉毒素b1为21.0~201.0μg/kg或总黄曲霉毒素为106.4~1036.6μg/kg的花生,在实现提高压榨毛油出油率的同时,还能有效降低花生中毒素,其中的黄曲霉毒素b1降低至≤10.5μg/kg,总黄曲霉毒素降低至≤21.2μg/kg;有效使制备得到的花生粕品质满足gb 10382和gb13078的要求。
24.3.本发明提供的一种油籽的处理方法,不仅仅可以有效提高压榨毛油出油率,还可以有效适用于污染油籽,对于污染油籽而言,该处理方法使熏蒸后油籽所制备得到的压榨毛油中黄曲霉毒素b1的含量≤11.6μg/kg,总黄曲霉毒素的含量≤25μg/kg,酸价、碘价、脂肪酸组成与未熏蒸处理的油籽的压榨毛油的相关指标基本一致,所制备的成品油中黄曲霉毒素b1的含量≤1.5μg/kg,总黄曲霉毒素的含量≤2.9μg/kg,进而可以保证成品油品质满足gb 1534和gb 2761的要求。
具体实施方式
25.提供下述实施例是为了更好地进一步理解本发明,并不局限于所述最佳实施方式,不对本发明的内容和保护范围构成限制,任何人在本发明的启示下或是将本发明与其他现有技术的特征进行组合而得出的任何与本发明相同或相近似的产品,均落在本发明的保护范围之内。
26.实施例中未注明具体实验步骤或条件者,按照本领域内的文献所描述的常规实验步骤的操作或条件即可进行。所用试剂或仪器未注明生产厂商者,均为可以通过市购获得的常规试剂产品。
27.本发明中所涉及指标的测定方法如下:
28.(1)黄曲霉毒素根据ls/t 6128的方法测定;
29.(2)黄曲霉毒素降解率(par,%)按照以下公式计算:
[0030][0031]
af0和af1分别表示样品在处理前和处理后的毒素水平,可以是afb1(黄曲霉毒素b1)、afb2(黄曲霉毒素b2)、afg1(黄曲霉毒素g1)、afg2(黄曲霉毒素g2)或总黄曲霉毒素。
[0032]
(3)压榨油脂得率按下式计算:
[0033][0034]
w1和w2分别为压榨前花生质量与压榨后花生油的质量。
[0035]
(4)水分根据gb5009.3的方法测定;
[0036]
(5)酸价根据gb 5009.229的方法测定;
[0037]
(6)碘价根据endo,y.,tagiri-endo,m.,&kimura,k.(2005).rapid determination of iodine value and saponification value of fish oils by near-infrared spectroscopy.journal of food science,70(2),c127-c131方法,使用ft-nir光谱仪测定(abb mb3600,abb公司);
[0038]
(7)过氧化值根据gb 5009.227的方法测定;
[0039]
(8)脂肪酸组成根据gb 5009.168的方法测定。
[0040]
实施例1
[0041]
一种熏蒸施药对脱壳花生及其制品进行处理的方法,主要包括:
[0042]
(1)仓房气密性检测,检测方法如下:仓房密封后,用毕托管和测压计及风机以正压测定仓房气密性;气密性标准为:仓内压力从500pa下降到250pa的时间,平房仓不少于40s,浅圆仓、立筒仓不少于60s。将花生放置到仓内,仓内粮垛厚度约2m。
[0043]
(2)准备药剂和施药装置,具体的:根据制定熏蒸方案的总用药量备足药剂。施药装置可采用气体发生器施药装置或钢瓶施药装置,或其它保障熏蒸安全的施药方法和装置。本实施例中采用气体发生器施药装置。
[0044]
(3)熏蒸施药:采取环流熏蒸方式施药,往仓室内通入二氧化氯气体,使仓室内二氧化氯气体的总浓度为30g/m3,气体与花生的比例为0.5%(w/w,相对花生干重);熏蒸持续时间为6小时,仓室内平均花生温度为20℃,空气相对湿度60%。环流熏蒸的实现过程为:仓外施药前先开启环流风机,形成气流循环,并充入二氧化碳气体,然后开始施药制备熏蒸气体。立筒仓和浅圆仓在环流管道上设置气体取样点,必要时可在仓内空间或粮堆中设置气体取样点。各气体取样点最低与最高浓度比>0.6时视为基本均匀。发生器中熏蒸气体可与二氧化碳混合,当堆内各取样点测得的熏蒸气体浓度均达到设定浓度并基本均匀后,即可停止环流。
[0045]
(4)当熏蒸密闭时间达到设定时间后通风散气;散气可采用自然通风散气和/或机械通风散气。采用机械通风散气时,散气时间一般为3d~5d;采用自然通风散气时,散气时间一般为5d~7d。本实施例中采用机械通风散气4天。
[0046]
(5)分别采用熏蒸前的油籽和熏蒸后的油籽采用相同的常规压榨工艺制备得到压榨毛油和油籽饼。具体的,本实施例中采用熏蒸前后的花生依次进行破碎、轧坯、蒸炒、压榨取油后获得压榨油和花生饼,压榨油经除渣后获得压榨毛油。
[0047]
(6)对花生饼采用常规浸出工艺进行处理获得浸出毛油和湿粕,具体的,将有机溶剂加入到花生饼中进行浸提,浸出得到的混合油经过常规的净化、蒸发、汽提、除去其中的粕末的处理步骤获得浸出毛油和湿粕。
[0048]
(7)对湿粕进行溶剂脱除、加热干燥、冷却等处理后获得花生粕。
[0049]
(8)将步骤(5)获得的压榨毛油和步骤(6)获得的浸出毛油进行精炼后即可获得成
品油。
[0050]
所得熏蒸前后花生、压榨毛油、成品油和花生粕的黄曲霉毒素水平及其他理化指标如下表1所示:
[0051]
表1
[0052][0053]
通过上述表1可知,采用二氧化氯气体熏蒸,可以有效提高压榨毛油出油率,降低溶剂消耗以及去除成本;并且通过检测结果对比可知,本方法制备得到的成品油既能满足gb 1534和gb 2761的要求,又能保留油脂的物化品质、风味等感官特性,以及不对副产品饲用感官等方面产生显著影响,效果显著。
[0054]
实施例2
[0055]
本实施例与实施例1的区别在于,本实施例中采用的原料花生不同,本实施例中原料花生为afb1浓度为21μg/kg、总黄曲霉毒素为106.4μg/kg的污染花生。其他步骤均与实施例1相同。本实施例制备得到的熏蒸前后花生、压榨毛油、成品油和花生粕的黄曲霉毒素水平及其他理化指标如下表2所示。
[0056]
表2
[0057][0058]
经检测,本实施例中不仅仅能够达到提高压榨毛油出油率的效果,还能显著降低花生中毒素,有效使制备得到的花生粕品质满足gb 10382和gb13078的要求;成品油品质满足gb 1534和gb 2761的要求。本实施例中,花生中黄曲霉毒素b1的消除率为80.5%,总黄曲霉毒素的消除率为92.6%;压榨毛油中的黄曲霉毒素b1的消除率为58.3%,总黄曲霉毒素的消除率为77.9%;花生粕中的黄曲霉毒素b1的消除率为83.3%,总黄曲霉毒素的消除率为94.0%。
[0059]
实施例3
[0060]
本实施例与实施例1的区别在于,本实施例中采用的原料花生、熏蒸施药的步骤以及机械通风散气的时间不同,其他步骤均与实施例1相同。
[0061]
本实施例中原料花生为afb1浓度为136μg/kg、总黄曲霉毒素为705μg/kg的污染花生。本实施例的熏蒸施药步骤中,仓室内通入二氧化氯气体的总浓度为60g/m3,气体与花生的比例为0.4%(w/w,相对花生干重),熏蒸持续时间为48小时,仓室内平均花生温度为5℃,空气相对湿度75%。机械通风散气时间为3天。
[0062]
本实施例制备得到的熏蒸前后花生、压榨毛油、成品油和花生粕的黄曲霉毒素水平及其他理化指标如下表3所示。
[0063]
表3
[0064][0065]
经检测,花生中黄曲霉毒素b1的消除率为95.2%,总黄曲霉毒素的消除率为98.2%;压榨毛油中的黄曲霉毒素b1的消除率为88.9%,总黄曲霉毒素的消除率为94.2%;花生粕中的黄曲霉毒素b1的消除率为96.0%,总黄曲霉毒素的消除率为98.6%。
[0066]
实施例4
[0067]
本实施例与实施例1的区别在于,本实施例中采用的原料花生、原料花生堆放厚度、熏蒸施药的步骤以及机械通风散气的时间不同,其他步骤均与实施例1相同。
[0068]
本实施例中原料花生为afb1浓度为201μg/kg、总黄曲霉毒素为1036.6μg/kg的污染花生,原料花生堆放厚度约5m。本实施例的熏蒸施药步骤中,仓室内通入二氧化氯气体的总浓度为300g/m3,气体与花生的比例为0.5%(w/w,相对花生干重),熏蒸持续时间为24小时,仓室内平均花生温度为0℃,空气相对湿度60%。机械通风散气时间为5天。
[0069]
本实施例制备得到的熏蒸前后花生、压榨毛油、成品油和花生粕的黄曲霉毒素水平及其他理化指标如下表4所示。
[0070]
表4
[0071][0072][0073]
经检测,花生中黄曲霉毒素b1的消除率为95.6%,总黄曲霉毒素的消除率为98.4%;压榨毛油中的黄曲霉毒素b1的消除率为90.0%,总黄曲霉毒素的消除率为94.9%;花生粕中的黄曲霉毒素b1的消除率为96.3%,总黄曲霉毒素的消除率为98.7%。
[0074]
实施例5
[0075]
本实施例与实施例1的区别在于,本实施例中采用的原料花生、原料花生堆放厚度、熏蒸施药的步骤以及通风散气的方式和时间不同,其他步骤均与实施例1相同。
[0076]
本实施例中原料花生为afb1浓度为130.0μg/kg、总黄曲霉毒素为658.0μg/kg的污染花生,原料花生堆放厚度约6m。本实施例的熏蒸施药步骤中,仓室内通入二氧化氯气体的总浓度为400g/m3,气体与花生的比例为0.1%(w/w,相对花生干重),熏蒸持续时间为48小时,仓室内平均花生温度为22℃,空气相对湿度85%。自然通风散气时间为7天。
[0077]
本实施例制备得到的熏蒸前后花生、压榨毛油、成品油和花生粕的黄曲霉毒素水平及其他理化指标如下表5所示。
[0078]
表5
[0079]
[0080][0081]
经检测,花生中黄曲霉毒素b1的消除率为96.0%,总黄曲霉毒素的消除率为98.5%;压榨毛油中的黄曲霉毒素b1的消除率为91.3%,总黄曲霉毒素的消除率为95.1%;花生粕中的黄曲霉毒素b1的消除率为96.6%,总黄曲霉毒素的消除率为98.8%。
[0082]
实施例6
[0083]
本实施例与实施例1的区别在于,本实施例中采用的原料花生、原料花生堆放厚度、熏蒸施药的步骤以及通风散气的方式和时间不同,其他步骤均与实施例1相同。
[0084]
本实施例中原料花生为afb1浓度为155μg/kg、总黄曲霉毒素为803μg/kg的污染花生,原料花生堆放厚度约3m。本实施例的熏蒸施药步骤中,仓室内通入二氧化氯气体的总浓度为200g/m3,气体与花生的比例为0.05%(w/w,相对花生干重),熏蒸持续时间为96小时,仓室内平均花生温度为20℃,空气相对湿度95%。自然通风散气时间为5天。
[0085]
本实施例制备得到的熏蒸前后花生、压榨毛油、成品油和花生粕的黄曲霉毒素水平及其他理化指标如下表6所示。
[0086]
表6
[0087][0088]
经检测,花生中黄曲霉毒素b1的消除率为93.0%,总黄曲霉毒素的消除率为97.2%;压榨毛油中的黄曲霉毒素b1的消除率为85.2%,总黄曲霉毒素的消除率为91.0%;花生粕中的黄曲霉毒素b1的消除率为94.0%,总黄曲霉毒素的消除率为97.8%。
[0089]
实施例7
[0090]
本实施例与实施例1的区别在于,本实施例中采用的原料芝麻、原料芝麻堆放厚度、熏蒸施药的步骤以及通风散气的方式和时间不同,其他步骤均与实施例1相同。
[0091]
本实施例中原料芝麻为afb1浓度为23μg/kg、总黄曲霉毒素为117μg/kg的污染芝麻,原料芝麻堆放厚度约2m。本实施例的熏蒸施药步骤中,仓室内通入二氧化氯气体的总浓度为100g/m3,气体与芝麻的比例为0.05%(w/w,相对芝麻干重),熏蒸持续时间为96小时,仓室内平均芝麻温度为20℃,空气相对湿度75%。机械通风散气时间为4天。
[0092]
本实施例制备得到的熏蒸前后芝麻、压榨毛油、成品油和芝麻粕的黄曲霉毒素水平及其他理化指标如下表7所示。
[0093]
表7
[0094][0095]
经检测,芝麻中黄曲霉毒素b1的消除率为99.6%,总黄曲霉毒素的消除率为99.7%;压榨毛油中的黄曲霉毒素b1的消除率为99.1%,总黄曲霉毒素的消除率为99.3%;芝麻粕中的黄曲霉毒素b1的消除率为99.6%,总黄曲霉毒素的消除率为99.8%。
[0096]
实施例8
[0097]
本实施例与实施例1的区别在于,本实施例中采用的原料葵花籽、原料葵花籽堆放厚度、熏蒸施药的步骤以及通风散气的方式和时间不同,其他步骤均与实施例1相同。
[0098]
本实施例中原料葵花籽为afb1浓度为4.5μg/kg、总黄曲霉毒素为22.6μg/kg的污染葵花籽,原料葵花籽堆放厚度约2m。本实施例的熏蒸施药步骤中,仓室内通入二氧化氯气体的总浓度为150g/m3,气体与葵花籽的比例为0.05%(w/w,相对葵花籽干重),熏蒸持续时间为48小时,仓室内平均葵花籽温度为20℃,空气相对湿度75%。机械通风散气时间为4天。
[0099]
本实施例制备得到的熏蒸前后葵花籽、压榨毛油、成品油和葵花籽粕的黄曲霉毒素水平及其他理化指标如下表8所示。
[0100]
表8
[0101][0102]
经检测,葵花籽中黄曲霉毒素b1的消除率为88%,总黄曲霉毒素的消除率为95.2%;压榨毛油中的黄曲霉毒素b1的消除率为74.6%,总黄曲霉毒素的消除率为85.8%;葵花籽粕中的黄曲霉毒素b1的消除率为89.5%,总黄曲霉毒素的消除率为96%。
[0103]
对比例1
[0104]
本对比例与实施例1的区别在于,本实施例中采用的原料花生、原料花生堆放厚度、熏蒸施药的步骤以及通风散气的方式和时间不同,其他步骤均与实施例1相同。
[0105]
本实施例中原料花生为afb1浓度为96μg/kg、总黄曲霉毒素为521μg/kg的污染花生,原料花生堆放厚度约2m。本实施例的熏蒸施药步骤中,仓室内通入二氧化氯气体的总浓度为100g/m3,气体与花生的比例为0.03%(w/w,相对花生干重),熏蒸持续时间为24小时,仓室内平均花生温度为5℃,空气相对湿度75%。机械通风散气时间为4天。
[0106]
本实施例制备得到的熏蒸前后花生压榨毛油的得率分别为22.11%和22.10%。
[0107]
显然,上述实施例仅仅是为清楚地说明所作的举例,而并非对实施方式的限定。对于所属领域的普通技术人员来说,在上述说明的基础上还可以做出其它不同形式的变化或变动。这里无需也无法对所有的实施方式予以穷举。而由此所引伸出的显而易见的变化或变动仍处于本发明创造的保护范围之中。