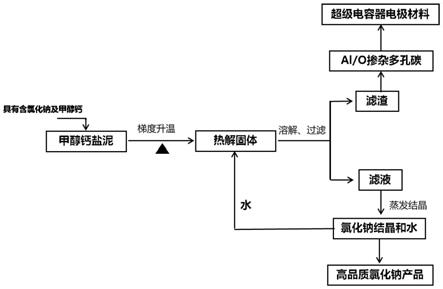
1.本发明属于工业废盐渣提纯回收领域,具体涉及一种有机废盐热解提纯氯化钠同时制取掺杂碳的方法。
技术背景
2.在许多精细化工、化学农药产品或中间体的生产过程中,产生大量含有毒有害化学物质的副产废盐(以下简称“废盐”)。废盐中主要含有氯化钠、硫酸钠等无机盐,其有机成分常常含有一些有毒有害成分。目前国内每年化工副产盐渣的数量达70万吨以上,且此数值正在逐年增加。这些化工生产副产废盐因含有毒有害化学物质而无法直接作为工业原料使用,因此大部分企业将其露天堆存或直接向江河中倾倒。这些粗放的管理方式易导致可溶性盐及有毒有害化学物质释放到环境中,造成严重的二次污染。因此,在2016年,废盐已通过《国家危险废物名录》被定义为“危险废物”。如今,废盐的有效处理和处置已成为固体废物领域迫切的技术需求。
3.目前,废盐的传统处理方式一般为填埋处置,随着原有化工生产规模的扩大及新化学品的涌现,化工废盐的产生量也与日剧增,填埋需占用大量场地,造成土地资源浪费的同时,还会对地下水资源和生态系统造成严重破坏。直接热力焚烧法是一种可行的废盐处理技术,例如季根忠等人利用该方法将废盐渣投加至气化炉,在高温(1250-1300℃)、高压(4.0mpa)的条件下,将氯化钠晶体转化为蒸汽回收(专利公开号:cn112320822a)。其次,溶解精制后二次浓缩结晶法也是常用的废盐处理手段:该方法是将废盐渣重新溶解于新鲜水中,通过化学处理后再次浓缩结晶后回收,例如专利公开号:cn105883911b——熔盐氯化渣资源化处理方法。但这些方法处置成本高,且有次生废水产生,溶解后物理化学处置的效果难以保障,重结晶回收的盐含水率高,有些还存在大量的结晶水,二次利用价值低。(3)无害化填埋处置:该方法是将各类废盐渣混合并经混凝土等固化剂固化后,按照国家危险废物管理及处置的相关法规和技术规范进行特殊填埋处置。该处置方法代价高昂,不但占用大量的土地,同时还存在因地质灾害等外来因素造成二次环境危害的风险。
4.目前对于虽然大多数人都集中在前端化工产品合成与制备的方法的研究,而对其工艺废盐综合回收处理方法的研究比较少,因此许多化工产品合成过程中产生的废盐一直没有得到有效的处理,造成了大量可回收资源的浪费。
技术实现要素:
5.本发明的目的是针对现有原氯化钠废盐渣提纯研究力度的不足,提供一种有机废盐热解提纯氯化钠同时制取掺杂碳的方法。该方法工艺简单、成本低、见效快、处理量大、提纯彻底,可以实现氯化钠废盐渣全利用。采用该方法提取的氯化钠可以回用于制造氯气、漂白粉、金属钠等工业原料,采用该方法得到的al/o掺杂碳材料可用作超级电容器领域的电极材料,实现彻底的变废为宝。
6.本发明的目的通过以下技术方案实现。
7.一种有机废盐热解提纯氯化钠同时制取掺杂碳的方法,包括如下步骤:
8.(1)将甲醇钙废盐研磨充分,并过筛;
9.(2)步骤(1)得到的质地均匀的甲醇钙废盐置于管式炉,在中低温度下惰性气氛中热解;
10.(3)在步骤(2)冷却到室温后的热解固体中加入水,搅拌使其溶解完全,再静置分层,得到上下层液体;
11.(4)过滤分离步骤(3)得到的上下层液体,上层液体过滤后的滤渣进行烘干回收得到al/o掺杂碳材料;
12.(5)将步骤(4)得到的滤液和步骤(3)的下层液体蒸发结晶,并再进一步干燥分离加热析出氯化钠晶体。
13.优选地,步骤(1)所述过筛的孔径为100-200目。
14.优选地,步骤(2)所述热解的温度为350~550℃。
15.优选地,步骤(2)所述惰性气氛为氮气、氩气中的一种。
16.优选地,步骤(3)所述水与热解固体的质量比为(3~6):1。
17.优选地,步骤(3)所述静置时间为25~45min。
18.优选地,步骤(4)所述碳材料为具有高电化学活性的al/o掺杂多孔碳。
19.优选地,步骤(4)所述烘干温度为60-80℃。
20.优选地,步骤(5)所述蒸发结晶温度为60-90℃。
21.优选地,步骤(5)所述氯化钠晶体为高纯度产品。
22.本发明提供一种有机废盐热解提纯氯化钠同时制取掺杂碳的方法,原理如下:
23.利用有机物低沸点的特征,对有机废盐进行惰性气体低温焙烧使其碳化,从而达到提纯氯化钠的目的。
24.与现有技术相比,本发明具有如下优点和有益效果:
25.(1)突破了含高浓度有机物的氯化钠盐渣乃至其它废盐渣处理的技术瓶颈,提供了一种含高浓度有机物的氯化钠盐渣可行的处理方案。
26.(2)通过低温处理,高效、彻底地碳化盐渣中的有机物,实现盐资源化利用,同时回收可高值化利用的碳,为化工行业实现节能减排提供技术支撑,促进化工行业的可持续协调发展。
附图说明
27.图1为本发明的工艺流程图。
28.图2为实施例3提纯得到的氯化钠产品的sem图。
29.图3为实施例3制备得到的al/o掺杂碳材料的sem谱图。
30.图4为实施例3制备得到的al/o掺杂碳材料的xps al 2p谱图。
31.图5为实施例3制备得到的al/o掺杂碳材料的充放电曲线。
具体实施方式
32.下面结合具体实施例对本发明做进一步说明,但本发明所保护范围不局限于所述内容。以下实施例涉及的氯化钠废盐渣来源为原甲酸三甲酯工艺副产废盐渣。
33.图1为本发明的工艺流程图。
34.实施例1
35.(1)将5g甲醇钙废盐研磨充分且过筛(200目);
36.(2)步骤(1)得到的质地均匀的甲醇钙废盐置于管式炉中,并于氮气气氛、350℃下热解2h;
37.(3)在室温24℃条件下,将步骤(2)所得热解固体冷却至室温后,称取4g热解固体,并向称取的热解固体中加入12g水,充分搅拌5分钟后,使得废盐充分溶解完全,再静置25min分层,得到上下层液体;
38.(4)过滤分离步骤(3)得到的上下层液体,上层液体过滤后的滤渣进行烘干,烘干温度为60℃,回收得到al/o掺杂碳材料;
39.(5)将步骤(4)得到的滤液和步骤(3)的下层液体在60℃下蒸发结晶,并再进一步干燥分离加热析出氯化钠晶体;
40.(6)取出晶种,于80℃干燥至恒重后称量。
41.本实施例处理5克氯化钠废盐渣,回收了4.81克氯化钠,产品经测试达到工业氯化钠(gb/t 6009-2014)ii类一等品标准。同时回收了0.35克al/o掺杂碳材料,其电容性能达到313.2f g-1
。
42.实施例2
43.(1)将5g甲醇钙废盐研磨充分且过筛(150目);
44.(2)步骤(1)得到的质地均匀的甲醇钙废盐渣置于管式炉中,并于氮气气氛、450℃下热解2h;
45.(3)在室温24℃条件下,将步骤(2)所得热解固体冷却至室温后,称取4g热解固体,并向称取的热解固体中加入20g水,充分搅拌5分钟后,使得废盐充分溶解完全,再静置35min分层,得到上下层液体;
46.(4)过滤分离步骤(3)得到的上下层液体,上层液体过滤后的滤渣进行烘干,烘干温度为70℃,回收得到al/o掺杂碳材料;
47.(5)将步骤(4)得到的滤液和步骤(3)的下层液体在80℃下蒸发结晶,并再进一步干燥分离加热析出氯化钠晶体;
48.(6)取出晶种,于85℃干燥至恒重后称量。
49.本实施例处理5克氯化钠废盐渣,回收了4.86克氯化钠,产品经测试达到工业氯化钠(gb/t 6009-2014)ii类一等品标准。同时回收了0.44克铝al/o掺杂碳材料,其电容性能达到356.5f g-1
。
50.实施例3
51.(1)将5g甲醇钙废盐研磨充分且过筛(100目);
52.(2)步骤(1)得到的质地均匀的甲醇钙废盐渣置于管式炉中,并于氩气气氛、550℃下热解2h;
53.(3)在室温24℃条件下,将步骤(2)所得热解固体冷却至室温后,称取4g热解固体,并向称取的热解固体中加入24g水,充分搅拌5分钟后,使得废盐充分溶解完全,再静置45min分层,得到上下层液体;
54.(4)过滤分离步骤(3)得到的上下层液体,上层液体过滤后的滤渣进行烘干,烘干
温度为80℃,回收得到al/o掺杂碳材料;
55.(5)将步骤(4)得到的滤液和步骤(3)的下层液体在90℃下蒸发结晶,并再进一步干燥分离加热析出的氯化钠晶体;
56.(6)取出晶种,于90℃干燥至恒重后称量。
57.本实施例处理5克氯化钠废盐渣,回收了4.60克氯化钠,产品经测试达到工业氯化钠(gb/t 6009-2014)ii类一等品标准。图2为实施例3提纯得到的氯化钠的sem图,由图2可观察到氯化钠晶体的表面较为光滑,杂质较少。同时回收了0.56克同时回收了0.35克al/o掺杂碳材料。图3为实施例3制备得到的al/o掺杂碳材料的sem谱图,由图3可观察到碳材料上丰富的多孔结构。图4为实施例3制备得到的al/o掺杂碳材料的xps al 2p谱图,由图4可观察到碳材料在al/o结合能的位置均有出峰,证实了其结构中具有一定量的al/o掺杂。图5为实施例3制备得到的al/o掺杂碳材料的充放电曲线,由图5可观察到碳材料在电流密度为0.5a g-1
条件下的充放电情况,其电容性能达到416.35f g-1
。
58.上述实施例为本发明较佳的实施方式,但本发明的实施方式并不受上述实施例的限制,其他的任何未背离本发明的精神实质与原理下所作的改变、修饰、替代、组合、简化,均应为等效的置换方式,都包含在本发明的保护范围之内。