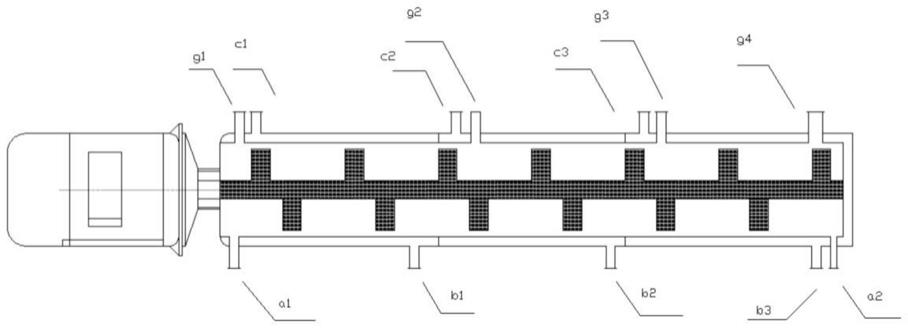
1.本发明属于对硝基甲苯邻磺酸的制备技术领域,具体涉及一种利用动态管式反应器连续制备对硝基甲苯邻磺酸的方法。
背景技术:
2.对硝基甲苯邻磺酸是一种活性物质,是制取二苯乙烯系直接染料、荧光增白剂和多染料的重要中间体,故研究合成对硝基甲苯邻磺酸的先进工艺路线具有较好的实用价值。对硝基甲苯磺化反应是亲电取代反应,甲基是给电子基团,对邻位的活化作用大于对位;硝基是吸电子基团,对邻位的钝化作用大于间位,虽然对硝基甲苯的苯环上有四个可直接被取代的氢,但磺化基团取代甲基邻位的氢发生磺化反应,其他位置极难发生磺化反应,一次磺化完成后,由于空间位阻效应,基本上没有二磺化。
3.目前对硝基甲苯邻磺酸的合成方法主要有高温烘焙法、三氧化硫/熔剂法、过量发烟硫酸法、氯磺酸法。高温烘焙法劳动量大,对硝基甲苯挥发和焦化现象比较严重;过量发烟硫酸法稀酸量多,处理难度大;氯磺酸虽然质量好,但氯磺酸价格昂贵,副产稀盐酸,生产操作复杂。三氧化硫/熔剂法是最近研究人员提出的一种新磺化工艺,由于该法增加了溶剂使用、回收等工艺,操作复杂,存在一定的安全风险,溶剂还存在被碳化、氧化的现象,影响产品质量,且溶剂损耗大,成本较高。近几年又有人采用50.0%或65.0%发烟硫酸磺化对硝基甲苯,磺化废酸量可以减少75.0%,但是采用50.0%或 65.0%发烟硫酸磺化pnt,存在局部的三氧化硫浓度过高,产品质量有待于提高。此外,上述工艺都采用间歇釜式反应,磺化时间长,过磺化现象比较严重,副产多,产业化现象存在诸多困难。
4.中国日用化学品工业研究院报道了一种对硝基甲苯的连续合成方法 (201810469086.0),其采用低浓度的三氧化硫做磺化试剂,低浓度的三氧化硫气体要高速通入膜式反应器中,由于对硝基甲苯非常容易升华,高速流动的高温气体很容易带出易升华的对硝基甲苯,降低产品的收率,并增加尾气处理的难度。同时三氧化硫要用干燥空气稀释,而制备干燥空气需要经过深度冷凝、干燥脱水等工艺,增加了生产成本。另外为了保证物料在膜反应器中有良好的流动性和均匀分散性,其需要使用有机溶剂或无机溶剂,后续需要增加溶剂回收、溶剂脱水等工艺。其还提到无机溶剂中的一种为浓硫酸,而作为溶剂使用的硫酸无法分离出来,最终转化为废稀硫酸,虽然和发烟硫酸相比废酸量会有所下降,但依然会产生较多的废酸。
5.目前国内企业依然是采用20%发烟硫酸磺化对硝基甲苯的传统釜式工艺生产对硝基甲苯邻磺酸,该工艺采用在反应釜中进行,反应时间长,生产效率低,副产的废酸量大,每吨产品副产6-8吨浓度50.0%左右的稀硫酸,稀硫酸颜色深,处理难度大。因此不管是经济成本还是环保角度考虑使用发烟硫酸磺化已经不能适应社会发展的需要。发烟硫酸磺化在2019年被列入限制目录。而清洁生产、本质安全的连续磺化、三氧化硫磺化新技术的开发和应用属于鼓励类。
技术实现要素:
6.本发明针对现有技术中存在的技术问题,提供一种利用动态管式反应器连续制备对硝基甲苯邻磺酸的方法,不仅生产成本低、工艺简单、安全性高、废酸量极少,可连续生产,而且生产效率、产品质量及收率高,此外不需要使用溶剂,生产工艺简化。
7.本发明解决上述技术问题的技术方案如下:
8.一种利用动态管式反应器连续制备对硝基甲苯邻磺酸的方法,包括如下步骤:
9.(1)将液态对硝基甲苯与三氧化硫体积浓度不低于50%的混合气体通入带有搅拌装置的动态管式反应器中分段磺化,其中对硝基甲苯与三氧化硫的摩尔比为1.0:1.02-1.20;
10.(2)磺化完成液经气液分离器分离,气体经过旋风、电除雾、酸洗、碱洗后排空,液体从气液分离器的底部排入水解釜,同时开启水解釜的搅拌装置,温度保持在100-120℃之间;
11.(3)水解釜中磺化完成液达到预设液位后,真空脱除游离三氧化硫;
12.(4)水解釜中磺化完成液脱除游离三氧化硫后,加入去离子水、稀酸母液,去离子水为磺化完成液质量的20-30%,稀酸母液量为磺化完成液质量的2-5倍,在90-120℃下水解45-120min,加入活性炭,在80-100℃下保温搅拌30-60min,趁热过滤,滤液送入结晶釜低温结晶,过滤得到对硝基甲苯邻磺酸晶体。
13.在上述技术方案的基础上,本发明还可以做如下改进。
14.进一步,步骤(3)中,真空脱除游离三氧化硫的具体操作如下:开启连接于水解釜的真空系统脱除游离三氧化硫,所述真空脱除的真空度为
ꢀ‑
0.1~-0.08mpa,时间为20-60min。
15.进一步,步骤(1)中,所述动态管式反应器的长度为1-3m,管式反应器置于换热区域中,换热区域分为三段,每段有独立的温控区域,每段换热区域对应反应器部分布有进气口,第一段除布有进气口外,还布有液体对硝基甲苯进料口,第三段除布有进气口外,还布有磺化完成液排液口和排气口。
16.进一步,步骤(1)中,混合气体分三部分进入动态管式反应器中,第一段三氧化硫通入量为三氧化硫总量的40-50%,第二段三氧化硫通入量为三氧化硫总量的30-40%,第三段三氧化硫通入量为三氧化硫总量的10-30%。
17.进一步,步骤(1)中,所述动态管式反应器分三段控温磺化,第一段磺化反应温度控制在60-85℃,第二段磺化反应温度控制在80-90℃,第三段磺化反应温度控制在90-110℃。
18.进一步,步骤(2)中,旋风、电除雾捕捉下来的液体回流到水解釜中水解。
19.进一步,步骤(2)中,所述酸洗的气体吸收液为45-55%稀酸母液,吸收气体后的稀酸母液用于磺化完成液的水解。
20.进一步,步骤(4)中,水解釜中加入硫酸浓度为5-50%的稀酸母液。
21.进一步,步骤(4)中,水解釜中加入硫酸浓度为45-50%的稀酸母液。
22.进一步,步骤(1)中,所述动态管式反应器的出口安装有电导率仪监控进程,电导率仪与动态管式反应器的搅拌速度连锁,通过调整搅拌速度保证对硝基甲苯完全磺化。
23.本发明的有益效果是:本发明不仅生产成本低、工艺简单、安全性高、废酸量极少,
每吨产品废酸量为10-30kg(硫酸浓度50-55%),可连续生产,而且生产效率、产品质量及收率高,此外不需要使用溶剂,生产工艺简单。
附图说明
24.图1为本发明所述动态管式反应器的结构示意图;
25.图2为本发明所述利用动态管式反应器连续制备对硝基甲苯邻磺酸的方法的工艺流程图。
具体实施方式
26.以下对本发明的原理和特征进行描述,所举实例只用于解释本发明,并非用于限定本发明的范围。
27.除非另有说明,本发明中所采用的百分数均为质量百分数。
28.本发明采用的原料及设备为本技术领域常规原料及设备(常规市售品),皆可于市场购得。
29.如图2所示,本发明所设计的一种利用动态管式反应器连续制备对硝基甲苯邻磺酸的方法,包括如下步骤:
30.(1)将液态对硝基甲苯与三氧化硫体积浓度不低于50%的混合气体通入带有搅拌装置的动态管式反应器中分段磺化,其中对硝基甲苯与三氧化硫的摩尔比为1.0:1.02-1.20;
31.(2)磺化完成液经气液分离器分离,气体经过旋风、电除雾、酸洗、碱洗后排空,液体从气液分离器的底部排入水解釜,同时开启水解釜的搅拌装置,温度保持在100-120℃之间;
32.(3)水解釜中磺化完成液达到预设液位后,真空脱除游离三氧化硫,,以减少稀酸的产生量;
33.(4)水解釜中磺化完成液脱除游离三氧化硫后,加入去离子水、稀酸母液,去离子水为磺化完成液质量的20-30%,稀酸母液量为磺化完成液质量的2-5倍,在90-120℃下水解45-120min,即得到对硝基甲苯邻磺酸溶液,向对硝基甲苯邻磺酸溶液中加入活性炭,在80-100℃下保温,搅拌30-60min,趁热过滤,滤液送入结晶釜低温结晶,过滤得到对硝基甲苯邻磺酸晶体。
34.控制去离子水的添加量,是为了保证能够长期保持体系的水平衡和稀酸平衡,同时产品的质量及收率能够控制在较佳的范围。本发明中,去离子水的用途主要有如下三个:1)提供对硝基甲苯邻磺酸产品需要的结晶水;2) 提供磺化完成液中没有脱除干净的三氧化硫转化为硫酸所需的水,以及硫酸转化为50-55%左右的稀酸所需要的水;3)提供对硝基甲苯邻磺酸产品需要的游离水。发明人经过充分研究和大量的实验,发现若要长期保持体系的水平衡和稀酸平衡,稀酸母液浓度不会高于55%外排,则去离子水的添加量不应少于磺化完成液的20%。偶尔一两次去离子水的添加量过少,对单次试验的结果不会有影响,因为上述三部分的水可以从加入的稀酸母液中获得,但若加入的水长期偏少,会导致母液的酸浓不断提高,产品结晶母液酸度大于 55%,从而导致产品粒度变细,携带的游离水含量增加,产品质量降低。而且去离子水的添加量不应多于磺化完成液的30%,这是由于若去离
子水的添加量过多,同时添加的稀酸母液浓度也较低的情况下,会影响到产品的收率。因此在本发明中,控制去离子水的添加量极为重要。
35.优选的,步骤(1)中,在60-110℃范围内分段磺化。为了提供三氧化硫浓度稳定的混合气体,本发明从硫酸系统工业硫酸吸收塔出口引入干燥空气来调节混合气体中的三氧化硫浓度。
36.本发明以动态管式反应器做磺化设备,高浓度三氧化硫气体做磺化试剂,三氧化硫气体和液态对硝基甲苯以接近理论摩尔比通过动态管式反应器,瞬间完成磺化反应,快速高效,产品质量较好、收率高,有效解决发烟硫酸磺化废硫酸产量大的问题,同时不需要使用溶剂,生产工艺简单。
37.在上述实施方式的基础上,本发明还具有优选的改进方案。
38.优选的,步骤(3)中,真空脱除游离三氧化硫的具体操作如下:开启连接于水解釜的真空系统脱除游离三氧化硫,所述真空脱除的真空度为
ꢀ‑
0.1~-0.08mpa,时间为20-60min。
39.优选的,如图1所示,步骤(1)中,所述动态管式反应器的长度为1-3m,管式反应器置于换热区域中,换热区域分为三段,每段有独立的温控区域,每段换热区域对应反应器部分布有进气口,第一段除布有进气口外,还布有液体对硝基甲苯进料口,第三段除布有进气口外,还布有磺化完成液排液口和排气口。
40.所述动态管式反应器采用三段式结构设计,能够使气液两相接触更加充分,实现减少三氧化硫气体用量的同时,确保三氧化硫气体与液态对硝基甲苯充分磺化,从而在提升产品质量及收率的同时,有效减少稀酸的产生量及废酸量。
41.步骤(1)中,混合气体分三部分进入动态管式反应器中,第一段三氧化硫通入量为三氧化硫总量的40-50%,第二段三氧化硫通入量为三氧化硫总量的30-40%,第三段三氧化硫通入量为三氧化硫总量的10-30%。
42.第一段、第二段、第三段通入三氧化硫的质量比采用上述设计是基于发明人研究的结果,不仅能够提高反应液在管式反应器中的流动性,同时有效防止过磺化现象发生。
43.步骤(1)中,根据原料和磺化物料的特性,发明人经过充分研究和实验的结果,将反应体系分阶段控温。具体而言,所述动态管式反应器的第一段磺化反应温度控制在60-85℃,第二段磺化反应温度控制在80-90℃,第三段磺化反应温度控制在90-110℃。
44.优选的,步骤(2)中,旋风、电除雾捕捉下来的液体回流到水解釜中进行水解回收,以进一步提高对硝基甲苯邻磺酸的收率,同时减少资源的浪费,此外不需要另外增加处理设备,能够降低生产成本。
45.优选的,步骤(2)中,所述酸洗的气体吸收液为45-55%稀酸母液,吸收气体后的稀酸母液用于磺化完成液的水解。
46.步骤(4)中,水解釜中加入硫酸浓度为5-50%的稀酸母液,优选的,水解釜中加入硫酸浓度为45-50%的稀酸母液,稀酸母液的加入量和硫酸浓度是反向关系。从而保证能够长期保持体系的水平衡和稀酸平衡的同时,进一步提升产品的收率。
47.本发明采用动态管式反应器做磺化设备替代釜式反应器,不使用溶剂的前提下,通过搅拌可以使气液两相充分接触,并推动磺化完成液向前流动,满足高粘度反应体系的要求。
48.为保证磺化反应的连续稳定运行,动态管式反应器中的磺化完成液从排液口排入气液分离器,不凝性气体从排气口排入旋风分离器,气液分离器底部出口连接有多台水解釜,连续磺化一段时间后,水解釜中磺化完成液收集到预设液位后,磺化完成液切入其他空水解釜。
49.优选的,在所述动态管式反应器的出口安装有电导率仪监控进程,电导率仪与动态管式反应器的搅拌速度连锁,当发现对硝基甲苯未完全磺化,及时调整搅拌速度,延长反应时间,反之加快搅拌速度,缩短反应时间,从而实现通过调整搅拌速度保证对硝基甲苯完全磺化。
50.以下是本发明具体实施例。
51.实施例1
52.采用槽罐车运入的液态对硝基甲苯通过泵输送储罐区,再经管道输送到生产区域的中间罐,用泵打入高位计量罐。对硝基甲苯的温度控制在 60-70℃,以防止对硝基甲苯凝固。
53.开启动态管式反应器的搅拌装置,开启b1、b2、b3换热介质进口阀门, c1、c2、c3换热介质出口阀门。然后再同时开启对硝基甲苯进料泵和混合气体风机,液态对硝基甲苯以25.0g/s速度从a1进料口连续匀速泵入动态管式反应器中,三氧化硫体积浓度为92%的混合气体分别以1.82l/s、1.82l/s、 0.91l/s速度从管式反应器的g1、g2、g3进气口引入动态管式反应器中磺化对硝基甲苯。此时对硝基甲苯与三氧化硫进入动态管式反应器的摩尔比为1: 1.02,第一段、第二段、第三段通入三氧化硫的质量比为4:4:2。通过调整b1、b2、b3换热介质进口阀门和c1、c2、c3换热介质出口阀门,分别把第一段磺化反应温度控制在70-75℃区域,第二段磺化反应温度控制在 80-90℃区域,第三段磺化反应温度控制在100-105℃区域。
54.不凝性气体从动态管式反应器的g4排气口排入旋风分离器,经旋风、电除雾、酸洗、碱洗后排空;磺化完成液从动态反应器a2排液口排入气液分离器,经气液分离器底部流入带搅拌装置的水解釜中,开启水解釜的搅拌装置并保持温度100-105℃。连续磺化120min,水解釜收集到285kg磺化完成液,开启连接于水解釜的真空系统脱除游离三氧化硫,同时磺化完成液切入另外一个空水解釜。
55.磺化完成液经真空脱除游离三氧化硫后,加入57kg去离子水和1200kg 硫酸浓度为15%的稀酸母液;105-110℃保温水解60min,加入活性炭,80-90℃保温搅拌60min,趁热过滤,滤液送入结晶釜低温结晶,过滤得到含游离水 3.4%,含两个结晶水的对硝基甲苯邻磺酸产品337kg;收率为98.1%,母液泵入储罐,用于下一批磺化完成液水解。
56.为了保证系统连续、正常运行,需要把磺化完成液中的游离三氧化硫以稀硫酸的形式及时从系统排出,本实施例每生产1吨对硝基甲苯邻磺酸产品,外排15kg,硫酸浓度50%的废酸母液。
57.实施例2
58.采用槽罐车运入的液态对硝基甲苯通过泵输送储罐区,再经管道输送到生产区域的中间罐,用泵打入高位计量罐。对硝基甲苯的温度控制在 60-70℃,以防止对硝基甲苯凝固。
59.开启动态管式反应器的搅拌装置,开启b1、b2、b3换热介质进口阀门, c1、c2、c3换
热介质出口阀门。然后再同时开启对硝基甲苯进料泵和混合气体风机,液态对硝基甲苯以25.0g/s速度从a1进料口连续匀速泵入动态管式反应器中,三氧化硫体积浓度为80%的混合气体分别以2.94l/s、1.76l/s、 1.18l/s速度从管式反应器的g1、g2、g3进气口引入动态管式反应器中磺化对硝基甲苯。此时对硝基甲苯与三氧化硫进入动态管式反应器的摩尔比为1: 1.15,第一段、第二段、第三段通入三氧化硫的质量比为5:3:2。通过调整b1、b2、b3换热介质进口阀门和c1、c2、c3换热介质出口阀门,分别把第一段磺化反应温度控制在80-85℃区域,第二段磺化反应温度控制在 85-90℃区域,第三段磺化反应温度控制在105-110℃区域。
60.不凝性气体从动态管式反应器的g4排气口排入旋风分离器,经旋风、电除雾、酸洗、碱洗后排空,旋风、电除雾捕捉下来的液体回流到水解釜中水解;磺化完成液从动态反应器a2排液口排入气液分离器,经气液分离器底部流入带搅拌装置的水解釜中,开启水解釜的搅拌装置并保持温度 110-120℃。连续磺化120min,水解釜收集到290kg磺化完成液,开启连接于水解釜的真空系统脱除游离三氧化硫,真空脱除的真空度为-0.09mpa,时间为40min,同时磺化完成液切入另外一个空水解釜。
61.磺化完成液经真空脱除游离三氧化硫后,加入72.5kg去离子水和870kg 硫酸浓度为45%的稀酸母液;100-105℃保温水解80min,加入活性炭,80-90℃保温搅拌40min,趁热过滤,滤液送入结晶釜低温结晶,过滤得到含游离水 3.5%,含两个结晶水的对硝基甲苯邻磺酸产品340kg;收率为98.8%,母液泵入储罐,用于下一批磺化完成液水解。
62.为了保证系统连续、正常运行,需要把磺化完成液中的游离三氧化硫以稀硫酸的形式及时从系统排出,本实施例每生产1吨对硝基甲苯邻磺酸产品,外排23kg,硫酸浓度52%的废酸母液。
63.实施例3
64.采用槽罐车运入的液态对硝基甲苯通过泵输送储罐区,再经管道输送到生产区域的中间罐,用泵打入高位计量罐。对硝基甲苯的温度控制在 60-70℃,以防止对硝基甲苯凝固。
65.开启动态管式反应器的搅拌装置,开启b1、b2、b3换热介质进口阀门, c1、c2、c3换热介质出口阀门。然后再同时开启对硝基甲苯进料泵和混合气体风机,液态对硝基甲苯以25.0g/s速度从a1进料口连续匀速泵入动态管式反应器中,三氧化硫体积浓度为70%的混合气体分别以3.5l/s、2.8l/s、 0.7l/s速度从管式反应器的g1、g2、g3进气口引入动态管式反应器中磺化对硝基甲苯。此时对硝基甲苯与三氧化硫进入动态管式反应器的摩尔比为1:1.2,第一段、第二段、第三段通入三氧化硫的质量比为5:4:1。通过调整 b1、b2、b3换热介质进口阀门和c1、c2、c3换热介质出口阀门,分别把第一段磺化反应温度控制在75-80℃区域,第二段磺化反应温度控制在80-85℃区域,第三段磺化反应温度控制在90-95℃区域。
66.不凝性气体从动态管式反应器的g4排气口排入旋风分离器,经旋风、电除雾、酸洗、碱洗后排空,旋风、电除雾捕捉下来的液体回流到水解釜中水解;磺化完成液从动态反应器a2排液口排入气液分离器,经气液分离器底部流入带搅拌装置的水解釜中,开启水解釜的搅拌装置并保持温度 110-115℃。连续磺化120min,水解釜收集到288kg磺化完成液,开启连接于水解釜的真空系统脱除游离三氧化硫,真空脱除的真空度为-0.1mpa,时间为20min,同时磺化完成液切入另外一个空水解釜。
67.磺化完成液经真空脱除游离三氧化硫后,加入86.4kg去离子水和576kg 硫酸浓度为50%的稀酸母液;90-95℃保温水解120min,加入活性炭,80-90℃保温搅拌50min,趁热过滤,滤液送入结晶釜低温结晶,过滤得到含游离水 3.6%,含两个结晶水的对硝基甲苯邻磺酸产品339kg;收率为98.4%,母液泵入储罐,用于下一批磺化完成液水解。
68.为了保证系统连续、正常运行,需要把磺化完成液中的游离三氧化硫以稀硫酸的形式及时从系统排出,本实施例每生产1吨对硝基甲苯邻磺酸产品,外排30kg,硫酸浓度53%的废酸母液。
69.实施例4
70.采用槽罐车运入的液态对硝基甲苯通过泵输送储罐区,再经管道输送到生产区域的中间罐,用泵打入高位计量罐。对硝基甲苯的温度控制在 60-70℃,以防止对硝基甲苯凝固。
71.开启动态管式反应器的搅拌装置,开启b1、b2、b3换热介质进口阀门, c1、c2、c3换热介质出口阀门。然后再同时开启对硝基甲苯进料泵和混合气体风机,液态对硝基甲苯以12.5g/s速度从a1进料口连续匀速泵入动态管式反应器中,三氧化硫体积浓度为50%的混合气体分别以1.8l/s、1.8l/s、 0.9l/s速度从管式反应器的g1、g2、g3进气口引入动态管式反应器中磺化对硝基甲苯。此时对硝基甲苯与三氧化硫进入动态管式反应器的摩尔比为1: 1.1,第一段、第二段、第三段通入三氧化硫的质量比为4:4:2。通过调整 b1、b2、b3换热介质进口阀门和c1、c2、c3换热介质出口阀门,分别把第一段磺化反应温度控制在60-65℃区域,第二段磺化反应温度控制在80-85℃区域,第三段磺化反应温度控制在95-100℃区域。
72.不凝性气体从动态管式反应器的g4排气口排入旋风分离器,经旋风、电除雾、酸洗、碱洗后排空;磺化完成液从动态反应器a2排液口排入气液分离器,经气液分离器底部流入带搅拌装置的水解釜中,开启水解釜的搅拌装置并保持温度115-120℃。连续磺化120min,水解釜收集到144kg磺化完成液,开启连接于水解釜的真空系统脱除游离三氧化硫,同时磺化完成液切入另外一个空水解釜。
73.磺化完成液经真空脱除游离三氧化硫后,加入36kg去离子水和425kg 硫酸浓度为30%的稀酸母液;110-120℃保温水解45min,加入活性炭, 90-100℃保温搅拌45min,趁热过滤,滤液送入结晶釜低温结晶,过滤得到含游离水3.5%,含两个结晶水的对硝基甲苯邻磺酸产品169kg;收率为 98.2%,母液泵入储罐,用于下一批磺化完成液水解。
74.为了保证系统连续、正常运行,需要把磺化完成液中的游离三氧化硫以稀硫酸的形式及时从系统排出,本实施例每生产1吨对硝基甲苯邻磺酸产品,外排20kg,硫酸浓度51%的废酸母液。
75.实施例5
76.采用槽罐车运入的液态对硝基甲苯通过泵输送储罐区,再经管道输送到生产区域的中间罐,用泵打入高位计量罐。对硝基甲苯的温度控制在60-70℃,以防止对硝基甲苯凝固。
77.开启动态管式反应器的搅拌装置,开启b1、b2、b3换热介质进口阀门, c1、c2、c3换热介质出口阀门。然后再同时开启对硝基甲苯进料泵和混合气体风机,液态对硝基甲苯以25.0g/s速度从a1进料口连续匀速泵入动态管式反应器中,三氧化硫体积浓度为60%的混合气体分别以2.88l/s、2.16l/s、 2.16l/s速度从管式反应器的g1、g2、g3进气口引入动态
管式反应器中磺化对硝基甲苯。此时对硝基甲苯与三氧化硫进入动态管式反应器的摩尔比为1: 1.06,第一段、第二段、第三段通入三氧化硫的质量比为4:3:3。通过调整b1、b2、b3换热介质进口阀门和c1、c2、c3换热介质出口阀门,分别把第一段磺化反应温度控制在65-70℃区域,第二段磺化反应温度控制在 85-90℃区域,第三段磺化反应温度控制在105-110℃区域。
78.不凝性气体从动态管式反应器的g4排气口排入旋风分离器,经旋风、电除雾、酸洗、碱洗后排空,旋风、电除雾捕捉下来的液体回流到水解釜中水解;磺化完成液从动态反应器a2排液口排入气液分离器,经气液分离器底部流入带搅拌装置的水解釜中,开启水解釜的搅拌装置并保持温度 105-110℃。连续磺化75min,水解釜收集到180kg磺化完成液,开启连接于水解釜的真空系统脱除游离三氧化硫,真空脱除的真空度为-0.08mpa,时间为60min,同时磺化完成液切入另外一个空水解釜。
79.磺化完成液经真空脱除游离三氧化硫后,加入45kg去离子水和900kg 硫酸浓度为5%的稀酸母液;95-100℃保温水解100min,加入活性炭,90-100℃保温搅拌30min,趁热过滤,滤液送入结晶釜低温结晶,过滤得到含游离水 3.3%,含两个结晶水的对硝基甲苯邻磺酸产品211kg;收率为98.2%,母液泵入储罐,用于下一批磺化完成液水解。
80.为了保证系统连续、正常运行,需要把磺化完成液中的游离三氧化硫以稀硫酸的形式及时从系统排出,本实施例每生产1吨对硝基甲苯邻磺酸产品,外排20kg,硫酸浓度50%的废酸母液。
81.实施例6
82.采用槽罐车运入的液态对硝基甲苯通过泵输送储罐区,再经管道输送到生产区域的中间罐,用泵打入高位计量罐。对硝基甲苯的温度控制在 60-70℃,以防止对硝基甲苯凝固。
83.开启动态管式反应器的搅拌装置,开启b1、b2、b3换热介质进口阀门, c1、c2、c3换热介质出口阀门。然后再同时开启对硝基甲苯进料泵和混合气体风机,液态对硝基甲苯以25.0g/s速度从a1进料口连续匀速泵入动态管式反应器中,三氧化硫体积浓度为80%的混合气体分别以1.76l/s、2.94l/s、 1.18l/s速度从管式反应器的g1、g2、g3进气口引入动态管式反应器中磺化对硝基甲苯。此时对硝基甲苯与三氧化硫进入动态管式反应器的摩尔比为1: 1.15,第一段、第二段、第三段通入三氧化硫的质量比为3:5:2。通过调整b1、b2、b3换热介质进口阀门和c1、c2、c3换热介质出口阀门,分别把第一段磺化反应温度控制在90-95℃区域,第二段磺化反应温度控制在 95-100℃区域,第三段磺化反应温度控制在100-105℃区域。
84.不凝性气体从动态管式反应器的g4排气口排入旋风分离器,经旋风、电除雾、酸洗、碱洗后排空;磺化完成液从动态反应器a2排液口排入气液分离器,经气液分离器底部流入带搅拌装置的水解釜中,开启水解釜的搅拌装置并保持温度110-120℃。连续磺化120min,水解釜收集到286kg磺化完成液,开启连接于水解釜的真空系统脱除游离三氧化硫,同时磺化完成液切入另外一个空水解釜。
85.磺化完成液经真空脱除游离三氧化硫后,加入71.5kg去离子水和858kg 硫酸浓度为45%的稀酸母液;100-105℃保温水解80min,加入活性炭, 80-90℃保温搅拌40min,趁热过滤,滤液送入结晶釜低温结晶,过滤得到含游离水3.7%,含两个结晶水的对硝基甲苯邻
磺酸产品336kg;收率为97.5%,母液泵入储罐,用于下一批磺化完成液水解。
86.为了保证系统连续、正常运行,需要把磺化完成液中的游离三氧化硫以稀硫酸的形式及时从系统排出,本实施例每生产1吨对硝基甲苯邻磺酸产品,外排25kg,硫酸浓度55%的废酸母液。
87.以上所述仅为本发明的较佳实施例,并不用以限制本发明,凡在本发明的精神和原则之内,所作的任何修改、等同替换、改进等,均应包含在本发明的保护范围之内。