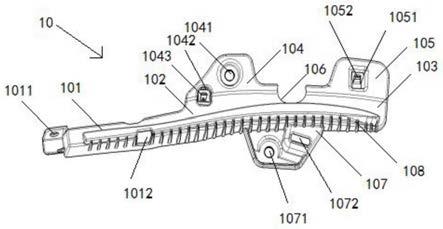
1.本技术涉及汽车配件技术领域,特别涉及一种非金属侧气帘导向支架及装配方法。
背景技术:
2.随着工业发展,对车辆被动安全的要求越来越高。一些高档车辆中会安装侧气帘保护车内乘员的安全,现有的侧气帘导向支架大多采用传统金属材质,成型工艺较复杂,需要多片钣金进行冲压并焊接,后续在车身上统一进行电泳处理,且材料成本较高。在要求整车轻量化以及降成本的前提下,非金属导向支架应运而生。
3.若使用塑料支架,与金属支架相比,其材料稳定性如强度、耐温性等表现较弱。在碰撞过程中,塑料支架存在支架破损或者掉落的问题,尤其是在低温点爆时,普通pp材料的支架会变得特别脆,从而增加了破损的概率。支架的破损会导致侧气帘展开无法按照既定轨迹展开,掉落在车身钣金和立柱内饰板之间,立柱内饰板受到侧气帘的强烈冲击导致立柱内饰板被打碎,不利于对乘员的保护。
4.因此,需要设计一种在低温环境中冲击性能好的侧气帘导向支架,使侧气帘在点爆过程中能顺利展开且不损坏自身以及内饰板,成功实现对乘员的侧面保护。
技术实现要素:
5.本技术实施例提供一种非金属侧气帘导向支架,该非金属侧气帘导向支架成本低、制作和安装工艺简单,在低温环境中具有良好的冲击性能。
6.第一方面,本技术提供了一种非金属侧气帘导向支架,包括支架本体,所述支架本体的制作材料为聚丙烯和玻璃纤维的混合物,所述支架本体上设置第一预装件和第二预装件,所述第一预装件和第二预装件分别卡接在顶棚内饰板上,所述支架本体与c柱内饰板卡接。
7.一些实施例中,所述支架本体包括支架本体左部,所述支架本体左部的端面上开设第一通孔和第二通孔,所述第一通孔与顶棚内饰板上的第一钣金孔配合,在所述第一通孔和顶棚内饰板上的第一钣金孔内插入螺栓进行紧固,所述第二通孔与c柱内饰板卡接。
8.一些实施例中,所述支架本体包括支架本体中部,所述支架本体中部的上端一体连接呈弧状分布的第一延伸部,所述第一延伸部上开设第三通孔和第四通孔,所述第三通孔与顶棚内饰板上的第二钣金孔配合,在第三通孔和顶棚内饰板上的第二钣金孔内插入螺栓进行紧固,所述第一预装件的固定端一体连接在第四通孔处,所述第一预装件的自由端卡设在顶棚内饰板上的第三钣金孔内。
9.一些实施例中,所述支架本体包括支架本体右部,所述支架本体右部的上端一体连接第二延伸部,所述第二延伸部上开设第五通孔,所述第二预装件的固定端一体连接在第五通孔处,所述第二预装件的自由端卡设在顶棚内饰板上的第四钣金孔内。
10.一些实施例中,所述支架本体的下方设置呈弧状分布的第三延伸部,所述第三延
伸部上开设第六通孔和第七通孔,所述第六通孔与c柱内饰板上的钣金孔配合,在第六通孔和c柱内饰板上的钣金孔内插入螺栓进行紧固,所述第七通孔与c柱内饰板卡接配合。
11.一些实施例中,所述支架本体上开设呈圆弧状的凹槽,所述凹槽用以避让顶棚内饰板。
12.一些实施例中,所述聚丙烯和玻璃纤维的质量比为4:1。
13.一些实施例中,所述支架本体采用注塑工艺制成。
14.一些实施例中,所述支架本体的端面上设置加强筋。
15.第二方面,本技术提供了上述非金属侧气帘导向支架的装配方法,包括以下步骤:
16.步骤s101,将第一预装件和第二预装件分别卡设在顶棚内饰板上,然后在支架本体上设置的第一通孔、第三通孔内插入螺栓,使支架本体与顶棚内饰板连接;
17.步骤s102,将c柱内饰板分别卡接在支架本体上设置的第二通孔和第七通孔内,然后在支架本体上设置的第六通孔内插入螺栓,使支架本体与c柱内饰板连接。
18.一些实施例中,所述支架本体的制作材料为聚丙烯和玻璃纤维的混合物。
19.一些实施例中,所述支架本体上开设呈圆弧状的凹槽,所述凹槽用以避让顶棚内饰板。
20.一些实施例中,所述聚丙烯和玻璃纤维的质量比为4:1。
21.一些实施例中,所述支架本体采用注塑工艺制成。
22.一些实施例中,所述支架本体的端面上设置加强筋。
23.本技术提供的技术方案带来的有益效果包括:本技术利用聚丙烯和玻璃纤维的混合物制作侧气帘导向支架,该混合物材料为热固性材料,悬臂梁缺口冲击强度高,使得侧气帘在高寒地区也能顺利点爆,避免因为低温材料变脆而有碎片飞出;本技术提供的侧气帘导向支架能够实现连接顶棚与c柱内饰板,保证顶棚与c柱内饰板无间隙。
附图说明
24.为了更清楚地说明本技术实施例中的技术方案,下面将对实施例描述中所需要使用的附图作简单地介绍,显而易见地,下面描述中的附图仅仅是本技术的一些实施例,对于本领域普通技术人员来讲,在不付出创造性劳动的前提下,还可以根据这些附图获得其他的附图。
25.图1为本技术实施例1提供的非金属侧气帘导向支架的结构示意图;
26.图2为本技术实施例1提供的非金属侧气帘导向支架的第一预装件的结构示意图;
27.图3为本技术实施例1提供的非金属侧气帘导向支架与顶棚内饰板、c柱内饰板的配合示意图。
28.图中:10、支架本体;101、支架本体左部;1011、第一通孔;1012、第二通孔;102、支架本体中部;103、支架本体右部;104、第一延伸部;1041、第三通孔;1042、第四通孔;1043、第一预装件;105、第二延伸部;1051、第五通孔;1052、第二预装件;106、凹槽;107、第三延伸部;1071、第六通孔;1072、第七通孔;108、加强筋;20、顶棚内饰板;30、c柱内饰板;40、侧气帘。
具体实施方式
29.为使本技术实施例的目的、技术方案和优点更加清楚,下面将结合本技术实施例中的附图,对本技术实施例中的技术方案进行清楚、完整地描述,显然,所描述的实施例是本技术的一部分实施例,而不是全部的实施例。基于本技术中的实施例,本领域普通技术人员在没有做出创造性劳动的前提下所获得的所有其他实施例,都属于本技术保护的范围。
30.实施例1:
31.本技术实施例1提供了一种非金属侧气帘导向支架,该非金属侧气帘导向支架成本低、制作和安装工艺简单,在低温环境中具有良好的冲击性能。
32.图1是本技术实施例1提供的非金属侧气帘导向支架的结构示意图,参考图1,该侧气帘导向支架包括支架本体10,该支架本体10的制作材料为聚丙烯和玻璃纤维按照质量比4:1混合而成的混合物,支架本体10的制作工艺为注塑成型。
33.参考图2和图3,支架本体10包括支架本体左部101、支架本体中部102和支架本体右部103,支架本体左部101的端面上开设第一通孔1011和第二通孔1012,第一通孔1011为圆形孔,第一通孔1011纵向贯穿支架本体左部101,第一通孔1011与顶棚内饰板20上的第一钣金孔配合,在第一通孔1011和顶棚内饰板20上的第一钣金孔内插入螺栓进行紧固,第二通孔1012横向贯穿支架本体左部101,第二通孔1012为方形孔,第二通孔1012与c柱内饰板30卡接,支架本体中部102的上端一体连接呈弧状分布的第一延伸部104,第一延伸部104上开设第三通孔1041和第四通孔1042,第三通孔1041和第四通孔1042均横向贯穿第一延伸部104,第三通孔1041为圆形孔,第四通孔1042为方形孔,第三通孔1041的开设位置高于第四通孔1042的开设位置,第三通孔1041与顶棚内饰板20上的第二钣金孔配合,在第三通孔1041和顶棚内饰板20上的第二钣金孔内插入螺栓进行紧固,第四通孔1042处设置第一预装件1043,第一预装件1043的固定端一体连接在第四通孔1042处,第一预装件1043呈弧状向内弯折,第一预装件1043与顶棚内饰板20上的第三钣金孔配合,第一预装件1043的自由端卡设在顶棚内饰板20上的第三钣金孔内,支架本体右部103的上端一体连接第二延伸部105,第二延伸部105上开设第五通孔1051,第五通孔1051为方形孔,第五通孔1051横向贯穿第二延伸部105,第五通孔1051处设置第二预装件1052,第二预装件1052的固定端一体连接在第五通孔1051处,第二预装件1052呈弧状向内弯折,第二预装件1052与顶棚内饰板20上的第四钣金孔配合,第二预装件1052的自由端卡设在顶棚内饰板20上的第四钣金孔内;本实施例中,第二预装件1052和第一预装件1043的形状、结构相同。
34.支架本体10上开设呈圆弧状的凹槽106,凹槽106位于支架本体中部102和支架本体右部103之间,第一延伸部104的边缘、凹槽106和第二延伸部105的边缘围合构成避让顶棚内饰板20的空间。
35.支架本体10的下方设置呈弧状分布的第三延伸部107,第三延伸部107的一端一体连接在支架本体中部102,第三延伸部107的另一端一体连接在支架本体右部103,第三延伸部107上开设第六通孔1071和第七通孔1072,第六通孔1071的开设位置低于第七通孔1072的开设位置,第六通孔1071为圆形孔,第七通孔1072为方形孔,第六通孔1071与c柱内饰板30上的钣金孔配合,在第六通孔1071和c柱内饰板30上的钣金孔内插入螺栓进行紧固,第七通孔1072与c柱内饰板30卡接配合。
36.本实施例中,支架本体10的端面为侧气帘40的导向面。
37.本实施例中,在支架本体10的端面上设置加强筋108以增强支架本体10与顶棚内饰板20连接的稳固性。
38.本实施例1还提供了一种非金属侧气帘导向支架的装配方法,包括以下步骤:
39.步骤s101,将第一预装件1043和第二预装件1052分别卡设在顶棚内饰板20上,然后在支架本体10上设置的第一通孔1011、第三通孔1041内插入螺栓,使支架本体10与顶棚内饰板20连接;
40.步骤s102,将c柱内饰板30分别卡接在第二通孔1012和第七通孔1072内,然后在支架本体10上设置的第六通孔1071内插入螺栓,使支架本体10与c柱内饰板30连接。
41.本技术实施例1采用的聚丙烯和玻璃纤维的混合材料的性能见表1。
42.表1:实施例1采用的聚丙烯和玻璃纤维的混合材料性能
[0043][0044][0045]
从表1可以看出,实施例1使用的聚丙烯和玻璃纤维的混合材料具有优异的机械性能和热性能。
[0046]
实施例2:
[0047]
本技术实施例2提供了一种非金属侧气帘导向支架,该非金属侧气帘导向支架成本低、制作和安装工艺简单,在低温环境中具有良好的冲击性能。
[0048]
本技术实施例2提供的非金属侧气帘导向支架的结构示意图参考图1-图3,该侧气帘导向支架包括支架本体10,该支架本体10的制作材料为聚丙烯和玻璃纤维按照质量比7:3混合而成的混合物,支架本体10的制作工艺为注塑成型。
[0049]
支架本体10包括支架本体左部101、支架本体中部102和支架本体右部103,支架本体左部101的端面上开设第一通孔1011和第二通孔1012,第一通孔1011为圆形孔,第一通孔
1011纵向贯穿支架本体左部101,第一通孔1011与顶棚内饰板20上的第一钣金孔配合,在第一通孔1011和顶棚内饰板20上的第一钣金孔内插入螺栓进行紧固,第二通孔1012横向贯穿支架本体左部101,第二通孔1012为方形孔,第二通孔1012与c柱内饰板30卡接,支架本体中部102的上端一体连接呈弧状分布的第一延伸部104,第一延伸部104上开设第三通孔1041和第四通孔1042,第三通孔1041和第四通孔1042均横向贯穿第一延伸部104,第三通孔1041为圆形孔,第四通孔1042为方形孔,第三通孔1041的开设位置高于第四通孔1042的开设位置,第三通孔1041与顶棚内饰板20上的第二钣金孔配合,在第三通孔1041和顶棚内饰板20上的第二钣金孔内插入螺栓进行紧固,第四通孔1042处设置第一预装件1043,第一预装件1043的固定端一体连接在第四通孔1042处,第一预装件1043呈弧状向内弯折,第一预装件1043与顶棚内饰板20上的第三钣金孔配合,第一预装件1043的自由端卡设在顶棚内饰板20上的第三钣金孔内,支架本体右部103的上端一体连接第二延伸部105,第二延伸部105上开设第五通孔1051,第五通孔1051为方形孔,第五通孔1051横向贯穿第二延伸部105,第五通孔1051处设置第二预装件1052,第二预装件1052的固定端一体连接在第五通孔1051处,第二预装件1052呈弧状向内弯折,第二预装件1052与顶棚内饰板20上的第四钣金孔配合,第二预装件1052的自由端卡设在顶棚内饰板20上的第四钣金孔内;本实施例中,第二预装件1052和第一预装件1043的形状、结构相同。
[0050]
支架本体10上开设呈圆弧状的凹槽106,凹槽106位于支架本体中部102和支架本体右部103之间,第一延伸部104的边缘、凹槽106和第二延伸部105的边缘围合构成避让顶棚内饰板20的空间。
[0051]
支架本体10的下方设置呈弧状分布的第三延伸部107,第三延伸部107的一端一体连接在支架本体中部102,第三延伸部107的另一端一体连接在支架本体右部103,第三延伸部107上开设第六通孔1071和第七通孔1072,第六通孔1071的开设位置低于第七通孔1072的开设位置,第六通孔1071为圆形孔,第七通孔1072为方形孔,第六通孔1071与c柱内饰板30上的钣金孔配合,在第六通孔1071和c柱内饰板30上的钣金孔内插入螺栓进行紧固,第七通孔1072与c柱内饰板30卡接配合。
[0052]
本实施例中,支架本体10的端面为侧气帘40的导向面。
[0053]
本实施例中,在支架本体10的端面上设置加强筋108以增强支架本体10与顶棚内饰板20连接的稳固性。
[0054]
本实施例2还提供了一种非金属侧气帘导向支架的装配方法,包括以下步骤:
[0055]
步骤s101,将第一预装件1043和第二预装件1052分别卡设在顶棚内饰板20上,然后在支架本体10上设置的第一通孔1011、第三通孔1041内插入螺栓,使支架本体10与顶棚内饰板20连接;
[0056]
步骤s102,将c柱内饰板30分别卡接在第二通孔1012和第七通孔1072内,然后在支架本体10上设置的第六通孔1071内插入螺栓,使支架本体10与c柱内饰板30连接。
[0057]
实施例3:
[0058]
本技术实施例3提供了一种非金属侧气帘导向支架,该非金属侧气帘导向支架成本低、制作和安装工艺简单,在低温环境中具有良好的冲击性能。
[0059]
本技术实施例3提供的非金属侧气帘导向支架的结构示意图参考图1-图3,该侧气帘导向支架包括支架本体10,该支架本体10的制作材料为聚丙烯和玻璃纤维按照质量比3:
1混合而成的混合物,支架本体10的制作工艺为注塑成型。
[0060]
支架本体10包括支架本体左部101、支架本体中部102和支架本体右部103,支架本体左部101的端面上开设第一通孔1011和第二通孔1012,第一通孔1011为圆形孔,第一通孔1011纵向贯穿支架本体左部101,第一通孔1011与顶棚内饰板20上的第一钣金孔配合,在第一通孔1011和顶棚内饰板20上的第一钣金孔内插入螺栓进行紧固,第二通孔1012横向贯穿支架本体左部101,第二通孔1012为方形孔,第二通孔1012与c柱内饰板30卡接,支架本体中部102的上端一体连接呈弧状分布的第一延伸部104,第一延伸部104上开设第三通孔1041和第四通孔1042,第三通孔1041和第四通孔1042均横向贯穿第一延伸部104,第三通孔1041为圆形孔,第四通孔1042为方形孔,第三通孔1041的开设位置高于第四通孔1042的开设位置,第三通孔1041与顶棚内饰板20上的第二钣金孔配合,在第三通孔1041和顶棚内饰板20上的第二钣金孔内插入螺栓进行紧固,第四通孔1042处设置第一预装件1043,第一预装件1043的固定端一体连接在第四通孔1042处,第一预装件1043呈弧状向内弯折,第一预装件1043与顶棚内饰板20上的第三钣金孔配合,第一预装件1043的自由端卡设在顶棚内饰板20上的第三钣金孔内,支架本体右部103的上端一体连接第二延伸部105,第二延伸部105上开设第五通孔1051,第五通孔1051为方形孔,第五通孔1051横向贯穿第二延伸部105,第五通孔1051处设置第二预装件1052,第二预装件1052的固定端一体连接在第五通孔1051处,第二预装件1052呈弧状向内弯折,第二预装件1052与顶棚内饰板20上的第四钣金孔配合,第二预装件1052的自由端卡设在顶棚内饰板20上的第四钣金孔内;本实施例中,第二预装件1052和第一预装件1043的形状、结构相同。
[0061]
支架本体10上开设呈圆弧状的凹槽106,凹槽106位于支架本体中部102和支架本体右部103之间,第一延伸部104的边缘、凹槽106和第二延伸部105的边缘围合构成避让顶棚内饰板20的空间。
[0062]
支架本体10的下方设置呈弧状分布的第三延伸部107,第三延伸部107的一端一体连接在支架本体中部102,第三延伸部107的另一端一体连接在支架本体右部103,第三延伸部107上开设第六通孔1071和第七通孔1072,第六通孔1071的开设位置低于第七通孔1072的开设位置,第六通孔1071为圆形孔,第七通孔1072为方形孔,第六通孔1071与c柱内饰板30上的钣金孔配合,在第六通孔1071和c柱内饰板30上的钣金孔内插入螺栓进行紧固,第七通孔1072与c柱内饰板30卡接配合。
[0063]
本实施例中,支架本体10的端面为侧气帘40的导向面。
[0064]
本实施例中,在支架本体10的端面上设置加强筋108以增强支架本体10与顶棚内饰板20连接的稳固性。
[0065]
本实施例3还提供了一种非金属侧气帘导向支架的装配方法,包括以下步骤:
[0066]
步骤s101,将第一预装件1043和第二预装件1052分别卡设在顶棚内饰板20上,然后在支架本体10上设置的第一通孔1011、第三通孔1041内插入螺栓,使支架本体10与顶棚内饰板20连接;
[0067]
步骤s102,将c柱内饰板30分别卡接在第二通孔1012和第七通孔1072内,然后在支架本体10上设置的第六通孔1071内插入螺栓,使支架本体10与c柱内饰板30连接。
[0068]
实施例4:
[0069]
本技术实施例4提供了一种非金属侧气帘导向支架,该非金属侧气帘导向支架成
本低、制作和安装工艺简单,在低温环境中具有良好的冲击性能。
[0070]
本技术实施例4提供的非金属侧气帘导向支架的结构示意图参考图1,该侧气帘导向支架包括支架本体10,该支架本体10的制作材料为聚丙烯和玻璃纤维按照质量比3:2混合而成的混合物,支架本体10的制作工艺为注塑成型。
[0071]
支架本体10包括支架本体左部101、支架本体中部102和支架本体右部103,支架本体左部101的端面上开设第一通孔1011和第二通孔1012,第一通孔1011为圆形孔,第一通孔1011纵向贯穿支架本体左部101,第一通孔1011与顶棚内饰板20上的第一钣金孔配合,在第一通孔1011和顶棚内饰板20上的第一钣金孔内插入螺栓进行紧固,第二通孔1012横向贯穿支架本体左部101,第二通孔1012为方形孔,第二通孔1012与c柱内饰板30卡接,支架本体中部102的上端一体连接呈弧状分布的第一延伸部104,第一延伸部104上开设第三通孔1041和第四通孔1042,第三通孔1041和第四通孔1042均横向贯穿第一延伸部104,第三通孔1041为圆形孔,第四通孔1042为方形孔,第三通孔1041的开设位置高于第四通孔1042的开设位置,第三通孔1041与顶棚内饰板20上的第二钣金孔配合,在第三通孔1041和顶棚内饰板20上的第二钣金孔内插入螺栓进行紧固,第四通孔1042处设置第一预装件1043,第一预装件1043的固定端一体连接在第四通孔1042处,第一预装件1043呈弧状向内弯折,第一预装件1043与顶棚内饰板20上的第三钣金孔配合,第一预装件1043的自由端卡设在顶棚内饰板20上的第三钣金孔内,支架本体右部103的上端一体连接第二延伸部105,第二延伸部105上开设第五通孔1051,第五通孔1051为方形孔,第五通孔1051横向贯穿第二延伸部105,第五通孔1051处设置第二预装件1052,第二预装件1052的固定端一体连接在第五通孔1051处,第二预装件1052呈弧状向内弯折,第二预装件1052与顶棚内饰板20上的第四钣金孔配合,第二预装件1052的自由端卡设在顶棚内饰板20上的第四钣金孔内;本实施例中,第二预装件1052和第一预装件1043的形状、结构相同。
[0072]
支架本体10上开设呈圆弧状的凹槽106,凹槽106位于支架本体中部102和支架本体右部103之间,第一延伸部104的边缘、凹槽106和第二延伸部105的边缘围合构成避让顶棚内饰板20的空间。
[0073]
支架本体10的下方设置呈弧状分布的第三延伸部107,第三延伸部107的一端一体连接在支架本体中部102,第三延伸部107的另一端一体连接在支架本体右部103,第三延伸部107上开设第六通孔1071和第七通孔1072,第六通孔1071的开设位置低于第七通孔1072的开设位置,第六通孔1071为圆形孔,第七通孔1072为方形孔,第六通孔1071与c柱内饰板30上的钣金孔配合,在第六通孔1071和c柱内饰板30上的钣金孔内插入螺栓进行紧固,第七通孔1072与c柱内饰板30卡接配合。
[0074]
本实施例中,支架本体10的端面为侧气帘40的导向面。
[0075]
本实施例中,在支架本体10的端面上设置加强筋108以增强支架本体10与顶棚内饰板20连接的稳固性。
[0076]
本实施例4还提供了一种非金属侧气帘导向支架的装配方法,包括以下步骤:
[0077]
步骤s101,将第一预装件1043和第二预装件1052分别卡设在顶棚内饰板20上,然后在支架本体10上设置的第一通孔1011、第三通孔1041内插入螺栓,使支架本体10与顶棚内饰板20连接;
[0078]
步骤s102,将c柱内饰板30分别卡接在第二通孔1012和第七通孔1072内,然后在支
架本体10上设置的第六通孔1071内插入螺栓,使支架本体10与c柱内饰板30连接。
[0079]
在本技术的描述中,需要说明的是,术语“上”、“下”等指示的方位或位置关系为基于附图所示的方位或位置关系,仅是为了便于描述本技术和简化描述,而不是指示或暗示所指的装置或元件必须具有特定的方位、以特定的方位构造和操作,因此不能理解为对本技术的限制。除非另有明确的规定和限定,术语“安装”、“相连”、“连接”应做广义理解,例如,可以是固定连接,也可以是可拆卸连接,或一体地连接;可以是机械连接,也可以是电连接;可以是直接相连,也可以通过中间媒介间接相连,可以是两个元件内部的连通。对于本领域的普通技术人员而言,可以根据具体情况理解上述术语在本技术中的具体含义。
[0080]
需要说明的是,在本技术中,诸如“第一”和“第二”等之类的关系术语仅仅用来将一个实体或者操作与另一个实体或操作区分开来,而不一定要求或者暗示这些实体或操作之间存在任何这种实际的关系或者顺序。而且,术语“包括”、“包含”或者其任何其他变体意在涵盖非排他性的包含,从而使得包括一系列要素的过程、方法、物品或者设备不仅包括那些要素,而且还包括没有明确列出的其他要素,或者是还包括为这种过程、方法、物品或者设备所固有的要素。在没有更多限制的情况下,由语句“包括一个
……”
限定的要素,并不排除在包括所述要素的过程、方法、物品或者设备中还存在另外的相同要素。
[0081]
以上所述仅是本技术的具体实施方式,使本领域技术人员能够理解或实现本技术。对这些实施例的多种修改对本领域的技术人员来说将是显而易见的,本文中所定义的一般原理可以在不脱离本技术的精神或范围的情况下,在其它实施例中实现。因此,本技术将不会被限制于本文所示的这些实施例,而是要符合与本文所申请的原理和新颖特点相一致的最宽的范围。