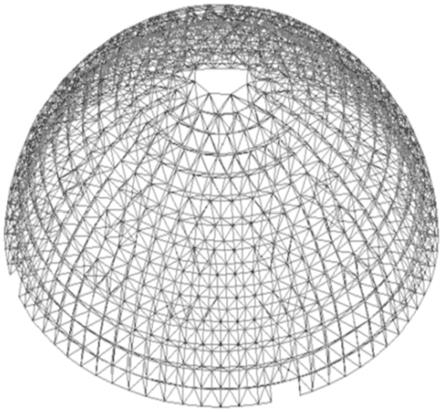
1.本发明涉及大跨度网架施工技术领域,尤其涉及一种大跨度球冠形螺栓球节点网架分块吊装施工方法。
背景技术:
2.露天堆场造成的扬尘污染已成为原料生产、运输、贮存过程中无组织排放的主要污染源。随着我国对环保要求的日益严格,国家环保政策明确要求各类储存料场必须进行全封闭。大跨度钢网架可以实现原料的全封闭储存和运输,避免扬尘现象对环境的污染,比传统的防风抑尘网更具优势。通常使用在煤矿、焦化厂、钢铁厂等污染比较严重的地方。但用于工业原料储仓的球冠形网架结构相较于其他网架结构而言空间跨度大,吊装作业半径大,高空作业难度大;建筑高度高,空中对接节点精度要求高;高空安全措施要求高。目前大跨度球网架的施工方法难以满足上述要求。
技术实现要素:
3.鉴于此,本发明的目的在于,提供一种大跨度球冠形螺栓球节点网架分块吊装施工方法,采用大跨度球冠形螺栓球节点网架地面拼装、分块吊装的施工方法,不仅缩短了施工工期,而且在施工过程可以减少对生产的影响。
4.为了达到上述发明目的,进而采取的技术方案如下:
5.大跨度球冠形螺栓球节点网架分块吊装施工方法,包括以下步骤:
6.步骤1、对网架构件进场进行验收;
7.步骤2、支承点进行放线、验线:首先检查混凝土柱强度,验收合格后在混凝土柱顶放线、验线,对网架支承点位置、尺寸进行复验,经复验检查轴线位置、标高尺寸符合设计要求后,把支座按照图纸及预埋板上的轴线标志,初步点焊固定;
8.步骤3、将底部两格网架分段地面拼装成中拼单元:将底部两格网架分为12段,每段网架分别在地面拼装成型,拼装好后采用吊车按照圆周顺序依次分段吊装至设计位置进行就位,同时采用缆风绳和临时固定支撑进行分段稳定加固,全部吊装完成后使底部两格网架形成一个圆圈的稳定体;
9.步骤4、第二圈网架在地面拼成小拼单元,依次吊装进行高空散装,然后将第二圈网架合拢;
10.步骤5、按照步骤4的方法拼装合拢第三圈网架,依次类推将剩余网架拼装完成;
11.步骤6、对拼装好的网架进行验收。
12.作为本发明的进一步改进,所述底部两格网架每段吊装长度为20.9m,重量为2.4吨,选用25t吊车,主臂长度33米,工作半径10米,吊车额定起重量为5.1吨,满足吊装要求。
13.作为本发明的进一步改进,吊装时采用四根钢丝绳,两根绑扎在下弦球点,另两根绑扎在上弦球节点并用两个5t倒链连接用于找平。
14.作为本发明的进一步改进,吊装网架时先要采用试吊,吊离地面200mm应检查吊具
是否牢稳,网架是否出现变形松动。
15.作为本发明的进一步改进,网架每段吊装至位置后,设置网架内侧支撑杆和网架外侧缆风绳,外侧缆风绳一端绑扎在支座处向上第三个上弦球,另一端固定在地锚上,缆风绳与地面夹角为40
°‑
50
°
,缆风绳通过倒链张紧。
16.本发明的有益效果是:采用大跨度球冠形螺栓球节点网架地面拼装、分块吊装的施工技术,不仅缩短了施工工期,而且在施工过程可以减少对生产的影响。
附图说明
17.构成本技术的一部分的附图用来提供对本发明的进一步理解,本发明的示意性实施例及其说明用于解释本发明,并不构成对本发明的不当限定。在附图中:
18.图1为本发明大跨度球冠形螺栓球节点网架的结构示意图;
19.图2为网架分段吊装吊点计算受力图;
20.图3为网架临时加固措施示意图,其中,(a)为第一视角网架临时加固措施示意图,(b)为第二视角网架临时加固措施示意图;
21.图4为缆风绳和临时支撑计算图;
22.图5为起步架吊装过程中临时加固示意图;
23.图6为起步架吊装过程中各工况吊装稳定性计算,其中,(a)为分段吊装第二段就位后第一段缆风绳和支撑杆的计算,(b)为第而段缆风绳和支撑杆的计算;
24.图7为起步架吊装过程示意图;
25.图8起步架合拢后受力分析图;
26.图9为网架吊装完成后的受力分析图。
具体实施方式
27.需要说明的是,在不冲突的情况下,本技术中的实施例及实施例中的特征可以相互组合。下面将参考附图并结合实施例来详细说明本发明。
28.为了使本技术领域的人员更好地理解本技术方案,下面将结合本技术实施例中的附图,对本技术实施例中的技术方案进行清楚、完整地描述,显然,所描述的实施例仅仅是本技术一部分的实施例,而不是全部的实施例。基于本技术中的实施例,本领域普通技术人员在没有做出创造性劳动前提下所获得的所有其他实施例,都应当属于本技术保护的范围。
29.如图1-9所示,大跨度球冠形螺栓球节点网架分块吊装施工方法,包括以下步骤:
30.步骤1、对网架构件进场进行验收;
31.步骤2、支承点进行放线、验线:首先检查混凝土柱强度,验收合格后在混凝土柱顶放线、验线,对网架支承点位置、尺寸进行复验,经复验检查轴线位置、标高尺寸符合设计要求后,把支座按照图纸及预埋板上的轴线标志,初步点焊固定;
32.步骤3、将底部两格网架分段地面拼装成中拼单元:将底部两格网架分为12段,每段网架分别在地面拼装成型,拼装好后采用吊车按照圆周顺序依次分段吊装至设计位置进行就位,同时采用缆风绳和临时固定支撑进行分段稳定加固,全部吊装完成后使底部两格网架形成一个圆圈的稳定体;
33.步骤4、第二圈网架在地面拼成小拼单元,依次吊装进行高空散装,然后将第二圈网架合拢;
34.步骤5、按照步骤4的方法拼装合拢第三圈网架,依次类推将剩余网架拼装完成;
35.步骤6、对拼装好的网架进行验收。
36.所述底部两格网架每段吊装长度为20.9m,重量为2.4吨,选用25t吊车,主臂长度33米,工作半径10米,吊车额定起重量为5.1吨,满足吊装要求。
37.吊装采用的设备是qy25k5-i吨汽车吊进行跨内吊装,不采用其余大型吊装设备,25t汽车吊满足40m以下高度的安装需要。当现场条件不允许相应的出杆角度时,应当预备一台50t汽车吊进行起吊装作业。
38.吊装时采用四根钢丝绳,两根绑扎在下弦球点,另两根绑扎在上弦球节点并用两个5t倒链连接用于找平。分段吊装吊点经计算后才可吊装,如图2所示。
39.吊装网架时先要采用试吊,吊离地面200mm应检查吊具是否牢稳,网架是否出现变形松动。如出现以上两种问题应及时整改方可继续起吊。钢丝绳采用《gb/t8918-2006》中6
×
19w+iwr-18.5mm,公称抗拉强度1670mpa,单根钢丝绳的破断拉力=18.5*18.5*1670*0.33/1000=185kn=18.5t。按6倍安全系数计算单根钢丝绳可以吊起:18.5t/6=3.14t的重物。网架重量为2.4吨满足吊装要求。
40.图2为利用midas/gen有限元分析软件对网架分段吊装吊点的计算受力图,通过计算可以得知起吊拉索内力,选择吊索直径。
41.网架每段吊装至位置后,如图3(a)、(b)所示,设置网架内侧支撑杆和网架外侧缆风绳,外侧缆风绳一端绑扎在支座处向上第三个上弦球,另一端固定在地锚上,缆风绳与地面夹角为40
°‑
50
°
,缆风绳通过倒链张紧。缆风绳和临时支撑计算如图4所示,分段吊装第一段就位后计算,通过midas/gen有限元分析软件计算,可以得知缆风绳和支撑杆所受反力,根据受力计算可以设计缆风绳和支撑杆的规格。
42.如图6所示,利用midas/gen有限元分析软件对分段吊装第二段就位后对第一段和第二段拉索和临时撑杆管的计算。如图5所示,支撑杆支点在两支座中间处第1个下弦球,使支点的平面位置及竖向高度能够在一定范围内调整。将支撑杆上端对下弦球节点进行定位,使网架能够准确定位。固定好后吊车脱钩,吊装下一段钢网架。
43.每段网架吊装就位后必须保证支撑杆和缆风绳固定牢固后方可落钩,每组装完一段,需检查人员检查所有支撑杆和缆风绳是否有松动情况,如有松动应及时加固整改。确保底层网架的准确合拢,使之具备较强刚度,给后续上部网架提供较好的安装条件。
44.支撑杆的设计设计根据网架下弦节点与砼平台间距确定支撑杆的最低高度为操作方便,宜结构简单、上下自如。
45.将支撑杆上端对上弦节点进行定位,使网架拼装既保证顺利实现,又起到消除拼装内应力的作用。杆件应力比较均匀,定位准确。
46.如图7-9所示,起步架安装完毕后,网架形成刚性整体,最终调整网架支座轴线到设计位置后,按照图纸的焊缝尺寸把支座底板与埋件进行焊接,焊接时为防止网架出现变形与应力,网架支座应对称焊接,这样起步阶段网架安装完毕。从图8可以看出:合拢后拉索张力很小,起步段临时支杆不拆除,结构基本自立。
47.应用实例:
48.本发明应用于山西省沁城煤矿原煤储煤场封闭工程。网架型式为球冠形螺栓球网架结构,网架为球冠型。球形网架外弦球支座轴线直径为80.0m,网架顶点高35.068m,网架净高31.118m。支座高0.45m,钢筋砼支柱高3.5m。网架支承方式采用外弦柱点支撑支承方式,设24个支座,每15
°
对应一个支座,支座中心布置在直径为80.0m的圆周上。开工日期为2019年05月20日,竣工日期为2019年11月30日。
49.以上所述仅为本发明的优选实施例而已,并不用于限制本发明,对于本领域的技术人员来说,本发明可以有各种更改和变化。凡在本发明的精神和原则之内,所作的任何修改、等同替换、改进、部件拆分或组合等,均应包含在本发明的保护范围之内。