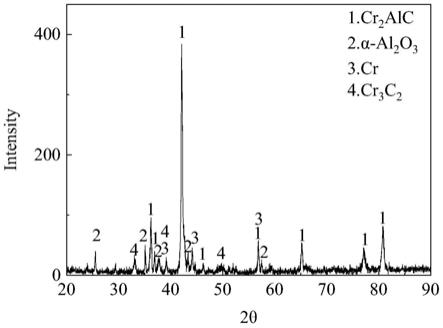
一种等离子熔覆增材制造的max相陶瓷材料及其制备方法
技术领域
1.本发明属于新型陶瓷材料技术领域,具体是一种max相陶瓷材料及其制备方法。
背景技术:
2.金属陶瓷,尤其是以碳化物和硼化物为增强相的金属陶瓷,在航空、航天、冶金、矿山、石油和化工等领域中的抗耐磨零部件的制造和修复中具有广泛的用途。其中,max相材料是一类具有六方晶格结构的三元纳米层状高性能陶瓷,cr2alc就是max相中的典型代表之一。这类材料不仅具有金属的高热导、高电导、高抗热震和易加工等性能,还具有陶瓷的高强度、高剪切模量、高杨氏模量、耐腐蚀、耐磨损及低密度等性能。在相对摩擦过程中,cr2alc表现出媲美石墨、mos2的自润滑性能。这些特性使得max相材料对于提升诸如燃气轮机、核电高温部件的性能及安全有重要意义。
3.目前,常用的max相金属陶瓷三维块体制备方法有热压烧结法、无压烧结法、脉冲放电烧结法、放电等离子烧结法、固液反应原位热压法、电弧熔化-退火法、高温自蔓延燃烧法、电场激活压力辅助燃烧合成法、液硅渗透法等,这些块体制备方法均存在工艺过程复杂、技术要求高及尺寸受限等的特点,随后将制得块体中以切削等加工方式产生零部件,这将极大影响max相金属陶瓷的性能及应用范围。
技术实现要素:
4.本发明的目的提供一种max相陶瓷材料及其制备方法,具有原材料易处理、制备工艺简单、制得块体尺寸受限少等优点。
5.为了实现上述目的,本发明采用了如下技术方案:
6.首先,本发明提供了一种max相陶瓷材料。
7.该max相陶瓷材料的原料包含cr、cr3c2和al,而且以摩尔比计,原料中cr︰al︰c=2︰(1.0~1.2)︰1。
8.优选的,以摩尔比计,原料中cr︰al︰c=2︰(1.05~1.2)︰1;更优的,以摩尔比计,原料中cr︰al︰c=2︰1.1︰1。由于等离子熔覆的高温条件下,al会发生挥发和烧蚀,所以应适当增加al的量。
9.优选的,所述原料通过等离子熔覆法堆焊制成块体,块体的尺寸为:20mm≤长度≤200mm,20mm≤宽度≤200mm,5mm≤厚度≤50mm。
10.其次,本发明还提供了上述max相陶瓷材料的具体制备方法。
11.该制备方法的步骤包括:
12.1)将cr、cr3c2和al的粉末混合;
13.2)将混合粉末用等离子熔覆,堆焊到导电基座上,焊枪由数控多轴机械臂控制,以获得所需要的块体形状和尺寸;
14.3)堆焊结束后保温缓冷。
15.步骤1)中,所述混合粉末的粒度优选为100~200目。
16.步骤2)中,所述等离子熔覆法的工艺条件为:喷嘴距离为8~12mm,焊接电流为260~280a,离子气流量为3~5l/min,送粉量为10~30g/min;离子气、保护气、送粉气均采用氩气。
17.步骤2)中,所述数控多轴机械臂至少具备x-y-z三维轨迹及摆动控制功能。优选的,焊枪摆动幅度为3~6mm,频率为0.5hz
18.步骤2)中,所述堆焊采用多层多道的焊道布置形式,焊道厚度为1~1.5mm。
19.步骤2)中,所述导电基座为低碳钢材料。
20.步骤3)中,所述保温缓冷采用硅酸铝保温棉进行。
21.本发明的有益效果是:
22.1)创新性地采用成本相对低廉的cr、cr3c2、al粉末作为熔覆材料,利用等离子弧作为热源,使得混合粉末在等离子弧和熔池中发生原位反应,一次性生成cr2alc max相金属陶瓷;制造的max相金属陶瓷具有耐磨性良好、耐熔盐腐蚀的特点。
23.2)制备过程结合数控多轴机械臂的精准控制,逐层堆积实现零部件的三维制造,该方法工艺性能良好、制造过程简单、成型精度高。
附图说明
24.图1为本发明实施例1所得max相陶瓷材料的xrd图谱。
25.图2为本发明实施例1所得max相陶瓷材料的断口形貌扫描电镜照片。
26.图3为本发明实施例1所得max相陶瓷材料的截面扫描电镜照片。
具体实施方式
27.下面将结合本发明实施例中的附图,对本发明实施例中的技术方案进行清楚、完整地描述,显然,所描述的实施例仅仅是本发明的优选实施例,而不是全部的实施例。
28.实施例1
29.max相陶瓷材料,通过以下步骤制得:
30.1)将cr、cr3c2、al粉末混合均匀,其中以摩尔比计,cr︰al︰c=2︰1.1︰1,经200℃烘焙1小时后待用,各种粉末的粒度为100~200目。粉末粒度过大易造成原位反应不彻底、cr2alc max相含量不足,粒度过小则易造成送粉不均匀、焊缝成形不良等缺陷。而且,原料组分之所以选用cr3c2,而不是纯单质的cr、al、c,是因为单质c的熔点较高,等离子熔覆时不易熔化,熔化需要耗费大量的能量,熔池保留时间段不利于原位反应的充分进行;此外,单质c密度较低,难以保证送粉的均匀性,同时由于c极易与空气中的氧反应发生烧蚀,导致最终进入涂层的含量偏低,不能满足形成max相。
31.2)选用低碳钢作为导电基座,以保证导电性,避免混入杂质,并要求表面平整、光洁,以防止锈、水等杂质混入块体,而影响cr2alc max相的性能。
32.3)使用等离子熔覆设备将混合后的粉末熔覆到导电基座上,主要工艺为:喷嘴距离9mm,以保证等离子电弧的刚性;焊接电流260a、离子气流量3l/min、送粉量10g/min。以此能保证适合的焊接热输入量及焊道之间的熔合,过小的热输入易形成层间未熔合、杂质偏析等缺陷,影响块体的结合强度;过大的热输入不仅影响块体的成型精度,更容易造成原先形成的cr2alc max相在长时间高温下分解、纯度下降,从而影响块体的性能;离子气、保护
气、送粉气均采用氩气,氩气是惰性气体,能保护熔池不被氧化。
33.4)熔覆时,焊枪由数控多轴机械臂控制,数控多轴机械臂至少具备x-y-z三维轨迹及摆动控制功能,焊枪摆动幅度4mm,频率0.5hz,通过多层多道的焊道布置形式进行堆焊,焊道厚度为1.0~1.5mm,焊接5~6层,最终获得高度5~6mm的块体。
34.5)堆焊结束后,采用硅酸铝保温棉包覆进行保温缓冷。
35.图1为实施例1所得max相陶瓷材料的xrd图,可见材料中主要含有cr2alc max相,仅仅含有微量的杂质相。图2为施例1所得材料的断口形貌扫描电镜照片,图中cr2alc max相的层状微观形貌特征明显。图3为实施例1所得材料的截面扫描电镜照片,图中显示为高纯度的cr2alc max相截面微观形貌。
36.实施例2
37.本实施例与实施例1的不同之处在于:步骤3)中,焊接电流为280a、送粉量15g/min,以获得单次不同厚度的焊道,提高熔覆效率。
38.实施例3
39.本实施例与实施例1的不同之处在于:步骤4)中,焊枪摆动幅度为6mm,频率为0.4hz,以获得单次不同宽度的焊道,调整块体的宽度。
40.实施例4
41.本实施例与实施例1的不同之处在于:步骤1)中,以摩尔比计,cr︰al︰c=2︰1.05︰1。采样该原料配比,同样可获得具有cr2alc max相的材料。
42.实施例5
43.本实施例与实施例1的不同之处在于:步骤1)中,以摩尔比计,cr︰al︰c=2︰1.2︰1。采样该原料配比,同样可获得具有cr2alc max相的材料。
44.显然,本领域的技术人员可以对本发明进行各种改动和变型而不脱离本发明的精神和范围。这样,倘若本发明的这些修改和变型属于本发明权利要求及其等同技术的范围之内,则本发明也意图包含这些改动和变型在内。