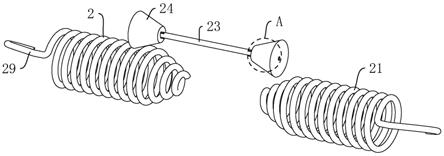
1.本技术涉及拉伸弹簧的领域,尤其是涉及一种拉伸弹簧制造工艺及应用该工艺制造的拉伸弹簧。
背景技术:
2.汽车的刹车相关结构中需要用到回位的拉伸弹簧,使得在制动结束后,拉伸弹簧能够将刹车片拉动复位以远离制动鼓,使得车辆不再处于刹车的状态以正常行驶。而刹车一般在市区内行驶使用频率较高,并且由于回位的拉伸弹簧靠近于车辆刹车片和制动鼓摩擦位置处,再加上外部例如夏季时的高温,使得拉伸弹簧容易处于200度甚至更高的温度下进行工作。
3.现有的车辆刹车回位用的拉伸弹簧较多使用碳素钢的钢丝进行卷绕制成,例如,我司现有所生产的一种拉伸弹簧,参照图1,包括呈螺旋状的弹簧左部1和呈螺旋状的弹簧右部11,弹簧左部1和弹簧右部11轴线相同,弹簧左部1和弹簧右部11相近一端一体成型有同一根连接丝12,弹簧左部1和弹簧右部11相背一端均一体成型有钩环13,钩环13、连接丝12、弹簧左部1、弹簧右部11由同一根碳素弹簧钢丝制造而成。
4.针对上述中的相关技术,发明人认为碳素钢的正常工作温度范围一般为-40~120度,低于车辆回位用拉伸弹簧的一个工作温度值,使得碳素钢弹簧长期在高温下工作时所能提供的拉力降低,存在拉伸弹簧热衰减较大的缺陷。
技术实现要素:
5.为了降低拉伸弹簧在高温下的热衰减,本技术提供一种拉伸弹簧制造工艺及应用该工艺制造的拉伸弹簧。
6.第一方面,本技术提供的一种拉伸弹簧制造工艺采用如下的技术方案:一种拉伸弹簧制造工艺,具体包括如下步骤。
7.步骤1、使用一根油淬火弹簧钢丝对应加工制成一个拉伸弹簧产品;步骤2、在280℃~380℃下保持0.5h~1h进行回火消应力;步骤3、对尺寸和性能进行检验;步骤4、对拉伸弹簧产品表面进行磷化处理;步骤5、包装。
8.通过采用上述技术方案,将原有的碳素钢材料选用油淬火材料进行替换,由此产生的拉伸产品能够满足在高温环境下低热衰减的使用要求。
9.可选的,所述步骤1油淬火弹簧钢丝c和si的含量降低且mn的含量以提高油淬火弹簧钢丝的塑性指标。
10.通过采用上述技术方案,油淬火处理后的弹簧原料钢丝虽然热衰减性能优异,并且强度提升,但是塑性降低,增加了拉伸弹簧产品进行绕制生产时难度,拉伸弹簧产品生产制造时容易出现断裂,成品率低,而通过改变弹簧原料钢丝中c、si和mn的含量,使得弹簧原
料钢丝的强度适当降低,塑性适当增加,以使得制得的油淬火弹簧钢丝进行拉伸弹簧产品的制造时难度降低,成品率获得提升。
11.可选的,所述步骤2之后对拉伸弹簧产品进行喷丸处理,然后再进行步骤3。
12.通过采用上述技术方案,油淬火弹簧钢丝进行卷簧端部弯钩的弯曲成型时,由于油淬火弹簧钢丝的强度较大并且塑性较低,使得弯钩处容易出现压痕,使得成型后的拉伸弹簧产品在使用过程中,弯钩存在压痕位置处容易出现断裂,使得拉伸弹簧产品的使用寿命降低,而通过喷丸将弯钩处的压痕去除,可有效提升拉伸弹簧产品的使用寿命。
13.可选的,所述拉伸弹簧产品喷丸处理后,将拉伸弹簧产品进行张拉,然后使用高压气枪将拉伸弹簧产品中的丸粒吹走,然后再进行步骤3。
14.通过采用上述技术方案,在拉伸弹簧产品完成喷丸后,将拉伸弹簧产品进行张拉,以将卡入拉伸弹簧中的丸粒吹走。
15.可选的,所述步骤1使用两根油淬火弹簧钢丝对应加工制成两个卷簧,两个卷簧之间连接一根杆以获得一个拉伸弹簧产品。
16.通过采用上述技术方案,进行背景技术中现有的一种拉伸弹簧的绕制时,弹簧左部和弹簧右部各自和连接丝连接处的弯折部分由于需要从原本的弧线转为直线,对弹簧钢丝的塑性要求较高,而油淬火弹簧钢丝的塑性相对较低,使得在弹簧左部或是弹簧右部弯折形成连接丝的位置处极易发生断裂,成品率极低,为此通过使用两根油淬火弹簧钢丝进行一个拉伸弹簧产品的两个卷簧部的绕设,然后再通过一根杆进行两个卷簧的连接以制成一个拉伸弹簧产品,可极大提升成品率。
17.第二方面,本技术提供的一种拉伸弹簧采用如下的技术方案:一种拉伸弹簧,应用上述一种拉伸弹簧制造工艺制造而成,包括由两根油淬火弹簧钢丝分别卷绕而成的弹簧左分部和弹簧右分部,弹簧左分部和弹簧右分部相背一端均设有分钩环,弹簧左分部和弹簧右分部之间设有同一根连接杆,连接杆两端均设有弹簧内块,两个弹簧内块一一对应分别位于弹簧左分部和弹簧右分部内,弹簧左分部和弹簧右分部相近一端内径减小并贴近于连接杆。
18.通过采用上述技术方案,弹簧内块位于弹簧左分部或是弹簧右分部内径减小处,使得弹簧内块难以从弹簧左分部或是弹簧右分部内径减小处脱离,使得弹簧左分部和弹簧右分部难以相远离,使得拉伸弹簧整体进行正常工作。
19.可选的,所述弹簧内块呈圆台型,弹簧内块远离连接杆一端的截面积大于弹簧内块靠近连接杆一端的截面积。
20.通过采用上述技术方案,使得弹簧内块圆周表面能够更好贴合于弹簧左分部或是弹簧右分部内径减小处,使得弹簧内块的周边不易对弹簧左分部或是弹簧右分部造成伤痕,使得弹簧左分部和弹簧右分部相近一端不易出现断裂的情况,有助于延长拉伸弹簧整体的使用寿命。
21.可选的,所述连接杆端部设有插接片,插接片插接于连接杆,弹簧内块背离连接杆的侧面穿设有螺纹连接于连接杆的连接螺丝。
22.通过采用上述技术方案,将连接杆和插接片对应插入至位于弹簧左分部或是弹簧右分部中的弹簧内块,然后将连接螺丝对应旋入,使得连接杆难以和弹簧内块相脱离,同时,插接片的存在使得连接杆难以出现随意转动的情况,使得连接杆和连接螺丝之间能够
保持较好的稳定连接。
23.可选的,所述连接杆端部同轴设有杆端螺丝,杆端螺丝螺纹连接于弹簧内块。
24.通过采用上述技术方案,使得在连接杆直径较小的情况下,不需要对连接杆端部进行开孔,以提升连接杆端部的强度,同时连接杆和弹簧内块之间也能保持较为稳定的连接。
25.可选的,所述杆端螺丝外露弹簧内块一端螺纹连接有抵紧块,抵紧块抵紧于弹簧内块。
26.通过采用上述技术方案,使得弹簧内块和连接杆之间不易出现相对转动,使得杆端螺丝和弹簧内块之间能够较好地保持稳定连接。
27.综上所述,本技术包括以下至少一种有益效果:1.将传统的碳素钢材料选用油淬火材料进行替换,由此产生的拉伸产品能够满足在高温环境下低热衰减的使用要求;2.通过使用两根油淬火弹簧钢丝进行一个拉伸弹簧产品的两个卷簧部的绕设,然后再通过一根杆进行两个卷簧的连接以制成一个拉伸弹簧产品,可极大提升成品率。
附图说明
28.图1是本技术背景技术中现有的一种拉伸弹簧的结构示意图;图2是实施例二中一种拉伸弹簧的结构,且将弹簧内块和连接杆沿弹簧左分部径向进行移动以远离弹簧左分部的部分爆炸示意图;图3是图2中a处放大图;图4是实施例三中一种拉伸弹簧的结构,且将弹簧内块和连接杆沿弹簧左分部径向进行移动以远离弹簧左分部的部分爆炸示意图。
29.附图标记说明:1、弹簧左部;11、弹簧右部;12、连接丝;13、钩环;2、弹簧左分部;21、弹簧右分部;23、连接杆;24、弹簧内块;25、插接片;26、连接螺丝;27、杆端螺丝;28、抵紧块;29、分钩环。
具体实施方式
30.以下结合附图对本技术作进一步详细说明。
31.实施例一:本技术实施例一公开一种拉伸弹簧制造工艺,具体包括如下步骤:步骤1、根据待制造的拉伸弹簧性能,选用对应热衰减指标和塑性指标均满足要求的油淬火材料进行油淬火弹簧钢丝的制造;步骤2、使用一根油淬火弹簧钢丝对应加工制成一个拉伸弹簧产品;步骤3、在280℃~380℃下保持0.5h~1h进行回火消应力;步骤4、对拉伸弹簧产品进行喷丸处理,喷丸结束后,将拉伸弹簧张拉,然后使用高压气枪对拉伸弹簧表面的丸粒清理;步骤5、对尺寸和性能进行检验;步骤6、对拉伸弹簧产品表面进行磷化处理;步骤7、包装。
32.其中,油淬火弹簧钢丝相较于传统的碳素弹簧钢丝,油淬火弹簧钢丝内部的c和si含量适当降低,可以降低弹簧原料钢丝的强度而提升塑性,同时油淬火弹簧钢丝内部的mn含量提升,可以使得在油淬火弹簧钢丝的强度获得提升的同时塑性不易产生较大的变化,继而使得本技术的油淬火弹簧钢丝最终的强度和塑性介于碳素钢材料和一般的油淬火材料之间,使得本技术的油淬火材料相较于一般的油淬火材料在进行拉伸弹簧的绕制过程中更加不易断裂,有助于成品率的提升。
33.本技术实施例一的一种拉伸弹簧制造工艺实施原理为:对传统的碳素弹簧钢丝进行材料上一定的改变,使得经过油淬火处理后形成的油淬火弹簧钢丝的强度和塑性保持一个较好的平衡,并且能够满足在高温下热衰减不易过大的要求。
34.实施例二:本技术实施例二公开一种拉伸弹簧制造工艺,与实施例一不同之处在于,步骤2中使用两根油淬火弹簧钢丝进分别进行卷绕,以获得同一拉伸弹簧的两个卷簧,两个卷簧之间安装一根钢杆进行连接,以形成一个拉伸弹簧产品。
35.本技术实施例二的一种拉伸弹簧制造工艺实施原理为:进行背景技术中现有的一种拉伸弹簧的绕制时,弹簧左部1和弹簧右部11各自和连接丝12连接处的弯折部分由于需要从原本的弧线转为直线,对弹簧钢丝的塑性要求较高,而油淬火弹簧钢丝的塑性相对较低,使得在弹簧左部1或是弹簧右部11弯折形成连接丝12的位置处极易发生断裂,成品率极低,为此通过使用两根油淬火弹簧钢丝进行一个拉伸弹簧产品的两个卷簧部的绕设,然后再通过一根杆进行两个卷簧的连接以制成一个拉伸弹簧产品,可极大提升成品率。
36.本技术实施例二还公开了一种拉伸弹簧,应用本实施例二的一种拉伸弹簧制造工艺制造而成,参照图2,包括呈卷簧状的弹簧左分部2和弹簧右分部21,弹簧左分部2和弹簧右分部21各自由一根油淬火弹簧钢丝卷绕而成,弹簧左分部2和弹簧右分部21相背一端均一体成型有分钩环29,分钩环29呈弯钩状。
37.参照图2和图3,弹簧左分部2和弹簧右分部21相近一端的内径逐渐减小,弹簧左分部2和弹簧右分部21相近一端内均安装有弹簧内块24,弹簧内块24呈圆台型,两个弹簧内块24相背一端的截面积大于两个弹簧内块24相近一端的截面积,两个弹簧内块24相近一端端面同轴插接有同一根连接杆23,弹簧左分部2和弹簧右分部21内径最小一端贴近于连接杆23圆周外壁。弹簧内块24背离连接杆23的侧面同轴穿设有连接螺丝26,连接螺丝26螺纹连接于连接杆23端部。
38.参照图2和图3,连接杆23端部圆周外壁绕自身轴线均匀固定连接有数个插接片25,插接片25沿连接杆23轴线方向紧密插接于弹簧内块24,使得连接杆23不易相对弹簧内块24出现随意转动,使得连接杆23和连接螺丝26之间能够更好保持紧密连接。弹簧左分部2和弹簧右分部21内径小的一端内径足够大,使得连接杆23设置插接片25一端能够顺利通过弹簧左分部2内径小的一端。
39.本技术实施例二的一种拉伸弹簧实施原理为:当连接杆23的直径较大时,用一根油淬火弹簧钢丝进行弹簧左分部2和对应的一个分钩环29的成型,再用另一根油淬火弹簧钢丝进行弹簧右分部21和对应的一个分钩环29的成型,然后在弹簧左分部2设置分钩环29一端处放入弹簧内块24,再将连接杆23从弹簧左分部2内径小的一端处插入,使得连接杆23和插接片25对应于弹簧内块24进行插接,再将连接螺丝26从弹簧内块24背离连接杆23的侧
面处旋入,然后弹簧右分部21中的弹簧内块24也是相同的方式和连接杆23进行连接,完成一个拉伸弹簧产品的装配过程。
40.实施例三:本技术实施例三公开了一种拉伸弹簧,和实施例二中的一种拉伸弹簧不同之处在于,连接杆23和弹簧内块24的可拆卸连接方式不同。
41.参照图4,连接杆23两端端面均同轴固定连接有杆端螺丝27,杆端螺丝27可顺利通过弹簧左分部2或是弹簧右分部21内径较小的一端处,杆端螺丝27穿设且螺纹连接于弹簧内块24,杆端螺丝27穿设弹簧内块24一端同轴螺纹连接有抵紧块28,抵紧块28抵紧于相近的弹簧内块24背离连接23的端面,使得杆端螺丝27和弹簧内块24之间不易随意转动。
42.本技术实施例三的一种拉伸弹簧实施原理为:当连接杆23的直径较小时,用一根油淬火弹簧钢丝进行弹簧左分部2和对应的一个分钩环29的成型,再用另一根油淬火弹簧钢丝进行弹簧右分部21和对应的一个分钩环29的成型,然后在弹簧左分部2设置分钩环29一端处放入弹簧内块24,将杆端螺丝27螺纹连接于弹簧内块24并穿出弹簧内块24,再将抵紧块28和杆端螺丝27穿出弹簧内块24一端进行螺纹连接,弹簧右分部21中的弹簧内块24和连接杆23也是相同设置,完成一个拉伸弹簧产品的装配过程。
43.以下为针对本技术中的一种拉伸弹簧和背景技术中现有的一种拉伸弹簧进行热衰减试验的数据。
44.选用弹簧初拉力均为p0=49n的传统碳素钢拉伸弹簧和新型油淬火拉伸弹簧,试验弹簧开始正常工作的长度,即使得刹车片和制动鼓刚好相接触时的长度为280mm。试验弹簧工作时的最大长度为322mm。试验条件为拉伸至322mm,在200℃保持16小时。然后进行试验弹簧拉伸至280mm时在试验前后的拉力值。
45.试验一:弹簧种类试验前(n)试验后(n)衰减量(n)衰减率传统碳素钢299.4121.6177.859.4%新型油淬火298.3229.7668.5423%试验二:弹簧种类试验前(n)试验后(n)衰减量(n)衰减率传统碳素钢252.9136.6116.346%新型油淬火254.3205.2249.0819.3%试验三:弹簧种类试验前(n)试验后(n)衰减量(n)衰减率传统碳素钢27114013148.3%新型油淬火272212.259.822%由三组试验结果可知,本技术使用油淬火弹簧钢丝制成的拉伸弹簧热衰减性能优异,相较于传统的碳素钢弹簧热衰减性能提升了50%以上。
46.以上均为本技术的较佳实施例,并非依此限制本技术的保护范围,故:凡依本技术的结构、形状、原理所做的等效变化,均应涵盖于本技术的保护范围之内。