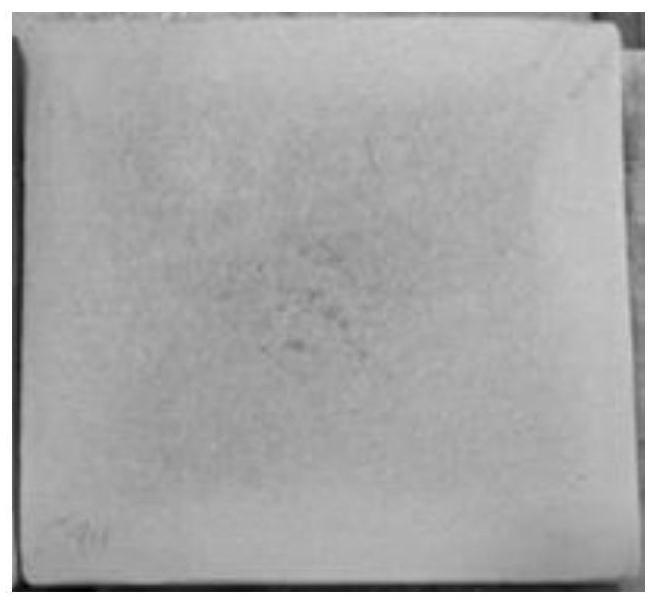
1.本发明属于碳素钢连铸坯制备技术领域,尤其涉及一种高均质碳素盘条用200方连铸坯的制备方法。
背景技术:
2.碳含量在0.35~0.65%之间的中碳碳素钢线材广泛用于加工低松弛预应力钢丝、钢丝绳、弹簧制品、钢绞线等。碳素钢线材的加工方法主要是拉拔,因此要求碳素钢母材具有优良的拉拔性能。在线材加工过程中产生拉拔断裂的主要原因是碳素钢母材局部出现碳偏析,并在冷却过程中形成马氏体组织所导致,因此在生产碳素盘条线材所用碳素钢铸坯时要控制铸坯的偏析情况。然而铸坯在凝固过程中存在自然选分结晶,导致铸坯微观组织中不可避免的存在碳化物偏析现象。如何通过综合控制碳素盘条用方坯连铸过程各工艺参数,对铸坯的偏析进行有效控制是本领域亟待解决的问题。
技术实现要素:
3.为解决现有碳素盘条线材用碳素钢连铸坯存在的碳化物偏析导致线材加工的拉拔性能较差的问题,本发明提供了一种高均质碳素盘条用200方连铸坯的制备方法。
4.本发明的技术方案:
5.一种高均质碳素盘条用200方连铸坯的制备方法,包括电炉/转炉冶炼、精炼和连铸;
6.电炉/转炉冶炼工艺:出钢碳不低于0.10%,出钢温度为1610~1640℃,出钢过程中先加入碳粉,再加入铝锭进行脱氧,出钢1/2时加入合金进行合金化;
7.精炼工艺:加入石灰、萤石、扩散脱氧剂碳化硅、碳粉、电石,出站成分达到内控,温度达到工艺要求即上台浇注;
8.连铸工艺:过热度25~30℃,拉坯速度控制为1.30m/min,结晶器水流量控制在120m3/min,二冷比水量0.53kg/t,分配比为36/39/25%,电磁搅拌的首端电磁搅拌参数为150a/2hz,搅拌强度为350.3gs,末端电磁搅拌参数为100a/8hz,搅拌强度为120gs,首端和末端电磁搅拌的搅拌方式均为连续搅拌,末端轻压下参数控制为3/4/5/3,总压下量为15mm。
9.进一步的,所述碳素盘条用200方连铸坯的化学成分按重量百分含量包括:c:0.35~0.70%、si:0.17~0.37%、mn:0.50~0.80%、p≤0.020%、s≤0.020%,其余为fe及不可避免杂质。
10.进一步的,所述电炉/转炉冶炼工艺中,出钢量为100~105t时,根据出钢碳及生产钢种的内控成分,先配入20%碳粉在包底,随着出钢的进行将剩余所需碳粉加入到钢水中;出钢20t时加入硅钙钡60kg/t、铝锭80kg/t,出钢40t时加入石灰600kg/t;
11.进一步的,所述电炉/转炉冶炼工艺中,合金提前烘烤至900~1000℃再加入钢水中进行合金化。
12.进一步的,所述精炼工艺中,出钢量为100~105t时,加入石灰0~200kg/t,萤石0~200kg/t,扩散脱氧剂碳化硅30kg/t,碳粉10kg/t,电石40kg/t。
13.进一步的,所述连铸工艺使用弧形半径为10m的六机六流200*200连铸机进行生产。
14.进一步的,所述连铸工艺使用的中间包为40t中间包,连铸生产前对中间包进行吹氩操作,减少中间包内的氧含量。
15.进一步的,所述连铸工艺的浇注液面控制在不低于850mm。
16.进一步的,所述结晶器工装水缝控制在4
±
0.2mm,铜管内壁镀铬层良好,结晶器进水压力控制在0.90mpa以上,结晶器水流速控制在9.5m/s,结晶器进水温差控制在6
±
0.2℃。
17.进一步的,所述轻压下区间的末端凝固系数为0.3~0.9。
18.本发明的有益效果:
19.本发明提供为了一种高均质碳素盘条用200方连铸坯的制备方法,通过精确控制冶炼、精炼和浇注过热度、拉坯速度、冷却速度、电磁搅拌与轻压下等连铸工艺参数,使轻压下与铸坯的凝固收缩精确匹配,改善铸坯的中心疏松、缩孔和偏析等缺陷,提高了碳素钢铸坯的成分均匀性和中心致密性,实现了碳素钢连铸坯成分均质化,为后续轧钢生产碳素盘条等线材提供了优质的母材。
20.本发明提供的连铸工艺操作简便,不需要增加成本及工序,极大提高了轻压下的压下效率,将压下效率提高了40%以上,所得碳素盘条用200方连铸坯的低倍评级中心疏松为1级,整体偏析指数控制在0.950~1.080。
附图说明
21.图1为实施例3所得碳素钢连铸坯低倍试样1的横向低倍试样照片;
22.图2为实施例3所得碳素钢连铸坯低倍试样2的横向低倍试样照片;
23.图3为实施例3所得碳素钢连铸坯低倍试样3的横向低倍试样照片;
24.图4为实施例3所得碳素钢连铸坯低倍试样4的横向低倍试样照片;
25.图5为实施例3所得碳素钢连铸坯低倍试样5的横向低倍试样照片;
26.图6为实施例3所得碳素钢连铸坯低倍试样6的纵向低倍试样照片;
27.图7为实施例3所得碳素钢连铸坯低倍试样7的纵向低倍试样照片;
28.图8为实施例3所得碳素钢连铸坯低倍试样8的纵向低倍试样照片;
29.图9为实施例3生产过程中抽取5炉试样所得碳素钢连铸坯的整体偏析检验结果对比图;
30.图10为对比例1所得碳素钢连铸坯低倍试样的横向低倍试样照片;
31.图11为对比例1所得碳素钢连铸坯低倍试样的纵向低倍试样照片。
具体实施方式
32.下面结合实施例对本发明的技术方案做进一步的说明,但并不局限于此,凡是对本发明技术方案进行修改或者等同替换,而不脱离本发明技术方案的精神和范围,均应涵盖在本发明的保护范围中。下列实施例中未具体注明的工艺设备或装置均采用本领域内的
常规设备或装置,若未特别指明,本发明实施例中所用的原料等均可市售获得;若未具体指明,本发明实施例中所用的技术手段均为本领域技术人员所熟知的常规手段。
33.实施例1
34.本实施例提供了一种高均质碳素盘条用200方连铸坯的制备方法,包括电炉/转炉冶炼、精炼和连铸;
35.电炉/转炉冶炼工艺:出钢碳不低于0.10%,出钢温度为1610~1640℃,出钢过程中先加入碳粉,再加入铝锭进行脱氧,出钢1/2时加入合金进行合金化;
36.精炼工艺:加入石灰、萤石、扩散脱氧剂碳化硅、碳粉、电石,出站成分达到内控,温度达到工艺要求即上台浇注;
37.连铸工艺:过热度25~30℃,拉坯速度控制为1.30m/min,结晶器水流量控制在120m3/min,二冷比水量0.53kg/t,分配比为36/39/25%,电磁搅拌的首端电磁搅拌参数为150a/2hz,搅拌强度为350.3gs,末端电磁搅拌参数为100a/8hz,搅拌强度为120gs,首端和末端电磁搅拌的搅拌方式均为连续搅拌,末端轻压下参数控制为3/4/5/3,总压下量为15mm。
38.实施例2
39.为了在冶炼和精炼工艺中进一步提高钢水的成分均匀性,本实施例提供了一种高均质碳素盘条用200方连铸坯的制备方法,包括电炉/转炉冶炼、精炼和连铸。
40.电炉/转炉冶炼工艺:
41.初炼炉冶炼使用85%的铁水与15%的废钢,出钢量控制在100~105t,铁水成分控制为:p≤0.12%、si:0.30~0.65%、s≤0.045%;铁水温度不低于1200℃,使其释放出最大的热能,保证出钢c≥0.10%、p≤0.012%,出钢温度为1610-1640℃。
42.根据出钢碳及生产钢种的内控成分,先配入20%碳粉在包底,随着出钢的进行将剩余所需碳粉加入到钢水中;出钢20t时加入硅钙钡60kg/t、铝锭80kg/t,出钢40t时加入石灰600kg/t,保证化渣良好,不结壳。
43.碳粉与钢水中的氧发生反应,生成co2,再向钢中加入铝锭进行沉淀脱氧,充分做好沉淀脱氧工作,保证钢中的氧含量在一定的时间内完成脱氧效果,可有效的提高金属收得率与到铝成分的控制。
44.合金提前进行烘烤,烘烤至900~1000℃再加入钢水中进行合金化,保证与钢水接触时减少钢水的热量损失,做好深脱氧最大限度的保证合金收得率。出钢40t时加入合金,按钢种成分要求的下线
±
2进行调整,保证到位成分为精炼提供有利条件。
45.精炼工艺:
46.加入石灰0~200kg/t,萤石0~200kg/t,扩散脱氧剂碳化硅30kg/t,碳粉10kg/t,电石40kg/t,精炼位1次给电后出站成分达到内控,温度达到工艺要求即可上台浇注,无需进入真空工序,有效的降低生产成本。本实施例当温度达到钢水过热度25
±
3℃即可吊包上台。
47.连铸工艺:过热度25~30℃,拉坯速度控制为1.30m/min,结晶器水流量控制在120m3/min,二冷比水量0.53kg/t,分配比为36/39/25%,电磁搅拌的首端电磁搅拌参数为150a/2hz,搅拌强度为350.3gs,末端电磁搅拌参数为100a/8hz,搅拌强度为120gs,首端和末端电磁搅拌的搅拌方式均为连续搅拌,末端轻压下参数控制为3/4/5/3,总压下量为
15mm。
48.实施例3
49.为了进一步精确控制连铸工艺参数,改善铸坯的偏析,本实施例提供了一种高均质碳素盘条用200方连铸坯的制备方法,包括电炉/转炉冶炼、精炼和连铸。
50.电炉/转炉冶炼工艺:
51.初炼炉冶炼使用85%的铁水与15%的废钢,总体装炉控制在110
±
3吨,铁水成分控制为:p≤0.12%、si:0.30~0.65%、s≤0.045%;铁水温度不低于1200℃,使其释放出最大的热能,保证出钢c≥0.10%、p≤0.012%,出钢温度为1640℃。
52.根据出钢碳及生产钢种的内控成分,需要碳粉180kg/t,先配入20%碳粉在包底,随着出钢的进行将剩余所需碳粉加入到钢水中;出钢20t时加入硅钙钡60kg/t、铝锭80kg/t,出钢40t时加入石灰600kg/t,保证化渣良好,不结壳。
53.合金提前进行烘烤,烘烤至900~1000℃再加入钢水中进行合金化,保证与钢水接触时减少钢水的热量损失,做好深脱氧最大限度的保证合金收得率。出钢40t时加入合金,按钢种成分要求的下线
±
2进行调整,保证到位成分为精炼提供有利条件。
54.精炼工艺:
55.加入石灰100kg/t,萤石100kg/t,扩散脱氧剂碳化硅30kg/t,碳粉10kg/t,电石40kg/t,精炼位1次给电后出站成分达到内控,温度达到工艺要求即可上台浇注,无需进入真空工序,有效的降低生产成本。本实施例当温度达到钢水过热度25
±
3℃即可吊包上台。
56.连铸工艺:
57.本实施例使用弧形半径为10m的六机六流200*200连铸机进行生产,中间包使用40t,连铸生产前对中间包进行吹氩操作,减少中间包内的氧含量,从而减少钢水二次氧化。
58.本实施例使用较大的中间包能够有效的控制分流钢水,同时可将钢水的多余的夹杂物上浮,改善钢水的纯净度。浇注液面控制在850mm以上,增加钢水在中间包内的停留时间,使夹杂物充分上浮。浇注过程中使用双氩封保护浇注长水口,防止钢水与空气接触造成二次氧化形成氧化类的夹杂物,污染钢水。
59.本实施例连铸工艺浇注过程中严格控制浇注温度,保证恒温恒速,过程不易过多的调整拉速,能够有效的控制铸坯内部质量和成分的均匀性。
60.采用过热度30℃,过热度过低容易影响末端凝固位置,造成轻压下与末端电磁搅拌无法发挥预期效果。本实施例根据连铸机的弧形半径和进矫直温度,将拉坯速度控制为1.30m/min,能够保证轻压下末端凝固系数在0.3~0.9。
61.拉坯速度和温度是控制铸坯质量的重要因素,本实施例通过过热度和拉坯速度的控制降低铸坯成分偏析,同时稳定末端凝固位置,配合轻压下使铸坯质量达到预期的效果。
62.合理控制冷却是解决铸坯偏析的重要手段。本实施例使用的结晶器工装水缝控制在4
±
0.2mm,铜管内壁镀铬层良好,结晶器进水压力控制在0.90mpa以上,结晶器水流量控制在120m3/min,结晶器水流速控制在9.5m/s,结晶器进水温差控制在6
±
0.2℃。保证结晶器一次冷却均匀,初生坯壳满足要求。
63.在控制冷却过程中,若二冷强度不够,铸坯回温大,柱状晶在生长过程中体积膨胀不断扩张,以造成铸坯鼓肚及凹陷,产生角裂缺陷。若二冷强度太大,铸坯在凝固过程中柱状晶发达,影响铸坯内部组织及成分的均匀性,甚至穿晶。为保证冷却强度足够,本实施二
次冷却使用动态分配比稳定浇注拉速1.30m/min,比水量0.53kg/t,使用7段喷淋环进行分配,分配比为36/39/25%分为3区,保证铸坯在二冷段反复回温均匀,防止产生的热应力造成铸坯皮下裂纹缺陷。
64.电磁搅拌作为改善铸坯偏析指数的重要技术,一方面抑制柱状晶发展、促进成分均匀与夹杂物上浮细化的热力学和动力学条件,进而控制铸坯凝固组织改善铸坯质量;另一方面增加钢液流动,提高了凝固相间的热传递,有利于降低过热度,减小凝固前沿的温度梯度,抑制了柱状晶的定向增大。
65.本实施例电磁搅拌控制参数具体为:首端电磁搅拌参数为150a/2hz,搅拌强度为350.3gs,搅拌方式为连续搅拌,适当的增加搅拌强度可有效控制结晶器钢水过热度降低,同时促进激冷的层的生长,保证铸坯表面质量。末端电磁搅拌参数为100a/8hz,搅拌强度为120gs,首端和末端的电磁搅拌的搅拌方式均为连续搅拌,末端电磁搅拌可有效控制铸坯进入末端电磁搅拌时铸坯液芯的大小,通过末端电磁搅拌促进钢液对流,消除晶间的搭桥,消除因选分结晶造成的钢液各成分浓度不均匀现象,从而减轻铸坯中心偏析和中心疏松,扩大等轴晶区域,消除铸坯的v型偏析,提高铸坯的内部质量。
66.考虑到连铸生产过程中的稳定性和有效发挥轻压下的作用,本实施例在拉坯速度1.30m/min的基础上进入拉矫机的压下区间,保证凝固末端凝固系数在0.3~0.9,将末端轻压下参数控制为3/4/5/3,总压下量为15mm。在合理的压下区间范围内适当的增加压下量能够明显改善铸坯内部组织,适当增加总压下量将缩孔压实,使铸坯质量更加稳定。
67.对本实施例生产的高碳铬轴承高大方坯进行质量检验,具体检验方法如下:
68.(一)低倍质量检验:将铸坯连续切割5~10块低倍试样,表面经加工后,进行热酸洗后进行评级。同时加取纵向试样。
69.低倍质量检验结果:图1-图5为低倍试样1-5的横向低倍试样照片和图6-图8为铸坯试样6-8的纵向低倍试样照片。如图所示铸坯的低倍评级为中心疏松≤1级、缩孔<0.5级、其余缺陷为0,纵向低倍试样无明显的v型偏析。
70.(二)偏析检验:生产过程共计抽取5炉试样,分别对垂直面、横截面、对角线过中心分别间隔20mm/点,采用“米”字钻点方法间隔2cm/点。使用~φ5钻头进行钻点取沫,使用红外碳硫分析仪进行检验实际碳含量。计算公式:偏析指数=各点c含量/中间包熔炼c含量。
71.偏析检验结果如图9所示,铸坯的偏析指数控制在0.950~1.080。
72.对比例1
73.本对比例与实施例3的区别仅在于:
74.连铸工艺:过热度33℃,拉坯速度控制为1.30m/min,结晶器水流量控制在130m3/min,二冷比水量0.53kg/t,分配比为36/39/25%,电磁搅拌的首端电磁搅拌参数为260a/3hz,搅拌强度为350.3gs,搅拌方式为连续搅拌,末端电磁搅拌参数为350a/5hz,搅拌强度为120gs,末端轻压下参数控制为6/0/6/4,总压下量为14mm。
75.图10为本对比例所得碳素钢连铸坯低倍试样的横向低倍试样照片;图11为本对比例所得碳素钢连铸坯低倍试样的纵向低倍试样照片,如图所示,铸坯的低倍评级为中心疏松为1级、缩孔0.5级、其余缺陷为0,纵向低倍试样中心部位可见典型的v型偏析。对对比例1制备的碳素钢连铸坯进行整体偏析检验,对比例1碳素钢连铸坯的偏析指数为0.980~
1.250。