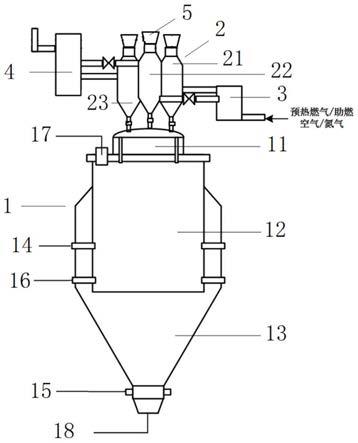
1.本发明涉及还原铁冶炼技术领域,特别涉及一种基于外部预热炉料的氢气竖炉炼铁装置及其炼铁方法。
背景技术:
2.钢铁行业作为能源密集型行业,能源消耗量巨大,且碳排放量也占到了碳排放总量的15%左右,而炼铁环节的碳排放又占钢铁行业中碳排放总量的80%以上。因此,降低炼铁工序的碳排放是实现炼铁行业可持续发展的关键。而以氢能为主的氢冶金炼铁工艺因为其具有生产效率高,绿色低碳,产品品质好等优点,被认为是目前减少炼铁行业碳排放量、促进冶铁行业可持续发展的重要途径。
3.氢冶金一般是指入炉还原气含氢量大于55%(h2/co大于1.5)条件下还原铁矿石、球团矿生产直接还原铁(dri)的氢气竖炉直接还原工艺,属于短流程工艺,以氢代替碳作为主要还原剂,更没有焦炭的消耗,成为世界上炼铁研发的热点。目前世界上氢冶金直接还原炼铁工艺的应用非常广泛,主要有midrex、hyl
‑ⅲ
、pered等工艺,生产过程中h2还原会大量吸热,生产一吨直接还原铁通常需要1800m3的富氢还原气,纯氢竖炉还原的入炉氢气量甚至高达2400m3/t。由于目前氢冶金炼铁的氢气消耗量大,且生产效率相对比较低,而且氢气的制造成本还比较高,因此目前氢冶金炼铁的生产成本比较高,经济效益相对较低。
4.当前公开的许多氢气还原炼铁工艺或方法,而这些工艺方法往往存在如下问题:有的方法采用电加热造成所需设备能耗较高,难以有效控制成本;有的方法将电加热设备设置于竖炉内部,设备消耗较快,维修难度大,成本高;有的方法重复还原会降低设备使用效率,增加设备工艺难度;还有的方法重复还原过程中,对其金属化率控制比较困难,影响产品质量。
5.因此,当前亟需一种能够减少单位产品氢气消耗量、降低产品成本、提高生产率的氢气还原炼铁工艺。
技术实现要素:
6.本发明所要解决的技术问题是提供一种能够减少单位产品氢气消耗量、降低产品成本、提高生产效率的基于外部预热炉料的氢气竖炉炼铁装置及其炼铁方法。
7.为解决上述技术问题,本发明提供了一种基于外部预热炉料的氢气竖炉炼铁装置,包括
8.氢气竖炉,用于承载含铁炉料并对含铁炉料进行还原;
9.多个预热料仓,每个预热料仓下部与氢气竖炉顶部连通,用于对进入氢气竖炉内的含铁炉料预加热;
10.燃烧室,与每个预热料仓下部一侧管道连通,燃烧室内燃烧产生的高温烟气对预热料仓内的含铁炉料预加热;
11.烟气回收与净化装置,与每个预热料仓上部一侧管道连通,对预热料仓内排出的
烟气净化和资源回收。
12.进一步地,所述氢气竖炉包括设置在氢气竖炉上部的分配仓、连接在分配仓下部的还原段、及连接在还原段下部的冷却段,所述还原段设置还原气体入口,所述冷却段下部设置冷却气入口,所述冷却段上部设置冷却气出口,所述还原段顶部设置炉顶气出口,所述冷却段底部设置还原铁出口。
13.进一步地,所述预热料仓包括第一预热料仓、第二预热料仓和第三预热料仓,三个预热料仓上部分别与受料斗管道连通、下部分别与所述分配仓管道连通,三个预热料仓与所述分配仓、受料斗、燃烧室及烟气回收与净化装置连通的管道上分别设置由预定程序控制的密封阀门。
14.进一步地,所述三个预热料仓与燃烧室连通的管道上还分别设置法兰密封阀。
15.进一步地,所述燃烧室上设置双层套筒喷枪,与所述双层套筒喷枪连接处的燃烧室内设置两组与两路不同供电电源连接的点火电炉丝。
16.本发明还提供了一种基于外部预热炉料的氢气竖炉炼铁装置的炼铁方法,包括如下步骤:
17.在预热料仓内加入含铁炉料,同时喷入燃烧室的助燃空气和气体燃料燃烧产生的高温烟气进入预热料仓对含铁炉料预热;
18.预热后的含铁炉料由氢气竖炉的分配仓进入还原段,与通入氢气竖炉的还原气体反应生成还原铁;
19.还原铁进入氢气竖炉的冷却段,经冷却后从氢气竖炉底部排出;
20.预热料仓内的高温烟气对含铁炉料预热后排入烟气回收与净化装置。
21.进一步地,所述第一预热料仓、第二预热料仓和第三预热料仓轮流向氢气竖炉内供应经过预热后的含铁炉料,可以保证向氢气竖炉内连续不间断地供应含铁炉料。
22.进一步地,所述燃烧室内的高温烟气温度为1100℃-1200℃,所述预热料仓内的含铁炉料预热到的预定温度为950℃-1050℃。
23.进一步地,所述还原气体为氢气或氢气含量大于65%的富氢,所述气体燃料包括但不仅限于转炉煤气、高炉煤气、焦炉煤气或/和化工生产尾气。
24.进一步地,所述含铁炉料为铁矿石固体颗粒或/和含铁精块矿氧化球团,所述铁矿石固体颗粒的含铁品位为67%-70%,所述含铁精块矿氧化球团的含铁品位为65%以上,且含铁精块矿氧化球团中的含铁精块矿比例不超过10%。
25.本发明提供的一种基于外部预热炉料的氢气竖炉炼铁装置及其炼铁方法,由于含铁炉料已经在预热料仓中被高温烟气加热到预定的温度,氢气竖炉已经不需要炉料预热段,因此氢气竖炉的高度也减少了将近一半,使设备向小型化发展。并且,由于进入氢气竖炉的高温还原气体一部分是用于还原反应,另一部分是用于通过高温对含铁炉料进行加热,由于含铁炉料在进入氢气竖炉之前已经被加热到发生还原反应的温度,含铁炉料可直接与还原气体发生反应,无需进入氢气竖炉的高温还原气体再对含铁炉料进行加热,相当于减少了用于加热含铁炉料的还原气体的使用,因此能够大大减少昂贵的氢气的使用量,降低生产成本。同时,进入还原段的含铁炉料无需再进行加热,即可直接与还原气体发生还原反应,使得含铁炉料在氢气竖炉内停留的时间大大缩短,从而可使炼铁的生产效率大大提高,其炼铁效率可提高20%-50%。
附图说明
26.图1为本发明实施例提供的基于外部预热炉料的氢气竖炉炼铁装置结构示意图。
具体实施方式
27.参见图1,本发明实施例提供的一种基于外部预热炉料的氢气竖炉炼铁装置,包括
28.氢气竖炉1,用于承载含铁炉料并对含铁炉料进行还原。
29.多个预热料仓2,每个预热料仓2下部与氢气竖炉1顶部连通,用于对进入氢气竖炉1内的含铁炉料预加热。
30.燃烧室3,与每个预热料2仓下部一侧通过管道连通,燃烧室3内燃烧产生的高温烟气对预热料仓2内的含铁炉料预加热。
31.烟气回收与净化装置4,与每个预热料仓2上部一侧通过管道连通,对预热料仓2内排出的烟气净化和资源回收。
32.其中,氢气竖炉1包括上部的分配仓11、连接在分配仓11下部的还原段12、及连接在还原段12下部的冷却段13。在还原段12设置有还原气入口14,在冷却段13下部设置冷却气入口15,在冷却段13上部设置冷却气出口16,在还原段12顶部设置炉顶气出口17,在冷却段13底部设置还原铁出口18。
33.作为本发明的一种具体实施方式,预热料仓2包括第一预热料仓21、第二预热料仓22和第三预热料仓23,预热料仓2上部分别与受料斗5通过管道连通,通过受料斗5可以分别顺次向三个预热料仓内添加含铁炉料。由于三个预热料仓与氢气竖炉顶部连接的位置不同,如果直接将每个预热料仓内预热后的含铁炉料由氢气竖炉1顶部不同位置排入氢气竖炉1中,容易导致炉料含铁炉料在氢气竖炉1内的分布不均,会影响炼铁的质量和效率。因此,在氢气竖炉1的顶部设置分配仓11,三个预热料仓的下部分别与分配仓11通过管道连通,分配仓11可将三个不同位置的预热料仓2内的含铁炉料调整至同一下料位置,然后由分配仓11将含铁炉料从同一下料位置排入氢气竖炉1的还原段12,从而确保含铁炉料在还原段12内分布的均匀性。预热料仓2与分配仓11、受料斗5、燃烧室3及烟气回收与净化装置4连通的管道上分别设置有密封阀门,由预定程序控制各个密封阀门的关闭与打开。通过预定程序控制各个密封阀门的开关,第一预热料仓21、第二预热料仓22和第三预热料仓23可轮流向氢气竖炉1内供应经过预热后的含铁炉料,从而保证三个预热料仓向氢气竖炉1内连续不间断地供应含铁炉料。
34.由于含铁炉料已经在预热料仓中被高温烟气加热到预定的温度,因此,氢气竖炉已经不需要炉料预热段,从而使氢气竖炉的高度也减少了将近一半,使整个设备向小型化发展。
35.作为本发明的一种具体实施方式,在预热料仓2与燃烧室3连通的各管道上还分别设置有法兰密封阀,用于防止因空气向内渗入和氢气向外泄漏而发生事故,同时也便于定期维护燃烧室3或更换因长期燃烧而损坏的燃烧室3。
36.作为本发明的一种具体实施方式,在燃烧室3上设置有一个双层套筒喷枪,通过双层套筒喷枪可向燃烧室3内吹入经过预热的空气和廉价的气体燃料。为了将双层套筒喷枪喷入燃烧室3内的空气和气体燃料的混合气体点燃,在与双层套筒喷枪连接处的燃烧室3内设置有与供电电源连接的点火电炉丝,点火电炉丝在供电电源作用下,温度可以保持在高
于1000℃-1200℃的红热状态,能够将喷入燃烧室3内的混合气体迅速点燃。
37.作为本发明的一种具体实施方式,燃烧室3内设置两组与两路不同供电电源连接的点火电炉丝,若与一组点火电炉丝的供电电源突然停电后,可以启用另一组与另一路供电电源连接的点火电炉丝,可以保证生产不会因突然停火而出现生产事故。
38.本发明提供的一种基于外部预热炉料的氢气竖炉炼铁装置的炼铁方法,包括如下步骤:
39.首先,预定程序打开第一预热料仓21与受料斗5之间的密封阀门,经受料斗5向第一预热料仓21内添加含铁炉料,同时通过双层套管喷枪向燃烧室3内喷入经过预先加热后的助燃空气和气体燃料,助燃空气和气体燃料的混合气体经点火电炉丝点燃,在燃烧室3燃烧产生1100℃-1200℃的高温烟气。作为本发明的一种具体实施方式,含铁炉料为铁矿石固体颗粒或/和含铁精块矿氧化球团,其中,铁矿石固体颗粒的含铁品位为67%-70%,含铁精块矿氧化球团的含铁品位为65%以上,且含铁精块矿氧化球团中的含铁精块矿比例不超过10%。作为本发明的一种具体实施方式,气体燃料包括但不仅限于转炉煤气、高炉煤气、焦炉煤气或/和化工生产尾气等廉价气体。
40.待第一预热料仓21加料完成后,预定程序关闭第一预热料仓21与受料斗5间的密封阀门、打开第一预热料仓21与燃烧室3之间的密封阀门,燃烧室3内的1100℃-1200℃高温烟气进入第一预热料仓21对第一预热料仓21内的含铁炉料预热,第一预热料仓21内含铁炉料在预热过程中第二预热料仓22经受料斗5进料。
41.当第一预热料仓21内的含铁炉料预热到950℃-1050℃时,预定程序关闭第一预热料仓21与燃烧室3之间的密封阀门、打开第一预热料仓21与分配仓11之间的密封阀门以及第一预热料仓21与烟气回收与净化装置4之间的密封阀门,第一预热料仓21内暂停供应高温烟气、第一预热料仓21内的950℃-1050℃含铁炉料排入氢气竖炉1的分配仓11,第一预热料仓21内的烟气进入烟气回收与净化装置4内。
42.同时预定程序关闭第二预热料仓22与受料斗5之间的密封阀门、打开第二预热料仓22与燃烧室3之间的密封阀门,燃烧室3内的1100℃-1200℃高温烟气进入第二预热料仓22对第二预热料仓22内的含铁炉料预热,在第二预热料仓22内含铁炉料预热过程中第三预热料仓23经受料斗5进料。
43.当第二预热料仓22内的含炉原料预热到950℃-1050℃时,预定程序关闭第二预热料仓22与燃烧室3之间的密封阀门、打开第二预热料仓22与分配仓11之间的密封阀门以及第二预热料仓22与烟气回收与净化装置4之间的密封阀门,第二预热料仓22内暂停供应高温烟气、第二预热料仓22内的950℃-1050℃含铁炉料排入氢气竖炉1的分配仓11,第二预热料仓22内的烟气进入烟气回收与净化装置4内。
44.与此同时预定程序关闭第三预热料仓23与受料斗5之间的密封阀门,打开第三预热料仓23与燃烧室3间的密封阀门,燃烧室3内的1100℃-1200℃高温烟气进入第三预热料仓23对第三预热料仓23内的含铁炉料预热,在第三预热料仓23内含铁炉料预热过程中第一预热料仓21经受料斗5进料。
45.第三预热料仓23内的含炉原料预热到950℃-1050℃时,预定程序关闭第三预热料仓23与燃烧室3之间的密封阀门、打开第三预热料仓23与分配仓11之间的密封阀门及第三预热料仓23与烟气回收与净化装置4之间的密封阀门,第三预热料仓23内暂停供应高温烟
气、第三预热料仓23内预热到950℃-1050℃的含铁原料排入氢气竖炉1的分配仓11、第三预热料仓23内的烟气进入烟气回收与净化装置4。
46.作为本发明的一种具体实施方式,当双层套筒喷枪停止向燃烧室3内喷吹燃烧气体时,立即通过双层套筒喷枪向燃烧室3内补充通入等量的氮气,使燃烧炉内保持一定量的正压力,防止燃烧室3吸入空气或燃气发生回火,造成安全事故。
47.按上述方式往复循环,三组预热料仓2可以连续不断地向氢气竖炉1内供应预热到950℃-1050℃的含铁炉料。
48.然后,预热到950℃-1050℃的含铁炉料进入到氢气竖炉1的分配仓11后,分配仓11可将不同位置的预热料仓2排入的含铁炉料调整至同一下料位置,然后由分配仓11将含铁炉料从同一下料位置排入氢气竖炉1的还原段12,使含铁炉料均匀分布在还原段12内,可提高含铁炉料的反应效率。进入还原段12的含铁炉料,与从还原气入口14通入到氢气竖炉1还原段12的还原气体反生还原生成直接还原铁,还原段12内反应后产生的炉顶气从还原段12顶部的炉顶气出口17排出。作为本发明的一种具体实施方式,还原气体为氢气或氢气含量大于65%的富氢。
49.由于进入氢气竖炉1的还原气体一部分是用于还原反应,另一部分是用于形成高温气体对含铁炉料进行加热,而本发明提供的炼铁方法在含铁炉料进入氢气竖炉1的还原段12之前已经在预热料仓2中被高温烟气加热到了950℃-1050℃,该温度下的含铁炉料可直接与还原气体发生反应,无需还原气体再对含铁炉料进行加热,相当于减少了用于加热炉料的这部分还原气体的使用,因此,本发明提供的炼铁方法能够大大减少昂贵的氢气的使用量,能够降低生产成本。
50.而且,由于进入还原段12的含铁炉料无需再进行加热,即可直接与还原气体发生还原反应,使得含铁炉料在氢气竖炉1内的停留时间大大缩短,从而可使炼铁的生产效率大大提高,本发明提供的炼铁方法能够使炼铁的效率提高20%-50%。
51.最后,氢气竖炉1的还原段12产生的还原铁进入冷却段13,从冷却段13下部的冷却气入口15进入的冷却气向上运行与从上部下来的还原铁接触,对还原铁进行冷却,经冷却后的还原铁从冷却段13底部的还原铁出口18排出,生产得到的直接还原铁(dri)中金属铁与全铁的比例不低于90%。同时对还原铁冷却后的冷却气从冷却段13上部的冷却气出口16排出。
52.作为本发明的一种具体实施方式,烟气回收与净化装置包括余热回收锅炉、高温烟气除尘单元、控制烟气流动的程序控制阀门组、及温度与正压力控制单元。对于预热料仓2内对含铁炉料预热后排入烟气回收与净化装置的高温烟气,先经过高温烟气除尘单元除尘后,再通入余热回收锅炉进行余热回收,经过余热回收得到的助燃空气和回收得到的含铁粉尘可以循环利用,除尘后的尾气可用作对喷涂过水泥浆的入炉球团矿进行烘干的气源。
53.下面通过实例对本发明提供的一种基于外部预热炉料的氢气竖炉炼铁方法做具体说明。
54.实施例1
55.本实施例采用铁品位为67%的氧化球团及全铁品位66%的铁矿块矿为原料,利用氢气还原氧化球团和铁矿块矿制备dri,具体步骤如下:
56.1)选用中热值的氧气顶吹转炉煤气(ldg)做气体燃料,该煤气的低热值约8000kj/m3,通过双层套筒喷枪将煤气与预热至600℃的助燃空气喷入燃烧室3,在进入燃烧室3时被红热的点火电炉丝点燃,在燃烧室3内燃烧生成1200℃的高温烟气。
57.2)燃烧室3内的高温烟气自下而上进入预热料仓2,对预热料仓2内的铁矿块矿和氧化球团充分接触并加热这些含铁炉料,当含铁炉料到达1050℃后停止预热(将高温烟气切换到另一个已经装满含铁炉料球团与块矿的料仓开始加热其中的含铁炉料),关闭烟气进出的密封阀门后,中控室预定程序发出指令打开预热料仓2下部的密封阀门,高温的含铁炉料即自上而下进入氢气竖炉1,三组预热料仓可实现不间断加热供料。
58.3)进入氢气竖炉1的炉料温度为1000℃,被通入氢气竖炉的950℃的氢气还原,入炉氢气量约1600m3/tdri(即还原铁),作为还原剂消耗的氢气为600m3/tdri,其余的1000m3/tdri的氢气通过氢气竖炉煤气余热回收(可预热新补充的氢气的温度到500℃),循环使用与新补充的氢气混合进入加热炉,加热至950℃后再进入竖炉。与没有炉料预热系统的竖炉相比,本发明实施例使得氢气消耗量减少:1900-1300=700m3/tdri,降低了富氢还原气体消耗量的成本约25%-30%。
59.4)生产过程中经氢气竖炉1下部排出的还原后产品dri的金属化率达到94%,获得了增产20%dri的效果,提高了生产率及设备使用率,扣除加热炉料的成本,单位产品的燃料成本降低了15%。
60.实施例2
61.本实施例采用铁品位为68%的氧化球团为原料,利用氢气还原铁矿氧化球团制备dri,具体步骤如下:
62.1)选用钢铁厂副产的高热值的焦炉煤气(cog)做为气体燃料,该煤气的低热值约18000kj/m3,通过双层套筒喷枪将煤气与预热至600℃的助燃空气喷入燃烧室3,在进入燃烧室3时被红热的点火电炉丝点燃,在燃烧室3内燃烧生成1200℃的高温烟气。
63.2)燃烧室3内的高温烟气自下而上进入预热料仓2,对预热料仓2内的铁矿块矿和含铁氧化球团充分接触并加热这些含铁炉料,当含铁炉料到达980℃后停止预热(将高温烟气切换到另一个已经装满含铁炉料球团与块矿的料仓开始加热其中的含铁炉料),关闭烟气进出的密封阀门后,中控室预定程序发出指令打开预热料仓2下部的密封阀门,高温的含铁炉料即自上而下进入氢气竖炉1,三组预热料仓可实现不间断加热供料。
64.3)进入氢气竖炉1的炉料温度为980℃,被通入氢气竖炉的950℃的富氢气体还原,入炉氢气量约1300m3/tdri(即还原铁),作为还原剂消耗的氢气为600m3/tdri,其余的700m3/tdri的氢气通过氢气竖炉煤气余热回收(可预热新补充的氢气的温度到500℃),循环使用与新补充的氢气混合进入加热炉,加热至950℃后再进入竖炉。与没有炉料预热系统的竖炉相比,本发明实施例使得氢气消耗量减少:2400-1600=800m3/tdri,降低了富氢还原气体消耗量的成本约25%-30%。
65.4)还原结束后,经氢气竖炉1下部排出的还原后产品dri的金属化率为93%,获得了增产30%dri的效果,提高了生产率及设备使用率,扣除加热炉料的成本,单位产品的燃料成本降低了20%。
66.最后所应说明的是,以上具体实施方式仅用以说明本发明的技术方案而非限制,尽管参照实例对本发明进行了详细说明,本领域的普通技术人员应当理解,可以对本发明
的技术方案进行修改或者等同替换,而不脱离本发明技术方案的精神和范围,其均应涵盖在本发明的权利要求范围当中。