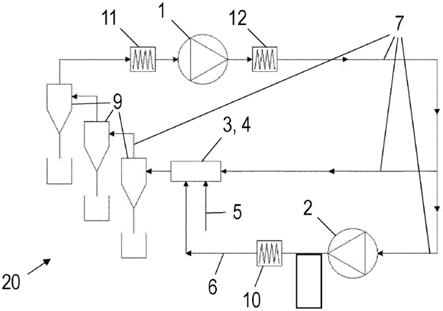
1.本发明涉及一种根据权利要求1的前序部分所述的用于制备材料粉末的方法。
2.本发明此外涉及一种根据权利要求8的前序部分所述的用于制备材料粉末的设备。
背景技术:
3.借助于雾化气体由熔体制备材料粉末在现有技术中已知并且以工业规模实施。存在一系列不同的用于制备材料粉末的方法,这些方法可以被分类称外混合式和内混合式方法。在两种方法类型中,对熔化的材料的流加载雾化气体,所述雾化气体将熔化的材料雾化成精细的颗粒。这些精细的颗粒产生材料粉末。过去研发出的粉末加工方法、例如以粉末床方法的3d打印然而在材料粉末的颗粒尺寸、颗粒尺寸分布、产品纯度以及颗粒形状方面对材料粉末提出强烈提高的质量上的要求。特别是,精细的材料粉末亦或具有窄的颗粒尺寸分布的材料粉末、氧气、氮气或低氢材料粉末、在粉末表面上的低湿度、无由于异物粉末或坩埚材料污染物的污染以及球形的、低伴生矿物(satellitenarm)的材料粉末(其具有良好的流动性)都是有利的。利用在现有技术中已知的方法制备的材料粉末不提供如下的质量特性,这些质量特性以新型的粉末加工方法为前提。由此必要的是,借助于已知的方法制备的材料粉末经历耗费的质量分析和筛除或视觉方法(sichtverfahren),以便所述最终产品提供所需的产品特性。然而这导致,所制备的材料粉末的大部分份额被剔除、生产成本提高、单位数量的所制备的高质量的材料粉末的能量消耗提高以及利润降低。传统的用于制备材料粉末的方法的这些不利的特性因此反映到在针对最终消费者的市场上的高的价格和低的产品可用性上。
4.按照现有技术的用于制备材料粉末的方法和设备在us4,534,917中公开。该用于制备材料粉末的方法包括向雾化装置提供材料,所述雾化装置将所述材料熔化。所述熔化的材料在雾化装置中被加载雾化气体并且被所述雾化气体所雾化。在此,熔化的材料和雾化气体通过喷嘴引导,所述喷嘴是雾化装置的部分。在此产生的材料粉末被吹入到收集容器中。
5.文献ep 3 459 658 a1公开了一种用于制备材料粉末的方法,其中,所产生的材料粉末的表面借助于含氧气体钝化。
6.文献wo 2018/035202 a1公开了一种用于制备材料粉末的设备,所述设备具有鼓风组件。
7.文献wo 97/41986 a1公开了一种用于在雾化装置中制备金属粉末的方法,所述方法包括反应锅、铸箱、粉末容器和沉淀装备。
8.文献us 6,444,009 b1公开了一种用于利用反应性的合金处理由金属成分产生超精细的和环境稳定的粉末的两级的方法。
技术实现要素:
9.本发明的任务在于形成用于制备材料粉末的方法和设备,其克服现有技术的缺陷。
10.按照本发明,所述任务通过一种具有权利要求1的特征的方法和一种具有权利要求10的特征的设备来解决。
11.按照本发明的用于制备材料粉末的方法包括向雾化装置提供材料。此外,向雾化装置提供借助于雾化气体压缩机加载雾化气体压力的雾化气体。利用雾化装置将材料熔化,并且将熔化的材料雾化成材料粉末,其方式为,借助于雾化装置、优选在雾化装置的雾化压力容器中对所述熔化的材料加载雾化气体。接着,由雾化装置将材料粉末引入到压力容器中,在所述压力容器中冷却和收集材料粉末。压力容器例如可以与雾化装置连接,或者所述雾化装置可以容纳到压力容器中。按照本发明的方法此外包括向压力容器提供以输送气体压力加载的输送气体,其中,借助于输送气体压缩机给所述输送气体加载输送气体压力。在此,输送气体压力这样选择,使得所述输送气体压力处于大气压力之上并且处于雾化气体压力之下。
12.对于现有技术中的所有方法共同的是,超出于影响温度的方法步骤,未设置用于有针对性地控制雾化气体在雾化中与熔化的材料的表面接触点上的热力学状态的措施。本发明因此基于如下关键考虑,在雾化区域之内除了合适的气流引导,雾化气体在熔化的材料的表面上的热力学状态点是对于雾化结果有重要意义的。气体状态点能通过在雾化容器中的温度和特别是压力、或者说静压、亦即静态超压来控制并且造成气体的确定的可达到的气体密度或者说静态气体密度。由于在雾化区域中在气流和熔体之间的更高的脉冲传输,更高的气体密度在此提供更好的雾化结果。就此而言,在本发明的过程中获得下述认知,在雾化区域中的气体密度能够最为有效地通过在雾化装置的喷嘴之后的压力来控制并且不是像在现有技术中已知的那样通过气体在雾化装置的喷嘴之前的雾化压力来控制。
13.通过所述用于制备材料粉末的方法的按照本发明的实施方式,附加于具有雾化气体压力的雾化气体,向压力容器提供具有输送气体压力的输送气体。所述输送气体压力处于大气压力之上并且处于雾化气体压力之下。由此创造出如下可能性,即,调节特别是在雾化点上的气体密度,并且达到在熔化的材料与包围或穿流熔化的材料的气体之间的更高的脉冲传输。由此达到相对于现有技术更精细的雾化结果,亦即利用按照本发明的方法所产生的材料粉末的颗粒尺寸缩小。此外,按照本发明的方法提供具有颗粒尺寸方面更小的分布宽度的材料粉末。此外,按照本发明的方法能实现借助于输送气体压力和雾化气体压力而与产量无关地改变颗粒尺寸。此外,所述方法能以成本有利地制备的按照本发明的装置来实施。输送气体此外具有特别是如下任务,阻止气流在喷嘴附近的再循环和因此粉末聚集,以及所生产的材料粉末的冷却,由此可以放弃分开的外部冷却。该冷却效果同样可以通过输送气体的压力来影响。输送气体压力选择得越高,输送气体的冷却效果更好。
14.根据按照本发明的方法的优选的实施形式,将所述输送气体由压力容器引导回至输送气体压缩机,由此所述方法作为循环过程运行,并且不丢失输送气体。由此实现下述优点,即,按照本发明的方法具有低的能量需求和因此低的运行成本。特别是在使用成本高昂的输送气体、如co2、氮气、氦气或氩气亦或气体混合物时此外实现如下优点,即,输送气体不丢失并且可以在循环过程中重复使用。这导致运行成本的进一步减少、高的产品纯度和
降低的灰尘排放。
15.优选地,将具有输送气体压力的输送气体的部分在将其向压力容器提供之前分支出,并且借助于雾化气体压缩机压缩成具有处于输送气体压力之上的雾化气体压力的雾化气体。由此达到如下优点,即,所述雾化气体不必分开地提供,而是从输送气体流产生。这导致运行成本的进一步减少和雾化气体集成到循环过程中。
16.按照本发明的方法此外包括:利用输送气体将材料粉末从压力容器输送到分离装置并且接着利用分离装置将材料粉末分级为具有第一颗粒尺寸范围的材料粉末和具有第二颗粒尺寸范围的材料粉末。接着从分离装置取出具有第一颗粒尺寸范围的材料粉末。由此达到如下优点,利用按照本发明的方法能够产生具有还更窄的颗粒尺寸范围的材料粉末。
17.优选地,按照本发明的方法还包括:利用输送气体将具有第二颗粒尺寸范围的材料粉末从分离装置输送到至少一个另外的分离装置。在所述至少一个另外的分离装置中,利用所述至少一个另外的分离装置将具有第二颗粒尺寸范围的材料粉末分级成具有至少两个另外的颗粒尺寸范围的材料粉末。接着,从输送气体取出具有所述至少两个另外的颗粒尺寸范围中的至少一个颗粒尺寸范围的材料粉末。由此实现如下优点,即,能够将所述材料粉末分级成另外的颗粒尺寸范围。
18.按照本发明的方法包括:在优选的实施形式中利用雾化气体热交换器加热雾化气体。由此达到如下优点,借助于加热的雾化气体能够达到更好的雾化。
19.按照本发明的方法还可以包括:利用第一输送气体热交换器来冷却输送气体。通过冷却输送气体可以预防实施按照本发明的方法的按照本发明的设备过热。
20.按照本发明的用于制备材料粉末的设备包括输送气体压缩机、雾化气体压缩机、雾化装置和压力容器,所述设备构成为用于实施按照本发明的方法。优选地,按照本发明的设备还包括至少一个分离装置。根据按照本发明的设备的优选的实施形式,所述设备还可以具有冷却装置、雾化气体热交换器、第一输送气体热交换器和/或第二输送气体热交换器。
21.按照本发明,所述用于制备材料粉末的设备包括输送气体压缩机、雾化气体压缩机、雾化装置和压力容器。所述雾化气体压缩机构成为用于向雾化装置提供以雾化气体压力加载的雾化气体,并且所述雾化装置构成为用于使材料熔化并且对熔化的材料加载雾化气体、将熔化的材料雾化成材料粉末并且将材料粉末引入到压力容器中。所述设备还构成为用于向压力容器提供借助于输送气体压缩机加载输送气体压力的输送气体,所述输送气体压力处于大气压力之上并且处于雾化气体压力之下。
22.优选地,所述设备构成为用于将输送气体从压力容器引导回至输送气体压缩机。
23.此外,所述设备优选构成为用于将具有输送气体压力的输送气体的部分在将其向压力容器提供之前分支出。所述雾化气体压缩机优选构成为用于将输送气体的分支出的部分压缩成具有雾化气体压力的雾化气体,所述雾化气体压力处于所述输送气体压力之上。
24.所述设备按照一种优选的实施形式具有至少一个分离装置并且构成为用于利用输送气体将材料粉末从压力容器输送至分离装置。所述分离装置按照该实施形式构成为用于将材料粉末分级为具有第一颗粒尺寸范围的材料粉末和具有第二颗粒尺寸范围的材料粉末,其中,所述设备构成为用于从输送气体取出具有第一颗粒尺寸范围的材料粉末。
25.优选地,所述设备还构成为用于利用输送气体将具有第二颗粒尺寸范围的材料粉末从分离装置输送到至少一个另外的分离装置,并且所述至少一个另外的分离装置构成为用于将具有第二颗粒尺寸范围的材料粉末分级成具有至少两个另外的颗粒尺寸范围的材料粉末。所述设备在此还构成为用于从输送气体取出具有所述至少两个另外的颗粒尺寸范围中的至少一个颗粒尺寸范围的材料粉末。
26.根据按照本发明的设备的一种实施变型方案,所述设备包括雾化气体热交换器,所述雾化气体热交换器构成为用于加热雾化气体。
27.所述设备此外优选包括第二输送气体热交换器,所述第二输送气体热交换器构成为用于冷却输送气体。
28.以下借助附图更详细地阐述按照本发明的方法和按照本发明的设备的有利的实施方案。
附图说明
29.图1示出按照本发明的方法的流程图或者说按照本发明的设备的构造的示意图。
30.图2a以第一实施变型方案示出按照本发明的设备的雾化装置。
31.图2b以第二实施变形方案示出按照本发明的设备的雾化装置。
32.图3示出输送气体压力对利用按照本发明的方法制备的材料粉末的颗粒尺寸的影响。
33.图4示出利用按照本发明的方法生产的材料粉末的颗粒直径的分布。
具体实施方式
34.图1示出按照本发明的方法的流程图或者说按照本发明的设备20的示意图,所述设备具有输送气体压缩机1、雾化气体压缩机2、雾化装置3和压力容器4,其中,所述压力容器4和雾化装置3在流程图中作为一个共同的单元3和4示出。在按照本发明的用于制备材料粉末的方法中,向雾化装置3提供材料5和借助于雾化气体压缩机2加载雾化气体压力的雾化气体6。在按照本发明的方法的范畴内可以使用在现有技术中已知的不同雾化装置3。示例性地,这里列举开放(自由)射流(open(free)jet)雾化器、受限(或闭合耦合)(confined(or closed couple))雾化器、闭合耦合(close coupled)雾化器、等离子体雾化器以及普遍的内混合和外混合雾化装置3。在雾化装置3中使材料5熔化并且使所述材料雾化成材料粉末,其方式为,利用雾化装置3对熔化的材料5加载雾化气体6。材料粉末在图1的示意图中未示出。接着,将所述材料粉末从雾化装置3引入到压力容器4中,所述压力容器在图1中示出在具有雾化装置3的单元3和4中。按照本发明,向压力容器4提供借助于输送气体压缩机1加载输送气体压力的输送气体7。由此,附加地将输送气体7以自身的气流引入到压力容器4中,如在图2a和图2b中详细示出的那样。所述输送气体压力在此处于大气压力之上并且处于雾化气体压力之下。在压力容器4中接着出现平衡压力。由此创造如下可能性,调节特别是在雾化点上的气体密度,并且达到在熔化的材料5与包围或穿流熔化的材料5的气体之间的脉冲传输,所述脉冲传输比在现有技术中已知的方法所能达到的而更高。由此达到相比于现有技术更好的雾化结果,并且改善利用按照本发明的方法产生的材料粉末的颗粒精细度。通过相对于大气压力提高的输送气体压力附加地达到如下优点,即,在按照本发明的方
法中没有低于期望(unterw
ü
nscht)的环境空气可以污染材料粉末。由此提高所产生的材料粉末的纯净度,因为避免与氧气、氮气或氢气的不希望的反应。此外,通过输送气体压力提供改善的冷却效果。通过量和颗粒尺寸同样可以借助于输送气体压力来控制。通过对输送气体7加载压力和因此最终也对雾化装置3的在图2a和2b示出的排出开口8逆着对熔化的材料5排出的射流的流动方向加载压力,可以分开地调节材料粉末的精细度和生产率。在雾化装置3的排出开口之后的气体压力相对于熔化的材料5的压力越高,生产率越低。气体通过量相对于熔化的材料5的通过量越高,所产生的材料粉末就越精细。由此产生对粉末精细度和生产率的独立调节的可能性。通过输送气体压力可以调整材料粉末的所产生的颗粒的精细度。熔化的材料的通过量可以通过对熔化的材料5起作用的压力来调节。通过将熔化的材料5雾化到以输送气体加载的压力容器4中,给出用于调节材料粉末的精细度的选项。
35.按照本发明的方法适合于由不同的材料5制备材料粉末。示例性地这里列举金属、如铁、铜和钛、金属合金、矿物熔体和矿渣、蜡、聚合物、塑料和塑料混合物。在由蜡制备材料粉末的情况下,在按照本发明的方法中有利地使用氮气或氩气作为雾化气体6和/或输送气体7。在由聚合物制备材料粉末的情况下,在按照本发明的方法中有利地使用co2作为雾化气体6和/或输送气体7。不同的材料粉末与不同的气体或气体混合物的其他有利的组合对于本领域技术人员普遍已知。
36.如在图1中所示,在所述方法中按照本发明将气体优选部分地或者完全地循环引导。根据按照本发明的方法的优选的实施形式,将输送气体7从压力容器4引导回至输送气体压缩机1。由此达到如下优点,即,所述输送气体7不丢失,而是在按照本发明的方法中被重复使用。这点在使用昂贵的输送气体7、例如稀有气体的情况下是特别有利的。
37.根据按照本发明的方法的优选的实施形式,具有输送气体压力的输送气体7的部分(如图1中所示)在将所述部分向压力容器4提供之前分支出。该分支出的输送气体7加上雾化气体6借助于雾化气体压缩机2压缩到雾化气体压力。所述雾化气体压力处于输送气体压力之上。雾化气体6紧接于雾化装置3提供。由此达到如下优点,同一个气体用作雾化气体6和输送气体7。由此,按照本发明的方法得以简化并且能成本更有利地使用。
38.紧接于利用雾化装置3将熔化的材料5雾化成材料粉末并且将材料粉末引入到压力容器4中,将材料粉末优选从压力容器4借助于输送气体7输送到分离装置9中。所述分离装置9将所述材料粉末分级为具有第一颗粒尺寸范围的材料粉末和具有第二颗粒尺寸范围的材料粉末。接着,从输送气体7取出具有第一颗粒尺寸范围的材料粉末。分离装置9例如可以实施为旋风分离器。备选地,所述分离装置9也可以实施为过滤器、磁性或静电分离装置9。分离装置9的其他实施形式对于本领域技术人员普遍已知。
39.在按照本发明的方法的在图1中示出的优选的实施形式中,将具有第二颗粒尺寸范围的材料粉末从分离装置9输送至两个另外的分离装置9。按照本发明,将具有第二颗粒尺寸范围的材料粉末从分离装置9输送到至少一个另外的分离装置9。在所述至少一个另外的分离装置9中,将具有第二颗粒尺寸范围的材料粉末分离成具有至少两个另外的颗粒尺寸范围的材料粉末。接着,从输送其他7取出具有所述至少两个另外的颗粒尺寸范围中的至少一个颗粒尺寸范围的材料粉末。由此达到如下优点,可以将所述材料粉末分开成不同的颗粒尺寸范围。所述另外的分离装置9可以如同所述分离装置9那样构成,或者应用备选的分离方法。
40.例如,所述分离装置9实施为旋风分离器,其中,提供另外的、跟随的分离装置9,所述分离装置实施为过滤器。备选地也可以使用两个旋风分离器串联一个接连的过滤器。按照本发明的设备的一个另外的示例性的实施变型方案包括粗分离器、旋风分离器以及一个或两个跟随的过滤器。代替过滤器也可以使用湿分离器。
41.如图1中所示,按照本发明的方法在优选的实施形式中包括:利用雾化气体热交换器10加热雾化气体6。由此达到如下优点,提高雾化气体6的温度,由此可以达到更好的雾化结果。
42.优选地,按照本发明的方法此外包括利用第一输送气体热交换器11冷却输送气体7。所述第一输送气体热交换器11优选在利用输送气体压缩机1压缩输送气体之前冷却输送气体7。由此,避免输送气体在输送气体压缩机1中出现过热。
43.在按照本发明的方法的优选实施形式中,此外提供第二输送气体热交换器12,所述第二输送气体热交换器冷却输送气体7。由此达到如下优点,即,阻止所述方法或者执行按照本发明的方法的按照本发明的设备20的输送气体7或者各个部件过热。
44.在图1示出的按照本发明的用于制备材料粉末的设备20包括输送气体压缩机1、雾化气体压缩机2、雾化装置3和压力容器4。优选地,按照本发明的设备20此外包括所述至少一个分离装置9,以用于将材料粉末分离成不同的颗粒尺寸范围。在按照本发明的设备20的优选的实施形式中,所述设备20还包括冷却装置、雾化气体热交换器10、第一输送气体热交换器11和第二输送气体热交换器12。
45.图2a示出按照本发明的设备20的雾化装置3的第一实施变型方案。雾化装置3在第一实施变型方案中实施为等离子体雾化装置、优选用于金属。所述材料5以金属丝的形状引入到雾化装置3中,其中,通过对金属丝施加电压借助于电弧13来熔化材料5。通过连续地熔化金属丝来改变金属丝的各端部的距离,这通过持续地送丝来补偿。对电弧13加载具有雾化气体压力的雾化气体6,由此将熔化的材料5雾化成材料粉末。通过雾化气体6将材料粉末引入到压力容器4中,其中,所述压力容器4加载有处于输送气体压力之下的输送气体7。输送气体7优选如图2a中所示那样以多个气体射流或者平行于材料粉末的推出从雾化装置3引入到压力容器4中。但也可能以切线方向的入口亦或沿用于推出材料粉末的径向方向而引入。由此避免涡流,借此预防在材料粉末上形成伴生(satellitenbildung)。在此,形成伴生普遍地可理解为较小的颗粒积聚在材料粉末中的较大的颗粒上。此外由此也达到对压力容器4的冷却,借此减少按照本发明的方法或按照本发明的设备20的能量需要。通过调节雾化气体压力和输送气体压力可以影响电弧13的长度,由此同样达到所产生的材料粉末的颗粒尺寸分布和平均颗粒尺寸的改变。
46.图2b示出按照本发明的设备20的雾化装置3的第二实施变型方案,其中,在该实施变型方案中热学上熔化材料5。所述材料5例如可以借助于感应来熔化。其他熔化方法对于本领域技术人员普遍已知。在雾化装置3中对熔化的材料5加载雾化气体6并且将熔化的材料雾化成材料粉末。输送气体7优选如在雾化装置3的第一实施变型方案中以多个气体射流或者相对于材料粉末的推出平行地亦或沿切线或径向方向从雾化装置3引入到压力容器4中。由此又预防形成伴生。此外,由此达到压力容器4的冷却,由此减少按照本发明的方法或按照本发明的设备20的能量需求。所述雾化装置3除了金属及其合金也适合于例如不导电的材料5、如蜡和塑料、例如聚合物,也或者适合于矿物熔体和矿渣。此外也可能的是,借助
于微波发生器来熔化可熔融的介电的材料5。其他雾化方法对于本领域技术人员普遍已知。
47.输送气体压力优选高出于大气压力至少0.5bar,并且可以高出于大气压力直至100bar。输送气体压力越高,所产生的材料粉末越精细并且冷却效果越好。优选地,所述输送气体压力处于1至10bar之间。
48.雾化气体压力通常处于临界压缩比之上,以便在雾化装置3的最窄的喷嘴横截面中至少达到声速。通过在气体与熔化的材料5之间更高的相对速度而产生更精细的材料颗粒。即使在较低的压力情况下也能实现材料粉末的雾化和因此材料粉末的生产,特别地必要时,制备具有窄颗粒尺寸分布的较大的材料粉末。
49.作为雾化气体6和作为输送气体7,已知的气体对于本领域技术人员认为对于要雾化的材料5是合适的。但也可以使用气体混合物。例如在除此之外惰性气体(氮气、氩气、氦气或类似气体)中低份额的氧气可以实现,对材料粉末的表面覆盖氧化层,这导致钝化。还原性的气体混合物也是合适的,例如按份额含有低量氧气的气体。这提供如下可能性,在化学上从颗粒形的材料还原污染物、如氧化物或类似物。特别有利的是,在按照本发明的设备20中或者在按照本发明的方法中使用反应性的气体混合物。所述气体混合物的热力学平衡组成能够通过所引入的反应组分、如具有按份额含量的co、co2、h2o、h2、nh3等等的气体来调整,作为在输送气体流中的压力和温度关于在宽的范围内可控制的氧气剩余势能(restpotential)的函数。这样的可选地具有放热的或吸热性质的反应性的气氛对于本领域技术人员例如从用于冶金流程的反应性的熔炉气氛已知。以此,利用按照本发明的方法,氧化、碳化和氮化流程或备选地用于非常氧化敏感的产品(例如强烈含铬的不锈钢、其无污染的产品)的无氧的粉末生产方法变得可用,这些粉末生产方法以传统的仅基于氮气或氩气的惰性气氛中是无法实现的。最后,与按照本发明的方法作为循环过程的实施形式不同地,按照本发明的方法能作为开放的方法实现,在所述方法中作为雾化气体6和输送气体7使用不同的气体或气体混合物。由此例如可以先通过输送气体7实现材料粉末的钝化。
50.图3以铝粉末的生产为例示出输送气体压力对材料粉末的颗粒尺寸的影响,所述铝粉末通过按照本发明的方法借助于坩埚蒸发进行。图3将在给定质量d50(质量中位直径mmd)下平均颗粒直径的比例与雾化气体7对材料熔体(m
‘
gas/m
‘
liq)的质量比进行对比。图3中的图表的曲线a代表在1bar输送气体压力下的所提到的关联,曲线b代表在4bar下而曲线c代表在10bar下。可看出的是,输送气体压力的提高令人惊奇地导致所产生的材料粉末的平均颗粒直径的缩小。
51.本技术人还在使用在图2b中示出的雾化装置3的情况下利用按照本发明的方法根据等离子体雾化方法实施了用于关于输送气体压力确定平均颗粒直径d50和颗粒直径的分布宽度的实验。这些实验的结果在表1和图4中示例性地综述。在表1中示出的结果是在使用铜作为材料5的情况下实现的:
[0052][0053]
表1
[0054]
利用按照本发明的方法在使用不同射流、钼和不同金属合金的情况下实现了可相比的结果。
[0055]
以下给出按照本发明的方法的另外两个实施例。
[0056]
实施例1:
[0057]
在按照本发明的方法的该实施例中,50kg/h铝在750℃下熔化。雾化气体6选为氩气,所述氩气以150kg/h的速率在500℃的温度下引入。相应的压力情况为
[0058]
输送气体压力:3bar
[0059]
雾化气体压力:10bar
[0060]
通过供应雾化气体6和输送气体7在压力容器4中出现4bar的设备压力。
[0061]
由此生产出具有平均直径d50.3低于10μm的铝颗粒,连同分布宽度为d84/d50《1.6。
[0062]
实施例2:
[0063]
以20kg/h的速率以通过焊接电流源产生的电弧13生产熔化的不锈钢。雾化气体6的流以质量通过量为150kg/h引入到雾化装置3中并且将熔化的不锈钢雾化。电弧13可以通过在压力容器4中的输送气体压力或者作用到其上的反压力来缩小。由此产生非常均匀的雾化情况。所雾化的不锈钢颗粒具有22μm的平均直径d50.3和分布宽度d84/d50=1.38。