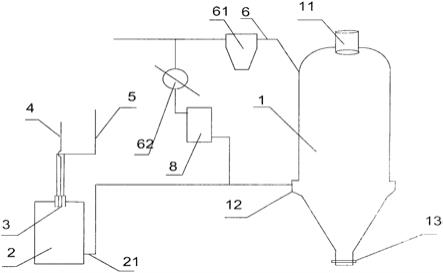
1.本发明属于直接还原领域,具体涉及一种气基竖炉直接还原方法。
背景技术:
2.气基竖炉直接还原的现有技术,如,专利申请号201210379144.3,名称为一种利用富ch4煤气生产海绵铁的直接还原工艺的专利提出,“将经调压后的富ch4煤气和依次经降温、除尘、及加压处理后的气基竖炉炉顶气输入外部转化炉,并向外部转化炉中补充作为ch4发生改质反应氧化剂的蒸汽,使外部转化炉中的ch4、h2o和co2在催化剂作用下发生改质反应生成主要包括co和h2的高温还原煤气”,“转化炉出口的还原煤气的温度为850℃”;又如,专利号201710676084.4,名称为一种气基竖炉还原气的制备系统及方法的专利提出,“气基竖炉还原气的制备系统包括气基竖炉炉顶气洗涤器、炉顶气脱碳装置、焦炉煤气净化装置、焦炉煤气脱硫装置、转化炉、热回收装置、合成气除尘装置、合成气脱硫脱碳装置及混合器”,“所述催化剂管为多根,其并列设置”,“热回收装置为换热器”,“本发明催化重整反应中,焦炉煤气中的ch4、co2和炉顶气中的co2作为原料被重整为富含co和h2的高温变换气,温度为800~1000℃”;再如,申请号:cn201910952204.8,名称为,一种用于生产还原气的新型重整炉的专利提出,“重整炉包括辐射室箱体,重整炉管,燃烧器,过渡段以及对流段;所述的重整炉管成2m排立式并联布置于辐射室箱体内;一排重整炉管对应一根重整原料气进口支干管,每根重整原料气进口支干管上开设与每排重整炉管数量相同的分支,通过柔性管将重整炉管气体进口与重整原料气进口支干管相连;燃烧器成(2m+1)排布置于辐射室下方底壁板;重整炉管气体出口通过斜三通与冷壁支管连接;过渡段是辐射室箱体的两侧壁板上方设有若干个过渡段分支管引出至过渡段分支干管,两分过渡段分支干管在辐射室箱体的一端汇集成过渡段总管;过渡段总管与对流段相连,所述的对流段通过引风机与烟囱相连;所述的对流段由≥4个换热器组成,所述换热器为急速蒸发器、重整原料预热器、蒸汽过热器、脱硫焦炉气预热器、炉顶气预热器和燃烧空气预热器中的至少4种;将910℃的高温重整气产物送至竖炉进行下级反应”。以上三个现有专利技术是将富烃气(如,天然气、焦炉煤气)和竖炉炉顶煤气混合后,在管式转化炉加热,并将混合气加热到850~1000℃温度后,喷入竖炉。此种工艺存在以下问题:(1)由于重整炉管采用外加热,因此限制了重整管直径,造成单个重整管体积小,重整炉管数量庞大。重整炉管多达几百根,燃烧器几十个。这造成辐射室加热系统设备庞大,安装复杂;(2)耐高温重整炉管和燃烧器价格非常昂贵,一套重整炉设备通常需要几百根重整炉管,因此,投资过大;(3)由于受耐高温炉管材质的限制,气体加热温度不能超过1000℃,因此限制了无催化剂条件下的碳氧化合物的转化率;(4)排放烟气和利用烟气余热的过渡段以及对流段设备庞大,结构复杂,再次增加投资成本;(5)富ch4煤气和非烃类炉顶煤气混合后一起参与ch1的重整,增加了重整炉的体积和催化剂的数量。
3.又再如,申请号cn201280070307.8,专利名为利用焦炉气制备直接还原铁(dri)的方法和设备的专利提出,“提供一种气体加热器设计,所述设计在加热cog或类似合成气时
使碳沉积物最大限度地减少,或者提供在线清洁措施定期去除碳沉积物,以避免污染和堵塞加热器管。”,其主要措施是,将不含烃的氢和一氧化碳混合气体作为第一还原气体流,包含焦炉气的气体作为第二流,将第一流加热后,再将第二流混入第一流,以便所得混合物在高于700℃的温度形成第三气体流,从而将来自包括cog的第二流中存在的碳化合物的所述碳沉积物最大限度地减小。该方案的问题是:(1)该方案采用外热,受管材耐热限制,其最高温度不超过980℃,即该专利第三气体流在700℃~980℃之间,且为了兑入焦炉气量,第三气体流更接近700℃,而烃类重整成h2和co的反应在700℃以上才开始,因此在此温度范围内,重整成h2和co的转化率也有限,烃类的转化率越低,析碳量越大,所以解决积碳量有限,不足以解决积碳问题;(2)清理积碳时,管路复杂,高温阀门多,实际应用时实施困难。
技术实现要素:
4.为了解决上述技术问题,本发明提供了一种气基竖炉直接还原方法。
5.本发明目的之一是降低项目整体投资。
6.本发明目的之二是简化气体加热装置结构。
7.本发明目的之三是不使用催化剂。
8.本发明目的之四是提高原料气的利用率。
9.本发明目的之五是提高富烃气转化率,降低积碳风险。
10.本发明的其它目的将在后面指出,或者对本领域的技术人员显而易见。
11.为实现此目的,本发明还原方法采用以下的技术方案:
12.一种气基竖炉直接还原方法,包括将一定粒度的铁氧化物从炉顶装料装置加入气基竖炉,还原气从竖炉外加热后,喷入气基竖炉内,在气基竖炉内,铁氧化物与还原气反应,被还原成直接还原铁,直接还原铁经气基竖炉下部排出炉外,反应产生的粗煤气由竖炉炉顶排出,还原气包括富烃类还原气和非烃类还原气,其中将富烃类还原气与氧化剂在加热装置一中加热到1100℃~1350℃,形成第一气流,然后再向第一气流中加入非烃类还原气,形成第二气流,将第二气流喷入气基竖炉内,加热装置一内衬为耐火材料,并由耐火材料构成一个腔体,氧化剂为o2、h2o或co2中的一种或两种以上的混合物,非烃类还原气为h2和co中的任何一种或两种混合气体。
13.与现有技术相比,本发明方法具有以下有益效果:
14.(1)降低项目整体投资:a使用耐火材料内衬的加热炉代替数百根耐热钢管组成的加热炉,降低投资;b不使用催化剂,降低对富烃气的硫含量要求,进而简化工序,减少投资;c无复杂庞大的换热系统,进一步降低投资。
15.(2)提高原料气的利用率:与富烃气中混入h2和/或co后和氧反应相比,单独的富烃气ch1含量更高,当与氧反应生成高温气体时,生成有效气体h2+co的量更大,这会提高原料气的利用率,同时降低能耗。而混入h2和/或co后,为达到高温,会增加h2和co的消耗,生成无效成分h2o或co2。
16.(3)富烃气与氧化剂在1100~1350℃反应转化率高,降低积碳风险:富烃气与纯氧缺氧燃烧,在压力为0.1~0.5mpa时,加热至1100~1200℃时,ch1几乎全部转化为h2和co;在压力大于0.5mpa时,加热至1200~1350℃时,ch1几乎全部转化为h2和co,温度高于1350℃时,转化为h2和co的有效气体量减少,h2o和co2量增加,因此1100~1350℃是富烃气与氧化
剂反应的最佳温度区间。
17.(4)气体加热炉结构简单,只有一个腔体,而传统的管式加热炉由数百根钢管腔体构成。
18.(5)无庞大的换热系统。
19.本发明方法的优选方案为:
20.加热装置一采用部分氧化转化炉,在部分氧化转化炉中,富烃类还原气与纯氧缺氧燃烧,形成高温第一气流。
21.加热装置中,压力为0.1~0.5mpa时,富烃类还原气与纯氧缺氧燃烧,加热至1100~1200℃。
22.加热装置中,压力大于0.5mpa时,富烃类还原气与纯氧缺氧燃烧,加热至1200~1350℃℃。
23.进一步地,非烃类气的加热和喷入气基竖炉过程再分为如下方案:
24.第一种方案,一部分非烃类还原气加入第一气流中,形成第二气流,另一部分非烃类还原气在加热装置二中加热,形成第三气流,第二气流从气基竖炉还原段上的一排风口喷入竖炉,第三气流从气基竖炉还原段上另一排风口喷入竖炉。
25.第二种方案,将非烃类还原气在加热装置二中加热后,再加入第一气流中,形成第二气流,将第二气流从气基竖炉还原段风口喷入竖炉。
26.进一步地,在第二种方案中,将非烃类还原气经加热装置二加热到500~800℃,再加入第一气流中。
27.进一步地,在加热装置一中加入水蒸气,有利于烃类气体重整为h2和co。
28.进一步地,第一种方案中,竖炉本体还原段的上排风口与下排风口错位布置,即上下风口不在一条垂直线上。
29.再进一步地,上排的每一个风口位于相邻的下排两个风口连成水平弧线的垂直平分线上。
附图说明
30.图1为本发明一种气基竖炉直接还原流程图;
31.图2为本发明第二种气基竖炉直接还原流程图;
32.图3为本发明第三种气基竖炉直接还原流程图;
33.图4为本发明第四种气基竖炉直接还原流程图。
34.图5为本发明气基竖炉主视图和气基竖炉上的风口布置示意图。
35.图中标记为:1-气基竖炉,2-部分氧化转化炉(加热装置一),3烧嘴,4-氧气,5-富烃气总管,6-竖炉炉顶煤气,7-水蒸气总管,8-加热装置二,9-co气管路,11-装料装置,12-竖炉风口,13-出料装置,21-转化炉出口管路,61-除尘器,62-脱二氧化碳装置,121-竖炉第一排风口,122-竖炉第二排风口,a1-第一排第一个风口,a2-第一排第二个风口,a3-第一排第三个风口,a4-第一排第四个风口,a5-第一排第五个风口,b1-第二排第一个风口,b2-第二排第二个风口,b3-第二排第三个风口,b4-第二排第四个风口,b5-第二排第五个风口。
具体实施方式
36.为充分了解本发明之目的、特征及功效,借由下述具体的实施方式,对本发明做详细说明,但本发明并不仅仅限于此。
37.请参阅图1和图2。富烃气采用天然气、煤层气或焦炉煤气,该气基竖炉直接还原方法如下:将铁氧化物从炉顶装料装置11加入气基竖炉1。富烃气总管5内的富烃气和氧气4通入转化炉2内的烧嘴3中,氧气4与富烃气的体积比约为20~70%,部分氧化转化炉2内压力0.1~1.0mpa,氧气4与富烃气在转化炉内缺氧燃烧,生成h2和co,在转化炉2出口管路21处,气体达到1100~1350℃。将一部分竖炉炉顶煤气6经除尘器61和脱二氧化碳装置62处理后(或其它来源的h2和co混合气体)注入转化炉2出口管路21中,或经加热装8加热后注入转化炉2出口管路21中,形成混合气体,混合后气体温度约900~1100℃。混合后的气体经风口12进入气基竖炉,在气基竖炉1内,铁氧化物与风口12进入的混合气反应,被还原成直接还原铁,直接还原铁经气基竖炉1下部出料装置13排出炉外,反应产生的竖炉炉顶煤气6由竖炉炉顶排出。
38.请参阅图3。此流程是,在图1和图2工艺流程的基础上,气基竖炉设两排风口,h2和co混合气体在加热装置二8中加热后,经气基竖炉第一排风口121进入竖炉;经转化炉2加热后形成的混合气体由气基竖炉第二排风口122进入竖炉,这种多排风口的方法,有利于竖炉内气流均匀分布。此外水蒸气总管7向转化炉2的烧嘴3中通入水蒸气。这种方法既能有助于富烃气中甲烷重整成h2和co,又能通过水蒸气降温,保护转化炉2的炉顶和烧嘴3。
39.请参阅图4。此流程是,在图1流程的基础上,将脱出二氧化碳的竖炉炉顶净化煤气混入co气管路9中的co气后,由加热装置二8加热,混入co气目的是用于调节h2与co的比值。co气由转炉煤气或高炉煤气分离提取。
40.请参阅图5。图5为本发明气基竖炉主视图和气基竖炉上的风口布置示意图。气基竖炉还原段设两排风口,每一排风口均环绕气基竖炉还原段均匀分布,即a1、a2、a3、a4、a5.....相邻风口间距离相等,b1、b2、b3、b4、b5.......相邻风口间距离相等,且上排的风口与下排风口错位布置,例如,a1风口位于b1和b2风口之间连成弧线的垂直线上,优选地a1风口位于b1和b2风口之间连成弧线的垂直平分线上。解决了气基竖炉横截面上气基竖炉横截面上气流和温度分布不均问题。例如b1和b2风口之间的垂直上方增加了风口a1,解决了b1和b2风口之间的气流弱和温度低的问题。还可以通过调整上下排风口直径,达到上排风口吹透气基竖炉中心,下排风口吹透气基竖炉周边的目的。上下排风口出可以互换,即下排风口吹透气基竖炉中心,上排风口吹透气基竖炉周边。两排风口的设置增加了气基竖炉操作调节手段,提高了产品质量。
41.实施例一
42.请参阅图1。富烃气采用天然气。该气基竖炉直接还原方法如下:将铁氧化物从炉顶装料装置11加入气基竖炉1。富烃气总管5内的富烃气和氧气4通入转化炉2内的烧嘴3中,氧气4与富烃气的体积比约为70%,部分氧化转化炉2内压力0.55mpa,氧气4与富烃气在转化炉内缺氧燃烧,生成h2和co,在转化炉2出口管路21处,气体达到1350℃。将一部分竖炉炉顶煤气6经除尘器61和脱二氧化碳装置62处理后,炉顶净化煤气在加热装置二8中加热至约550℃后,注入转化炉2出口管路21中,形成混合气体,形成混合气体的炉顶净化煤气与富烃气流量比2.5~3.5,混合后气体温度约950℃。混合后的气体经风口12进入气基竖炉,在气
基竖炉1内,铁氧化物与风口12进入的混合气反应,被还原成直接还原铁,直接还原铁经气基竖炉1下部出料装置13排出炉外,反应产生的竖炉炉顶煤气6由竖炉炉顶排出。另一部分竖炉炉顶煤气6,送往焦炉、高炉热风炉或轧钢加热炉作为加热的燃料。
43.实施例二
44.请参阅图2。富烃气采用焦炉煤气。该气基竖炉直接还原方法如下:将铁氧化物从炉顶装料装置11加入气基竖炉1。富烃气总管5内的富烃气和氧气4通入转化炉2内的烧嘴3中,氧气4与富烃气的体积比约为30%,部分氧化转化炉2内压力0.8mpa,氧气4与富烃气在转化炉内缺氧燃烧,生成h2和co,在转化炉2出口管路21处,气体达到1350℃。将一部分竖炉炉顶煤气6经除尘器61和脱二氧化碳装置62处理后,炉顶净化煤气注入转化炉2出口管路21中,形成混合气体,形成混合气体的富烃气与炉顶净化煤气流量比2~3,混合后气体温度约1050℃。混合后的气体经风口12进入气基竖炉,在气基竖炉1内,铁氧化物与风口12进入的混合气反应,被还原成直接还原铁,直接还原铁经气基竖炉1下部出料装置13排出炉外,反应产生的竖炉炉顶煤气6由竖炉炉顶排出。另一部分竖炉炉顶煤气6,送往焦炉、高炉热风炉或轧钢加热炉作为加热的燃料。
45.实施例三
46.请参阅图3和图5。富烃气采用焦炉煤气。该气基竖炉直接还原方法如下:将铁氧化物从炉顶装料装置11加入气基竖炉1。富烃气总管5内的富烃气(约600m1)和氧气4通入转化炉2内的烧嘴3中,氧气4与富烃气的体积比约为26%,部分氧化转化炉2内压力0.5mpa,氧气4与富烃气在转化炉内缺氧燃烧,生成h2和co,在转化炉2出口管路21处,气体达到1200℃。将一部分竖炉炉顶煤气6经除尘器61和脱二氧化碳装置62处理后,分成两个气流,一个气流约750m3的炉顶净化煤气在加热装置二8中加热至约980℃后,从气基竖炉第一排风口121喷入竖炉;另一个气流,约150m3的炉顶净化煤气注入转化炉2出口管路21中,形成混合气体,混合后气体温度约1020℃。混合后的气体经气基竖炉第二排风口122进入气基竖炉,在气基竖炉1内,铁氧化物与风口12进入的混合气反应,被还原成直接还原铁,直接还原铁经气基竖炉1下部出料装置13排出炉外,反应产生的竖炉炉顶煤气6由竖炉炉顶排出。未使用的竖炉炉顶煤气6,送往焦炉、高炉热风炉、烧结、球团或轧钢加热炉作为加热的燃料。此外水蒸气总管7向转化炉2的烧嘴3中通入水蒸气。这种方法既能有助于富烃气中甲烷重整成h2和co,又能通过水蒸气降温,保护转化炉2的炉顶和烧嘴3。第一排风口包括a1风口、a2风口、a3风口、a4风口、a5风口.....,第二排风口包括b1风口、b2风口、b3风口、b4风口、b5风口.....。
47.实施例四
48.请参阅图4。富烃气采用焦炉煤气。该气基竖炉直接还原方法如下:将铁氧化物从炉顶装料装置11加入气基竖炉1。富烃气总管5内的富烃气(约500m3)和氧气4通入转化炉2内的烧嘴3中,氧气4与富烃气的体积比约为20%,部分氧化转化炉2内压力0.1mpa,氧气4与富烃气在转化炉内缺氧燃烧,生成h2和co,在转化炉2出口管路21处,气体达到11()0℃。将一部分竖炉炉顶煤气6经除尘器61和脱二氧化碳装置62处理后,约800m3的炉顶净化煤气混入约250m3的co气(co气来源于转炉煤气或高炉煤气)后,在加热装置二8中加热至约750℃后,注入转化炉2出口管路21中,形成混合气体,混合后气体温度约900℃。混合后的气体经风口12进入气基竖炉,在气基竖炉1内,铁氧化物与风口12进入的混合气反应,被还原成直
接还原铁,直接还原铁经气基竖炉1下部出料装置13排出炉外,反应产生的竖炉炉顶煤气6由竖炉炉顶排出。另一部分竖炉炉顶煤气6,送往焦炉、高炉热风炉或轧钢加热炉作为加热的燃料。在此方法中,也可将氧气4与富烃气的体积比改为25%,部分氧化转化炉2内压力为0.2mpa,氧气4与富烃气在转化炉内缺氧燃烧,生成h2和c(),在转化炉2出口管路21处,气体达到1200℃。将一部分竖炉炉顶煤气6经除尘器61和脱二氧化碳装置62处理后,约800m3的炉顶净化煤气混入约250m3的co气(co气来源于转炉煤气或高炉煤气)后,在加热装置二8中加热至约680℃后,注入转化炉2出口管路21中,形成混合气体,混合后气体温度约900℃。再将混合气体吹入气基竖炉。
49.以上列举的仅是本发明的优选实施例,当然本领域的技术人员可以对本发明进行改动和变型,倘若这些修改和变型属于本发明权利要求及其等同技术的范围之内,均应认为是本发明的保护范围。