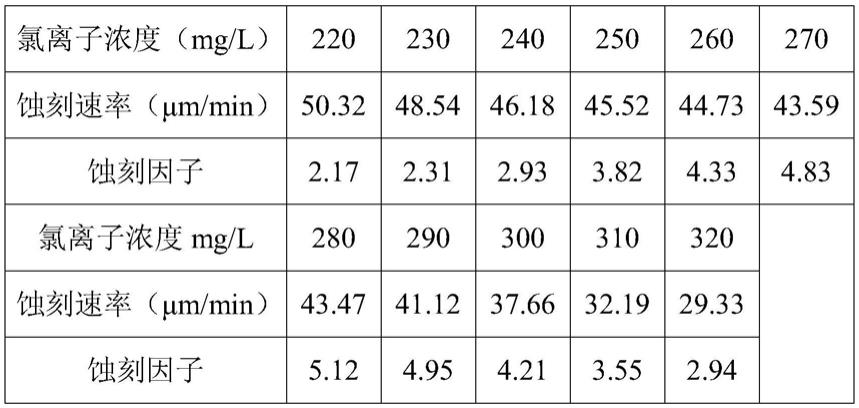
一种用于pcb板的低酸度蚀刻生产方法以及双液型酸性蚀刻液体系
技术领域
1.本发明属于酸性蚀刻的技术领域,具体涉及一种用于pcb板的低酸度蚀刻生产方法以及双液型酸性蚀刻液体系。
背景技术:
2.随着电子产品的更新迭代、功能日益强大,对于组合电子产品的各项配件的要求同样也水涨船高,尤其是被称为“电子产品之母”的pcb,对其精密度和电导率的要求不断提升。因此,pcb制造企业也在不断的提升自己的综合制程能力,目前全世界50%以上的pcb制造产能在中国,中国的pcb制造企业不仅要面对技术和制造能力的提升还要面对人力成本上升、环保压力日益增大等一系列的问题。
3.pcb企业核心的利益在于制造线路板的速度(蚀刻速率),所能制造的线路板的最大精密程度(蚀刻因子),这两点决定了企业的竞争能力和获得经济效益的上限。
4.另外,在制造过程中的环境污染问题,也是pcb制造企业核心关注的问题之一。比如,酸性蚀刻生产中,酸当量越高蚀刻速率就会越快,当酸性蚀刻生产槽中的酸当量超过2.5时会带来如下的负面效果:首先,酸性蚀刻生产槽中的酸度超过2.5当量时容易出现攻击油墨的或干膜的情况,使得线路出现缺口或狗牙状,影响电导率;其次,酸度超过2.5当量时生产槽容易发生如下副反应:6h
+
+5cl-+clo
3-→
2cl2↑
+3h2o,该反应所产生的氯气为剧毒气体,可造成严重的安全事故;第三,酸性蚀刻生产槽酸当量超过2.5时,由于生产槽液长期保持在50℃以上使得生产槽液中的氯化氢大量挥发到空气中。其中绝大部分被尾气吸收系统吸收造成尾气吸收系统片碱用量增加同时对尾气吸收系统的单位时间吸收量要求提高,增加运行费用以及设备投入。少部分氯化氢溢散到车间的空气中,对生产员工的身体健康造成影响,严重的将引发呼吸道的职业病;第四,酸性蚀刻生产槽的酸当量在2.5以上时,水洗水中的酸度随之增高,废水站需要加入更多的片碱来中和,增加废水处理成本。
技术实现要素:
5.为了解决上述问题,本发明的目的在于提供一种用于pcb板的低酸度蚀刻生产方法以及双液型酸性蚀刻液体系,还提供了一种添加进酸性蚀刻液的蚀刻液降酸助剂,所述蚀刻液降酸助剂,用于蚀刻生产中能够提高蚀刻速率、提高蚀刻因子以及降低蚀刻体系的酸当量。
6.本发明的技术内容如下:
7.本发明提供了一种用于提高酸性蚀刻生产质量的蚀刻液降酸助剂,所述蚀刻液降酸助剂的组成包括氰酸盐和乙二酸二酰肼的一种或两种;
8.所述氰酸盐包括氰酸钠、氰酸钾或氰酸铵;
9.所述酸性蚀刻生产中,所述氰酸盐的浓度为400~1000mg/l,所述乙二酸二酰肼的浓度为70~100mg/l;
10.当氰酸盐和乙二酸二酰肼混合使用时,其使用体积比为(1~4):(1~4)。
11.本发明还提供了一种用于提高酸性蚀刻生产质量的蚀刻液添加剂,所述蚀刻液添加剂的组成包括上述降酸助剂、氯化铵以及氯化钠;
12.所述蚀刻液添加剂的酸当量为4.0~7.0;
13.所述酸性蚀刻生产中,氯化铵的工作浓度为3000-30000mg/l,氯化钠的工作浓度为5000-50000mg/l。
14.本发明还提供了一种蚀刻液添加剂应用于pcb板生产的低酸度双液型酸性蚀刻液体系。
15.本发明还提供了一种应用于pcb板低尾气生产的低酸度的双液型酸性蚀刻液体系,所述酸性蚀刻液的组成包括氧化剂、上述蚀刻液添加剂;
16.所述酸性蚀刻液应用于pcb生产中,所形成的工作槽液酸当量为0.4~1.5,氧化剂的浓度为180~400g/l,槽液氯离子浓度为240~270g/l;
17.所述氧化剂包括氯酸钠、次氯酸钠的一种。
18.本发明还提供了一种用于pcb板的低酸度蚀刻生产方法,包括如下步骤,采用上述酸性蚀刻液体系对pcb板进行蚀刻生产,生产中工作槽液的酸当量为0.4~1.5,并实现了蚀刻速率提高到40~50μm/min,蚀刻因子在4.0~5.0。
19.本发明的有益效果如下:
20.本发明的低酸度生产蚀刻方法中,采用的氰酸盐、乙二酸二酰肼作为降酸助剂,与氯化钠、氯化钠等形成蚀刻液添加剂,应用于pcb板酸性蚀刻液中,可以加快蚀刻速率,提高蚀刻因子;并且pcb板低尾气生产所用的酸性蚀刻液,采用的氧化剂浓度为180~400g/l之间。相对于传统的酸性蚀刻,本发明的酸性蚀刻的生产槽液酸度更低,所用的蚀刻液添加剂可以代替传统采用的31%工业浓盐酸,不再使用危险性高且易挥发的31%工业浓盐酸,减少了污染,改善了环境,总体上符合酸性蚀刻发展的方向;并且使得酸性蚀刻的生产当中,蚀刻速率达到40~50μm/min,蚀刻因子达到4.0~5.0,大大优于传统酸性蚀刻液(蚀刻速率25~35μm/min,蚀刻因子3.0~4.0);
21.本发明将氰酸盐、乙二酸二酰肼应用于pcb板生产的酸性蚀刻液中,形成低酸度体系,既提高了蚀刻速率、蚀刻因子,又降低了酸当量,减少了氯气的产生,满足pcb制造企业的生产需求的同时,极大地改善了pcb制造环境,适应了市场的发展,走向环境友好型路线,这对蚀刻技术的应用与拓展能够带来极大的贡献。
具体实施方式
22.以下通过具体的实施案例对本发明作进一步详细的描述,应理解这些实施例仅用于说明本发明而不用于限制本发明的保护范围,在阅读了本发明之后,本领域技术人员对本发明的各种等价形式的修改均落于本技术所附权利要求所限定。
23.若无特殊说明,本发明的所有原料和试剂均为常规市场的原料、试剂。
24.在现有pcb板的酸性蚀刻生产中,由于需要投入盐酸蚀刻单质铜,因此酸性蚀刻槽液中存在大量的氯离子:
25.蚀刻生产中,槽液中的二价的铜离子氧化单质铜生成一价铜:cu
2+
+cu
→
2cu
+
,该反应直接发生在pcb板上,把多余的单质铜从pcb板上蚀刻下来;
26.然后槽液中的蚀刻液把一价铜离子氧化成二价铜离子:6h
+
+6cu
+
+clo
3-→
6cu
2+
+cl-+3h2o,该反应发生在槽液中,可视为二价铜离子的再生过程;
27.由上可见,槽液中的氯离子作为二价铜离子的主要络合剂主要起到稳定游离二价铜离子的作用;因此,氯离子浓度影响着酸性蚀刻的速率。为了研判最佳的氯离子浓度,将其它生产条件固定,蚀刻温度为50℃,上压2.2kg,下压2.0kg,氧化还原电位550mv,酸当量1.2,比重1.290,单独改变槽液中氯离子的浓度。
28.测试平均蚀刻速率和蚀刻因子如下:
29.表1蚀刻效果测试
[0030][0031]
由表1可见,氯离子浓度较低时平均蚀刻速率虽然很高但是蚀刻因子根本达不到生产的要求,当氯离子的浓度超过300克每升时平均蚀刻速率和平均蚀刻因子都是下降的,这种情况是由于蚀刻速率的急剧下降使得蚀刻沙滩位大大增加所致。
[0032]
因此,可以判定酸性蚀刻生产槽中氯离子最佳浓度范围为250~300g/l。
[0033]
此外,蚀刻环境的酸度也很关键,一定范围内,酸当量越高蚀刻速率就会越快;但会产生一系列负面效果,而降低酸度会影响蚀刻速率。因此,通过添加本发明实施例的降酸助剂,可以促进如下反应的进行:
[0034]
cu
2+
+cu
→
2cu
+
;
[0035]
6cu
+
+clo
3-→
6cu
2+
+cl-+3h2o;
[0036]
4h
+
+o2+4cu
+
→
6cu2+3h2o;
[0037]
可同时实现蚀刻速率和蚀刻因子的提高,减低体系的酸当量。
[0038]
当固定其它反应条件,蚀刻温度为50℃,上压2.2kg,下压2.0kg,氧化还原电位550mv,酸当量1.2,比重1.290,改变氰酸盐在酸性蚀刻槽液中的浓度,所得到的蚀刻速率和蚀刻因子的结果如表2、表3和表4所示。
[0039]
实施例1
[0040]
一种应用于pcb板低尾气低酸度的蚀刻生产方法,其蚀刻生产采用的酸性蚀刻液体系的组成包括氧化剂、蚀刻液添加剂;
[0041]
所述氧化剂包括氯酸钠、次氯酸钠的一种;
[0042]
所述蚀刻液添加剂包括氰酸盐、氯化铵、氯化钠,其酸当量为5.0~5.5,添加剂的使用使得所形成的酸性蚀刻工作槽液中,经检测酸当量为0.8~1.2,氧化剂的浓度为320~
370g/l,槽液氯离子浓度为240~250g/l,表明,相比传统使用了31%工业浓盐酸的酸性蚀刻液,本发明的酸性蚀刻液体系酸度更低,高效且安全;
[0043]
所述氯化铵的工作浓度为15000-20000 mg/l,氯化钠的工作浓度为35000-40000 mg/l;
[0044]
所述氰酸盐包括氰酸钠、氰酸钾或氰酸铵,其不同浓度的使用效果分别如下表所示,其酸性蚀刻环境为50℃,上压2.2
㎏
,下压2.0
㎏
,氧化还原电位550mv,酸当量1.2n的条件下,蚀刻时间为1h,每隔10min记录蚀刻效果数据,得到蚀刻的速率范围以及平均蚀刻因子的数值如下表所示。
[0045]
表2蚀刻效果测试
[0046]
氰酸钠浓度(mg/l)100200300400500蚀刻速率(μm/min)28~3230~3433~3738~4240~43蚀刻因子3.13.23.84.24.3氰酸钠浓度(mg/l)6007008009001000蚀刻速率(μm/min)44~4842~4641~4538~4133~38蚀刻因子4.44.74.64.54.0
[0047]
由表2可见,加入氰酸钠可以加快蚀刻速率,提高蚀刻因子;其浓度的最佳范围在400~800 mg/l。
[0048]
表3蚀刻效果测试
[0049][0050][0051]
由表3可见,加入氰酸钾可以加快蚀刻速率,提高蚀刻因子;其浓度的最佳范围在600~1000 mg/l。
[0052]
表4蚀刻效果测试
[0053]
氰酸铵浓度(mg/l)100200300400500蚀刻速率(μm/min)30~3332~3635~3936~4038~43蚀刻因子3.23.33.33.74.1氰酸铵浓度(mg/l)6007008009001000蚀刻速率(μm/min)42~4644~4943~4643~4742~45蚀刻因子4.34.34.54.74.6
[0054]
由表4可见,加入氰酸铵可以加快蚀刻速率,提高蚀刻因子;其浓度的最佳范围在500~900 mg/l。
[0055]
实施例2
[0056]
一种应用于pcb板低尾气低酸度的蚀刻生产方法,其蚀刻生产采用的酸性蚀刻液体系的组成包括氧化剂、蚀刻液添加剂;
[0057]
所述氧化剂包括氯酸钠、次氯酸钠的一种;
[0058]
所述蚀刻液添加剂包括乙二酸二酰肼、氯化铵、氯化钠,其酸当量为4.0~5.0,添加剂的使用使得所形成的酸性蚀刻工作槽液中,经检测酸当量为0.4~0.8,氧化剂氯酸钠的浓度为300~400 g/l,氯离子浓度为260~270 g/l;
[0059]
所述氯化铵的工作浓度为20000-30000 mg/l,氯化钠的工作浓度为5000-10000mg/l。
[0060]
酸性蚀刻环境为50℃,上压2.2
㎏
,下压2.0
㎏
,氧化还原电位550mv,酸当量1.2n的条件下,改变溶液中乙二酸二酰肼的浓度,结果如下表所示。
[0061]
表5蚀刻效果测试
[0062]
乙二酸二酰肼浓度(mg/l)01020304050蚀刻速率(μm/min)30~4631~4533~4535~4635~4436~47蚀刻因子3.43.63.73.73.64.1乙二酸二酰肼浓度(mg/l)60708090100110蚀刻速率(μm/min)35~4637~4838~4739~4938~4736~45蚀刻因子4.34.34.44.84.53.9
[0063]
由表5可见,加入乙二酸二酰肼可以加快蚀刻速率,提高蚀刻因子,当溶液中的乙二酸二酰肼浓度在70~100mg/l之间时,蚀刻速率稳定性较高,蚀刻因子较为理想。
[0064]
实施例3
[0065]
一种应用于pcb板低尾气低酸度的蚀刻生产方法,其蚀刻生产采用的酸性蚀刻液体系的组成包括氧化剂、蚀刻液添加剂;
[0066]
所述蚀刻液添加剂包括降酸助剂、氯化铵、氯化钠,所述降酸助剂为700mg/l的氰酸钠和90mg/l的乙二酸二酰肼混合,其酸当量为5.0~6.0,其混合使用之后所形成的酸性蚀刻工作槽液中,经检测酸当量为1.0~1.2,氧化剂的浓度为200~300g/l,槽液氯离子浓度为250~260g/l;
[0067]
所述氯化铵的工作浓度为10000-15000mg/l,氯化钠的工作浓度为25000-30000mg/l;
[0068]
酸性蚀刻环境为50℃,上压2.2
㎏
,下压2.0
㎏
,氧化还原电位550mv,酸当量1.2n的条件下,改变溶液中氰酸盐和乙二酸二酰肼的体积配比。
[0069]
表6蚀刻效果测试
[0070]
混合体积比1:11:21:31:41:51:6蚀刻速率(μm/min)44~4743~4644~4745~4840~4340~42蚀刻因子4.64.74.54.63.83.9混合体积比7:16:15:14:13:12:1蚀刻速率(μm/min)39~4239~4140~4240~4244~4745~48
蚀刻因子4.03.94.14.04.54.6
[0071]
由表6可见,当氰酸钠与乙二酸二酰肼的混合体积比为1:(1~3)以及(2~4):1时,蚀刻速率以及蚀刻因子均较高,表明氰酸钠与乙二酸二酰肼的混合体积比在较优范围为(1~4):(1~3)。
[0072]
实施例4
[0073]
一种应用于pcb板低尾气低酸度的蚀刻生产方法,其蚀刻生产采用的酸性蚀刻液体系的组成包括氧化剂、蚀刻液添加剂;
[0074]
所述酸性蚀刻液的组成包括氧化剂、蚀刻液添加剂;
[0075]
所述蚀刻液添加剂包括降酸助剂、氯化铵、氯化钠,所述降酸助剂为1000mg/l的氰酸钾和70mg/l的乙二酸二酰肼混合,其酸当量为5.5~6.0,其混合使用之后所形成的酸性蚀刻工作槽液中,经检测酸当量为1.3~1.5,氧化剂的浓度为180~230g/l,槽液氯离子浓度为250~260g/l;
[0076]
所述氯化铵的工作浓度为5000-10000mg/l,氯化钠的工作浓度为45000-50000mg/l。
[0077]
蚀刻环境条件同上。
[0078]
表7蚀刻效果测试
[0079]
混合体积比1:11:21:31:41:51:6蚀刻速率(μm/min)43~4644~4845~5043~4839~4239~40蚀刻因子4.64.54.54.74.34.3混合体积比7:16:15:14:13:12:1蚀刻速率(μm/min)38~4038~4040~4244~4645~4944~47蚀刻因子4.04.14.24.44.74.5
[0080]
由表7可见,当氰酸钾与乙二酸二酰肼的混合体积比为1:(1~4)以及(1~4):1时,蚀刻速率以及蚀刻因子均较高,蚀刻速率以及蚀刻因子均较高,表明氰酸钾与乙二酸二酰肼的混合体积比在较优范围为(1~4):(1~4)。
[0081]
实施例5
[0082]
一种应用于pcb板低尾气低酸度的蚀刻生产方法,其蚀刻生产采用的酸性蚀刻液体系的组成包括氧化剂、蚀刻液添加剂;
[0083]
所述蚀刻液添加剂包括降酸助剂、氯化铵、氯化钠,所述降酸助剂为900mg/l的氰酸铵和80mg/l的乙二酸二酰肼混合,其酸当量为6.5~7.0,其混合使用之后所形成的酸性蚀刻工作槽液中,经检测酸当量为1.1~1.4,氧化剂的浓度为230~250g/l,槽液氯离子浓度为260~270g/l;
[0084]
所述氯化铵的工作浓度为3000-8000mg/l,氯化钠的工作浓度为5000-10000mg/l。
[0085]
蚀刻环境条件同上。
[0086]
表8蚀刻效果测试
[0087]
混合体积比1:11:21:31:41:51:6蚀刻速率(μm/min)44~4743~4743~4643~4640~4240~41蚀刻因子4.74.54.64.54.14.0混合体积比7:16:15:14:13:12:1
蚀刻速率(μm/min)38~4140~4239~4142~4644~4843~47蚀刻因子4.14.24.04.54.74.8
[0088]
由表8可见,当氰酸铵与乙二酸二酰肼的混合体积比为1:(1~4)以及(1~4):1时,蚀刻速率以及蚀刻因子均较高,蚀刻速率以及蚀刻因子均较高,表明氰酸铵与乙二酸二酰肼的混合体积比在较优范围为(1~4):(1~4)。
[0089]
由上可见,在pcb板低尾气低酸度的蚀刻生产中,当氰酸盐与乙二酸二酰肼混合作为蚀刻液降酸助剂时,可以加快蚀刻速率,提高蚀刻因子;并且pcb板生产的酸性蚀刻液经过以上降酸助剂混合之后,相对于传统的酸性蚀刻,本发明的酸性蚀刻的生产槽液酸度更低,所用的蚀刻液添加剂可以代替传统采用的31%工业浓盐酸,使得生产环境更优越;并且使得酸性蚀刻的生产当中,蚀刻速率达到40~50μm/min,蚀刻因子达到4.0~5.0,大大优于传统酸性蚀刻液(蚀刻速率25~35μm/min,蚀刻因子3.0~4.0)。