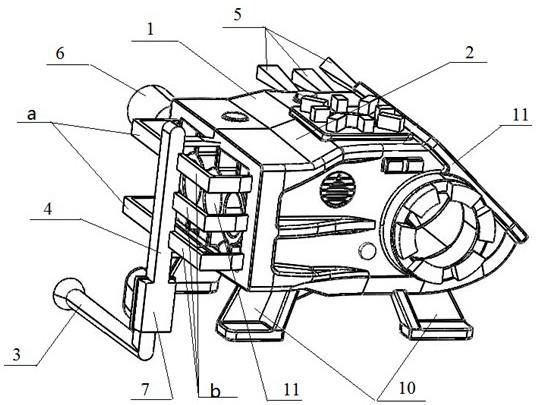
采油机齿轮箱体的铸造模具及采油机齿轮箱的制备方法
1.技术领域
2.本发明涉及采油机齿轮箱领域,特别涉及一种采油机齿轮箱体的铸造模具及采油机齿轮箱的制备方法。
背景技术:
3.齿轮箱是油田开采常用的设备,齿轮箱的制备通常是浇注制备,由于用于浇注齿轮箱体的钢水温度高达1400℃,而模具通常只能耐500℃左右的高温,所以通常是使用呋喃树脂与沙子混合后,先使用齿轮箱的外壳模具的上模通过沙子制作成上模沙型,使用下模通过沙子制作成下模沙型,在上模沙型和下模沙型内安装放置好坭芯后,将上模沙型和下模沙型卡合定位形成齿轮箱体的腔体,然后通过直浇道向腔体内浇注高温钢水,待高温钢水凝固冷却凝固后将上模沙型和下模沙型剥离后完成齿轮箱的制备。
4.由于齿轮箱尺寸较大,上述浇注成型的过程中经常会出现铸件内部温差较大,应力较大的情况,导致齿轮箱成品内部容易产生裂纹,无法保证齿轮箱的性能。
技术实现要素:
5.发明目的:针对现有技术中存在的问题,本发明提供一种采油机齿轮箱体的铸造模具及采油机齿轮箱的制备方法,本发明能够使得后续浇注成型齿轮箱体的过程中温差较小,有效缓解内部应力集中、应力较大的问题,通过浇注系统/冒口/冷铁的合理配合使用可以得到组织更加致密、综合机械性能更加优秀的采油机齿轮箱,使得制成的产品不易产生裂纹,性能较好,能够在零下60摄氏度的低温工况连续工作20年。
6.技术方案:本发明提供了一种采油机齿轮箱体的铸造模具,包括上模和下模,所述上模包括相互连通的直浇道和横浇道,其中,所述上模中还包括至少一条与所述横浇道连通的内浇道,所述下模中包括至少两条与所述横浇道连通的内浇道,且所述下模中的内浇道的数量大于所述上模中的内浇道的数量;所述上模和下模中还分别包括与所述内浇道连通的模腔。
7.优选地,所述上模中的内浇道,靠近所述横浇道的一端内径较大,靠近所述模腔的一端内径较小。高温钢水经内浇道注入温度较低的上模沙型的腔体内后,上模沙型的腔体内的钢水会冷却凝固,由于铁水温差体积收缩的作用,腔体内的钢水冷却时可能会出现钢水倒流入内浇道的情况,所以本技术将内浇道靠近模腔的一端设计成内径较小,内径较小则此处的钢水会比较快速的先凝固,有效防止钢水倒流入浇道。
8.优选地,所述下模中的内浇道,靠近所述横浇道的一端内径较大,靠近所述模腔的一端内径较小。高温钢水经内浇道注入温度较低的下模沙型的腔体内后,下模沙型的腔体内的钢水会冷却凝固,由于铁水温差体积收缩的作用,腔体内的钢水冷却时可能会出现钢水倒流入内浇道的情况,所以本技术将内浇道靠近模腔的一端设计成内径较小,内径较小
则此处的钢水会比较快速的先凝固,有效防止钢水倒流入浇道。
9.进一步地,所述下模中还设置有中空锲形脚活块,所述中空锲形脚活块与所述下模之间相互独立,用于形成采油机齿轮箱体的锲形脚。中空锲形脚活块的设置是为了在最终齿轮箱产品的下部形成锲形脚,便于齿轮箱的放置,如果该中空锲形脚活块与下模是一体结构,在制备下模沙型的时候,沙子凝固后形成下模沙型后,需要将下模沙型从下模外壁拔下来,而锲形脚腔体由于是倾斜的锲形,且下模沙型的硬度相对较低,在拔出的过程中很容易出现下模沙型在锲形脚的位置被损坏。所以,在本技术中,在齿轮箱体的下模中设计与其相互独立的中空锲形脚活块,在形成下模沙型的过程中,该中空锲形脚活块最终能够与沙子凝固成一体形成一个包括中空锲形脚活块的下模沙型(此时的中空锲形脚活块与下模分离),当向下模沙型的腔体内注入钢水后,则钢水就可以流入中空锲形脚活块的腔体内,最终凝固后形成与产品一体结构的锲形脚,有效避免下模沙型的制备过程中被损坏的情况。
10.进一步地,所述上模中的模腔外壁还分散设置有若干出气孔模柱。出气孔模柱的设置,使得后续能够在上模沙型的侧壁上形成出气孔,当后期向上模沙型的腔体内注入高温钢水时,上模沙型中的呋喃树脂在高温状态下燃烧形成的气体会经出气孔排出至上模沙型外,避免该气体混入钢水中导致最终产品内产生孔洞缺陷。
11.进一步地,所述上模中的模腔外壁还分散设置有若干冒口模柱。冒口模柱的设置,使得后续能够在上模沙型的内壁上形成冒口腔体,进而在产品上形成用于补缩的冒口。
12.进一步地,所述直浇道与所述横浇道之间通过过滤网放置腔连通。过滤网放置腔的设置使得最终产品能够形成用于防止过滤网的腔体,过滤网是为了将铁水中的杂质过来掉而设置的。
13.进一步地,所述上模的外壁还设置有定位柱;所述下模的外壁与所述定位柱对应的位置还设置有定位孔。上模上的定位柱,对应上模沙型中的定位孔,下模上的定位孔,对应下模沙型中的定位柱,定位柱和定位孔的设置是为了上模沙型和下模沙型能够卡合的更准确,铸件尺寸精度更高。
14.进一步地,所述定位柱在所述上模的外壁上对角设置,所述定位孔在所述下模的外壁上对角设置。定位柱和定位孔对角设置使得上模沙型和下模沙型能够卡合的更准确。
15.进一步地,所述上模的模腔还连通有本体试棒腔体。本体试棒腔体的设置是为了在最终产品外壳上形成本体试棒,本体试棒在产品形成后会被锯掉,用于产品的成分分析检测。
16.本发明还提供了一种所述的模具制备采油机齿轮箱的方法,包含以下步骤:s1:在齿轮箱体较厚的位置对应的上模外壁位置处放置冷铁,然后将呋喃树脂与沙子混合后浇注包裹在所述上模和冷铁外壁,凝固后形成沙子与冷铁成为一体的上模沙型,然后将凝固成型后的上模沙型从上模外壁拔出待用;s2:在齿轮箱体较厚的位置对应的下模外壁位置处放置冷铁然后将呋喃树脂与沙子混合后浇注包裹在所述下模、冷铁和中空锲形脚活块外壁,凝固后形成沙子、冷铁以及中空锲形脚活块成为一体的下模沙型,然后将凝固成型后的下模沙型从下模外壁拔出待用;s3:将下模沙型置于下方,将使用芯盒制备出的坭芯组装好之后置于下模沙型的腔体内对应位置,然后将上模沙型上的定位孔正对下模沙型上的定位柱卡扣在一起,在上模沙型的外壁对应冒口模柱的位置撒上发热剂;s4:通过上模沙型上形
成的直浇道向上模沙型和下模沙型卡扣形成的腔体内浇注钢水,钢水凝固后,分别将上模沙型和下模沙型剥离,完成采油机齿轮箱的浇铸成型;s5:对浇铸成型好的采油机齿轮箱进行退火处理,退火处理的条件为:在880~900℃条件下保温3-4小时,之后炉冷至700~720℃,保温3.0-4.0h,然后转移至冷却液中等温冷却至540~560℃后空冷至室温。。
17.有益效果:本技术中的采油机齿轮箱体的铸造模具中,上模中的内浇道数量小于下模中的内浇道数量的设计,能够使得后续浇注成型齿轮箱体的过程中温差较小,有效缓解内部应力集中、应力较大的问题,使得制成的产品不易产生裂纹,性能较好。原因如下:使用本技术中的模具制备出上模沙型和下模沙型后,上模沙型和下模沙型卡合后经上模沙型中的直浇道向腔体内注入高温钢水,由于下模沙型位于下方,在经直浇道注入钢水后,钢水沿横浇道进入首先经下模沙型的内浇道进入下模沙型的腔体内,高温的钢水进入到冷的下模沙型中后,钢水温度会降低,新进入的钢水温度较高,这样就会产生温差。当钢水注满下模沙型后再继续注入钢水时,钢水就会沿上模沙型的内浇道进入上模沙型的腔体。本技术中将下模的内浇道数量设计的比上模的内浇道数量多,由于上模沙型中的内浇道数量较少,经上模沙型的内浇道进入到上模沙型的钢水的速度小于经下模沙型中数量较多的内浇道进入至下模沙型的钢水的速度,在下模沙型的腔体已经注满钢水的情况下,下模沙型中的钢水的温度相对刚进入上模沙型腔体内的钢水温度低,而通过将上模中内浇道的数量设计成少于下模中内浇道数量来减缓进入上模沙型腔体内的钢水的速度,则可以减小刚进入上模沙型腔体内的钢水温度与已经位于下模沙型腔体内的铁水的温差之差,这样就能够减少产品内部应力集中,避免产品产生裂纹,保证产品性能。
18.本技术中制备采油机齿轮箱的方法,能够使得浇注成型齿轮箱体的过程中温差较小,有效缓解内部应力集中、应力较大的问题,使得制成的产品不易产生裂纹,性能较好。原因如下:(1)在制备上模沙型和下模沙型的时候,在齿轮箱体较厚的位置对应的上模和下模外壁位置处放置冷铁,沙子凝固后与冷铁形成一体结构的上模沙型和下模沙型,该冷铁设置在产品侧壁较厚的位置,这样就使得后续浇注高温钢水时,冷铁能够对产品侧壁较厚的位置进一步冷却,如果没有该冷铁,则产品侧壁较厚的位置相对其他较薄的位置冷却速度较慢,会造成产品局部温差较大,应力集中,应力较大,导致后续产品产生裂纹。本技术中通过在制备上模沙型的时候加入冷铁的设计,能够有效避免上述情况的发生,提高产品性能。
19.(2)本技术中,在将上模沙型和下模沙型卡扣在一起后,浇注钢水前,还在上模沙型的外壁对应冒口模柱的位置撒上发热剂,因为最终的产品在冒口模柱的位置形成用于补缩的冒口,冒口的冷却速度要慢于其他部位才能起到补缩的效果,所以,本技术中,在浇注钢水前,还在上模沙型的外壁对应冒口模柱的位置撒上发热剂,以减缓冒口位置的冷却速度。
20.(3)本技术中,在浇铸成型好采油机齿轮箱后对其进行退火处理,目的是细化铸件的组织晶粒,部分支柱状晶优化成等轴晶,组织更加稳定。可以让产品在20年连续工作不产生尺寸变化,在低温工况上使用更加优秀。
附图说明
21.图1为采油机齿轮箱体的铸造模具的立体结构示意图;图2为采油机齿轮箱体的铸造模具的立体结构示意图;图3为采油机齿轮箱体的铸造模具的仰视图。
具体实施方式
22.下面结合附图对本发明进行详细的介绍。
23.实施方式1:本实施方式提供了一种采油机齿轮箱体的铸造模具,如图1至3所示,包括上模1和下模2,上模1包括相互连通的直浇道3和横浇道4,直浇道3与横浇道4之间通过过滤网放置腔7连通。其中,上模1中还包括两条与横浇道4连通的内浇道a,下模2中包括三条与横浇道4连通的内浇道b,且下模2中的内浇道b的数量大于上模1中的内浇道a的数量;上模1和下模2中还分别包括与内浇道a和内浇道b连通的模腔,上模1的模腔还连通有本体试棒腔体8。上模1中的模腔外壁还分散设置有若干出气孔模柱5和若干冒口模柱6。上模1的外壁还对角设置有定位柱12;下模2的外壁与定位柱12对应的对角位置还设置有定位孔13。下模2中还设置有与该下模2之间相互独立的中空锲形脚活块10,该中空锲形脚活块10用于后续浇铸形成采油机齿轮箱体的锲形脚。
24.使用上述采油机齿轮箱体的铸造模具制备采油机齿轮箱的方法如下:s1:在齿轮箱体较厚的位置对应的上模1外壁位置处放置冷铁9,然后将呋喃树脂与沙子混合后浇注包裹在上模1和冷铁9外壁,凝固后形成沙子与冷铁9成为一体的上模沙型,然后将凝固成型后的上模沙型从上模1外壁拔出待用。
25.此时上模沙型中形成直浇道位置、横浇道位置、内浇道位置、出气孔、冒口位置、过滤网放置腔位置、定位孔以及本体试棒腔体位置;冷铁9能够对产品侧壁较厚的位置进一步冷却,使得产品侧壁较厚的位置相对其他较薄的位置冷却速度不会相差太大,使得产品局部温差较小,应力较小,保证后续产品不会产生裂纹。
26.s2:在齿轮箱体较厚的位置对应的下模2外壁位置处放置冷铁9,然后将呋喃树脂与沙子混合后浇注包裹在下模2、冷铁9和中空锲形脚活块10外壁,凝固后形成沙子、冷铁9以及中空锲形脚活块10成为一体的下模沙型,然后将凝固成型后的下模沙型从下模2外壁拔出待用。
27.此时,下模沙型中形成内浇道位置、定位柱以及锲形脚位置;在形成下模沙型的过程中,下模2外壁的中空锲形脚活块10与下模沙型形成一个整体,后续浇注钢水后,钢水能够在该中空锲形脚活块10内形成锲形脚,避免在下模2上直接设置锲形脚腔体导致的下模沙型拔下时造成损坏的情况。
28.s3:将下模沙型置于下方,将使用芯盒制备出的坭芯11(齿轮箱体内的一个部件)组装好之后置于下模沙型的腔体内对应位置,然后将上模沙型上的定位孔正对下模沙型上的定位柱卡扣在一起,在上模沙型的外壁对应冒口模柱6的位置撒上发热剂。
29.在浇注钢水前,在上模沙型的外壁对应冒口模柱6的位置撒上发热剂,以减缓冒口位置的冷却速度,使得冒口的冷却速度慢于其他部位以起到补缩的效果。
30.s4:通过上模沙型上形成的直浇道3向上模沙型和下模沙型卡扣形成的腔体内浇
注钢水,钢水凝固后,分别将上模沙型和下模沙型剥离,完成采油机齿轮箱的浇铸成型。
31.上模沙型和下模沙型卡合后经上模沙型中的直浇道3向腔体内注入高温钢水,由于下模沙型位于下方,在经直浇道注入钢水后,钢水沿横浇道4进入首先经下模沙型的三个内浇道b进入下模沙型的腔体内,当钢水注满下模沙型后再继续注入钢水时,钢水就会沿上模沙型的内浇道a进入上模沙型的腔体。本实施方式中由于上模沙型中的内浇道a数量较少,经上模沙型的内浇道a进入到上模沙型的钢水的速度小于经下模沙型中内浇道b进入至下模沙型的钢水的速度,在下模沙型的腔体已经注满钢水的情况下,下模沙型中的钢水的温度相对刚进入上模沙型腔体内的钢水温度低,而通过将上模1中内浇道a的数量设计成少于下模2中内浇道b数量来减缓进入上模沙型腔体内的钢水的速度,则可以减小刚进入上模沙型腔体内的钢水温度与已经位于下模沙型腔体内的钢水的温差之差,这样就能够减少产品内部应力集中,避免产品产生裂纹,保证产品性能。
32.s5:对浇铸成型好的采油机齿轮箱进行退火处理,退火处理的条件为::在890℃条件下保温3.5小时,之后炉冷至710℃,保温3.5h,然后转移至冷却液中等温冷却至550℃后空冷至室温。
33.在浇铸成型好采油机齿轮箱后,对该采油机齿轮箱进行退火处理,目的是细化铸件的组织晶粒,部分支柱状晶优化成等轴晶,组织更加稳定。可以让产品在20年连续工作不产生尺寸变化,在低温工况上使用更加优秀。
34.实施方式3:本实施方式为实施方式1的进一步改进,主要改进之处在于,在实施方式1中,高温钢水经内浇道a和内浇道b注入温度较低的上模沙型和下模沙型组成的腔体内后,腔体内的钢水会冷却凝固,由于热胀冷缩的作用,腔体内的钢水冷却时可能会出现钢水倒流入内浇道的情况。而本实施方式中能够有效避免上述情况,具体地说,本实施方式中,将上模1和下模2中的内浇道a和内浇道b,靠近横浇道4的一端设计内径较大,靠近模腔的一端设计内径较小。这样,在形成的上模沙型和下模沙型中,靠近横浇道4的一端内径较大,靠近模腔的一端内径较小,进而在后续的浇注钢水过程中,内径较小的内浇道一端在热胀冷缩过程中钢水会比较快速的凝固,从而能够有效防止钢水倒流入浇道。
35.除此之外,本实施方式与实施方式1完全相同,此处不再赘述。
36.上述实施方式只为说明本发明的技术构思及特点,其目的在于让熟悉此项技术的人能够了解本发明的内容并据以实施,并不能以此限制本发明的保护范围。凡根据本发明精神实质所做的等效变换或修饰,都应涵盖在本发明的保护范围之内。