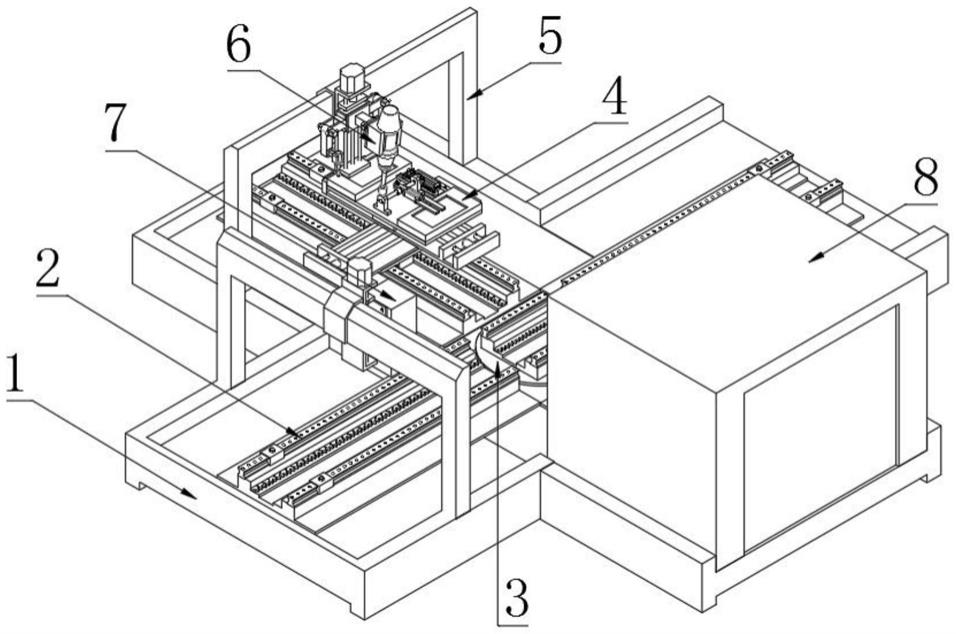
1.本发明涉及制造技术领域,尤其涉及一种桌面式复杂曲面增减材集成制造设备。
背景技术:
2.增材制造(additive manufacturing,am)俗称3d打印,融合了计算机辅助设计、材料加工与成型技术、以数字模型文件为基础,通过软件与数控系统将专用的金属材料、非金属材料以及医用生物材料,按照挤压、烧结、熔融、光固化、喷射等方式逐层堆积,制造出实体物品的制造技术。相对于传统的、对原材料去除-切削、组装的加工模式不同,是一种“自下而上”通过材料累加的制造方法,从无到有。这使得过去受到传统制造方式的约束,而无法实现的复杂结构件制造变为可能。
3.但是,增材技术目前来说难以媲美已经发展了数百年的减材工艺,普遍存在成品表面质量差的缺陷,因此,现在市场上主流的都是结合增材技术和减材技术两者优势的增减复合设备,既能提高材料的利用率,打印出的成品表面质量也比单一的增材设备要高。
4.然而,现有的增减复合设备中减材时抛光加工一般仅能实现三到四轴的加工,这使得很难实现加工曲面结构复杂产品的制造;此外增材与减材又共享同一个工位,增、减材工位进行切换时耗费大量的时间,大大降低了工作效率。
技术实现要素:
5.本发明的目的在于提供一种桌面式复杂曲面增减材集成制造设备以解决上述背景技术中提出的问题。
6.为实现上述目的,本发明的技术方案如下:
7.一种桌面式复杂曲面增减材集成制造设备,包括十字型机座、齿轮传动运输轨道、变轨装置、工件加工平台、龙门支架、工件抛光减材模块、工件增材模块和测温控温模块,所述齿轮传动运输轨道设置有四组且分别固定安装在十字型机座顶端的前后左右四侧中部,所述变轨装置固定安装在十字型机座中心位置,所述变轨装置能够与四组齿轮传动运输轨道分别对接,所述工件加工平台包括工件x向驱动机构、固定安装在x向驱动机构输出端的工件y向驱动机构和固定安装在工件y向驱动机构输出端的工件翻转机构,所述工件加工平台底部设置有自驱动机构,所述自驱动机构用于驱动工件加工平台沿着齿轮传动运输轨道或变轨装置滑动位移,所述龙门支架设置有两组,两组龙门支架分别设置在十字型机座顶端的减材工位和增材工位上,所述工件抛光减材模块和工件增材模块分别固定安装在两组龙门支架上部,所述工件抛光减材模块包括刀具z向驱动机构和固定安装在刀具z向驱动机构输出端的刀具转动机构,所述测温控温模块设置在十字型机座顶端的热处理工位上。
8.进一步的,所述齿轮传动运输轨道包括工位滚珠滑轨、工位轨道底座和工位齿条,所述工位滚珠滑轨设置有两条,两条工位滚珠滑轨对称固定安装在工位轨道底座上端面两侧,所述工位轨道底座内侧端下部与工位滚珠滑轨平行的一侧设置有工位齿条,所述工位轨道底座设置有四组,四组工位轨道底座均匀设置在十字型机座顶端前后左右四侧中部。
9.进一步的,所述工位滚珠滑轨外侧末端固定安装有限位滑台。
10.进一步的,所述变轨装置包括圆盘支座、变轨轨道底座、变轨滚珠滑轨、变轨齿条、涡轮、圆台底座、蜗杆和蜗杆支架,所述变轨轨道底座固定连接在圆盘支座顶端中部,所述变轨滚珠滑轨设置有两条,两条变轨滚珠滑轨对称固定安装在变轨轨道底座上端面两侧,所述变轨轨道底座内侧端下部与变轨滚珠滑轨平行的一侧设置有变轨齿条,所述涡轮固定连接在圆盘支座底端中部,所述圆台底座上端转动连接涡轮,所述圆台底座底端固定连接在十字型机座顶端中部,所述蜗杆啮合涡轮,所述蜗杆两端分别转动连接在两个蜗杆支架上,两个蜗杆支架固定连接在十字型机座顶端,所述蜗杆一端固定连接有步进电机的输出端,所述变轨齿条能够与工位齿条对齐,两条变轨滚珠滑轨能够与两条工位滚珠滑轨对齐。
11.进一步的,所述工件加工平台还包括平台底板、滑块、上平台和工件放置平台,所述滑块设置有两条且两条滑块分别固定连接在平台底板底端两侧,两条滑块滑动连接同侧的两条工位滚珠滑轨或两条变轨滚珠滑轨,所述工件x向驱动机构固定安装在平台底板顶端,所述上平台固定安装在工件y向驱动机构的输出端,所述工件放置平台设置有两个,两个工件放置平台对称设置在上平台的y向两端,所述工件翻转机构固定安装在上平台中部。
12.进一步的,所述工件翻转机构包括丝杆电机、电机支架、连接板、驱动齿条、齿条支架、从动齿轮、中心轴、轴支架和气动手指,所述丝杆电机通过两组电机支架固定安装在上平台中部靠近边缘的位置处,所述连接板一端固定连接在丝杆电机输出端,所述连接板另一端固定连接在驱动齿条一端,所述齿条支架底端固定连接在上平台顶端,所述驱动齿条底端滑动连接在齿条支架顶端开设的限位滑槽,所述驱动齿条啮合从动齿轮,所述从动齿轮固定连接在中心轴一端,所述中心轴两侧分别转动连接两个轴支架,两个轴支架底端固定连接在上平台顶端,所述气动手指固定端固定连接在中心轴中部,所述气动手指输出端能够与两个工件放置平台相配合。
13.进一步的,所述自驱动机构包括电机安装座、c形护板、伺服电机和驱动齿轮,所述电机安装座固定安装在平台底板底端中部,所述c形护板固定安装在电机安装座底端,所述伺服电机固定安装在电机安装座内,所述伺服电机输出端伸出电机安装座下端和c形护板上端并在c形护板内侧固定连接驱动齿轮,所述驱动齿轮啮合工位齿条或变轨齿条。
14.进一步的,所述驱动齿轮在与变轨齿条刚脱离时,所述滑块一端滑动连接在变轨滚珠滑轨上,所述滑块另一端滑动连接在工位滚珠滑轨;由于惯性作用,驱动齿轮滑动至与工位齿条相啮合的位置。
15.进一步的,所述工件抛光减材模块还包括z向支撑板、抛光减材装置、喷液装置支架、喷液装置、烘干装置支架和烘干装置,所述z向支撑板固定安装在减材工位上龙门支架中部,所述刀具z向驱动机构固定安装在z向支撑板上,所述抛光减材装置固定安装在刀具转动机构输出端,所述喷液装置支架和烘干装置支架分别固定安装在刀具z向驱动机构输出端两侧,所述喷液装置和烘干装置分别固定安装在喷液装置支架和烘干装置支架上。
16.与现有技术相比,本发明的有益效果是:
17.1.通过工件x向驱动机构、固定安装在x向驱动机构输出端的工件y向驱动机构、固定安装在工件y向驱动机构输出端的工件翻转机构、刀具z向驱动机构和固定安装在刀具z向驱动机构输出端的刀具转动机构配合使用,能够实现对工件的五轴加工,从而实现对复杂曲面结构产品的制造。
18.2.将减材工位和增材工位分别设置在十字型机座上,并通过中间的变轨装置进行运送切换,使工件能够快速的在减材工位和增材工位进行运送,很好的避免了增减材加工时工件抛光减材模块和工件增材模块共享同一个工位,增、减材工位切换快速,大大提高了工作效率。
附图说明
19.图1是本发明的结构示意图;
20.图2是本发明齿轮传动运输轨道的结构视图;
21.图3是本发明变轨装置的结构视图;
22.图4是本发明变轨装置的底部视角视图;
23.图5是本发明工件加工平台的主视图;
24.图6是本发明工件加工平台的底部视角视图;
25.图7是本发明工件加工平台的结构视图;
26.图8是本发明工件抛光减材模块的结构视图;
27.图9是本发明工件抛光减材模块的主视图。
28.附图中的标号为:1-十字型机座,2-齿轮传动运输轨道,201-工位滚珠滑轨,202-工位轨道底座,203-工位齿条,3-变轨装置,301-圆盘支座,302-变轨轨道底座,303-变轨滚珠滑轨,304-变轨齿条,305-涡轮,306-圆台底座,307-蜗杆,308-蜗杆支架,4-工件加工平台,4x-工件x向驱动机构,4y-工件y向驱动机构,401-平台底板,402-电机安装座,403-c形护板,404-伺服电机,405-驱动齿轮,406-滑块,407-上平台,408-工件放置平台,409-丝杆电机,410-电机支架,411-连接板,412-驱动齿条,413-齿条支架,414-从动齿轮,415-中心轴,416-轴支架,417-气动手指,5-龙门支架,6-工件抛光减材模块,6z-刀具z向驱动机构,6a-刀具转动机构,601-z向支撑板,602-抛光减材装置,603-喷液装置支架,604-喷液装置,605-烘干装置支架,606-烘干装置,7-工件增材模块,8-测温控温模块。
具体实施方式
29.下面结合附图和实施例,对本发明作进一步详细说明。
30.参见图1~9所示,一种桌面式复杂曲面增减材集成制造设备,包括十字型机座1、齿轮传动运输轨道2、变轨装置3、工件加工平台4、龙门支架5、工件抛光减材模块6、工件增材模块7和测温控温模块8,齿轮传动运输轨道2设置有四组且分别固定安装在十字型机座1顶端的前后左右四侧中部,变轨装置3固定安装在十字型机座1中心位置,变轨装置3能够与四组齿轮传动运输轨道2分别对接,工件加工平台4包括工件x向驱动机构4x、固定安装在x向驱动机构4x输出端的工件y向驱动机构4y和固定安装在工件y向驱动机构4y输出端的工件翻转机构,工件加工平台4底部设置有自驱动机构,自驱动机构用于驱动工件加工平台4沿着齿轮传动运输轨道2或变轨装置滑动位移,龙门支架5设置有两组,两组龙门支架5分别设置在十字型机座1顶端的减材工位和增材工位上,工件抛光减材模块6和工件增材模块7分别固定安装在两组龙门支架5上部,工件抛光减材模块6包括刀具z向驱动机构6z和固定安装在刀具z向驱动机构6z输出端的刀具转动机构6a,测温控温模块8设置在十字型机座1顶端的热处理工位上。
31.齿轮传动运输轨道2包括工位滚珠滑轨201、工位轨道底座202和工位齿条203,工位滚珠滑轨201设置有两条,两条工位滚珠滑轨201对称固定安装在工位轨道底座202上端面两侧,工位轨道底座202内侧端下部与工位滚珠滑轨201平行的一侧设置有工位齿条203,工位轨道底座202设置有四组,四组工位轨道底座202均匀设置在十字型机座1顶端前后左右四侧中部。
32.工位滚珠滑轨201外侧末端固定安装有限位滑台,该限位滑台作限位作用。
33.变轨装置3包括圆盘支座301、变轨轨道底座302、变轨滚珠滑轨303、变轨齿条304、涡轮305、圆台底座306、蜗杆307和蜗杆支架308,变轨轨道底座302固定连接在圆盘支座301顶端中部,变轨滚珠滑轨303设置有两条,两条变轨滚珠滑轨303对称固定安装在变轨轨道底座302上端面两侧,变轨轨道底座302内侧端下部与变轨滚珠滑轨303平行的一侧设置有变轨齿条304,涡轮305固定连接在圆盘支座301底端中部,圆台底座306上端转动连接涡轮305,圆台底座306底端固定连接在十字型机座1顶端中部,蜗杆307啮合涡轮305,蜗杆307两端分别转动连接在两个蜗杆支架308上,两个蜗杆支架308固定连接在十字型机座1顶端,蜗杆307一端固定连接有步进电机的输出端,变轨齿条304能够与工位齿条203对齐,两条变轨滚珠滑轨303能够与两条工位滚珠滑轨201对齐,该变轨装置3通过控制主机控制步进电机转动固定的圈数,使变轨滚珠滑轨303能够转动90
°
、180
°
、270
°
和360
°
,从而实现工件能够在四个工位之间的自由切换。
34.工件加工平台4还包括平台底板401、滑块406、上平台407和工件放置平台408,滑块406设置有两条且两条滑块406分别固定连接在平台底板401底端两侧,两条滑块406滑动连接同侧的两条工位滚珠滑轨201或两条变轨滚珠滑轨303,工件x向驱动机构4x固定安装在平台底板401顶端,上平台407固定安装在工件y向驱动机构4y的输出端,工件放置平台408设置有两个,两个工件放置平台408对称设置在上平台407的y向两端,工件翻转机构固定安装在上平台407中部。
35.工件翻转机构包括丝杆电机409、电机支架410、连接板411、驱动齿条412、齿条支架413、从动齿轮414、中心轴415、轴支架416和气动手指417,丝杆电机409通过两组电机支架410固定安装在上平台407中部靠近边缘的位置处,连接板411一端固定连接在丝杆电机409输出端,连接板411另一端固定连接在驱动齿条412一端,齿条支架413底端固定连接在上平台407顶端,驱动齿条412底端滑动连接在齿条支架413顶端开设的限位滑槽,驱动齿条412啮合从动齿轮414,从动齿轮414固定连接在中心轴415一端,中心轴415两侧分别转动连接两个轴支架416,两个轴支架416底端固定连接在上平台407顶端,气动手指417固定端固定连接在中心轴415中部,气动手指417输出端能够与两个工件放置平台408相配合,通过丝杆电机409上丝杆的伸缩,丝杆电机409通过连接板411带动驱动齿条412沿y向位移,此时从动齿轮414在驱动齿条412带动下转动一定角度,从而通过中心轴415带动气动手指417转动一定角度,实现气动手指417夹持工件在两个工件放置平台408之间上方的0~180
°
空间内任意位置停留,配合工件x向驱动机构4x、工件y向驱动机构4y、刀具z向驱动机构6z和刀具转动机构6a实现对工件的五轴加工,从而实现曲面结构复杂产品的制造。
36.自驱动机构包括电机安装座402、c形护板403、伺服电机404和驱动齿轮405,电机安装座402固定安装在平台底板401底端中部,c形护板403固定安装在电机安装座402底端,伺服电机404固定安装在电机安装座402内,伺服电机404输出端伸出电机安装座402下端和
c形护板403上端并在c形护板403内侧固定连接驱动齿轮405,驱动齿轮405啮合工位齿条203或变轨齿条304。
37.驱动齿轮405在与变轨齿条304刚脱离时,滑块406一端滑动连接在变轨滚珠滑轨303上,滑块406另一端滑动连接在工位滚珠滑轨201;由于惯性作用,驱动齿轮405滑动至与工位齿条203相啮合的位置,通过设置的自驱动机构能够使工件快速准确的在减材工位和增材工位之间进行运送,很好的避免了增减材加工时工件抛光减材模块6和工件增材模块7共享同一个工位,增、减材工位进行切换快速,大大提高了工作效率。
38.工件抛光减材模块6还包括z向支撑板601、抛光减材装置602、喷液装置支架603、喷液装置604、烘干装置支架605和烘干装置606,z向支撑板601固定安装在减材工位上龙门支架5中部,刀具z向驱动机构6z固定安装在z向支撑板601上,抛光减材装置602固定安装在刀具转动机构6a输出端,喷液装置支架603和烘干装置支架605分别固定安装在刀具z向驱动机构6z输出端两侧,喷液装置604和烘干装置606分别固定安装在喷液装置支架603和烘干装置支架605上。
39.在使用该装置的时候,工件加工平台4初始位置在十字型机座1顶端的进出料工位上;在需要对工件进行直接减材加工时,控制主机控制伺服电机404驱动驱动齿轮405沿着进出料工位上的工位齿条203转动行进,带动工件行进至变轨装置3上,变轨装置3通过控制主机控制步进电机转动固定的圈数,使变轨滚珠滑轨303逆时针转动90
°
,此时两条变轨滚珠滑轨303与减材工位上的两条工位滚珠滑轨201对齐,控制主机再次驱动伺服电机404转动,使工件行进至减材工位上,通过工件抛光减材模块6对工件进行减材加工即可;在需要进行直接增材加工时,控制主机控制伺服电机404驱动驱动齿轮405沿着进出料工位上的工位齿条203转动行进,带动工件行进至变轨装置3上,变轨装置3通过控制主机控制步进电机转动固定的圈数,使变轨滚珠滑轨303转动180
°
,此时两条变轨滚珠滑轨303与增材工位上的两条工位滚珠滑轨201对齐,控制主机再次驱动伺服电机404转动,使工件行进至增材工位上,通过工件增材模块7进行工件的增材的加工即可;在需要对工件进行增、减材加工时,只需通过控制主机控制伺服电机404驱动驱动齿轮405在增材工位、变轨装置或减材工位上工位齿条203或变轨齿条304转动行进,实现工件从增材工位快速运送至减材工位或从减材工位快速运送至增材工位,避免由于增材与减材共享同一个工位导致增、减材工位进行切换时耗费大量的时间,大大提高了工作效率,设置在热处理工位上的测温控温模块8,能够避免由于减材工艺切换过程中温度等状态的变化造成减材加工不连续,而造成加工质量难以保证问题的发生;在进行减材加工时,工件被夹持在气动手指417上,通过工件x向驱动机构4x、固定安装在x向驱动机构4x输出端的工件y向驱动机构4y、固定安装在工件y向驱动机构4y输出端的工件翻转机构、刀具z向驱动机构6z和固定安装在刀具z向驱动机构6z输出端的刀具转动机构6a配合使用,能够实现对工件的五轴加工,从而实现对复杂曲面结构产品的制造;完成最终加工的工件最后都是运送至进出料工位上,便于工件的取放。
40.需要说明的是,本设备中的伺服电机404采用高功率蓄电池进行供电,该高功率蓄电池固定安装在电机安装座402内,且该高功率蓄电池受控与控制主机。
41.以上所述,仅是本发明的较佳实施例,并非对本发明作任何形式上的限制,任何熟悉本专业的技术人员,在不脱离本发明技术方案范围内,依据本发明的技术实质,对以上实施例所作的任何简单的修改、等同替换与改进等,均仍属于本发明技术方案的保护范围之内。